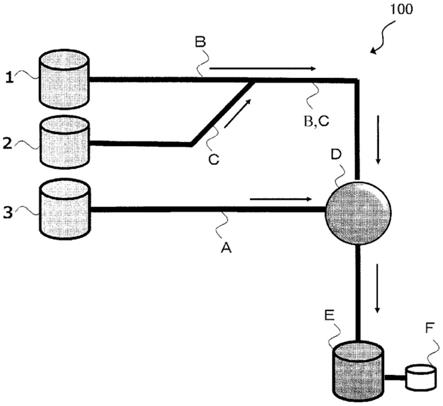
1.本发明涉及一种能够连续合成将单金属微粒子或固溶体微粒子负载于载体粒子的负载催化剂(以下,也称为负载催化剂)的负载型催化剂合成装置及能够连续合成单金属微粒子或固溶体微粒子的微粒子合成装置。
背景技术:2.一般来说,汽车等的排气净化处理中所使用的催化剂或化合物合成等各种反应处理中所使用的催化剂中,广泛地利用含有稀有金属的催化剂。但是,由于稀有金属价格高且产出量少,因此一边抑制稀有金属的使用量一边关注高活性的固溶体微粒子,正在推进固溶体微粒子的开发。
3.为了合成此类固溶体微粒子,实施批次式合成,也就是说,通过在将三乙二醇等高沸点的还原剂加热至高温的状态下慢慢地添加贵金属盐溶液而进行合成。但是,由于欲合成的还原剂溶液中所存在的贵金属浓度逐渐地变浓,因此存在引起粒径的粗大化等问题,较难量产小粒径的合金。
4.近年来,一边减少贵金属使用量一边谋求活性更高的催化剂,工业上也要求量产1nm以下的固溶体微粒子负载于载体粒子的负载催化剂。作为防止此类固溶体微粒子的粗大化的方法,有使用微反应器的固溶体微粒子的合成方法(例如,参照专利文献1)。于微反应器内在存在还原剂的条件下进行加压而使钯金属盐溶液与钌金属盐溶液反应,由此生成钯与钌的固溶体微粒子。
5.[背景技术文献]
[0006]
[专利文献]
[0007]
[专利文献1]日本专利特开2018-141235号公报
技术实现要素:[0008]
[发明要解决的问题]
[0009]
但是,专利文献1中所记载的技术中,平均粒径至少为2.2nm,在用作催化剂的情况下,为了使粒子活性化,要求以表面积变得更大的方式实现0.5~2nm的小粒子化、优选为1nm以下的小粒子化。此外,并没有示出负载催化剂的合成实施例,进一步来说,没有示出能够将负载催化剂的合成所需的载体粒子稳定地导入至系统内的结构。
[0010]
在专利文献1中,虽获得了达成固溶体微粒子的大量合成的成果,但固溶体微粒子的粒径也需要进一步小粒径化。也就是说,存在下述课题:为了使粒径变小而需要的还原力不足,必须在进一步提高还原力的状态下进行反应。进一步来说,存在量产装置必须实现进一步的小粒径化的课题。
[0011]
进一步来说,专利文献1中,负载催化剂的合成并非在装置内进行。进一步来说,就一边导入载体粒子一边稳定地量产负载催化剂的方面来说,专利文献1中存在未考虑背压阀中的载体粒子的流通的致命性缺陷。也就是说,存在下述课题:当已将作为固体粒子的载
体粒子导入至装置时,载体粒子在背压阀发生滞留、堵塞,使得无法以所需的流速、压力、温度进行合成反应。进一步来说,存在量产装置必须解决载体粒子的滞留、堵塞的课题。
[0012]
因此,本发明的目的在于提供一种在将单金属微粒子或固溶体微粒子负载于载体粒子的负载催化剂中,能实现单金属微粒子或固溶体微粒子的0.5~2nm左右的小粒径化,且能够稳定地量产负载催化剂的负载型催化剂合成装置。此外,提供一种能实现单金属微粒子或固溶体微粒子的0.5~2nm左右的小粒径化,且能够稳定地量产这些微粒子的微粒子合成装置。
[0013]
[解决问题的技术手段]
[0014]
本发明人等为了解决所述课题,进行锐意研究,结果发现通过设置使下述液体合流之后进行反应、进一步在回收所获得的反应产物的部位控制压力的机构可解决所述课题,并完成本发明,所述液体是指:(1)含有还原剂的液体及含有构成单金属微粒子或者固溶体微粒子的元素的液体,或(2)含有还原剂的液体、含有构成负载的单金属微粒子或者固溶体微粒子的元素的液体及含有载体粒子的液体。也就是说,本发明的负载型催化剂合成装置的特征在于:至少具有:含有还原剂的液体的第1供给源;含有构成负载的单金属微粒子或者固溶体微粒子的元素的液体的第2供给源;含有载体粒子的液体的第3供给源;使所述含有还原剂的液体、所述含有构成负载的单金属微粒子或者固溶体微粒子的元素的液体及所述含有载体粒子的液体合流的反应部(d);连结所述第1供给源与所述反应部(d)的送液路径(a);连结所述第2供给源与所述反应部(d)的送液路径(b);连结所述第3供给源与所述反应部(d)的送液路径(c)、及经由配管连接于所述反应部(d),回收所生成的反应物的回收部(e);且进一步具有连接于所述回收部(e)的压力调整机构(f)。
[0015]
本发明的负载型催化剂合成装置中,优选为具有将流经所述送液路径(b)或所述送液路径(c)的任一者或两者的液体向一方向移送的机构(g)。在送液路径(b)及送液路径(c)中,能够稳定地限定含有构成负载的单金属微粒子或者固溶体微粒子的元素的液体及含有载体粒子的液体的流量及流速,因此能够稳定地进行负载催化剂的合成。
[0016]
本发明的负载型催化剂合成装置中,优选为所述送液路径(c)具有搅拌机构(h)。能够抑制比重大于水的载体粒子在泵内发生沉降,将移送至反应部的载体粒子的浓度固定。
[0017]
本发明的负载型催化剂合成装置中,优选为在所述送液路径(a)中具有加热保温机构(i)。通过将含有还原剂的液体从室温加热至反应所需的温度,从而能够赋予还原所需的热量。
[0018]
本发明的负载型催化剂合成装置中,优选为在所述反应部(d)与所述回收部(e)之间具有冷却机构(j2)。通过使反应部(d)中所产生的含有负载催化剂的液体急冷,从而能够抑制单金属微粒子彼此的熔结或者固溶体微粒子彼此的熔结。
[0019]
本发明的微粒子合成装置的特征在于:至少具有:含有还原剂的液体的第1供给源;含有构成单金属微粒子或者固溶体微粒子的元素的液体的第2供给源;使所述含有还原剂的液体、及所述含有构成单金属微粒子或者固溶体微粒子的元素的液体合流的反应部(d);连结所述第1供给源与所述反应部(d)的送液路径(a);连结所述第2供给源与所述反应部(d)的送液路径(b);及经由配管连接于所述反应部(d),回收所生成的反应物的回收部(e);且进一步具有连接于所述回收部(e)的压力调整机构(f)。
[0020]
本发明的微粒子合成装置中,优选为具有将流经所述送液路径(b)的液体向一方向移送液体的机构(g)。在送液路径(b)中,能够稳定地限定含有构成单金属微粒子或者固溶体微粒子的元素的液体的流量及流速,因此能够稳定地进行微粒子的合成。
[0021]
本发明的微粒子合成装置中,优选为在所述送液路径(a)中具有加热保温机构(i)。通过将含有还原剂的液体从室温加热至反应所需的温度,从而能够赋予还原所需的热量。
[0022]
本发明的微粒子合成装置中,优选为在所述反应部(d)与所述回收部(e)之间具有冷却机构(j2)。通过使反应部(d)中所产生的含有单金属微粒子或者固溶体微粒子的液体急冷,从而能够抑制单金属微粒子彼此的熔结或者固溶体微粒子彼此的熔结。
[0023]
[发明的效果]
[0024]
根据本发明,可提供一种将单金属微粒子或固溶体微粒子负载于载体粒子的负载催化剂中能实现单金属微粒子或固溶体微粒子的0.5~2nm左右的小粒径化,且能够稳定地量产负载催化剂的负载型催化剂合成装置。此外,可提供一种能实现单金属微粒子或固溶体微粒子的0.5~2nm左右的小粒径化,且能够稳定地量产这些微粒子的微粒子合成装置。
附图说明
[0025]
图1是本实施方式的负载型催化剂合成装置的第一例的概略图。
[0026]
图2是本实施方式的负载型催化剂合成装置的第二例的概略图。
[0027]
图3是本实施方式的负载型催化剂合成装置的第三例的概略图。
[0028]
图4(a)是表示将液体向一方向移送的机构(g)的一例的概略图,且是按下柱塞时的概略图。
[0029]
图4(b)是表示将液体向一方向移送的机构(g)的一例的概略图,且是上推柱塞时的概略图。
[0030]
图5是表示将液体向一方向移送的机构(g)进一步具有搅拌机构(h)时的一例的概略图。
[0031]
图6是在本实施方式的负载型催化剂合成装置的第二例中进一步设置有加热保持机构(i)及冷却机构(j1、j2)的负载型催化剂合成装置的第四例的概略图。
[0032]
图7是本实施方式的微粒子合成装置的第一例的概略图。
[0033]
图8是本实施方式的微粒子合成装置的第二例的概略图。
[0034]
图9是在本实施方式的微粒子合成装置的第二例中进一步设置有加热保持机构(i)及冷却机构(j1、j2)的微粒子合成装置的第三例的概略图。
具体实施方式
[0035]
以下,表示实施方式,对本发明详细地进行说明,但本发明不受这些记载限定地解释。只要发挥本发明的效果,那么实施方式也可以作各种变形。
[0036]
(负载型催化剂合成装置)
[0037]
参照图1,对负载型催化剂合成装置进行说明。本实施方式的负载型催化剂合成装置100至少具有:含有还原剂的液体的第1供给源3;含有构成负载的单金属微粒子或者固溶体微粒子的元素的液体的第2供给源1;含有载体粒子的液体的第3供给源2;使含有还原剂
的液体、含有构成负载的单金属微粒子或者固溶体微粒子的元素的液体及含有载体粒子的液体合流的反应部(d);连结第1供给源3与反应部(d)的送液路径(a);连结第2供给源1与反应部(d)的送液路径(b);连结第3供给源2与反应部(d)的送液路径(c);及经由配管连接于反应部(d),回收所生成的反应物的回收部(e);且进一步具有连接于回收部(e)的压力调整机构(f)。根据本实施方式的负载型催化剂合成装置,能够在不使用背压阀的情况下进行装置内的压力控制,不易引起作为课题的装置内浆料的堵塞,能够稳定地进行负载催化剂的合成。
[0038]
本实施方式的负载型催化剂合成装置中,在反应部(d)中,能够还原含有构成负载的单金属微粒子或者固溶体微粒子的元素的液体,形成单金属微粒子或者固溶体微粒子,将通过还原制得的单金属微粒子或者固溶体微粒子负载于载体粒子。
[0039]
含有还原剂的液体的第1供给源3优选为储存含有还原剂的液体的容器。作为还原剂,使用:甲醇、乙醇、正丙醇、异丙醇、正丁醇、乙二醇、三乙二醇、1,3-丙二醇、二乙二醇等具有还原性的有机溶剂,可利用水等溶剂使这些有机溶剂稀释,进一步来说,也可为了调节还原性而在水等溶剂中添加碱、有机酸等。
[0040]
含有构成负载的单金属微粒子或者固溶体微粒子的元素的液体的第2供给源1优选为储存含有构成负载的单金属微粒子或者固溶体微粒子的元素的液体的容器。所谓构成单金属微粒子或者固溶体微粒子的元素,可例举:钯、钌、铑、银、锇、铱、铂、金、钼、铼、钨、3d过渡元素、碳、硼等。如果制造单金属微粒子,那么使用含有这些元素之中的1种金属元素的原料。利用水等液体将该原料制备成原料溶液。如果制造固溶体微粒子,那么使用含有这些元素之中的2种以上的金属元素的原料。利用水等液体将这些金属原料制备成原料溶液。作为2种以上的金属元素的组合,有在合金状态图中固溶的组合、不固溶的组合、成为金属间化合物的组合。
[0041]
含有载体粒子的液体的第3供给源2优选为储存含有载体粒子的液体的容器。作为载体粒子的种类,可例举:二氧化硅、氧化铝、氧化铈、氧化锆、氧化铈氧化锆、二氧化钛、氧化镁、氧化锡、活性碳、碳黑、乙炔黑、纳米碳管、碳纳米纤维、碳纳米角等。含有载体粒子的液体是利用分散介质使载体粒子分散而成的液体,作为分散介质,可例举水等。对于分散介质,可适当使用甲醇、乙醇、正丙醇、异丙醇、正丁醇、乙二醇、三乙二醇、1,3-丙二醇、二乙二醇等具有还原性的有机溶剂,为了适当调节还原性也可以在分散介质等中添加碱、有机酸等。
[0042]
连结第1供给源3与反应部(d)的送液路径(a)包含配管。作为流经配管内的液体的流量调整方法,有将第1供给源3配置于高于反应部(d)的位置而利用高低差的方法。在这种情况下,可仅利用配管搬送含有还原剂的液体。此时,也可以在送液路径(a)配置针阀、停止阀等限制流量的阀。
[0043]
连结第2供给源1与反应部(d)的送液路径(b)包含配管。作为流经配管内的液体的流量调整方法,有将第2供给源1配置于高于反应部(d)的位置而利用高低差的方法。此时,与送液路径(a)同样地,也可以在送液路径(b)配置针阀、停止阀等限制流量的阀。
[0044]
连结第3供给源2与反应部(d)的送液路径(c)包含配管。作为流经配管内的液体的流量调整方法,有将第3供给源2配置于高于反应部(d)的位置而利用高低差的方法。此时,与送液路径(a)同样地,也可以在送液路径(c)配置针阀、停止阀等限制流量的阀。
[0045]
送液路径(b)与送液路径(c)也可以分别各自连接于反应部(d)。如图1所示那样,也可以在到达反应部(d)之前使送液路径(b)与送液路径(c)合流,将合流的共享路径(b,c)连接于反应部(d)。
[0046]
本实施方式的负载型催化剂合成装置中,优选为具有将流经送液路径(b)或送液路径(c)的任一者或两者的液体向一方向移送的机构(g)。图2所示的负载型催化剂合成装置200中,示出在送液路径(b)及送液路径(c)的两者具有机构(g)的形态。在该形态中,于送液路径(b)及送液路径(c),能够稳定地限定含有构成负载的单金属微粒子或者固溶体微粒子的元素的液体及含有载体粒子的液体的流量及流速,因此能够稳定地进行负载催化剂的合成。
[0047]
如图2所示那样,本实施方式的负载型催化剂合成装置200也可以进一步具有将流经送液路径(a)的液体向一方向移送的机构(g)。在该形态中,于送液路径(a),能够稳定地限定含有还原剂的液体的流量及流速,因此能够稳定地进行负载催化剂的合成。
[0048]
机构(g)是流经配管内的液体的流量调整机构,例如为:柱塞、汽缸或调节器。
[0049]
如图3所示那样,本实施方式的负载型催化剂合成装置300中,也可以具有储存含有构成负载的单金属微粒子或者固溶体微粒子的元素的液体与含有载体粒子的液体的混合液的第4供给源4、与送液路径(b)及送液路径(c)的共享路径(b,c),来代替如图2所示般的第2供给源1与送液路径(b)及第3供给源2与送液路径(c)。
[0050]
其次,参照图4(a)及图4(b)。图4(a)及图4(b)是表示将液体向一方向移送的机构(g)的一例的概略图,图4(a)是按下柱塞时的概略图,图4(b)上推柱塞时的概略图。如图4(a)所示那样,当按下柱塞12时,流出侧的球10b使流出侧配管11b封闭,吸入侧的球10a使吸入侧配管11a开放。这样的结果是,在空间13内的容积变大,同时,液体的贮存量变大。其次,如图4(b)所示那样,当上推柱塞12时,流出侧的球10b使流出侧配管11b开放,吸入侧的球10a使吸入侧配管11a封闭。这样的结果是,在空间13内的容积变小,同时,液体的贮存量变小,变少的液体的贮存量成为自流出侧流出的液体的流出量。在送液路径(b)、送液路径(c)及送液路径(a)中,通过机构(g)调整送液量,抑制逆流,不会产生律动,且能够将液体连续地以相同流速向反应部(d)移送。柱塞可为单柱塞方式也可为双柱塞方式,也可以使用滚子泵方式、注射泵方式。图4(a)及图4(b)中,也可以使用电磁阀或球阀,代替使用吸入侧的球10a及流出侧的球10b的止回阀。此外,也可以使用隔膜,代替柱塞。
[0051]
本实施方式的负载型催化剂合成装置中,送液路径(c)优选为具有搅拌机构(h)。当将载体粒子从送液路径(c)向反应部(d)移送时,虽设置有机构(g),但在机构(g)所在的部位,载体粒子有时下沉于下方。因此,通过在机构(g)设置搅拌机构(h),能够抑制载体粒子下沉于机构(g)所在部位的下方,从而能将载体粒子均匀地移送至反应部(d)。图5是表示将液体向一方向移送的机构(g)进一步具有搅拌机构(h)时的一例的概略图。作为搅拌机构(h),是图5所示的搅拌叶片14。作为搅拌机构(h)的另一例,可例举:液体循环装置、搅拌器等。
[0052]
反应部(d)是使含有还原剂的液体、含有构成负载的单金属微粒子或者固溶体微粒子的元素的液体及含有载体粒子的液体合流至1处的反应容器。也可以通过对反应容器的形状、容积、容器内的液体的流动方式进行多种选择、调整,而控制反应条件。反应容器中也包含配管形状的容器。反应部(d)优选为压力容器,使得能于加压条件下进行反应。进一
步来说,反应部(d)也可为对进入至其中的液体进行加热的加热机构,加热机构例如为电阻发热体、远红外线照射装置、微波照射装置、直接通电加热、介电加热、感应加热、电炉、加热器等。
[0053]
回收部(e)是经由配管连接于反应部(d),回收所生成的反应物的容器。回收部(e)优选为压力容器,使得反应部(d)中能在加压条件下进行反应。
[0054]
压力调整机构(f)连接于回收部(e)。压力调整机构(f)也可以经由配管连接于回收部(e)。此外,压力调整机构(f)也可以以一体化的状态连接于回收部(e)。压力调整机构(f)例如有柱塞、汽缸、调节器等加压、减压机构,优选为不易引起装置的磨耗或堵塞的汽缸。通过压力调整机构(f),调整回收部(e)内部的压力、及经由配管连接于回收部(e)的反应部(d)内的压力。由于反应部(d)上游侧的送液路径(a)、送液路径(b)、送液路径(c)均连接于反应部(d),因此路径的内部空间成为加压状态,在高于该压力的压力下液体朝向反应部(d)送液。当在回收部(e)回收具有负载有单金属微粒子或者固溶体微粒子的载体的液体时,通过利用压力调整机构(f)调整回收部(e)内的压力,从而调整反应部(d)内的压力,这样的结果是,有助于反应部(d)中构成单金属微粒子或者固溶体微粒子的元素的还原。为了使得条件可有助于还原,优选为赋予高能量,能够通过压力调整机构(f)调整回收部(e)内的压力以使反应部(d)中还原剂保持高温且不会沸腾。
[0055]
如图6所示那样,本实施方式的负载型催化剂合成装置400中,优选为在送液路径(a)中具有加热保温机构(i)。通过将含有还原剂的液体从室温加热至反应所需的温度,从而能够赋予还原所需的热量,且能够提高还原剂的反应性。作为加热保持机构(i),有通过直接通电加热、介电加热、感应加热、利用电炉、加热器的加热等,更佳为避免因向配管的传热造成的预料之外的金属盐的还原等、且温度控制的响应性较高的直接通电加热、介电加热或感应加热。
[0056]
如图6所示那样,本实施方式的负载型催化剂合成装置400中,在反应部(d)与回收部(e)之间优选为具有冷却机构(j2)。通过使反应部(d)中所产生的含有负载催化剂的液体急冷,从而能够抑制单金属微粒子的熔结或者固溶体微粒子彼此的熔结。为了更加抑制粒子彼此的熔结,冷却机构(j2)优选为设置于尽可能靠近反应部(d)的位置,更佳为冷却机构(j2)的端部中的靠近反应部(d)的端部设置于相对于反应部(d)距离1~1000mm的位置。冷却机构(j2)设置于反应部(d)与回收部(e)之间,也可以除了冷却机构(j2)以外进一步设置有冷却机构(j1)。含有构成负载的纳米粒子的元素的液体及含有载体粒子的液体通过送液路径(b)及送液路径(c)导入至反应部(d)时,也可以在即将导入至反应部(d)之前设置冷却机构(j1)。为了防止因传热的影响造成预料之外的金属的析出,也可以视需要在送液路径(b)及/或送液路径(c)设置冷却机构(j1)。作为冷却方式,可例举:水冷、气冷等。
[0057]
作为使用本实施方式的负载型催化剂合成装置的负载催化剂的制作例,如下所述:将含有含乙醇的水溶液的液体作为还原剂加入至第1供给源3,在移送还原剂的送液路径(a)中,通过加热保温机构(i)使用加热器使其从室温加热至450℃,并移送至反应部(d)。将pd原料溶液与ru原料溶液作为含有负载的单金属元素的液体加入至第2供给源1,经由送液路径(b)将其移送至反应部(d)。将含有氧化铝的液体作为负载的载体加入至第3供给源2,一边运转将流动的液体向一方向移送的机构(g)、搅拌机构(h),一边将其移送至反应部(d)。使含乙醇的水溶液、pd原料溶液、ru原料溶液、氧化铝在反应部(d)合流之后,通过含乙
醇的水溶液使得pd原料、ru原料在氧化铝上同时还原,且pd元素与ru元素结合,形成固溶体微粒子,固溶体微粒子负载于氧化铝上,形成负载催化剂。对于所形成的负载催化剂使用冷却机构(j2)的水冷急冷恢复至室温。通过急冷抑制粒子彼此的熔结。经急冷的负载催化剂被回收至连接于压力调整机构(f)的回收部(e)内,并且通过将压力控制为0.1mpa~138mpa,从而抑制还原剂的沸腾,提高压力,由此使得整个装置的压力提高,提升反应部(d)内的反应的活性。
[0058]
(微粒子合成装置)
[0059]
其次,对微粒子合成装置进行说明,由于包含与负载型催化剂合成装置共通的内容,因此以不同的方面为中心进行说明。
[0060]
首先,参照图7,对微粒子合成装置进行说明。本实施方式的微粒子合成装置500至少具有:含有还原剂的液体的第1供给源3;含有构成单金属微粒子或者固溶体微粒子的元素的液体的第2供给源1;使所述含有还原剂的液体、及所述含有构成单金属微粒子或者固溶体微粒子的元素的液体合流的反应部(d);连结所述第1供给源3与所述反应部(d)的送液路径(a);连结所述第2供给源1与所述反应部(d)的送液路径(b);及经由配管连接于所述反应部(d),回收所生成的反应物的回收部(e);且进一步具有连接于所述回收部(e)的压力调整机构(f)。根据本实施方式的微粒子合成装置,能够在不使用背压阀的情况下进行装置内的压力控制,不易引起作为课题的装置内的单金属微粒子或者固溶体微粒子的堵塞,能够稳定地进行单金属微粒子或者固溶体微粒子的合成。
[0061]
本实施方式的微粒子合成装置中,在反应部(d)中,能够使含有构成单金属微粒子或者固溶体微粒子的元素的液体还原,形成单金属微粒子或者固溶体微粒子。
[0062]
关于第1供给源3、还原剂的种类、第2供给源1、送液路径(a)、送液路径(b)、反应部(d)、回收部(e)及压力调整机构(f),与本实施方式的负载型催化剂合成装置的情况同样。此外,含有构成单金属微粒子或者固溶体微粒子的元素的液体的种类与在本实施方式的负载型催化剂合成装置的情况中的“含有构成负载的单金属微粒子或者固溶体微粒子的元素的液体的种类”同样。
[0063]
本实施方式的微粒子合成装置中,优选为具有将流经所述送液路径(b)的液体向一方向移送液体的机构(g)。在送液路径(b)中,能够稳定地限定含有构成单金属微粒子或者固溶体微粒子的元素的液体的流量及流速,因此能够稳定地进行微粒子的合成。图8所示的负载型催化剂合成装置600中,示出在送液路径(b)及送液路径(a)的两者具有机构(g)的形态。在该形态中,于送液路径(b)及送液路径(a),能够稳定地限定含有构成单金属微粒子或者固溶体微粒子的元素的液体及含有还原剂的液体的流量及流速,因此能够稳定地进行微粒子的合成。
[0064]
关于机构(g)的具体的结构,与本实施方式的负载型催化剂合成装置的情况同样。
[0065]
本实施方式的微粒子合成装置中,如图9所示那样,在送液路径(a)中优选为具有加热保温机构(i)。通过将含有还原剂的液体从室温加热至反应所需的温度,从而能够赋予还原所需的热量。关于加热保温机构(i)的具体的结构,与本实施方式的负载型催化剂合成装置的情况同样。
[0066]
本实施方式的微粒子合成装置中,如图9所示那样,优选为在反应部(d)与回收部(e)之间具有冷却机构(j2)。通过使反应部(d)中所产生的含有单金属微粒子或者固溶体微
粒子的液体急冷,从而能够抑制粒子彼此的熔结。关于冷却机构(j2)的具体的结构,与本实施方式的负载型催化剂合成装置的情况同样。也可以除了冷却机构(j2)以外,进一步设置有冷却机构(j1)。含有构成纳米粒子的元素的液体通过送液路径(b)导入至反应部(d)时,也可以在即将导入至反应部(d)之前设置冷却机构(j1)。为了预防因传热的影响造成预料的外的金属的析出,也可以视需要在送液路径(b)设置冷却机构(j1)。关于冷却机构(j1)的具体的结构,与本实施方式的负载型催化剂合成装置的情况同样。
[0067]
作为使用本实施方式的微粒子合成装置的微粒子的制作例,将含有含乙醇的水溶液的液体作为还原剂加入至第1供给源3,在移送还原剂的送液路径(a)中,通过加热保温机构(i)使用加热器使其从室温加热至450℃,并移送至反应部(d)。将pd原料溶液与ru原料溶液作为含有构成固溶体微粒子的元素的液体加入至第2供给源1,经由送液路径(b)将其移送至反应部(d)。使含乙醇的水溶液、pd原料溶液与ru原料溶液在反应部(d)合流之后,通过含乙醇的水溶液使得pd原料及ru原料同时还原,且pd元素与ru元素结合,形成固溶体微粒子。所形成的固溶体微粒子通过冷却机构(j2)的水冷而急冷恢复至室温。通过急冷而抑制粒子彼此的熔结。经急冷的固溶体微粒子回收至连接于压力调整机构(f)的回收部(e)内,并且通过将压力控制为0.1mpa~138mpa,从而抑制还原剂的沸腾,提高压力,由此使得整个装置的压力提高,提升反应部(d)内的反应的活性。
[0068]
[符号的说明]
[0069]
100,200,300,400 负载型催化剂合成装置
[0070]
500,600,700
ꢀꢀꢀꢀꢀ
微粒子合成装置
[0071]aꢀꢀꢀꢀꢀꢀꢀꢀꢀꢀꢀꢀꢀꢀꢀ
连结第1供给源与反应部的送液路径
[0072]bꢀꢀꢀꢀꢀꢀꢀꢀꢀꢀꢀꢀꢀꢀꢀ
连结第2供给源与反应部的送液路径
[0073]cꢀꢀꢀꢀꢀꢀꢀꢀꢀꢀꢀꢀꢀꢀꢀ
连结第3供给源与反应部的送液路径
[0074]
(b,c)
ꢀꢀꢀꢀꢀꢀꢀꢀꢀꢀꢀ
送液路径(b)及送液路径(c)的共享路径
[0075]dꢀꢀꢀꢀꢀꢀꢀꢀꢀꢀꢀꢀꢀꢀꢀ
反应部
[0076]eꢀꢀꢀꢀꢀꢀꢀꢀꢀꢀꢀꢀꢀꢀꢀ
回收部
[0077]fꢀꢀꢀꢀꢀꢀꢀꢀꢀꢀꢀꢀꢀꢀꢀ
压力调整机构
[0078]gꢀꢀꢀꢀꢀꢀꢀꢀꢀꢀꢀꢀꢀꢀꢀ
将液体向一方向移送的机构
[0079]hꢀꢀꢀꢀꢀꢀꢀꢀꢀꢀꢀꢀꢀꢀꢀ
搅拌机构
[0080]iꢀꢀꢀꢀꢀꢀꢀꢀꢀꢀꢀꢀꢀꢀꢀ
加热保温机构
[0081]
j1,j2
ꢀꢀꢀꢀꢀꢀꢀꢀꢀꢀꢀ
冷却机构
[0082]1ꢀꢀꢀꢀꢀꢀꢀꢀꢀꢀꢀꢀꢀꢀꢀ
含有构成单金属微粒子或者固溶体微粒子的元素的液体的第2供给源
[0083]2ꢀꢀꢀꢀꢀꢀꢀꢀꢀꢀꢀꢀꢀ
含有载体粒子的液体的第3供给源
[0084]3ꢀꢀꢀꢀꢀꢀꢀꢀꢀꢀꢀꢀꢀ
含有还原剂的液体的第1供给源
[0085]4ꢀꢀꢀꢀꢀꢀꢀꢀꢀꢀꢀꢀꢀ
储存含有构成负载的单金属微粒子或者固溶体微粒子的元素的液体与含有载体粒子的液体的混合液的第4供给源
[0086]
10a
ꢀꢀꢀꢀꢀꢀꢀꢀꢀꢀꢀ
吸入侧的球
[0087]
10b
ꢀꢀꢀꢀꢀꢀꢀꢀꢀꢀꢀ
流出侧的球
[0088]
11a
ꢀꢀꢀꢀꢀꢀꢀꢀꢀꢀꢀ
吸入侧配管
[0089]
11b
ꢀꢀꢀꢀꢀꢀꢀꢀꢀꢀꢀ
流出侧配管
[0090]
12
ꢀꢀꢀꢀꢀꢀꢀꢀꢀꢀꢀꢀ
柱塞
[0091]
13
ꢀꢀꢀꢀꢀꢀꢀꢀꢀꢀꢀꢀ
空间
[0092]
14
ꢀꢀꢀꢀꢀꢀꢀꢀꢀꢀꢀꢀ
搅拌叶片。