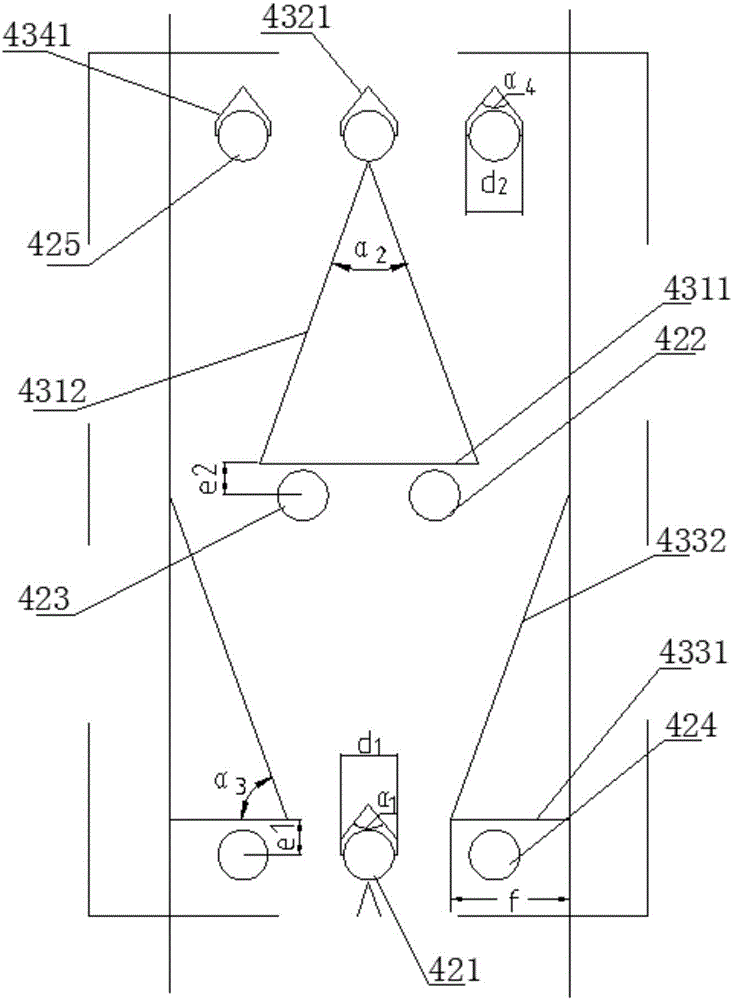
本发明涉及热解反应器,具体涉及一种移动床热解反应器。
背景技术:
:现代煤化工为实现低阶煤等含碳燃料的高效清洁转化利用,已开发出多种综合煤化工技术,热解-燃烧解耦、热解-化学品解耦、热解-气化解耦等,但真正实现工业化的却不多,从中试向工业化放大的过程中遇到了各式技术难题。其中尤以热解反应器设计、后续净化处理工艺尤为突出。一些干馏炉只能用来热解块状油页岩和煤,小粒径物料无法利用,资源利用率低,粉状物料因无法利用而大量堆积;以气体为热载体的炉型,因冷凝回收系统庞大,热解气热值低,焦油收率低等问题,难以进一步推广示范;以固体为热载体的炉型,则存在原料和热载体均匀混合,分离等问题,而限制了其进一步发展。技术实现要素:为解决上述问题,本发明提供了一种粉状含碳燃料热解用的移动床热解反应器。本发明提供的一种快速热解反应器,所述移动床热解反应器包括反应器本体、辐射管和多个金属挡板组件;所述辐射管为多个,水平同方向间隔排布在所述反应器本体内的不同高度,相邻高度层的所述辐射管错列布置;所述金属挡板组件为多个,所述金属挡板组件包括水平挡板和斜板,所述金属挡板组件位于对应的辐射管上方,所述金属挡板组件的竖向投影覆盖对应的辐射管。进一步地,所述水平挡板与其下方最近的辐射管中心的垂直距离为该辐射管直径的1-1.5倍。进一步地,所述辐射管包括第一辐射管、第二辐射管、第三辐射管,所述金属挡板组件包括第一金属挡板组件和第二金属挡板组件,所述水平挡板包括第一水平挡板,所述斜板包括第一斜板和第二斜板;所述第一金属挡板组件由一个所述第一水平挡板和两个所述第一斜板连接而成,所述第一水平挡板位于所述第一斜板的下方,所述第一金属挡板组件是等腰三角形;所述第一金属挡板组件的顶端与所述第一辐射管的底端相连;所述第二辐射管和所述第三辐射管位于同一水平面上,且被所述第一金属挡板组件的竖向投影覆盖;所述第二金属挡板组件包括两个所述第二斜板,所述第二金属挡板组件开口向下;两个所述第二斜板的一端相连,并形成所述第二金属挡板组件的顶角α1;所述第一辐射管上方设置有所述第二金属挡板组件,所述第一辐射管与所述第二金属挡板组件相连,且被所述第二金属挡板组件的竖向投影覆盖。进一步地,所述第一金属挡板组件的顶角α2为15°-60°。进一步地,所述顶角α1为60°-90°,所述第二金属挡板组件的竖直截面的宽度为所述第一辐射管直径的1.1-1.5倍。进一步地,所述辐射管包括还第四辐射管,所述金属挡板组件还包括成对出现的第三金属挡板组件,所述水平挡板还包括第二水平挡板,所述斜板还包括第三斜板;所述第三金属挡板组件由一个所述第二水平挡板和一个所述第三斜板连接而成,所述第二水平挡板在所述第三斜板的下方;所述第二水平挡板的一端和所述第三斜板的一端分别与所述反应器本体的内侧壁相连,所述第二水平挡板的另一端和所述第三斜板的另一端相连并形成夹角α3;所述第四辐射管被所述第三金属挡板组件的竖向投影覆盖。进一步地,所述夹角α3的角度范围为40°-70°。进一步地,所述第二水平挡板的水平长度为所述反应器本体的宽度的1/3-1/2。进一步地,所述辐射管还包括第五辐射管,所述金属挡板组件还包括第四金属挡板组件,所述斜板包括第四斜板;所述第四金属挡板组件包括两个所述第四斜板,所述第四金属挡板组件开口向下;两个所述第四斜板的一端相连,并形成所述第四金属挡板组件的顶角α4;所述第五辐射管与所述第四金属挡板组件相连,且被所述第四金属挡板组件的竖向投影覆盖。进一步地,所述顶角α4为60°-90°,所述第四金属挡板组件的竖直截面的宽度为所述第五辐射管直径的1.1-1.5倍。本发明提供的移动床热解反应器能有效的热解粉状含碳燃料。本发明提供的移动床热解反应器采用了蓄热式无热载体辐射管加热技术,无需气、固热载体,提高了热解气的热值,该反应器结构简单、占地面积小,易于工业化。其次,反应器内设置了金属挡板组件,金属挡板组件能增加含碳燃料在热解反应器内停留的时间。因此,添加金属挡板组件后,反应器的高度可降低。若不改变反应器本体的高度,添加金属挡板组件后,可将辐射管的垂直间距加大,从而可减少反应器内辐射管的数量。而且,金属挡板组件还能有效地起到保护辐射管不受受到物料冲刷,延长辐射管的使用寿命。此外,金属挡板组件还可以起到打散物料的作用,提高含碳燃料的热解效果。附图说明图1为实施例中一种移动床热解反应器的结构示意图;图2为图1中A区的局部放大图。图中:1、进料料斗;2、螺旋进料器;3、螺旋出料器;41、反应器本体;421、第一辐射管;422、第二辐射管;423、第三辐射管;424、第四辐射管;425、第五辐射管;4311、第一水平挡板;4312、第一斜板;4321、第二斜板;4331、第二水平挡板;4332、第三斜板;4341、第四斜板;44、燃料气进口;45、空气入口;46、烟气出口;47、油气出口。具体实施方式以下结合附图和实施例,对本发明的具体实施方式进行更加详细的说明,以便能够更好地理解本发明的方案及其各个方面的优点。然而,以下描述的具体实施方式和实施例仅是说明的目的,而不是对本发明的限制。需要说明的是,本发明中的“水平挡板”指得是水平放置的金属挡板,“斜板”指得是倾斜放置的金属挡板,“辐射管”指得是蓄热式无热载体辐射管。其次,术语“上”、“下”、“左”、“右”等指示的方位或位置关系为基于附图所示的方位或位置关系,仅是为了便于描述本发明,而不是要求本发明必须以特定的方位构造和操作,因此,不能理解为对本发明的限制。此外,本发明中的术语“第一”、“第二”、“第三”、“第四”或“第五”仅用于描述目的,而不能理解为指示或暗示相对重要性或隐含指明所指示的技术特征的数量,由此,限定有“第一”、“第二”、“第三”、“第四”或“第五”的特征可以明示或隐含地包括一个或者更多个该特征。本发明提供了一种移动床热解反应器(本发明中也简称为“反应器”)。参见图1,根据本发明的实施例对该移动床热解反应器进行解释说明,该反应器包括:反应器本体41、辐射管、金属挡板组件、燃料气进口44、空气入口45、烟气出口46、油气出口47、进料口和出料口。辐射管为多个,水平同方向间隔排布在反应器本体41的不同高度,相邻高度层的辐射管错列布置。金属挡板组件为多个,金属挡板组件包括水平挡板和斜板金属挡板组件位于对应的辐射管上方,金属挡板组件的竖向投影覆盖对应的辐射管。反应器本体41上设有进料口、出料口、燃料气进口44、空气入口45、烟气出口46和油气出口47。本发明提供的移动床热解反应器采用了蓄热式无热载体辐射管加热技术,无需气、固热载体,提高了热解气的热值,该反应器结构简单、占地面积小,易于工业化。参见图2,根据本发明的实施例,辐射管包括第一辐射管421、第二辐射管422、第三辐射管423、第四辐射管424和第五辐射管425,挡板包括第一金属挡板组件、第二金属挡板组件、第三金属挡板组件和第四金属挡板组件。第一金属挡板组件由一个第一水平挡板4311和两个第一斜板4312连接而成,第二金属挡板组件包括两个第二斜板4321,第三金属挡板组件由一个第二水平挡板4331和一个第三斜板4332连接而成,第四金属挡板组件包括两个第四斜板4341。根据本发明的实施例,第二金属挡板组件和第四金属挡板组件可只有两个第四斜板4341组成,也可再添加其他挡板,如图2所示。为了阐述方便,将图2中所显示的三层辐射管分别记为第一层辐射管、第二层辐射管和第三层辐射管。从图中可见,第一层辐射管包括两个第五辐射管425和一个第一辐射管421,第二层辐射管包括一个第二辐射管422和一个第三辐射管423,第三层辐射管包括两个第四辐射管424和一个第一辐射管421。根据本发明的实施例,除了第四辐射管424一定是毗邻于反应器本体41的辐射管外,其余的辐射管和金属挡板组件的具体位置、形状并不需要特别限定。挡板组件的材质为金属是原因是金属的热传导性好,能提高含碳燃料热解的效果。根据本发明的实施例,每层辐射管的种类也并不需要特别限定,辐射管可只有第一辐射管421、第二辐射管422和第三辐射管423,此时对应的金属挡板组件为第一金属挡板组件和第二金属挡板组件。辐射管也可只有成对出现的第四辐射管424,此时对应的金属挡板组件为第三金属挡板组件。在这两种基础上,辐射管还可增加第五辐射管425,对应的金属挡板组件为第四金属挡板组件。当然,这四种辐射管和这四种金属挡板组件都有是最佳的选择。参见图2,第一金属挡板组件的顶端与第一辐射管421的底端相连;第二辐射管422和第三辐射管423位于同一水平面上,且被第一金属挡板组件的竖向投影覆盖。第二金属挡板组件开口向下,两个第二斜板4321的一端相连,并形成第二金属挡板组件的顶角α1;第一辐射管421的上方设置有第二金属挡板组件,第一辐射管421与第二金属挡板组件相连,且被第二金属挡板组件的竖向投影覆盖。第四辐射管424被第三金属挡板组件的竖向投影覆盖;第二水平挡板4331的一端和第三斜板4332的一端分别与反应器本体41的内侧壁相连,第二水平挡板4331的另一端和第三斜板4332的另一端相连并形成第三金属挡板组件的夹角α3。第四金属挡板组件开口向下,两个第四斜板4341的一端相连,并形成第四金属挡板组件的顶角α4;第五辐射管425的上方设置有第四金属挡板组件,第五辐射管425与第四金属挡板组件相连,且被第四金属挡板组件的竖向投影覆盖。含碳燃料从进料口进入后,开始下落,碰到挡板后,被弹起,然后再下落;含碳燃料每碰到一次斜板,即被弹到一定高度,其下落速度被减缓,因此,增加了含碳燃料在热解反应器内的停留时间。而且,斜板还起到对含碳燃料的引流作用,增加了含碳燃料在反应器本体内移动的距离,这也能增加含碳燃料在热解反应器内的停留时间。因此,添加金属挡板组件后,反应器的高度可降低。若不改变反应器本体的高度,添加金属挡板组件后,可将辐射管的垂直间距加大,从而可减少反应器内辐射管的数量。其次,斜板还能有效地起到保护辐射管不受受到物料冲刷,延长辐射管的使用寿命。此外,斜板还可以起到打散物料的作用,提高含碳燃料的热解效果。参见图2,在第一金属挡板组件和第三金属挡板组件中,水平挡板都位于其对应的斜板的下方,水平挡板的作用是支撑斜板。根据本发明的实施例,α1的角度并不需要特别限定,发明人发现,α1的角度优选为60°-90°。α1的角度主要影响含碳燃料在第二斜板4321上停留的时间。α1太大,含碳燃料容易堆积到第二斜板4321上;α1太小,含碳燃料在第二斜板4321上的停留时间短,热解效果不好。根据本发明的实施例,第二金属挡板组件的竖直截面的宽度d1并不需要特别限定,只要大于第一辐射管421的直径即可。发明人发现,d1的长度最佳为第一辐射管421的直径的1.1-1.5倍,过长会影响辐射管热量的有效利用,过短对分散物料的作用不大。根据本发明的实施例,第一金属挡板组件的顶角α2的角度并不需要特别限定,发明人发现,α2的角度优选为15°-60°。α2的角度主要影响含碳燃料在第一斜板4312上的停留时间。α2太大,含碳燃料也容易堆积到第一斜板4312上;α1太小,含碳燃料在第一斜板4312上的停留时间短,热解效果不好。根据本发明的实施例,第一水平挡板4311距第二辐射管422或第三辐射管423的中心的垂直距离e1并不需要特别限定,发明人发现,e1最佳为第二辐射管422或第三辐射管423的直径的1-1.5倍。根据本发明的实施例,α3的角度并不需要特别限定,发明人发现,α3的角度优选为40°-70°。α3的角度主要影响含碳燃料在第三斜板4332上停留的时间。α3太大,含碳燃料也容易堆积到第三斜板4332;α3太小,含碳燃料在第三斜板4332上的停留时间短,热解效果不好。根据本发明的实施例,第二水平挡板4331的水平长度f并不需要特别限定,发明人发现,第二水平挡板4331的水平长度f的最佳长度为反应器本体41的宽度(其内壁的宽度)的1/3-1/2。参见图1,第三金属挡板组件可设置在某层辐射管的上方或下方,其具体位置并不需要限定,可以按实际需求进行设置,其最佳位置为两层辐射管之间。根据本发明的实施例,当第三金属挡板组件位于第四辐射管424上方时,第二水平挡板4331距第四辐射管424的中心的垂直距离e2并不需要特别限定,发明人发现,e2最佳为第四辐射管424的直径的1-1.5倍。根据本发明的实施例,α4的角度并不需要特别限定,发明人发现,α4的角度优选为60°-90°。α4的角度主要影响含碳燃料在第四斜板4341上停留的时间。α4太大,含碳燃料容易堆积到第四斜板4341上;α2太小,含碳燃料在第四斜板4341上的停留时间短,热解效果不好。根据本发明的实施例,第四金属挡板组件的竖直截面的宽度d2并不需要特别限定,只要大于第五辐射管425的直径即可。发明人发现,d2的长度最佳为第五辐射管425的直径的1.1-1.5倍,过长会影响辐射管热量的有效利用,过短对分散物料的作用不大。参见图1,根据本发明的实施例,反应器的进料口和螺旋进料器2的一端相连,螺旋进料器2的另一端与进料料斗1相连;反应器的出料口与螺旋出料器3相连。进料料斗1和螺旋进料器2用于将粉状含碳燃料送入反应器中,螺旋出料器3用于将含碳燃料热解后产生的固体产物运送至下一工段。进料料斗1、螺旋进料器2和螺旋出料器3并不是必要装置,可视现场情况和具体的工艺决定是否要添加。根据本发明的实施例,辐射管的直径及形状并不需要限定,公称直径为200-300mm的圆形管是最佳选择。根据本发明的实施例,左右相邻的两辐射管的水平间距也不需要限定,其最佳间距为200-400mm。根据本发明的实施例,上下相邻的两辐射管的竖直间距也不需要限定,其最佳间距为500-1200mm。根据本发明的实施例,反应器本体41的最佳高度为5-20m、最佳宽度(其内壁的宽度)为2-6m、最佳长度(其内壁的长度)为5-15m,反应器本体41中辐射管的最佳层数为10-25层。燃料气进口44和空气入口45分别与辐射管相连。下面参见具体实施例,对本发明进行说明。下述实施例中所取工艺条件数值均为示例性的,其可取数值范围如前述
发明内容中所示。下述实施例所用的检测方法均为本行业常规的检测方法。实施例用本发明提供的移动床热解反应器对珲春褐煤进行热解,该珲春褐煤的成分分析如表1所示,所用的移动床热解反应器的结构示意图如图1所示。其中,α1为70°,α2为40°,α3为60°,α4为70°,d1为330mm,d2为330mm,e1为300mm,e2为300mm,f为2m,辐射管均为是公称直径为300mm的圆形管,左右相邻的两辐射管的水平间距为400mm,上下相邻的两辐射管的竖直间距为1200mm。反应器本体41的高度为20m、内壁的宽度为6m、内壁的长度为15m,有25层辐射管。珲春褐煤热解的具体过程如下:将珲春褐煤送入进料料斗1中,经螺旋进料器2进入反应器中。每根辐射管单独控温,反应器自上而下设有三个区:干燥脱水区、热解反应区和半焦生成区。往辐射管中分别通入燃料气和空气,将干燥脱水区的温度控制在700℃、热解反应区的温度在控制600℃,半焦成熟区的温度控制在550℃。珲春褐煤自上而下依次通过干燥脱水区、热解反应区和半焦生成区,完成热解过程。热解产生的热解气和焦油从油气出口47中排出反应器本体41外并被进一步处理,产生的半焦通过螺旋出料器3送入下一个工序。热解还会产生烟气,烟气从烟气出口46中排出反应器本体1外,烟气与空气换热后会降温至200℃左右。将降温后的烟气用于干燥进入反应器的珲春褐煤。表2为反应器内各区温度分布,表3为热解产物的产量。表1珲春褐煤的成分分析Mad/%Vad/%Aad/%Fcad/%8.2937.2114.8239.68表2反应器各区温度分布序号反应区反应器内温度分布/℃1干燥脱水区7002热解反应区6003半焦生成区550表3热解产物产量序号反应物产物分析比例值/%1热解气14.692热解水10.793焦油12.374半焦62.15从表3可知,本发明提供的移动床热解反应器能有效的热解粉状含碳燃料。上述实施例中,干燥脱水区的温度设置得比较高,这样有利于速脱去入炉的含碳燃料所含的水分,而且还能减少干燥脱水区的所占用的空间。此外,将降温后的烟气用于干燥进入反应器的含碳燃料,这样能进一步提高反应器效率和燃烧效率。综上可知,本发明提供的移动床热解反应器采用了蓄热式无热载体辐射管加热技术,无需气、固热载体,提高了热解气的热值,该反应器结构简单、占地面积小,易于工业化。其次,反应器内设置了金属挡板组件,金属挡板组件能增加含碳燃料在热解反应器内停留的时间。因此,添加金属挡板组件后,反应器的高度可降低。若不改变反应器本体的高度,添加金属挡板组件后,可将辐射管的垂直间距加大,从而可减少反应器内辐射管的数量。而且,金属挡板组件还能有效地起到保护辐射管不受受到物料冲刷,延长辐射管的使用寿命。此外,金属挡板组件还可以起到打散物料的作用,提高含碳燃料的热解效果。需要说明的是,以上参照附图所描述的各个实施例仅用以说明本发明而非限制本发明的范围,本领域的普通技术人员应当理解,在不脱离本发明的精神和范围的前提下对本发明进行的修改或者等同替换,均应涵盖在本发明的范围之内。此外,除非特别说明,那么任何实施例的全部或一部分可结合任何其它实施例的全部或一部分来使用。当前第1页1 2 3