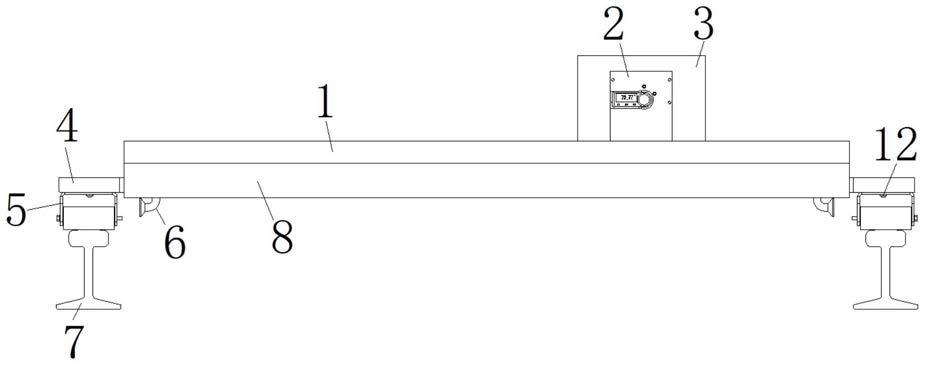
1.本发明涉及轨道领域,尤其涉及重力平衡式数显超高检测装置。
背景技术:2.轨道检查车,用来检测轨道的几何状态和不平顺状况,以便评价轨道几何状态的特种车辆,简称轨检车。它是保障行车安全、平稳、舒适和指导轨道养护维修的重要工具。
3.根据轨检车的记录,可以发现轨道平顺状态不良的地点,以便采取紧急补修或限速措施,并确定应进行计划维修的里程段落,编制维修作业计划。
4.中国于1953年试制成功第一辆自己设计的客车式机械轨检车。1971年中国又制成“tsk22”型电气轨道检查车。这种电气轨检车长约26米,自重约62吨,能同中国的特快列车联挂进行检测。
5.这种电气轨检车采用旋转变压器作位移传感器,借助三个轮对所构成的18.5米不对称弦测量轨道高低,用三轴转向架的三个轮对构成的3.4米对称弦测量钢轨接头低陷;轨道水平状态由陀螺装置测量,三角坑由相距15.1米的两个轮对测得。测量结果用电磁笔记录仪记录在纸带上。
6.70年代中期,中国开始进行轨检新技术的研究,现已先后研制出能测量轨道高低、水平、轨面不平顺的“惯性基准轨道不平顺检测装置”和“轨道超高检测装置”、“充电式轨距检测装置”、“多功能振动检测装置”等新装置。正在进一步研制用这些新装置和其他先进设备(如电子计算机等)装备的新型轨道检查车。
7.在轨道初调过程中,轨道超高调整次数多,大型设备使用不便,由于现在用的装置并不能很好的显示出超高值的数据,仍需工作人员进行测量,不仅麻烦数据还不连续,都是随机抽检数据,还不利于操作,不利于和理论值进行对比,因此,我们设计出重力平衡式数显超高检测装置。
技术实现要素:8.本发明的目的在于提供重力平衡式数显超高检测装置,以解决上述技术问题。
9.本发明为解决上述技术问题,采用以下技术方案来实现:
10.重力平衡式数显超高检测装置,包括变速箱支撑架,所述变速箱支撑架底部固设有可调节辅助机构,所述可调节辅助机构上固设有多个移动组件,所述变速箱支撑架背面设置有变速箱,所述变速箱背面设置有平衡块,所述变速箱支撑板上设置有防护罩,所述变速箱、平衡块皆位于防护罩内部,所述变速箱支撑板表面有旋转型光栅液晶显示模块。
11.优选的,所述平衡块为钢材质,所述平衡块为双肾形状。
12.优选的,所述可调节辅助机构包括第一铝板、第二铝板、蓄油箱、安装架、插槽、刻度尺、安装管、第二弹簧、活动板、插杆、滑块,所述第一铝板与变速箱支撑架固接,所述第一铝板底部固设有两个安装架,两个所述安装架之间固设有隔板,所述隔板底部对称镶嵌有两个刻度尺,所述隔板上贯穿设置有多个插槽,所述隔板与安装架的相对面上皆固设有滑
块,两个所述滑块之间滑动连接有第二铝板,两个所述第二铝板相背离的一端皆固设有蓄油箱,所述第二铝板上贯穿固设有多个安装管,所述安装管内部滑动连接有活动板,所述活动板上贯穿固设有插杆,所述插杆顶端延伸至安装管外侧并与插槽插接,所述插杆底端延伸至安装管下方,所述安装管内部设置有第二弹簧,所述第二弹簧套设在插杆上,所述第二弹簧一端与活动板固接,所述第二弹簧另一端与安装管固接。
13.优选的,所述移动组件与蓄油箱固接,所述蓄油箱底部贯穿固设有电动阀门。
14.优选的,所述隔板上方设置有固定管,所述固定管内部固设有抽风机,所述固定管上固设有两个折叠连接管,两个所述折叠连接管分别与两个第二铝板固接并贯穿第二铝板延伸至第二铝板下方。
15.优选的,所述隔板上贯穿固设有多个安装盒,所述安装盒内部滑动连接有滑板,所述滑板顶部通过多个伸缩杆、多个第一弹簧与安装盒相连接,所述第一弹簧套设在伸缩杆上,所述滑板顶部固设有按压柱,所述按压柱上方设置有按压开关,所述按压开关与安装盒固接,所述第二铝板上皆贯穿固设有螺纹套,所述螺纹套内部螺纹连接有螺杆。
16.优选的,两个所述按压开关分别与抽风机、电动阀门电性连接。
17.优选的,所述第一铝板、第二铝板皆为6061航空铝板。
18.优选的,所述安装盒内腔固设有多个限位板。
19.本发明的有益效果是:
20.1、本发明轨道初调中为了能直接显示超高值方便和理论值进行对比,本检测车采用了旋转型光栅液晶显示模块,轨检车通过曲线段外侧轨道会抬高,导致车体会旋转一个角度,因为超高值相对于轨距方向夹角小,所以车体旋转角度也不大,为了通过平衡块及变速箱使超高值1:1显示出来,由于1435毫米轨距的铁路外轨每超高26.27毫米就对应车体每旋转1度。最终通过变速箱放大角度值26.27倍来实现变速箱输出轴每旋转一度就等于高度方向一毫米,这样就将超高造成的角度值转换为长度方向的毫米值。因为圆周为360度,所以本小车理论上测量范围为-360~360毫米,本超高显示器相对于第一代,齿轮模数由0.5改成了0.25,直齿轮改成了斜齿轮,增加了防护罩,读数由机械指针显示改为数字显示,这样每个位置能充分咬合避免了细微摆动间隙,避免了平衡块迎风面较大影响读数,运行更顺畅,由于数显读数更方便,读数分辨率由1毫米提高到0.05毫米提高了20倍所以精度更高。
21.2、变速箱使用齿轮采用二级减速斜齿轮,齿轮模数选用0.25,齿轮采用3毫米厚的45号中碳钢,通过数控铣齿机进行慢走丝加工,齿轮中间通过挖孔进行减重处理,同时对齿轮进行热处理保证其有足够的强度、硬度和冲击韧性,为了减少工作阻力和保证良好的工作状态。
22.3、通过设置多个第二铝板,并进行限位第二铝板,从而可使第一铝板、第二铝板组合长度得以变化,从而将适用于不同规格的轨道,且借助刻度尺还能精准的进行调节,减少误差的产生。
23.4、通过调节螺杆,可使抽风机、电动阀门进行运作,由于第二铝板上设有折叠连接管,从而第二铝板延伸时,折叠连接管也将随之移动,且折叠连接管的出风端对准移动组件,借助抽风机,可使折叠连接管的排风,从而进行对移动组件吹风,起到散热作用,避免移动组件在钢轨上移动时产生热量过大,而造成损坏,电动阀门打开,蓄油箱内的润滑油将缓
慢的不断滴落,从而可供移动组件提供润滑效果。
附图说明
24.图1为本发明的结构示意图;
25.图2为本发明变速箱支撑架与旋转型光栅液晶显示模块的连接示意图;
26.图3为本发明可调节辅助机构的结构示意图;
27.图4为本发明图3的a部放大示意图;
28.图5为发明第一铝板与第二铝板的连接示意图;
29.图6为本发明图5的b部放大示意图;
30.图7为本发明图5的c部放大示意图;
31.附图标记:1、第一铝板;2、变速箱支撑架;3、防护罩;4、蓄油箱;5、移动组件;6、折叠连接管;7、钢轨;8、安装架;9、旋转型光栅液晶显示模块;10、变速箱;11、平衡块;12、电动阀门;13、第二铝板;14、刻度尺;16、插槽;17、隔板;18、固定管;19、抽风机;21、滑块;22、滑板;23、安装盒;24、限位板;25、螺杆;26、螺纹套;27、第一弹簧;28、伸缩杆;29、按压开关;30、按压柱;31、插杆;32、活动板;33、安装管;34、第二弹簧。
具体实施方式
32.为了使本发明实现的技术手段、创作特征、达成目的与功效易于明白了解,下面结合具体实施例和附图,进一步阐述本发明,但下述实施例仅仅为本发明的优选实施例,并非全部。基于实施方式中的实施例,本领域技术人员在没有做出创造性劳动的前提下所获得其它实施例,都属于本发明的保护范围。
33.下面结合附图描述本发明的具体实施例。
34.如图1-7所示,重力平衡式数显超高检测装置,包括变速箱10支撑架2,变速箱支撑架2底部固设有可调节辅助机构,可调节辅助机构上固设有多个移动组件5,变速箱支撑架2背面设置有变速箱10,变速箱10背面设置有平衡块11,变速箱10支撑板上设置有防护罩3,变速箱10、平衡块11皆位于防护罩3内部,变速箱10支撑板表面有旋转型光栅液晶显示模块9,平衡块11为钢材质,平衡块11为双肾形状,第一铝板1、第二铝板13皆为6061航空铝板;
35.铁路轨道超高值一般为0-150毫米之间,对应水平距离1505毫米标准轨距1435+钢轨宽70,当检测车通过曲线段时,外侧钢轨7的抬高会造成车体横向旋转一个角度,由正切公式tana=超高值/钢轨7中心距1505可知,算得的角度值很小所以反应不敏感,同时如果直接靠吊锤自重指示旋转角度的话,要想知道实际超高值则需要根据旋转的角度值套公式计算,费时费力非常麻烦,为了直接采用标准的360度度盘按1:1将超高值显示出来即指针每旋转一度就等于距离方向一毫米,目的是利用变速箱10实现角度和长度单位之间的数值转换,那么就要通过平衡块11及加速箱进行数值放大;
36.首先进行模拟计算,先在cad图上画一条1505毫米长的直线,然后沿直线一头为端点画一条角度为1度长度为1505毫米的直线,最后通过标注开口的宽度为26.27毫米,然后通过计算器计算验证tan1
°
=超高值/1505,算得超高值也为26.27毫米,由此可知当车体每旋转1度时那么对应的超高值就为26.27毫米,以此为基准设计了两级加速箱,两级齿轮比分别为20:100和20:105.08,考虑到动力损耗及齿轮加工方便最终采用加速比为1:26.5,对
应齿数为20:100和20:106,本超高显示器相对于第一代,齿轮模数由0.5改成了0.25,直齿轮改成了斜齿轮,增加了防护罩,机械指针表盘换成了旋转型光栅显示器,这样每个位置能充分咬合避免了细微摆动间隙,避免了平衡块11迎风面较大影响读数,运行更顺畅读数更精准。齿轮采用3毫厚的45号中碳钢,显示模块选用旋转型光栅传感器,显示器及定栅固定在显示器支架上,动栅通过联轴器与变速箱10输出轴连接。
37.这样当小车通过曲线路段时,车体左右旋转而平衡块11始终保持水平状态从而带动变速箱10输入轴也稳定在原始状态,这样就通过车体旋转带动旋转光栅传感器的定栅跟随车体顺时针或逆时针旋转,旋转光栅传感器的动栅通过联轴器与变速箱10的输出轴连接也会跟着加速旋转,通过变速箱10将角度值进行放大26.27倍,这样变速箱10就将角度值转换成毫米值就实现了显示实际超高值的目的,此时只需要在超高液晶显示器屏幕上看数值就行了,比如显示器显示的数值为70.77
°
就代表超高值为右超高77.77毫米;
38.由于本超高显示器是根据标准轨距1435毫米设计的,当采用宽轨或者窄轨时需要进行加速比重新计算,重新匹配齿轮,其计算原理与此相同。因超高显示器属于可拆装,故应在每次组装后进行一次校准,校准方法是利用尼龙车轮上的棱镜组,先测同一里程的右轨轨面高程,然后旋转车体180
°
测左轨轨面的高程,两个轨面的高程差即超高值,然后将尼龙轮放在低轨一侧,下面通过楔形块将左右车体抬至车体水平,然后将平衡块11保持水平,通过液晶显示器下的归零键将角度值归0就可以进行正常作业了;
39.因超高显示器反应太敏感,稍微一点活动影响力会通过变速箱10放大26.27倍,考虑到平衡块11迎风面较大,本检测装置安装了防护罩3,为防止齿轮摩擦阻力、震动等因素可能会引起平衡块11自平衡复位误差导致显示数值不准,因此在每次读数时特别注意平衡块11上的水平气泡是否居中,如果不居中请手动转一下平衡块11,等气泡居中就可以精确读数了,有砟轨道因大机捣固遍数较多,前几遍可用超高显示器验证超高,进入精调阶段请用棱镜测量,无砟轨道粗调阶段超高一律用棱镜测量,超高测量棱镜插孔在尼龙车轮中间正上方;
40.可调节辅助机构包括第一铝板1、第二铝板13、蓄油箱4、安装架8、插槽16、刻度尺14、安装管33、第二弹簧34、活动板32、插杆31、滑块21,第一铝板1与变速箱支撑架2固接,第一铝板1底部固设有两个安装架8,两个安装架8之间固设有隔板17,隔板17底部对称镶嵌有两个刻度尺14,隔板17上贯穿设置有多个插槽16,隔板17与安装架8的相对面上皆固设有滑块21,两个滑块21之间滑动连接有第二铝板13,两个第二铝板13相背离的一端皆固设有蓄油箱4,第二铝板13上贯穿固设有多个安装管33,安装管33内部滑动连接有活动板32,活动板32上贯穿固设有插杆31,插杆31顶端延伸至安装管33外侧并与插槽16插接,插杆31底端延伸至安装管33下方,安装管33内部设置有第二弹簧34,第二弹簧34套设在插杆31上,第二弹簧34一端与活动板32固接,第二弹簧34另一端与安装管33固接,移动组件5与蓄油箱4固接,蓄油箱4底部贯穿固设有电动阀门12,隔板17上方设置有固定管18,固定管18内部固设有抽风机19,固定管18上固设有两个折叠连接管6,两个折叠连接管6分别与两个第二铝板13固接并贯穿第二铝板13延伸至第二铝板13下方,隔板17上贯穿固设有多个安装盒23,安装盒23内部滑动连接有滑板22,滑板22顶部通过多个伸缩杆28、多个第一弹簧27与安装盒23相连接,第一弹簧27套设在伸缩杆28上,滑板22顶部固设有按压柱30,按压柱30上方设置有按压开关29,按压开关29与安装盒23固接,第二铝板13上皆贯穿固设有螺纹套26,螺纹套
26内部螺纹连接有螺杆25,两个按压开关29分别与抽风机19、电动阀门12电性连接,安装盒23内腔固设有多个限位板24,具体使用时,可通过拉动插杆,使插杆与插槽风力,从而可移动第二铝板,使第一铝板、第二铝板的总长变长,从而可更好的适用于不同规格的钢轨,且在移动第二铝板13的时候,可通过刻度尺14进行观察其移动的距离,从而可精准的进行调节,便于操作,减小误差,在是使用时,将移动组件5放置在对应的钢轨7上,使其工作,在工作前,可转动螺杆25,使螺杆25进行挤压滑板22,从而使滑板22上移,滑板22带动挤压柱上移,从而使挤压柱挤压按压开关29,两个按压开关29分别启动抽风机19和电动阀门12,由于第二铝板13上设有折叠连接管6,从而第二铝板13延伸时,折叠连接管6也将随之移动,且折叠连接管6的出风端对准移动组件5,借助抽风机19,可使折叠连接管6的排风,从而进行对移动组件5吹风,起到散热作用,避免移动组件5在钢轨7上移动时产生热量过大,而造成损坏,电动阀门12打开,蓄油箱4内的润滑油将缓慢的不断滴落,从而可供移动组件5提供润滑效果。
41.以上显示和描述了本发明的基本原理、主要特征和本发明的优点。本行业的技术人员应该了解,本发明不受上述实施例的限制,上述实施例和说明书中描述的仅为本发明的优选例,并不用来限制本发明,在不脱离本发明精神和范围的前提下,本发明还会有各种变化和改进,这些变化和改进都落入要求保护的本发明范围内。本发明要求保护范围由所附的权利要求书及其等效物界定。