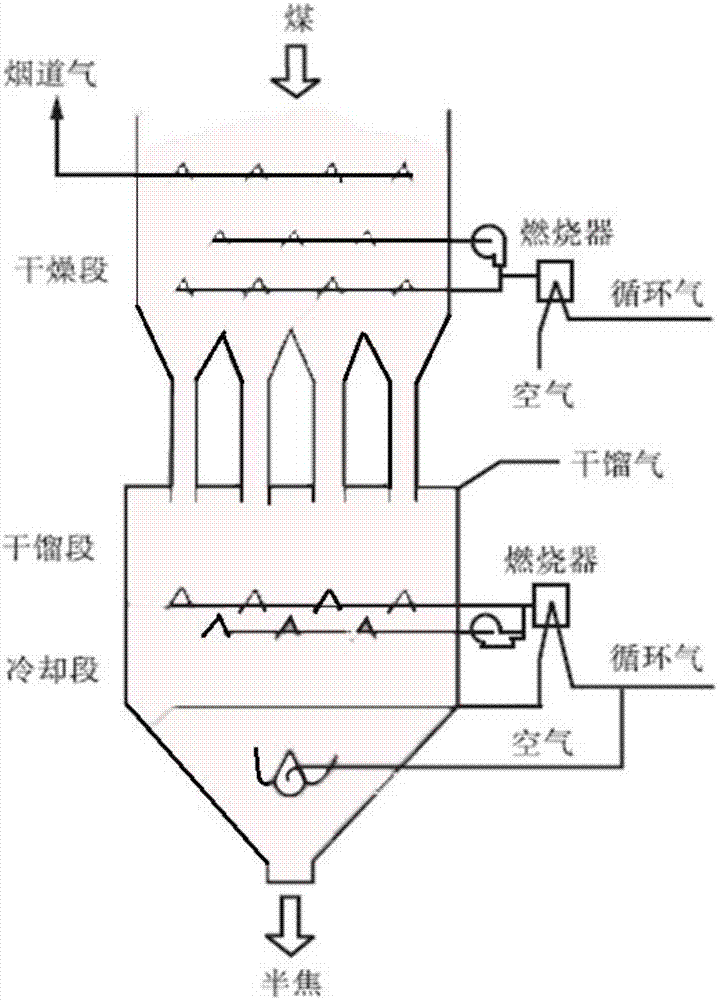
本实用新型总地涉及热解系统,具体涉及一种煤热解系统。
背景技术:
:我国煤炭资源丰富,原煤除了部分用于炼焦、转化加工外,绝大部分用于直接燃烧。煤直接燃烧,使得煤炭中富含的油气资源不能被提炼而得到充分利用,且直接燃烧热效率低,对环境污染严重。煤的热解是将煤在惰性气氛下加热,制取半焦、煤气和焦油等产品,得到的这些产品,又可以梯级利用。因而煤热解对油气资源充分提取的同时,又提高了煤炭的综合利用效率。煤热解工艺可分为外热式和内热式两类。外热式热效率低,挥发产物二次分解严重。内热式工艺克服了外热式的缺点,借助热载体(固体热载体和气体热载体)把热量传递给煤。气体热载体工艺,存在干馏气被冲稀,冷凝回收系统庞大,气体热值低,难以进一步综合利用的缺点。固体热载体工艺相对来说具有一定的优势,但是存在工艺复杂而导致操作环节太多、制造成本高昂等缺点。此外,目前煤干馏技术均未设有预活化装置,存在热解油较重、分子量较大等问题。图1是现有技术一的煤热解工艺流程图。该技术的工艺流程为:原料煤由煤仓9经螺旋给料器10进入破碎机11,原料煤被破碎至6mm以下。破碎后的原料煤和高温热烟气(约550℃)在煤干燥管中接触换热,原料煤被换热至100-120℃左右,同时经干燥后煤含水量<4%。煤经煤干燥管后,同热烟气一块被输送至干煤旋风分离器2中。在干煤旋风分离器2中,煤和热烟气经旋风分离,烟气经风机排放。预热后的粉煤与粉焦同加热提升管6中的热载体粉焦混合,热载体粉焦温度约为800℃。热粉焦和粉煤在干馏槽5中混合热解,产生半焦、煤热解气和焦油。热解产生的粉焦一部分经冷却塔7冷却后排出,一部分经返料腿进粉焦加热提升管做为热载体被循环利用。现有技术一的缺点为:干馏炉的干馏段不能够及时导出热解油气,一次热解产物滞留易发生二次裂解;干馏后的粉焦作为热载体被循环使用,其工艺流程复杂;未与发电系统相联合;物料在反应炉内分布不够均匀;未预先对原料活化,热解油较重,品质低。图2是现有技术二的煤热解工艺流程图。其工艺流程为:低阶煤经压制成型后(25-60mm)进热解炉,煤自上而下移动,与燃烧后逆流而上的热烟气直接接触换热。煤由炉顶进料时水分约15%,在干燥段可脱除至1.0%以下。逆流而上的热烟气由250℃降至80-100℃。干燥后的原料在干馏/热解段被600-700℃的热烟气加热至500℃左右,发生热解反应后,热烟气温度降至250℃左右,如前述的逆流上升再用于原料煤的干燥。热解后生成的半焦进入冷却段与冷空气换热后由炉底排出,干馏/热解段生成的热解油气经冷却、冷凝等步骤,得到焦油和热解气。现有技术二的缺点为:不能处理小颗粒物料,原料利用率不高;或者粉煤需要经过压制成型后才可利用,增加生产成本;半焦中的固定碳未能得到充分利用,热效率低;油气不能快速导出,油收率不高;未与发电系统相联合;未预先对原料活化,热解油较重,品质低。因此,为了提高原料的利用率,提高加热燃烧的热效率,得到品质较高的热解油,快速导出油气,避免油气的二次裂解,提高油收率,有必要提出一种新的煤热解系统。技术实现要素:本实用新型的目的在于提供一种煤热解系统,以解决未预先对煤进行干燥和活化、原料利用率低、油气二次裂解、热解油品质较低的问题。本实用新型提供了一种煤热解系统,其包括煤料斗、微波干燥器、机械活化器、热解料斗和移动床热解反应器,其中移动床热解反应器包括:煤入口,所述煤入口位于所述反应器的顶部;半焦出口,所述半焦出口位于所述反应器的底部;蓄热式辐射管,所述蓄热式辐射管在所述移动床热解反应器的内部沿着所述反应器的高度方向多层布置,每层具有多根在水平方向上彼此平行的蓄热式辐射管;油气抽出伞,所述油气抽气伞布置在所述反应器内部、位于所述蓄热式辐射管顶层的上方,并与所述反应器的侧壁上的油气出口相连通;所述煤料斗、微波干燥器、机械活化器和热解料斗依次连通,所述热解料斗与所述移动床热解反应器的煤入口相连通。上述的系统,所述机械活化器为球磨机。上述的系统,所述系统还包括第二螺旋进料器,所述第二螺旋进料器分别与所述热解料斗的出口和所述热解反应器的煤入口相连通。上述的系统,所述系统还包括第一螺旋进料器,所述第一螺旋进料器分别与所述煤料斗的出口和所述微波干燥器的入口相连通。上述的系统,所述系统还包括热解旋风分离器、过滤器和分馏塔,所述热解旋风分离器分别与所述热解反应器的油气出口和所述过滤器的入口相连通,所述过滤器的出口与所述分馏塔的入口相连通。上述的系统,所述系统还包括燃气罐,所述分馏塔的气体出口与所述燃气罐相连通。上述的系统,所述系统还包括气化炉,所述气化炉通过螺旋输送机与所述热解反应器的半焦出口相连通。上述的系统,所述系统还包括可燃气通道,所述可燃气通道将所述气化炉和所述热解反应器的蓄热式辐射管的可燃气入口相连通。本实用新型的有益效果在于,采取蓄热式辐射管下行床工艺加热煤,热解温度分布均匀,加热效果好,可实现物料的快速热解,油气产率高。该系统应用微波干燥技术,干燥速度快,效率高,干燥均匀,实现了节能、清洁生产,且易于实现自动化控制。该系统还对煤进行了预先机械活化,增加了煤的化学反应活性,降低了热解反应所需要的温度,从而热解焦油较轻,品质好,汽柴油馏分高。该系统还设有油气抽出伞,热解产生的油气能被迅速导出,有效地抑制了油气的二次裂解,提高了油收率。整体而言,该系统的热解炉操作温度低,能耗低,且装置易于日常维护。附图说明图1为现有技术一的煤热解工艺流程图;图2为现有技术二的煤热解工艺流程图;以及图3为本实用新型的煤热解工艺流程图。具体实施方式以下结合附图和实施例,对本实用新型的具体实施方式进行更加详细的说明,以便能够更好地理解本实用新型的方案及其各个方面的优点。然而,以下描述的具体实施方式和实施例仅是说明的目的,而不是对本实用新型的限制。如图3所示,本实用新型实施例的一种煤热解炉系统流程图,其工艺流程简单描述如下:热解煤原料与燃气及助燃气体作为输入源输入热解炉,原料经过加热分解,输出热解气及热解焦油,分别经不同通道输出。下面结合图3对本系统加以详细说明。本实用新型实施例的一种煤热解系统流程图,该蓄热式下行床热解系统包括:1.煤料斗;2.微波干燥器;3.蓄热式下行床反应器;4.球磨机(机械活化器)5.热解料斗;6.螺旋进料器;7.热解旋风分离器;8.过滤器;9.分馏塔;10.燃气引风机;11.燃气罐;12.燃气送风机;13.气化炉;14.螺旋输送机;15.油气抽出伞。煤料斗1通过进料装置连接至微波干燥器2入口,微波干燥器2出口与球磨机4入口相连接。球磨机4出口与热解料斗5入口相连接,热解料斗出口通过螺旋进料器6连接到蓄热式下行床反应器3的入料口。下行床反应器3包括上部进料煤入口,燃气、空气入口和油气、烟气、半焦出口,油气抽出伞。油气抽出伞出口通过反应器的油气出口与一级热解旋风分离器7的入口连接,二级热解旋风分离器7的出气口与过滤器8入口连接。过滤器8出口与分馏塔9入口连接,分馏塔9出气口与燃气引风机10入口连接。燃气引风机10出口与燃气罐11入口连接,燃气罐11出口与燃气送风机12入口连接;燃气送风机12出口与下行床反应器3的燃气入口连接。下行床反应器3半焦出口设计在底部,连接在螺旋输送机14的入口。二级热解旋风分离器7出料口与螺旋输送机14的入口相连接。螺旋输送机14的出口与气化炉13的入口连接。气化炉13的燃气出口与下行床反应器3的燃气入口相连接。本实用新型的蓄热式下行床热解工艺包括:(1)破碎至粒度≤20mm的颗粒煤通过煤料斗1进入微波干燥器2,在微波干燥器中,煤被快速、均匀的干燥后进入到球磨机4中进行机械活化,球磨机中装有球磨介质钢球若干,由搅拌电机带动旋转,旋转过程中钢球对煤进行摩擦、碰撞、冲击、剪切等机械力作用,增加了煤的化学活性。机械活化时间控制在10min-2h范围内。经过机械活化的粉末煤进入到热解料斗5中。(2)煤在热解料斗5中经螺旋进料器6进入蓄热式下行床反应器3,在蓄热式下行床反应器中均匀布置了单向蓄热式辐射管,管壁温度利用燃气调节阀控制在400-700℃范围,煤在反应器中自上而下停留5s-5min,并被加热到400-600℃,完成热解过程。(3)热解产生的油气经过油气抽出伞,在2秒内汇集到一起,迅速排出反应器外,有效地抑制了油气的二次裂解,提高了装置的油收率。油气从反应器排出并通过两级旋风分离器7后进入过滤器8中过滤,过滤后的油气进入分馏塔9分馏得到汽油、柴油和重油。分馏之后剩下的干馏气经燃气引风机10送入燃气罐11,干馏气经燃气送风机12和气化炉13产生的可燃气一起送入热解反应器3的辐射管燃气入口。(4)煤热解产生的半焦与两级旋风分离器7分离下来的粉末半焦一起通过螺旋输送机14送入气化炉13,气化后的灰渣被排出。该系统应用微波干燥技术,将微波能转化为分子运动能,并以热量的形式表现出来,使水的温度升高而脱离物料,从而使物料得到干燥。在传统的干燥工艺中,为提高干燥速度,需升高外部温度,加大温差梯度,然而随之容易产生物料外焦内生的现象。但采用微波加热时,不论物料形状如何,热量都能均匀渗透,并可产生膨化效果,利于粉碎。因微波能穿透物料直接加热,物料中的极性分子在微波场的作用下极速震荡,提高了化学反应的活化能,加快了反应速度,同时干燥均匀,效率高,实现了节能、清洁生产,且易于实现自动化控制。该系统还可以对煤进行预先机械活化,机械活化是指固体物质在摩擦、碰撞、冲击、剪切等机械力作用下,使晶体结构及物化性能发生改变,使部分机械能转变成物质的内能,从而引起固体的化学活性增加,煤化学活性增强,颗粒化学能增加,提高了煤的化学反应活性,热解反应所需要的温度降低,从而热解焦油较轻,品质好。机械活化后的煤进入蓄热式快速热解反应装置中,经过快速热解可大量提取油气产品。该系统还在蓄热式反应器内部安装有油气抽出伞,热解产生的油气被迅速导出,有效地抑制了油气的二次裂解,提高了油收率。实施例利用蓄热式下行床热解系统对新疆煤进行处理,原料的基础数据、工艺操作参数和物料平衡见表1-表2。表1:新疆长焰煤基础数据表1中Mad代表空干基水分;Ad代表干燥基灰分;Vad代表空干基挥发分;表2:工艺操作参数序号参数名称参数值序号参数名称参数值1上部辐射管壁面温度505℃反应器下部温度450℃2中部辐射管壁面温度500℃反应器出口温度445℃3下部辐射管壁面温度465℃旋风出口温度430℃4反应器上部温度430℃反应器压力1.7Kpa5反应器中部温度455℃利用该系统制得的热解油品性质:热解油密度为1.02g·cm-3,密度较低,油品较轻;对热解油品进行模拟蒸馏得到,汽油馏分占14%,柴油馏分占49%,汽柴油馏分含量高。用该系统处理新疆长焰煤,得到的焦油产率高达9%,是铝甑含油率的96%,油收率高。最后应说明的是:显然,上述实施例仅仅是为清楚地说明本实用新型所作的举例,而并非对实施方式的限定。对于所属领域的普通技术人员来说,在上述说明的基础上还可以做出其它不同形式的变化或变动。这里无需也无法对所有的实施方式予以穷举。而由此所引申出的显而易见的变化或变动仍处于本实用新型的保护范围之中。当前第1页1 2 3