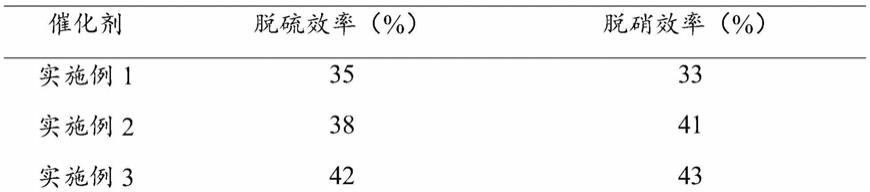
1.本发明涉及烟气脱硫脱硝治理技术领域,尤其涉及一种脱硫脱硝催化剂及其制备方法和再生方法。
背景技术:2.煤炭、石油等化石燃料的大量消耗,在促进经济快速发展的同时,所带来的大气污染问题也日益严重,二氧化硫、氮氧化物排放量呈上升趋势。据统计,2015年二氧化硫和氮氧化物排放超过3900万吨,粉尘排放总量1500万吨,给大气环境造成严重污染。特别是近几年来,全国大范围连续出现雾霾天气,严重危害生态环境和人类身体健康。
3.目前,烟气净化技术主要以湿法脱硫和选择性催化还原(scr)脱硝技术为主。湿法脱硫技术以钙基脱硫工艺最为常见,其中,石灰石-石膏工艺成熟,工程应用也较多;选择性催化还原脱硝技术,其反应温度为250-450℃时,脱硝率可达70%-90%,在全球尤其是发达国家得到广泛应用。但是,脱硫和脱硝技术为两个独立的工艺过程,存在占地面积大、投资量大、回报周期长等问题。尤其是湿法脱硫技术不可避免向大气中排放大量水蒸汽,不仅易与漂浮的细小颗粒物相互作用形成二次粒子,而且还加重了雾霾气象。而采用scr技术的工艺设备投资大,需预热处理烟气,除此之外,催化剂以钒钛体系为主,存在价格昂贵、使用寿命短,二次利用失效后,被环保部列为固体废弃物的问题,同时存在氨泄漏、设备易腐蚀等问题。
4.因此,同时脱硫脱硝技术得到很大的关注和发展,其中,活性炭法、高能电子活化氧化法和吸收剂喷射法等技术都有工业化应用报道,但由于活性炭法工艺较为复杂,高能电子活化氧化法成本高昂,吸收剂喷射法使用范围小,这几种技术的发展应用均受到相应限制。而催化还原脱硫脱硝技术可将烟气中的so2和no同时还原为s和n2,工艺简单,无二次污染,具有很大的发展潜力,而相关催化剂及其制备方法和再生方法的研究则成为开发这一技术的研究重点。
技术实现要素:5.本发明的第一目的在于提供一种脱硫脱硝催化剂,该催化剂能够协同脱除烟气中的so2和no;
6.本发明的第二目的在于提供一种脱硫脱硝催化剂的制备方法,旨在提供一种制备成本低、催化效率高的催化剂制备方法;
7.本发明的第三目的在于提供一种脱硫脱硝催化剂的再生方法,旨在解决现有再生技术效果不佳、过程复杂的问题。
8.本发明提供的一种脱硫脱硝催化剂,包括载体和活性成分,所述活性成分负载在所述载体表面,且以质量百分比计,载体占比为60-90%,活性成分占比为10-40%;
9.其中,所述载体为氧化铝、蒙脱石和硅酸盐中的任意一种或多种以任意比例混配的混合物;
10.所述活性成分为钛、铁、铜、铈、锰、锆和钨中的任意一种或多种以任意比例组成的金属氧化物。
11.本发明的脱硫脱硝催化剂由载体和负载在载体表面的活性成分组成,其中,载体占比为60-90%,活性成分占比为10-40%,其中,载体为氧化铝、蒙脱石和硅酸盐中的任意一种或多种,而以钛、铁、铜、铈、锰、锆和钨中的任意一种或多种以任意比例组成的金属氧化物组成的活性成分,因其混合物在载体表面形成的致密且均匀的氧化层,使得催化剂具有较高的催化活性,并且该催化剂大大降低了其使用的窗口温度,可在25-260℃范围内对不同浓度的二氧化硫和氮氧化合物进行脱除。
12.本发明催化剂的制备方法,包括以下步骤:
13.将载体活化处理后,依次使用第一活性组分溶液和第二活性组分溶液处理,处理后依次进行洗涤、干燥和焙烧,即得脱硫脱硝催化剂;
14.其中,所述第一活性组分溶液为硝酸铁、硝酸铜、高铁酸钾、硫酸铈、钛酸钠、锰酸钾、高锰酸钾、硅酸锆、钨酸钠、氯酸钾和氯化钠中的任意一种或多种以任意比例混配的混合物;
15.所述第二活性组分溶液为硫酸亚铁、氯化亚铁、氯化钛、硝酸亚铜、氯化亚铜、氯化锰、硫酸锰、硫化钠、亚硫酸钾、亚硫酸钠中的任意一种或多种以任意比例混配的混合物。
16.本发明还公开了上述脱硫脱硝催化剂的制备方法,首先,将载体表面进行活化处理,以增加载体与活性成分的接触面积及共价结合力,使活性成分牢固的负载在载体表面,防止后期使用过程中活性成分的脱落。其次,依次使用第一活性组分溶液和第二活性组分溶液进行处理,第一活性组分溶液为硝酸铁、硝酸铜、高铁酸钾、硫酸铈、钛酸钠、锰酸钾、高锰酸钾、硅酸锆、钨酸钠、氯酸钾和氯化钠中的任意一种或多种,第二活性组分溶液为硫酸亚铁、氯化亚铁、氯化钛、硝酸亚铜、氯化亚铜、氯化锰、硫酸锰、硫化钠、亚硫酸钾、亚硫酸钠中的任意一种或多种,第一活性组分和第二活性组分在载体表面发生复分解反应生成钛、铁、铜、铈、锰、锆和钨中的任意一种或多种以任意比例组成的金属氧化物,上述氧化物具有良好的低温氧化还原的效果,实现了对二氧化硫及氮氧化物的协同脱除,不仅提高了脱硫脱硝效率,而且具有较高的使用寿命。
17.进一步,具体包括以下步骤:
18.s1、将载体依次使用盐酸和氢氧化钠进行活化处理;
19.s2、将活化处理后的载体置于第一活性组分溶液中,并滴加第二活性组分溶液,滴加完成后陈化处理0.5-24h;
20.s3、将陈化处理后的载体依次进行洗涤、干燥、焙烧和研磨,即得脱硫脱硝催化剂。
21.进一步,步骤s1具体包括:将载体先置于ph为2-4的盐酸溶液中处理5-8h,再置于ph为10-12的氢氧化钠溶液中处理5-8h。
22.活化处理主要是通过酸碱交替处理载体表面,其中,酸性溶液可使用ph为2-4的盐酸溶液,而碱性溶液可使用ph为10-12的氢氧化钠溶液、氢氧化钾、氢氧化镁等其他碱性溶液。上述酸碱液的交替处理,可显著提高载体表面的粗糙性,便于后期活性成分的负载。
23.进一步,步骤s2中,将活化处理后的载体加入所述第一活性组分溶液中,并置于30-90℃的水浴中搅拌处理0.3-0.7h,且所述第二活性组分溶液的滴加速度为400-600ml/(min
·
cm2)。
24.在使用第一活性组分溶液、第二活性组分溶液对载体进行处理时,首先将载体加入第一活性组分溶液中,并于30-90℃的水浴中搅拌处理0.3-0.7h,以增加第一活性组分溶液与载体表面的接触面积,而第二活性组分溶液以滴加的方式加入,主要是为了控制第一活性组分和第二活性组分的反应速度,以保证在载体表面形成致密均一的活性氧化物,使催化剂具有较高的催化活性和使用寿命。
25.进一步,所述第一活性组分溶液的浓度为0.01-1.5mol/l,所述第二活性组分溶液的浓度为0.01-1.5mol/l。
26.控制载体表面活性氧化物分布的另一种方法便是通过控制第一活性组分溶液和第二活性组分溶液的浓度,控制复分解反应的速率,进而控制活性氧化物的密度。
27.进一步,步骤s3中,所述干燥时,于90-110℃下处理2-36h;所述焙烧时,于200-800℃下处理1-48h;所述研磨时,研磨后过80-120目筛。
28.本发明还公开了上述催化剂的再生方法,包括以下步骤:
29.将失活的催化剂置于再生溶液中,并依次进行搅拌、静置、过滤和干燥,即得再生后的催化剂;
30.其中,所述再生溶液为邻苯二甲酸-盐酸缓冲溶液、柠檬酸-柠檬酸钠缓冲液、磷酸氢二钠-磷酸二氢钠缓冲溶液、磷酸氢二钠-柠檬酸缓冲溶液、硼砂-氢氧化钠缓冲溶液中的任意一种或多种以任意比例混配的混合物。
31.现有技术中也面临着催化剂使用寿命短、再生效果差、再生过程复杂的问题,因此,本发明还公开了上述催化剂的再生方法,首先,将失活的催化剂置于再生溶液中,并通过搅拌不断增加催化剂与再生溶液的接触面积和相互作用,使再生溶液完成对催化剂表面的活化处理,然后依次进行静置、过滤和干燥,即完成对催化剂的再生。这里的再生溶液为邻苯二甲酸-盐酸缓冲溶液、柠檬酸-柠檬酸钠缓冲液、磷酸氢二钠-磷酸二氢钠缓冲溶液、磷酸氢二钠-柠檬酸缓冲溶液、硼砂-氢氧化钠缓冲溶液中的任意一种或多种。
32.进一步,所述再生溶液的ph值为2-12,浓度为1.2-1.8mol/l。
33.进一步,所述搅拌时,于200-400rpm搅拌速率下处理1-3h;所述静置的时间为0.3-0.8h。
34.研究表明,当使用200-400rpm转速搅拌处理再生溶液中的催化剂时,既可实现对催化剂表面的活化,又不会对催化剂表面的活性氧化层造成不利影响。
35.本发明的脱硫脱硝催化剂,与现有技术相比,具有以下优点:
36.1、本发的脱硫脱硝催化剂催化活性高,性能稳定,不会造成二次污染,可高效地将烟气中的二氧化硫还原为单质硫、将氮氧化物还原为氮气,实现对二氧化硫和氮氧化物的同时脱除;
37.2、本发明的脱硫脱硝催化剂不仅具有良好的催化效果,而且能够大幅降低催化剂的使用温度,能够在25-260℃范围内对烟气处理过程中不同浓度的二氧化硫和氮氧化物进行脱除;
38.3、本发明的脱硫脱硝催化剂能够适用于电厂、供暖、钢铁、水泥、玻璃、建材等行业的烟气处理。
具体实施方式
39.应该指出,以下详细说明都是例示性的,旨在对本技术提供进一步的说明。除非另有指明,本文使用的所有技术和科学术语具有与本技术所属技术领域的普通技术人员通常理解的相同含义。
40.需要注意的是,这里所使用的术语仅是为了描述具体实施方式,而非意图限制根据本技术的示例性实施方式。如在这里所使用的,除非上下文另外明确指出,否则单数形式也包括复数形式,此外,还应当理解的是,当在本说明中使用术语“包含”和/或“包括”时,其指明存在特征、步骤、操作、器件、组件和/或它们的组合。
41.下面将结合实施例对本发明的技术方案进行清楚、完整地描述,显然,所描述的实施例是本发明一部分实施例,而不是全部的实施例。基于本发明中的实施例,本领域普通技术人员在没有做出创造性劳动前提下所获得的所有其他实施例,都属于本发明保护的范围。
42.实施例1
43.s11、将氧化铝载体先置于ph为2的盐酸溶液中处理5h,再置于ph为10的氢氧化钠溶液中处理8h,洗涤、干燥后备用;
44.s12、将活化处理后的载体加入以0.04mol/l的钛酸钠、0.06mol/l的高锰酸钾和0.06mol/l的硝酸铜组成的第一活性组分溶液中,并置于30℃的水浴中搅拌处理0.7h,然后以400ml/(min
·
cm2)的速度滴加以0.08mol/l的硫酸锰、0.06mol/l的氯化钛和0.06mol/l的硝酸亚铜组成的第二活性组分溶液,滴加完成后陈化处理0.5h;
45.s13、将陈化处理后的载体过滤,并使用蒸馏水洗涤至滤液中无so
42-(使用0.2mol/l的氯化钡溶液检测),滤饼于90℃下处理36h进行干燥,然后于200℃下处理48h进行焙烧,冷却后进行研磨,研磨后过100目筛,即得脱硫脱硝催化剂。
46.实施例2
47.s21、将蒙脱石载体先置于ph为4的盐酸溶液中处理8h,再置于ph为12的氢氧化钠溶液中处理5h,洗涤、干燥后备用;
48.s22、将活化处理后的载体加入以0.06mol/l的氯酸钠、0.04mol/l的钨酸钠、0.06mol/l的硝酸铜和0.08mol/l硫锰酸钾组成的第一活性组分溶液中,并置于90℃的水浴中搅拌处理0.3h,然后以600ml/(min
·
cm2)的速度滴加以0.08mol/l的硫酸亚铁、0.06mol/l的氯化亚铜和0.06mol/l的硫酸锰组成的第二活性组分溶液,滴加完成后陈化处理24h;
49.s23、将陈化处理后的载体过滤,并使用蒸馏水洗涤至滤液中无so
42-(使用0.2mol/l的氯化钡溶液检测),滤饼于110℃下处理2h进行干燥,然后于800℃下处理1h进行焙烧,冷却后进行研磨,研磨后过100目筛,即得脱硫脱硝催化剂。
50.实施例3
51.s31、将硅酸盐载体先置于ph为3的盐酸溶液中处理6h,再置于ph为11的氢氧化钠溶液中处理6h,洗涤、干燥后备用;
52.s32、将活化处理后的载体加入以0.5mol/l的高锰酸钾、0.5mol/l的硝酸铁、0.1mol/l的硝酸铜和0.3mol/l硫酸铈组成的第一活性组分溶液中,并置于60℃的水浴中搅拌处理0.5h,然后以500ml/(min
·
cm2)的速度滴加以1.2mol/l的一水合硫酸锰、0.8mol/l的氯化亚铁和1.0mol/l的氯化亚铜组成的第二活性组分溶液,滴加完成后陈化处理12h;
53.s33、将陈化处理后的载体过滤,并使用蒸馏水洗涤至滤液中无so
42-(使用0.2mol/l的氯化钡溶液检测),滤饼于100℃下处理19h进行干燥,然后于600℃下处理24h进行焙烧,冷却后进行研磨,研磨后过100目筛,即得脱硫脱硝催化剂。
54.实施例4
55.s41、将氧化铝、蒙脱石和硅酸盐载体先置于ph为3的盐酸溶液中处理6h,再置于ph为11的氢氧化钠溶液中处理6h,洗涤、干燥后备用;
56.s42、将活化处理后的载体加入以0.2mol/l的硫酸亚铁、0.3mol/l的氯化亚铜、0.1mol/l的氯化钛和0.2mol/l硫酸锰组成的活性组分溶液中,并置于80℃的水浴中搅拌处理0.5h,然后滴加1.2mol/l的氢氧化钠,在不断搅拌的条件下,逐滴加入1.5mol/l的过硫酸铵溶液,滴加完成后陈化处理20h;
57.s43、将陈化处理后的载体过滤,并使用蒸馏水洗涤至滤液中无so
42-(使用0.2mol/l的氯化钡溶液检测),滤饼于100℃下处理30h进行干燥,然后于600℃下处理30h进行焙烧,冷却后进行研磨,研磨后过100目筛,即得脱硫脱硝催化剂。
58.将实施例1-4所制备的脱硫脱硝催化剂于固定反应器内测试其催化性能,测试用的催化剂为100目颗粒,催化剂使用量为60g,反应温度为25℃,模拟烟气中so2的浓度为1500ppm,no的浓度为800ppm,烟气出口使用德图350进行检测。表1为实施例1-4所制备催化剂的评价效果。
59.表1实施例1-4所制备催化剂的评价效果
[0060][0061][0062]
由表1数据可知,本发明所制备的脱硫脱硝催化剂,脱硫效率在35%以上,最高可达50%,而脱硝效率在33%以上,最高可达50%,因此,本发明的脱硫脱硝催化剂不仅具有良好的催化效果,而且能够大幅降低催化剂的使用温度,能够在25-260℃范围内对烟气处理过程中不同浓度的二氧化硫和氮氧化物进行脱除。
[0063]
将实施例4所制备的脱硫脱硝催化剂在模拟烟气中进行脱硫脱硝实验,当催化剂失活后,按照实施例5-7方法进行再生。
[0064]
实施例5
[0065]
将失活的催化剂置于ph值为2-12,浓度为1.2-1.8mol/l的邻苯二甲酸-盐酸缓冲溶液中,并于200-400rpm转速下搅拌处理1-3h,然后静置0.3-0.8h,过滤、干燥后,即得再生后的催化剂。
[0066]
实施例6
[0067]
将失活的催化剂置于ph值为2-12,浓度为1.2-1.8mol/l的磷酸氢二钠-磷酸二氢钠缓冲溶液中,并于200-400rpm转速下搅拌处理1-3h,然后静置0.3-0.8h,过滤、干燥后,即得再生后的催化剂。
[0068]
实施例7
[0069]
将失活的催化剂置于ph值为2-12,浓度为1.2-1.8mol/l的磷酸氢二钠-磷酸二氢钠缓冲溶液和磷酸氢二钠-柠檬酸缓冲溶液的混合溶液中,并于200-400rpm转速下搅拌处理1-3h,然后静置0.3-0.8h,过滤、干燥后,即得再生后的催化剂。
[0070]
对实施例5-7再生后的催化剂使用固定反应器测试其催化性能,催化剂使用量为60g,反应温度为25℃,模拟烟气中so2的浓度为1500ppm,no的浓度为800ppm,烟气出口使用德图350进行检测。表2为实施例5-7再生后催化剂的评价效果。
[0071]
表2实施例5-7再生后催化剂的评价效果
[0072][0073]
由表1和表2数据可知,再生后的催化剂脱硫效率可达到原来的80%左右,而脱硝效率可也达到原来的70%左右,因此,本发明提供的再生方法具有再生效率高、过程简单的优点。
[0074]
最后应说明的是:以上各实施例仅用以说明本发明的技术方案,而非对其限制;尽管参照前述各实施例对本发明进行了详细的说明,本领域的普通技术人员应当理解:其依然可以对前述各实施例所记载的技术方案进行修改,或者对其中部分或者全部技术特征进行等同替换;而这些修改或者替换,并不使相应技术方案的本质脱离本发明各实施例技术方案的范围。