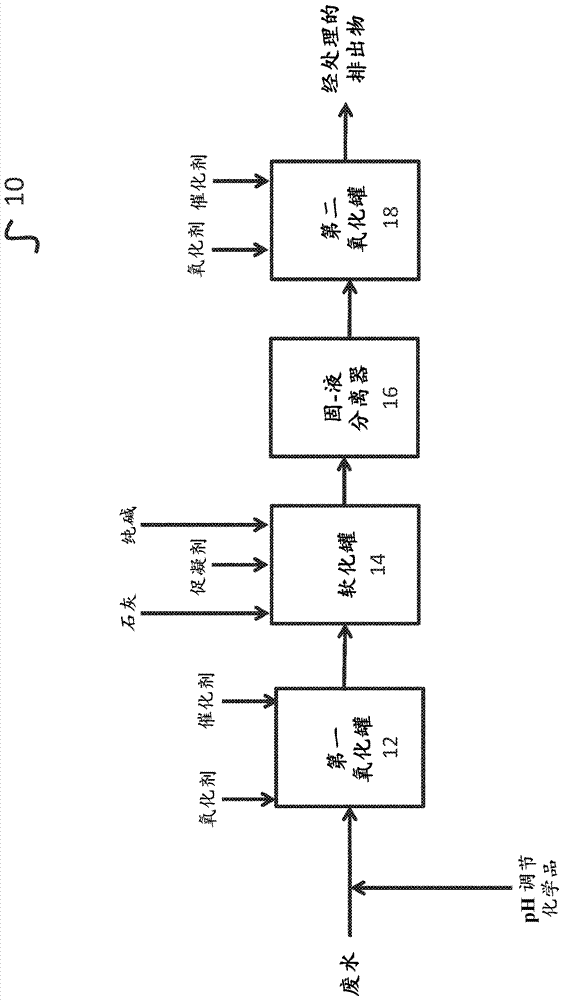
本申请根据35U.S.C.§119(e)要求以下美国临时申请的优先权:2016年2月15日提交的申请序列号62/295182。本申请在此通过引用以其整体结合。
技术领域:
本申请涉及水和废水的处理。
背景技术:
:自然和工业过程在环境中产生硫化物。自然界中存在的硫化物主要由厌氧条件下的生物过程产生,并在低于7.0的pH作为游离的硫化氢(H2S)存在。在碱性条件下,其作为二硫化物(HS-)/硫化物(S2-)离子存在。源于生物的H2S可见于地下水、沼泽和湿地、污水、天然气矿藏等。来自工业的废水中的硫化物源包括煤炭处理、油气精炼以及金属和采矿操作。从审美、健康、生态和工业观点来看,含硫化物的水必须在排放之前谨慎处理。此外,随着对水再利用越来越关注,膜(NF/RO)过程越来越普遍。从硫化物产生的元素硫对于膜堵塞是潜在的威胁。为了保护膜,硫化物必须在膜过程之前被减少至极低水平(优选地检测不到)。数种硫化物处理备选方案是可用的,包括:洗提,用氯、过氧化氢、臭氧、高锰酸盐氧化;化学沉淀、吸附,和生物过程。各过程具有由水质、流量、过程目标和适用性支配的小生境。由于合宜性、过程可靠性和灵活性,利用过氧化氢的化学氧化越来越普遍。然而,为了将硫化物彻底氧化成硫酸盐,需要高剂量的过氧化氢,这常常使得该过程在经济上不利。因此,需要一种改进的成本效益高的将硫化物氧化为硫酸盐而不产生任何元素硫的方法。概述本申请涉及用于从废水流除去硫化物的方法。在一个实施方案中,废水流的pH被调节为7.0-8.0。将第一氧化剂与废水流混合,氧化所述硫化物为元素硫。废水流然后通过将石灰与废水流混合而软化。添加石灰还升高废水流的pH至10.0或更高,并将元素硫转变成可溶性硫化物(S2-)和/或硫代硫酸盐。碳酸钙被沉淀,而硫化物(S2-)和/或硫代硫酸盐被吸附于其上。此后,废水流被导向固-液分离过程,后者从废水流分离碳酸钙和吸附的硫化物(S2-)和/或硫代硫酸盐。固-液分离器产生包含残留元素硫的排出物(通常在碱性条件下表现为S2-)。然后将排出物与第二氧化剂混合,后者将残留元素硫氧化为硫酸盐,产生经处理的排出物。在另一个实施方案中,提供一种用于从废水流除去硫化物的两步氧化方法。在第一步骤中,将氧化剂与废水流混合。至少一些硫化物被氧化为元素硫。此后,添加软化剂至废水流。软化剂增加废水流的pH。该pH的增加将元素硫转变成可溶性硫化物(S2-)和/或硫代硫酸盐,并引起硬度化合物沉淀。可溶性硫化物和/或硫代硫酸盐此后吸附到硬度化合物上。在第一步骤之后,废水流被导向固-液分离器。固-液分离器除去其上吸附有硫化物和/或硫代硫酸盐的硬度化合物,并产生包含残留元素硫的排出物。在第二步骤中,将氧化剂与来自固-液分离器的排出物混合,引起残留元素硫被转变成硫酸盐。在第二步骤之后,废水流可被进一步处理或排放。附图简述图1描述本文所述方法的一个实施方案。图2描述本文所述方案的第二实施方案。图3描述本文所述方法的另一个实施方案。详述本发明的目的是开发成本效益高的硫化物处理技术。基本的理念包括一种将硫化物氧化为硫酸盐的两步氧化方法:通过石灰-苏打软化来除去钙和镁;通过吸附到软化期间产生的碳酸钙淤泥上来除去第1步骤氧化过程中产生的元素硫;在第2步骤氧化过程中将残留硫化物彻底氧化为硫酸盐;后中和;淤泥处理和处置。本发明的一个新特征是以成本效益高的方式彻底地从水除去硫化物。另一个新特征是通过氧化以及通过共沉淀和吸附过程(吸附到软化过程中形成的CaCO3淤泥上)彻底除去硫/硫化物来保护RO/NF膜免于该污染物堵塞。转向附图,图1描述本文公开的方法的一个实施方案10。提供含有硫化物的废水。如果废水的pH在7.0-8.0的范围之外,那么将其调节为7.0-8.0。废水被导向第一氧化罐12。在一个优选实施方案中,第一氧化罐12是具有用于废气的通风口连接的密闭的顶部罐(toptank)。在第一氧化罐12中,废水与过氧化氢混合。在一个优选实施方案中,过氧化物和硫化物之间的重量比是0.8:1。此外,可在第一氧化罐12中添加铁催化剂。在一些实施方案中,铁催化剂是氯化铁或硫酸铁。废水中的硫化物在铁催化剂的存在下被过氧化氢氧化为元素硫。也可能产生一些硫酸盐。添加铁作为催化剂的目的是增强氧化反应动力学。因此,在pH7.0-8.0下的第1阶段氧化过程中的化学反应为:H2S+H2O2→S0+2H20来自第一氧化罐12的排出物被导向软化罐14。将石灰添加到软化罐14中以调节pH高于10,优选地为10.0-10.5。在一些实施方案中,也可添加纯碱。添加石灰到软化罐14中还引起碳酸钙(CaCO3)沉淀。在一些实施方案中,氢氧化镁(Mg(OH)2)沉淀或与碳酸钙共沉淀。在一些实施方案中,废水还可包含镁,其可通过调节软化罐14中的pH至10.8-11.2而经沉淀除去。在碱性条件下,第一氧化罐12中产生的不溶性元素硫在软化罐14中被转变成可溶性硫化物(S2-)和硫代硫酸盐。可溶性硫化物和硫代硫酸盐被吸附到CaCO3或Mg(OH)2淤泥上。硫化物和硫代硫酸盐的浓度取决于未净化水质和过氧化氢剂量。软化罐14的内容物被导向分离器16。在一个优选实施方案中,分离器16是澄清器。在一些实施方案中,软化罐14和分离器16可组合在单个软化澄清器单元中。分离器16分离沉淀的淤泥,并产生排出物。来自分离器16的排出物被导向第二氧化罐18。将过氧化氢添加到第二氧化罐18中。在一些实施方案中,也可添加铁催化剂到第二氧化罐18中。应当注意,对于pH高于10.5的废水,没有观察到添加铁催化剂的额外益处。在第二氧化罐18中,将残留元素硫(在碱性条件下表现为硫化物离子)氧化为硫酸盐通过遵从下述反应发生:S2-+4H2O2→SO42-+4H2O在一些实施方案中,推荐的H2O2与硫化物的重量比是5:1到6.1。然而,该比值取决于水质。图2描述本文所述方法的另一个实施方案20。含有硫化物的废水被导向第一反应器22。将氧化剂与废水流混合。废水流中的至少一些硫化物被氧化。在一个优选实施方案中,氧化剂是过氧化氢。也可在第一反应器22中添加铁催化剂。在硫化物被氧化之后,将软化剂添加到废水中。在一些实施方案中,软化剂是石灰。软化剂增加废水的pH。因此,硬度化合物从废水沉淀,而元素硫被转变成硫化物和/或硫代硫酸盐。硫化物和/或硫代硫酸盐吸附到沉淀的硬度化合物上。在软化步骤之后,废水被导向固-液分离器24。其上吸附有硫化物和/或硫代硫酸盐的沉淀的硬度化合物被除去,产生包含残留元素硫的排出物。排出物被导向第二反应器26。将氧化剂与排出物混合。氧化剂可为与在第一反应器22中使用的氧化剂相同的氧化剂,或可为不同的氧化剂。在一个优选实施方案中,在第二反应器中使用的氧化剂是过氧化氢。氧化剂引起残留元素硫被转变成硫酸盐。来自第二反应器的带有硫酸盐的废水流可随后进行进一步处理。例如,在一些实施方案中,可调节废水的pH为更低,并可使其通过过滤器28。过滤器28可除去任何额外的悬浮固体。可用于过滤器28的过滤器实例包括多介质过滤器、砂滤器、微量过滤器和超滤器。在通过过滤器28处理之后,废水还可通过反渗透或纳米过滤处理以回收。也可将其放出。在其他实施方案中,废水可在离开第二反应器26之后进一步处理以除去额外的污染物。例如,废水可被送至罐27。可添加硫酸或盐酸以调节pH至7.0-8.0。可添加预定剂量的次氯酸盐到罐27中作为消毒剂,以除去水中存在的氨。次氯酸盐的剂量取决于水质。然而,可将pH调节罐中残留的游离氯维持在0.5mg/L以确保彻底的分界点氯化。废水然后可经如上所述的过滤器28过滤。图3提供本文所述方法的第三实施方案30。提供含有硫化物的废水。视需要调节废水的pH,使得pH是7.0-8.0。废水被导向第一阶段氧化罐32。将氧化剂和铁催化剂添加到第一阶段氧化罐32中。在优选实施方案中,氧化剂是过氧化氢,且铁催化剂是氯化铁或硫酸铁。废水中的硫化物被氧化为元素硫,如上所述。来自第一阶段氧化罐32的排出物被导向软化反应罐34。添加石灰以调节pH至高于10,优选地至10.0-10.5。如果需要除去镁,则可升高pH至10.8-11.2。视需要,可额外地添加纯碱。碱性条件导致硬度化合物沉淀。在第一阶段氧化罐32中产生的不溶性元素硫进一步被转变成硫化物和硫代硫酸盐,其将会吸附到沉淀的硬度上。一些实施方案还可包括添加促凝剂以助于凝结沉淀的硬度。沉淀物经固-液分离器36除去。可利用任何固-液分离器。在一些实施方案中,固-液分离器36是澄清器。在一些实施方案中,在固-液分离器36中除去的淤泥可循环至软化反应罐34,可被导向淤泥保持罐44,可被导向压滤机46,或可通过其任何组合处理。在包括压滤机46的实施方案中,可产生滤饼以处置,同时压滤机46中产生的滤液可循环至软化反应罐34。经固体分离器除去固体包括:从废水流除去在CaCO3上吸附的硫化物(S2-)和/或硫代硫酸盐。这具有增加的益处,即减少可在下游任选包括的任何膜分离单元堵塞的趋势。来自固-液分离器36的排出物被导向第二阶段氧化罐38。将氧化剂添加到第二阶段氧化罐38,将残留元素硫氧化为硫酸盐,如上所述。在一个优选实施方案中,氧化剂是过氧化氢。如果pH低于10.5,也可添加铁催化剂,例如氯化铁或硫酸铁。在氧化之后,来自第二阶段氧化罐的排出物被导向pH调节罐40。添加酸以降低pH至7.0-8.0。可用的酸实例包括但不限于盐酸和硫酸。在一些实施方案中,还可添加次氯酸盐至pH调节罐40以对水消毒,并除去水中可能存在的氨。来自pH调节罐40的排出物被导向过滤器42。在一些实施方案中,在过滤之前添加助滤剂。过滤器42除去在过程中产生的残留的悬浮固体。可用的合适过滤器实例包括但不限于多介质过滤器、砂滤器、微量过滤器和超滤器。在过滤之后,经处理的水可被排放或进一步处理,例如通过反渗透或纳米过滤。利用本文所述方法进行了试验。处理来自常见废水的等量样品。一个样品用现有技术的一阶段氧化方法处理,而第二样品用本文公开的两阶段方法处理。这些试验的结果示于以下:如表1可见,对于单阶段氧化方法,需要约1050mg/L的过氧化氢以将硫化物从210mg/L减少至<0.1mg/L(分析方法的硫化物检测限<0.1mg/L),并且过氧化氢的相关估算成本是US$13.80MM/年。对于两阶段氧化方法,需要的总过氧化氢是约410mg/L,以实现经处理的水中<0.5mg/L的硫化物(该分析方法的硫化物检测限<0.1mg/L),并且过氧化氢的相关估算成本是US$5.60MM/年。基于4920gpm的流量和210mg/L(作为S2-)的流入物硫化物浓度,估算了上述两种模式的成本。然而应当注意,化学品成本是流量和水质的函数。两种方法之间的成本比较表明,在本发明中讨论的方法(两阶段氧化和共沉淀和吸附)将会节省化学品(过氧化氢)成本超过US$8.0MM/年。在另一试验中,用下表2所示的组分制备了合成废水:污染物浓度钙(mg/LCa)820镁(mg/LMg)270钠(mg/LNa)1900碱度(mg/LCaCO3)450氯化物(mg/LCl)4900硫酸盐(mg/LSO4)0TDS(mg/L)8500表2:合成废水中污染物的浓度合成废水用于制备淤泥。合成废水还用于测试本文公开的方法。该样品包含2升表2中公开的合成废水。除了表2中所示的组分之外,样品还包含200mg/L硫化物。然后处理第二样品,以按照本文讨论的方法除去硫化物。在软化之后,将来自软化器的上清液分成两份样品。一份样品利用5:1的过氧化物与硫比进行第二阶段氧化,而第二样品利用8:1的过氧化物与硫比进行第二阶段氧化。结果示于下表3。该研究的结果证实,1:1的过氧化氢与硫化物比足以氧化为元素硫。进行了软化,并且根据滤饼的分析性分析显示,除去了大部分的硫。基于先前获得的硫结果,利用8:1的靶标过氧化氢比(240mg/L)将上清液中残余的硫完全氧化为了硫酸盐。当然,本发明可以以不同于本文具体示出的那些的方式实施,而不偏离本发明的必要特征。本发明的实施方案在所有方面均应考虑为说明性而非限制性的,所有落入附加权利要求书的含义和等同范围的改变旨在涵盖于其中。当前第1页1 2 3