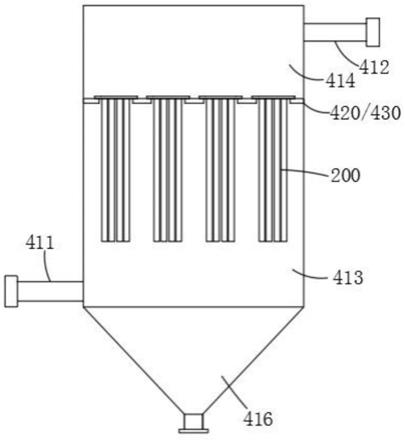
过滤器
1.本申请要求申请号为2020102681879、申请日2020年4月8日、名称为“滤管、集束式滤芯及其应用”的中国首次申请的优先权。
技术领域
2.本实用新型涉及薄片状材料及过滤的技术领域,具体而言,涉及过滤器。
背景技术:3.薄片状材料具有明显优于非金属布袋的耐高温性能和比陶瓷滤芯更小的过滤阻力,因此由薄片状材料卷制而成的管状滤芯受到广泛应用。
4.本申请的申请人已提交的专利公开号为cn104759630a、cn104759629a、cn104874798a、cn104959611a、cn104959612a和cn104874801a等中国发明专利申请公开了无支撑或有支撑(指将原料粉末附着于支撑体上并一起烧结成型)的烧结金属多孔薄膜,并且成功将烧结金属多孔薄膜进一步制成的管状滤芯产品及过滤器进行销售。通常,为了保证较高的过滤面积,管状滤芯通常具有较大的直径和长度。然而,在较为长期的制造和销售过程中,较大的直径和长度的滤芯遇到了以下几方面的问题:
5.(1)滤芯的内侧或外侧设置有支撑体,这显著增加了重量和成本;
6.(2)由于滤芯直径大,因此对滤芯两端的密封尤为复杂(如申请号为2018103243431的中国发明专利公布的内滤式过滤装置),并且滤芯一旦损坏,由于修复困难,通常采用直接更换,维护成本非常高;
7.(3)滤芯直径较大,过滤装置需要很大的占地面积;
8.(4)若想减少接缝以提升滤芯强度,则需要使卷制之前的多孔薄膜具有非常大的面积,这不仅显著增加了制作成本,且造成切割后小面积多孔薄膜的浪费;
9.(5)由于滤芯很长,且增加的支撑体显著增重,因此滤芯的搬运及安装需要多名工作人员配合,费时且费力;
10.(6)当滤芯很长时,反吹效果沿滤芯轴向分布的均匀性变差;
11.(7)由于场地等限制因素,导致滤芯的过滤面积提升受限。
12.然而,除了增加直径和长度以及设置支撑体之外,目前尚无有效且低成本的手段来提升由薄片状材料卷制而成的滤芯的过滤面积以及强度。
技术实现要素:13.本实用新型的第一个目的在于提供滤管、滤管的制备方法以及滤芯。
14.技术方案如下:
15.滤管,使用时被阵列密布于一过滤器中用以对待过滤物进行气固分离过滤和/或液固分离过滤,该滤管的管体是由金属或以金属为基体的薄片状材料以被卷制的方式塑形并对接缝进行密封加工而成的;并且通过所述卷制成型的管体的外径仅为20~200mm,优选为20~90mm,进一步优选为20~60mm,更进一步优选为25~50mm。
16.滤管的制备方法,包括步骤:将厚度为0.2~2.5mm的薄片状材料卷制成外径为20~200mm的管体。
17.滤芯,包括上述的滤管。
18.本实用新型的小直径滤管具有以下的优点:(1)本申请的申请人发现,对于由金属或以金属为基体的薄片状材料卷制而成的滤管,滤管的直径越小,滤管的强度越高,尤其是当滤管的直径缩小至200mm以下时,即使不再设置支撑体,滤管自身的强度也可以维持管状,能够实现自支撑,由此可以显著降低重量和成本;(2)由于滤管的直径缩小,因此滤芯两端固定时的工作面缩小,更便于密封;(3)由于滤管的直径缩小,因此卷制前的薄片状材料的面积更小,不仅有助于减少接缝,而且切割浪费量更少;(4)能够承受远高于非金属布袋的过滤温度;(5)具有远小于陶瓷滤芯的过滤阻力。可见,本实用新型的滤管和滤芯有效解决了现有技术中滤芯存在的成本高和强度低的技术问题。
19.本实用新型的第二个目的在于提供滤芯。
20.第一种滤芯的技术方案如下:
21.滤芯,使用时被放置于一过滤器中用以对待过滤物进行气固分离过滤和/或液固分离过滤,滤芯包括至少两个间隔排列的滤管,其中,滤管的管体是由金属或以金属为基体的薄片状材料以被卷制的方式塑形并对接缝进行密封加工而成的;并且通过所述卷制成型的管体的外径仅为20~200mm,优选为20~90mm,进一步优选为20~60mm,更进一步优选为25~50mm。
22.在第一种滤芯中,将多个小直径的滤管集束化后的集束式滤芯替换传统的大直径单管滤芯,不仅可以在有限的安装空间内显著提升过滤面积;滤管具有自支撑性,强度高且成本低,能够承受高过滤温度,过滤阻力小。可见,本实用新型的第一种滤芯有效解决了现有技术中滤芯存在的过滤面积小的技术问题。
23.第二种滤芯的技术方案如下:
24.滤芯,使用时被放置于一过滤器中用以对待过滤物进行气固分离过滤和/或液固分离过滤,滤芯包括至少两个间隔排列的滤管,其中,滤管的管体是由金属或以金属为基体的薄片状材料以被卷制的方式塑形并对接缝进行密封加工而成的;并且通过所述卷制成型的管体的外径仅为20~200mm,优选为20~90mm,进一步优选为20~60mm,更进一步优选为25~50mm;滤管的长度为100~5000mm,优选为100~3000mm,进一步优选为100~2000mm,更进一步优选为200~1500mm。
25.在第二种滤芯中,将多个小直径的滤管集束化后的集束式滤芯替换传统的大直径单管滤芯,可以在有限的安装空间内显著提升过滤面积;对于体积较小的过滤器,通过滤管的集束化可以缩短滤芯长度,从而解决滤芯长度与过滤面积不相匹配的技术问题;通过缩小滤芯的长度,还可以使反吹效果沿滤管轴向分布地更加均匀;滤管具有自支撑性,强度高且成本低,能够承受高过滤温度,过滤阻力小。可见,本实用新型的第二种滤芯有效解决了现有技术中滤芯存在的过滤面积小和反吹有效性差的技术问题。
26.第三种滤芯的技术方案如下:
27.滤芯,使用时被放置于一过滤器中用以对待过滤物进行气固分离过滤和/或液固分离过滤,滤芯具有多个过滤单元,在滤芯的横截面上所述多个过滤单元呈同心圆环和/或平行直线排列的,每个过滤单元包括一个或多个间隔排列的滤管;其中,滤管的管体是由金
属或以金属为基体的薄片状材料以被卷制的方式塑形并对接缝进行密封加工而成的;并且通过所述卷制成型的管体的外径仅为20~200mm,优选为20~90mm,进一步优选为20~60mm,更进一步优选为25~50mm。
28.在第三种滤芯中,将多个小直径的滤管集束化后的集束式滤芯替换传统的大直径单管滤芯,可以在有限的安装空间内显著提升过滤面积;通过合理安排滤管的排列方式,可以使滤芯的过滤面积进一步增大;滤管具有自支撑性,强度高且成本低,能够承受高过滤温度,过滤阻力小。可见,本实用新型的第三种滤芯有效解决了现有技术中滤芯存在的过滤面积小的技术问题。
29.第四种滤芯的技术方案如下:
30.滤芯,使用时被放置于一过滤器中用以对待过滤物进行气固分离过滤和/或液固分离过滤,滤芯包括滤管和固定组件,所述固定组件包括:头部固定结构,所述头部固定结构包括上接头,所述上接头具有与所述滤管一端相配合的安装孔,所述安装孔内壁与所述滤管的外壁密封连接;以及尾部固定结构,所述尾部固定结构包括与所述滤管另一端相配合的堵头,所述堵头与所述滤管的内壁和/或外壁密封连接;其中,所述安装孔、滤管和堵头为至少两组;滤管的管体是由金属或以金属为基体的薄片状材料以被卷制的方式塑形并对接缝进行密封加工而成的;并且通过所述卷制成型的管体的外径仅为20~200mm,优选为20~90mm,进一步优选为20~60mm,更进一步优选为25~50mm;上接头一侧的待过滤气体穿过滤管的管壁后形成的洁净气体在上接头的另一侧排出。
31.在第四种滤芯中,将多个小直径的滤管集束化后的集束式滤芯替换传统的大直径单管滤芯,可以在有限的安装空间内显著提升过滤面积;将多个滤管同时固定于上接头上,然后再安装于过滤器内,可以显著提升安装速度;由于滤管的直径显著降低,因此密封更加简单;滤管具有自支撑性,强度高且成本低,能够承受高过滤温度,过滤阻力小。可见,本实用新型的第四种滤芯有效解决了现有技术中滤芯存在的过滤面积小以及安装结构复杂的技术问题。
32.第五种滤芯的技术方案如下:
33.滤芯,使用时被放置于一过滤器中用以对待过滤物进行气固分离过滤和/或液固分离过滤,滤芯包括至少两个间隔排列的滤管,其中,滤管的管体是由金属或以金属为基体的薄片状材料以被卷制的方式塑形并对接缝进行密封加工而成的;并且通过所述卷制成型的管体的外径仅为20~200mm,优选为20~90mm,进一步优选为20~60mm,更进一步优选为25~50mm;相邻两个滤管的间距为5~100mm,优选为5~60mm,进一步优选为5~40mm,更进一步优选为8~30mm;滤芯还包括文氏管,所述至少两个间隔排列的滤管的出气方向均位于文氏管的内侧。
34.在第五种滤芯中,将多个小直径的滤管集束化后的集束式滤芯替换传统的大直径单管滤芯,可以在有限的安装空间内显著提升过滤面积;通过对每个滤芯中的多个滤管同时进行反吹,可以显著提升反吹效率;滤管具有自支撑性,强度高且成本低,能够承受高过滤温度,过滤阻力小。可见,本实用新型的第五种滤芯不仅解决了现有技术中滤芯存在的过滤面积小的技术问题,还解决了滤管集束化后的反吹问题。
35.第六种滤芯的技术方案如下:
36.滤芯,使用时被放置于一过滤器中用以对待过滤物进行气固分离过滤和/或液固
分离过滤,滤芯包括至少两个间隔排列的滤管,其中,滤管的管体是由金属或以金属为基体的薄片状材料以被卷制的方式塑形并对接缝进行密封加工而成的;并且通过所述卷制成型的管体的外径仅为20~200mm,优选为20~90mm,进一步优选为20~60mm,更进一步优选为25~50mm;相邻两个滤管的间距为5~100mm,优选为5~60mm,进一步优选为5~40mm,更进一步优选为8~30mm;滤芯还包括清灰结构,所述清灰结构包括:对滤管内部进行清灰的内部清灰机构;以及对滤管外部进行清灰的外部清灰机构。
37.在第六种滤芯中,将多个小直径的滤管集束化后的集束式滤芯替换传统的大直径单管滤芯,可以在有限的安装空间内显著提升过滤面积;滤管的间距缩小将导致粉尘架桥的可能性增加,因此,通过设置内部清灰机构和外部清灰机构,可以显著提升反吹效果,快速恢复气通量;滤管具有自支撑性,强度高且成本低,能够承受高过滤温度,过滤阻力小。可见,本实用新型的第六种滤芯不仅解决了现有技术中滤芯存在的过滤面积小的技术问题,还解决了滤管集束化后的反吹有效性问题。
38.本实用新型的第三个目的在于提供过滤器。
39.第一种过滤器的技术方案如下:
40.过滤器,用以对待过滤物进行气固分离过滤和/或液固分离过滤,过滤器包括过滤结构,过滤结构包括滤芯,滤芯包括至少两个间隔排列的滤管,其中,滤管的管体是由金属或以金属为基体的薄片状材料以被卷制的方式塑形并对接缝进行密封加工而成的;并且通过所述卷制成型的管体的外径仅为20~200mm,优选为20~90mm,进一步优选为20~60mm,更进一步优选为25~50mm;滤管的长度为100~5000mm,优选为100~3000mm,进一步优选为100~2000mm,更进一步优选为200~1500mm。
41.在第一种过滤器中,由于滤管的集束化,使得达到相同过滤面积所需过滤结构的高度显著降低,从而有助于缩小过滤器体积;滤管具有自支撑性,强度高且成本低,能够承受高过滤温度,过滤阻力小。可见,与现有技术相比,本实用新型的第一种过滤器可以达到更高的过滤面积以及更小的过滤器体积。
42.第二种过滤器的技术方案如下:
43.过滤器,用以对待过滤物进行气固分离过滤和/或液固分离过滤,过滤器包括过滤结构,过滤结构包括至少两个间隔排列的滤芯;滤芯包括至少两个间隔排列的滤管,其中,滤管的管体是由金属或以金属为基体的薄片状材料以被卷制的方式塑形并对接缝进行密封加工而成的;并且通过所述卷制成型的管体的外径仅为20~200mm,优选为20~90mm,进一步优选为20~60mm,更进一步优选为25~50mm。
44.在第二种过滤器中,采用多个小直径滤管集束而成的集束式滤芯,可以显著提升过滤面积;对于较大体积的过滤器,采用多个集束式滤芯可以在确保高过滤面积时降低单个滤芯重量,简化安装;对于所需滤管数量较多的过滤结构,采用多个集束式滤芯分别进行安装还可以确保较均匀的反吹效果;滤管具有自支撑性,强度高且成本低,能够承受高过滤温度,过滤阻力小。可见,与现有技术相比,本实用新型的第二种过滤器不仅可以达到更高的过滤面积,而且解决了滤管集束化后的安装问题和反吹问题。
45.第三种过滤器的技术方案如下:
46.过滤器,用以对待过滤物进行气固分离过滤和/或液固分离过滤,过滤器包括过滤结构,过滤结构包括滤芯和第一支撑结构,滤芯包括滤管和固定组件,所述固定组件包括:
头部固定结构,所述头部固定结构包括上接头,所述上接头具有与所述滤管一端相配合的安装孔;以及尾部固定结构,所述尾部固定结构包括与所述滤管另一端相配合的堵头;其中,所述安装孔、滤管和堵头为至少两组;滤管的管体是由金属或以金属为基体的薄片状材料以被卷制的方式塑形并对接缝进行密封加工而成的;并且通过所述卷制成型的管体的外径仅为20~200mm,优选为20~90mm,进一步优选为20~60mm,更进一步优选为25~50mm;过滤结构包括至少两个间隔排列的滤芯;第一支撑结构具有与滤芯形状匹配的第一安装通道,上接头与所述第一安装通道通过压紧机构密封连接;第一支撑结构和上接头一侧的待过滤气体穿过滤管的管壁后形成的洁净气体在另一侧排出。
47.在第三种过滤器中,将多个滤管集束化后的集束式滤芯替换传统的大直径单管滤芯,可以在有限的安装空间内显著提升过滤面积;其次,将多个滤管同时固定于上接头上,然后再安装于过滤器内,可以显著提升安装速度;滤管具有自支撑性,强度高且成本低,能够承受高过滤温度,过滤阻力小。可见,与现有技术相比,本实用新型的第三种过滤器不仅解决了过滤器过滤面积小的技术问题,还解决了滤管集束化后的安装问题。
48.第四种过滤器的技术方案如下:
49.过滤器,用以对待过滤物进行气固分离过滤和/或液固分离过滤,过滤器包括过滤结构,过滤结构包括至少两个间隔排列的滤芯;滤芯包括至少两个间隔排列的滤管,其中,滤管的管体是由金属或以金属为基体的薄片状材料以被卷制的方式塑形并对接缝进行密封加工而成的;并且通过所述卷制成型的管体的外径仅为20~200mm,优选为20~90mm,进一步优选为20~60mm,更进一步优选为25~50mm;过滤器还包括清灰结构,所述清灰结构包括对滤管内部进行清灰的内部清灰机构和对滤管外部进行清灰的外部清灰机构;其中,所述外部清灰机构包括第一机构和/或第二机构;所述第一机构包括出气口位于每个滤芯中滤管与滤管之间的第一外部吹扫气输气管,所述第二机构包括出气口位于滤芯与滤芯之间的第二外部吹扫气输气管。
50.在第四种过滤器中,由于滤管的集束化,使得达到相同过滤面积所需过滤结构的高度显著降低,从而有助于缩小过滤器体积;通过设置内部清灰机构和外部清灰机构,可以提升反吹效果,快速恢复气通量;第一机构和/或第二机构可以全面地对滤管外部进行吹扫,有效防止滤管与滤管之间发生粉尘架桥现象;滤管具有自支撑性,强度高且成本低,能够承受高过滤温度,过滤阻力小。可见,与现有技术相比,本实用新型的第四种过滤器不仅解决了过滤器过滤面积小的技术问题,还解决了滤管集束化后的反吹有效性问题。
51.第五种过滤器的技术方案如下:
52.过滤器,用以对待过滤物进行气固分离过滤和/或液固分离过滤,过滤器包括过滤结构,过滤结构包括至少两个间隔排列的滤芯;滤芯包括至少两个间隔排列的滤管,其中,滤管的管体是由金属或以金属为基体的薄片状材料以被卷制的方式塑形并对接缝进行密封加工而成的;并且通过所述卷制成型的管体的外径仅为20~200mm,优选为20~90mm,进一步优选为20~60mm,更进一步优选为25~50mm;过滤器还包括压力检测结构,所述压力检测结构包括对过滤前的气体压力进行检测的第一压力检测器和/或对过滤后的气体压力进行检测的第二压力检测器,其中,在每个滤芯的出气口均设有所述第二压力检测器。
53.在第五种过滤器中,由于滤管的集束化,使得达到相同过滤面积所需过滤结构的高度显著降低,从而有助于缩小过滤器体积;通过对每个滤芯的出气口压力进行检测,有助
于针对性对堵塞的滤芯进行清灰以及对漏气的滤芯进行维护;滤管具有自支撑性,强度高且成本低,能够承受高过滤温度,过滤阻力小。可见,与现有技术相比,本实用新型的第五种过滤器不仅解决了过滤器过滤面积小的技术问题,还解决了滤管集束化后的清灰和维护问题。
54.第六种过滤器的技术方案如下:
55.过滤器,用以对待过滤物进行气固分离过滤和/或液固分离过滤,过滤器包括原气腔、净气腔和位于原气腔和净气腔之间的过滤结构,过滤结构包括滤芯,滤芯包括至少两个间隔排列的滤管,其中,滤管的管体是由金属或以金属为基体的薄片状材料以被卷制的方式塑形并对接缝进行密封加工而成的;并且通过所述卷制成型的管体的外径仅为20~200mm,优选为20~90mm,进一步优选为20~60mm,更进一步优选为25~50mm;滤管的长度为100~5000mm,优选为100~3000mm,进一步优选为100~2000mm,更进一步优选为200~1500mm;过滤器还包括化学催化和/或物理吸附挥发性气体的净化结构,所述净化结构设于净气腔的出气口与过滤结构之间。
56.在第六种过滤器中,由于滤管的集束化,使得达到相同过滤面积所需过滤结构的高度显著降低,从而有助于缩小过滤器体积;进一步,由于过滤器过滤结构的长度缩短,因此可以增大净气腔的尺寸用于安装净化结构,使除尘和净化的总占地面积显著减小;滤管具有自支撑性,强度高且成本低,能够承受高过滤温度,过滤阻力小。可见,与现有技术相比,本实用新型的第六种过滤器不仅可以达到更高的过滤面积,而且能够使过滤和净化一体化,显著节约成本。
57.第七种过滤器的技术方案:
58.过滤器,用以对待过滤物进行气固分离过滤和/或液固分离过滤,过滤器包括过滤结构,过滤结构包括滤芯,过滤器还包括维护结构;所述维护结构包括:封堵机构,用于在滤芯出现故障时对滤芯出气口进行封堵;以及连杆机构,用于在滤芯出现故障时控制封堵机构对滤芯出气口进行封堵;以及驱动机构,用于在滤芯出现故障时驱动所述连杆机构;当滤芯未发生故障时,所述封堵机构位于滤芯出气口上方;当滤芯发生故障时,所述封堵机构降落至滤芯出气口。
59.现有技术中,一旦滤芯出现漏气现象,通常只有停车维修这一条途径,具有非常大的经济隐患。在本实用新型的第七种过滤器中,当滤芯出现故障时,可以及时对故障滤芯进行封堵,对于含有多个滤芯的过滤器,其它未发生故障的滤芯还可以正常使用;封堵过程可以在过滤器外部操作,不影响过滤器的运行。可见,与现有技术相比,本实用新型的第七种过滤器解决了滤芯故障时不能及时有效处理的技术问题。
60.本实用新型的第四个目的在于提供电改膜除尘器以及电改膜除尘系统。
61.电改膜除尘器的技术方案如下:
62.由电除尘器改造而成的电改膜除尘器,包括过滤结构,过滤结构设于电除尘器的电极板放置区内;过滤结构包括滤芯和第一支撑结构;其中,第一支撑结构与电除尘器的壳体连接并将所述电极板放置区分隔为分别位于第一支撑结构两侧的原气腔和净气腔,所述原气腔与电除尘器的进气通道连接,所述净气腔与电除尘器的出气通道连接,原气腔中的来自于进气通道的待过滤气体穿过滤芯后形成的洁净气体进入净气腔后从出气通道排出,而经滤芯拦截的粉尘从电除尘器的排灰口排出;滤芯包括至少两个间隔排列的滤管,其中,
滤管的管体是由金属或以金属为基体的薄片状材料以被卷制的方式塑形并对接缝进行密封加工而成的;并且通过所述卷制成型的管体的外径仅为20~200mm,优选为20~90mm,进一步优选为20~60mm,更进一步优选为25~50mm;滤管的长度为100~5000mm,优选为100~3000mm,进一步优选为100~2000mm,更进一步优选为200~1500mm。
63.电改膜除尘系统的技术方案如下:
64.由电除尘系统改造而成的电改膜除尘系统中,改造前的电除尘系统具有至少两个电除尘器,改造后的电改膜除尘系统具有至少一个电改膜除尘器。
65.电除尘器的除尘精度低,一般除尘后气体含尘量尚有100~300mg/nm3,除尘效率不稳定,随前工序原料、炉况变化而波动大,耗电量高,易产生电晕,不仅效率下降,还存在安全隐患,维护费用高。但是由于电除尘器的设备投资成本高,对于已使用电除尘器的企业而言,对电除尘器进行合理改造以节约成本和提升除尘效果是最为优选的方式。但是电除尘器的改造主要面临以下问题:(1)传统非金属布袋达不到耐高温要求和高过滤精度要求;(2)由于电除尘器的电极板放置区的空间有限,传统的由薄片状材料构成的单管滤芯难以满足过滤面积要求。
66.在本实用新型的电改膜除尘器以及电改膜除尘系统中,滤管的集束化使得过滤结构即使长度很短也可以保证较高的过滤面积,并且薄片状材料构成的管体能够承受远高于非金属布袋的过滤温度,非常适合于安装在电除尘器的电极板放置区中。与电除尘器相比,电改膜除尘器具有更强的耐高温性能和除尘精度,因此,电改膜除尘器或仅含有电改膜除尘器的电改膜除尘系统具有更高的使用温度。可见,与现有技术相比,本实用新型的电改膜除尘器以及电改膜除尘系统有效解决了电除尘器以及电除尘系统改造难的技术问题。
67.本实用新型的第五个目的在于提供除尘方法。
68.技术方案如下:
69.除尘方法,包括采用除尘装置,除尘装置包括过滤结构,过滤结构包括滤芯,滤芯包括至少两个间隔排列的滤管,其中,滤管的管体是由金属或以金属为基体的薄片状材料以被卷制的方式塑形并对接缝进行密封加工而成的;并且通过所述卷制成型的管体的外径仅为20~200mm,优选为20~90mm,进一步优选为20~60mm,更进一步优选为25~50mm;相邻两个滤管的间距为5~100mm,优选为5~60mm,进一步优选为5~40mm,更进一步优选为8~30mm;过滤风速为0.8~2m/min,待过滤气体温度≤800℃。
70.在本实用新型的除尘方法中,由于采用过滤面积更高的过滤结构,因此过滤阻力更小,过滤风速更低;同时,采用由金属或以金属为基体的薄片状材料构成的管体,具有明显小于陶瓷滤芯的过滤阻力,能够承受远高于非金属布袋的过滤温度;滤管具有自支撑性,强度高且成本低,且能达到高过滤精度。可见,与现有技术相比,本实用新型的除尘方法既解决了因非金属布袋不耐高温、精度不高的问题,又解决了因过滤面积小而产生的过滤阻力较大的技术问题。
71.下面结合附图和具体实施方式对本实用新型做进一步的说明。本实用新型附加的方面和优点将在下面的描述中部分给出,部分将从下面的描述中变得明显,或通过本实用新型的实践了解到。
附图说明
72.构成本实用新型的一部分的附图用来辅助对本实用新型的理解,附图中所提供的内容及其在本实用新型中有关的说明可用于解释本实用新型,但不构成对本实用新型的不当限定。在附图中:
73.图1为滤管的一种具体实施方式的结构示意图。
74.图2为滤管的第二种具体实施方式的结构示意图。
75.图3为滤管的第三种具体实施方式的结构示意图。
76.图4为一种具体实施方式中卷制得到的管体。
77.图5为另一种具体实施方式中卷制得到的管体。
78.图6为第一种滤芯的一种具体实施方式的结构示意图。
79.图7为第三种滤芯中多个过滤单元同时呈同心圆环排列和平行直线排列的一种具体实施方式的结构示意图。
80.图8为第三种滤芯中多个过滤单元呈平行直线排列的另一种具体实施方式的结构示意图。
81.图9为第四种滤芯中采用胀接时为了提升密封效果的第一种具体实施方式的结构示意图
82.图10为第四种滤芯中采用胀接时为了提升密封效果的第二种具体实施方式的结构示意图。
83.图11为第四种滤芯的第二种具体实施方式的结构示意图。
84.图12为第五种滤芯的一种具体实施方式的结构示意图。
85.图13为第六种滤芯的一种具体实施方式的结构示意图。
86.图14为第一种过滤器的一种具体实施方式的结构示意图。
87.图15为第二种过滤器的一种具体实施方式的结构示意图。
88.图16为第一支撑结构的第一种具体实施方式的结构示意图。
89.图17为第一支撑结构的第二种具体实施方式的结构示意图。
90.图18为第二支撑结构的第一种具体实施方式的结构示意图。
91.图19为第二支撑结构的第二种具体实施方式的结构示意图。
92.图20为采用由上至下推入式安装时压紧机构的第一种具体实施方式中的结构示意图。
93.图21为采用由下至上推入式安装时压紧机构的第一种具体实施方式中的结构示意图。
94.图22为压紧机构的第二种具体实施方式的结构示意图。
95.图23为压紧机构的第三种具体实施方式的结构示意图。
96.图24为第四种过滤器的第一种具体实施方式的结构示意图。
97.图25为第四种过滤器的第二种具体实施方式的结构示意图。
98.图26为第四种过滤器的第三种具体实施方式的结构示意图。
99.图27为第四种过滤器的第四种具体实施方式的结构示意图。
100.图28为第五种过滤器的第一种具体实施方式的结构示意图。
101.图29为第六种过滤器的第一种具体实施方式的结构示意图。
102.图30为第六种过滤器中净化结构的第一种具体实施方式的结构示意图。
103.图31为第六种过滤器的第二种具体实施方式的结构示意图。
104.图32为滤芯正常工作时维护结构的使用状态图。
105.图33为滤芯出现故障时维护结构的使用状态图。
106.图34为滤芯正常工作时连杆机构的使用状态图。
107.图35为滤芯出现故障时连杆机构的使用状态图。
108.图36为驱动机构和第一杆体的剖视图。
109.图37为由电除尘器改造而成的电改膜除尘器的一种实施方式的结构示意图。
110.图38为由电除尘系统改造而成的电改膜除尘系统的第一种具体实施方式的结构示意图。
111.图39为由电除尘系统改造而成的电改膜除尘系统的第二种具体实施方式的结构示意图。
112.上述附图中的有关标记为:
113.100
‑
滤管,110
‑
管体,111
‑
薄片状材料,112
‑
接缝,120
‑
连接头,131
‑
支撑环,132
‑
龙骨,200
‑
滤芯,210
‑
上接头,211
‑
胀头,212
‑
密封结构,213
‑
第一清灰孔,220
‑
堵头,230
‑
尾架,240
‑
拉杆,300
‑
文氏管,311
‑
第一椎管段,321
‑
第一竖管段,312
‑
第二椎管段,322
‑
第二竖管段,330
‑
台阶,340
‑
通孔,411
‑
进气管,412
‑
出气管,413
‑
原气腔,414
‑
净气腔,415
‑
无尘腔,416
‑
灰斗,417
‑
壳体,420
‑
第一支撑结构,421
‑
第一安装通道,422
‑
第一孔板,423
‑
第一支撑梁,430
‑
第二支撑结构,431
‑
第二安装通道,432
‑
第二孔板,433
‑
第二支撑梁,441
‑
压紧板,442
‑
垫板,443
‑
密封层,444
‑
螺母,445
‑
螺栓,446
‑
螺杆,451
‑
内部吹扫气输气管,452
‑
第一总阀,453
‑
支管,461
‑
第一外部吹扫气输气管,462
‑
第二总阀,471
‑
第二外部吹扫气输气管,472
‑
第三总阀,481
‑
第一压力检测器,482
‑
第二压力检测器,483
‑
温度检测器,500
‑
净化结构,510
‑
支撑条,520
‑
支撑板,530
‑
进气板,540
‑
出气板,550
‑
通气孔,560
‑
隔板,611
‑
堵头槽,612
‑
堵头盖,613
‑
堵塞球,620
‑
平行四边形组件,621
‑
第一杆体,622
‑
第二杆体,623
‑
第三杆体,624
‑
连杆,624
‑
连杆,631
‑
第一转动部,632
‑
第一铰接部,633
‑
滑槽,634
‑
自由端,635
‑
第二铰接部,636
‑
第二转动部,637
‑
凸环,638
‑
槽体,640
‑
驱动机构,641
‑
气缸,642
‑
活塞,643
‑
进气口,644
‑
弹簧,651
‑
控制气管,652
‑
控制阀,700
‑
电改膜除尘器,710
‑
进气通道,720
‑
出气通道,730
‑
排灰口,740
‑
电极板放置区,750
‑
第一挡板,760
‑
第二挡板,770
‑
排气通道,800
‑
电除尘器。
具体实施方式
114.下面结合附图对本实用新型进行清楚、完整的说明。本领域普通技术人员在基于这些说明的情况下将能够实现本实用新型。在结合附图对本实用新型进行说明前,需要特别指出的是:
115.本实用新型中在包括下述说明在内的各部分中所提供的技术方案和技术特征,在不冲突的情况下,这些技术方案和技术特征可以相互组合。
116.此外,下述说明中涉及到的本实用新型的实施例通常仅是本实用新型一部分的实施例,而不是全部的实施例。因此,基于本实用新型中的实施例,本领域普通技术人员在没有做出创造性劳动的前提下所获得的所有其他实施例,都应当属于本实用新型保护的范
围。
117.关于本实用新型中术语和单位。本实用新型的说明书和权利要求书及有关的部分中的术语“包括”、“具有”以及它们的任何变形,意图在于覆盖不排他的包含。
118.其中,术语“过滤风速”的含义是:过滤时,待过滤物(气体或液体)单位时间穿过滤材(金属膜)的距离,一般用米/秒(m/s)表示。
119.一、滤管
120.针对背景技术所介绍的现有由薄片状材料构成的滤芯存在的成本高、强度差等技术问题,本实用新型提供了新型的滤管。
121.图1为滤管的一种具体实施方式的结构示意图。如图1所示,滤管(100)的管体(110)是由金属或以金属为基体的薄片状材料(111)以被卷制的方式塑形并对接缝(112)进行密封加工而成的。其中,通过所述卷制成型的管体(110)的外径仅为20~200mm,优选为20~90mm,进一步优选为20~60mm,更进一步优选为25~50mm;管体(110)的管壁厚度为0.2~2.5mm,优选为0.2~1.5mm,进一步优选为0.25~0.8mm;薄片状材料(111)的孔径为0.3~200μm,优选为1~100μm,进一步优选为1.5~50μm,更进一步优选为2~30μm;滤管(100)的长度为100~5000mm,优选为100~3000mm,进一步优选为100~2000mm,更进一步优选为200~1500mm;薄片状材料(111)为金属纤维毡、烧结金属多孔薄膜或金属网。
122.对于由薄片状材料111构成的管体110,当滤管100的外径为20~200mm时,滤管具有自支撑性。其中,当滤管100的外径为20~90mm,优选为20~60mm,进一步优选为25~50mm时,自支撑性最好。具体实施时,滤管100的外径可以为20mm、25mm、30mm、40mm、50mm、60mm、90mm、120mm、150mm、180mm、200mm或其它数值。
123.当管体110的管壁厚度为0.2~2.5mm时,可以兼具低过滤阻力和高强度。其中,当管体110的管壁厚度为0.2~1.5mm,优选为0.25~0.8mm时,过滤阻力和强度配合度最好。具体实施时,管体110的管壁厚度可以为0.2mm、0.25mm、0.3mm、0.4mm、0.5mm、0.6mm、0.7mm、0.8mm、1mm、1.2mm、1.5mm、1.8mm、2.1mm、2.3mm、2.5mm或其它数值。
124.所述的薄片状材料111,既可以是背景技术中申请人独有的烧结金属多孔薄膜,也可以其它的烧结金属多孔薄膜,或金属纤维毡,或金属网。当采用烧结金属多孔薄膜时,所述的卷制过程,既可以在烧结之前进行,也可以在烧结之后进行。
125.当所述的薄片状材料111的厚度为0.2~2.5mm时,既具有较高的强度,又具有较好的柔性,能够弯曲和折叠,因此,当管体110仅由一层所述的薄片状材料111构成时,所得滤管100能够保证最好过滤稳定性,此时,薄片状材料111的厚度即为管体110的管壁厚度。
126.当薄片状材料111的孔径在0.3~200μm内,尤其是1~100μm内时,滤管具有较好的过滤精度。当孔径为1.5~50μm,优选为2~30μm时,除了保证较好的过滤精度之外,还能具有较好的透气性。具体实施时,薄片状材料111的孔径可以为0.3μm、0.5μm、1μm、1.5μm、2μm、2.5μm、3μm、5μm、8μm、10μm、15μm、20μm、25μm、30μm、50μm、100μm、150μm、200μm或其它数值。
127.相邻两个滤管100的间距越大,有限安装空间内的滤管100数量约少,相邻两个滤管100的间距越小,则滤管100之间越容易出现粉尘架桥;当相邻两个滤管100的间距为5~100mm时,既可以在有限空间获取较多的过滤面积,也可以降低粉尘在相邻滤管100之间架桥的情况。当相邻两个滤管100的间距为5~60mm,优选为5~40mm,进一步优选为8~30mm时,粉尘架桥和过滤面积的协调性最好。具体实施时,相邻两个滤管100的间距为5mm、6mm、
7mm、8mm、10mm、15mm、20mm、25mm、30mm、40mm、60mm、80mm、100mm或其它数值。
128.当滤管100的长度为100~5000mm时,尤其是100~3000mm时,可以兼具较好的反吹均匀性和较高的过滤面积,并且便于运输。当滤管100的长度为100~2000mm,优选为200~1500mm时,可以显著缩小过滤器体积。具体实施时,滤管100的长度可以为100mm、200mm、300mm、400mm、500mm、800mm、1000mm、1200mm、1500mm、2000mm、2500mm、3000mm或其它数值。
129.图2为滤管100的第二种具体实施方式的结构示意图。如图2所示,在第一种具体实施方式的基础上,当滤管100的长度较长时(例如≥3000mm),为了便于运输,所述滤管100具有通过连接头120首尾连接的至少两个管体110,管体110的长度优选为100~2000mm,进一步优选为200~1500mm;为了便于焊接或粘接,所述连接头120两端具有与管体110匹配的凸起或凹槽。
130.图3为滤管的第三种具体实施方式的结构示意图。如图3所示,在第一种具体实施方式的基础上,对于外径较大的管体110(例如为90~200mm),为了提升管体110的自支撑性,在管体110的内部设有支撑体,支撑体包括支撑环131和与支撑环131内侧连接的龙骨132,所述的龙骨132为沿滤管100轴向分布的杆体。
131.上述的支撑体与现有技术中非金属布袋内置的支撑体具有明显的区别:布袋中的支撑体具有非常多的龙骨132,且龙骨132位于支撑环131的外侧,即龙骨132对滤袋进行支撑。而在本实用新型的滤管100中,设于支撑环131内侧的龙骨132数量可以低至一个,龙骨132仅仅对支撑环131的位置进行固定,这是由于管体110的强度远高于滤袋,因此管体110仅需要支撑环131对其进行简易支撑,这样不仅可以降低重量,而且可以避免因支撑体结构复杂而提升过滤阻力。
132.与现有技术中的金属陶瓷滤芯相比,本实用新型的滤管具有明显优势:首先,管体110由很薄的、可以弯曲折叠的薄片状材料111构成,透气性更好,过滤阻力更低;其次,管体110由薄片状材料111卷制而成,无需模具以及进行复杂的压制成型操作,成本显著降低。
133.与现有技术中的非金属布袋相比,本实用新型的滤管具有明显优势:首先,管体110由薄片状材料111构成,具有更优异的耐高温性能,并且能够达到更高的过滤精度;其次,管体110的管径更小,并且由于金属多孔材料优于布袋材质的强度,管体110内部即使不设置支撑体也能在使用时维持形状。
134.另外,本实用新型提供了上述滤管100的制备方法,包括步骤:将厚度为0.2~2.5mm的薄片状材料111卷制成外径为20~200mm的管体110,接缝112的固定和密封采用焊接或粘接。
135.图4为一种具体实施方式中卷制得到的管体。如图4所示,管体110的接缝112与滤管100的中心轴平行,该管体110通过将宽边与管体110直径匹配的矩形薄片状材料111的长边对接得到。
136.图5为另一种具体实施方式中卷制得到的管体。如图5所示,管体110的接缝112呈螺旋线形状,该管体110采用申请号为2019102093126、名称为“过滤结构以及过滤结构的制备方法”的中国发明专利公布的制备方法制备得到。
137.上述的滤管100可以单独使用,但优选应用到下面的滤芯200和过滤器中,即使用时被阵列密布于一过滤器中用以对待过滤物进行气固分离过滤和/或液固分离过滤。
138.二、滤芯
139.基于传统大直径单管滤芯过滤面积小的缺陷,本实用新型提供了如下的第一种滤芯。
140.图6为第一种滤芯的一种具体实施方式的结构示意图。如图6所示,滤芯200包括至少两个间隔排列的滤管100,其中,滤管100的管体110是由金属或以金属为基体的薄片状材料111以被卷制的方式塑形并对接缝112进行密封加工而成的;并且通过所述卷制成型的管体110的外径仅为20~200mm,优选为20~90mm,进一步优选为20~60mm,更进一步优选为25~50mm;滤芯200还包括固定组件,所述固定组件包括头部固定结构和尾部固定结构;所述头部固定结构包括上接头210,所述上接头210具有与所述滤管100一端相配合的安装孔,所述尾部固定结构包括与所述滤管100另一端相配合的堵头220,上接头210一侧的待过滤气体穿过滤管100的管壁后形成的洁净气体在上接头210的另一侧排出。
141.由此,通过将管径远小于传统大直径单管滤芯200的滤管100集束化为一体,使得在相同的安装空间内,本实用新型的第一种滤芯200具有远高于传统大直径单管滤芯200的过滤面积。
142.当第一种滤芯200中的滤管100进一步具有上述滤管100的使用间距、长度、管壁厚度、材质和孔径中的任意一种时,将取得更好的使用效果。
143.为了解决传统大直径单管滤芯200因受限于过滤器尺寸而导致长度不能进一步增加、以及滤芯200因长度过长而反吹有效性差的技术问题,本实用新型提供了如下的第二种滤芯。
144.滤芯200包括至少两个间隔排列的滤管100以及图6所示的固定组件;其中,滤管100的管体110是由金属或以金属为基体的薄片状材料111以被卷制的方式塑形并对接缝112进行密封加工而成的;并且通过所述卷制成型的管体110的外径仅为20~200mm,优选为20~90mm,进一步优选为20~60mm,更进一步优选为25~50mm,滤管100的长度为100~5000mm,优选为100~3000mm,进一步优选为100~2000mm,更进一步优选为200~1500mm。
145.由此,对于体积较小的过滤器,可以通过滤管100集束化来缩短滤芯200长度以解决滤芯200长度与过滤面积不相匹配的缺陷,并且能取得较均匀的反吹效果。
146.当第二种滤芯200中的滤管100进一步具有上述滤管100的使用间距、管壁厚度、材质和孔径中的任意一种时,将取得更好的使用效果。
147.为了在有限的空间内最大化地获得过滤面积,除了调整相邻滤管100之间的间距之外,还可以通过特殊的排列方式达到过滤面积的最大化。由此,本实用新型提供了如下的第三种滤芯。
148.滤芯200具有多个过滤单元,在滤芯200的横截面上所述多个过滤单元呈同心圆环和/或平行直线排列的,每个过滤单元包括一个或多个间隔排列的滤管100以及图6所示的固定组件;其中,滤管100的管体110是由金属或以金属为基体的薄片状材料111以被卷制的方式塑形并对接缝112进行密封加工而成的;并且通过所述卷制成型的管体110的外径仅为20~200mm,优选为20~90mm,进一步优选为20~60mm,更进一步优选为25~50mm。
149.图7为第三种滤芯200中多个过滤单元同时呈同心圆环排列和平行直线排列的一种具体实施方式的结构示意图。在图7中,在滤芯200的横截面上,相邻三个滤管100的中心的连线为等边三角形。
150.图8为第三种滤芯200中多个过滤单元呈平行直线排列的另一种具体实施方式的
结构示意图。在图8中,在滤芯200的横截面上,相邻四个滤管100的中心的连线为方形。
151.当上接头210的形状为矩形时,优选采用图8所示的滤管100排列方式,可以最大化地在上接头210上安装尽可能多的滤管100。
152.对于圆形和方形的上接头210,当直径和边长相同时以及滤管使用间距相同时,方形的上接头210可以安装更多地滤管100,可以获取更大的过滤面积。
153.当第三种滤芯200中的滤管100进一步具有上述滤管100的使用间距、长度、管壁厚度、材质、孔径中的任意一种时,将取得更好的使用效果。
154.由于滤芯200由多个滤管100集束而成,并且滤管100的管径显著降低,安装面减小,并且可以不再设置内部支撑,因此不宜再采用传统大直径单管滤芯200的固定方式。由此,本实用新型提供了提供了如下的第四种滤芯。
155.滤芯200包括至少两个间隔排列的滤管100以及图6所示的固定组件,即所述安装孔、滤管100和堵头220为至少两组;其中,滤管100的管体110是由金属或以金属为基体的薄片状材料111以被卷制的方式塑形并对接缝112进行密封加工而成的;并且通过所述卷制成型的管体110的外径仅为20~200mm,优选为20~90mm,进一步优选为20~60mm,更进一步优选为25~50mm;上接头210为圆形或矩形,便于制造以及安装。
156.最外侧的安装孔与上接头210边缘之间的间距为1~30mm,优选为2~15mm,由此,有足够的安装面将滤芯200密封安装于过滤器内。具体实施时,所述的间距为1mm、2mm、4mm、6mm、8mm、10mm、12mm、15mm、20mm、25mm、30mm或其它的数值。
157.所述安装孔内壁与所述滤管100的外壁密封连接,密封连接方式为焊接、粘接或胀接;所述安装孔与所述滤管100之间的连接面宽度为5~50mm,优选为8~20mm。
158.所述堵头220与所述滤管100的内壁和/或外壁密封连接,密封连接方式为焊接或粘接,所述堵头220具有与滤管100内壁配合的凸起或与滤管100外壁配合的凹槽;所述堵头220与所述滤管100之间的连接面宽度为5~50mm,优选为8~20mm。
159.上述的连接面越宽,则越容易取得较优的密封效果,但是相应地会增加头部固定结构的厚度,从而增加重量,因此,当连接面宽度为5~50mm时,优选为8~20mm时,可以兼具高密封性和低重量。具体实施时,连接面的宽度为5mm、8mm、10mm、15mm、20mm、30mm、50mm或其它的数值。
160.当采用胀接时,所述头部固定结构还包括设于滤管100内部的胀头211。
161.图9为第四种滤芯200中采用胀接时为了提升密封效果的第一种具体实施方式的结构示意图。如图9所示,所述胀头211与所述滤管100呈曲面接触。
162.图10为第四种滤芯200中采用胀接时为了提升密封效果的第二种具体实施方式的结构示意图。如图10所示,所述头部固定结构还包括设于滤管100与安装孔之间的密封结构212。
163.为了达到最优的密封效果,在提升密封效果的第三种具体实施方式中,所述胀头211与所述滤管100呈曲面接触,同时,所述头部固定结构还包括设于滤管100与安装孔之间的密封结构212。
164.所述的密封结构212优选采用能够承受高温的密封材料。
165.图11为第四种滤芯的第二种具体实施方式的结构示意图。如图11所示,在第一种具体实施方式的基础上,为了防止滤芯200在使用时相邻滤管100在流体作用下摆动而碰
撞,因此滤芯200还包括与堵头220连接的尾架230以及连接上接头210和尾架230的拉杆240,所述拉杆240为三个且呈对称分布。由此,通过尾架230对堵头220进行固定,从而防止滤管100摆动,而拉杆240可以提升滤芯200的强度。
166.当第四种滤芯200中的滤管100进一步具有上述滤管100的使用间距、长度、管壁厚度、材质和孔径中的任意一种时,将取得更好的使用效果。
167.滤管100集束化后,采用传统的文氏管300进行单管反吹,会使反吹结构安装复杂,难以控制。由此,本实用新型提供了第五种滤芯。
168.图12为第五种滤芯的一种具体实施方式的结构示意图。如图12所示,滤芯200具有至少两个间隔排列的滤管100以及图6所示的固定组件;其中,滤管100的管体110是由金属或以金属为基体的薄片状材料111以被卷制的方式塑形并对接缝112进行密封加工而成的;并且通过所述卷制成型的管体110的外径仅为20~200mm,优选为20~90mm,进一步优选为20~60mm,更进一步优选为25~50mm,相邻两个滤管100的间距为5~100mm,优选为5~60mm,进一步优选为5~40mm,更进一步优选为8~30mm;滤芯200还包括文氏管300,所述至少两个间隔排列的滤管100的出气方向均位于文氏管300的内侧,所述文氏管300的内部吹扫气出气口形状以及上接头210的形状同为矩形或同为圆形。
169.由此,通过文氏管300对一个滤芯200中的所有滤管100同时进行反吹,更易控制和安装。
170.所述文氏管300具有依次连接的第一椎管段311、第一竖管段321和第二椎管段312,其中,所述第一椎管段311的横截面面积沿内部吹扫气流动方向递减,所述第二椎管段312的横截面面积沿内部吹扫气流动方向递增。为了便于增设文氏管300后滤芯200的安装,文氏管300还进一步包括第二竖管段322和台阶330,其中,所述第二竖管段322与所述第二椎管段312连接,所述安装孔位于第二竖管段322内侧,所述台阶330设于第二竖管段322外侧底部,所述台阶330与上接头210通过压紧机构密封连接。
171.当台阶330的宽度为1~30mm,优选为2~15mm时,便于安装。具体实施时,台阶330的宽度为1mm、2mm、4mm、6mm、8mm、10mm、12mm、15mm、20mm、25mm、30mm或其它的数值。
172.所述第二椎管段312的侧壁与文氏管300中心轴的夹角为10~30
°
,由此反吹效果最好。具体实施时,所述的夹角为10
°
、12
°
、14
°
、16
°
、18
°
、20
°
、22
°
、23
°
、25
°
、28
°
、30
°
或其它的数值。
173.所述第二椎管段312的内部吹扫气输出端尺寸为输入端尺寸的2~4倍,由此反吹效果最好。具体实施时,所述的倍数为2倍、2.4倍、2.8倍、3.2倍、3.6倍、4倍或其它的数值。
174.当第五种滤芯200中的滤管100进一步具有上述滤管100的管壁厚度、材质、孔径和长度中的任意一种时,将取得更好的使用效果。
175.由于滤管100集束化得到的滤芯200的过滤面积显著提升,因此采用传统反吹清灰方式将需要施加更大的反吹压力,并且由于滤管100间的间距变小,因此粉尘容易在滤管100与滤管100之间架桥,不易反吹去除。由此,本实用新型提供了第六种滤芯。
176.图13为第六种滤芯的一种具体实施方式的结构示意图。如图13所示,滤芯200具有至少两个间隔排列的滤管100以及图6所示的固定组件;其中,滤管100的管体110是由金属或以金属为基体的薄片状材料111以被卷制的方式塑形并对接缝112进行密封加工而成的;并且通过所述卷制成型的管体110的外径仅为20~200mm,优选为20~90mm,进一步优选为
20~60mm,更进一步优选为25~50mm,相邻两个滤管100的间距为5~100mm,优选为5~60mm,进一步优选为5~40mm,更进一步优选为8~30mm;滤芯200还包括清灰结构,所述清灰结构包括对滤管100内部进行清灰的内部清灰机构和对滤管100外部进行清灰的外部清灰机构。
177.由此,通过同时设置内部清灰机构和外部清灰机构,不仅可以显著提升清灰效果,快速恢复气通量,而且可以快速清除滤管100之间的粉尘架桥。
178.所述内部清灰机构包括图12所示的设于滤芯200出气口的文氏管300。
179.所述外部清灰机构包括设于上接头210上的第一清灰孔213。为了便于外部吹扫气的输送,在所述文氏管300的侧壁上设置通孔340,外部吹扫气依次通过该通孔340和第一清灰孔213后对滤管100外表面进行吹扫。所述第一清灰孔213为至少两个,且呈均匀分布,由此,提升外部清灰效果。
180.当第六种滤芯200中的滤管100进一步具有上述滤管100的管壁厚度、材质、孔径和长度中的任意一种时,将取得更好的使用效果。
181.上述的六种滤芯200在具体实施时,滤管100的外径、滤管100的使用间距、滤管100的长度、滤管100的管壁厚度、薄膜状材料111的孔径以及材质的取值同上。
182.上述的六种滤芯200也可以采用图2
‑
5中的任一种滤管100。
183.上述的六种滤芯200在不冲突的情况下,技术方案和技术特征可以相互组合。
184.上述的六种滤芯200,一方面可以应用于对电除尘器800或其它除尘设备的改造,另一方面可以应用于下面的过滤器中用以对待过滤物进行气固分离过滤和/或液固分离过滤,其中,可以根据过滤器壳体417的大小,调节每个滤芯200中滤管100的数量、滤芯200的个数以及滤芯200的长度。
185.三、过滤器
186.首先,为了解决过滤器过滤面积小以及为了提升过滤面积而造成体积过大的技术问题,本实用新型提供了第一种过滤器。
187.图14为第一种过滤器的一种具体实施方式的结构示意图。如图14所示,过滤器包括过滤结构,所述过滤结构包括滤芯200,滤芯200具有至少两个间隔排列的滤管100以及图6所示的固定组件;其中,滤管100的管体110是由金属或以金属为基体的薄片状材料111以被卷制的方式塑形并对接缝进行密封加工而成的;并且通过所述卷制成型的管体110的外径仅为20~200mm,优选为20~90mm,进一步优选为20~60mm,更进一步优选为25~50mm,滤管100的长度为100~5000mm,优选为100~3000mm,进一步优选为100~2000mm,更进一步优选为200~1500mm;过滤器还包括原气腔413和净气腔414,所述过滤结构位于原气腔413和净气腔414之间,所述原气腔413与灰斗416和进气管411相连,所述净气腔414与出气管412相连,原气腔413中的待过滤气体穿过过滤结构的滤芯200后形成的洁净气体进入净气腔414后从出气管412排出,而经滤芯200拦截的粉尘从灰斗416排出。
188.由此,通过采用由管径远小于现有大直径单管滤芯200的滤管100集束化而成的集束式滤芯200,使得在相同的安装空间内,本实用新型的过滤器更容易达到高的过滤面积。同时,对于体积较小的过滤器,可以通过滤芯200集束化来缩短滤芯200长度以解决滤芯200长度与过滤面积不相匹配的缺陷。
189.为了便于粉尘的排出,滤芯200通常竖向设置于原气腔413的上方,但是,滤芯200
既可以朝向上接头210的上方延伸,也可以朝向上接头210的下方延伸。
190.当第一种过滤器中的滤管100进一步具有上述滤管100的使用间距、管壁厚度、材质和孔径中的任意一种时,将取得更好的使用效果。
191.对于体积较大而需要很多滤管100的过滤器,为了简化安装,本实用新型提提供了第二种过滤器。
192.图15为第二种过滤器的一种具体实施方式的结构示意图。如图15所示,过滤器包括过滤结构,过滤结构包括第一支撑结构420和至少两个间隔排列的滤芯200;滤芯200包括至少两个间隔排列的滤管100以及图6所示的固定组件;其中,滤管100的管体110是由金属或以金属为基体的薄片状材料111以被卷制的方式塑形并对接缝112进行密封加工而成的;并且通过所述卷制成型的管体110的外径仅为20~200mm,优选为20~90mm,进一步优选为20~60mm,更进一步优选为25~50mm;所述第一支撑结构420具有第一安装通道421,所述上接头210与所述第一安装通道421密封连接;过滤器还包括图14所示的原气腔413、净气腔414、灰斗416、进气管411和出气管412。
193.由此,采用多个滤芯200可以在确保高过滤面积时降低滤芯200重量,简化安装;同时,对于所需滤管100数量较多的过滤结构,通过分为多个滤芯200分别进行安装还可以确保较均匀的反吹效果。
194.当第二种过滤器中的滤管100进一步具有上述滤管100的使用间距、管壁厚度、材质、长度和孔径中的任意一种时,将取得更好的使用效果。
195.为了便于集束式滤芯200的安装,本实用新型提供了第三种过滤器。
196.第三种过滤器的第一种具体实施方式中,在第二种过滤器的基础上,第三种过滤器中的上接头210与所述第一安装通道421通过压紧机构密封连接。
197.图16为第一支撑结构420的第一种具体实施方式的结构示意图。如图16所示,第一支撑结构420为与过滤器壳体417连接的第一孔板422,所述第一孔板422具有所述的第一安装通道421。
198.图17为第一支撑结构420的第二种具体实施方式的结构示意图。如图17所示,第一支撑结构420为至少两个与过滤器壳体417连接的第一支撑梁423,第一支撑梁423与第一支撑梁423之间形成所述第一安装通道421,此时,第一安装通道421以及过滤器壳体417截面均为矩形。
199.第三种过滤器的第二种具体实施方式中,与第一种具体实施方式的区别在于:过滤器还具有过滤组件,过滤组件包括至少两个间隔排列的过滤结构和第二支撑结构430,所述第二支撑结构430具有第二安装通道431,第一支撑结构420与第二安装通道431同样通过压紧机构密封连接。此时,具有多个滤芯200的过滤结构可以事先组装好后再整体安装于第二支撑结构430的第二安装通道431上。
200.图18为第二支撑结构430的第一种具体实施方式的结构示意图。如图18所示,第二支撑结构430为与过滤器壳体417连接的第二孔板432,所述第二孔板432具有所述的第二安装通道431。
201.图19为第二支撑结构430的第二种具体实施方式的结构示意图。如图19所示,第二支撑结构430为至少两个与过滤器壳体417连接的第二支撑梁433,第二支撑梁433与第二支撑梁433之间形成所述第二安装通道431,此时,第一安装通道421、第二安装通道431以及过
滤器壳体417截面均为矩形。
202.第一支撑结构420与第二安装通道431的连接以及上接头210与第一安装通道421的连接可以采用相同或不相同的压紧机构。
203.以图12所示的含有文氏管300的滤芯200与所述第一安装通道421之间的压紧机构连接为例,压紧机构可以但是不限于分为以下三种具体实施方式:
204.图20
‑
21为压紧机构的第一种具体实施方式的结构示意图。如图20
‑
21所示,压紧机构包括:压紧板441,所述上接头210和台阶330被夹持于所述压紧板441和第一支撑结构420之间;压紧组件,所述压紧组件连接所述压紧板441和第一支撑结构420。其中,图20采用由上至下推入式安装,图21采用由下至上推入式安装。
205.图22为压紧机构的第二种具体实施方式的结构示意图。如图22所示,压紧机构包括:压紧板441,所述台阶330被夹持于所述压紧板441和第一支撑结构420之间;压紧组件,所述压紧组件连接所述压紧板441、上接头210和第一支撑结构420。
206.图20
‑
22中,压紧板441可以同时固定2~4个滤芯200,也可以只固定一个滤芯200;当压紧板441仅与一个滤芯200相连时,优选在压紧板441的底部设置与第一支撑结构420连接的垫板442。
207.图23为压紧机构的第三种具体实施方式的结构示意图。如图23所示,压紧机构包括压紧组件,所述压紧组件连接所述上接头210和第一支撑结构420,所述台阶330被夹持于所述上接头210和第一支撑结构420之间。
208.上述的三种具体实施方式中,压紧组件为螺杆446和螺母444,或为螺栓445和螺母444,当采用螺杆446时,螺杆446的一端应当与最上端或最下端的配合面连接为一体。
209.上述的三种具体实施方式中,在压紧板441以及第一支撑结构420的配合面上设有密封层443。
210.当第一支撑结构420与第二安装通道431采用上述的压紧机构进行连接时,第一支撑结构420与上接头210对应,第二支撑结构430与第一支撑结构420对应。
211.上述安装连接方式可以根据原气腔413和净气腔414的尺寸进行选择。当净气腔414的尺寸足够安装人员进行操作时,优选采用向下推入式安装,此时若上接头210的宽度大于第一安装通道421的宽度,那么上接头210将卡在第一支撑结构420的上方,从而第一支撑结构420将对滤芯200进行预支撑,无需在安装压紧机构时对滤芯200进行托举。
212.当第三种过滤器中的滤管100进一步具有上述滤管100的使用间距、管壁厚度、材质、长度和孔径中的任意一种时,将取得更好的使用效果。
213.由于过滤器的滤管100数量显著增多,并且可以具有多个滤芯200,因此采用传统单管反吹的反吹结构和反吹效果将不再满足工艺需求。由此,本实用新型提供了第四种过滤器。
214.图24为第四种过滤器的第一种具体实施方式的结构示意图。如图24所示,在第二种过滤器或第三种过滤器的基础上,第四种过滤器还包括清灰结构,所述清灰结构包括对滤管100内部进行清灰的内部清灰机构和对滤管100外部进行清灰的外部清灰机构;其中,所述外部清灰机构包括第一机构。
215.图25为第四种过滤器的第二种具体实施方式的结构示意图。如图25所示,与第一种具体实施方式的区别在于:所述外部清灰机构包括第二机构。
216.图26为第四种过滤器的第三种具体实施方式的结构示意图。如图26所示,与第一种具体实施方式的区别在于:所述外部清灰机构包括第一机构和第二机构。
217.所述的内部清灰机构包括包括内部吹扫气输气管451以及图12所示的文氏管300,所述内部吹扫气输气管451贯穿过滤器壳体417,在过滤器内部的内部吹扫气输气管451上设有朝向文氏管300的支管453。
218.所述支管453的出气口与文氏管300之间的间距为3~10cm,具体实施时,所述的间距为3cm、4cm、5cm、6cm、7cm、8cm、9cm、10cm或其它的数值。
219.所述支管453的出气口与文氏管300之间的间距指的是所述支管453的出气口与文氏管300的内部吹扫气进气口所在平面之间的距离。
220.所述的支管453的横截面既可以为圆形,也可以在当文氏管300的横截面为长方形时,支管453的横截面为长方形。
221.在所述内部吹扫气输气管451上设有第一总阀452,所述第一总阀452为脉冲阀。
222.所述第一机构包括出气口位于每个滤芯200中滤管100与滤管100之间的第一外部吹扫气输气管461以及设于上接头210上的第一清灰孔213,文氏管300上设有通孔340,所述第一外部吹扫气输气管461依次穿过过滤器壳体417和通孔340后与所述第一清灰孔213密封连接;第一外部吹扫气输气管461上设有第二总阀462,所述第二总阀462为电磁阀。
223.所述第二机构包括出气口位于滤芯200与滤芯200之间的第二外部吹扫气输气管471以及设于第一支撑结构420上的第二清灰孔,所述第二外部吹扫气输气管471穿过过滤器壳体417后与第二清灰孔密封连接;第二外部吹扫气输气管471上设有第三总阀472,所述第三总阀472为电磁阀。
224.图27为第四种过滤器的第四种具体实施方式的结构示意图。如图27所示,在前述三种具体实施方式的基础上,当滤芯200数量较多时,采用成组反吹的方式,即所述内部清灰机构包括至少两个内部吹扫气输气管451,每个内部吹扫气输气管451上设有至少两个支管453。
225.当第四种过滤器中的滤管100进一步具有上述滤管100的使用间距、管壁厚度、材质、长度和孔径中的任意一种时,将取得更好的使用效果。
226.由于过滤器可以具有多个滤芯200,并且每个滤芯200具有多个滤管100,因此,过滤器出现因滤管100堵塞和损坏而造成系统波动的可能性提升。由此,本实用新型提供了第五种过滤器。
227.图28为第五种过滤器的第一种具体实施方式的结构示意图。如图28所示,在第二种过滤器、第三种过滤器或第四种过滤器的基础上,过滤器还包括压力检测结构;所述压力检测结构包括对过滤前的气体压力进行检测的第一压力检测器481以及对过滤后的气体压力进行检测的第二压力检测器482,其中,在每个滤芯200的出气口均设有图12所示的文氏管300,每个文氏管300的内部反吹气进气口643均设有所述第二压力检测器482;为了达到更好的过滤效果,在进气管411路和出气管412路上设有温度检测器483。
228.由此,通过对每个滤芯200的出气口压力进行检测,有助于针对性对堵塞的滤芯200进行清灰以及对漏气的滤芯200进行维护。
229.在第五种过滤器的第二种具体实施方式中,在第一种具体实施方式的基础上,采用控制器根据压力检测结构的检测结果控制第一总阀452、第二总阀462和第三总阀472的
闭合,从而实现对清灰的自动控制以节约人力。
230.当第五种过滤器中的滤管100进一步具有上述滤管100的使用间距、管壁厚度、材质、长度和孔径中的任意一种时,将取得更好的使用效果。
231.当过滤器采用滤管100集束而成的滤芯200时,可以降低过滤结构的安装高度,增大原气腔413的空间。由此,为了合理利用原气腔413,本实用新型提供了第六种过滤器。
232.图29为第六种过滤器的第一种具体实施方式的结构示意图。如图29所示,过滤器包括原气腔413、净气腔414和位于原气腔413和净气腔414之间的过滤结构,过滤结构包括一个或多个滤芯200以及第一支撑结构420,滤芯200包括至少两个间隔排列的滤管100以及图6所示的固定组件;其中,滤管100的管体110是由金属或以金属为基体的薄片状材料111以被卷制的方式塑形并对接缝112进行密封加工而成的;并且通过所述卷制成型的管体110的外径仅为20~200mm,优选为20~90mm,进一步优选为20~60mm,更进一步优选为25~50mm,滤管100的长度为100~5000mm,优选为100~3000mm,进一步优选为100~2000mm,更进一步优选为200~1500mm;过滤器还包括化学催化和/或物理吸附挥发性气体的净化结构500,所述净化结构500设于净气腔414的出气口与过滤结构之间;净化结构500与过滤器壳体417之间采用可拆卸的连接方式,即在过滤器内部设有支撑条510,所述支撑条510与所述净化结构500之间采用螺栓445和螺母444连接。
233.由此,过滤器兼具过滤和净化功能,占地面积小,可以充分地降低设备成本。
234.图30为第六种过滤器中净化结构500的第一种具体实施方式的结构示意图。如图30所示,所述净化结构500具有进气板530、出气板540以及位于进气板530和出气板540之间的空腔,在进气板530和出气板540上设有通气孔550,在空腔内放置有蜂窝状的隔板560,在隔板560的每个槽内填充有化学催化和/或物理吸附挥发性气体的活性材料。
235.净化结构500的第二种具体实施方式中,所述净化结构500具有透气支撑物和附着在透气支撑物上的化学催化和/或物理吸附挥发性气体的活性材料。当所述净化结构500折叠为波纹状时,可以在有限空间内提升活性工作面;所述透气支撑物采用纤维毡、泡沫状多孔支撑体或支撑网;当所述透气支撑物采用支撑网时,所述支撑网为编织网、冲孔网、斜拉网中的任意一种。
236.净化结构500的第三种具体实施方式中,所述净化结构500具有由化学催化和/或物理吸附挥发性气体的活性材料和粘接剂混合压制成的蜂窝形状。
237.图31为第六种过滤器的第二种具体实施方式的结构示意图。如图31所示,在第一种具体实施方式的基础上,过滤器内设置有支撑板520,净化结构500直接放置于支撑板520上。
238.活性材料的第一种实施方式中,所述的化学催化挥发性气体的活性材料可以但是不限于任一种甲醛催化剂和脱硝催化剂。
239.活性材料的第二种实施方式中,所述的物理吸附挥发性气体的活性材料可以但是不限于活性炭、硅藻土、硅胶、分子筛和活性氧化铝。
240.活性材料的第三种实施方式中,所述的活性材料采用由化学催化挥发性气体的活性材料和物理吸附挥发性气体的活性材料形成的混合材料,例如,申请号为2019110855507、名称为“甲醛净化多孔薄膜及其制备方法”的中国发明专利公布的甲醛净化材料及含有该甲醛净化材料的甲醛净化多孔薄膜,以及申请号为2019110854345、名称为
“
甲醛净化材料制剂、制备方法及应用”的中国发明专利公布的甲醛净化材料及含有该甲醛净化材料的甲醛净化材料制剂。
241.活性材料的第四种实施方式中,所述的活性材料采用由化学催化挥发性气体的活性材料和物理吸附挥发性气体的活性材料形成的复合材料,例如,申请号为2019110855583、名称为“甲醛吸附
‑
催化分解复合材料、制备方法及应用”的中国发明专利公布的甲醛吸附
‑
催化分解复合材料及含有该甲醛吸附
‑
催化分解复合材料的甲醛净化多孔薄膜,以及申请号为2019110854326、名称为“甲醛净化材料制剂、制备方法及应用”的中国发明专利公布的甲醛吸附
‑
催化分解复合材料及含有该甲醛吸附
‑
催化分解复合材料的甲醛净化材料制剂。
242.在净化结构500与过滤结构之间留有无尘腔415,在无尘腔415内设有上述的清灰结构。
243.当第六种过滤器中的滤管100进一步具有上述滤管100的使用间距、管壁厚度、材质和孔径中的任意一种时,将取得更好的使用效果。
244.为了解决因滤芯200出现损坏故障而不能及时有效低成本处理的技术问题,本实用新型提供了第七种过滤器。
245.图32
‑
36为第七种过滤器的第一种具体实施方式的结构示意图。其中,图32为滤芯正常工作时维护结构的使用状态图,图33为滤芯出现故障时维护结构的使用状态图,图34为滤芯正常工作时连杆机构的使用状态图,图35为滤芯出现故障时连杆机构的使用状态图,图36为驱动机构和第一杆体的剖视图。
246.如图32
‑
36所示,过滤器包括过滤结构、清灰结构和维护结构,所述过滤结构包括一个或多个间隔排列的滤芯200;所述清灰结构至少具有上述的内部清灰机构;所述维护结构包括:封堵机构,用于在滤芯200出现故障时对滤芯200出气口进行封堵;以及连杆机构,用于在滤芯200出现故障时控制封堵机构对滤芯200出气口进行封堵;以及驱动机构640,用于在滤芯200出现故障时驱动所述连杆机构;当滤芯200未发生故障时,所述封堵机构设置于内部吹扫气输气管451的支管453上;当滤芯200发生故障时,所述封堵机构对文氏管300的内部吹扫气进气口进行封堵。
247.所述封堵机构包括:堵头220槽,所述堵头220槽底部具有与所述支管453配合的第一通孔340,所述堵头220槽的外部形状与文氏管300的内部吹扫气进气口形状相配合;以及堵头220盖,所述堵头220盖与所述堵头220槽连接,所述堵头220盖具有与所述支管453配合的第二通孔340;以及堵塞球613,所述堵塞球613位于所述堵头220槽和堵头220盖形成的空腔内;当滤芯200未发生故障时,所述支管453依次穿过所述第一通孔340和第二通孔340从而使堵塞球613位于支管453与堵头220槽内壁之间;当滤芯200发生故障时,堵头220槽落入文氏管300的内部吹扫气进气口且支管453与第二通孔340分离从而使堵塞球613堵塞第二通孔340。
248.所述连杆机构包括:连杆624,所述驱动机构640驱动所述连杆624沿支管453的径向运动;以及平行四边形组件620,所述平行四边形组件620与所述封堵机构和连杆(624)连接并随连杆624的运动发生变形;当滤芯200未发生故障时,连杆624和平行四边形组件620静止,所述封堵机构固定于所述支管453上;当滤芯200发生故障时,所述连杆(624)运动从而带动平行四边形组件620发生变形致使封堵机构落入文氏管300的内部吹扫气进气口。
249.所述平行四边形组件620包括依次连接的第一杆体621、第二杆体622和第三杆体623;其中,所述第一杆体621具有固定于所述堵头220盖上的第一转动部631、与所述第二杆体622铰接的第一铰接部632以及与所述连杆624铰接的滑槽633,所述滑槽633位于第一转动部631和第一铰接部632之间;所述第三杆体623具有自由端634、与所述第二杆体622铰接的第二铰接部635以及固定于所述堵头220盖上的第二转动部636,所述第二转动部636位于自由端634和第二铰接部635之间;
250.所述支管453外部设有凸环637,所述第一杆体621和第三杆体623上设有与所述凸环637配合的槽体638,当滤芯200未发生故障时,所述凸环637和槽体638连接,此时,所述第一杆体621与凸环637的第一连接处位于第一转动部631和第一铰接部632之间,所述第三杆体623与凸环637的第二连接处位于第二转动部636与自由端634之间;第一杆体621与连杆624铰接处中心位于第一转动部631中心和第一铰接部632中心连线的中点,第二转动部636中心与第二铰接部635中心的连线长度为第一转动部631中心和第一铰接部632中心连线的四分之一,第一连接处中心以及第二连接处中心的连线穿过第一杆体621与连杆624铰接处中心和支管453的中心。
251.所述驱动机构640包括:气缸641,所述气缸641固定于所述堵头220盖上,所述气缸641具有进气口643和供连杆624运动的通孔340;以及活塞642,所述活塞642的四周与气缸641内壁连接并可沿气缸641内壁运动,所述连杆624一端与活塞642连接,另一端穿过通孔340后与平行四边形组件620连接;以及弹簧644,所述弹簧644连接气缸641内壁和活塞642,所述活塞642的一个侧面与弹簧644连接,另一个侧面与连杆624连接;以及控制气管651,所述控制气管651与所述气缸641的进气口643连接,当滤芯200发生故障时,所述控制气管651输入推动活塞642压缩弹簧644的气体。
252.第七种过滤器的第二种具体实施方式中,为了进一步提升响应速度,在第一种具体实施方式的基础上,进一步采用控制器和图28所示的压力检测结构,控制气管651上设有控制阀652,控制阀652为电磁阀,控制器根据压力检测结构的检测结果控制电磁阀的开合,从而及时封堵故障的滤芯200。
253.所述的第七种过滤器既可以采用传统的大直径单管滤芯200,也可以采用上述的由多个小直径的滤管100集束而成的集束式滤芯200。同时,第七种过滤器可以具有多个滤芯200,当对故障的滤芯200进行封堵时不影响其它正常滤芯200的运行。
254.当采用集束式滤芯200时,当滤管100进一步具有上述滤管100的外径、使用间距、管壁厚度、材质、长度和孔径中的任意一种时,过滤器将取得更好的使用效果。
255.上述的七种过滤器在具体实施时,滤管100的外径、滤管100的使用间距、滤管100的长度、滤管100的管壁厚度、薄膜状材料111的孔径以及材质的取值同上。
256.上述的七种过滤器也可以采用图2
‑
5中的任一种滤管100或图6
‑
13所示的任一种滤芯200。
257.上述的七种过滤器在不冲突的情况下,技术方案和技术特征可以相互组合。
258.四、电除尘器改造
259.以往的电除尘器改造常常因为过滤面积、过滤精度和耐高温性能达不到要求而难以进行。由此,本实用新型提供了由电除尘器改造而成的电改膜除尘器。
260.图37为由电除尘器改造而成的电改膜除尘器的一种实施方式的结构示意图。如图
37所示,电改膜除尘器包括过滤结构,过滤结构设于电除尘器的电极板放置区740内;过滤结构包括一个或多个间隔排列的滤芯200以及第一支撑结构420,第一支撑结构420与电除尘器的壳体417连接并将所述电极板放置区740分隔为分别位于第一支撑结构420两侧的原气腔413和净气腔414,所述原气腔413与电除尘器的进气通道710连接,所述净气腔414与电除尘器的出气通道720连接,原气腔413中的来自于进气通道710的待过滤气体穿过滤芯200后形成的洁净气体进入净气腔414后从出气通道720排出,而经滤芯200拦截的粉尘从电除尘器的灰斗416排出。
261.滤芯200包括至少两个间隔排列的滤管100以及图6所示的固定组件,其中,滤管100的管体110是由金属或以金属为基体的薄片状材料111以被卷制的方式塑形并对接缝112进行密封加工而成的;并且通过所述卷制成型的管体110的外径仅为20~200mm,优选为20~90mm,进一步优选为20~60mm,更进一步优选为25~50mm,滤管100的长度为100~5000mm,优选为100~3000mm,进一步优选为100~2000mm,更进一步优选为200~1500mm。
262.由此,采用由小直径的滤管100集束而成的集束式滤芯200对电极板放置区740进行改造,采用较短的滤管即可充分地满足高过滤面积需求,并且薄片状材料111构成的管体110具有优异的耐高温性能和高过滤精度。可见,本实用新型的电改膜除尘器合理利用了电除尘器的内部空间,具有耐高温性、高过滤精度和高过滤面积,实用性强。
263.为了尽可能充分地利用电极板放置区740空间以及便于过滤结构的安装,过滤结构还包括第一挡板750和第二挡板760;其中,所述第一挡板750下方与所述第一支撑结构420连接,其余方向与电除尘器的壳体连接;所述第二挡板760上方与所述第一支撑结构420连接,其余方向与电除尘器的壳体连接;所述第一支撑结构420水平设置,所述原气腔413位于第一支撑结构420的下方,所述净气腔414位于第一支撑结构420的上方。
264.另外,本实用新型还提供了由电除尘系统改造而成的电改膜除尘系统,用于对含有多个电除尘器800的电除尘系统进行改造。
265.图38为由电除尘系统改造而成的电改膜除尘系统的第一种具体实施方式的结构示意图。如图38所示,并联结构的电改膜除尘系统具有两个电改膜除尘器700和一个未改造的电除尘器800。
266.图39为由电除尘系统改造而成的电改膜除尘系统的第二种具体实施方式的结构示意图。如图39所示,串联结构的电改膜除尘系统具有两个电改膜除尘器700和一个未改造的电除尘器800,其中,电除尘器800设于两个串联的电改膜除尘器700之前,由此,靠前的电除尘器800可以对含尘气体进行预处理;两个电改膜除尘器700的第一支撑结构420连接为一体,第一挡板750与靠近进气通道710的第一支撑结构420连接,第二挡板760与远离进气通道710的第一支撑结构420连接;为了促进过滤后气体的输出,在电极板放置区740上方增设有排气通道770,所述排气通道770与所述出气通道720连接。
267.由电除尘系统改造而成的电改膜除尘系统的第三种具体实施方式中,由三个图39所示的电改膜除尘系统单元并联而成。
268.当上述的滤芯200中的滤管100进一步具有上述滤管100的使用间距、管壁厚度、材质和孔径中的任意一种时,电改膜除尘器和电改膜除尘系统将取得更好的使用效果。
269.具体实施时,滤管100的外径、滤管100的使用间距、滤管100的长度、滤管100的管壁厚度、薄膜状材料111的孔径以及材质的取值同上。
270.电改膜除尘器和电改膜除尘系统也可以采用图2
‑
5中的任一种滤管100或图6
‑
13所示的任一种滤芯200。
271.也可以将电除尘器改造为与图14
‑
36所示的任一种过滤器相同的电改膜除尘器。
272.五、除尘方法
273.为了解决现有除尘方法存在的过滤风速小的技术问题,本实用新型提供了除尘方法。
274.除尘方法的第一种具体实施方式中,采用除尘装置,所述除尘装置包括过滤结构,所述过滤结构包括滤芯200,所述滤芯200包括至少两个间隔排列的滤管100;其中,滤管100的管体110是由金属或以金属为基体的薄片状材料111以被卷制的方式塑形并对接缝112进行密封加工而成的;并且通过所述卷制成型的管体110的外径仅为20~200mm,优选为20~90mm,进一步优选为20~60mm,更进一步优选为25~50mm,相邻两个滤管100的间距为5~100mm,优选为5~60mm,进一步优选为5~40mm,更进一步优选为8~30mm;过滤风速为0.8~2m/min,待过滤气体温度≤800℃。
275.由于采用的滤芯200的过滤面积显著提升,因此,过滤风速可以达到0.8~2m/min,并且当采用上述的薄片状材料111时,可以处理温度高达800℃的待过滤气体。具体实施时,过滤风速为0.8m/min、1m/min、1.1m/min、1.2m/min、1.4m/min、1.5m/min、1.7m/min、1.9m/min、2m/min或其他数值,待过滤气体温度为100℃、180℃、200℃、260℃、300℃、400℃、500℃、600℃、800℃或其它数值。
276.通过调整薄片状材料111的孔径,过滤得到的洁净气体的含尘量可以为1mg/nm3、2mg/nm3、4mg/nm3、5mg/nm3、7mg/nm3、8mg/nm3、10mg/nm3或≤20mg/nm3的其它数值。
277.第一种应用场景中,用于处理炼钢转炉高温烟气,待过滤气体温度为180~250℃,过滤风速为1~2m/min,过滤得到的洁净气体的含尘量≤5mg/nm3。
278.第二种应用场景中,用于处理有色金属冶炼炉气,待过滤气体温度为200~500℃,过滤风速为0.8~1.5m/min,过滤得到的洁净气体的含尘量≤10mg/nm3。
279.第三种应用场景中,用于处理钼焙烧高温炉气,待过滤气体温度为200~400℃,过滤风速为0.8~1.5m/min,过滤得到的洁净气体的含尘量≤10mg/nm3。
280.第四种应用场景中,用于处理高温脱砷烟气,待过滤气体温度为300~500℃,过滤风速为0.8~1.5m/min,过滤得到的洁净气体的含尘量≤5mg/nm3。
281.除尘方法的第二种具体实施方式中,在第一种实施方式的基础上,在过滤之前对待过滤气体进行预处理,预处理采用重力除尘器、旋风除尘器、电除尘器中的任意几种。
282.当滤管100进一步具有上述滤管100的管壁厚度、长度、材质和孔径中的任意一种时,除尘方法将取得更好的使用效果。
283.具体实施时,滤管100的外径、滤管100的使用间距、滤管100的长度、滤管100的管壁厚度、薄膜状材料111的孔径以及材质的取值同上。
284.除尘装置也可以采用图2
‑
5中的任一种滤管100或图6
‑
13所示的任一种滤芯200。
285.除尘装置也可以是图14
‑
36所示的任一种过滤器,也可以是图37
‑
39所示的电改膜除尘器或电改膜除尘系统。
286.以上对本实用新型的有关内容进行了说明。本领域普通技术人员在基于这些说明的情况下将能够实现本实用新型。基于本实用新型的上述内容,本领域普通技术人员在没
有做出创造性劳动的前提下所获得的所有其他实施例,都应当属于本实用新型保护的范围。