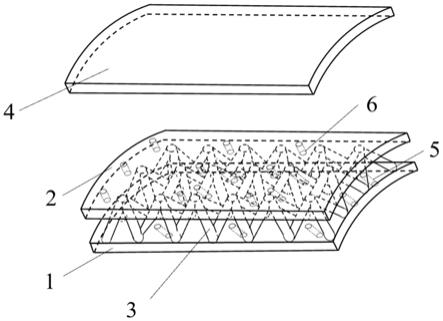
1.本发明属于燃气涡轮发动机领域,具体涉及一种带有用于航空发动机燃烧室的多面体桁架式结构隔热屏结构和成膜方法。
背景技术:2.航空发动机在加力状态下,流经燃烧室与尾喷管的燃气温度超过2000k,已远远超过可用高温材料的耐热极限,因此,必须对燃烧室与尾喷管的承力结构进行有效的热防护。
3.此前公开了几种燃烧室隔热屏,包括一种多孔波纹板燃烧室隔热屏(us005465572a),其波纹状结构的伸缩性可以有效防止振动核筒体热变形造成的影响,又通过波纹板上离散气膜孔的冷却射流对隔热屏的高温燃气侧进行气膜冷却。然而,正是由于波纹状结构,冷却气膜射流难以覆盖整个表面,使其局部壁温过高,无法形成有效的气膜覆盖和换热;另外一种为带扰流柱的发散冷却隔热屏结构(us 20140096527a1),通过发散的冷却形式在壁面形成气膜覆盖,阻隔高温燃气的直接接触,同时,隔热屏冷气侧壁面上的扰流柱结构可以对冷气进行扰动混合,强化对流换热,使冷气带走更多的热量而降低壁温。然而,单纯的发散冷却形式难以使扰流柱发挥更好的作用,冷却流动混合不够强烈,无法提升其冷却效率。
4.基于以上的经验,结合传统的气膜冷却、冲击冷却等方式,专利(cn103968418a)公开了一种用于加力燃烧室的双层壁隔热屏。此结构包括靠近燃气侧带有气膜孔的壁面、靠近冷气侧带有冲击孔的壁面以及气膜孔板和冲击孔板之间的梯形强化框,这样就形成了冷气侧冲击冷却、内部对流换热和燃气测气膜覆盖的复合冷却形式。此种结构可以通过对流换热带走传入的热量,提高冷气利用率,同时具有较好的力学性能,然而,此结构并未考虑梯形强化框在内部对流换热的过程中带来的流动阻力。
5.随着先进高性能燃气涡轮发动机的发展,流经燃烧室的燃气温度不断提高。另外,随着主流燃烧需要的空气流量的增大,导致用于冷却的空气流量减少,因此,必须应用具有高效冷却能力的隔热屏结构,即以尽可能少的冷气空气达到更好的冷气效果。
技术实现要素:6.本发明的目的在于避免现有技术的不足提供一种结构简单,使用方便的用于航空发动机燃烧室的多面体桁架式结构隔热屏。
7.为实现上述目的,本发明采取的技术方案为:一种用于航空发动机燃烧室的多面体桁架式结构隔热屏,包括用于构成燃烧室筒体内壁的气膜孔板和在所述气膜孔板外侧的冲击孔板,在所述的气膜孔板上设有气膜孔;在所述冲击孔板上设有冲击孔;所述气膜孔板内侧为燃烧室主燃气涵道,所述冲击孔板与燃烧室的外壁面共同构成冷气外涵道;在所述气膜孔板与冲击孔板之间矩阵排列有多个多面体桁架,多面体桁架是由至少三根桁架杆组成,至少三根桁架杆一端的交叉顶点固连在冲击孔板上,在冲击孔板上形成连接点,所述连
接点以点阵形式固连在冲击孔板上;所述至少三根桁架杆的另一端也以点阵形式固连在气膜孔板上;所述的气膜孔板、冲击孔板和多面体桁架共同构成所述的隔热屏;
8.所述的多个多面体桁架的矩阵排列具体为:以s
x
为多面体桁架轴向排布间距,s
z
为多面体桁架周向排布间距,h为气膜孔板与冲击孔板之间的距离,d为多面体桁架的桁架杆直径,则所述s
x
和s
z
形成的矩阵单元大小为:
9.h≥s
x
≥2d、h≥s
z
≥2d;
10.多个多面体桁架以所述s
x
和s
z
形成的矩阵单元在所述气膜孔板与冲击孔板之间周向和轴向延展排布,且在所述s
x
和s
z
形成的矩阵单元内对应设有一个多面体桁架。
11.进一步的,所述的冲击孔为沿冲击孔板的法向方向设置的多排通孔,冲击孔位于多面体桁架与冲击孔板连接点沿气流方向的前方,所述的冲击孔的直径为1~2mm;所述的气膜孔为与气膜孔板法向呈20~60度设置的通孔,气膜孔位于多面体桁架与气膜孔板的连接点沿气流方向的后方;所述气膜孔直径为0.3~10mm。
12.进一步的,所述的多面体桁架是由三根桁架杆组成,三根桁架杆的一端相交与一点,即为交叉顶点,形成四面体桁架,所述的三根桁架杆分别为第一桁架杆、第二桁架杆和第三桁架杆,其中第一桁架杆和第二桁架杆与气膜孔板的连接点设置在所述矩阵单元的两个角点上,第三桁架杆与气膜孔板的连接点设置在所述矩阵单元另外两个角点的连线中点上。
13.进一步的,所述的四面体桁架在气膜孔板与冲击孔板之间周向上,按照所述的矩阵单元依次排列,且每个交叉顶点均伸出三个桁架杆,左、右相邻两个四面体桁架之间的第一桁架杆和第二桁架杆与气膜孔板的连接点交接重合在所述矩阵单元的角点上;在所述气膜孔板与冲击孔板之间轴向上,前排四面体桁架的第三桁架杆与气膜孔板的连接点又交接重合在后排左、右相邻两个四面体桁架之间的第一桁架杆和第二桁架杆与气膜孔板的连接点的交接重合点上,并依此延展设置。
14.进一步的,所述的多面体桁架是由四根桁架杆组成,四根桁架杆的一端相交与一点,形成五面体桁架,所述的四根桁架杆与气膜孔板连接的连接点设置在所述矩阵单元的四个角点上。
15.进一步的,所述多面体桁架的直径d与冲击孔板和气膜孔板间距h的比值变化范围为:0.05~0.25。
16.进一步的,所述的多面体桁架与所述的气膜孔板的壁面法向角度为θ,θ为30
‑
60
°
;所述组成多面体桁架的桁架杆长度为l,h为气膜孔板与冲击孔板之间的距离,则l=h/cosθ。
17.本发明还提供一种所述的用于航空发动机燃烧室的多面体桁架式结构隔热屏在气膜孔板上形成气膜的方法,
18.在所述冷气外涵道中的冷却气流的部分垂直与冲击孔板的冲击射流,经所述冲击孔板上的冲击孔进入气膜孔板和冲击孔板之间的空腔;
19.进入气膜孔板和冲击孔板之间空腔的冲击射流,一部分为直接对所述的气膜孔板内壁面进行冲击冷却的冲击射流,形成冲击冷却气流,另一部分冲击所述的多面体桁架,并与多面体桁架表面碰撞形成环绕多面体桁架的绕流,
20.由所述多面体桁架环绕下降的绕流对气膜孔板的内壁面进行扫掠和斜冲击,并与
所述冲击冷却气流混合后,在所述的多面体桁架的各个桁架杆之间形成混合气流;
21.所述的混合气流进入气膜孔板的气膜孔中形成气流射流,由气膜孔板的外壁面流出的气流射流形成气膜冷气隔热层,降低燃烧室主燃气涵道内主流高温燃气a对燃烧室壁面的热负荷。
22.本发明的有益效果是:一种带有用于航空发动机燃烧室的多面体桁架式结构隔热屏,即在冲击孔板和气膜孔板之间布置多面体桁架结构,一方面,可以通过冲击
‑
气膜的复合冷却方式在隔热屏的燃气侧形成气膜覆盖,阻隔燃气与发动机承力结构的直接接触;另一方面,可以通过多面体桁架结构对冲击射流进行扰动混合,强化内部的对流换热,从而降低冷气利用量。同时,多面体桁架结构可以将冲击孔板和气膜孔板有效固定,有较好的力学性能,增强其结构性能,提高燃烧室的寿命和可靠性。
附图说明
23.图1为本发明带有四面多面体桁架的双层壁隔热屏结构示意图;
24.图2为本发明带有四面体桁架单元及其阵列结构图;
25.图3为本发明带有四面体桁架的双层壁隔热屏剖面示意图;
26.图4为本发明带有四面体桁架的双层壁隔热屏结构局部耦合作用示意图;
27.图5为本发明带有五面体桁架的双层壁隔热屏结构示意图;
28.图6为本发明带有五面体桁架单元及其阵列结构图;
29.图7为本发明带有五面体桁架的双层壁隔热屏剖面示意图;
30.图8为本发明带有五面体桁架的双层壁隔热屏结构局部耦合作用示意图。
31.图中:
32.1气膜孔板、2冲击孔板、3多面体桁架、4燃烧室的外壁面、5气膜孔、6冲击孔、7冷气外涵道、8主流燃气涵道。
具体实施方式
33.以下结合附图对本发明的原理和特征进行描述,所举实例只用于解释本发明,并非用于限定本发明的范围。
34.实施例1:如图1、图2、图3所示,一种用于航空发动机燃烧室的多面体桁架式结构隔热屏,包括用于构成燃烧室筒体内壁的气膜孔板1和在所述气膜孔板1外侧的冲击孔板2,在所述的气膜孔板1上设有气膜孔5;在所述冲击孔板2上设有冲击孔6;所述气膜孔板1内侧为燃烧室主燃气涵道8,所述冲击孔板2与燃烧室的外壁面4共同构成冷气外涵道7;在所述气膜孔板1与冲击孔板2之间矩阵排列有多个多面体桁架3,多面体桁架3是由至少三根桁架杆组成,至少三根桁架杆一端的交叉顶点固连在冲击孔板2上,在冲击孔板2上形成连接点,所述连接点以点阵形式固连在冲击孔板2上;所述至少三根桁架杆的另一端也以点阵形式固连在气膜孔板1上;所述的气膜孔板1、冲击孔板2和多面体桁架3共同构成所述的隔热屏。
35.所述的多个多面体桁架3的矩阵排列具体为:以s
x
为多面体桁架轴向排布间距,s
z
为多面体桁架周向排布间距,h为气膜孔板1与冲击孔板2之间的距离,d为多面体桁架的桁架杆直径,则所述s
x
和s
z
形成的矩阵单元大小为:
36.h≥s
x
≥2d、h≥s
z
≥2d。
37.多个多面体桁架3以所述s
x
和s
z
形成的矩阵单元在所述气膜孔板1与冲击孔板2之间周向和轴向延展排布,且在所述s
x
和s
z
形成的矩阵单元内对应设有一个多面体桁架3。
38.多面体桁架3是由三根桁架杆组成,三根桁架杆的一端相交与一点,即为交叉顶点,形成四面体桁架,所述的三根桁架杆分别为第一桁架杆31、第二桁架杆32和第三桁架杆33,其中第一桁架杆31和第二桁架杆32与气膜孔板1的连接点设置在所述矩阵单元的两个角点上,第三桁架杆33与气膜孔板1的连接点设置在所述矩阵单元另外两个角点的连线中点上。
39.四面体桁架在气膜孔板1与冲击孔板2之间周向上,按照所述的矩阵单元依次排列,且每个交叉顶点均伸出三个桁架杆,左、右相邻两个四面体桁架之间的第一桁架杆31和第二桁架杆32与气膜孔板1的连接点交接重合在所述矩阵单元的角点上;在所述气膜孔板1与冲击孔板2之间轴向上,前排四面体桁架的第三桁架杆33与气膜孔板1的连接点又交接重合在后排左、右相邻两个四面体桁架之间的第一桁架杆31和第二桁架杆32与气膜孔板1的连接点的交接重合点上,并依此延展设置。
40.冲击孔6为沿冲击孔板2的法向方向设置的多排通孔,冲击孔6位于多面体桁架3与冲击孔板2连接点沿气流方向的前方,所述的冲击孔6的直径为1~2mm;所述的气膜孔5为与气膜孔板1法向呈20~60度设置的通孔,气膜孔5位于多面体桁架3与气膜孔板1的连接点沿气流方向的后方;所述气膜孔5直径为0.3~10mm。
41.多面体桁架的直径d与冲击孔板2和气膜孔板1间距h的比值变化范围为:0.05~0.25。所述的多面体桁架与所述的气膜孔板1的壁面法向角度为θ,θ为30
‑
60
°
;所述组成多面体桁架3的桁架杆长度为l,h为气膜孔板1与冲击孔板2之间的距离,则l=h/cosθ。
42.参阅图1、图3,本实施例为用于燃烧室的双层壁隔热屏,包括气膜孔板1、冲击孔板2、多面体桁架夹芯结构3。燃气侧气膜孔板1为构成燃烧室筒体内壁,内侧为燃烧室主燃气涵道8,即燃烧室主流高温燃气a的流动通道;冷气侧冲击孔板2与外壁面4共同构成冷气涵道7;冲击孔板2与气膜孔板1之间设置有多面体桁架夹芯结构3,共同形成双层壁隔热屏;冲击孔板2、气膜孔板1和多面体桁架结构3在轴向为多个单元周期结构,每个单元的冲击孔板2壁面环向均布有冲击孔6,气膜孔板1壁面环向均布有气膜孔5。由于多面体桁架结构3为典型的点阵结构,其与气膜孔板1和冲击孔板2采用点接触的焊接形式固定,构成结构性完整的一体化结构。气膜孔5为与主燃气涵道的斜孔,气膜孔5与主流高温燃气a之间具有一定的倾斜角度以提高气膜冷气效果。气膜孔5直径为0.3
‑
10mm。
43.图2中展示了多面体桁架单元和阵列结构的排列方式。阴影下为多面体桁架结构单元,由三根桁架杆交于一点。一般情况下,三根桁架杆具有相同的倾斜角度、长度和直径,构成正多面体桁架结构。此多面体桁架单元的顶点与冲击孔板相连,而三根桁架杆的底点在气膜孔板上又分别与其他单元的桁架杆底点相交,从而构成了多面体桁架阵列结构,相邻桁架杆在z方向的间距s
z
以及相邻两列单体在x方向的列间距s
x
可以为非恒定值。
44.随着其角度的变化,桁架杆长度变化,导热能力变化,对流体的流动阻力也发生变化;直径的增加或减小影响了固体率以及与流体接触面积的变化,直径影响了流动阻力和换热性能的变化。阵列结构的疏密程度可以由单体的间距s
x
和s
z
来控制,当其间距为恒定值时,多面体桁架阵列即为规则的结构,而当阵列结构的形式发生变化时,其对冲击射流的扰动混合也发生变化,导致内冷结构冷却效率的变化和冷气用量的变化。
45.本发明提供的弯折桁架夹芯结构的双层壁隔热屏,在实施时,一般用于航空发动机的燃烧室,用于替换燃烧室腔体隔热内壁,尤其是本技术方案更适合燃烧器的高温段,因为其采用了多面体桁架结构及多排孔配合,可以通过冲击
‑
气膜的复合冷却方式在隔热屏的燃气侧形成气膜覆盖,阻隔燃气与发动机承力结构的直接接触,强化内部的对流换热,提高了冷却气流在隔热层内的冷却效率;同时,该结构增强了冷却气流在隔热屏的气膜孔板1、冲击孔板2之间的混合效果;气膜孔板1上的气膜孔5的结构更有利于隔热屏内气流通过气膜孔5对气膜孔板1的气膜出流的贴壁效果,有效保护了燃烧室的腔体内、外壁。
46.实施例2:如图5、图6、图7所示,与实施例1相同,不同的是所述的多面体桁架是由四根桁架杆组成,四根桁架杆的一端相交与一点,形成五面体桁架,所述的四根桁架杆与气膜孔板1连接的连接点设置在所述矩阵单元的四个角点上;如图中所示,每个交叉顶点均伸出四个桁架杆,使得所述设置相邻矩阵单元角点上的连接点也是相邻桁架杆的交叉顶点。
47.实施例3:本发明还提供一种所述的用于航空发动机燃烧室的多面体桁架式结构隔热屏在气膜孔板上形成气膜的方法,
48.在所述冷气外涵道7中的冷却气流b的部分垂直与冲击孔板2的冲击射流c1,经所述冲击孔板2上的冲击孔6进入气膜孔板1和冲击孔板2之间的空腔;
49.进入气膜孔板1和冲击孔板2之间空腔的冲击射流c1,一部分为直接对所述的气膜孔板1内壁面进行冲击冷却的冲击射流,形成冲击冷却气流c3,另一部分冲击所述的多面体桁架,并与多面体桁架表面碰撞形成环绕多面体桁架的绕流c2,
50.由所述多面体桁架环绕下降的绕流c2对气膜孔板1的内壁面进行扫掠和斜冲击,并与所述冲击冷却气流c3混合后,在所述的多面体桁架的各个桁架杆之间形成混合气流c4;
51.所述的混合气流c4进入气膜孔板的气膜孔5中形成气流射流c5,由气膜孔板1的外壁面流出的气流射流c5形成气膜冷气隔热层,降低燃烧室主燃气涵道8内主流高温燃气a对燃烧室壁面的热负荷。
52.图4中展示了多面体桁架是由三根桁架杆组成,三根桁架杆的一端相交与一点,形成四面体桁架,所述的三根桁架杆分别为第一桁架杆31、第二桁架杆32和第三桁架杆33,其中第一桁架杆31和第二桁架杆32与气膜孔板1的连接点设置在所述矩阵单元的两个角点上,第三桁架杆33与气膜孔板1的连接点设置在所述矩阵单元另外两个角点的连线中点上,此时,双层壁结构与通道内的四面体桁架结构的耦合作用,即冷却气流c1经冲击孔6进入双层壁结构,一部分气流对其正对面的气膜孔板内壁面形成冲击冷却,另一部分气流c2直接冲击桁架单体表面形成扰流结构,以不同的角度对气膜孔内壁面进行扫掠或斜冲击,或与直接冲击壁面的部分冲击射流混合作用,形成气流c3;气流c3与桁架阵列间的扰流c2混合,形成气流c4;桁架单体表面扰流c2、混合气流c3、c4进入到与气膜孔板5具有一定角度的气膜孔中,流出后形成气膜射流c5,对气膜孔板1外壁面进行有效的气膜覆盖,形成冷气隔热层,降低主流高温燃气a对燃烧室壁面的热负荷。
53.图8中展示了多面体桁架是由四根桁架杆组成,四根桁架杆的一端相交与一点,形成五面体桁架,所述的四根桁架杆与气膜孔板1连接的连接点设置在所述矩阵单元的四个角点上,此时,双层壁结构与通道内的五面多面体桁架结构的耦合作用,即冷却气流c1经冲击孔6进入双层壁结构,一部分气流对其正对面的气膜孔板内壁面形成冲击冷却,另一部分
气流c2直接冲击桁架单体表面形成扰流结构,以不同的角度对气膜孔内壁面进行扫掠或斜冲击,或与直接冲击壁面的部分冲击射流混合作用,形成气流c3;气流c3与桁架阵列间的扰流c2混合,形成气流c4;桁架单体表面扰流c2、混合气流c3、c4进入到与气膜孔板5具有一定角度的气膜孔中,流出后形成气膜射流c5,对气膜孔板1外壁面进行有效的气膜覆盖,形成冷气隔热层,降低主流高温燃气a对燃烧室壁面的热负荷。
54.以上所述仅为本发明的较佳实施例,并不用以限制本发明,凡在本发明的精神和原则之内,所作的任何修改、等同替换、改进等,均应包含在本发明的保护范围之内。