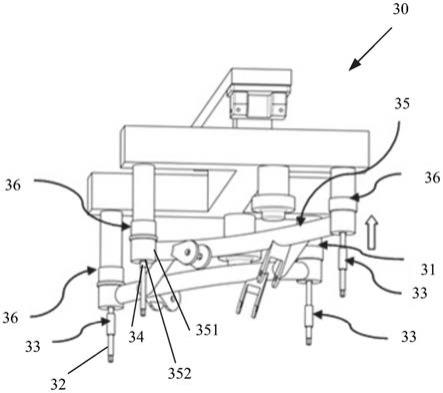
1.本实用新型涉及车辆领域,特别涉及一种用于副车架定位及车身弹簧辅助压装的压装机构。
背景技术:2.多通道道路模拟试验是汽车开发过程中一项重要的室内试验验证环节。在试验室中进行多通道道路模拟试验前,需要临时组装底盘系统,包括副车架、控制臂、连杆、减震器、螺旋弹簧、转向机和制动系统等。当汽车后悬架采用独立悬架时,通常采用的是多连杆式独立悬架,这种悬架的螺旋弹簧与减震器是分开的。
3.随着人们对汽车舒适性的追求提升,像suv这样的大型车越来越受欢迎,汽车悬架中的螺旋弹簧也改用刚度更大的弹簧,因此,在试验室安装弹簧的难度也随之变大。
4.通常是在副车架安装好之后,需要开始对螺旋弹簧安装,用弹簧压缩工具将弹簧压缩后送入弹簧安装位置。压缩弹簧的工具目前主要有两种,一种是爪式压缩工具,另一种是滑柱丝杆式弹簧压缩工具。
5.图1为现有技术中爪式压缩工具的结构示意图。如图1所示,爪式压缩工具10的丝杆11上有一对抱爪12,可以抱住弹簧,在弹簧两侧各使用一个爪式压缩工具,可以先实现压缩弹簧,再将弹簧送入装车位置,这种方法的不足之处有:
6.一、因为抱爪11的爪钩与弹簧不完全匹配,爪钩会损坏弹簧表面橡胶保护层,引起试验委托方的投诉,严重的情况则更需要更换弹簧。
7.二、将弹簧送入安装位置之后,压缩工具可能无法顺利取出而需再一次进行拆卸,从而导致增加工作量。
8.三、弹簧放入安装位置时,即使上下弹簧垫端面与弹簧末端面贴合,但松开弹簧之后,弹簧会有一定的旋转,使弹簧端面与弹簧垫端面分离,因而会导致分离间隙过大,会造成不满足装车要求的问题则需要返工。
9.四、当弹簧刚度很大时,普通的爪钩式弹簧压缩工具会出现压缩困难的现象,还会出现丝杆弯曲、弹簧逃出爪钩等危险工况的问题出现。
10.图2为现有技术中滑柱丝杆式弹簧压缩工具的结构示意图。如图2所示,滑柱丝杆式弹簧压缩工具20的丝杆21上设置有一对抱爪22同样存在上一种工具第二、三点的不足。所以这两种工具都不适用于螺旋弹簧与减震器分离式悬架系统试验台架搭建。
技术实现要素:11.本实用新型要解决的技术问题是为了克服现有技术中副车架安装弹簧难度大,不适用于螺旋弹簧与减震器分离式悬架系统试验台架搭建的缺陷,提供一种用于副车架定位及车身弹簧辅助压装的压装机构。
12.本实用新型是通过下述技术方案来解决上述技术问题的:
13.一种用于副车架定位及车身弹簧辅助压装的压装机构,其特点在于,压装机构包
括多个车身安装点位、多个螺纹杆、多个导向管和多个导向管定位螺套,每一螺纹杆安装至对应车身安装点位的底部,导向管套设在对应螺纹杆上;
14.副车架具有多个安装部,每一安装部开设有贯通的安装孔,安装孔的孔径与导向管的外径相互匹配,使得副车架的安装部套设在对应导向管外,导向管定位螺套套设在对应螺纹杆上,位于副车架的安装部的底端,用于紧固副车架的安装部。
15.一种用于副车架定位及车身弹簧辅助压装的压装机构,其特点在于,压装机构包括多个第一车身安装点位、多个螺纹杆、多个导向管、多个挡板和多个调节螺母,每一螺纹杆安装至对应的第一车身安装点位的底部,导向管套设在对应螺纹杆上;
16.副车架具有多个安装部,每一安装部开设有贯通的安装孔,安装孔的孔径与导向管的外径相互匹配,使得副车架的安装部套设在对应导向管外,挡板和调节螺母依次套设在对应螺纹杆上,位于副车架的安装部的底端,用于紧固副车架的安装部。
17.根据本实用新型的一个实施例,压装机构还包括多个弹簧压装位、第二车身安装点位和多个螺旋弹簧,每一螺旋弹簧的一端与对应弹簧压装位的端面贴合,另一端与减震器连接,且减震器的安装点与车身安装点位连接。
18.根据本实用新型的一个实施例,弹簧压装位的端面为弹簧橡胶垫端面。
19.根据本实用新型的一个实施例,螺纹杆与车身安装点位的底部之间为螺纹连接。
20.根据本实用新型的一个实施例,螺纹杆尾端为正六边形。
21.根据本实用新型的一个实施例,导向管的内径为14mm-16mm,导向管的外径为20mm-25mm。
22.根据本实用新型的一个实施例,导向管定位螺套的内螺纹与螺纹杆的螺纹相同,且内螺纹和螺纹杆的螺纹长度为20mm-25mm。
23.根据本实用新型的一个实施例,挡板为圆形,且挡板的上下端面均为平面。
24.根据本实用新型的一个实施例,调节螺母的外形为正六边形。
25.本实用新型的积极进步效果在于:
26.本实用新型用于副车架定位及车身弹簧辅助压装的压装机构,具有如下的诸多优势:
27.一、采用本实用新型的方法,可以保证更换前后的副车架位置基本一致。
28.二、在定位好副车架以后,可以将副车架向下调节,直到弹簧可以自由放入,放入弹簧后,弹簧橡胶垫的端面与弹簧端面自然贴合,可以直接完成安装。
附图说明
29.本实用新型上述的以及其他的特征、性质和优势将通过下面结合附图和实施例的描述而变的更加明显,在附图中相同的附图标记始终表示相同的特征,其中:
30.图1为现有技术中爪式压缩工具的结构示意图。
31.图2为现有技术中滑柱丝杆式弹簧压缩工具的结构示意图。
32.图3为本实用新型用于副车架定位及车身弹簧辅助压装的压装机构的结构示意图。
33.图4为本实用新型用于副车架定位及车身弹簧辅助压装的压装机构的实施例一的结构示意图。
34.图5为本实用新型用于副车架定位及车身弹簧辅助压装的压装机构的实施例一的使用状态示意图。
35.图6为本实用新型用于副车架定位及车身弹簧辅助压装的压装机构的实施例二中安装螺旋弹簧的结构示意图一。
36.图7为本实用新型用于副车架定位及车身弹簧辅助压装的压装机构的实施例二中安装螺旋弹簧的结构示意图二。
37.图8为本实用新型用于副车架定位及车身弹簧辅助压装的压装机构的实施例二中安装螺旋弹簧的结构示意图三。
38.图9为本实用新型用于副车架定位及车身弹簧辅助压装的压装机构的实施例二中安装螺旋弹簧的结构示意图四。
39.【附图标记】
40.爪式压缩工具
ꢀꢀꢀꢀꢀꢀꢀꢀꢀꢀꢀꢀꢀꢀꢀꢀꢀꢀꢀꢀꢀꢀꢀꢀ
10
41.丝杆
ꢀꢀꢀꢀꢀꢀꢀꢀꢀꢀꢀꢀꢀꢀꢀꢀꢀꢀꢀꢀꢀꢀꢀꢀꢀꢀꢀꢀꢀꢀꢀꢀ
11
42.抱爪
ꢀꢀꢀꢀꢀꢀꢀꢀꢀꢀꢀꢀꢀꢀꢀꢀꢀꢀꢀꢀꢀꢀꢀꢀꢀꢀꢀꢀꢀꢀꢀꢀ
12
43.滑柱丝杆式弹簧压缩工具
ꢀꢀꢀꢀꢀꢀꢀꢀꢀꢀꢀꢀꢀꢀ
20
44.丝杆
ꢀꢀꢀꢀꢀꢀꢀꢀꢀꢀꢀꢀꢀꢀꢀꢀꢀꢀꢀꢀꢀꢀꢀꢀꢀꢀꢀꢀꢀꢀꢀꢀ
21
45.抱爪
ꢀꢀꢀꢀꢀꢀꢀꢀꢀꢀꢀꢀꢀꢀꢀꢀꢀꢀꢀꢀꢀꢀꢀꢀꢀꢀꢀꢀꢀꢀꢀꢀ
22
46.压装机构
ꢀꢀꢀꢀꢀꢀꢀꢀꢀꢀꢀꢀꢀꢀꢀꢀꢀꢀꢀꢀꢀꢀꢀꢀꢀꢀꢀꢀ
30
47.车身安装点位
ꢀꢀꢀꢀꢀꢀꢀꢀꢀꢀꢀꢀꢀꢀꢀꢀꢀꢀꢀꢀꢀꢀꢀꢀ
31
48.螺纹杆
ꢀꢀꢀꢀꢀꢀꢀꢀꢀꢀꢀꢀꢀꢀꢀꢀꢀꢀꢀꢀꢀꢀꢀꢀꢀꢀꢀꢀꢀꢀ
32
49.导向管
ꢀꢀꢀꢀꢀꢀꢀꢀꢀꢀꢀꢀꢀꢀꢀꢀꢀꢀꢀꢀꢀꢀꢀꢀꢀꢀꢀꢀꢀꢀ
33
50.导向管定位螺套
ꢀꢀꢀꢀꢀꢀꢀꢀꢀꢀꢀꢀꢀꢀꢀꢀꢀꢀꢀꢀꢀꢀ
34
51.副车架
ꢀꢀꢀꢀꢀꢀꢀꢀꢀꢀꢀꢀꢀꢀꢀꢀꢀꢀꢀꢀꢀꢀꢀꢀꢀꢀꢀꢀꢀꢀ
35
52.安装部
ꢀꢀꢀꢀꢀꢀꢀꢀꢀꢀꢀꢀꢀꢀꢀꢀꢀꢀꢀꢀꢀꢀꢀꢀꢀꢀꢀꢀꢀꢀ
351
53.安装孔
ꢀꢀꢀꢀꢀꢀꢀꢀꢀꢀꢀꢀꢀꢀꢀꢀꢀꢀꢀꢀꢀꢀꢀꢀꢀꢀꢀꢀꢀꢀ
352
54.第一车身安装点位
ꢀꢀꢀꢀꢀꢀꢀꢀꢀꢀꢀꢀꢀꢀꢀꢀꢀꢀꢀꢀ
36
55.挡板
ꢀꢀꢀꢀꢀꢀꢀꢀꢀꢀꢀꢀꢀꢀꢀꢀꢀꢀꢀꢀꢀꢀꢀꢀꢀꢀꢀꢀꢀꢀꢀꢀ
37
56.调节螺母
ꢀꢀꢀꢀꢀꢀꢀꢀꢀꢀꢀꢀꢀꢀꢀꢀꢀꢀꢀꢀꢀꢀꢀꢀꢀꢀꢀꢀ
38
57.弹簧压装位
ꢀꢀꢀꢀꢀꢀꢀꢀꢀꢀꢀꢀꢀꢀꢀꢀꢀꢀꢀꢀꢀꢀꢀꢀꢀꢀ
39
58.第二车身安装点位
ꢀꢀꢀꢀꢀꢀꢀꢀꢀꢀꢀꢀꢀꢀꢀꢀꢀꢀꢀꢀ
40
59.螺旋弹簧
ꢀꢀꢀꢀꢀꢀꢀꢀꢀꢀꢀꢀꢀꢀꢀꢀꢀꢀꢀꢀꢀꢀꢀꢀꢀꢀꢀꢀ
41
60.减震器
ꢀꢀꢀꢀꢀꢀꢀꢀꢀꢀꢀꢀꢀꢀꢀꢀꢀꢀꢀꢀꢀꢀꢀꢀꢀꢀꢀꢀꢀꢀ
42
61.减震器的安装点
ꢀꢀꢀꢀꢀꢀꢀꢀꢀꢀꢀꢀꢀꢀꢀꢀꢀꢀꢀꢀꢀꢀ
421
具体实施方式
62.为让本实用新型的上述目的、特征和优点能更明显易懂,以下结合附图对本实用新型的具体实施方式作详细说明。
63.现在将详细参考附图描述本实用新型的实施例。现在将详细参考本实用新型的优选实施例,其示例在附图中示出。在任何可能的情况下,在所有附图中将使用相同的标记来
表示相同或相似的部分。
64.此外,尽管本实用新型中所使用的术语是从公知公用的术语中选择的,但是本实用新型说明书中所提及的一些术语可能是申请人按他或她的判断来选择的,其详细含义在本文的描述的相关部分中说明。
65.此外,要求不仅仅通过所使用的实际术语,而是还要通过每个术语所蕴含的意义来理解本实用新型。
66.实施例一:
67.图3为本实用新型用于副车架定位及车身弹簧辅助压装的压装机构的结构示意图。图4为本实用新型用于副车架定位及车身弹簧辅助压装的压装机构的实施例一的结构示意图。图5为本实用新型用于副车架定位及车身弹簧辅助压装的压装机构的实施例一的使用状态示意图。
68.如图3至图5所示,本实用新型公开了一种用于副车架定位及车身弹簧辅助压装的压装机构30,压装机构30包括多个车身安装点位31、多个螺纹杆 32、多个导向管33和多个导向管定位螺套34,每一螺纹杆32安装至对应车身安装点位31的底部,导向管33套设在对应螺纹杆32上。副车架35具有多个安装部351,每一安装部351开设有贯通的安装孔352,安装孔352的孔径与导向管33的外径相互匹配,使得副车架35的安装部351套设在对应导向管33 外,导向管定位螺套34套设在对应螺纹杆32上,位于副车架35的安装部351 的底端,用于紧固副车架的安装部351。
69.例如,首先将螺纹杆32螺旋装入副车架35的四个车身安装点位31。然后,在车身安装点位31依次装上导向管33、导向管定位螺套34。最后,借助外力将副车架35由下往上安装。
70.优选地,螺纹杆32与车身安装点位31的底部之间为螺纹连接。螺纹杆32 尾端优选为正六边形。通过将螺纹杆32尾端设置为正六边形,可以方便内六角套筒进行安装操作。
71.根据上述结构描述,本实用新型用于副车架定位及车身弹簧辅助压装的压装机构中,螺纹杆32的螺纹规格与副车架35的车身安装点螺栓规格相同。通过调研和统计各大主机厂车型的车身安装螺栓,基本为m16和m14,具体规格为:m16
×
1.5、m16
×
1、m14
×
1.5、m14
×
1。
72.为保证通用性,即满足不同车型需求,共设置四种规格的螺纹杆:m16
×
1.5、m16
×
1、m14
×
1.5、m14
×
1,每种规格四件。螺纹杆尾端为正六边形,方便使用内六角套筒操作。
73.以下说明以m16螺纹杆为例,例如导向管33的内径为16mm,则导向管 33的外径优选为20mm-25mm。例如,将导向管33的外径设置为25mm、24mm、 23mm、22mm、21mm、20mm,共6种规格,从而提高通用性,每种规格四个。导向管33的长度小于副车架35的车身安装点悬置厚度。
74.优选地,导向管定位螺套34的内螺纹与螺纹杆32的螺纹相同,且内螺纹和螺纹杆的螺纹长度为20mm。例如,螺旋杆32可以m16的螺纹,则导向管定位螺套34的外径可以采用19mm的外径。
75.所述用于副车架定位及车身弹簧辅助压装的压装机构的使用方法具体为:
76.当安装副车架时,首先将螺纹杆32装入副车架35的四个车身安装点位31,螺纹杆32需拧入螺纹孔底部,防止其意外滑出。如图4所示,在车身安装点位31依次装上导向管33、
导向管定位螺套34,导向管33的外径与副车架安装点孔径相同。
77.将副车架35的四个安装孔套在四个螺纹杆上,借助外力将副车架35由下往上安装到夹具上,因为车身安装点位31处的导向管33的外径与安装点孔径相同,所以此处导向管33与安装孔完全匹配。
78.如图5所示,分别在车身安装点位31试装直径由大到小的导向管33,直到刚好可以装入匹配的导向管33,然后装入导向管定位螺套34,保证导向管与安装孔无间隙,安装好导向管之后副车架无晃动。记录好车身安装点位31 所装导向管33的直径。
79.若无需安装螺旋弹簧,则先取出车身安装点位31处的螺纹杆32、导向管 33、导向管限位螺套34,并装入车身螺栓。为保证副车架安装位置固定不变,每次只更换一个螺栓,依次完成车身安装点位31处的车身螺栓换装,完成副车架安装。
80.当需要进行换装副车架35时,先取出车身安装点位31处的车身螺栓,装入螺纹杆32、首次装副车架35时该点使用导向管33、导向管限位螺套34。依次换装车身安装点位31处的螺纹杆32、导向管33、导向管限位螺套34。取下副车架时,换上新副车架。再依据上一步方法,换装上车身螺栓。采用这种方法,能保证更换前后的副车架位置基本一致。
81.实施例二:
82.图6为本实用新型用于副车架定位及车身弹簧辅助压装的压装机构的实施例二中安装螺旋弹簧的结构示意图一。图7为本实用新型用于副车架定位及车身弹簧辅助压装的压装机构的实施例二中安装螺旋弹簧的结构示意图二。图8 为本实用新型用于副车架定位及车身弹簧辅助压装的压装机构的实施例二中安装螺旋弹簧的结构示意图三。图9为本实用新型用于副车架定位及车身弹簧辅助压装的压装机构的实施例二中安装螺旋弹簧的结构示意图四。
83.如图6至图9所示,本实用新型公开了一种用于副车架定位及车身弹簧辅助压装的压装机构30,压装机构包括多个第一车身安装点位36、多个螺纹杆32、多个导向管33、多个挡板37和多个调节螺母38,每一螺纹杆32安装至对应的第一车身安装点位36的底部,导向管套35设在对应螺纹杆32上。副车架35具有多个安装部351,每一安装部351开设有贯通的安装孔352,安装孔352的孔径与导向管33的外径相互匹配,使得副车架35的安装部351套设在对应导向管33外,挡板37和调节螺母38依次套设在对应螺纹杆32上,位于副车架35的安装部351的底端,用于紧固副车架35的安装部351。
84.例如,在定位好副车架35后,若需要进一步安装螺旋弹簧41,则将第一车身安装点位36处的导向管限位螺套34拆除,并分别装上挡板37与调节螺母38。
85.优选地,压装机构30还包括多个弹簧压装位39、第二车身安装点位40和多个螺旋弹簧41,每一螺旋弹簧41的一端与对应的弹簧压装位39的端面贴合,另一端与减震器42连接,且减震器42的安装点421与第二车身安装点位40 连接。通过设置减震器42,可以在进行换装螺旋弹簧41的时候减少震动。
86.如图7至图9所示,通过旋动第一车身安装点位36的调节螺母38,将副车架35向下调节,直到螺旋弹簧41可以自由放入,放入螺旋弹簧41后,弹簧压装位39的端面与螺旋弹簧41的端面自然贴合。将减震器42与第二车身安装点40连接。然后,拧紧四个第一车身安装点位36的调节螺母38,当副车架35到达装车位置时,螺旋弹簧41也完成了安装。最后使用副车架35的第一车身安装点位36的螺栓依次替换掉导向机构即可完成安装。
87.优选地,弹簧压装位39的端面设置为弹簧橡胶垫端面,通过将弹簧压装位39的端面设置为弹簧橡胶垫端面,使得弹簧压装位39的端面与螺旋弹簧41 的端面自然贴合。
88.进一步地,螺纹杆32与第一车身安装点位36的底部之间为螺纹连接。螺纹杆32的尾端优选为正六边形,通过将螺纹杆32尾端设置为正六边形,可以方便内六角套筒进行安装操作。
89.优选地,螺纹杆32与车身安装点位31的底部之间为螺纹连接。螺纹杆32 尾端优选为正六边形。通过将螺纹杆32尾端设置为正六边形,可以方便内六角套筒进行安装操作。
90.根据上述结构描述,本实用新型用于副车架定位及车身弹簧辅助压装的压装机构中,螺纹杆32的螺纹规格与副车架35的车身安装点螺栓规格相同。通过调研和统计各大主机厂车型的车身安装螺栓,基本为m16和m14,具体规格为:m16
×
1.5、m16
×
1、m14
×
1.5、m14
×
1。
91.为保证通用性,即满足不同车型需求,共设置四种规格的螺纹杆:m16
×ꢀ
1.5、m16
×
1、m14
×
1.5、m14
×
1,每种规格四件。螺纹杆尾端为正六边形,方便使用内六角套筒操作。
92.以下说明以m16螺纹杆为例,例如导向管33的内径为14mm-16mm,则导向管33的外径优选为20mm-25mm。例如,将导向管33的外径设置为25mm、 24mm、23mm、22mm、21mm、20mm,共6种规格,从而提高通用性,每种规格四个。导向管33的长度小于副车架35的车身安装点悬置厚度。
93.优选地,导向管定位螺套34的内螺纹与螺纹杆32的螺纹相同,且内螺纹和螺纹杆的螺纹长度为20mm-25mm。例如,螺旋杆32可以m16的螺纹,则导向管定位螺套34的外径可以采用19mm的外径。
94.本实施例中挡板37为圆形,且挡板37的上下端面均为平面。优选地,挡板37的外圆直径可以为90mm,挡板37的内圆直径和螺旋杆32的外径相同,使得挡板37和螺旋杆的外圆更加紧密配合。调节螺母38的外形为正六边形。进一步地,所述调节螺母38与螺纹杆32的螺纹相同。
95.所述用于副车架定位及车身弹簧辅助压装的压装机构的使用方法具体为:
96.当安装螺旋弹簧41时,在定位好副车架35后,若需要安装螺旋弹簧41,则将第一车身安装点36处的导向管限位螺套34解除并分别装上挡板37与调节螺母38。
97.如图6和图7所示,旋动四个第一车身安装点36的调节螺母38,将副车架35向下调节,直到螺旋弹簧41可以自由放入,放入螺旋弹簧41后,弹簧橡胶垫端面(弹簧压装位39)与螺旋弹簧41的端面自然贴合,将减震器42上安装点42与第二车身安装点位40连接。
98.如图8和图9所示,拧紧四个第一车身安装点36的调节螺母38,当副车架35到达装车位置时,螺旋弹簧41也完成了安装。最后使用副车架车身安装点螺栓依次替换掉导向机构即可。
99.综上所述,本实用新型用于副车架定位及车身弹簧辅助压装的压装机构,具有如下诸多优势:
100.一、采用本实用新型的方法,可以保证更换前后的副车架位置基本一致。
101.二、在定位好副车架以后,可以将副车架向下调节,直到弹簧可以自由放入,放入弹簧后,弹簧橡胶垫的端面与弹簧端面自然贴合,可以直接完成安装。
102.虽然以上描述了本实用新型的具体实施方式,但是本领域的技术人员应当理解,
这些仅是举例说明,本实用新型的保护范围是由所附权利要求书限定的。本领域的技术人员在不背离本实用新型的原理和实质的前提下,可以对这些实施方式作出多种变更或修改,但这些变更和修改均落入本实用新型的保护范围。