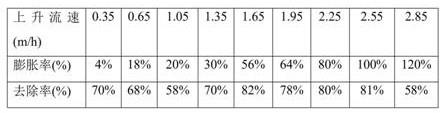
1.本发明属于污水处理技术领域,具体涉及一种生物糖制造业反渗透浓水资源化处理工艺。
背景技术:2.反渗透工艺作为一种高效、清洁的脱盐技术在生物糖制造行业中广泛应用,经反渗透处理后,会有大约占总进水量30%的反渗透浓水排放,由于行业的特殊性,反渗透浓水中的有机物污染物及盐的含量均很高,处理难度大,早期反渗透浓水多采用直接排放,深井注射、喷灌等方法处理,但以上方法并未能从根本上减少反渗透浓水的排放,造成了水资源的浪费和对环境的污染;现在,为避免对环境的污染,多对反渗透浓水进行深度处理,如cn101993162b公开了一种反渗透浓水的处理方法,涉及高浓度难降解有机废水的处理方法,包括以下步骤:调节反渗透浓水ph值;混凝沉淀,去除反渗透浓水中的部分悬浮物、胶体和杂质;炭黑
‑
超声波
‑
fenton氧化;沉淀:经过炭黑
‑
超声波
‑
fenton氧化处理后的反渗透浓水进入沉淀箱,向经过炭黑
‑
超声波
‑
fenton氧化处理后的反渗透浓水中加入碱,调节ph值在8
‑
8.5之间,进行沉淀处理,实现固液分离。该方法采用混凝/沉淀+炭黑
‑
超声波
‑
fenton氧化工艺处理干法腈纶生产废水经处理后剩余的反渗透浓水,提高了污水cod去除率,降低了浊度,缩短了反应时间,减少了h2o2用量。但是该处理方法存在处理不彻底、无法直接排放的问题,而且处理后的水可再利用率低。
技术实现要素:3.本发明针对现有技术中反渗透浓水处理工艺无法深度去除有机物污染物和盐的问题,提供一种生物糖制造业反渗透浓水资源化处理工艺,经处理后的反渗透浓水可达到回用标准,作为制备生物糖的纯水使用。
4.本发明的发明目的是通过以下技术方案实现的:一种生物糖制造业反渗透浓水资源化处理工艺,包括以下步骤:步骤一:絮凝沉淀:向反渗透浓水加入絮凝剂,进行絮凝沉淀处理1
‑
2h,去除反渗透浓水中的部分悬浮物、胶体和杂质。首先采用聚合无机沉淀剂及高分子有机助沉剂将反渗透浓水中难溶盐离子絮凝沉淀去除,减轻浓水生化处理过程对生化微生物的抑制及毒性。
5.步骤二:一级生化处理:对混凝沉淀后的反渗透浓水进行预处理,然后泵入厌氧反应器中,并由厌氧反应器的下方进水,所述厌氧反应器包括下部反应区和上部固液气分离区,下部反应区内设厌氧颗粒污泥,厌氧颗粒污泥的粒径在0.4
‑
0.8mm之间,生化处理过程中产生的沼气上升到厌氧反应器顶部,固液气分离区对沼气进行分离后收集利用;厌氧反应器的一部分出水经管道输送到二级生化处理系统,剩余部分出水进行回流。通过回流可以使系统的上升流速加快,从而使基质的传质作用加强,回流还可对进水进行稀释,使进水的cod浓度降低,以减轻厌氧反应器的底部污泥负荷;同时,可重新利用ph值较高的出水,调
节进水的ph值,以减少碱性物质的投入,节省处理成本。
6.步骤三:二级生化处理:二级生化处理系统包括前段厌氧段和后段好氧段,厌氧段与好氧段串联,经好氧段处理过的一部分泥水混合物回流至厌氧段,进入二级处理系统的处理水首先在厌氧段与回流的泥水混合液进行反硝化作用,再进入好氧段进行硝化作用,好氧段的泥水混合液一部分进行回流,一部分进出二沉池沉淀,其中,厌氧段溶氧浓度小于0.18mg/l,好氧段溶氧浓度为2.5
‑
3.8mg/l。
7.步骤四:深度物化处理:在除盐塔中对二沉池的出水进行除盐处理,首先利用真空泵对除盐塔作抽真空处理,使其真空度达到0.015
‑
0.085mpa,利用恒热循环泵将二沉池的出水泵入恒热器内部加热至70
‑
75℃,再利用液体超重力机将加热后的出水撕裂成微米至纳米级的液滴,大量的水蒸发成汽液后进入冷凝塔冷凝收集制得纯水,未蒸发的液体甩出超重力机进入除盐塔中继续循环除盐。采用高旋转产生超重力效应,形成巨大的快速更新的汽化相界面大幅增强液体湍动程度,提高液体的汽化程度,并减少设备结垢现象。
8.厌氧处理技术对废水的处理浓度范围较广,可处理极高浓度的有机废水,好氧处理技术更适应处理低浓度废水,因此针对生物糖制造过程中产生的反渗透浓水具有高浓度可生化的特性,本工艺选择一级处理进行厌氧处理,二级处理进行好氧处理,且厌氧处理技术有较高的处理负荷能力,占地面积小,需要的能源量比较少,并且可以产生相当多的能源,能够实现反渗透浓水的资源化处理;在厌氧反应器中,颗粒污泥床处于悬浮状态,在上升流速较高的条件下和气流流动进行搅拌的条件下,增大了废水与颗粒污泥之间的接触面积,缩短了水力停留时间,因此厌氧反应器的处理负荷能力和处理效果能够显著提高;厌氧反应器使经过处理的一部分废水进行回流,对于浓度很高的反渗透浓水,进行回流能够很好的对其浓度进行稀释,削减其对系统中微生物的抑制以及毒害作用;反渗透浓水经厌氧处理后,有机污染物浓度大幅降低,为后续二级处理创造有利条件,经厌氧处理后的反渗透浓水再经二级处理系统处理实现对有机污染物的深度处理,二级处理系统将前段厌氧段和后段好氧段串联在一起,硝化液一部分回流至厌氧段,脱氮菌利用进水中的碳源对其进行反硝化,硝化过程各种耗碱的50%可在反硝化过程中得到补偿,所以只需少量投碱或不投碱,工艺流程简单,无需另外投加碳源,建设运行成本低。
9.作为优选,所述步骤二中厌氧反应器内的ph值为7.1
‑
7.4。ph值作为影响厌氧处理的重要因素,其波动会对微生物活性产生影响,无论ph值过高还是过低,都会抑制产甲烷菌的活性,因此将厌氧反应器内的ph值控制在适宜的范围内,并减小其波动范围,以有效提高处理效果。
10.作为优选,所述步骤二中厌氧反应器中进水的表面上升流速为1.65
‑
2.55m/h。污泥床层的膨胀率与上升流速呈正比关系,污泥床层的膨胀率随着上升流速的提高而不断升高。上升流速较低时,污泥膨胀率也较低;上升流速提高到1.65m/h,膨胀率升高到56%;上升流速提高到2.55m/h,膨胀率升高到较高值,污泥层的顶部几乎膨胀到固液气分离区的底端,导致污泥流失;上升流速继续提升,污泥膨胀至固液气分离区内,导致出气管堵塞,污泥大量流失。因此厌氧反应器进水的表面上升流速需控制在合适的范围内,使厌氧颗粒床具备良好的膨胀状态,以使系统内的污泥量保持一个较高值,并能使反渗透浓水与厌氧颗粒污泥充分接触,提高cod去除率。
11.作为优选,所述步骤二中厌氧反应器下部反应区的高径比为3:1
‑
6:1,且在下部反
应区的顶部逐渐扩径形成固液气分离区,固液气分离区与下部反应区的直径比为2:1
‑
3:1。下部反应区采用较高的高径比,在保证厌氧反应器有足够的负荷能力的同时,降低反应器的占地面积,并延长反渗透浓水与厌氧污泥颗粒的接触时间;固液气分离区设在扩径区,可使在下部反应区高速流动的固液气混合物在进入固液气分离区后流速降低,从而使大部分沉降性能好的厌氧颗粒污泥返回下部反应区,减少厌氧颗粒污泥流失。
12.作为优选,所述固液气分离区内沿周向设有弧形缓冲壁,所述弧形缓冲壁平面端设于固液气分离区的内壁,其弧面端朝向固液气分离区中心轴设置。上述设置可进一步减少厌氧污泥颗粒的流失,弧形缓冲壁可降低固液混合体的流速,夹杂在处理水中的大部分厌氧污泥颗粒会被弧形缓冲壁的下弧面阻挡在下部反应区,少量进入固液气分离区的厌氧污泥颗粒则会沿弧形缓冲壁的上弧面返回下部反应区。
13.作为优选,所述步骤二中出水的回流比为4.5
‑
7.5。通过回流可以使系统的上升流速加快,从而加强基质的传质作用,并能对进水进行稀释,使污染物浓度降低,并提高厌氧反应器抗温度变化能力和抗冲击负荷能力,但是回流比的提高会增加厌氧反应器的运行成本,因此,回流比需控制在合适的范围内。
14.作为优选,所述步骤三中厌氧段的水力停留时间为4小时;好氧段的水力停留时间为10小时。
15.作为优选,所述步骤三中泥水混合液的回流比为3.5。好氧段混合液回流直接影响反硝化速率,当回流量过低时,则厌氧段中c/n过高,将没有足够的硝酸根作为电子受体提供给反硝化细菌,反硝化速率降低;当内回流过高时,则会导致没有足够的碳源作为电子供体提供给反硝化细菌,反硝化速率也会降低。
16.作为优选,所述步骤四中的超重力机的转速为800
‑
1400转/分钟。
17.与现有技术相比,本发明具有以下有益效果:本发明通过絮凝沉淀、一级生化处理、二级生化处理、深度物化处理四个步骤的相互配合,实现了生物糖制造业反渗透浓水的深度处理,污染物去除彻底,节能减排;一级生化处理及二级生化处理工艺参数设计合理,有机污染污染物去除彻底,运行成本低;在真空和超重力的环境下对处理水进行蒸发冷凝,提高了液体的汽化程度,能够高效提纯,并减少设备结垢现象;厌氧反应器结构及工艺参数设计合理,增大了废水与颗粒污泥之间的接触面积,并较少颗粒污泥流失,缩短了水力停留时间,反应器的处理负荷能力和处理效果显著提高。
具体实施方式
18.下面通过所表示的实施例对本发明作进一步描述:实施例1本实施例公开一种生物糖制造业反渗透浓水资源化处理工艺,处理过程中主要设备如下:配水井,配置温度调节系统及提升泵;厌氧反应器,呈圆柱状塔形,并配备污泥回流泵;厌氧池及好氧池,配置微孔曝气系统,均布于好氧池池底,并配置混合液回流泵;二沉池,配置污泥回流泵;污泥浓缩池,并配备污泥脱水设备;除盐塔,并配备真空泵、恒热循环泵、液体超重力机。
19.待处理反渗透浓水的原始参数为cod7000mg/l,bod55000mg/l,tss800mg/l,cl
﹣
1200mg/l,ph6.0,电导率1200μs/cm,处理步骤如下:步骤一,絮凝沉淀:向反渗透浓水加入絮凝剂,进行絮凝沉淀处理1.5h,去除反渗透浓水中的部分悬浮物、胶体和杂质,本实施例中絮凝剂采用聚合氯化铝浓度为150mg/l,聚丙烯酰胺浓度为7mg/l,首先采用聚合无机沉淀剂及高分子有机助沉剂将反渗透浓水中难溶盐离子絮凝沉淀去除,减轻浓水生化处理过程对生化微生物的抑制及毒性。
20.步骤二,生化一级处理:将絮凝沉淀后的反渗透浓水排入配水井中进行预处理,对其进行ph调节,调节ph值到7.1,若水温超过40℃,则进行降温处理,以避免水温过高,对反应器中的微生物造成影响。预处理完成后,由提升泵泵送至厌氧反应器中,进水流量为120m3/h。ph值作为影响厌氧处理的重要因素,其波动会对微生物活性产生影响,无论ph值过高还是过低,都会抑制产甲烷菌的活性,因此将厌氧反应器内的ph值控制在适宜的范围内,并减小其波动范围,以有效提高处理效果。
21.厌氧反应器包括下部反应区和上部固液气分离区,下部反应区内设厌氧颗粒污泥,厌氧颗粒污泥的粒径在0.6
‑
0.8mm之间,较大粒径的颗粒污泥机械强度高,凝聚及沉降性能好。
22.混凝沉淀后的反渗透浓水由厌氧反应器的下方进水,上升流速控制在1.65m/h。污泥床层的膨胀率与上升流速呈正比关系,污泥床层的膨胀率随着上升流速的提高而不断升高。上升流速较低时,污泥膨胀率也较低;上升流速提高到1.65m/h,膨胀率升高到56%;上升流速提高到2.55m/h,膨胀率升高到较高值,污泥层的顶部几乎膨胀到固液气分离区的底端,导致污泥流失;上升流速继续提升,污泥膨胀至固液气分离区内,导致出气管堵塞,污泥大量流失,具体数据参见下表1:表1:不同上升流速下的膨胀率及cod去除效果因此厌氧反应器进水的表面上升流速控制在合适的范围内,使厌氧颗粒床具备良好的膨胀状态,以使系统内的污泥量保持一个较高值,并能使反渗透浓水与厌氧颗粒污泥充分接触,提高cod去除率。
23.厌氧反应器下部反应区的高径比为5:1,且在下部反应区的顶部逐渐扩径形成固液气分离区,固液气分离区与下部反应区的直径比为2:1。下部反应区采用较高的高径比,在保证厌氧反应器有足够的负荷能力的同时,降低厌氧反应器的占地面积,并延长反渗透浓水与厌氧污泥颗粒的接触时间;固液气分离区设在扩径区,可使在下部反应区高速流动的固液气混合物在进入固液气分离区后流速降低,从而使大部分沉降性能好的厌氧颗粒污泥返回下部反应区,减少厌氧颗粒污泥流失;为进一步减少厌氧颗粒污泥流失,所述固液气分离区内沿周向设有弧形缓冲壁,所述弧形缓冲壁平面端设于固液气分离区的内壁,其弧面端朝向固液气分离区中心轴设置,弧形缓冲壁可降低固液混合体的流速,夹杂在处理水中的大部分厌氧污泥颗粒会被弧形缓冲壁的下弧面阻挡在下部反应区,少量进入固液气分离区的厌氧污泥颗粒则会沿弧形缓冲壁的上弧面返回下部反应区。
24.一级生化处理过程中产生的沼气上升到厌氧反应器顶部,固液气分离区对沼气进行分离后收集利用,沼气通过集气罩收集,送往发电机组发电,不会对周围环境造成影响。厌氧反应器的一部分出水经管道输送到二级生化处理系统,剩余部分出水进行回流,通过回流可以使系统的上升流速加快,从而使基质的传质作用加强,回流还可对进水进行稀释,使进水的cod浓度降低,以减轻厌氧反应器的底部污泥负荷;同时,可重新利用ph值较高的出水,调节进水的ph值,以减少碱性物质的投入,节省处理成本。
25.本实施例中,一级生化处理过程中的回流比为4.5,通过回流可以使系统的上升流速加快,从而加强基质的传质作用,并能对进水进行稀释,使污染物浓度降低,并提高厌氧反应器抗温度变化能力和抗冲击负荷能力,但是回流比的提高会增加厌氧反应器的运行成本,因此,回流比需控制在合适的范围内,具体参数请参见下表2:表2由上表数据可知,当回流比达到4.5时,cod去除率达到82%,回流比再继续提高,cod去除率提高不明显,甚至随着回流比的增加,cod去除率反而有所下降,因此本工艺中回流比优选4.5。
26.按上述工艺参数,反渗透浓水经絮凝沉淀和一级生化处理后,处理效果参见表3:表3步骤三,生化二级处理,二级处理系统包括前段厌氧段和后段好氧段,厌氧段与好氧段串联,经好氧段处理过的一部分泥水混合物回流至厌氧段,进入二级处理系统的处理水首先在厌氧段与回流的泥水混合液进行反硝化作用,再进入好氧段进行硝化作用,好氧段的泥水混合液一部分进行回流,一部分进出二沉池沉淀,其中,厌氧段溶氧浓度为0.15mg/l,好氧段溶氧浓度为2.5mg/l,污泥沉降比控制在30%,污泥活性较好,呈褐色絮状。
27.步骤三中厌氧段的水力停留时间为4小时;好氧段的水力停留时间为10小时。水力停留时间越长,污染物质在微生物的作用下,被降解的越彻底,但是这会增加处理费用降低处理效率,因此需根据实际情况选择合适的水力停留时间。本实施例中,通过不断试验,选择了上述最优水力停留时间。
28.厌氧段的水力停留时间对cod去除率的影响参见表4:表4
好氧段的水力停留时间对cod去除率的影响参见表5:表5由表4可以看出:cod的去除率随着水解酸化过程水力停留时间的延长而升高,当水力停留时间在4小时的时候,cod去除率在50%以上,继续延长hrt,cod去除率也不会有较大幅度的提高,因此,本工艺中确定厌氧段最佳水力停留时间为4小时;由表5可以看出:cod的去除率随着好氧段的水力停留时间的延长而上升,当水力停留时间达10小时时,cod去除率在85%左右,继续延长水力停留时间,cod去除率不会随之提高,甚至有些降低,这说明,当水力停留时间超过12小时的时候,曝气池中的微生物的代谢活动已经得不到充分的营养来维持,水力停留时间增加将导致污泥解体,沉降性能差,因此,本工艺中确定好氧段最佳水力停留时间为10小时。
29.生化二级处理工艺中,控制其回流比为3。好氧段的混合液内回流直接影响最终处理效果,当回流量过低时,则厌氧段中c/n过高,将没有足够的no
3﹣
作为电子受体提供给反硝化细菌,反硝化速率降低;当内回流过高时,则会导致bod/no
3﹣
过低,又将没有足够的碳源作为电子供体提供给反硝化细菌,反硝化速率也会降低。以系统总氮(tn)去除率为评价指标,对回流比与tn去除率关系进行了实验,结果见表6,由表中数据可知,r由1.0提高到3.5,此时的c/n相对较大,系统tn去除率升高,这说明提高回流比可以增加no
3﹣
浓度,使反硝化速率加快;r由3.5提高到6.0,此时tn去除率却逐渐下降,这说明通过no
3﹣
浓度的增加以及回流的稀释作用,导致c/n过低,反硝化速率减慢。因此,本工艺中确定采用的最佳回流比r为3:5。
30.步骤四:深度物化处理,在除盐塔中对二沉池的出水进行雾化深度处理处理,对高浓度盐进行去除。首先利用真空泵对除盐塔作抽真空处理,使其真空度达到0.015
‑
0.085mpa,利用恒热循环泵将二沉池的出水泵入恒热器内部加热至70
‑
75℃,再利用液体超重力机将加热后的出水撕裂成微米至纳米级的液滴,超重力机的转速为1600转/分钟,同时在真空环境,水的蒸发速率大大加快,大量的水蒸发成汽液后进入冷凝塔冷凝收集制得纯水,未蒸发的液体甩出超重力机进入除盐塔中继续循环除盐。采用高旋转产生超重力效应,形成巨大的快速更新的汽化相界面大幅增强液体湍动程度,提高液体的汽化程度,并减少设备结垢现象,避免化学除垢,产生二次污染,经深度物化处理后,反渗透浓水的除盐率达98%以上,反渗透浓水制取纯水产生的高盐水,经脱除盐份等杂质后的水仍可回流到系统继续制取纯水,减少淡水资源浪费,最大化利用水资源无浓水排放。
31.本实施例通过絮凝沉淀、生化一级处理、生化二级处理、深度物化处理,可完成生物糖制造业中反渗透浓水的深度处理,处理后所得沼气可送往发电组发电,所得纯水可作为生产用水,cod去除率达99.4%,采用电导率仪测定纯水的电导率为11μs/cm,制得纯水中ca
2+
、mg
2+
、na
+
、k
+
、cl、so
42
‑
、fe
2+
、sio
32
‑
、co
32
‑
、hco3等均未检出,实现反渗透浓水的资源化处理。最终处理效果见表6:
表6实施例2待处理反渗透浓水的原始参数为cod9000mg/l,bod56000mg/l,tss800mg/l,cl
﹣
1400mg/l,ph6.1,电导率1600μs/cm,处理步骤如下:步骤一:絮凝沉淀:向反渗透浓水加入絮凝剂,进行絮凝沉淀处理2.0h,去除反渗透浓水中的部分悬浮物、胶体和杂质,本实施例中絮凝剂采用聚合氯化铝浓度为300mg/l,聚丙烯酰胺浓度为10mg/l,首先采用聚合无机沉淀剂及高分子有机助沉剂将反渗透浓水中难溶盐离子絮凝沉淀去除,减轻浓水生化处理过程对生化微生物的抑制及毒性。
32.步骤二:生化一级处理:将絮凝沉淀后的反渗透浓水排入配水井中进行预处理,对其进行ph调节,调节ph值到7.3,若水温超过40℃,则进行降温处理,以避免水温过高,对反应器中的微生物造成影响。预处理完成后,由提升泵泵送至厌氧反应器中,进水流量为100m3/h。ph值作为影响厌氧处理的重要因素,其波动会对微生物活性产生影响,无论ph值过高还是过低,都会抑制产甲烷菌的活性,因此将厌氧反应器内的ph值控制在适宜的范围内,并减小其波动范围,以有效提高处理效果。
33.厌氧反应器包括下部反应区和上部固液气分离区,下部反应区内设厌氧颗粒污泥,厌氧颗粒污泥的粒径在0.6
‑
0.8mm之间,较大粒径的颗粒污泥机械强度高,凝聚及沉降性能好。
34.混凝沉淀后的反渗透浓水由厌氧反应器的下方进水,上升流速控制在2.55m/h。污泥床层的膨胀率与上升流速呈正比关系,污泥床层的膨胀率随着上升流速的提高而不断升高。上升流速较低时,污泥膨胀率也较低;上升流速提高到1.65m/h,膨胀率升高到56.5%;上升流速提高到2.64m/h,膨胀率升高到较高值,污泥层的顶部几乎膨胀到固液气分离区的底端,导致污泥流失;上升流速继续提升,污泥膨胀至固液气分离区内,导致出气管堵塞,污泥大量流失,具体数据参见表1。因此厌氧反应器进水的表面上升流速控制在合适的范围内,使厌氧颗粒床具备良好的膨胀状态,以使系统内的污泥量保持一个较高值,并能使反渗透浓水与厌氧颗粒污泥充分接触,提高cod去除率。
35.厌氧反应器下部反应区的高径比为5:1,且在下部反应区的顶部逐渐扩径形成固液气分离区,固液气分离区与下部反应区的直径比为2:1。下部反应区采用较高的高径比,在保证厌氧反应器有足够的负荷能力的同时,降低厌氧反应器的占地面积,并延长反渗透浓水与厌氧污泥颗粒的接触时间;固液气分离区设在扩径区,可使在下部反应区高速流动的固液气混合物在进入固液气分离区后流速降低,从而使大部分沉降性能好的厌氧颗粒污泥返回下部反应区,减少厌氧颗粒污泥流失;为进一步减少厌氧颗粒污泥流失,所述固液气分离区内沿周向设有弧形缓冲壁,所述弧形缓冲壁平面端设于固液气分离区的内壁,其弧面端朝向固液气分离区中心轴设置,弧形缓冲壁可降低固液混合体的流速,夹杂在处理水中的大部分厌氧污泥颗粒会被弧形缓冲壁的下弧面阻挡在下部反应区,少量进入固液气分
离区的厌氧污泥颗粒则会沿弧形缓冲壁的上弧面返回下部反应区。
36.一级生化处理过程中产生的沼气上升到厌氧反应器顶部,固液气分离区对沼气进行分离后收集利用,沼气通过集气罩收集,送往发电机组发电,不会对周围环境造成影响。厌氧反应器的一部分出水经管道输送到二级生化处理系统,剩余部分出水进行回流,通过回流可以使系统的上升流速加快,从而使基质的传质作用加强,回流还可对进水进行稀释,使进水的cod浓度降低,以减轻厌氧反应器的底部污泥负荷;同时,可重新利用ph值较高的出水,调节进水的ph值,以减少碱性物质的投入,节省处理成本。
37.本实施例中,一级生化处理过程中的回流比为7.5,通过回流可以使系统的上身流速加快,从而较强基质的传质作用,并能对进水进行稀释,使污染物浓度降低,并提高厌氧反应器抗温度变化能力和抗冲击负荷能力,但是回流比的提高会增加厌氧反应器的运行成本,因此,回流比需控制在合适的范围内,具体参数请参见表2。
38.按上述工艺参数,反渗透浓水经絮凝沉淀和一级生化处理后,处理效果参见表7:表7实施例2中步骤三、步骤四的处理工艺与实施例1相同,本实施例通过絮凝沉淀、生化一级处理、生化二级处理、深度物化处理,可完成生物糖制造业中反渗透浓水的深度处理,处理后所得沼气可送往发电组发电,所得纯水可作为生产用水,cod去除率达99.1%,采用电导率仪测定纯水的电导率为16μs/cm,制得纯水中ca
2+
、mg
2+
、na
+
、k
+
、cl、so
42
‑
、fe
2+
、sio
32
‑
、co
32
‑
、hco3等均未检出,实现反渗透浓水的资源化处理。最终处理效果见下表8:表8实施例3待处理反渗透浓水的原始参数为cod8000mg/l,bod55500mg/l,tss600mg/l,cl
﹣
1200mg/l,ph6.2,电导率1300μs/cm,处理步骤如下:步骤一,絮凝沉淀:向反渗透浓水加入絮凝剂,进行絮凝沉淀处理1.5h,去除反渗透浓水中的部分悬浮物、胶体和杂质,本实施例中絮凝剂采用聚合氯化铝浓度为250mg/l,聚丙烯酰胺浓度为8mg/l,首先采用聚合无机沉淀剂及高分子有机助沉剂将反渗透浓水中难溶盐离子絮凝沉淀去除,减轻浓水生化处理过程对生化微生物的抑制及毒性。
39.步骤二,生化一级处理:将絮凝沉淀后的反渗透浓水排入配水井中进行预处理,对其进行ph调节,调节ph值到7.2,若水温超过40℃,则进行降温处理,以避免水温过高,对反应器中的微生物造成影响。预处理完成后,由提升泵泵送至厌氧反应器中,进水流量为
110m3/h。ph值作为影响厌氧处理的重要因素,其波动会对微生物活性产生影响,无论ph值过高还是过低,都会抑制产甲烷菌的活性,因此将厌氧反应器内的ph值控制在适宜的范围内,并减小其波动范围,以有效提高处理效果。
40.厌氧反应器包括下部反应区和上部固液气分离区,下部反应区内设厌氧颗粒污泥,厌氧颗粒污泥的粒径在0.6
‑
0.8mm之间,较大粒径的颗粒污泥机械强度高,凝聚及沉降性能好。
41.混凝沉淀后的反渗透浓水由厌氧反应器的下方进水,上升流速控制在2.15m/h。污泥床层的膨胀率与上升流速呈正比关系,污泥床层的膨胀率随着上升流速的提高而不断升高。上升流速较低时,污泥膨胀率也较低;上升流速提高到1.65m/h,膨胀率升高到56.5%;上升流速提高到2.64m/h,膨胀率升高到较高值,污泥层的顶部几乎膨胀到固液气分离区的底端,导致污泥流失;上升流速继续提升,污泥膨胀至固液气分离区内,导致出气管堵塞,污泥大量流失,具体数据参见表1。因此厌氧反应器进水的表面上升流速控制在合适的范围内,使厌氧颗粒床具备良好的膨胀状态,以使系统内的污泥量保持一个较高值,并能使反渗透浓水与厌氧颗粒污泥充分接触,提高cod去除率。
42.厌氧反应器下部反应区的高径比为5:1,且在下部反应区的顶部逐渐扩径形成固液气分离区,固液气分离区与下部反应区的直径比为2:1。下部反应区采用较高的高径比,在保证厌氧反应器有足够的负荷能力的同时,降低厌氧反应器的占地面积,并延长反渗透浓水与厌氧污泥颗粒的接触时间;固液气分离区设在扩径区,可使在下部反应区高速流动的固液气混合物在进入固液气分离区后流速降低,从而使大部分沉降性能好的厌氧颗粒污泥返回下部反应区,减少厌氧颗粒污泥流失;为进一步减少厌氧颗粒污泥流失,所述固液气分离区内沿周向设有弧形缓冲壁,所述弧形缓冲壁平面端设于固液气分离区的内壁,其弧面端朝向固液气分离区中心轴设置,弧形缓冲壁可降低固液混合体的流速,夹杂在处理水中的大部分厌氧污泥颗粒会被弧形缓冲壁的下弧面阻挡在下部反应区,少量进入固液气分离区的厌氧污泥颗粒则会沿弧形缓冲壁的上弧面返回下部反应区。
43.一级生化处理过程中产生的沼气上升到厌氧反应器顶部,固液气分离区对沼气进行分离后收集利用,沼气通过集气罩收集,送往发电机组发电,不会对周围环境造成影响。厌氧反应器的一部分出水经管道输送到二级生化处理系统,剩余部分出水进行回流,通过回流可以使系统的上升流速加快,从而使基质的传质作用加强,回流还可对进水进行稀释,使进水的cod浓度降低,以减轻厌氧反应器的底部污泥负荷;同时,可重新利用ph值较高的出水,调节进水的ph值,以减少碱性物质的投入,节省处理成本。
44.本实施例中,一级生化处理过程中的回流比为6.4,通过回流可以使系统的上身流速加快,从而较强基质的传质作用,并能对进水进行稀释,使污染物浓度降低,并提高厌氧反应器抗温度变化能力和抗冲击负荷能力,但是回流比的提高会增加厌氧反应器的运行成本,因此,回流比需控制在合适的范围内,具体参数请参见表2。
45.按上述工艺参数,反渗透浓水经絮凝沉淀和一级生化处理后,处理效果参见表9:
表9实施例3中步骤三、步骤四的处理工艺与实施例1相同,本实施例通过絮凝沉淀、生化一级处理、生化二级处理、深度物化处理,可完成生物糖制造业中反渗透浓水的深度处理,处理后所得沼气可送往发电组发电,所得纯水可作为生产用水,cod去除率达98.9%,采用电导率仪测定纯水的电导率为17μs/cm,制得纯水中ca
2+
、mg
2+
、na
+
、k
+
、cl、so
42
‑
、fe
2+
、sio
32
‑
、co
32
‑
、hco3等均未检出,实现反渗透浓水的资源化处理。最终处理效果见下表10:表10本发明公开的生物糖制造业中反渗透浓水资源化处理工艺,通过絮凝沉淀、一级生化处理、二级生化处理、深度物化处理四个步骤的相互配合,实现了反渗透浓水的深度处理。
46.针对生物糖制造中反渗透浓水有机污染物浓度高,可生化性好的特性,首先通过絮凝沉淀将反渗透浓水中难溶盐离子絮凝沉淀去除,减轻浓水生化处理过程对生化微生物的抑制及毒性,为后续以及生化处理和二级生化处理提供了有利条件;厌氧反应器在成功启动后,通过控制回流比、系统ph值、上升流速等工艺参数,可以降解绝大部分的有机污染物,并产生可利用的沼气;反渗透浓水内残留的有机污染物再通过生化二级处理即可达到99%左右的去除率;去除有机污染物后反渗透浓水在真空条件和超重力效应下快速汽化,最终冷凝制得可再利用的纯水,实现反渗透浓水的资源化处理。
47.本文中所描述的具体实施例仅仅是对本发明精神作举例说明。本发明所属技术领域的技术人员可以对所描述的具体实施例做各种各样的修改或补充或采用类似的方式替代,但并不会偏离本发明的精神或者超越所附权利要求书所定义的范围。