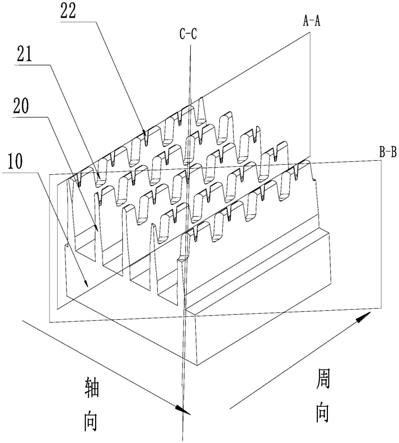
[0001]
本实用新型涉及空调技术领域,具体而言,涉及一种换热管及空调器。
背景技术:[0002]
蒸汽在水平管外冷凝是一种重要的传热方式,在制冷空调、化工、食品加工、发电厂等工业领域中有着广泛的应用:其传热过程中管内流通低温流体,通过管壁带走管外蒸汽热量促使管外蒸汽冷凝。多年来伴随着传热设备的发展,学术界和工业应用中都重点研发更高效的冷凝传热表面。冷凝的两种方式中,珠状冷凝的换热效率远高于膜状冷凝,但由于加工成本和性能稳定的可维持性阻碍了其在工业中的普及应用;而膜状冷凝由于可采用强化传热表面,如外加翅片,在工业中得到了广泛的应用,并成为了工业应用中的主要的冷凝传热方式。
[0003]
如图1所示,在二十世纪三十年代开发出的在管外简单的挤压成型的梯形外翅片,通常称为2d翅片1,在传热领域得到广泛的应用,它可以增加传热面积从而可提高传热效率。
[0004]
但是膜状冷凝主要传热热阻在于冷凝液膜对蒸汽和管壁接触的阻碍,因此为进一步提高冷凝传热系数,需要进一步加强减薄冷凝液膜并促进冷凝液迅速排走。经过几十年的发展,如图2所示,复杂的冷凝表面也已开发出来并得到了广泛应用,通常称为3d翅片2。3d翅片2不仅可增加传热面积,而且利用液态制冷剂表面张力的作用减薄液膜促进冷凝液流动。
[0005]
但是不管是2d翅片1还是3d翅片2,在管体下半部,由于液膜表面张力的方向和液膜重力方向相反,会使管下半部形成冷凝液的滞留区,该区域内会充满冷凝液,如图1和图2所示的φ区域,该区域被称为滞留区,滞留区的存在会减少蒸汽和管外壁的接触面积,从而使冷凝传热效率不能得到进一步的提升。
技术实现要素:[0006]
本实用新型实施例提供了一种换热管及空调器,以解决现有技术中换热管存在的滞留区导致的冷凝传热效率受限的技术问题。
[0007]
本申请实施方式提供了一种换热管,包括管体和设置在管体上的翅片,翅片的顶部形成有第一切口和第二切口,第一切口的深度大于第二切口的深度,第一切口的延伸方向相对于翅片的周向方向呈正角度设置,第二切口的延伸方向相对于翅片的周向方向呈负角度设置。
[0008]
在一个实施方式中,第一切口的深度为h1,0.1mm≤h1≤0.95mm。
[0009]
在一个实施方式中,第二切口的深度为h2,0.005mm≤h2≤0.65mm。
[0010]
在一个实施方式中,第一切口的延伸方向相对于翅片的周向方向α1,5
°
≤α1≤90
°
。
[0011]
在一个实施方式中,第二切口的延伸方向相对于翅片的周向方向α2,-85
°
≤α2<0
°
。
[0012]
在一个实施方式中,第一切口和第二切口在翅片上依次交替排布设置。
[0013]
在一个实施方式中,翅片为多个,多个翅片螺旋分布在管体上。
[0014]
在一个实施方式中,每个翅片上分布有10~120个第一切口以及10~120个第二切口。
[0015]
在一个实施方式中,第一切口的宽度为l1,第二切口的宽度为l2,0.05mm≤l1≤1mm,0.005mm≤l2≤0.5mm。
[0016]
在一个实施方式中,第一切口的开口角度为θ1,第二切口的开口角度为θ2,10
°
≤θ1≤120
°
,0
°
<θ2≤90
°
。
[0017]
在一个实施方式中,翅片的根部与管体表面垂直。
[0018]
本申请还提供了一种空调器,包括换热管,换热管为上述的换热管。
[0019]
在上述实施例中,第一切口和第二切口的作用可使翅片的顶部尖锐,从而能刺穿冷凝液膜,并使顶部液相压力达到最大值,能增大冷凝液翅片顶部和根部间的压差,从而可促使冷凝液快速拉向翅片根部。另外深度不一的第一切口和第二切口,能使液膜经切口底部转折,使液膜厚度高低不一,从而增强“gregorig”效应,即冷凝液膜不均匀分布可减小平均热阻。再则,第一切口的延伸方向相对于翅片的周向方向呈正角度设置,第二切口的延伸方向相对于翅片的周向方向呈负角度设置,还可以充分利用表面张力作用,使相邻翅片间冷凝液的流动进一步加强,可以减弱翅片间液体“搭桥”现象,使更多的液体能够随着相邻翅片间的下滴冷凝液流动,从而进一步减小冷凝液滞留区,进一步减小滞留角,增加蒸汽与管体的传热面积,从而增强冷凝传热效率。
附图说明
[0020]
构成本申请的一部分的附图用来提供对本实用新型的进一步理解,本实用新型的示意性实施例及其说明用于解释本实用新型,并不构成对本实用新型的不当限定。在附图中:
[0021]
图1是根据现有技术中的2d翅片式换热管的主视图及剖面图;
[0022]
图2是根据现有技术中的3d翅片式换热管的主视图及剖面图;
[0023]
图3是根据本实用新型的换热管的实施例的局部结构示意图;
[0024]
图4是图3的换热管的左视结构示意图;
[0025]
图5是图3的换热管的a-a剖面的结构示意图;
[0026]
图6是图3的换热管的b-b剖面的结构示意图;
[0027]
图7是图3的换热管的c-c剖面的结构示意图;
[0028]
图8是图3的换热管的俯视结构示意图。
具体实施方式
[0029]
为使本实用新型的目的、技术方案和优点更加清楚明白,下面结合实施方式和附图,对本实用新型做进一步详细说明。在此,本实用新型的示意性实施方式及其说明用于解释本实用新型,但并不作为对本实用新型的限定。
[0030]
现有冷凝传热方式主要以膜状凝结为主,蒸汽冷凝后形成的液膜覆盖在传热管外表面,成为了阻碍传热的主要热阻。所以为提高冷凝传热效率,不仅要增加传热面积,而且
要促进冷凝液膜迅速排走,同时要防止翅片间冷凝液搭桥,在管下部形成滞留区,即存在较大滞留角,阻碍蒸汽和管壁接触,使冷凝传热系数不能进一步提高。随着国家“节能减排”及“绿色建筑”等政策的要求下,提高空调机组的能效也成为行业必须面对的课题,而换热管的换热能力强弱直接决定了换热管及整个空调机组能效的高低。为此,在本实用新型的技术方案,对翅片的结构进行了改进,以进一步提高冷凝传热效率。
[0031]
如图3、图4和图5所示,在本实用新型的技术方案中,换热管包括管体10和设置在管体10上的翅片20。在翅片20的顶部形成有第一切口21和第二切口22,第一切口21的深度大于第二切口22的深度,第一切口21的延伸方向相对于翅片20的周向方向呈正角度设置,第二切口22的延伸方向相对于翅片20的周向方向呈负角度设置。
[0032]
应用本实用新型的技术方案,第一切口21和第二切口22的作用可使翅片20的顶部尖锐,从而能刺穿冷凝液膜,并使顶部液相压力达到最大值,能增大冷凝液翅片20顶部和根部间的压差,从而可促使冷凝液快速拉向翅片20根部。另外深度不一的第一切口21和第二切口22,能使液膜经切口底部转折,使液膜厚度高低不一,从而增强“gregorig”效应,即冷凝液膜不均匀分布可减小平均热阻。再则,第一切口21的延伸方向相对于翅片20的周向方向呈正角度设置,第二切口22的延伸方向相对于翅片20的周向方向呈负角度设置,还可以充分利用表面张力作用,使相邻翅片20间冷凝液的流动进一步加强,可以减弱翅片20间液体“搭桥”现象,使更多的液体能够随着相邻翅片20间的下滴冷凝液流动,从而进一步减小冷凝液滞留区,进一步减小滞留角,增加蒸汽与管体10的传热面积,从而增强冷凝传热效率。
[0033]
如图4所示,在本实施例的技术方案中,翅片20的根部与管体10表面垂直。由公式
[0034]
p
l
=p
v
+2σ/r
c
[0035]
可知,沿翅片高度液相的压力p
l
与蒸汽相的压力p
v
及表面张力σ与翅片局部的曲率半径r
c
有关。本实用新型中翅片根部加工成直角,此时根部曲率半径最小,使翅根部液相压力达到最大值,能减少冷凝液翅片顶部和根部间的压差,从而可减弱冷凝液拉向翅片根部的力,使管下部冷凝液向下排走的能力增强,从而减小滞留角,使冷凝持续不断地进行,增强冷凝换热效率。同时,翅根为直角,可最大限度增大翅根部翅片间距,使冷凝液流动更顺畅,从而加快冷凝液下滴,提高冷凝换热效率。
[0036]
如图5所示,在本实施例的技术方案中,在本实施例的技术方案,第一切口21和第二切口22在翅片20上依次交替排布设置,这样可以更加均衡的起到增强冷凝传热效率的效果。
[0037]
在本实施例的技术方案,如图4所示,翅片20为多个,多个翅片20螺旋分布在管体10上。翅片20沿轴向每英寸设有5~60个,螺旋角为0.2~2.5
°
。优选的,在本实施例的技术方案中,每个翅片20上分布有10~120个第一切口21以及10~120个第二切口22。
[0038]
如图6和图7所示,可选的,在本实施例的技术方案,第一切口21的深度为h1,0.1mm≤h1≤0.95mm。可选的,第二切口22的深度为h2,0.005mm≤h2≤0.65mm。
[0039]
可选的,在本实施例的技术方案,第一切口21的延伸方向相对于翅片20的周向方向α1,5
°
≤α1≤90
°
;第二切口22的延伸方向相对于翅片20的周向方向α2,-85
°
≤α2<0
°
。
[0040]
如图6和图7所示,可选的,在本实施例的技术方案,第一切口21的宽度为l1,第二切口22的宽度为l2,0.05mm≤l1≤1mm,0.005mm≤l2≤0.5mm。经过试验,确定第一切口21的
开口角度为θ1,第二切口22的开口角度为θ2,10
°
≤θ1≤120
°
,0
°
<θ2≤90
°
。
[0041]
更为优选的,在本实施例的技术方案中,管体10的内腔表面还设有螺纹状的内齿,增大传热管的传热面积,并且能够增强传热管内流体紊流,使管内换热效率增加。可选的,管体10的内齿为螺纹状,该螺纹状的内齿截面为类三角形,内齿的齿顶角范围为10~120
°
。优选的,螺纹内齿与管体的轴线夹角范围为0~75
°
,内齿条数为6~90个,内齿高度为0.1~0.6mm。
[0042]
在一具体实施例中,管体10名义外径19.05mm,翅片20每英寸设有44个,翅片20高度为0.95mm,翅片20根部为直角;第一切口21周向个数为60个,第一切口21的延伸方向相对于翅片20的周向方向的夹角为45
°
,深度h1为0.35mm;第二切口22周向个数为60个,第二切口22的延伸方向相对于翅片20的周向方向的夹角为-35
°
,方向与第一切口21相反,深度h2为0.2mm;管内内齿高度为0.4mm,内齿条数为45个,内齿螺旋角为45
°
。经测试,流动冷媒时该管型比同参数的普通“3d”型翅片管外侧换热性能提高约18%。
[0043]
上述的尺寸限定,对于不同的制冷剂,可根据不同使用工况,适当调整翅片间距及切口密度、深度等尺寸,以满足换热效率的要求。
[0044]
本实用新型的传热管采用专用机床进行加工,并且管内管外翅型一体化成型,管外具体加工过程为:先在管体10上加工出翅片20,接着利用翅根刀具将翅片20的根部压制成直角,进而使用滚花刀将翅片20切割出第一切口21,形成多个独立翅片20,随后用另一专用切刀对翅片20进行第二切口22形成第二切口22。采用滚压和旋压技术加工不增加传热管的制造材料,既节约了生产成本,又能增加传热管的强度和传热面积。
[0045]
本实用新型还提供了一种空调器,包括上述的换热管,采用上述的换热管可以提高空调器的工作效率。
[0046]
以上所述仅为本实用新型的优选实施例而已,并不用于限制本实用新型,对于本领域的技术人员来说,本实用新型实施例可以有各种更改和变化。凡在本实用新型的精神和原则之内,所作的任何修改、等同替换、改进等,均应包含在本实用新型的保护范围之内。