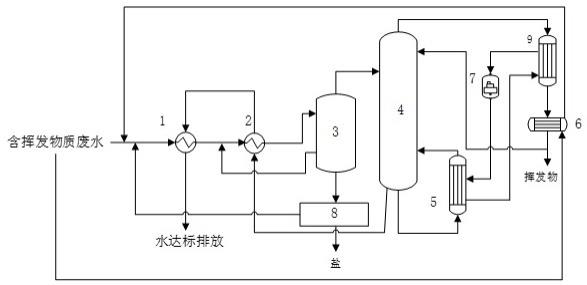
1.本实用新型属于废水处理设备技术领域,涉及含挥发性物质废水的节能资源化处理系统。
背景技术:2.利用废水中挥发性物质与水沸点的不同,汽提精馏技术是应用最为成熟的分离技术,尤其是对于挥发物质附加值较高的废水,常规的精馏系统模式为向汽提精馏塔塔釜通入蒸汽供热,废水中的有机物受热挥发,从汽提精馏塔塔顶蒸出并经冷凝冷却收集回收,塔釜出水与进水换热后达标排放。常规的精馏技术虽然有效,但蒸汽能耗较大,尤其是分离于沸点与水差距不大的有机物,蒸汽能耗更大。为降低能耗,研究者尝试开发了不同的节能技术,中国专利cn113233529a一种节能/低能耗的氨氮废水处理和资源化回收工艺及装置,提出脱氨出水闪蒸并经压缩后产生的蒸汽和新鲜饱和蒸汽一起作为汽提精馏塔釜热源,进料用闪蒸后脱氨出水和塔顶含氨蒸汽冷凝后的气相换热,塔顶含氨蒸汽用闪蒸后脱氨出水冷凝,冷凝后的气相再用进水降温,该系统设计目的为实现系统热能回收最大化,同时节省输入的冷量,减少新鲜蒸汽需求量。中国专利cn112374561a和cn214031795u提出双热泵法的脱氨工艺,汽提精馏塔塔釜出水利用蒸汽热泵汽化,产生的二次蒸汽作为塔釜再沸器1热源,汽化后剩余水给进料加热;同时,塔顶含氨蒸汽压缩为过热蒸汽,给塔釜再沸器2提供热源,含氨蒸汽被移走热量后,一部分转变为稀氨水,另外一部份未被冷凝的含氨蒸汽进入综合反应器和氨水储罐制备氨水,稀氨水从氨汽再沸器排出进入凝液罐缓存,被凝液泵增压后,一部分作为喷淋液使用,另外一部分与进料混合后进入汽提精馏塔循环脱氨。中国专利cn111825145a和cn212609643u设置单热泵,汽提精馏塔塔顶含氨蒸汽进入塔顶冷凝器,冷侧水受热汽化产生的蒸汽压缩后产生的二次蒸汽进入塔釜再沸器供热,再沸器排出的冷凝水返回塔顶冷凝器作为冷侧介质,这种系统也可以起到回收塔顶含氨蒸汽热能的作用,同时减少用于含氨蒸汽冷凝冷却的循环水用量。中国专利cn103964528b设置汽提精馏塔和氨气汽提精馏塔两级装置,汽提精馏塔塔顶含氨蒸汽压缩后进入塔釜再沸器,再沸器排出的稀氨水收集并回流到汽提精馏塔顶,未冷凝的氨蒸汽进入氨气汽提精馏塔制备浓氨水。中国专利cn10264948b提出系统设置至少两级汽提精馏塔,二级汽提精馏塔塔釜输入蒸汽由自身塔釜出水被上一级塔顶含氨蒸汽加热汽化产生的蒸汽和上一级塔釜出水闪蒸所得的蒸汽提供,如此交叉回收热能,达到节省能耗的目标。
3.中国专利cn104671307b一种dmf废水的处理工艺,将塔顶蒸汽压缩作为再沸器热源。中国专利cn214059976u和cn112479296a一种脱氨处理系统和方法,设置汽提精馏塔和蒸发器,汽提精馏塔塔釜再沸器冷凝水进入闪蒸罐产生的蒸汽返回作为塔釜热源,闪蒸后剩余水进入蒸发器,塔顶含氨蒸汽进入蒸发器作为热源将剩余水加热汽化,汽化产生的蒸汽被压缩为过热蒸汽,返回塔釜再沸器作为热源。中国专利cn113880168a一种脱氨处理系统,包括3种模式,分别为常规模式、塔釜再沸器冷凝水闪蒸产生蒸汽返回再沸器供热模式和塔顶含氨蒸汽压缩作为再沸器热源模式。中国专利cn103408086a一种mvr汽提脱氨系统
及方法,设置汽提精馏塔和氨水提浓塔,汽提精馏塔塔顶含氨蒸汽压缩进入塔釜再沸器,再沸器出来的稀氨水不回流到汽提精馏塔,进入氨水提浓塔制备浓氨水,氨水提浓塔底部直接通入蒸汽,汽提精馏塔进水依次与汽提精馏塔塔釜出水、氨水提浓塔塔釜出水换热。中国专利cn113651380a一种对含氨氮杂盐废水进行蒸氨处理的系统及方法,汽提精馏塔进水依次与塔顶含氨蒸汽、塔釜出水换热,这种方法虽然能降低循环冷却水的用量,但并不能显著降低蒸汽消耗,也无法将系统热能全部回收。中国专利cn111170389a一种氨氮废水汽提蒸氨系统和方法,设置汽提精馏塔和氨水提浓塔,汽提精馏塔塔顶蒸汽压缩进入再沸器作为热源,再沸器得到的稀氨水进入氨水提浓塔,氨水提浓塔塔釜出水与汽提精馏塔进水混合,然后与汽提精馏塔进水换热。中国专利cn108910992a一种应用于高含盐高cod废水的精馏、mvr蒸发装置,设置精馏和mvr蒸发两级装置,汽提精馏塔将废水中cod去除,汽提精馏塔出水进入蒸发器,蒸发器顶部蒸汽压缩形成的过热蒸汽提供汽提精馏塔和蒸发器供热热源。中国专利cn104926609a,一种处理布洛芬合成工序中新戊二醇母液的方法及其工艺流程,设置汽提塔和汽提精馏塔,利用汽提塔去除有机物,汽提精馏塔塔顶蒸汽压缩后产生的二次蒸汽作为汽提塔和汽提精馏塔塔釜热源。
4.上述各种节能系统均能不同程度的降低蒸汽能耗,但均存在废水与汽提精馏塔直接接触的问题,废水中成分复杂,会造成汽提精馏塔堵塞和腐蚀,设备造价较高。另外,含氨蒸汽被压缩后形成的过热蒸汽腐蚀性非常强,对金属材质设备和管道具有很强的腐蚀性,设备和安装材料造价也比较高。双热泵法虽然能降低新鲜蒸汽消耗,但两台压缩机的动能消耗较大,处理每吨废水的单耗并没有明显降低。再者,以上各种节能工艺并不能完全将系统中的热能回收,也无法完全不输入冷量,无法实现节能最大化。
技术实现要素:5.鉴于现有节能系统的不足,本实用新型提供含挥发物质废水的节能处理系统,能够节能处理含挥发物质废水的同时,实现含挥发物质废水的资源化利用。所述挥发物质是指沸点小于水的所有具有挥发性且气相状态下可被压缩的物质,如氨等无机物和醇类、酮类等有机物。
6.含挥发性物质废水的节能资源化处理系统,其中的一个技术方案包括第一级预热器、第二级预热器、闪蒸罐、汽提精馏塔、再沸器、冷凝器、压缩机、蒸发器和塔顶换热器;
7.所述含挥发性物质废水出口与第一级预热器冷流体进口相连,第一级预热器冷流体出口与第二级预热器冷流体进口相连,第二级预热器冷流体出口与闪蒸罐进液口相连,闪蒸罐蒸汽出口与汽提精馏塔进料口连接;
8.所述汽提精馏塔塔顶蒸汽出口与塔顶换热器热流体进口连接,塔顶换热器热流体出口与冷凝器热流体进口连接,冷凝器热流体出口分别与汽提精馏塔塔顶回流液进口和挥发物质产品出口连接;冷凝器冷流体进口与含挥发性物质废水出口连接,冷凝器冷流体出口与第一级预热器冷流体进口连接;
9.所述塔顶换热器冷流体进口与塔釜再沸器热流体出口连接,塔顶换热器冷流体出口与压缩机蒸汽进口连接,压缩机蒸汽出口与再沸器热流体进口连接;
10.所述汽提精馏塔塔釜出水口与第二级预热器热流体进口连接,第二级预热器热流体出口与第一级预热器热流体进口连接,第一级预热器热流体出口与达标水排放口连接;
11.所述闪蒸罐出水口与第二级预热器冷流体进口连接,闪蒸罐出盐口与蒸发器进液口连接,蒸发器冷凝水出口与第一级预热器冷流体进口连接,蒸发器固体出口为盐产品出口。
12.该系统的工作流程为:含挥发物质废水先进入第一级预热器预热,然后进入第二级预热器预热,进入闪蒸罐,闪蒸罐得到的含挥发物质蒸汽进入汽提精馏塔。汽提精馏塔塔釜设置再沸器,再沸器冷凝水进入塔顶换热器,塔顶含挥发物质蒸汽在塔顶换热器中将冷凝水汽化,产生的蒸汽进入压缩机,压缩得到的二次蒸汽返回塔釜再沸器作为热源。塔顶换热器中排出的含挥发物质冷凝液及未冷凝气体进入冷凝器进行二级冷凝,用含挥发物质废水原水作循环冷却水。含挥发物质冷凝液部分回流至汽提精馏塔塔顶,部分采出。汽提精馏塔塔釜出水,先进入第二级预热器回收大部分热量,然后进入第一级预热器回收剩余热量,最后达标排放。闪蒸罐中剩余水与含挥发物质原水混合后返回第二级预热器;待闪蒸罐中剩余水中盐达到一定浓度,将其从闪蒸罐排出送往蒸发器,蒸发冷凝水和含挥发物质原水混合一起进入一级预热器,然后去后续的精馏系统。
13.进一步地,第一级预热器、第二级预热器、闪蒸罐、汽提精馏塔、再沸器、冷凝器、压缩机、蒸发器和塔顶换热器均设有测温装置。
14.该系统具有以下有益技术效果:(1)废水两级预热后闪蒸,含挥发物质蒸汽进入汽提精馏塔,废水中的盐分不直接进入汽提精馏塔,避免了废水中腐蚀性物质对汽提精馏塔的腐蚀,塔材质要求较低,设备投资大大下降。(2)塔顶含挥发物质蒸汽不直接压缩,避免了压缩后的含挥发物质过热蒸汽对压缩机设备和管道的腐蚀,设备投资也大大降低。塔顶含挥发物质蒸汽将再沸器冷凝水汽化,有效回收了热量,并且大大降低了用于含挥发物质蒸汽冷凝的冷量需求。用废水原水对含挥发物质冷凝液冷凝冷却,将热流体携带的热量几乎全部回收,且不需要外界额外的循环冷却水。(3)塔釜出水经两级换热,携带的热量全部被回收,并以不含杂质的纯水形式被回收,可直接回用于工艺。(4)全系统实现废水中挥发物质、水和盐分的同步回收,进入蒸发器的溶液量减少90%,大大降低了蒸发器的投资费用。(5)全系统热量回收率超过95%,大大降低了能耗。
15.本实用新型提供的另一个技术方案包括:第一级预热器、第二级预热器、闪蒸罐、汽提精馏塔、再沸器、冷凝器、压缩机和蒸发器;
16.所述含挥发性物质废水出口与第一级预热器冷流体进口相连,第一级预热器冷流体出口与第二级预热器冷流体进口相连,第二级预热器冷流体出口与闪蒸罐进液口相连,闪蒸罐蒸汽出口与汽提精馏塔进料口连接;
17.所述汽提精馏塔塔顶蒸汽出口与压缩机蒸汽进口连接,压缩机蒸汽出口与再沸器热流体进口连接;再沸器热流体出口与冷凝器热流体进口连接,冷凝器热流体出口分别与汽提精馏塔塔顶回流液进口和挥发物质产品出口连接;冷凝器冷流体进口与含挥发性物质废水出口连接,冷凝器冷流体出口与第一级预热器冷流体进口连接;
18.所述汽提精馏塔塔釜出水口与第二级预热器热流体进口连接,第二级预热器热流体出口与第一级预热器热流体进口连接,第一级预热器热流体出口与达标水排放口连接;
19.所述闪蒸罐出水口与第二级预热器冷流体进口连接,闪蒸罐出盐口与蒸发器进液口连接,蒸发器冷凝水出口与第一级预热器冷流体进口连接,蒸发器固体出口为盐产品出口。
20.该系统的工作流程为:含挥发物质废水先进入第一级预热器预热,然后进入第二级预热器预热,进入闪蒸罐,闪蒸罐得到的含挥发物质蒸汽进入汽提精馏塔。汽提精馏塔塔釜设置再沸器,塔顶含挥发物质蒸汽进入压缩机,压缩得到的二次蒸汽返回塔釜再沸器作为热源。塔釜再沸器排出的含挥发物质冷凝液及未冷凝气体进入冷凝器进行二级冷凝,用含挥发物质废水原水作循环冷却水。含挥发物质冷凝液部分回流至汽提精馏塔塔顶,部分采出。汽提精馏塔塔釜出水,先进入第二级预热器回收大部分热量,然后进入第一级预热器回收剩余热量,最后达标排放。闪蒸罐中剩余水与含挥发物质原水混合后返回第二级预热器;待闪蒸罐中剩余水中盐达到一定浓度,将其从闪蒸罐排出送往蒸发器,蒸发冷凝水和含挥发物质原水混合进入一级预热器,然后去后续的精馏系统。
21.进一步地,第一级预热器、第二级预热器、闪蒸罐、汽提精馏塔、再沸器、冷凝器、压缩机和蒸发器均设有测温装置。
22.该系统具有以下有益技术效果:(1)废水两级预热后闪蒸,含挥发物质蒸汽进入汽提精馏塔,废水中的盐分不直接进入汽提精馏塔,避免了废水中腐蚀性物质对汽提精馏塔的腐蚀,塔材质要求较低,设备投资大大下降。(2)塔顶含挥发物质蒸汽直接压缩为高压蒸汽,给再沸器供热,有效回收了热量,并且大大降低了用于含挥发物质蒸汽冷凝的冷量需求。用废水原水对含挥发物质冷凝液冷凝冷却,将热流体携带的热量几乎全部回收,且不需要外界额外的循环冷却水。(3)塔釜出水经两级换热,携带的热量全部被回收,并以不含杂质的纯水形式被回收,可直接回用于工艺。(4)全系统实现废水中挥发物质、水和盐分的同步回收,进入蒸发器的溶液量减少90%,大大降低了蒸发器的投资费用。(5)全系统热量回收率超过95%,大大降低了能耗。
23.本实用新型涉及到的第一级预热器、第二级预热器、闪蒸罐、汽提精馏塔、再沸器、冷凝器、压缩机、蒸发器、塔顶换热器、测温装置均为常规设备,可以按照生产工艺参数需要选购现有设备。
24.本实用新型相对于现有技术具有以下优点:(1)全系统不仅适用于氨氮等碱性溶液,也同时适用于醇(酮)类有机废水中挥发性物质的回收;(2)系统设计进塔两级换热,蒸发器、闪蒸罐、汽提精馏塔均作为上述换热器的热源,不引入额外蒸汽换热,充分利用了塔釜、闪蒸罐、蒸发器的热量,使热量回收效果更高,全系统热量回收率超过95%,真正实现了节能降耗;(3)使用汽提精馏塔顶蒸汽冷凝后压缩升温,作为塔釜换热器的热源,不额外引入热源,蒸汽不与废水接触;(4)用废水原水对含挥发物质冷凝液冷凝冷却,不需要额外的冷却水;(5)整个系统的热量全部自循环,包括初次开车在内,不需要额外引入热蒸汽、冷凝水;(6)全系统实现废水中挥发物质、水和盐分的同步回收和资源化处理;(7)增设闪蒸罐,使废水中仅挥发性成分进入汽提精馏塔,其中的盐分不直接进入汽提精馏塔,避免了废水中腐蚀性物质对汽提精馏塔的腐蚀,塔材质要求较低,降低设备投资;(8)传统方式中无闪蒸罐,则含盐水直接进入汽提精馏塔,后塔釜出水进入蒸发器进行蒸发,而塔釜水量与进水水量一致,本专利增设闪蒸罐后,挥发性组分进入汽提精馏塔,含盐组分进入蒸发器,使进入蒸发器的溶液量减少90%,大大降低了蒸发器的投资费用。
附图说明
25.图1是实施例1的结构示意图。
26.图2是实施例2的结构示意图。
27.图中:1-第一级预热器,2-第二级预热器,3-闪蒸罐,4-汽提精馏塔,5-再沸器,6-冷凝器,7-压缩机,8-蒸发器,9-塔顶换热器。
具体实施方式
28.下面结合说明书附图,对本实用新型的技术方案进行清楚、完整的描述。显然,所描述的实施方式仅仅是本实用新型一部分实施方式,而不是全部的实施方式。基于本实用新型的实施方式,本领域普通技术人员在没有做出创造性劳动前提下所获得的所有其他实施方式,都属于本实用新型的保护范围。
29.在本实用新型的描述中,需要理解的是,术语“中心”、“纵向”、“横向”、“上”、“下”、“前”、“后”、“左”、“右”、“竖直”、“水平”、“顶”、“底”、“内”、“外”等指示的方位或位置关系为基于附图所示的方位或位置关系,仅是为了便于描述本实用新型和简化描述,而不是指示或暗示所指的装置或元件必须具有特定的方位、以特定的方位构造和操作,因此不能理解为对本实用新型的限制。此外,术语“第一”、“第二”仅用于描述目的,而不能理解为指示或暗示相对重要性或数量或位置。
30.在本实用新型的描述中,需要说明的是,除非另有明确的规定和限定,术语“安装”、“相连”、“连接”应做广义理解,例如,可以是固定连接,也可以是可拆卸连接,或一体地连接;可以是机械连接,也可以是电连接;可以是直接相连,也可以通过中间媒介间接相连,可以是两个元件内部的连通。对于本领域的普通技术人员而言,可以根据具体情况理解上述术语在本实用新型中的具体含义。
31.实施例1
32.如图1所示,含挥发性物质废水的节能资源化处理系统,包括第一级预热器1、第二级预热器2、闪蒸罐3、汽提精馏塔4、再沸器5、冷凝器6、压缩机7、蒸发器8和塔顶换热器9;
33.含挥发性物质废水出口与第一级预热器1冷流体进口相连,第一级预热器1冷流体出口与第二级预热器2冷流体进口相连,第二级预热器2冷流体出口与闪蒸罐3进液口相连,闪蒸罐3蒸汽出口与汽提精馏塔4进料口连接;
34.所述汽提精馏塔4塔顶蒸汽出口与塔顶换热器9热流体进口连接,塔顶换热器9热流体出口与冷凝器6热流体进口连接,冷凝器6热流体出口分别与汽提精馏塔4塔顶回流液进口和挥发物质产品出口连接;冷凝器6冷流体进口与含挥发性物质废水出口连接,冷凝器6冷流体出口与第一级预热器1冷流体进口连接;
35.所述塔顶换热器9冷流体进口与塔釜再沸器5热流体出口连接,塔顶换热器9冷流体出口与压缩机7蒸汽进口连接,压缩机7蒸汽出口与再沸器5热流体进口连接;
36.所述汽提精馏塔4塔釜出水口与第二级预热器2热流体进口连接,第二级预热器2热流体出口与第一级预热器1热流体进口连接,第一级预热器1热流体出口与达标水排放口连接;
37.所述闪蒸罐3出水口与第二级预热器2冷流体进口连接,闪蒸罐3出盐口与蒸发器8进液口连接,蒸发器8冷凝水出口与第一级预热器1冷流体进口连接。
38.该系统的工作流程为:含挥发物质废水先进入第一级预热器1预热,然后进入第二级预热器2预热,进入闪蒸罐3,闪蒸罐3得到的含挥发物质蒸汽进入汽提精馏塔4。汽提精馏
塔4塔釜设置再沸器5,再沸器5冷凝水进入塔顶换热器9,塔顶含挥发物质蒸汽在塔顶换热器9中将冷凝水汽化,产生的蒸汽进入压缩机7,压缩得到的二次蒸汽返回塔釜再沸器5作为热源。塔顶换热器9中排出的含挥发物质冷凝液及未冷凝气体进入冷凝器6进行二级冷凝,用含挥发物质废水原水作循环冷却水。含挥发物质冷凝液部分回流至汽提精馏塔塔顶,部分采出。汽提精馏塔4塔釜出水,先进入第二级预热器2回收大部分热量,然后进入第一级预热器1回收剩余热量,最后达标排放。闪蒸罐3中剩余水与原水(经第一级预热器1预热出水)混合后返回第二级预热器2;待剩余水中盐达到一定浓度,将其从闪蒸罐3排出送往蒸发器8,蒸发冷凝水和含挥发物质原水混合一起去第一级预热器1,然后进入精馏系统。
39.实施例2
40.如图2所示,含挥发性物质废水的节能资源化处理系统,包括:第一级预热器1、第二级预热器2、闪蒸罐3、汽提精馏塔4、再沸器5、冷凝器6、压缩机7和蒸发器8;
41.所述含挥发性物质废水出口与第一级预热器1冷流体进口相连,第一级预热器1冷流体出口与第二级预热器2冷流体进口相连,第二级预热器2冷流体出口与闪蒸罐3进液口相连,闪蒸罐3蒸汽出口与汽提精馏塔4进料口连接;
42.所述汽提精馏塔4塔顶蒸汽出口与压缩机7蒸汽进口连接,压缩机7蒸汽出口与再沸器5热流体进口连接;再沸器5热流体出口与冷凝器6热流体进口连接,冷凝器6热流体出口分别与汽提精馏塔4塔顶回流液进口和挥发物质产品出口连接;冷凝器6冷流体进口与含挥发性物质废水出口连接,冷凝器6冷流体出口与第一级预热器1冷流体进口连接;
43.所述汽提精馏塔4塔釜出水口与第二级预热器2热流体进口连接,第二级预热器2热流体出口与第一级预热器1热流体进口连接,第一级预热器1热流体出口与达标水排放口连接;
44.所述闪蒸罐3出水口与第二级预热器2冷流体进口连接,闪蒸罐3出盐口与蒸发器8进液口连接,蒸发器8冷凝水出口与第一级预热器1冷流体进口连接。
45.该系统的工作流程为:含挥发物质废水先进入第一级预热器1预热,然后进入第二级预热器2预热,进入闪蒸罐3,闪蒸罐3得到的含挥发物质蒸汽进入汽提精馏塔4。汽提精馏塔4塔釜设置再沸器5,塔顶含挥发物质蒸汽进入压缩机7,压缩得到的二次蒸汽返回塔釜再沸器5作为热源。塔釜再沸器5排出的含挥发物质冷凝液及未冷凝气体进入冷凝器6进行二级冷凝,用含挥发物质废水原水作循环冷却水。含挥发物质冷凝液部分回流至汽提精馏塔4塔顶,部分采出。汽提精馏塔4塔釜出水,先进入第二级预热器2回收大部分热量,然后进入第一级预热器1回收剩余热量,最后达标排放。闪蒸罐3中剩余水与原水(经第一级预热器1预热出水)混合后返回第二级预热器2;待剩余水中盐达到一定浓度,将其从闪蒸罐3排出送往蒸发器8,蒸发冷凝水和含挥发物质原水混合一起去第一级预热器1,然后进入精馏系统。
46.尽管上面已经示出和描述了本实用新型的实施方式,可以理解的是,上述实施方式是示例性的,不能理解为对本实用新型的限制,本领域的普通技术人员在不脱离本实用新型的原理和宗旨的情况下在本实用新型的范围内可以对上述实施方式进行变化、修改、替换和变型。本实用新型的保护范围由权利要求书及其等同技术方案限定。