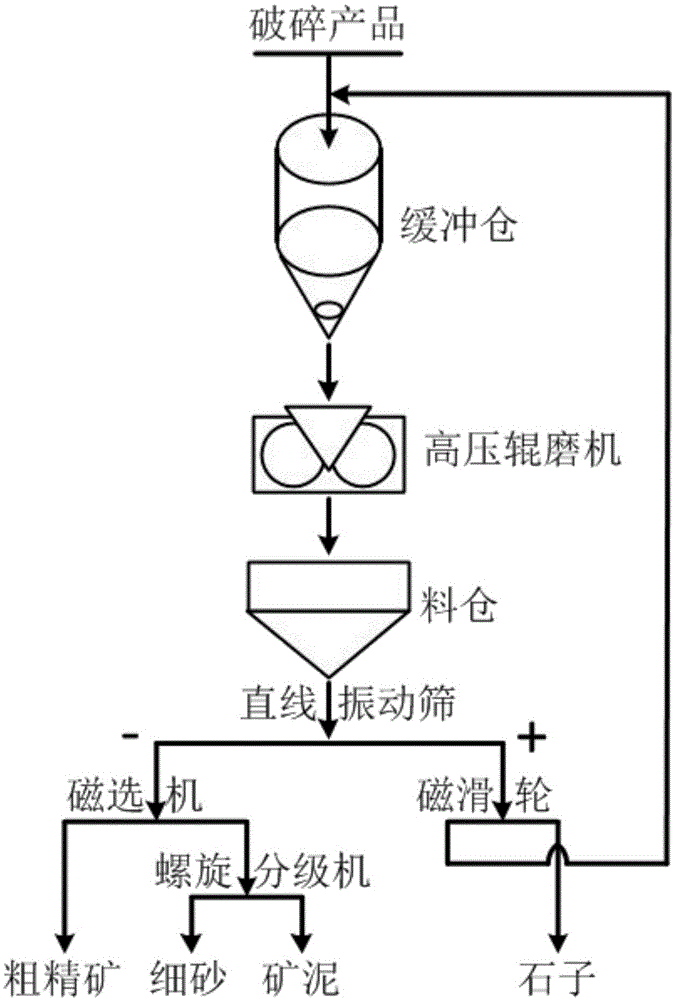
本发明涉及矿料筛选
技术领域:
,更具体地说,涉及一种铁矿超细碎循环解离抛尾及尾矿再利用工艺。
背景技术:
:近年来,我国经济高速发展,大量资源被开发利用,优质矿产资源日渐枯竭,贫、细、杂等难利用资源逐步开采,在开采这些资源的过程中,有价矿物嵌布粒度越来越细、大量连生体难解离的问题也随之暴露出来。我国铁矿主要有磁铁矿、赤铁矿、黄铁矿、菱铁矿、褐铁矿等,其中脉石矿物主要有石英、长石、磷灰石、金红石、阳起石等,从全产业链协同利用尾矿和废石的角度,对铁矿尾矿和废石在混凝土中替换开山炸石生产砂石料是完全可行的。现有技术中,通常采用“多碎少磨”的方式,以达到节能降耗的目的,但是在抛尾及尾矿再利用方面并未涉及,仅停留在设备粉碎层次的节能降耗。在整个选矿工艺流程中,对其他工段技术参数的优化调整,仍缺乏实践指导作用。技术实现要素:1.发明要解决的技术问题针对现有技术存在的缺陷与不足,本发明提供了一种铁矿超细碎循环解离抛尾及尾矿再利用工艺,该发明有效提升抛尾效果,改善现有技术中解离不充分、抛尾不理想及尾矿不回收利用等现象,有效提高资源利用率,节约资源成本。2.技术方案为达到上述目的,本发明提供的技术方案为:本发明的一种铁矿超细碎循环解离抛尾及尾矿再利用工艺,其步骤为:步骤一:将原矿破碎,破碎产品粒度控制在10mm~30mm;步骤二:将破碎产品输送到缓冲仓,缓冲仓的下端安装有高压辊磨机与皮带给料机,缓冲仓与高压辊磨机之间由皮带给料机相连接,皮带给料机位于缓冲仓的仓底;步骤三:高压辊磨机将物料辊压粉碎,高压辊磨机的输出端设置有料仓,高压辊磨机将粉碎后的物料通过皮带输送至料仓内;步骤四:料仓下设皮带给料机,皮带给料机的另一端连接有直线振动筛,皮带给料机将料仓的物料均匀稳定给入到直线振动筛,并在皮带给料机靠近直线振动筛一端补加水,进行湿式筛分;步骤五:直线振动筛的输出端并联设置有磁滑轮和磁选机,直线振动筛的筛上部分给入到磁滑轮,由磁滑轮进行一次抛尾,强磁性矿物和连生体返回至缓冲仓,进入闭路循环解离;步骤六:直线振动筛的筛下部分给入到磁选机,由磁选机进行二次抛尾,分选出磁选精矿和磁选尾矿,磁选精矿即为超细碎作业粗精矿,磁选尾矿给入到螺旋分级机,进行分级,获得粗粒级的细砂,螺旋分级机溢流为矿泥。进一步地,磁滑轮为永磁磁滑轮,筒体外圈皮带线速度1.5m/s~2.0m/s,滚筒表面场强2500gs~5000gs。进一步地,直线振动筛的筛网尺寸控制在1mm~5mm,振动频率15hz~20hz,双振幅5mm~10mm。进一步地,磁选机为逆流型永磁筒式磁选机,筒体表面线速度1.2m/s~1.3m/s,筒体表面磁感应强度300mt~550mt,磁偏角13°~18°。进一步地,螺旋分级机为低堰式螺旋螺旋分级机,螺旋转速3.6r/min~5.5r/min。进一步地,缓冲仓、高压辊磨机、料仓、直线振动筛与磁滑轮组成闭合回路,磁滑轮一次抛尾与磁选机二次抛尾构成双抛尾。进一步地,直线振动筛以粒度界限分成筛上和筛下两部分。进一步地,磁滑轮一次抛尾,抛除掉非磁性脉石和弱磁性贫连生体,强磁性产品返回至缓冲仓,进入下一轮辊压粉碎,构成闭路循环解离抛尾。3.有益效果采用本发明提供的技术方案,与现有技术相比,具有如下有益效果:本发明集成了循环解离、双抛尾和尾矿再利用等工序,充分发挥超细碎特点,减少入磨矿石量、减小入磨矿石粒度同时提升入磨矿石品位,深化“多碎少磨”,与传统技术相比,经过超细碎循环解离后有价矿物的解离度得到大幅提高,高压辊磨机主要进行层间粉碎,高强度挤压应力可适当降低磨矿功耗,后续磨矿选别效果更好,可提高选矿指标和降低选矿成本,此外,缓冲仓、高压辊磨机、料仓、直线振动筛与磁滑轮组成闭合回路,磁滑轮一次抛尾与磁选机二次抛尾构成双抛尾,不仅形成了循环解离,也形成了循环抛尾,大幅改善了抛尾效果,改善现有技术中解离不充分、抛尾不理想及尾矿不回收利用等现象,有效提高资源利用率,节约资源成本。附图说明图1为本发明的工艺流程图。具体实施方式下面结合附图和实施例对本发明作进一步的描述:实施例1从图1可以看出,本实施例的一种铁矿超细碎循环解离抛尾及尾矿再利用工艺,其步骤为:步骤一:将原矿破碎,破碎产品粒度控制在10mm~30mm以内;步骤二:将破碎产品输送到缓冲仓,缓冲仓的下端安装有高压辊磨机与皮带给料机,缓冲仓与高压辊磨机之间由皮带给料机相连接,皮带给料机位于缓冲仓的仓底,缓冲仓和皮带给料机共同完成物料的连续稳定供应;步骤三:高压辊磨机有动辊和定辊,矿石的辊压粉碎由两辊完成,两辊工作参数不同,高压辊磨机工作时主要参数为:电机转速率65%~85%、水端辊间压力值18mpa~21mpa(脆软矿石可适当下调压力值1mpa~3mpa)、电机端辊间压力值15mpa~19mpa(脆软矿石可适当下调压力值1mpa~2.5mpa)、辊间距45mm~60mm(水端辊间距和电机端辊间距之差的绝对值需控制在25以内),高压辊磨机将物料辊压粉碎,高压辊磨机的输出端设置有料仓,高压辊磨机将粉碎后的物料通过皮带输送至料仓内;步骤四:料仓下设皮带给料机,皮带给料机的另一端连接有直线振动筛,直线振动筛的筛网尺寸控制在1mm~5mm,振动频率15hz~20hz,双振幅5mm~10mm,皮带给料机将料仓的物料均匀稳定给入到直线振动筛,并在皮带给料机靠近直线振动筛一端补加水,进行湿式筛分;步骤五:直线振动筛的输出端并联设置有磁滑轮和磁选机,直线振动筛以粒度界限分成筛上和筛下两部分,直线振动筛的筛上部分给入到磁滑轮,由磁滑轮进行一次抛尾,抛出部分即为30mm以内粒级的石子,强磁性矿物和连生体返回至缓冲仓,进入闭路循环解离,磁滑轮为永磁磁滑轮,筒体外圈皮带线速度1.5m/s~2.0m/s,滚筒表面场强2500gs~5000gs;步骤六:直线振动筛的筛下部分给入到磁选机,磁选机为逆流型永磁筒式磁选机,筒体表面线速度1.2m/s~1.3m/s,筒体表面磁感应强度300mt~550mt,磁偏角13°~18°,由磁选机进行二次抛尾,分选出磁选精矿和磁选尾矿,磁选精矿即为超细碎作业粗精矿,磁选尾矿给入到螺旋分级机,螺旋分级机为低堰式螺旋螺旋分级机,螺旋转速3.6r/min~5.5r/min,螺旋分级机进行分级,获得粗粒级的细砂,螺旋分级机溢流为矿泥,磁滑轮抛出的石子即为建筑用混凝土骨料,螺旋分级机分离出的粗粒级产品即为建设用砂。缓冲仓、高压辊磨机、料仓、直线振动筛与磁滑轮组成闭合回路,磁滑轮一次抛尾与磁选机二次抛尾构成双抛尾,磁滑轮一次抛尾,抛除掉非磁性脉石和弱磁性贫连生体,强磁性产品返回至缓冲仓,进入下一轮辊压粉碎,构成闭路循环解离抛尾。具体实施过程中,以选取某地品位为18.60%的铁矿为例,磁性铁14.55%,矿石普氏硬度系数f=12~15,结构致密,主要为细脉浸染状构造,细粒磁铁矿浸染分布在闪长玢岩中,并有细脉状磁铁矿穿插其中,此外,局部可见细脉网脉状构造、块状构造,矿石嵌布粒度极细,连生体含量较多。采用颚式破碎机、圆锥破碎机等破碎设备将原矿石破碎至18mm(低于18mm粒级含量大于88%即可)以下,将破碎好的细碎产品给入到缓冲仓,高压辊磨机工作参数设置为电机转速率75%、水端辊间压力值19.5mpa、电机端辊间压力值18mpa、辊间距50mm,然后由缓冲仓底的皮带给料机将细碎产品连续均匀给入到高压辊磨机,进行辊压超细碎,辊压后的物料由皮带输送到料仓,料仓进行缓存分配物料,然后由料仓底的皮带给料机将物料连续均匀地给入到直线振动筛,此时直线振动筛工作参数为振动频率16hz、振幅8mm,选用3mm筛网,进行筛分作业,筛上粗颗粒矿石给入到磁滑轮,此时磁滑轮工作参数为筒体外圈皮带线速度1.75m/s、滚筒表面场强2600gs,进行一次抛尾作业,抛出非磁性的脉石及弱磁性的贫连生体,即抛出的石子,由承矿漏斗收集并由皮带运输到堆场;磁滑轮未抛出部分由承矿漏斗收集并由皮带运输到缓冲仓,进入闭路循环解离过程,筛下细粒级矿石给入到磁选机,此时磁选机的工作参数为筒体表面线速度1.25m/s、筒体表面磁感应强度320mt、磁系偏角15°,进行二次抛尾作业,再次抛出非磁性的脉石及弱磁性的贫连生体,磁选机精矿即为本工艺的粗精矿,磁选机尾矿自流进入螺旋分级机,采用螺旋直径为φ2000mm的螺旋分级机,螺旋转速4.5r/min,进行尾矿分级作业,获得粗粒级的细砂,螺旋分级机溢流(矿泥)即为最终尾矿。经过超细碎作业后矿石粒度从18mm减小至3mm,破碎比为6,解离度大幅提高,且入磨粒度大幅减小;两次抛尾后品位从原矿的18.60%提高到粗精矿的31.65%,入磨矿石品位得到大幅提升;石子、细砂及矿泥的产率之和为51.32%,即磨矿作业量减少51.32%;粗精矿回收率为82.83%,金属量流失较少。大幅降低磨矿作业能耗和钢耗,大幅降低选矿成本,建设用碎石和建设用砂市场价值可观,大幅减轻排尾系统和尾矿库的压力,增加大量的额外经济效益,详细数据如表1所示:表1超细碎作业产品(%)产品产率tfe磁性铁回收率粗精矿48.6831.6526.2782.83石子12.537.135.064.80细砂17.826.273.766.01矿泥20.975.642.656.36尾矿产品中,石子主要矿物为sio2,粒级为18mm+3mm以内,粗细均匀,硬度系数f=12~15,完全符合gbt14685-2011《建设用卵石、碎石标准》,是上好的建设用混凝土骨料;细砂主要矿物也为sio2,粒级为3mm+0.15mm以内,符合gbt14684-2011《建设用砂标准》ⅱ类标准。实施例2选取某鞍山式贫赤铁矿,tfe品位为23.81%,二氧化硅含量为63.72%,硫、磷等有害元素含量较少,矿石普氏硬度系数f=11~13,结构比较致密。采用颚式破碎机、圆锥破碎机等破碎设备将原矿石破碎至16mm(低于16mm粒级含量大于85%即可)以下,将破碎好的细碎产品给入到缓冲仓,将主体设施的工作参数定位:高压辊磨机电机转速率75%、水端辊间压力值17mpa、电机端辊间压力值16.5mpa、辊间距55mm;直线振动筛振动频率16hz、振幅8mm,选用3.5mm筛网;磁滑轮筒体外圈皮带线速度1.5m/s、滚筒表面场强5000gs;磁选机筒体表面线速度1.2m/s、筒体表面磁感应强度550mt、磁系偏角15°;螺旋直径为φ2000mm的螺旋分级机,螺旋转速4.5r/min,细砂产品由皮带给料机从缓冲仓均匀稳定地给入到高压辊磨机进行辊压粉碎作业,压碎后的矿石运输到料仓,再由皮带给料机给入到直线振动筛进行筛分作业,筛上矿石给入到磁滑轮进行一次抛尾,抛出部分为石子,留下磁性矿物返回到缓冲仓进行循环解离,筛下矿石给入到磁选机,进行二次抛尾作业,磁选精矿即为本工艺粗精矿,磁选尾矿自流入螺旋分级机,进行分级作业,粗粒级即为细砂,螺旋分级机溢流即为矿泥。贫赤铁矿经过超细碎作业加工处理后,获得粗精矿品位35.89%,回收率82.56%,双抛尾抛出率为45.23%,大幅减少了入磨矿石量及显著提升入磨矿石品位,改善磨矿环境,并获得11.47%的石子和15.83%的细砂,经检测,石子、细砂分别符合gbt14685-2011《建设用卵石、碎石标准》和gbt14684-2011《建设用砂标准》,两次抛尾共抛出45.23%的尾矿,其中27.30%得以回收利用,本工艺很好地实现了“节能减排”。实施例3选取某地超贫磁铁矿,tfe品位为13.27%,mfe含量为8.015%,磁性铁占有率为60.40%,矿石中主要的有价矿物为磁铁矿,其次还含有少量的赤铁矿、褐铁矿等,脉石以长石为主,另外含有少量的高岭土、黑云母、方解石、绿泥石等,磁铁矿在矿石中呈浸染状分布,嵌布粒度粗细不均匀,粗颗粒比较容易实现单体解离。如图1所示,将破碎产品粒度放宽至30mm(低于30mm的粒级含量约90%),降低磁滑轮滚筒表面场强至4000gs,磁选机筒体表面线速度1.25m/s、筒体表面磁感应强度450mt,其余工艺条件均相同。超贫磁铁矿经过超细碎作业加工处理后,获得粗精矿品位27.35%,回收率71.36%,双抛尾抛出率达65.38%,并获得16.13%的石子和21.59%的细砂,砂石利用率占抛尾量的57.69%,相比于超贫磁铁矿干式预选工艺,本工艺技术先进,循环解离双抛尾工艺大幅减少了金属流失,回收率高出约10~20个百分点。本发明集成了循环解离、双抛尾和尾矿再利用等工序,充分发挥超细碎特点,减少入磨矿石量、减小入磨矿石粒度同时提升入磨矿石品位,实现“多碎少磨”,与传统技术相比,经过超细碎循环解离后有价矿物的解离度得到大幅提高,高压辊磨机主要进行层间粉碎,高强度挤压应力可适当降低磨矿功耗,后续磨矿选别效果更好,可提高选矿指标和降低选矿成本,此外,缓冲仓、高压辊磨机、料仓、直线振动筛与磁滑轮组成闭合回路,磁滑轮一次抛尾与磁选机二次抛尾构成双抛尾,不仅形成了循环解离,也形成了循环抛尾,大幅改善了抛尾效果,改善现有技术中解离不充分、抛尾不理想及尾矿不回收利用等现象,有效提高资源利用率,节约资源成本。以上示意性的对本发明及其实施方式进行了描述,该描述没有限制性,附图中所示的也只是本发明的实施方式之一,实际的结构并不局限于此。所以,如果本领域的普通技术人员受其启示,在不脱离本发明创造宗旨的情况下,不经创造性的设计出与该技术方案相似的结构方式及实施例,均应属于本发明的保护范围。当前第1页12