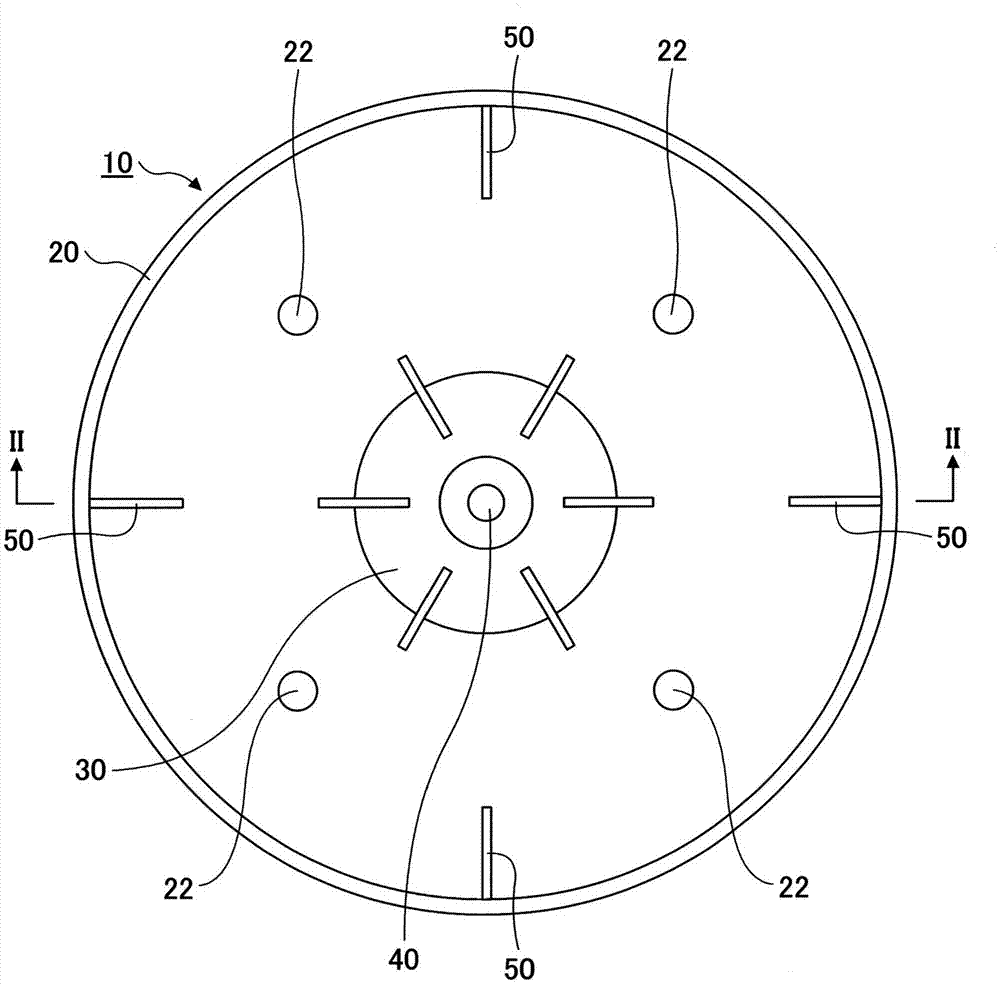
本发明涉及一种化学反应装置、以及使用了化学反应装置的颗粒的制造方法。
背景技术:
:近年来,随着便携式电话、笔记本型个人计算机等便携式电子设备的普及,需要开发具有高能量密度的小型且轻量化的二次电池。另外,作为以混合动力汽车为首的电动汽车用的电池,还需要开发高输出的二次电池。作为满足此类要求的非水系电解质二次电池,存在锂离子二次电池。锂离子二次电池由负极、正极、电解液等构成,对于负极和正极的活性物质,使用能够脱出和插入锂的材料。对于使用锂复合氧化物作为正极材料的锂离子二次电池,特别是对于使用合成较容易的锂钴复合氧化物作为正极材料的锂离子二次电池,由于能够得到4v级的高电压,因此期待将其用作具有高能量密度的电池,其应用化正在进展。对于使用锂钴复合氧化物的电池,至今已经进行了大量的为了获得优异初始容量特性或循环特性的开发,并已经获得了各种成果。然而,由于锂钴复合氧化物使用价格昂贵的钴化合物作为原料,因此使用该锂钴复合氧化物的电池的每单位容量的单价较镍氢电池大幅升高,可适用的用途被极大限制。因此,不仅对于便携式设备用的小型二次电池,即便对于蓄电用或电动汽车用的二次电池等大型二次电池来说,也非常期待能够降低正极材料的成本,能够制造更廉价的锂离子二次电池,可以说其实现在工业上具有重大意义。作为锂离子二次电池用活性物质的新的材料,可以举出使用了比钴更廉价的镍的锂镍复合氧化物。该锂镍复合氧化物由于显示出比锂钴复合氧化物更低的电化学势,因此难以引起因电解液的氧化而分解的问题,能够期待更高的容量,并显示出与钴系同样高的电池电压,因而正在积极地进行开发。然而,在以仅纯粹由镍所合成的锂镍复合氧化物作为正极材料来制作锂离子二次电池的情况下,存在与钴系相比循环特性较差、以及因在高温环境下使用或保存使得电池性能较易受损的缺点,因此通常已知以钴或铝来取代一部分镍的锂镍复合氧化物。关于正极活性物质的通常的制造方法,已知以下的方法:(1)首先,利用中和析晶法制作作为锂镍复合氧化物的前驱体的镍复合氢氧化物,(2)将该前驱体与锂化合物混合并进行烧成。其中,作为利用(1)的中和析晶法制造颗粒的方法,代表性的实施方式是使用搅拌槽的工序。在专利文献1中,向搅拌槽内供应包含镍盐和钴盐的混合水溶液、包含铵离子提供体的水溶液、以及苛性碱性水溶液并使其反应,使镍钴复合氢氧化物的颗粒析出。记载了通过使混合水溶液的每个供给口的供应量与反应水溶液量的比率为0.04体积%/分钟以下,从而能够获得粒径较大、结晶性较高、形状大致为球形的颗粒。现有技术文献专利文献专利文献1:日本国特开2011-201764号公报技术实现要素:发明所要解决的课题以往以来,为了使用搅拌槽来获得所需特性的颗粒,进行了各种研究。然而,如果搅拌叶轮的类型或叶轮径、搅拌槽的容积等装置构造改变,则每次都需要进行条件设定。本发明的发明人针对能够在各种构造的化学反应装置中普遍地提高颗粒的品质的条件进行了分析,并着眼于高过饱和区域在搅拌槽内的溶液中所占的体积比率。在此,高过饱和区域是指溶解于水溶液中的颗粒成分的浓度为预定值以上的区域。在高过饱和区域中,由于颗粒成分的浓度充分大于溶解度,因此颗粒成分的析出以显著的速度发生。本发明的发明人发现:高过饱和区域在搅拌槽内的溶液中所占的体积比率越小,则颗粒成分的析出进行得越缓慢,因此能够提高颗粒的品质。另一方面,高过饱和区域形成在用于向溶液中排出原料液的排出口附近。为了降低高过饱和区域的体积,需要颗粒成分迅速扩散,增加搅拌叶轮的转数较为有效。然而,如果增大搅拌叶轮的转数,则能量消耗会变大。鉴于上述问题,本发明的主要目的在于提供一种化学反应装置,其能够有效地提高颗粒的品质。用于解决课题的方法为了解决上述问题,本发明的一个方面提供一种化学反应装置,其一边向溶液中供应原料液,一边在所述溶液中使颗粒析出,所述化学反应装置具有容纳所述溶液的搅拌槽、以及对所述溶液进行搅拌的搅拌叶轮,所述化学反应装置具有向所述溶液中排出所述原料液的多个排出部。发明的效果根据本发明的一个方面,提供一种化学反应装置,其能够有效地提高颗粒的品质。附图说明图1是示出用于根据一个实施方式的化学反应装置的俯视图。图2是沿图1的ii-ii线的剖面图。图3是通过模拟来计算出根据一个实施方式的搅拌槽内的流场的uk的分布的图。图4是根据一个实施方式的含镍氢氧化物的制造方法的流程图。图5是在根据一个实施方式的颗粒生长步骤的前半部分中所形成的凝集体的示意性的剖面图。图6是在根据一个实施方式的颗粒生长步骤的后半部分中所形成的外壳的示意性的剖面图。图7是示出根据一个实施方式的核生成步骤中的反应水溶液中的第一高过饱和区域的图。图8是在第一高过饱和区域在连续式的搅拌槽内的反应水溶液中所占的体积比率为0.025%的情况下所得到的颗粒的示例的sem照片。图9是在第一高过饱和区域在连续式的搅拌槽内的反应水溶液中所占的体积比率为0.100%的情况下所得到的颗粒的示例的sem照片。图10是示出根据一个实施方式的颗粒生长步骤中的反应水溶液中的第二高过饱和区域的图。图11是在第二高过饱和区域在连续式的搅拌槽内的反应水溶液中所占的体积比率为0.379%的情况下所得到的颗粒的剖面的示例的sem照片。图12是在第二高过饱和区域在连续式的搅拌槽内的反应水溶液中所占的体积比率为0.624%的情况下所得到的颗粒的剖面的示例的sem照片。具体实施方式以下,参照附图对本发明的实施方式进行说明,在各附图中,针对相同或对应的结构标记相同或对应的符号并省略说明。图1是示出用于根据一个实施方式的化学反应装置的俯视图。图2是沿图1的ii-ii线的剖面图。化学反应装置10一边向溶液中供应原料液,一边在溶液中使颗粒析出。例如,溶液包含金属盐和盐基,原料液包含金属盐,颗粒通过中和析晶而析出。在金属盐包含镍盐的情况下,颗粒是含镍氢氧化物。需要说明的是,颗粒的种类不限定于含镍氢氧化物。化学反应装置10例如具有搅拌槽20、搅拌叶轮30、搅拌轴40、以及挡板50。搅拌槽20用于在圆柱形的内部空间中容纳反应溶液。搅拌叶轮30用于对搅拌槽20内的溶液进行搅拌。搅拌叶轮30安装在搅拌轴40的下端。马达等通过使搅拌轴40旋转,使得搅拌叶轮30旋转。搅拌槽20的中心线、搅拌叶轮30的中心线以及搅拌轴40的中心线可以一致,可以为铅垂。挡板50也称为遮流板。挡板50从搅拌槽20的内周面突出,并通过遮挡旋转流而产生上升流或下降流,提高溶液的搅拌效率。本发明的发明人针对能够在各种构造的化学反应装置中普遍地提高颗粒的品质的条件进行了分析,并着眼于高过饱和区域在搅拌槽20内的溶液中所占的体积比率。高过饱和区域是指溶解于水溶液中的颗粒成分的浓度为预定值以上的区域。在高过饱和区域中,由于颗粒成分的浓度充分大于溶解度,因此颗粒成分的析出以显著的速度发生。高过饱和区域在搅拌槽20内的溶液中所占的体积比率越小,则颗粒成分的析出进行得越缓慢,因此能够提高颗粒的品质。在此,在高过饱和区域的个数为多个的情况下,高过饱和区域的体积是指体积的总和。高过饱和区域形成在原料液的排出口附近。由于该排出口设置在溶液的流场中,因此高过饱和区域的体积等受到流场的影响。流场随着搅拌叶轮30的转数、以及除此以外的搅拌叶轮30的类型或叶轮径、搅拌槽20的容积等条件而变化。以下,将对搅拌槽20内的流场产生影响的条件称为搅拌条件。搅拌槽20内的流场以及高过饱和区域的体积可以通过模拟确认。以下,主要对在连续式的搅拌槽内使硫酸镍和氢氧化钠反应而制造氢氧化镍的情况下的定常状态的流体分析进行说明。作为流体分析软件,使用ansys公司制的ansyscfxver15.0(商品名)。分析条件等如下所示。<坐标系>·对于进行流体分析的区域(以下也称为“分析区域”)之中搅拌轴或搅拌叶轮的周围,以与搅拌轴或搅拌叶轮一起进行旋转的旋转坐标系来进行处理。以旋转坐标系进行处理的区域为圆柱形,使其中心线与搅拌轴或搅拌叶轮的中心线重叠,将其直径设定为搅拌叶轮的叶轮径的115%,使其上下方向的范围为自搅拌槽的内底面至液面。·对于分析区域之中的其他区域,以静止坐标系进行处理。·使用流体分析软件的接口功能连接旋转坐标系和静止坐标系。作为接口功能,使用可选的“frozenrotor”。<湍流模型>·搅拌槽内的流动是湍流,而非层流。作为其湍流模型,使用sst(shearstresstransport:剪应力传输)模型。<化学反应>在搅拌槽内发生的化学反应的公式如下所示。niso4+2naoh→ni(oh)2+na2so4·在流体分析中,对包含以下五种成分的单相多成分的流体进行处理。1)反应成分a:niso42)反应成分b:naoh3)生成成分c:ni(oh)24)生成成分d:na2so45)水·利用涡旋消散模型来计算化学反应的速度大小。涡旋消散模型是假设当因湍流分散使反应成分a和反应成分b混合至分子程度时会发生上述化学反应的反应模型。涡旋消散模型的设置保留了流体分析软件的默认设定。<各成分的质量分数的计算方法>·在分析区域内的任意位置和任何时间点,上述五种成分的质量分数的总和为1。因此,上述五种成分中除水以外的四种成分各自的质量分数是通过cfx求解输送方程而得到的值,水的质量分数是1减去上述四种成分的质量分数总和而得到的值。<边界条件>·壁边界(无流体出入的边界)在与搅拌槽、搅拌轴、搅拌叶轮、挡板等固体的边界处,假设无滑移。另一方面,在与外部空气的边界(液面)处,假设有滑移。需要说明的是,假设液面不因搅拌而变形,并且液面为高度恒定的平面。·流入边界(流体进入的边界)在搅拌槽内的流体中,分别设置包含反应成分a的水溶液(以下称为“水溶液a”。)流入的流入边界和包含反应成分b的水溶液(以下称为“水溶液b”。)流入的流入边界。假设水溶液a的流入流量和水溶液a中反应成分a所占的比例、水溶液b的流入流量和水溶液b中反应成分b所占的比例为恒定。以将搅拌槽内的水溶液的ph值维持为预定值(例如12.0)的方式来设定水溶液b的流入流量。·流出边界(流体流出的边界)在搅拌槽的一部分内周面上,设有搅拌槽内的流体流出的流出边界。流出的液体包含生成成分c及d、未反应的反应成分a及b、以及水。以分析区域与系统外部之间的压力为零的方式来设定其流出量。需要说明的是,在溢流型的连续式的情况下,液面为流出边界。<热量条件>·假设搅拌槽内的流体的温度恒定为25℃。假设不存在因化学反应引起的热量产生、流入边界或流出边界处的热量的出入。<初始条件>·假设搅拌槽内的流体在初始状态下为均匀的流体,并且仅包含上述五种成分之中的反应成分b和水两种成分。具体来说,将搅拌槽内的流体之中的反应成分a的初始质量分数、生成成分c的初始质量分数及生成成分d的初始质量分数设定为零,并以搅拌槽内的水溶液的ph值为上述预定值的方式来设定反应成分b的初始质量分数。需要说明的是,虽然在此将生成成分c的初始质量分数及生成成分d的初始质量分数设定为零,但是为了减少用于求出定常解的迭代计算的次数(即计算时间),也可以将其设定为预测在定常状态下达到的分析区域整体的平均值。对于分析区域整体的平均值,可以根据水溶液a的流入流量和水溶液a中反应成分a所占的比例、水溶液b的流入流量和水溶液b中反应成分b所占的比例、由化学反应式表示的量化关系等来计算。<收敛判定>·对于用于求出定常解的迭代计算,进行到分析区域内的任意位置处的流动的流速分量(m/s)、压力(pa)或上述四种成分各自的质量分数各自的均方根的残差为10-4以下。<高过饱和区域的体积的计算方法>·高过饱和区域是溶解于搅拌槽内的水溶液中的生成成分c的浓度为预定值以上的区域。对于上述预定值后面将详细说明,在核生成步骤中为5.0mol/m3,在颗粒生长步骤中为1.7mol/m3。以下,将在核生成步骤中设定的高过饱和区域也称为“第一高过饱和区域”,将在颗粒生长步骤中设定的高过饱和区域也称为“第二高过饱和区域”。第一高过饱和区域的浓度的下限值高于第二高过饱和区域的浓度的下限值是因为发生核生成的下限浓度高于发生颗粒生长的下限浓度。高过饱和区域形成在水溶液a的流入边界的周围。·另外,如上所述,在流体分析中,由于将上述五种成分作为单相多成分的流体处理,因此将全部生成成分c作为液体处理。另一方面,实际上,大部分生成成分c析出成为固体,只有剩余的一部分生成成分c作为液体溶解在水溶液中。·因此,通过对利用上述流体分析所获得的生成成分c的浓度分布进行校正来计算出高过饱和区域的体积。在该校正中,以在充分远离水溶液a的流入边界的流出边界处使生成成分c的浓度与溶解度相当的方式,在搅拌槽内的所有流体中整体将生成成分c的浓度下调预定值。·需要说明的是,如果搅拌槽是间歇式而非连续式,则不存在流出边界。在此情况下,可以在浓度分布的校正中,以在搅拌槽内的水溶液的液面处使生成成分c的浓度与溶解度相当的方式,在搅拌槽内的所有流体中整体将生成成分c的浓度下调预定值。换言之,在溢流型的连续式的情况下,液面为流出边界。需要说明的是,在上述说明中示出了获得氢氧化镍情况下的分析条件,对于获得镍复合氢氧化物情况下的分析条件也可以进行同样的设定。例如,在使硫酸镍和硫酸锰与氢氧化钠反应而得到镍锰复合氢氧化物的情况下,在流体分析中,对包含以下七种成分的单相多成分的流体进行处理。1)反应成分a1:niso42)反应成分a2:mnso43)反应成分b:naoh4)生成成分c1:ni(oh)25)生成成分c2:mn(oh)26)生成成分d:na2so47)水在此,假设在搅拌槽内发生“a1+2b→c1+d”和“a2+2b→c2+d”两个化学反应,分别使用与每个化学反应对应的涡旋消散模型作为反应模型。反应成分a1和反应成分a2以均匀地溶解于水中的状态从同一流入边界被供应。即,从流入边界供应包含反应成分a1和反应成分a2两者的水溶液a。在水溶液a的流入边界周围形成高过饱和区域。高过饱和区域是指溶解于搅拌槽内的水溶液中的生成成分之中全部金属氢氧化物(在此为生成成分c1和生成成分c2)的合计的摩尔浓度为上述预定值以上的区域。在此针对将生成成分之中全部金属氢氧化物的摩尔浓度进行合计的理由进行说明。首先,如上所述,反应成分a1和反应成分a2以均匀地溶解于水中的状态从同一流入边界流入。此时,反应成分a1和反应成分a2迅速与反应成分b反应,并生成生成成分c1和生成成分c2。由此,生成成分c1和生成成分c2在生成的时间点是以充分混合的状态存在。因此,生成成分c1和生成成分c2并不是作为个别的氢氧化物析出,而是各个成分复合的氢氧化物作为固溶体析出。另外,在使硫酸镍、硫酸钴及硫酸铝,获得含有镍、钴及铝的镍复合氢氧化物的情况下,在流体分析中,对包含以下九种成分的单相多成分的流体进行处理。1)反应成分a1:niso42)反应成分a2:coso43)反应成分a3:al2(so4)34)反应成分b:naoh5)生成成分c1:ni(oh)26)生成成分c2:co(oh)27)生成成分c3:al(oh)38)生成成分d:na2so49)水在此,假设在搅拌槽内发生“a1+2b→c1+d”、“a2+2b→c2+d”及“1/2a3+3b→c3+3/2d”三个化学反应,分别使用与每个化学反应对应的涡旋消散模型作为反应模型。反应成分a1、反应成分a2及反应成分a3以均匀地溶解于水中的状态从同一流入边界被供应。即,从流入边界供应包含反应成分a1、反应成分a2及反应成分a3的水溶液a。在水溶液a的流入边界周围形成高过饱和区域。高过饱和区域是指溶解于搅拌槽内的水溶液中的生成成分之中全部金属氢氧化物(在此为生成成分c1、生成成分c2及生成成分c3)的合计的摩尔浓度为上述预定值以上的区域。以下针对将生成成分之中全部金属氢氧化物的摩尔浓度进行合计的理由进行说明。首先,如上所述,反应成分a1、反应成分a2及反应成分a3以均匀地溶解于水中的状态从同一流入边界流入。此时,反应成分a1、反应成分a2及反应成分a3迅速与反应成分b反应,并生成生成成分c1、和生成成分c2及生成成分c3。由此,生成成分c1、生成成分c2及生成成分c3在生成的时间点是以充分混合的状态存在。因此,生成成分c1、生成成分c2及生成成分c3并不是作为个别的氢氧化物析出,而是各个成分复合的氢氧化物作为固溶体析出。再有,在使硫酸镍、硫酸锰及硫酸钴获得镍钴锰复合氢氧化物的情况下,在流体分析中,对包含以下九种成分的单相多成分的流体进行处理。1)反应成分a1:niso42)反应成分a2:mnso43)反应成分a3:coso44)反应成分b:naoh5)生成成分c1:ni(oh)26)生成成分c2:mn(oh)27)生成成分c3:co(oh)28)生成成分d:na2so49)水在此,假设在搅拌槽内发生“a1+2b→c1+d”、“a2+2b→c2+d”及“1/2a3+3b→c3+3/2d”三个化学反应,分别使用与每个化学反应对应的涡旋消散模型作为反应模型。反应成分a1、反应成分a2及反应成分a3以均匀地溶解于水中的状态从同一流入边界被供应。即,从流入边界供应包含反应成分a1、反应成分a2及反应成分a3的水溶液a。在水溶液a的流入边界周围形成高过饱和区域。高过饱和区域是指溶解于搅拌槽内的水溶液中的生成成分之中全部金属氢氧化物(在此为生成成分c1、生成成分c2及生成成分c3)的合计的摩尔浓度为上述预定值以上的区域。关于将生成成分之中全部金属氢氧化物的摩尔浓度进行合计的理由,由于与在上述获得包含镍、钴及铝的镍复合氢氧化物的情况中将生成成分之中全部金属氢氧化物的摩尔浓度进行合计的理由相同,因此省略说明。水溶液a的流入边界的个数可以是多个,高过饱和区域的个数可以是多个。在高过饱和区域的个数为多个的情况下,高过饱和区域的体积是指合计的体积。含镍氢氧化物的制造方法可以具有通过模拟对高过饱和区域在搅拌槽内的水溶液中所占的体积比率进行确认的步骤。该确认可以在每次改变制造条件时进行。该制造条件的改变例如可以举出搅拌槽的容量或形状、搅拌叶轮的个数、形状、尺寸或设置位置、搅拌叶轮的转数、原料液的流量或浓度、或者用于供应原料液的喷嘴的形状、根数或配置等。例如,在搅拌槽为间歇式的情况下,在制造条件相同的期间内进行一次确认即可,无需每次都进行确认。需要说明的是,在实际的反应水溶液中,还包含氨作为化学成分。然而,氨不直接参与固体颗粒的析出反应,其浓度也比镍氢氧化物的浓度低。因此,认为氨对氢氧化镍的高过饱和区域的体积产生的影响较小。由此,将模拟模型中待求解的化学成分中的氨作为水来对待。本发明的发明人通过模拟针对能够在搅拌条件相同且向搅拌槽20内的原料液的供应流量相同情况下减小高过饱和区域的体积的手段进行了研究。结果发现,高过饱和区域的体积主要取决于(1)原料液的排出口的个数n、以及(2)在原料液的排出口附近的uk(后面将详细说明)。uk是流动的速度u(m/s)与湍流扩散系数k(m2/s)的乘积。即使搅拌条件相同,uk也会随着搅拌槽20内的位置而不同。表1示出了搅拌条件相同且向搅拌槽20内的原料液的供应流量相同情况下的原料液的排出口的个数n与高过饱和区域的体积v1、v2之间的关系。将n为多个的情况下的来自各排出口的供应流量设为n为1的情况下的来自排出口的供应流量的1/n。供应流量是每单位时间的供应量。另外,将n为多个的情况下的各排出口附近处的uk设为与n为1的情况下的排出口附近处的uk大致相同。另外,以高过饱和区域彼此不重叠的方式,对n为多个的情况下的排出口彼此的间隔进行设定。在表1中,v1表示第一高过饱和区的体积,v2表示第二高过饱和区的体积。另外,v10表示n为1时的v1的值,v20表示n为1时的v2的值。在n为多个的情况下,v1表示n个第一高过饱和区的体积总和,v2表示n个第二高过饱和区域的体积总和。[表1]n(个)124v1/v101.000.530.19v2/v201.000.520.24从表1可以清楚地看出以下趋势,原料液的排出口的个数n越大,则高过饱和区域的体积v1、v2越小。即使改变搅拌条件,也同样可以看出该趋势。另外,即使改变向搅拌槽内的原料液的供应流量,也同样可以看出该趋势。本发明的发明人发现:通过将原料液分开并将其从多个排出口供应到搅拌槽内,从而能够减小高过饱和区域的体积v1、v2。如图1所示,本实施方式的化学反应装置具有向搅拌槽20内的溶液中排出原料液的多个排出部22。在各个排出部22上分别形成一个排出口。通过将原料液分开并将其从多个排出部22供应到搅拌槽20内,从而能够减小高过饱和区域在搅拌槽20内的溶液中所占的体积v1、v2。高过饱和区域的体积比率越小,则颗粒成分的析出进行得越缓慢。因此,能够提高所得到颗粒的品质。为了充分地获得该效果,优选高过饱和区域彼此不重叠的方式来设定排出部22彼此的间隔。如果排出部22彼此靠近至高过饱和区域彼此重叠的程度,则降低了将排出部22的个数设为多个的意义。对于高过饱和区域彼此是否重叠,可以通过上述模拟来判定。为了在核生成步骤中使第一高过饱和区域彼此不重叠,排出部22彼此中心之间的间隔例如为75mm以上。为了在颗粒生长步骤中使第二高过饱和区域彼此不重叠,排出部22彼此中心之间的间隔例如为120mm以上。可以以(a)在核生成步骤中使第一高过饱和区域彼此不重叠、以及(b)在颗粒生长步骤中使第二高过饱和区域彼此不重叠中仅一者成立的方式对排出部22彼此的间隔进行设置,也可以以两者均成立的方式对排出部22彼此的间隔进行设置。对于排出部22彼此的间隔,可以在核生成步骤和颗粒生长步骤中相同,在分别进行核生成步骤和颗粒生长步骤的情况下,可以按照步骤进行改变。图3示出了根据一个实施方式的搅拌槽内的流场的uk的分布。在图3中,在图3中,菱形网状阴影区域是uk为3.0×10-3m3/s2以上的区域。通过模拟求出图3所示的分布。在该模拟中,搅拌槽20的容积为2l,搅拌叶轮30的类型为盘式涡轮叶轮,搅拌叶轮30的叶片的片数为6片,搅拌叶轮的叶轮径为80mm,搅拌叶轮30与搅拌槽20的内底面之间的上下方向距离为5mm,搅拌叶轮30的转数为850rpm。如图3所示,搅拌槽内的uk根据位置而不同,在搅拌槽20的底部21附近趋于变得特别大。需要说明的是,即使改变搅拌叶轮30的类型或叶轮径、搅拌槽20的容积等搅拌条件,也可以看出同样的趋势。表2示出了在图3的位置p1~p3任意一处设置排出口的情况下的排出口附近的uk与高过饱和区域的体积v1、v2之间的关系。来自排出口的供应流量相同,而与排出口的位置无关。在表2中,v1'表示第一高过饱和区域的体积,v2'表示第二高过饱和区域的体积。另外,uk0表示排出口的位置为p1时的uk的值,v10'表示排出口的位置为p1时的v1'的值,v20'表示排出口的位置为p1时的v2'的值。[表2]p1p2p3uk/uk01.000.770.10v1′/v10′1.002.106.80v2′/v20′1.001.204.70从表2可以清楚地看出以下趋势,排出口附近的uk越大,则高过饱和区域的体积v1'和v2'越小。即使改变搅拌条件也可以同样地看出该趋势。另外,即使改变向搅拌槽内的原料液的供给流量,也可以同样地看出该趋势。本发明的发明人发现:通过将原料液的排出口设置在搅拌槽内的uk较大的位置处,能够减小高过饱和区域的体积v1'、v2'。由于k越大则原料液越容易扩散,因此v1'或v2'越小。另外,由于u越大则溶液的量在原料液与溶液的汇合点处越相对地增加,因此原料液越容易扩散,v1'或v2'越小。因此,例如如图1及图2所示,多个排出部22可以隔出间隔地设置在搅拌槽20的底部21,并向上排出原料液。在各排出部22上形成有排出口,从各排出口向上排出原料液。由于在搅拌槽20的底部21附近uk较大,因此能够有效地减小高过饱和区域的体积。高过饱和区域的体积比率越小,则颗粒成分的析出进行得越缓慢。因此,能够提高颗粒的品质。如图1所示,在俯视图中,多个排出部22可以设在搅拌叶轮30的径向外侧。由于搅拌叶轮30因旋转而形成向着径向外侧的流动,因此uk在搅拌叶轮30的径向外侧特别大,能够更有效地减小高过饱和区域12的体积。需要说明的是,从图3也明显看出uk在搅拌叶轮30的径向外侧特别大。如图1所示,在俯视图中,多个排出部22可以设在挡板50的径向内侧。由于挡板50妨碍流动并降低流动的速度,因此uk在挡板50的径向内侧特别大,能够更有效地减小高过饱和区域12的体积。需要说明的是,从图3也明显看出uk在挡板50的径向内侧特别大。需要说明的是,虽然在图2中多个排出部22从搅拌槽20的底部21向上突出,但是也可以不突出。另外,虽然在图2中多个排出部22形成在搅拌槽20的底部21,但是例如也可以在俯视图中形成为环状的板,并设置在搅拌槽20的底部21。图4是根据一个实施方式的含镍氢氧化物的制造方法的流程图。如图4所示,含镍氢氧化物的制造方法是通过中和析晶得到含镍氢氧化物的颗粒的方法,具有生成颗粒的核的核生成步骤s11以及使颗粒生长的颗粒生长步骤s12。以下将对各步骤进行说明,在此之前,对所得到的含镍氢氧化物进行说明。(含镍氢氧化物)含镍氢氧化物被用作锂离子二次电池的正极活性物质的前驱体。含镍氢氧化物例如是(1)以物质的量之比(摩尔比)为ni:co:al=1-x-y:x:y(其中,0≤x≤0.3,0.005≤y≤0.15)的方式包含镍(ni)、钴(co)以及铝(al)的镍复合氢氧化物,或者是(2)以物质的量之比(摩尔比)为ni:co:mn:m=x:y:z:t(其中,x+y+z+t=1,0.1≤x≤0.7,0.1≤y≤0.5,0.1≤z≤0.8,0≤t≤0.02)的方式包含镍(ni)、钴(co)、锰(mn)以及m(m为选自ti、v、cr、zr、nb、mo、hf、ta以及w的一种以上的添加元素)的镍钴锰复合氢氧化物。关于根据一个实施方式的含镍氢氧化物中所包含的氢氧根离子的量,其通常具有化学计量比,但是也可以以不影响本实施方式的程度过量或不足。另外,可以以不影响本实施方式的程度以阴离子(例如碳酸根离子或硫酸根离子等)来取代一部分氢氧根离子。需要说明的是,通过x射线衍射(xrd)测量,根据一个实施方式的含镍氢氧化物为含镍氢氧化物的单相(或者主成分为含镍氢氧化物)即可。含镍氢氧化物含有镍,优选进一步含有镍以外的金属。将进一步含有镍以外的金属的氢氧化物成为镍复合氢氧化物。由于镍复合氢氧化物的金属的组成比(例如ni:co:mn:m)在所得到的正极活性物质中也被保持,因此将其调整为与正极活性物质所要求的金属的组成比一致。(含镍氢氧化物的制造方法)如上所述,含镍氢氧化物的制造方法具有核生成步骤s11以及颗粒生长步骤s12。在本实施方式中,通过使用间歇式(batch-type)搅拌槽,并对搅拌槽内的水溶液的ph值等进行控制,从而分开实施核生成步骤s11和颗粒生长步骤s12。在核生成步骤s11中,核生成较颗粒生长优先发生,几乎不发生颗粒生长。另一方面,在颗粒生长步骤s12中,颗粒生长较核生长优先发生,几乎不生成新的核。通过分开实施核生成步骤s11和颗粒生长步骤s12,能够形成粒度分布的范围较窄且均质的核,之后,能够使核均质地生长。以下,对核生成步骤s11和颗粒生长步骤s12进行说明。关于核生成步骤s11中的搅拌槽内的水溶液与颗粒生长步骤s12中的搅拌槽内的水溶液,虽然两者的ph值的范围不同,但氨浓度的范围或温度的范围可以实质上相同。需要说明的是,在本实施方式中,虽然是使用间歇式搅拌槽,但也可以使用连续式的搅拌槽。在后者的情况下,核生成步骤s11和颗粒生长步骤s12被同时实施。在该情况下,搅拌槽内的水溶液的ph值的范围理所当然变为相同,例如可以被设定为大约12.0。(核生成步骤)首先,预先调制原料液。原料液至少含有镍盐,优选进一步含有镍盐以外的金属盐。作为金属盐,使用硝酸盐、硫酸盐、盐酸盐等。更具体来说,例如使用硫酸镍、硫酸锰、硫酸钴、硫酸铝、硫酸钛、过氧钛酸铵、草酸钛钾、硫酸钒、钒酸铵、硫酸铬、铬酸钾、硫酸锆、硝酸锆、草酸铌、钼酸铵、硫酸铪、钽酸钠、钨酸钠、钨酸铵等。由于原料液的金属的组成比(例如ni:co:mn:m)在所得到的镍复合氢氧化物中也被保持,因此将其调整为与镍复合氢氧化物所要求的组成比一致。另外,在搅拌槽内贮存供给碱性水溶液、氨水溶液以及水并进行混合的水溶液。以下将混合的水溶液称为“反应前水溶液”。对于反应前水溶液的ph值,在液温25℃的基准下,预先将其调节为12.0~14.0的范围内,优选预先调节为12.3~13.5的范围内。另外,对于反应前水溶液中的氨的浓度,优选预先将其调节为3~25g/l的范围内,更优选预先将其调节为5~20g/l的范围内,进一步优选预先将其调节为5~15g/l的范围内。再有,对于反应前水溶液的温度,优选预先将其调节为20~60℃的范围内,更优选预先将其调节为35~60℃的范围内。作为碱性水溶液,例如使用包含氢氧化钠、氢氧化钾等碱金属氢氧化物的水溶液。虽然碱金属氢氧化物可以作为固体提供,但优选作为水溶液提供。作为氨水溶液,使用包含氨提供体的水溶液。作为氨提供体,例如可以使用氨、硫酸铵、氯化铵、碳酸铵、或氟化铵等。需要说明的是,在本实施方式中,作为非还原性络合剂,虽然是使用氨提供体,但也可以使用乙二胺四乙酸、次氮基三乙酸、尿嘧啶二乙酸、或甘氨酸等。非还原性络合剂只要是能够在搅拌槽内的水溶液中与镍离子等进行键合而形成络合物者即可。在对反应前水溶液的ph值、氨浓度、温度等进行调节后,一边对反应前水溶液进行搅拌一边向搅拌槽内供应原料液。由此,在搅拌槽内,形成混合了反应前水溶液和原料液的反应水溶液,通过中和析晶而生成核,开始进行核生成步骤s11。在核生成步骤s11中,如果反应水溶液的ph值为12.0以上,则核生成较颗粒生长更占优势。另外,在核生成步骤s11中,如果反应水溶液的ph值为14.0以下,则能够防止核过度细小化,能够防止反应水溶液的凝胶化。在核生成步骤s11中,反应水溶液的ph值的变动幅度(最大值与最小值之间的幅度)优选为0.4以下。另外,在核生成步骤s11中,如果反应水溶液中的氨浓度为3g/l以上,则能够将金属离子的溶解度保持恒定,易于生成形状和粒径整齐的核。在核生成步骤s11中,如果反应水溶液中的氨浓度为25g/l以下,则未析出而残留在溶液中的金属离子会减少,生产效率得到提高。在核生成步骤s11中,反应水溶液的ph值的变动幅度(最大值与最小值之间的幅度)优选为5g/l以下。另外,在核生成步骤s11中,如果反应水溶液的温度为20℃以上,则含镍氢氧化物的溶解度较大,核产生缓慢进行,容易对核产生进行控制。另一方面,如果反应水溶液的温度为60℃以下,则能够抑制氨的挥发,因此能够减少氨水的使用量,能够降低制造成本。在核生成步骤s11中,以将反应水溶液的ph值、氨浓度及温度维持在上述范围内的方式,向搅拌槽内供应原料液、以及除原料液以外的碱性水溶液、氨水溶液。由此,在反应水溶液中核的生成持续进行。并且,当生成预定量的核时,结束核生成步骤s11。对于是否生成了预定量的核,可以根据金属盐的供应量来估计。(颗粒生长步骤)在核生成步骤s11结束后、颗粒生长步骤s12开始前,在液温25℃的基准下,将搅拌槽内的反应水溶液的ph值调整为10.5~12.0、优选调整为11.0~12.0,并且低于核生成步骤s11中的ph值。对于该ph值的调整,可以通过停止向搅拌槽内供应碱性水溶液、向搅拌槽内供应以氢来取代金属盐的金属的无机酸(例如硫酸盐的情况下为硫酸)等来进行调整。在对反应水溶液的ph值、氨浓度、温度等进行调节后,一边对反应水溶液进行搅拌一边向搅拌槽内供应原料液。由此,通过中和析晶使核的生长(颗粒生长)开始进行,开始进行颗粒生长步骤s12。需要说明的是,在本实施方式中,对于核生成步骤s11和颗粒生长步骤s12,可以在相同的搅拌槽中进行,也可以在不同的搅拌槽中进行。在颗粒生长步骤s12中,如果反应水溶液的ph值为12.0以下且低于核生成步骤s11中的ph值,则几乎不会生成新的核,与核生成相比颗粒生长优先发生。需要说明的是,在ph值为12.0的情况下,由于其为核生成与颗粒生长之间的边界条件,因此优先级会根据反应水溶液中是否存在核而改变。例如,如果在使核生成步骤s11的ph值高于12.0并生成大量的核后,在颗粒生长步骤s12中将ph值设为12.0,则由于在反应水溶液中存在大量的核,因此颗粒生长优先。另一方面,当在反应水溶液中不存在核的状态下,即在核生成步骤s11中将ph值设为12.0时,由于不存在用于生长的核,因此核生成优先。之后,如果在颗粒生长步骤s12中使ph值小于12.0,则所生成的核生长。为了清楚地分离核生成与颗粒生长,优选使颗粒生长步骤的ph值低于核生成步骤的ph值0.5以上,更优选使颗粒生长步骤的ph值低于核生成步骤的ph值1.0以上。另外,在颗粒生长步骤s12中,如果反应水溶液的ph值为10.5以上,则由氨所带来的溶解度较低,因此未析出而残留在溶液中的金属离子会减少,生产效率得到提高。在颗粒生长步骤s12中,以将反应水溶液的ph值、氨浓度及温度维持在上述范围内的方式,向搅拌槽内供应原料液、以及除原料液以外的碱性水溶液、氨水溶液。由此,在反应水溶液中,颗粒生长持续进行。颗粒生长步骤s12通过切换搅拌槽内的气氛从而能够分成前半部分和后半部分。前半部分的气氛是与核生成步骤s11同样的氧化性气氛。氧化性气氛中的氧浓度为1容量%以上,优选为2容量%以上,更优选为10容量%以上。氧化性气氛可以是易于控制的大气气氛(氧气浓度:21容量%)。虽然对于氧化性气氛的氧浓度的上限并无特别限定,但其为30容量%以下。另一方面,后半部分的气氛是非氧化性气氛。非氧化性气氛中的氧浓度为1容量%以下,优选为0.5容量%以下,更优选为0.3容量%以下。通过混合氧气或空气与惰性气体来控制非氧化性气氛的氧浓度。图5是在根据一个实施方式的颗粒生长步骤的前半部分中所形成的凝集体的示意性的剖面图。图6是在根据一个实施方式的颗粒生长步骤的后半部分中所形成的外壳的示意性的剖面图。在颗粒生长步骤s12的前半部分中,通过核生长而形成晶种颗粒2,当晶种颗粒2增大到一定程度时,晶种颗粒2彼此碰撞,形成由多个晶种颗粒2构成的凝集体4。另一方面,在颗粒生长步骤s12的后半部分中,在凝集体4周围形成致密的外壳6。由此,获得由凝集体4和外壳6构成的颗粒。需要说明的是,含镍氢氧化物的颗粒的构造并不限于图6所示的构造。例如,在同时实施核生成步骤s11和颗粒生长步骤s12的情况下,在中和析晶完成时所得到的颗粒为与图6所示的构造不同的构造。该构造例如是相当于晶种颗粒2的部分与相当于外壳6的部分混合在一起,难以明确其边界的均等的构造。在含镍氢氧化物的颗粒生长到预定的粒径的时间点,结束颗粒生长步骤s12。可以根据核生成步骤s11和颗粒生长步骤s12各自中的金属盐的供应量来估计其粒径。需要说明的是,可以在核生成步骤s11结束后、颗粒生长步骤s12的中途,停止原料液等的供应并停止反应水溶液的搅拌,使颗粒沉淀,排出上清液。由此,能够提高因中和析晶而降低的反应水溶液中的金属离子浓度。图7是示出根据一个实施方式的核生成步骤中的反应水溶液中的第一高过饱和区域的图。在图7中,箭头方向表示排出部22附近处的流动的方向。第一高过饱和区域12a是指溶解于反应水溶液中的含镍氢氧化物的摩尔浓度为5.0mol/m3以上的区域。在第一高过饱和区域12a中,由于含镍氢氧化物的摩尔浓度充分大于溶解度,因此核生成以显著的速度发生。在此,溶解度是指溶解于100g水中的含镍氢氧化物的极限量(g/100g-h2o)。氢氧化镍(ni(oh)2)的溶解度例如为10-7(g/100g-h2o)。这样一来,由于含镍氢氧化物的溶解度接近于零,因此与第一高过饱和区域12a的摩尔浓度的下限值5.0mol/m3相比小得可以忽略不计。图8是在第一高过饱和区域在连续式的搅拌槽内的反应水溶液中所占的体积比率为0.025%的情况下、即在实施例1-1的情况下所得到的颗粒的示例的sem照片。图8所示的颗粒的外表面光滑,几乎未发现凹凸不平。另一方面,图9是在第一高过饱和区域在连续式的搅拌槽内的反应水溶液中所占的体积比率为0.100%的情况下、即在比较例1-1的情况下所得到的颗粒的示例的sem照片。在图9所示的颗粒的外表面发现了明显的凹凸不平。从图8及图9可以看出,从对在中和析晶完成时所得到的颗粒的外表面的凹凸不平的发生进行抑制的观点来看,优选第一高过饱和区域在核生成步骤s11中的反应水溶液中所占的体积比率(以下称为第一体积比率)小于0.100%。关于如果第一体积比率小于0.100%则能够对在中和析晶完成时所得到的颗粒的外表面的凹凸不平的发生进行抑制的理由,作以下推断。在核生成步骤s11中,核主要在第一高过饱和区域12a中生成,之后分散在整个反应水溶液中。如果第一体积比率小于0.100%,则反应水溶液的每单位体积的核的产生数量较少。因此,在颗粒生长步骤s12的前半部分中,反应水溶液的每单位体积的晶种颗粒2的数量也较少,由多个晶种颗粒2构成的凝集体4的数量也较少。因此,在颗粒生长步骤s12的后半部分中,在凝集体4周围形成的外壳6的厚度变厚。外壳6的厚度变厚的原因在于:在作为外壳6的生长的起点的凝集体4的数量较多的情况与较少的情况下,相对于各个凝集体4的用于形成外壳6的材料的供应比率不同。与凝集体4的数量较多的情况相比,在凝集体4的数量较少的情况下,相对于各个凝集体4的用于形成外壳6的材料的供应比率较高。因此,在凝集体4的数量较少的情况下,能够使各个凝集体4的外壳6变厚。由此,通过使第一体积比率小于0.100%,并抑制核的产生数量,从而能够以较厚的外壳6来覆盖凝集体4的外表面,能够降低最终所获得的颗粒的外表面的凹凸不平。需要说明的是,在同时进行核生成步骤s11和颗粒生长步骤s12的情况下也能够获得该效果。从降低在中和析晶完成时所得到的颗粒的外表面的凹凸不平的观点来看,优选第一体积比率越小越好。第一体积比率取决于排出部34附近的流场的u或k等。u或k越大,则第一体积比率越小。第一体积比率优选为0.070%以下,更优选为0.050%以下,进一步优选为0.030%以下。但是,由于u或k受到用于使搅拌轴40旋转的马达的容量等的制约,因此第一体积比率优选为0.004%以上。在核生成步骤s11中,可以将原料液分开并将其从多个排出部22排出到反应水溶液中。由此,能够有效地减小第一体积比率。此时,优选以由多个排出部22所排出的多个第一高过饱和区域12a不重叠的方式,对多个排出部22的间隔进行设定。图10是示出根据一个实施方式的颗粒生长步骤中的反应水溶液中的第二高过饱和区域的图。在图7中,箭头方向表示排出部22附近处的流动的方向。第二高过饱和区域12b是指溶解于反应水溶液中的含镍氢氧化物的摩尔浓度为1.7mol/m3以上的区域。在第二高过饱和区域12b中,由于含镍氢氧化物的摩尔浓度充分大于溶解度,因此颗粒生长以显著的速度发生。需要说明的是,如上所述,由于含镍氢氧化物的溶解度接近于零,因此与第二高过饱和区域12b的摩尔浓度的下限值1.7mol/m3相比小得可以忽略不计。图11是在第二高过饱和区域在连续式的搅拌槽内的反应水溶液中所占的体积比率为0.379%的情况下、即在实施例2-1的情况下所得到的颗粒的剖面的示例的sem照片。在图11所示的颗粒的剖面上未确认出年轮状的构造。另一方面,图12是在第二高过饱和区域在连续式的搅拌槽内的反应水溶液中所占的体积比率为0.624%的情况下、即在比较例2-1的情况下所得到的颗粒的剖面的示例的sem照片。在图12所示的颗粒的剖面上在箭头所示的地方确认出年轮状的构造。从图11及图12可以看出,从对年轮装的构造的发生进行抑制的观点来看,优选第二高过饱和区域12b在反应水溶液中所占的体积比率(以下称为第二体积比率)小于0.624%。关于如果第二体积比率小于0.624%则能够对年轮状的构造的发生进行抑制的理由,作以下推断。在颗粒生长步骤s12中,颗粒分散在整个反应水溶液中,并且主要在通过第二高过饱和区域12b时生长。如果第二高过饱和区域12b在整个反应水溶液中所占的体积比率小于0.624%,则颗粒生长缓慢发生,能够对由密度不同的多个层所构成的年轮状的构造的发生进行抑制。推测其原因是:通过使颗粒生长缓慢发生,从而能够对晶体生长方位的变化或因该变化所引起的空隙的产生等进行抑制。从对年轮状的构造的发生进行抑制的观点来看,优选第二体积比率越小越好。第二体积比率取决于排出部34附近的流场的u或k等。u或k越大,则第二体积比率越小。第二体积比率优选为0.600%以下,更优选为0.500%以下,进一步优选为0.400%以下。但是,由于u或k受到用于使搅拌轴40旋转的马达的容量等的制约,因此第二体积比率优选为0.019%以上。在颗粒生长步骤s12中,可以将原料液分开并将其从多个排出部22排出到反应水溶液中。由此,能够有效地减小第二体积比率。此时,优选以由多个排出部22所排出的多个第二高过饱和区域12b不重叠的方式,对多个排出部22的间隔进行设定。实施例[实施例1-1]在实施例1-1中,使用溢流型连续式的搅拌槽,通过中和析晶,同时进行生成镍复合氢氧化物的颗粒的核的核生成步骤和使颗粒生长的颗粒生长步骤。搅拌槽的容积为200l,搅拌叶轮的类型为盘式涡轮叶轮,搅拌叶轮的叶片的片数为6片,搅拌叶轮的叶轮径为250mm,搅拌叶轮与搅拌槽的内底面之间的上下方向距离为140mm,搅拌叶轮的转数为280rpm。搅拌槽内的反应水溶液的液量为200l,反应水溶液的ph值为11.3,反应水溶液的氨浓度为12g/l,反应水溶液的温度维持在50℃。反应水溶液的周围气氛为大气气氛。以可得到ni0.82co0.15al0.03(oh)2作为镍复合氢氧化物的方式调制原料液。原料液供给管的根数为1根,来自1根原料液供给管的供应量为400ml/分钟。在核生成步骤或颗粒生长步骤期间,向搅拌槽内供应原料液、以及除此之外的氢氧化钠水溶液及氨水,并维持反应水溶液的ph值和反应水溶液的氨浓度。通过模拟所计算出的第一高过饱和区域在反应水溶液中所占的体积比率为0.025%。需要说明的是,对分析条件的设定与上述分析条件同样。图8示出了在实施例1-1中所得到的镍复合氢氧化物的颗粒的sem照片。如图8所示,在中和析晶完成时所得到的颗粒的外表面光滑,几乎未发现凹凸不平。[实施例1-2]在实施例1-2中,除了将实施例1-1中的搅拌叶轮的转数为150rpm以外,与实施例1-1同样地制造镍复合氢氧化物的颗粒。与实施例1-1同样地通过模拟所计算出的第一高过饱和区域在反应水溶液中所占的体积比率为0.090%。需要说明的是,对分析条件的设定与上述分析条件同样。关于在实施例1-2中得到的镍复合氢氧化物的颗粒,也与图8所示的实施例1-1的颗粒同样,在中和析晶完成时所得到的颗粒的外表面光滑,几乎未发现凹凸不平。[实施例1-3]在实施例1-3中,除了以可得到ni0.88co0.09al0.03(oh)2作为镍复合氢氧化物的方式调整原料液以外,与实施例1-1同样地制造镍复合氢氧化物的颗粒。与实施例1-1同样地通过模拟所计算出的第一高过饱和区域在反应水溶液中所占的体积比率为0.025%。需要说明的是,对分析条件的设定与上述分析条件同样。关于在实施例1-3中得到的镍复合氢氧化物的颗粒,也与图8所示的实施例1-1的颗粒同样,在中和析晶完成时所得到的颗粒的外表面光滑,几乎未发现凹凸不平。[实施例1-4]在实施例1-4中,搅拌槽的容积为60l,搅拌叶轮的类型为盘式涡轮叶轮,搅拌叶轮的叶片的片数为6片,搅拌叶轮的叶轮径为168mm,搅拌叶轮与搅拌槽的内底面之间的上下方向距离为100mm,搅拌叶轮的转数为425rpm。搅拌槽内的反应水溶液的液量为60l。以可得到ni0.82co0.15al0.03(oh)2作为镍复合氢氧化物的方式调制原料液。原料液供给管的根数为1根,来自1根原料液供给管的供应量为120ml/分钟。除此以外,与实施例1-1同样地制造镍复合氢氧化物的颗粒。与实施例1-1同样地通过模拟所计算出的第一高过饱和区域在反应水溶液中所占的体积比率为0.015%。需要说明的是,对分析条件的设定与上述分析条件同样。关于在实施例1-4中得到的镍复合氢氧化物的颗粒,也与图8所示的实施例1-1的颗粒同样,在中和析晶完成时所得到的颗粒的外表面光滑,几乎未发现凹凸不平。[实施例1-5]在实施例1-5中,搅拌槽的容积为60l,搅拌叶轮的类型为45°倾斜浆叶轮、搅拌叶轮的叶片的片数为4片、搅拌叶轮的叶轮径为168mm、搅拌叶轮与搅拌槽的内底面之间的上下方向距离为100mm、搅拌叶轮的转数为500rpm。另外,搅拌槽内的反应水溶液的液量为60l。以可得到ni0.82co0.15al0.03(oh)2作为镍复合氢氧化物的方式调制原料液。原料液供给管的根数为1根,来自1根原料液供给管的供应量为120ml/分钟。除此以外,与实施例1-1同样地制造镍复合氢氧化物的颗粒。与实施例1-1同样地通过模拟所计算出的第一高过饱和区域在反应水溶液中所占的体积比率为0.027%。需要说明的是,对分析条件的设定与上述分析条件同样。关于在实施例1-5中得到的镍复合氢氧化物的颗粒,也与图8所示的实施例1-1的颗粒同样,在中和析晶完成时所得到的颗粒的外表面光滑,几乎未发现凹凸不平。[实施例1-6]在实施例1-6中,除了以可得到ni0.34co0.33mn0.33(oh)2作为镍复合氢氧化物的方式调制原料液以外,与实施例1-1同样地制造镍复合氢氧化物的颗粒。与实施例1-1同样地通过模拟所计算出的第一高过饱和区域在反应水溶液中所占的体积比率为0.025%。需要说明的是,对分析条件的设定与上述分析条件同样。关于在实施例1-6中得到的镍复合氢氧化物的颗粒,也与图8所示的实施例1-1的颗粒同样,在中和析晶完成时所得到的颗粒的外表面光滑,几乎未发现凹凸不平。[实施例1-7]在实施例1-7中,除了以可得到ni0.60co0.20mn0.20(oh)2作为镍复合氢氧化物的方式调制原料液以外,与实施例1-1同样地制造镍复合氢氧化物的颗粒。与实施例1-1同样地通过模拟所计算出的第一高过饱和区域在反应水溶液中所占的体积比率为0.025%。需要说明的是,对分析条件的设定与上述分析条件同样。关于在实施例1-7中得到的镍复合氢氧化物的颗粒,也与图8所示的实施例1-1的颗粒同样,在中和析晶完成时所得到的颗粒的外表面光滑,几乎未发现凹凸不平。[实施例1-8]在实施例1-8中,搅拌槽的容积为60l,搅拌叶轮的类型为盘式涡轮叶轮,搅拌叶轮的叶片的片数为6片,搅拌叶轮的叶轮径为168mm,搅拌叶轮与搅拌槽的内底面之间的上下方向距离为100mm,搅拌叶轮的转数为425rpm。搅拌槽内的反应水溶液的液量为60l。以可得到ni0.34co0.33mn0.33(oh)2作为镍复合氢氧化物的方式调制原料液。原料液供给管的根数为1根,来自1根原料液供给管的供应量为120ml/分钟。除此以外,与实施例1-1同样地制造镍复合氢氧化物的颗粒。与实施例1-1同样地通过模拟所计算出的第一高过饱和区域在反应水溶液中所占的体积比率为0.015%。需要说明的是,对分析条件的设定与上述分析条件同样。关于在实施例1-8中得到的镍复合氢氧化物的颗粒,也与图8所示的实施例1-1的颗粒同样,在中和析晶完成时所得到的颗粒的外表面光滑,几乎未发现凹凸不平。[实施例1-9]在实施例1-9中,搅拌槽的容积为60l,搅拌叶轮的类型为45°倾斜浆叶轮、搅拌叶轮的叶片的片数为4片、搅拌叶轮的叶轮径为168mm、搅拌叶轮与搅拌槽的内底面之间的上下方向距离为100mm、搅拌叶轮的转数为500rpm。另外,搅拌槽内的反应水溶液的液量为60l。以可得到ni0.34co0.33mn0.33(oh)2作为镍复合氢氧化物的方式调制原料液。原料液供给管的根数为1根,来自1根原料液供给管的供应量为120ml/分钟。除此以外,与实施例1-1同样地制造镍复合氢氧化物的颗粒。与实施例1-1同样地通过模拟所计算出的第一高过饱和区域在反应水溶液中所占的体积比率为0.027%。需要说明的是,对分析条件的设定与上述分析条件同样。关于在实施例1-9中得到的镍复合氢氧化物的颗粒,也与图8所示的实施例1-1的颗粒同样,在中和析晶完成时所得到的颗粒的外表面光滑,几乎未发现凹凸不平。[比较例1-1]在比较例1-1中,除了将来自1根原料液供给管的供应量为800ml/分钟以外,与实施例1-1同样地制造镍复合氢氧化物的颗粒。与实施例1-1同样地通过模拟所计算出的第一高过饱和区域在反应水溶液中所占的体积比率为0.100%。图9示出了在比较例1中所得到的镍复合氢氧化物的颗粒的sem照片。如图9的箭头所示,在中和析晶完成时所得到的颗粒的外表面发现了明显的凹凸不平。[比较例1-2]在比较例1-2中,除了以可得到ni0.34co0.33mn0.33(oh)2作为镍复合氢氧化物的方式调制原料液,将来自1根原料液供给管的供应量为800ml/分钟以外,与实施例1-1同样地制造镍复合氢氧化物的颗粒。与实施例1-1同样地通过模拟所计算出的第一高过饱和区域在反应水溶液中所占的体积比率为0.100%。关于在比较例1-2中得到的镍复合氢氧化物的颗粒,也与图9所示的比较例1的颗粒同样,在中和析晶完成时所得到的颗粒的外表面发现了明显的凹凸不平。[总结]根据实施例1-1~1-9和比较例1-1及1-2可以看出,如果第一高过饱和区域在反应水溶液中所占的体积比率小于0.100%,则即使搅拌叶轮的类型或叶轮径、搅拌槽的容积改变,也能够降低颗粒外表面的凹凸不平。[实施例2-1]在实施例2-1中,使用溢流型连续式的搅拌槽,通过中和析晶,同时进行生成镍复合氢氧化物的颗粒的核的核生成步骤和使颗粒生长的颗粒生长步骤。搅拌槽的容积为200l,搅拌叶轮的类型为盘式涡轮叶轮,搅拌叶轮的叶片的片数为6片,搅拌叶轮的叶轮径为250mm,搅拌叶轮与搅拌槽的内底面之间的上下方向距离为140mm,搅拌叶轮的转数为280rpm。搅拌槽内的反应水溶液的液量为200l,反应水溶液的ph值为11.8,反应水溶液的氨浓度为12g/l,反应水溶液的温度维持在50℃。反应水溶液的周围气氛为氮气气氛。以可得到ni0.82co0.15al0.03(oh)2作为镍复合氢氧化物的方式调制原料液,各个金属离子浓度的合计为2.0mol/l。原料液供给管的根数为2根,来自各原料液供给管的供应量为400ml/分钟,来自2根原料液供给管的合计供应量为800ml/分钟。在核生成步骤或颗粒生长步骤期间,向搅拌槽内供应原料液、以及除此之外的氢氧化钠水溶液及氨水,并维持反应水溶液的ph值和反应水溶液的氨浓度。通过模拟所计算出的第二高过饱和区域在反应水溶液中所占的体积比率为0.379%。需要说明的是,对分析条件的设定与上述分析条件同样。图11示出了在实施例2-1中所得到的镍复合氢氧化物的颗粒的剖面的sem照片。如图11所示,在颗粒的剖面上未确认出年轮状的构造。需要说明的是,所得到的镍复合氢氧化物的振实密度(tapdensity)为1.40g/cc。[实施例2-2]在实施例2-2中,除了将原料液供给管的根数设为1根,将来自1根原料液供给管的供应量设为400ml/分钟以外,与实施例2-1同样地制造镍复合氢氧化物的颗粒。与实施例2-1同样地通过模拟所计算出的第二高过饱和区域在反应水溶液中所占的体积比率为0.190%。根据所得到的镍复合氢氧化物的颗粒的剖面的sem照片,在颗粒的剖面上未确认出年轮状的构造。[实施例2-3]在实施例2-3中,除了将搅拌槽的容积设为60l、将搅拌叶轮的叶轮径为160mm、将搅拌叶轮与搅拌槽的内底面之间的上下方向距离设为60mm、将搅拌叶轮的转数为375rpm、将原料液供给管的根数设为1根,将来自1根原料液供给管的供应量设为97ml/分钟以外,与实施例2-1同样地制造镍复合氢氧化物的颗粒。与实施例2-1同样地通过模拟所计算出的第二高过饱和区域在反应水溶液中所占的体积比率为0.100%。根据所得到的镍复合氢氧化物的颗粒的剖面的sem照片,在颗粒的剖面上未确认出年轮状的构造。[实施例2-4]在实施例2-4中,除了将搅拌叶轮的转数为325rpm以外,与实施例2-3同样地制造镍复合氢氧化物的颗粒。与实施例2-1同样地通过模拟所计算出的第二高过饱和区域在反应水溶液中所占的体积比率为0.134%。根据所得到的镍复合氢氧化物的颗粒的剖面的sem照片,在颗粒的剖面上未确认出年轮状的构造。[实施例2-5]在实施例2-5中,除了以可得到ni0.88co0.09al0.03(oh)2作为镍复合氢氧化物的方式调制原料液以外,与实施例2-1同样地制造镍复合氢氧化物的颗粒。与实施例2-1同样地通过模拟所计算出的第二高过饱和区域在反应水溶液中所占的体积比率为0.379%。根据所得到的镍复合氢氧化物的颗粒的剖面的sem照片,在颗粒的剖面上未确认出年轮状的构造。[实施例2-6]在实施例2-6中,除了将搅拌叶轮的转数为220rpm以外,与实施例2-1同样地制造镍复合氢氧化物的颗粒。与实施例2-1同样地通过模拟所计算出的第二高过饱和区域在反应水溶液中所占的体积比率为0.600%。需要说明的是,对分析条件的设定与上述分析条件同样。根据所得到的镍复合氢氧化物的颗粒的剖面的sem照片,在颗粒的剖面上未确认出年轮状的构造。[实施例2-7]在实施例2-7中,搅拌槽的容积为60l,搅拌叶轮的类型为45°倾斜浆叶轮、搅拌叶轮的叶片的片数为4片、搅拌叶轮的叶轮径为168mm、搅拌叶轮与搅拌槽的内底面之间的上下方向距离为100mm、搅拌叶轮的转数为400rpm。另外,搅拌槽内的反应水溶液的液量为60l。除此以外,与实施例2-3同样地制造镍复合氢氧化物的颗粒。与实施例2-1同样地通过模拟所计算出的第二高过饱和区域在反应水溶液中所占的体积比率为0.205%。需要说明的是,对分析条件的设定与上述分析条件同样。[实施例2-8]在实施例2-8中,除了以可得到ni0.34co0.33mn0.33(oh)2作为镍复合氢氧化物的方式调制原料液以外,与实施例2-1同样地制造镍复合氢氧化物的颗粒。与实施例2-1同样地通过模拟所计算出的第二高过饱和区域在反应水溶液中所占的体积比率为0.379%。需要说明的是,对分析条件的设定与上述分析条件同样。关于在实施例2-8中得到的镍复合氢氧化物的颗粒,也与图11所示的实施例2-1的颗粒同样,在颗粒的剖面上未确认出年轮状的构造。需要说明的是,所得到的镍复合氢氧化物的振实密度为1.40g/cc。[实施例2-9]在实施例2-9中,除了以可得到ni0.60co0.20mn0.20(oh)2作为镍复合氢氧化物的方式调制原料液以外,与实施例2-1同样地制造镍复合氢氧化物的颗粒。与实施例2-1同样地通过模拟所计算出的第二高过饱和区域在反应水溶液中所占的体积比率为0.379%。需要说明的是,对分析条件的设定与上述分析条件同样。关于在实施例2-9中得到的镍复合氢氧化物的颗粒,也与图11所示的实施例2-1的颗粒同样,在颗粒的剖面上未确认出年轮状的构造。需要说明的是,所得到的镍复合氢氧化物的振实密度为1.40g/cc。[实施例2-10]在实施例2-10中,搅拌槽的容积为60l,搅拌叶轮的类型为盘式涡轮叶轮,搅拌叶轮的叶片的片数为6片,搅拌叶轮的叶轮径为168mm,搅拌叶轮与搅拌槽的内底面之间的上下方向距离为60mm,搅拌叶轮的转数为375rpm。另外,搅拌槽内的反应水溶液的液量为60l。以可得到ni0.34co0.33mn0.33(oh)2作为镍复合氢氧化物的方式调制原料液。原料液供给管的根数为1根,来自1根原料液供给管的供应量为97ml/分钟。除此以外,与实施例2-1同样地制造镍复合氢氧化物的颗粒。与实施例2-1同样地通过模拟所计算出的第二高过饱和区域在反应水溶液中所占的体积比率为0.100%。需要说明的是,对分析条件的设定与上述分析条件同样。关于在实施例2-10中得到的镍复合氢氧化物的颗粒,也与图11所示的实施例2-1的颗粒同样,在中和析晶完成时所得到的颗粒的剖面上未确认出年轮状的构造。[实施例2-11]在实施例2-11中,搅拌槽的容积为60l,搅拌叶轮的类型为45°倾斜浆叶轮、搅拌叶轮的叶片的片数为4片、搅拌叶轮的叶轮径为168mm、搅拌叶轮与搅拌槽的内底面之间的上下方向距离为100mm、搅拌叶轮的转数为400rpm。另外,搅拌槽内的反应水溶液的液量为60l。以可得到ni0.34co0.33mn0.33(oh)2作为镍复合氢氧化物的方式调制原料液。原料液供给管的根数为1根,来自1根原料液供给管的供应量为97ml/分钟。除此以外,与实施例2-3同样地制造镍复合氢氧化物的颗粒。与实施例2-1同样地通过模拟所计算出的第二高过饱和区域在反应水溶液中所占的体积比率为0.205%。需要说明的是,对分析条件的设定与上述分析条件同样。关于在实施例2-11中得到的镍复合氢氧化物的颗粒,也与图11所示的实施例2-1的颗粒同样,在中和析晶完成时所得到的颗粒的剖面上未确认出年轮状的构造。[比较例2-1]在比较例2-1中,除了将原料液供给管的根数设为1根,将来自1根原料液供给管的供应量为800ml/分钟以外,与实施例2-1同样地制造镍复合氢氧化物的颗粒。与实施例2-1同样地通过模拟所计算出的第二高过饱和区域在反应水溶液中所占的体积比率为0.624%。图12示出了在比较例2-1中所得到的镍复合氢氧化物的颗粒的剖面的sem照片。如图12的箭头所示,在颗粒的剖面上确认出年轮状的构造。需要说明的是,所得到的镍复合氢氧化物的振实密度为1.24g/cc。[比较例2-2]在比较例2-2中,除了以可得到ni0.34co0.33mn0.33(oh)2作为镍复合氢氧化物的方式调制原料液,将来自1根原料液供给管的供应量为800ml/分钟以外,与实施例2-1同样地制造镍复合氢氧化物的颗粒。与实施例2-1同样地通过模拟所计算出的第二高过饱和区域在反应水溶液中所占的体积比率为0.624%。关于在比较例2-2中得到的镍复合氢氧化物的颗粒,也与图12所示的比较例1的颗粒同样,在颗粒的剖面上确认出年轮状的构造。需要说明的是,所得到的镍复合氢氧化物的振实密度为1.21g/cc。[总结]根据实施例2-1~2-11和比较例2-1及2-2可以看出,如果第二高过饱和区域在反应水溶液中所占的体积比率小于0.624%,则即使搅拌叶轮的类型或叶轮径、搅拌槽的容积改变,也能够对在颗粒的剖面中发生年轮状的构造进行抑制。推测其原因是颗粒生长缓慢发生。以上对化学反应装置的实施方式等进行了说明,但本发明并不限定于上述实施方式等。可以在权利要求书所记载的本发明的主旨的范围内进行各种变形、改进。本申请以2016年6月14日向日本专利局申请的日本专利申请第2016-118373号作为要求优先权的基础,本申请援引日本专利申请第2016-118373号的全部内容。符号说明2晶种颗粒4凝集体6外壳10化学反应装置12高过饱和区域20搅拌槽21底部22排出部30搅拌叶轮40搅拌轴50挡板60原料液供给管61排出部。权利要求书(按照条约第19条的修改)1.(修改后)一种化学反应装置,其一边向溶液中供应原料液,一边在所述溶液中使颗粒析出,所述化学反应装置具有容纳所述溶液的搅拌槽、对所述溶液进行搅拌的搅拌叶轮、以及从所述搅拌槽的内周面突出的挡板,所述化学反应装置具有向所述溶液中排出所述原料液的多个排出部。在俯视图中,多个所述排出部布置在所述挡板的径向内侧。2.根据权利要求1所述的化学反应装置,其中,多个所述排出部隔出间隔地设置在所述搅拌槽的底部,并向上排出所述原料液。3.根据权利要求2所述的化学反应装置,其中,在俯视图中,多个所述排出部布置在所述搅拌叶轮的径向外侧。4.(删除)5.(修改后)根据权利要求1至3中任一项所述的化学反应装置,其中,所述溶液是水溶液,所述原料液包含镍盐,所述颗粒是含镍氢氧化物,在所述排出部附近,形成有溶解于所述水溶液的所述含镍氢氧化物在所述水溶液中所占的摩尔浓度为5.0mol/m3以上的第一高过饱和区域,以在多个所述排出部附近所形成的多个所述第一高过饱和区域不重叠的方式,设定多个所述排出部的间隔。6.(修改后)根据权利要求1至3、或5中任一项所述的化学反应装置,其中,所述溶液是水溶液,所述原料液包含镍盐,所述颗粒是含镍氢氧化物,在所述排出部附近,形成有溶解于所述水溶液的所述含镍氢氧化物在所述水溶液中所占的摩尔浓度为1.7mol/m3以上的第二高过饱和区域,以在多个所述排出部附近所形成的多个所述第二高过饱和区域不重叠的方式,设定多个所述排出部的间隔。7.(修改后)一种颗粒的制造方法,使用根据权利要求1至3、5、或6中任一项所述的化学反应装置,一边向所述溶液中供应所述原料液,一边在所述溶液中使颗粒析出。说明或声明(按照条约第19条的修改)1.修改的内容(1)以权利要求4为权利要求1,将引用形式改变为独立形式。(2)删除权利要求4。(3)对权利要求5~7的引用权利要求序号进行修改。2.说明在权利要求1中,明确了用于排出原料液的排出部在俯视图中布置在挡板的径向内侧(参见段落[0070]、图1、以及图2)。本申请发明通过如上所述布置排出部,从而获得了uk特别大、能够更有效地减小高过饱和区域的体积的效果。文献中均未记载在俯视图中将用于供应原料液的供给口布置在挡板的径向内侧。当前第1页12