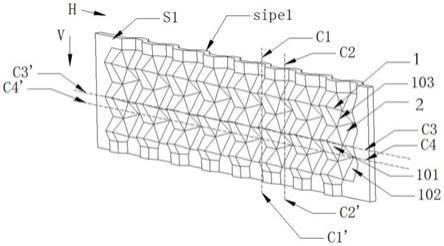
1.本发明涉及轮胎生产设备领域,具体涉及一种能够提升轮胎驱制动性能和磨耗性能的三维钢片。
背景技术:2.轮胎作为汽车的重要安全部件,关系到汽车的各项基本性能,故对轮胎的设计生产要求较高。从以往要求轮胎能够匹配汽车驾驶,到现在还要求轮胎能提供较高操控性能和乘坐舒适性。
3.为了提高轮胎在冰、雪地路面的驱动、制动能力和操控性能,会增加胎面内的刀槽数量。传统的刀槽与胎面垂直,在轮胎行驶过程中刀槽面会发生相对滑动,导致胎面花纹剧烈变形,从而造成胎面花纹的快速磨损。同时胎面布置过多刀槽会导致胎面花纹间接刚性不足,从而无法获得较好的抓地效果,降低了轮胎的驱动、制动性能和操控性能。
4.现有技术中会在刀槽面上布置三维花纹,胎面花纹在轮胎行驶过程中受力时,三维花纹的咬合面之间会形成互锁,从而有效降低刀槽面之间的相互摩擦损耗和生热。同时因为互锁结构的相互支撑,可以增强胎面花纹的刚性,在同等受力情况下三维钢片形成的胎面花纹变形量小于二维钢片形成的胎面花纹变形量,从而提升轮胎的磨耗性能。但是在实际轮胎受力时因为三维花纹咬合面之间在形成互锁时,并不能完全的紧紧咬合,导致接触面之间仍然会产生相对滑动。因此在咬合面上形成的间隙会导致两者之间产生相互摩擦,使得三维花纹的应用无法满足预期的效果,从而无法更好地提升轮胎的驱制动能力以及磨耗性能。
技术实现要素:5.为解决上述技术问题,本发明提供一种能够提升轮胎驱制动性能和磨耗性能的三维钢片。
6.为解决上述技术问题,本发明采用如下技术方案:
7.一种能够提升轮胎驱制动性能和磨耗性能的三维钢片,能伸入到胎面的刀槽中,在两个相对设置的刀槽面上形成三维花纹;包括平面s,以及排列在平面s上凹凸结构;所述凹凸结构包括位于平面s的一侧的凸块、位于平面s另一侧且与该凸块形状对应的凹槽;所述凸块在一个刀槽面上形成凹陷花纹,所述凹槽在另一个刀槽面上形成凸起花纹,所述凹陷花纹和凸起花纹形成的三维花纹在轮胎受力变形时能够形成互锁结构;所述凹凸结构与平面s的交线形成多边形t且该多边形的中心为o,凹凸结构最远离平面s处的几何形状的中心为b,则连线bo与平面s形成的夹角a应当满足:45
°
<a<90
°
;所述凹凸结构朝向靠近轮胎接地面的一侧倾斜;图7中,朝上的一侧为靠近轮胎接地面的方向,朝下的一侧为远离轮胎接地面的方向;本发明通过设置角度a,使凹凸结构为非对称结构,其凸起朝向靠近轮胎接地面的方向倾斜,最终生成的凸起花纹、凹陷花纹也朝向靠近轮胎接地面的方向倾斜。
8.进一步地,凹凸结构最远离平面s处的几何形状为线段l1;所述凹凸结构还包括连
接线段l1与多边形t并用于形成凹凸结构轮廓的三角形、四边形;所述多边形t至少具有四个边。
9.进一步地,线段l1与刀槽的长边方向平行,所述多边形t为正多边形,则线段l1的长度l1与多边形t的边l的长度l之间具有如下关系:1/3l≤l1≤l。
10.进一步地,刀槽的深度方向为v向,刀槽的长边方向为h向,v向与h向垂直且均于平面s平行;h向的凹凸结构的凸块方向交错设置,v向的凹凸结构的凸块方向同向设置或者交错设置。
11.进一步地,所述三维钢片的厚度为0.2mm~5.0mm。
12.与现有技术相比,本发明的有益技术效果是:
13.本发明连线bo与三维钢片深度方向上的夹角a为锐角,即通过本发明生产得到的轮胎三维花纹向靠近轮胎接地面的一侧倾斜,使得轮胎在行驶过程中三维花纹之间的互锁结构可以充分咬合,从而尽量减小咬合面之间的蠕动摩擦;同时,相较于原有的设计,改变角度后可以极大地提高凹凸结构的支撑效果,提升轮胎花纹刚性,从而提升轮胎驱制动能力和操控性能,并进一步提升轮胎的磨耗性能。
附图说明
14.图1为本发明实施例一中三维钢片的立体结构示意图;
15.图2为本发明实施例一中三维钢片的平面视图;
16.图3为本发明实施例一中三维钢片的侧视图;
17.图4为本发明实施例一中凹凸结构的结构示意图;
18.图5为本发明实施例一中凹凸结构的侧视图;
19.图6为本发明凹槽顶面和凸块底面的几何构型图;
20.图7为本发明实施例一中三维钢片在刀槽深度方向上形成的三维花纹剖切图;
21.图8为本发明实施例二中三维钢片的的平面视图;
22.图9为本发明实施例二中凹凸结构的结构示意图;
23.图10为本发明实施例二中凹凸结构的侧视图;
24.图11为本发明实施例二中三维钢片在刀槽深度方向上形成的三维花纹剖切图;
25.图12为对比例一中三维钢片的立体结构示意图;
26.图13为对比例一中三维钢片演变之前的立体结构示意图;
27.图14为对比例一中三维钢片的局部细节图;
28.图15为对比例二中三维钢片的平面示意图;
29.图16为对比例三中三维钢片的平面示意图。
具体实施方式
30.下面结合附图对本发明的一种优选实施方式作详细的说明。
31.本发明中刀槽的深度方向为v向,刀槽的长边方向为h向,v向与h向垂直且均在平面s内。
32.实施例一
33.如图1所示,三维钢片具有平面s1,以及多个由凸块1、凹槽2组成的凹凸结构。其中
凸块1与凹槽2为同一元件(凹凸结构),只是两者位于三维钢片的两侧,一侧形成凸块1则另一侧自然形成凹槽2。轮胎的胎面上具有刀槽,刀槽具有两个相对的刀槽面,三维钢片能够在刀槽中形成三维花纹;具体如图7所示,三维花纹包括由凸块1在一侧刀槽面上形成凹陷花纹、由凹槽2在刀槽面上对应凸起花纹,凸起花纹与凹陷花纹相对应,当轮胎受力变形时,凸起花纹伸入到凹陷花纹中,形成互锁结构,从而有效地抑制两者之间相互蠕动;凸起花纹与凹陷花纹的接触面称为咬合面。
34.实施例一中,三维钢片的凸块1与凹槽2关于公共边103进行连接,因此凹凸结构在h向形成错位咬合。由于凸块1和凹槽2为同一元件,凸块1的下表面101、凹槽2的下表面102也可以分别视为是凹槽2的上表面、凸块1的上表面。
35.实施例一中,三维钢片深度方向(v向),c1-c1’对应的一列凹凸结构的凸块1朝向,与c2-c2’对应的一列凹凸结构的凸块1朝向相反;如果从三维钢片的一侧看去,c1-c1’对应的一列凹凸结构均呈现为凸块1,c2-c2’对应的一列凹凸结构均呈现为凹槽2,即图2中元件一10、元件三12为凸块1,元件二11、元件四13为凹槽2。
36.如图2所示,凸块1与凹槽2关于公共边103交错排列。
37.实施例一中,三维钢片的凹凸结构还存在其他排列方式:c1-c1’对应的一列凹凸结构进行交错式排列,c2-c2’对应的一列凹凸结构也进行交错式排列,即v向相邻的凹凸结构的凸块1朝向相反;如果从三维钢片的一侧看去,v向相邻的两个凹凸结构中一个呈现为凸块1,另一个呈现为凹槽2;即元件一10为凸块1、元件二11为凹槽2、元件三12为凹槽2、元件四13为凸块1。那么,三维钢片不仅在h向上为交错排列,在v向上也是交错排列。
38.如图3所示,凹凸结构线段l1中点与多边形t中心之间的连线与三维钢片深度方向(v向)形成的夹角a小于90度,详见图5。
39.如图4所示,凹凸结构由底面的正六边形、顶面的线段l1、直线l1的两个端点向底面正六边形的各顶点引线段构成。其中线段l1为上顶面线,l2为底面正六边形的对角线,o点是l2中点也是正六边形的中心点。l为正六边形的边长,l1为线段l1的长度,其中1/3l≤l1≤l,l取值范围为0.2mm-10mm。凹凸结构在三维钢片上的排列方式,应使凹凸结构的上表面线l1平行于h向,a点位于o点上方,∠aob即夹角a应满足:45
°
《a《90
°
;图5为夹角a的示意图,即本发明中凸块1是向上倾斜的。
40.如图6所示,多边形t不局限于六边形,也可选自四边形、五边形、七边形、八边形、九边形、十边形、十一边形、十二边形。
41.图7中朝上的一侧为靠近轮胎接地面的方向,朝下的一侧为远离轮胎接地面的方向。互锁结构的上咬合面101’和下咬合面102’,在受力时会相互咬合支撑,由于本发明中的凸块1是向上倾斜的,所以形成的凸起花纹和凹陷花纹也向上倾斜。当轮胎滚动前进时,此时接地压力由上向下传递并作用于轮胎上,上咬合面101’和下咬合面102’会在力的作用下挤压到一起并形成相互支撑,凸起花纹和凹陷花纹向上倾斜,使得上咬合面101’和下咬合面102’接触更加充分,咬合面的作用力更多地作用在垂直于咬合面的方向,平行于咬合面方向的力减少,即通过设置角度a使互锁结构具有非对称的咬合面,一方面可以增加咬合面之间的压力从而增加摩擦极限,另一方面减少咬合面之间的摩擦运动趋势,能够减小互锁结构咬合面之间发生运动的可能性,从而极大地提高了轮胎花纹刚性。由于压力由上向下传递同时又存在侧向力使得刀槽面存在两两接触的互锁结构但又未完全闭合,刀槽内存在
一定的空隙,可以存水,从而带来较好的轮胎湿地性能。
42.如图3所示,实施例一中的三维钢片为非等厚设计,三维钢片的整体厚度保持在0.2mm至5.0mm之间。
43.实施例二
44.实施例二与实施例一的区别在于,所述凹凸结构与平面s的交线形成多边形t为正方形;与实施例一相同,实施例二中的凹凸结构在深度方向(v向)上也存在两种排列方式,即凹凸结构在v向的凸块1朝向相同(此时元件四14、元件五15、元件六16、元件七17分别为凸块1、凹槽2、凸块1、凹槽2),或者在v向的凸块1朝向交错排列(此时元件四14、元件五15、元件六16、元件七17分别为凸块1、凹槽2、凹槽2、凸块1);与实施例一相同,实施例二中的凹凸结构在h向进行交错排列,即凹凸结构在h向的两个相邻凸块1朝向相反。
45.对比例一
46.如图12所示,对比例一的三维钢片由图13中的二维钢片修改而来,在原有的折角面104处去除多个三棱锥形状,得到三棱凸块18、三棱凹槽19,并在h向和v向上均形成相互交错的凹凸结构,形成三维钢片。
47.如图14所示,四面体mnpq即为所挖去的三棱锥,其中由mp的中点到边qn的长度h2等于原二维钢片折角面高度h1时,h2=h1=1/2mp。
48.对比例二
49.如图15所示,对比例二与实施例二的唯一区别在于a的角度不同,a=90
°
,其余结构均相同。
50.对比例三
51.如图16所示,对比例三与实施例一的唯一区别在于a的角度不同,a=90
°
,其余结构均相同。
52.本发明对不同钢片花纹样式进行了仿真研究,仿真方案和仿真结果如下表所示,其中仿真结果为胎面花纹剪切刚度值。规定普通二维钢片对应的胎面花纹剪切刚度为100(基准),其余方案按照普通二维钢片的刚度百分比计算。从仿真结果可以看出,使用三维钢片得到的胎面花纹的剪切刚度,均大于二维钢片得到的胎面花纹的剪切刚度。采用本发明中三维钢片方案形成的胎面花纹,当三维钢片的凹凸结构角度a位于45
°
~90
°
(不取端点值)之间时,其对应胎面花纹剪切刚度最高,大于相同构型且角度a=90
°
对应的胎面花纹的剪切刚度,同时也大于对比例一中三维钢片对应的胎面花纹剪切刚度。
[0053][0054]
以实施例一中的三维钢片为例,本发明对三维钢片样式相同、但厚度不同时的胎面花纹剪切刚度,进行了仿真研究,仿真结果如下表所示,其中仿真结果为胎面花纹剪切刚度值。从仿真结果可以发现,三维钢片样式相同时,胎面花纹剪切刚度随着三维钢片厚度的增大而减小。随着三维钢片厚度的增大,三维钢片形成凹陷花纹和凸起花纹之间的接触面积和咬合度均呈下降趋势,从而导致胎面花纹剪切刚度的减小。将0.2mm厚度三维钢片仿真得到的胎面花纹刚度定为100,其余厚度对应的结构按基准的百分比计算。
[0055]
三维钢片厚度胎面花纹剪切刚度0.2mm1000.4mm99.20.6mm97.20.8mm95.31.0mm92.41.2mm90.4
[0056]
对于本领域技术人员而言,显然本发明不限于上述示范性实施例的细节,而且在不背离本发明的精神或基本特征的情况下,能够以其他的具体形式实现本发明。因此无论从哪一点来看,均应将实施例看作是示范性的,而且是非限制性的,本发明的范围由所附权利要求而不是上述说明限定,因此旨在将落在权利要求的等同要件的含义和范围内的所有变化囊括在本发明内,不应将权利要求中的任何附图标记视为限制所涉及的权利要求。
[0057]
此外,应当理解,虽然本说明书按照实施方式加以描述,但并非每个实施方式仅包含一个独立技术方案,说明书的这种叙述方式仅仅是为了清楚起见,本领域技术人员应当将说明书作为一个整体,各实施例中的技术方案也可以经适当组合,形成本领域技术人员可以理解的其他实施方式。