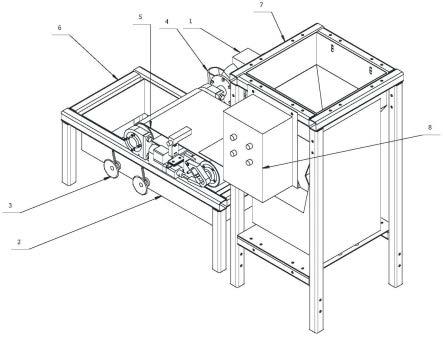
1.本实用新型涉及矿物分选设备的技术领域,特别是涉及一种用在矿物干式磁选装置中的磁力辊、磁选组件以及对应的矿物的干式磁选装置。
背景技术:2.常见的矿物分选技术有重选、浮选、磁选等。重选是利用待分选矿物颗粒间相对密度、粒度、形状的差异及其在介质(水、空气或其他相对密度较大的液体)中运动速率和方向的不同,使不同矿物分离的选矿方法,通常适用于比重较悬殊的矿物的分离。
3.浮选是在起泡剂(表面活性剂的一种)产生的大量气泡状态下,利用待分选矿物晶体表面性质的不同,使起捕集作用的表面活性剂(可以是阴离子、阳离子或脂肪胺类表面活性剂)有选择性地吸附在一些矿物颗粒表面,该表面活性剂的疏水端部分地插入起泡剂产生的气泡内,在气泡的上浮过程中把吸附了表面活性剂的矿物颗粒带走,达到矿物分选的目的。
4.根据矿物的磁性,即:按矿物的比磁化系数x的大小,可将矿物分为强磁性矿物、弱磁性矿物和非磁性矿物。强磁性矿物的比磁化系数x>3.8
×
10-5
m3/kg,弱磁性矿物的比磁化系数x在7.5
×
10-6
~1.26
×
10-7m3/kg之间,非磁性矿物的比磁化系数x<1.26
ꢀ×
10-7
m3/kg。磁选是利用待分选矿物中因不同矿物的比磁化系数不同而对磁场的反应 (即受到的磁力)不同,在磁场的磁力和机械力(包括重力、离心力、水流动力等) 的共同作用下,实现非磁性矿物与强磁性矿物、或弱磁性矿物与强磁性矿物之间分离的选矿方法,通常适用于钛铁矿的精选(即:去除钛铁矿中的非磁性矿物或弱磁性矿物)。
5.磁选又可根据使用的机械力不同,分为干式磁选(如在磁力和重力的共同作用下) 和湿式磁选(如在磁力、重力和水流动力的共同作用下)。湿式磁选一般在水介质中完成,可以实现弱磁性矿物和强磁性矿物之间的分选;由于水流动对非磁性矿物的冲击力比非磁性矿物受到的磁力大得多,因此很难将矿物中的非磁性矿物分选出来。而与湿式磁选相比,干式磁选一般在空气中完成,尤其对于颗粒直径>74μm的非磁性矿物,分选过程中非磁性矿物受到的空气阻力比受到的磁力小得多,使得非磁性矿物与非磁性矿物、弱磁性矿物和/或强磁性矿物之间的分选有实现的可能。
6.现有常用的干式磁选机通常包括给料装置、传输皮带、电机、磁力辊、皮带辊、出料腔体、翻板;其中磁力辊通常在其轴向表面等间隔设置多个具有较大宽度(5mm 以上)的环状的永磁环(永磁环的磁场方向与磁力辊的轴向平行,如图5所示),即:沿磁力辊的圆周表面等间隔分布多个相互平行的环状永磁环,相邻的永磁环之间用没有磁性的相互平行的环状聚磁环隔开。干式磁选机对矿物的分选过程为:待分选矿物经给料装置输送到传输皮带上,电机带动磁力辊旋转,磁力辊通过传输皮带带动皮带辊旋转;当传输皮带上的待分选矿物到达磁力辊时,待分选矿物沿水平方向被抛出,在抛出的过程中,待分选矿物的各组成由于比磁化系数x不同,在磁力辊磁场的作用下受到不同磁力的吸引,使得其中的非磁性矿物
被抛得远,磁性矿物(弱磁性矿物和/ 或强磁性矿物)被抛得近、甚至吸附在磁力辊上被带走;此时根据矿物的落点不同,将出料腔体中的翻板设置在非磁性矿物和磁性矿物的落点之间,即可将不同区域的矿物收集实现非磁性矿物与弱磁性矿物和/或强磁性矿物之间的分选。
7.然而,干式磁选机的传输皮带在转动过程中会发生跑偏,跑偏时传输皮带会被磁力辊和皮带辊绷紧和撕扯而容易损坏,使用寿命大大降低。为了延长传输皮带的使用寿命,惯用的传输皮带一般采用橡胶材质制成,且厚度较厚,一般>1-5mm。传输皮带较厚会加重对磁场的屏蔽效应,使得传输皮带上矿物受到的磁力吸引大幅减小,导致强磁性矿物和/或弱磁性矿物被抛出后的运动轨迹发生较大改变,最终的落点与非磁性矿物的落点之间间距小甚至有重叠,从而降低了不同磁性矿物分选的效果。通常仅用于非磁性矿物与磁性矿物(强磁性矿物和/或弱磁性矿物)的分选。
技术实现要素:8.本实用新型的目的是针对现有技术中存在的技术缺陷,第一方面,提供一种可提高磁场均匀性的矿物干式磁选装置用磁力辊,沿其轴向表面平行分布多个永磁环 (541)和聚磁环(542),永磁环和聚磁环间隔设置,每个永磁环的宽度相等,每个聚磁环的宽度相等,所述永磁环的宽度为1-4mm,永磁环和聚磁环的宽度比为 (1-4):1。
9.所述永磁环和聚磁环的宽度比为(2-4):1。
10.第二方面,本实用新型提供一种矿物干式磁选装置用磁选组件,包括组件框架 (51)、分别固定在组件框架两端的磁力辊(54)和皮带辊(55)以及包绕在磁力辊和皮带辊外侧表面的传输皮带(56),磁力辊为上述磁力辊。
11.还包括自动纠偏控制系统,所述自动纠偏控制系统包括传感器(53)、活动滑槽 (57)、伸缩杆(52)、固定滑槽(58)和控制模块;传感器设在磁力辊和皮带辊之间传输皮带的边缘,并与控制模块电连接;固定滑槽和活动滑槽分别设在皮带辊的轴的两端,活动滑槽和固定滑槽的槽口所在平面与皮带辊的轴垂直,且与水平方向呈一夹角;固定滑槽一端与皮带辊的轴固定连接,另一端与组件框架固定连接;活动滑槽内设有可在活动滑槽内滑动的滑块(59),滑块与皮带辊的轴固定连接;伸缩杆的一端与活动滑槽连接,另一端与控制模块电连接。
12.所述夹角为30-50
°
。
13.所述传输皮带的厚度为0.08-0.8mm。
14.所述传输皮带的材质选自聚氯乙烯或其他电阻值小于108ω的材料。
15.第三方面,本实用新型提供一种可提高分选效果的矿物的干式磁选装置,包括机架(6)、给料装置(7)、出料腔体(2)、翻板(3)、电机(1)和磁选组件(5),给料装置设在机架一端的上部,磁选组件水平设在机架的中部,出料腔体位于磁选组件的出料端,翻板设在出料腔体内并与磁力辊平行,至少设一个翻板以将出料腔体分隔出至少两个区域,所述磁选组件为上述磁选组件,磁选组件中的磁力辊的轴与电机连接。
16.所述干式矿物磁选装置包括一套或多套磁选组件,多套磁选组件的上一级磁选组件的出料端位于下一级磁选组件进料端的上方。
17.不同套磁选组件中的磁力辊不同,下一级的磁力辊永磁环宽度小于上一级磁力辊
永磁环宽度
18.本实用新型提供的磁力辊独创性地缩小了永磁环的宽度,使得磁辊表面的磁场更加均匀。将该磁力辊用于干式磁选装置后,漏选的矿物颗粒大大减少,即:本实用新型的干式磁选装置通过提高磁力辊的磁场均匀性提高了分选效果,而不是通过目前常见的提高磁场强度的方式来提高分选效果。同时本实用新型还设置传输皮带的纠偏系统,以对传输皮带进行纠偏,使其跑偏现象显著降低,传输皮带不易被绷紧和撕扯,从而可减小传输皮带的厚度;而由于传输皮带厚度减小,传输皮带对磁场的屏蔽作用也降低,磁力辊的磁场因传输皮带导致的衰减大大减少,使得磁性矿物受到的磁力增加,抛出后的落点与非磁性矿物的落点之间间距大,从而提高了分选的效果。本实用新型的干式磁选装置除了可用于非磁性矿物与磁性矿物(强磁性矿物和/或弱磁性矿物)之间的分选,还可用于非磁性矿物与非磁性矿物之间的分选,例如石英与其他硅酸盐非磁性矿物之间、或石英与萤石之间、或石英与黄铁矿之间的分选。
附图说明
19.图1所示为干法物料磁选装置用磁力辊的结构俯视图;
20.图2所示为磁力辊a部的放大图;
21.图3所示为干法物料磁选装置用磁选组件的立体结构图;
22.图4所示为实施例1干法物料磁选装置的立体线条图;
23.图5所示为实施例2干法物料磁选装置的立体线条图;
24.图6所示为现有干式磁选机和实施例1干法物料磁选装置中磁力辊的磁场强度均匀性示意图;
25.图7所示为实施例2干法物料磁选装置进行磁选的过程示意图。
具体实施方式
26.根据现有干式磁选机的结构和工作原理可知,干式磁选机的磁力辊在其轴向表面的磁性分布状态为:磁性-非磁性-磁性-非磁性
‑…‑
磁性-非磁性-磁性,磁力辊上磁极的分布状态为:n极-s极-聚磁环-s极-n极-聚磁环-n极-s极-聚磁环
…‑
s极-n极
‑ꢀ
聚磁环-n极-s极-聚磁环-s极-n极。可见,相邻两个永磁环541的磁场均汇聚至这两个永磁环夹着的聚磁环上,因此聚磁环处的磁场最强,而永磁环中部(宽度方向的中部,参见图6之a幅)的磁场最弱。在永磁环磁场较弱区域的待分选矿物颗粒9所受磁力较小,使得在该区域中的强磁性矿物和/或弱磁性矿物被抛出后的运动轨迹与非磁性矿物发生重叠,从而被漏选,导致分选效果不理想。
27.按照传统的改进理念,为了解决漏选问题,提高矿物的分选效果,尤其是比磁化系数较小的弱磁性矿物、非磁性矿物的分选效果,通常以继续增大磁场强度(一般要求提高至1t以上,甚至提高至1.5t以上)为解决方式,使强磁性矿物和弱磁性矿物受到的磁力增强。磁场强度一般是通过加大永磁环的宽度来实现的,目前永磁环的宽度为5-30mm,永磁环与聚磁环的宽度比为(5-30):1,磁场强度为0.4t-1.2t。然而,发明人研究发现,永磁环的宽度越大,永磁环中部磁场较弱的区域越宽(见图6的a 幅,以永磁环的宽度为6mm为例,磁场较弱的区域宽度约为1mm),落在该区域内的待分选矿物颗粒9越多,越容易导致该区域内的磁
性矿物被漏选。因此,常规的加大永磁环宽度的改进方式对矿物分选效果的提高程度有限。
28.因此,目前的干式磁选机仅适用于比磁化系数x差距较大(例如超过75
×ꢀ
10-7
m3/kg)的矿物之间的分选,如非磁性矿物与强磁性矿物、非磁性矿物与弱磁性矿物、或弱磁性矿物与强磁性矿物之间的分选;而对部分比磁化系数x差距小(例如小于55
×
10-9m3/kg)的弱磁性矿物与非磁性矿物、非磁性矿物与非磁性矿物之间的分选效果不理想。
29.本实用新型提供的干式磁选装置摒弃了上述传统的改造方向,不追求过高的磁场强度,采用新的技术构思,将改进方向放在磁场的均匀性上,通过减小永磁环541的宽度,使得磁辊表面磁场更加均匀(见图6的b幅,以永磁环的宽度为2mm为例,磁场较弱的区域宽度仅为0.2mm),从而大大减少被漏选的矿物颗粒9,提高磁选效果;同时还增设了传输皮带自动纠偏控制系统,使传输皮带的跑偏现象显著降低,跑偏现象的抑制可减少传输皮带被绷紧和撕扯的情况发生,使传输皮带不再容易损坏,从而可减小传输皮带的厚度。传输皮带的厚度减小会降低传输皮带对磁场的衰减作用,使分选矿物所受的磁力增强,进一步提高分选效果。虽然现有的含有传输皮带的传送装置(如地铁站、飞机场的安检装置)也设有传输皮带自动纠偏控制系统,但其系统仅适用于慢速转动(转速在0.1m/s-0.6m/s左右,允许跑偏距离一般为
±
10-50mm)的传输皮带,用于干式磁选机的快速转动(转速换算为线速度约为0.7-2.1m/s,允许跑偏距离仅为
±
5mm)的传输皮带时,对传输皮带的纠偏会有滞后性,纠偏精度和纠偏智能化程度低,且现有的自动纠偏控制系统的允许跑偏距离过大,会缩短传输皮带的寿命,无法解决干式磁选机中传输皮带跑偏和皮带因跑偏导致的使用寿命短的问题。
30.目前现有的干式磁选机仅用于非磁性矿物与强磁性矿物和/或弱磁性矿物之间的分选,对含有92wt%石英的待分选矿物(即92wt%石英+5wt%其他硅酸盐非磁性矿物 +3wt%弱磁性矿物和强磁性矿物)进行分选后,得到的非磁性矿物含量不超过96%,不能满足gb/t 9442-2010《铸造用硅砂》中铸钢用石英砂的指标要求,仅能满足该标准中铸铁用石英砂的指标要求。
31.而本实用新型的干式磁选装置除了适用于现有干式磁选机可分选的矿物种类,还适用于比磁化系数差异较小的弱磁性矿物与非磁性矿物、非磁性矿物与非磁性矿物之间的磁选,尤其适用于石英与其他硅酸盐非磁性矿物之间的磁选,对含有92wt%石英的待分选矿物(即92wt%石英+5wt%其他硅酸盐非磁性矿物+3wt%弱磁性矿物和强磁性矿物)进行分选后,得到的目标产物中二氧化硅含量可达97%以上,能够满足gb/t 9442-2010《铸造用硅砂》中铸钢用石英砂的要求,也实现了非磁性矿物之间的干式磁选分离。其中,待分选矿物为比磁化系数之差≤55
×
10-9m3/kg(优选≤27
×
10-9m3/kg,更优选≤0.2
×
10-9m3/kg)的非磁性矿物与弱磁性矿物和/或强磁性矿物的混合矿物;或比磁化系数之差≤1.1
×
10-9
m3/kg的非磁性矿物与非磁性矿物的混合矿物。待分选矿物可以为含有石英及其他硅酸盐非磁性矿物(如长石)与弱磁性矿物和强磁性矿物的混合矿物,或含有石英及萤石的非磁性矿物的混合矿物,或含有石英及黄铁矿的非磁性矿物的混合矿物。
32.以下结合具体实施例,更具体地说明本实用新型的内容,并对本实用新型作进一步阐述,但这些实施例绝非对本实用新型进行限制。
33.本实用新型提供的干式矿物磁选装置,参考图4,包括电机1、出料腔体2、翻板 3、联轴器4、磁选组件5、机架6、给料装置7和配电控制箱8。机架6为一水平放置的长方形框架,
框架的四角底面分别设有用于支撑框架的支腿。给料装置7设在机架 6一端(即宽边的一侧)的上部。磁选组件5水平设在机架6框架所在平面的中部(长边和宽边的中部)且进料端设在给料装置7的出料端处。磁选组件5的出料端处设有出料腔体2,出料腔体2为一顶部敞口的长方体容器,设在磁选组件5的底部,即出料腔体2设在机架6框架所在表面的下方,出料腔体2的顶部边缘与机架6的框架下表面连接。出料腔体2内设有1-3个翻板3,翻板3与机架6的宽边平行,将出料腔体2沿机架6的长边方向分隔出至少两个区域,以将分选后的矿物隔开。当翻板3有 2个或2个以上时,每个翻板3相互平行设置,以将分选后的不同比磁化系数的矿物隔开。电机1设在机架6一侧,且与磁选组件5连接,为磁选组件5提供驱动力。机架6的一侧还设有配电控制箱8,配电控制箱与电机1电连接,用来控制电机1的转速等。
34.磁选组件5如图3所示,包括组件框架51、磁力辊54、皮带辊55和传输皮带56。组件框架51为一长方形框架,固定在机架6的框架上。组件框架51的一端设有磁力辊54,另一端设有皮带辊55,磁力辊54和皮带辊55相互平行。传输皮带56缠绕在磁力辊54和皮带辊55的外侧,使得传输皮带56在竖直方向上的剖视图呈“跑道”状的封闭环形,“跑道”的直道段位于水平方向,弯道段的内部分别设置磁力辊54和皮带辊55,即传输皮带56绕在磁力辊54和皮带辊55外侧的表面,磁力辊54与皮带辊55之间的传输皮带56处于水平方向,形成“跑道”状的封闭环形,传输皮带56 的厚度为0.08-0.8mm(优选0.13mm),采用聚氯乙烯(或其它电阻值≤108ω的材料) 制成,聚氯乙烯是橡胶成本的1%。皮带辊55设在靠近给料装置7的传输皮带56的一端(即传输皮带56的进料端),磁力辊54则设在远离给料装置7的传输皮带56的另一端(即传输皮带56的出料端)。磁力辊54通过联轴器4与电机1连接,电机1的转动带动磁力辊54转动,磁力辊56的转动又带动皮带辊55转动,最终使得传输皮带 56在磁力辊54和皮带辊55外侧循环转动。给料装置7的进料端用来放入待分选的矿物,其出料端位于传输皮带56的进料端,传输皮带56的出料端位于出料腔体2的上方。其中,
35.磁力辊54的表面沿其轴向平行间隔分布多个环状的永磁环541,永磁环541沿磁力辊54的圆周设置,永磁环541的宽度为1-4mm,采用磁能积不小于310kj/m3的钕铁硼磁性材料制成(如《gb/t 13560-2017烧结钕铁硼永磁材料》中n42以上牌号的钕铁硼磁性材料)。永磁环541由环状的聚磁环542隔开,聚磁环542的宽度为1mm,由铁钴钒软磁合金制成;聚磁环542也沿磁力辊54的圆周设置,并沿磁力辊54的轴向在其表面平行间隔分布。也就是说,永磁环541和聚磁环542相互平行且间隔分布在磁力辊的轴向表面。相邻两个永磁环541的同一磁极相邻,即:磁力辊54上磁极的分布状态为:n极-s极-聚磁环-s极-n极-聚磁环-n极-s极-聚磁环
…‑
s极-n极-聚磁环
ꢀ‑
n极-s极-聚磁环-s极-n极。
36.上述磁选组件在一台干式矿物磁选装置中可以设置多套。当干式矿物磁选装置中仅设有一套磁选组件时,该装置为单级干式矿物磁选装置;当设有多套磁选组件时(多套磁选组件串联),该装置为多级干式矿物磁选装置。
37.上述干式矿物磁选装置还包括传输皮带自动纠偏控制系统,该系统包括控制模块、伸缩杆52、传感器53、固定滑槽58、活动滑槽57和滑块59。其中传感器53设置在皮带辊55和磁力辊54之间的传输皮带56边缘处,以实时监测传输皮带56的位置,传感器与控制模块电连接,以将传输皮带56的位置信息传送至控制模块。固定滑槽58设在皮带辊55的一端(传感器的对侧),槽口的一端与皮带辊的轴固定,另一端与组件框架51固定。活动滑槽57设在皮带辊55的另一端(传感器的同侧),活动滑槽57的槽口所在平面与皮带辊55的轴垂直,且
槽口与水平方向具有一定夹角(一般为30-50
°
,优选45
°
),即槽口呈一端高一端低的斜槽。活动滑槽57内设有一滑块 59,滑块59与皮带辊55的轴连接,且可在活动滑槽57内上下滑动。活动滑槽57的一端与伸缩杆52的一端连接,伸缩杆52的另一端与控制模块电连接,伸缩杆52为一长度可调的杆体,通过控制模块改变伸缩杆52杆体的长度从而控制活动滑槽57槽口与水平方向的夹角,使得滑块59在活动滑槽57内的位置发生变化,滑块59在竖直方向上的高度也发生变化,从而调整皮带辊55在活动滑槽57端的高度,以使传输皮带 56的位置发生变化。该系统的纠偏工作原理为:传感器53将监测到的传输皮带56的位置传送至控制模块,控制模块处理该位置信息,若传输皮带56发生偏移,控制模块对伸缩杆52发出收缩或伸长的指令,以调整活动滑槽57槽口与水平方向的夹角增大或减小,滑块59在活动滑槽57内的位置也随之上移或下移,从而抬高或降低皮带辊 55一端的位置。该系统纠偏的具体过程为:传感器53实时监测传输皮带56的位置,并将传输皮带56的位置传送给控制模块,当传输皮带56的位置向活动滑槽57方向靠近时,控制模块向伸缩杆52发出指令,伸缩杆52收缩以使活动滑槽57槽口与水平方向的夹角增大,滑块59也随之向活动滑槽57的高处滑动,设有活动滑槽的皮带辊55 的一端被抬高,高于设有固定滑槽58的皮带辊的一端,活动滑槽57端的传输皮带56 被绷紧,使得传输皮带56向固定滑槽58的方向移动,控制模块逐渐减小活动滑槽57 与水平方向的夹角,在传输皮带56移回规定位置时,皮带辊55两端处于同一水平线上,没有高度差。当传输皮带56的位置远离活动滑槽57时,控制模块控制伸缩杆52 伸长,活动滑槽57槽口与水平方向的夹角减小,滑块59向活动滑槽57的低处滑动,设有活动滑槽57的皮带辊55的一端被降低,且低于设有固定滑槽58的皮带辊55的一端,固定滑槽58端的传输皮带56被绷紧,使得传输皮带56向活动滑槽57方向靠近,在此过程中,控制模块逐渐增大活动滑槽57与水平方向的夹角,在传输皮带56 移回规定位置时,皮带辊55两端处于同一水平线上,没有高度差,如此保证传输皮带 56的位置始终位于磁力辊54和皮带辊55的中部。
38.使用上述干式矿物磁选装置对矿物进行磁选的方法,包括以下过程:
39.启动电机,电机的转动带动磁力辊54转动,磁力辊54的转动带动皮带辊55转动,磁力辊54和皮带辊55的转动带动传输皮带56在磁力辊54和皮带辊55外侧的表面上循环转动。
40.向给料装置7的进料端中投入待分选的矿物,矿物经出料端落在传输皮带56的进料端(皮带辊处),随着传输皮带56的转动,矿物被带至传输皮带56的出料端(磁力辊处),由于惯性矿物在传输皮带56的出料端沿水平方向被甩出,被甩出的矿物受到重力和磁力辊54上永磁环的磁力,并在这两个力的作用下作类抛物线运动;由于不同矿物的比磁化系数不同,受到的磁力就不同,被甩出后作类抛物线运动形成的运动轨迹也不同,比磁化系数较大的矿物落点(在出料腔体2内的落点)离传输皮带56 的出料端(磁力辊处)近,比磁化系数较小的矿物落点(在出料腔体2内的落点)则离传输皮带56的出料端远。上述矿物被甩出后沿不同抛物线轨迹作的类抛物运动即为分选矿物的过程;翻板3的角度可根据不同矿物的落点进行调整,以将分选后的不同比磁化系数的矿物隔开,完成分选。这一过程中磁力辊54的转速为100-300r/min,永磁环的厚度为1-4mm,永磁环与聚磁环的宽度比为(1-4):1,传输皮带56的厚度为0.08-0.8mm。
41.实施例1
42.本实施例的干式磁选装置为单级干式磁选装置,结构如图4所示,各部件的描述如前所述,其中设有一套磁选组件5。本实施例设计的磁力辊中永磁环的宽度为3mm,聚磁环的
宽度为1mm;传输皮带的材质采用聚氯乙烯,厚度为0.13mm;翻板3仅设1 个。工作中磁力辊在电机带动下转速为200r/min。
43.实施例2
44.本实施例的干式磁选装置为三级干式磁选装置(磁选过程的示意图见图7),与实施例1的区别是,其中磁选组件5有三套,三套磁选组件串联,上一级磁选组件的出料端位于下一级磁选组件进料端的上方,图5显示其串联方式。
45.多套磁选组件联用中,不同套中的磁力辊54可以相同或不同,例如,每一磁力辊上永磁环的宽度均为3mm,聚磁环的宽度均为1mm;或第一级、第二级、第三级磁选组件上永磁环的宽度分别为4mm、3mm和2mm,聚磁环的宽度均为1mm(第一级、第二级、第三级磁选组件的布置与物料的运动方向一致)。实施中,每级磁选组件5下方(且在下一级磁选组件上方)的翻板3数量可相同或不同,可设1个或2个,图5和图7 显示了2个翻板3。出料腔体2设在最后一级磁选组件的下方,每一级磁选组件在竖直方向的投影均落在出料腔体2的敞口空间内,出料腔体在水平方向的敞口面积能够覆盖所有磁选组件水平方面的面积,使得每一级磁选组件分选出的矿物均能落入出料腔体内,得到不同组成的分选后的矿物。
46.实验一:
47.用实施例1的单级干式磁选装置对同一批矿物(作为样本)进行磁选,该样本来自内蒙古赤峰市开采的天然硅砂原矿,由石英、长石、黑云母、角闪石、磁铁矿这些矿物组成,其成分为:92.2wt%石英、4.8wt%长石、1.5wt%黑云母、1.0wt%角闪石、 0.5wt%磁铁矿,sio2含量93.92wt%(见表1,其中石英和长石属于非磁性矿物,比磁化系数分别为-0.5
×
10-9
m3/kg、-0.33
×
10-9
m3/kg;黑云母和角闪石属于弱磁性矿物,比磁化系数分别为54.24
×
10-9
m3/kg、25.54
×
10-9
m3/kg;磁铁矿属于强磁性矿物,比磁化系数为92000
×
10-9
m3/kg)。用实施例1的磁选装置对该样本进行磁选,仅是对磁力辊中永磁环和聚磁环的宽度进行调整,永磁环和聚磁环的具体宽度见表1,磁选后得到的目标产物分别为硅砂精矿a-硅砂精矿e,其成分见表1。干式磁选装置中磁力辊上永磁环选用n45以上钕铁硼磁性材料制成,呈圆环状,直径100mm;聚磁环选用铁钴钒软磁合金制成,呈圆环状,直径100mm。磁选结果见表1,表1中的产率表示磁选后得到的目标产物硅砂精矿的质量占磁选前天然硅砂原矿质量的百分比。
48.表1使用不同磁力辊的干式磁选装置磁选后的结果
49.50.表1结果显示,本实用新型的干式磁选装置在保证产率基本不变的基础上,能使磁选后矿物(见硅砂精矿c、硅砂精矿d和硅砂精矿e)中sio2含量超过97%,完全满足gb/t 9442-2010《铸造用硅砂》中对铸钢用石英砂(要求sio2含量≥96%)的要求。而磁力辊中永磁环宽度较宽时(≥6mm),磁选后矿物(如硅砂精矿a和硅砂精矿b) 中sio2含量无法达到96%,不能满足gb/t 9442-2010《铸造用硅砂》中对铸钢用石英砂(要求sio2含量≥96%)的要求。
51.实验二:
52.选取河南嵩县车村阳桃沟开采的天然萤石原矿,属于萤石-石英类型(由石英和萤石组成),该地区的天然萤石矿石以块矿、砂矿为主,主要矿物萤石多呈浅紫色,石英呈乳白色,隐晶质结构,块状、条带状构造。以块矿挑选后的小颗粒矿石为萤石矿,主要由萤石70%、石英28%、少量黑云母(黑云母风化严重)组成。该萤石矿经破碎、分级后选取粒径为0.1-2mm的作为原矿样本用实施例1的单级干式磁选装置对该原矿样本进行磁选,其成分为:30.1wt%石英、69.9wt%萤石,caf含量69.48wt%(见表2,其中石英和萤石均属于非磁性矿物,比磁化系数分别为-0.5
×
10-9
m3/kg、0.51
×ꢀ
10-9
m3/kg)。用实施例1的磁选装置对该样本进行磁选,仅是对磁力辊中永磁环和聚磁环的宽度进行调整,永磁环和聚磁环的具体宽度见表2,磁选后得到的目标产物分别为萤石精矿a-萤石精矿e,其成分见表2。干式磁选装置中磁力辊上永磁环选用n45 以上钕铁硼磁性材料制成,呈圆环状,直径100mm;聚磁环选用铁钴钒软磁合金制成,呈圆环状,直径100mm。磁选结果见表2,表2中的产率表示磁选后得到的目标产物萤石精矿的质量占磁选前原矿样本质量的百分比。
53.表2使用不同磁力辊的干式磁选装置对原矿样本磁选后的结果
[0054][0055]
表2结果显示,本实用新型的干式磁选装置在保证产率基本不变的基础上,能使磁选后矿物(见萤石精矿c、萤石精矿d和萤石精矿e)中caf含量超过95%,完全满足yb/t 5217-2019《萤石》中对萤石精粉(要求caf含量≥93%)的要求。而磁力辊中永磁环宽度较宽时(≥6mm),磁选后矿物(如萤石精矿a和萤石精矿b)中caf 含量则不超过80%,远远不能满足yb/t 5217-2019《萤石》中对萤石精粉(要求caf 含量≥93%)的要求。
[0056]
实验三:
[0057]
选取四川省沐川县黄丹镇开采的石英砂岩矿,主要由石英(>90%)组成,还含有约 8%的粘土,以及少量黄铁矿(26.98
×
10-9
m3/kg,含有fe2o3)、金红石和钾长石等矿物,其
中fe2o3总含量(fe2o3来自于石英砂岩矿中的赤铁矿、磁铁矿、黄铁矿等)在0.18%左右。该石英砂岩矿经擦洗、脱除、20目过筛、160目过筛去除金红石、粘土及粗颗粒矿物后,作为原矿样本,该原矿样本中黄铁矿的含量为433ppm,fe2o3总含量为 812ppm。
[0058]
用现有的干式磁选装置仅能分离石英与赤铁矿和磁铁矿,无法分离石英与黄铁矿,黄铁矿中含有的fe2o3使得该原矿样本不能满足玻璃用石英砂的要求,若要符合要求,往往需要在磁选后再通过浮选等分离装置去除原矿样本中的fe2o3。因此用实施例1的单级干式磁选装置对该原矿样本进行磁选。用实施例1的磁选装置对该样本进行磁选,仅是对磁力辊中永磁环和聚磁环的宽度进行调整,永磁环和聚磁环的具体宽度见表3,磁选后得到的目标产物分别为石英精矿a-石英精矿e,其成分见表3。干式磁选装置中磁力辊上永磁环选用n45以上钕铁硼磁性材料制成,呈圆环状,直径100mm;聚磁环选用铁钴钒软磁合金制成,呈圆环状,直径100mm。磁选结果见表3,表3中的产率表示磁选后得到的目标产物石英精矿的质量占磁选前原矿样本质量的百分比。
[0059]
表3不同磁力辊的干式磁选对原矿样本磁选后的结果
[0060][0061]
表3结果显示,本实用新型的干式磁选装置在保证产率变化不大的基础上,能使磁选后矿物(见石英精矿c、石英精矿d和石英精矿e)中fe2o3含量低于0.06%(600ppm),同时满足qb/t 2196-1996《玻璃工业用石英砂的分级》中对一般浮法石英砂(要求 fe2o3含量<600ppm)的要求。而磁力辊中永磁环宽度较宽时(≥6mm),磁选后矿物(如石英精矿a和石英精矿b)中fe2o3含量无法均高于600ppm,不能满足qb/t 2196-1996 《玻璃工业用石英砂的分级》中对一般浮法石英砂(要求fe2o3含量《600ppm)的要求,仅能满足对普通石英砂(要求fe2o3含量<400ppm)的要求。本实验结果表明,本实用新型的干式磁选装置可以将石英砂岩矿中的黄铁矿分离去除,使得磁选后的石英精矿中fe2o3含量满足一般浮法石英砂的要求,无需再通过浮选等分离装置以去除石英砂岩矿中的黄铁矿。
[0062]
以上所述仅是本实用新型的优选实施方式,应当指出的是,对于本技术领域的普通技术人员来说,在不脱离本实用新型原理的前提下,还可以做出若干改进和润饰,这些改进和润饰也应视为本实用新型的内容。