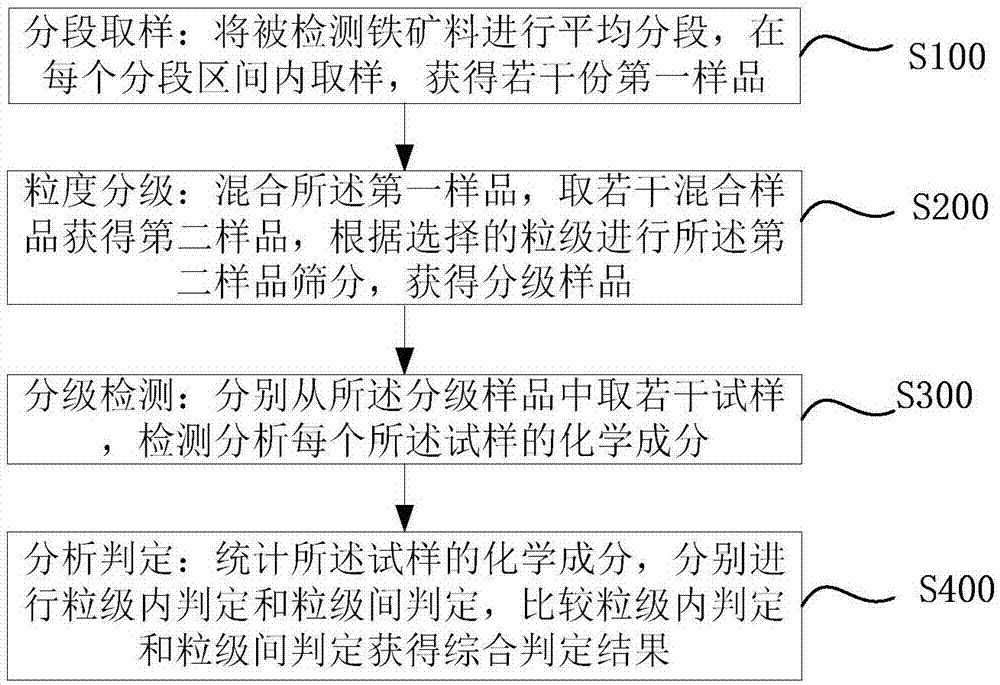
本申请涉及铁矿冶金
技术领域:
,尤其涉及一种铁矿料分类判定方法。
背景技术:
炼铁原料(矿料)能否稳定供应,一直是制约生产企业的瓶颈因素。受炼铁原料(矿料)供应以及市场条件等各种因素影响,近年来,钢铁业形势日趋紧张。为稳定钢铁业的紧张局势,目前各炼铁生产企业均已取消“长协矿”供应机制,改用“贸易矿”供应机制。贸易矿的使用,一方面因适应市场急剧变动的动态化管理,尽可能压缩了矿料成本,为生产企业争取了生存空间。然而,“贸易矿”供应机制因供应商的不断变动,带来了较多的采购技术难题,如:混杂矿粉、水分波动大、粉末高、掺杂异物等等。为保证采购成本的合理性,在进行采购过程中,需要对铁矿料进行分类判定。目前对铁矿料进行分类判定主要是通过成分检测,具体的将矿粉尽可能混匀后检测其平均成分,再根据其平均成分与经验数据对比判定其归属那类矿粉。通过成分检测进行铁矿料分类判定的方法,是在将被检测的铁矿料归结为一种矿料的前提下进行的铁矿料分类判定,因而无法识别出被检测的铁矿料是由一种矿料组成还是由几种矿料混杂而成。然而,若是无法对混杂类矿粉进行精准识别将极大地增加了矿粉采购成本,且对生产稳定造成不利影响。因此对混杂类矿粉进行精准识别已成为本
技术领域:
内亟待解决的技术难题。技术实现要素:本申请提供了一种铁矿料分类判定方法,用于铁矿粉的分类判定,精确识别铁矿料的掺杂情况。本申请提供了一种铁矿料分类判定方法,所述方法包括:分段取样:将被检测铁矿料进行平均分段,在每个分段区间内取样,获得若干份第一样品;粒度分级:混合所述第一样品,取若干混合样品获得第二样品,根据选择的粒级进行所述第二样品筛分,获得分级样品;分级检测:分别从所述分级样品中取若干试样,检测分析每个所述试样的化学成分;分析判定:统计所述试样的化学成分,分别进行粒级内判定和粒级间判定,比较粒级内判定和粒级间判定获得综合判定结果。可选的,上述铁矿料分类判定方法中,将被检测铁矿料进行平均分段,在每个分段区间内取样,获得若干份第一样品,包括:根据被检测铁矿料的料堆分别进行长、宽和高方向等距分段;在每个分段区间内取样并在位于料堆端边侧的分段区间的极端取样,获得若干份第一样品。可选的,上述铁矿料分类判定方法中,所述第一样品的样本数n1大于或等于30,所述第一样品的重量g>(粒级数*级别内检测频次*化验样本标准量/n1)/5%。可选的,上述铁矿料分类判定方法中,所述粒度分级中,还包括:当筛分获得分级样品比例小于所述第二样品总量的5%时,将所述分级样品并入相邻较大比例的分级样品中。可选的,上述铁矿料分类判定方法中,分别从所述分级样品中取若干试样,检测分析每个所述试样的化学成分,包括:分别从每一个粒级样品中取若干等量试样,并进行标号;检测分析每个所述试样的化学成分;将试样检测出的化学成分与其对应标号汇总编辑。可选的,上述铁矿料分类判定方法中,所述粒级内判定包括:确定极限区间值;根据所述极限区间值统计同成分各粒级内各间隔值对应的频次数,确定拐点、拐点个数、拐点间距和频次比值,所述拐点是指频次数大于其前后频次数所对应的间隔值,拐点个数为拐点数量,拐点间距是指最大拐点与最小拐点的间隔距离,频次比值为各拐点对应频次数与各拐点总频次数的比值;根据所述拐点个数、拐点间距和频次比值确定判定取值;根据所述判定取值确定铁矿料粒级内判定类别。可选的,上述铁矿料分类判定方法中,所述粒级间判定包括:确定极限区间值;根据所述极限区间值统计同成分各粒级间各间隔值对应的频次数,确定拐点、拐点个数、拐点间隔值和频次比值,所述拐点是指频次数大于其前后频次数所对应的间隔值,拐点个数为拐点数量,拐点间隔值是指最大拐点与最小拐点之间隔值,频次比值为各拐点对应频次数与各拐点总频次数的比值;根据所述拐点个数、拐点间距和频次比值确定判定取值;根据所述判定取值确定铁矿料粒级间判定类别。可选的,上述铁矿料分类判定方法中,比较粒级内判定和粒级间判定获得综合判定结果,包括:结合分级测量结果,比较粒级内判定和粒级间判定,获得综合判定结果。本申请提供的铁矿料分类判定方法,通过分段取样、粒度分级、分级检测和分析判定实现待检测铁矿料的分类判定,精确识别铁矿料的掺杂情况。本申请提供的铁矿料分类判定方法,克服了现有铁矿料分类判定方法的成分粒级并列分析、数据庞杂等弊端,能够对混杂矿粉进行精准分类判定,为矿料采购结算提供决策依据、为企业科学生产提供科学数据。且本申请提供的铁矿料分类判定方法,操作灵活、简单。附图说明为了更清楚地说明本申请的技术方案,下面将对实施例中所需要使用的附图作简单地介绍,显而易见地,对于本领域普通技术人员而言,在不付出创造性劳动性的前提下,还可以根据这些附图获得其他的附图。图1为本申请实施例提供的铁矿料分类判定方法的结构流程图;图2为本申请实施例提供的粒级内判定tfe分析1;图3为本申请实施例提供的粒级内判定tfe分析2;图4为本申请实施例提供的粒级内判定tfe分析3;图5为本申请实施例提供的粒级内判定sio2分析1;图6为本申请实施例提供的粒级内判定sio2分析2;图7为本申请实施例提供的粒级内判定sio2分析3;图8为本申请实施例提供的粒级间判定tfe分析;图9为本申请实施例提供的粒级间判定sio2分析。具体实施方式为了使本发明的目的、技术方案及优点更加清楚明白,以下结合附图及实施例,对本发明进行进一步详细说明。应当理解,此处所描述的具体实施例仅仅用以解释本发明,并不用于限定本发明。参见附图1,附图1示出了本申请实施例提供的铁矿料分类判定方法的具体流程步骤。如附图1所示,本申请实施例提供的铁矿料分类判定方法,包括:s100分段取样:将被检测铁矿料进行平均分段,在每个分段区间内取样,获得若干份第一样品。分段取样实现检测取样的全面覆盖性,有利于保证检测过程中所取的样品的能够全面代表被检测的铁矿料。分段可采取横向、纵向、水平三种方式,对含铁矿粉进行等距合理分段,对料堆等存在极端值的含铁矿粉还要设置极端段,以保证抽样代表性和操作便捷,满足采集包括极端和中间各分段含铁矿粉的目的。在本申请具体实施方式中,根据被检测铁矿料的料堆分别进行长、宽和高方向等距分段;在每个分段区间内取样并在位于料堆端边侧的分段区间的极端取样,获得若干份第一样品。第一样品的数量通常不少于30个,即第一样品的样本数n1大于或等于30,每个样品的重量g>(粒级数*级别内检测频次*化验样本标准量/n1)/5%。s200粒度分级:混合所述第一样品,取若干混合样品获得第二样品,根据选择的粒级进行所述第二样品筛分,获得分级样品。将分段取样中获得的第一样品进行混合,取若干混合样品作为第二样品,选择筛分粒级,根据选择的粒级进行所述第二样品筛分,获得分级样品。粒级是指在筛分前选定的筛分标准,如:选定粒级“≤0.08mm、0.08-3mm、≥3mm”,即按照0.08mm和3mm的标准将第二样品筛分成3个等级。在本申请中,粒级不局限于0.08mm和3mm,可从0.08、1mm、3mm、5mm、10mm等中根据实际需要进行选择。在本申请具体实施方式中,因为在实际生产中,不存在绝对精确单一粒级的矿种,每一个矿种粒级略微的临界粒级存在,所以当筛分获得分级样品比例小于所述第二样品总量的5%时,将所述分级样品并入相邻较大比例的分级样品中。s300分级检测:分别从所述分级样品中取若干试样,检测分析每个所述试样的化学成分。分别从不同粒级的含铁矿料中抽取等量试样,并做好标记进行试样编制;采用通用检测方式,对每个等量试样进行主要化学成分检测,所述主要化学成分一般可选取tfe、sio2、cao、al2o3等;将试样检测出的化学成分与其对应标号汇总编辑,如试样编号及检测结果录入统计表格,便于查看以及后续数据处理。通用的化学成分检测是指根据lqb95-2004《钢铁化学分析方法》和lqb99-2004《铁矿石、钛铁矿化学分析方法》对实验测试样品中的tfe、sio2、cao、al2o3等含量的定量分析。s400分析判定:统计所述试样的化学成分,分别进行粒级内判定和粒级间判定,比较粒级内判定和粒级间判定获得综合判定结果。根据分级检测中获得的试样成分,分别进行粒级内判定和粒级间判定。具体的:粒级内判定为:利用计算机常用办公软件,如mintab、excel等,根据行业经验设立不同成分的合理极限值,确定极限区间值,如tfe±0.5%、sio2±0.3%等,以频次数为纵轴、以极限区间为横轴区间,处理同成分不同粒级内数据,绘制直方图并确定拐点,计算同成分不同粒级内的拐点个数、拐点间距和频次比值,并根据行业经验,根据拐点个数、拐点间距和频次比值的判定取值,根据所述判定取值确定铁矿料粒级内判定类别。在本申请中,建立拐点个数、拐点间距和频次比值的判定取值原则。具体可如下(拐点个数的判定取值为t1,拐点间距的判定取值为t2,频次比值的判定取值为t3):当所述拐点个数小于或等于1时,取t1=0,表示正常;当所述拐点个数为2时,取t1=0.5,表示存疑;当所述拐点个数大于2时,取t1=1,表示异常;当拐点间距≤3*极限区间值,取t2=0,表示正常;当3*极限区间值<拐点间距≤5*极限区间值,取t2=0.5,表示存疑;当拐点间距>5*极限区间值,取t2=1,表示异常;当频次比值大于%15的拐点个数为1时,取t3=0,表示正常;当频次比值大于%15的拐点个数为2时,取t3=0.5,表示存疑;当频次比值大于%15的拐点个数大于或等于3个时,取t3=1,表示异常。建立判定原则,如下:拐点个数“=0”或“=1”,判定为“一类”,表示正常;拐点间距和频次比值的取值之和“=0”,判定为“一类”,表示正常;拐点间距和频次比值的取值之和“=0.5”,判定为“掺杂”,表示轻微异常;拐点间距和频次比值的取值之和“=1.0”,判定为“二类”,表示异常;拐点间距和频次比值的取值之和“=1.5”,判定为“二类掺杂”,表示明显异常;拐点个数、拐点间距和频次比值的取值之和“=2.0”,判定为“二类以上”,表示显著异常。计算拐点个数对应判定取值或拐点个数、拐点间距和频次比值对应判定取值之和,获得铁矿料粒级内判定类别。粒级间判定为利用计算机常用办公软件,如mintab、excel等,根据行业经验设立不同成分的合理极限值,确定极限区间值,如tfe±0.5%、sio2±0.3%等,以频次数为纵轴、以极限区间为横轴区间,处理同成分所有数据,绘制直方图并确定拐点,计算同成分不同粒级内的拐点个数、拐点间距和频次比值,并根据行业经验,根据拐点个数、拐点间距和频次比值的判定取值,根据所述判定取值确定铁矿料粒级内判定类别。其中判定取值原则以及判定原则参见上述粒级内判定所述的判定取值原则以及判定原则,在此不再赘述。比较粒级内判定、粒级间判定的判定结论,形成含铁矿料最终判定结论。在本申请具体实施方式中,具体比较判定方式如下:首先看粒级内是否掺杂:一般每个粒级内都呈现“一类”或个别出现“掺杂”均为正常,初步说明每个粒级均为正常的“一个料种”;如果每个粒级都出现“掺杂”以上结论,初步说明可能是一个较差的掺杂料种。再看不同成分粒级间是否掺杂:一般每个成分粒级间都呈现“一类”或个别出现“掺杂”均为正常,进一步说明为正常的“一个料种”;如果出现粒级间“掺杂”以上结论,初步说明可能是一个较差的掺杂料种或多料种掺杂。如此最后综合分析:如果粒级内、粒级间均判断“一个料种”,就可综合判定“一个料种”;出现“掺杂”可综合判断为一个料种掺杂;如果粒级内、判断“一个料种或掺杂”,粒级间判断出现“二类”及以上结论,综合判定以粒级间判断结论为主。下面结合具体实例对本申请实施例提供的铁矿料分类判定方法进行详细说明:以265m2烧结机生产系统为例,常用含铁矿粉有:巴粗、澳粗、国内矿粉等几大类,实际批料以堆为区别单位,使用料种中掺杂、混杂时有发生,以堆长10米、堆高8米、堆宽12米堆重16000吨的一堆国内铁精粉为例,下面结合附图进一步说明本发明的具体实施方式。第一步,分段取料。采取横向每2米一段、纵向每4米一段、水平每6米一段三种方式,对含铁矿料进行等距合理分段,因料堆两侧和两端均存在极端值还要设置两侧、两端极端段,共取样(10/2+2)*2*(12/6+2)=56个。参考实际含铁矿料粒度分布情况,选择确定粒度级数为3;根据含铁矿料总量16000吨,确定级别内检测频次取30;按照分段设置,每段需取料量>(3*30*1g/56)/5%(考虑中间损耗等因素,可在实际执行中控制250g左右),以保证抽样代表性和操作便捷。按照既定抽样方案共计抽样56个,每个样品约250g,总计14.5kg。第二步,粒度分级。首先参考实际含铁矿粉粒度分布情况,选定粒级“≤0.08mm、0.08-3mm、≥3mm”;再对56个抽样进行混合,取14.00kg混合样品,通过筛分方式,对采集含铁矿料进行筛分分级。得到“≤0.08mm”混合样品10.15kg,“0.08-3mm”混合样品2.82kg、“≥3mm”混合样品1.03kg。无比例小于5%的粒级矿粉,故确定为三级矿粉纳入分级检测。第三步,分级检测。首先编制试样,分别从“≤0.08mm、0.08-3mm、≥3mm”三个粒级的含铁矿料中抽取1g试样30个,即获得90个试样,并做好标记;对上述获得试样再做相同的成分检测,采用通用检测方式,即对每个试样主要化学成分“tfe、sio2”进行检测;最后采集数据,将试样编号及检测结果录入统计表格,如表1。表1:其中:数据101-130为颗粒小于0.08mm试样的成分tfe和sio2的检测数据;数据201-230为颗粒为0.08-3mm试样的成分tfe和sio2的检测数据;数据301-330为颗粒大于3mm试样的成分tfe和sio2的检测数据。第四步,分析判定。利用计算机常用办公软件,如mintab、excel等,根据行业经验设立不同成分的合理极限值,确定极限区间值,tfe±0.5%、sio2±0.25%,以频次数为纵轴、以极限区间为横轴区间,分别处理同成分不同粒级内数据以及处理同成分所有数据,绘制直方图并确定拐点,计算同成分不同粒级内的拐点个数、拐点间距和频次比值,并根据行业经验,根据拐点个数、拐点间距和频次比值的判定取值,根据所述判定取值确定铁矿料粒级内、粒级间判定类别。图2为粒级“≤0.08mm”的试样中tfe分析结果图,图3为粒级“0.08-3mm”的试样中tfe分析结果图,图4为粒级“≥3mm”的试样中tfe分析结果图,图5为粒级“≤0.08mm”的试样中sio2分析结果图,图6为粒级“0.08-3mm”的试样中sio2分析结果图,图7为图4为粒级“≥3mm”的试样中sio2分析结果图,图2-7展示的是粒级内判定;图8为所有试样中tfe分析结果图,图9为所有试样中sio2分析结果图,图8-9展示的是粒级间判定。下面结合附图对本申请进一步说明。由图2可知,粒级“≤0.08mm”的试样中tfe无拐点,粒级内判定为“一类”;由图3可知,粒级“0.08-3mm”的试样中tfe的拐点数为1,粒级内判定为“一类”;由图4可知,粒级“≥3mm”的试样中tfe的拐点数为1,粒级内判定为“一类”。由图5可知,粒级“≤0.08mm”的试样中sio2的拐点数为1,粒级内判定为“一类”;由图6可知,粒级“0.08-3mm”的试样中sio2的拐点数为1,粒级内判定为“一类”;由图7可知,粒级“≥3mm”的试样中sio2的拐点数为2、拐点间距为2、频次比值为1,拐点间距和频次比值的取值之和为1,粒级内判定为掺杂。由图8可知,所有试样中tfe拐点个数1,粒级间判定为“一类”;由图9可知,所有试样中sio2的拐点个数3、拐点间距6、频次比值2,拐点间距和频次比值的取值之和为1.5,粒级间判定为二类掺杂。通过上述分析可知:根据sio2粒级内判定分析,判定301-330(≥3mm)为掺杂,其他一类;根据sio2粒级间判定分析,判定二类掺杂。结合分级测量数据:≤0.08mm10.1572.50%0.08-3mm2.8220.14%≥3mm1.037.36%可形成综合判定:该堆国内铁精粉为二类矿粉掺杂组成,tfe66.5±1.0%,主要差异为掺杂矿粉硅含量偏高,主体矿粉sio23.0±0.5%、约占比例92.64%,掺杂矿粉sio27.0±0.5%、约占比例7.36%。本申请提供的铁矿料分类判定方法,通过分段取样、粒度分级、分级检测和分析判定实现待检测铁矿料的分类判定,精确识别铁矿料的掺杂情况。本申请提供的铁矿料分类判定方法,克服了现有铁矿料分类判定方法的成分粒级并列分析、数据庞杂等弊端,能够对混杂矿粉进行精准分类判定,为矿料采购结算提供决策依据、为企业科学生产提供科学数据。且本申请提供的铁矿料分类判定方法,操作灵活、简单。需要说明的是,本说明书中的各个实施例均采用递进的方式描述,各个实施例之间相同相似的部分互相参见即可,每个实施例重点说明的都是与其他实施例的不同之处,相关之处参见方法实施例的部分说明即可。本领域技术人员在考虑说明书及实践这里的发明后,将容易想到本发明的其它实施方案。本申请旨在涵盖本发明的任何变型、用途或者适应性变化,这些变型、用途或者适应性变化遵循本发明的一般性原理并包括本发明未发明的本
技术领域:
中的公知常识或惯用技术手段。说明书和实施例仅被视为示例性的,本发明的真正范围和精神由下面的权利要求指出。应当理解的是,本申请并不局限于上面已经描述并在附图中示出的精确结构,并且可以在不脱离其范围进行各种修改和改变。本申请的范围仅由所附的权利要求来限制。当前第1页12