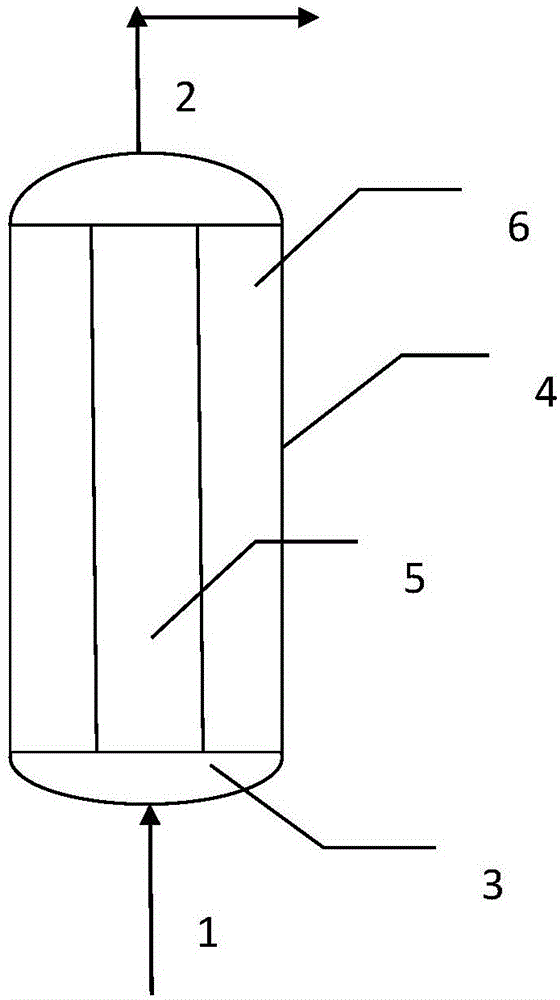
本发明涉及一种劣质重油的加氢处理方法,尤其是一种金属杂质含量高、残炭含量高的劣质重油的加氢处理方法。
背景技术:
:随着石油的日益变重、质量变差,给石油加工带来越来越大的困难。重油中含有大量金属杂质如ni、v等,大部分金属杂质存在于沥青质中,是很难脱除的成分。通常根据重油中金属杂质的含量来选择加工工艺。当金属杂质v+ni含量200μg/g以下,残炭值15%以下时,可以采用固定床工艺。固定床的工艺过程简单,投资小,容易维护,是重油加氢工艺过程的首选。当金属杂质v+ni含量200μg/g以上,残炭值15%以上时,一般采用沸腾床或悬浮床工艺。但是,沸腾床工艺极其复杂,装置投资大,很难维护,这是造成该工艺不易推广的重要原因。而悬浮床工艺也是比较复杂的,工艺也存在很多问题,不易推广。溶剂脱沥青是用萃取的方法将重质油中的胶质和沥青质取出,以生产脱沥青油和脱油沥青。目前,溶剂脱沥青在加工重质油方面,主要目的是获得脱沥青油,以作为催化裂化、固定床加氢处理等工艺的原料。但对于脱油沥青来说,由于其主要成分是沥青质,沥青质的基本结构单元是多个芳香环组成的稠合芳香环系,其周围连接有若干个环烷环、芳香环,环上带有若干个长度不一的烷基侧链,芳核结构中还有s、n、o杂原子基团,同时含有络合v,ni等多种金属。沥青质由若干个这类结构单元以烷基或杂原子形成的桥键连接而成,以缔合状态存在,是加氢反应中主要的结焦前驱物,因此,受现有加氢工艺的限制,很难将沥青质组分有效地转化为轻质燃料油。因此,能够经济有效地将高沥青质原料转化为轻质燃料油是本领域中的一个难题。cn200910162163.9公开了一种组合工艺加工劣质原油的方法。该方法是将劣质原油原料先经溶剂脱沥青得到脱沥青油;脱沥青油经预热后进入催化转化反应器的第一反应区,反应生成的油气和用过的催化剂任选与轻质原料油混合后进入第二反应区进行裂化反应、氢转移反应和异构化反应,经液固分离后,反应产物进一步分离为干气、液化气、汽油、柴油和催化蜡油,其中第一反应区和第二反应区反应条件足以使反应得到占原料油12%~60%的催化蜡油,催化蜡油加氢后引入催化转化装置进一步反应得到轻质燃料油产品,尤其是高辛烷值汽油。该方法主要是将脱沥青油转化为轻质燃料油,而并未涉及到脱油沥青的后续加工。cn201110352418.5公开了一种劣质重油加工方法。该方法包括:(1)劣质重油原料进入溶剂脱沥青装置,得到脱沥青油和脱油沥青;(2)将步骤(1)得到的脱油沥青进入沸腾床加氢处理装置,在氢气和沸腾床加氢处理催化剂存在下,进行沸腾床加氢处理;(3)将步骤(2)得到的沸腾床加氢处理反应流出物与脱沥青油混合进入固定床加氢处理装置,在氢气与固定床加氢处理催化剂存在下,进行固定床加氢处理,固定床加氢处理反应流出物得到的生成油作为催化裂化装置的原料。沸腾床工艺复杂,设备昂贵,固定资产投资大。cn200410050788.3公开了一种劣质重油或渣油的处理方法。该方法包括:重油或渣油原料先进入溶剂抽提装置;所得的脱沥青油进入固定床加氢处理装置进行加氢处理;所得的加氢尾油进入催化裂化装置,其中所得的油浆与脱油沥青一起进入悬浮床加氢装置,产物经分离得到轻质馏分和未转化尾油,其中未转化尾油循环至溶剂抽提装置。该方法还可将悬浮床加氢产生的轻石脑油作为溶剂抽提装置的溶剂。悬浮床加氢催化剂是均相催化剂,易使结焦物吸附在催化剂的活性中心,使其快速失活。综上,对于金属杂质含量高、残炭含量高的劣质重油的加氢处理,现有技术中的固定床工艺、沸腾床工艺和悬浮床工艺都各有弊端,一种更加适用于劣质重油加氢处理的方法一直是本领域的研究热点。技术实现要素:针对现有技术中的不足之处,本发明提供了一种劣质重油的加氢处理方法。本发明方法能够将劣质重油全馏分转化为轻质燃料油和重质燃料油,且重质燃料油性质良好,装置运转周期长。本发明提供一种劣质重油的加氢处理方法,采用立式膜芯式反应器,该反应器包括反应器本体、进料分布盘和中空催化剂膜芯元件;其中所述反应器本体设置有进料口和出料口,所述的中空催化剂膜芯元件竖直设置于反应器本体内部,所述的中空催化剂膜芯为设置有中空通道的膜层催化剂,所述反应器本体与中空催化剂膜芯元件周侧之间形成物料空间;所述中空催化剂膜芯包括载体组分和加氢活性金属组分,优选地,以中空催化剂膜芯的重量为基准,加氢活性金属的含量为30%~70%,优选为40%~70%;劣质重油与氢气由进料口进入立式膜芯式反应器,在加氢处理条件下,与中空催化剂膜芯接触进行加氢处理反应,所得加氢处理产物由出料口排出反应器。所述膜芯式反应器可以采用一个,也可以采用多个反应器串联,每个膜芯式反应器中,采用一个中空催化剂膜芯元件或采用多个并联的中空催化剂膜芯元件,该中空催化剂膜芯元件采用一个中空催化剂膜芯或者采用多个并联的中空催化剂膜芯,每个膜芯式反应器中,所述中空催化剂膜芯的总个数为1~24。所述中空催化剂膜芯的性质如下:体积密度为0.36~0.65g/cm3,侧压强度≥12n/mm,一般为12~30n/mm,孔容为0.5~1.2ml/g,比表面积为40~150m2/g,平均孔直径为20~65nm。优选地,所述中空催化剂膜芯的孔分布如下:孔道直径在10nm以上所占的孔容占总孔容的80%以上,优选为90%以上;进一步地,孔道直径在10nm以下所占的孔容占总孔容的20%以下,优选为10%以下,孔道直径10~30nm所占的孔容占总孔容的35%以下,优选为12%~35%,孔道直径为30~100nm所占的孔容占总孔容40%以上,优选为45%~80%,孔道直径在100nm以上的所占的孔容占总孔容的50%以下,优选为8%~30%。所述的中空催化剂膜芯的外形可以为柱状,比如圆柱状、棱柱状等。所述的中空催化剂膜芯中的中空通道的横截面可以为圆形、椭圆形、三角形、多边形或异形。所述膜芯式反应器中,中空催化剂膜芯优选为同心环状圆柱体,中空催化剂膜芯的高与外径比为1~20:1,优选为1.5~15:1,外径与内径之比为1.2~50:1,优选为2~30:1。优选地,所用的中空催化剂膜芯的高一般在2000mm以下。所述中空催化剂膜芯中,载体采用氧化铝基载体,其中也可以含有助剂组分,比如硅、镁、钛、锆中的至少一种,所述助剂含量以元素计占载体组分重量的15%以下。所述的加氢活性金属组分采用第vib族和/或第viii族金属组分,第vib族金属优选为w、mo中的至少一种,第viii族金属优选为ni、co中的至少一种,进一步优选为第vib族金属以氧化物计与第viii族金属以氧化物计的重量含量之比为1~8:1,优选为1~6:1。所述中空催化剂膜芯的制备方法可以采用发泡法、溶胶凝胶造孔法和胶束模板剂法中的至少一种方法制备含氢氧化铝的混合料,然后利用模具压制成具有中空通道的中空催化剂膜芯中间体,再经干燥和焙烧,得到中空催化剂膜芯。本发明所述的发泡法可以采用拟薄水铝石、水、粘结剂和树脂混合,利用模具压制成具有中空通道的中空催化剂膜芯,经100~120℃烘干,经800~1100℃焙烧,得到中空催化剂膜芯。本发明所述的溶胶凝胶造孔法是溶胶凝胶法制备拟薄水铝石,再加入造孔剂、胶溶酸、水捏合,利用模具压制成具有中空通道的中空催化剂膜芯,经100~120℃烘干,经550~1100℃焙烧,得到中空催化剂膜芯。本发明所述的胶束模板剂法是采用正向胶束法或反向胶束法制备成拟薄水铝石,加入胶溶酸、水捏合,利用模具压制成具有中空通道的中空催化剂膜芯,经100~120℃烘干,550~1100℃焙烧,得到中空催化剂膜芯。所述膜芯式反应器可以采用上进料,也可以采用下进料的进料方式,优选采用下进料的进料方式。所述膜芯式反应器物料可以采用从膜芯外部通过膜层流向中空通道,也可以采用中空通道通过膜层流向膜芯外,膜芯的外部物料空间与膜芯内部中空通道之间形成的压差在2mpa以下,优选为0.2~1.0mpa。本发明方法优选采用下进料和从膜芯外部通过膜层流向中空通道方式操作。其中,反应器本体下部设置有进料口。所述进料分布盘设置在中空催化剂膜芯元件之下。所述进料分布盘均布开口,所述开口与物料空间相通。所述本体的上部设置有出料口,所述的出料口与中空催化剂膜芯的中空通道相通。本发明所述中空催化剂膜芯的外层可设置可装卸的保护结构构件。所述保护结构构件可以是网状结构,包括冲孔网、焊接网、铸造筛网、金属丝网、金属菱形网、石笼网、开纹斜纹不锈钢轧花网、席型网、筛板或筛片中的至少一种,但不限于上述例举的网状结构。上述网状结构的保护结构构件可以采用如下步骤制备:采用激光刻缝技术、冷冲压成型技术或机械钻孔技术,将钢板制备成条缝或孔的网板或中空构件,或者采用编制技术将金属丝制备成网板或中空构件。所述的网板或中空构件可以为一个或多个,若为多个时,可以采用焊接等方式连接。所述的网板或中空构件设置于中空催化剂膜芯的外层,用于保护中空催化剂膜芯。所述的劣质重油为含有沥青质的重油,可以来源于石油烃和/或其它矿物油,其中石油烃可以源于渣油和/或原油,其中渣油可以选自减压渣油、常压渣油的一种或多种,原油可以选自稠油。其它矿物油为煤液化油、油砂油和页岩油中的一种或多种。所述劣质重油中,金属杂质v和ni的含量可以为150μg/g以上,还可以为200μg/g以上,一般可以为150~900μg/g,还可以为200μg/g~900μg/g,残炭的重量含量可以为10%以上,还可以为15%以上,一般可以为10%~28%,还可以为15%~28%。所述劣质重油中,硫的重量含量可以为3%以上,可以为4%以上,还可以为5%以上。所述的加氢进料还可以包括其他来源的沥青组分,比如煤焦沥青、直馏沥青、天然沥青中的一种或多种。所述的加氢处理的操作条件如下:反应压力为11.0~17.5mpa,液时体积空速为0.1~2.0h-1,氢油体积比为380~1000:1,反应温度为350~411℃,优选的操作条件如下:反应压力为12.0~16.0mpa,液时体积空速为0.2~0.6h-1,氢油体积比为500~1000:1,反应温度为375~390℃。所述膜芯反应器,尤其是采用多个膜芯反应器,各膜芯反应器流出物可以进行气液分离,所得到的气相产物脱除h2s和nh3,回收的氢气可以循环使用。其中,脱除h2s一般采用碱液吸收法,脱除nh3一般采用硫酸溶液吸收法。所述加氢处理产物经分馏可以得到轻馏分油(比如汽油、柴油)和重馏分油,其中重馏分油符合船用燃料的要求,可以作为船用燃料用。本发明所述的膜芯式反应器采用多个串联时,还设有切分管路,用于各个反应器的切分和切入,当催化剂活性不能满足应用要求时,可采用膜芯式反应器切出再生方法。本发明方法,可以监测每个膜芯式反应器,当监测到某膜芯式反应器的催化性能下降时,将该膜芯式反应器切出对其中的中空催化剂膜芯进行再生,再生后再切入继续进行反应,优选地,对每个膜芯反应器所得产物的残炭含量进行监测,以反应初始的脱残炭率为基础,切出脱残炭率降低5个百分点的膜芯式反应器,对其中的中空催化剂膜芯进行再生,再生后再切入继续进行反应。其中,反应初始的脱残炭率为反应器进原料后反应稳定时的脱残炭率。反应器进原料包括因各种原因反应器需重新切入原料的情形,比如装置新开工以及反应器切出催化剂再生后切入时等,此时均需重新测得反应初始的脱残炭率。本发明所述的膜芯式反应器中的中空催化剂膜芯采用切出再生方法,再生方法可以采用高温焙烧方法,具体如下:膜芯式反应器中的中空催化剂膜芯不能满足应用要求时,将该反应器温度降低到100℃以下,氢气压力降低到常压,使装置内物料全部流出反应器,用轻质馏分油洗涤反应器后,打开膜芯式反应器,取出活性降低的膜元件,将中空催化剂膜芯放入100℃烘箱中干燥1~5h,在放入焙烧炉中,通入空气,3~5℃/min,升温到150~250℃焙烧1~5h,然后继续升温到450~500℃焙烧4~6h。对于常规固定床渣油加氢处理催化剂来说,催化剂失活后通常需要全部新鲜催化剂来替换,而无法采用烧炭的方法进行再生。所述的加氢处理产物中,硫含量在0.5wt%以下,残炭值在5wt%以下,金属杂质,以ni和v的含量计在50μg/g以下。本发明的劣质重油的加工方法具有如下优点:1、本发明方法采用膜芯式反应器,不但能够有效地脱除劣质重油中的硫、氮和金属杂质,而且能够全部转化得到轻质燃料油和重质燃料油,重质燃料油可作为船用燃料使用。而对于劣质重油原料,若采用常规渣油固定床工艺,反应器的运转周期会很短,而且失活后的催化剂无法进行再生,需要全部替换为新鲜的催化剂,因此,常规渣油固定床加氢来说,各催化剂的利用率极低。2、本发明方法中,虽然中空催化剂膜芯没有固定床催化剂的空隙率,但有利于脱除的金属杂质缓慢地由下而上沉积在催化剂膜层中,并不会出现膜芯压降过高的问题,催化剂利用率高,催化效果稳定。3、本发明方法中,采用膜芯式反应器,其中的中空催化剂膜芯活性下降后,可以采用膜芯反应器轮换高温焙烧的再生方法,以恢复活性;在采用多个膜芯式反应器串联时,可以随时对各个反应器进行切入和切出,操作方便,也进一步的延长了反应器运转周期。附图说明图1为本发明的膜芯式反应器示意图;图2为本发明的中空催化剂膜芯示意图;图3为四个膜芯式反应器串联示意图;图4为五个中空催化剂膜芯并联的膜芯元件。具体实施方式下面结合实施例对本发明的技术方案作进一步详细说明,但本发明的保护范围不受以下实施例的限制。本发明中,wt%为质量分数。本发明中,中空催化剂膜芯的比表面积和孔性质(比如孔容、平均孔直径、孔分布)采用压汞分析方法测得。下面结合图1和图2对本发明的立式膜芯式反应器进行说明。所述的膜芯式反应器,包括反应器本体4、中空催化剂膜芯元件5、进料分布盘3、进料口1、出料口2、物料空间6,其中所述的中空催化剂膜芯元件5竖直设置于本体4内部,图2为图1中的中空催化剂膜芯元件5的示意图,中空催化剂膜芯元件5采用一个中空催化剂膜芯,中空催化剂膜芯为设置有中空通道7和膜层8的催化剂。其中,进料口1位于反应器本体4的下部,进料分布盘3设置在中空催化剂膜芯元件5之下,所述进料分布盘均布开口,所述开口与物料空间6相通,所述反应器本体4的上部设置有出料口2,所述的出料口2与中空催化剂膜芯的中空通道7相通。如图3,以采用四个膜芯式反应器串联为例,包括膜芯式反应器101、102、103、104,且相邻膜芯式反应器间设置气液分离器,还设有切分管路,用于各个反应器的切分和切入。例如,当膜芯式反应器101中催化剂活性不能满足应用要求时,通过控制切分管路及相应的阀门,将膜芯式反应器101切出,使进料直接进入到膜芯式反应器102中进行反应,膜芯式反应器101经过再生方法进行再生处理后,再通过控制相应的阀门的开闭来进行切入,使进料重新由膜芯式反应器101进入。每个膜芯式反应器采用1个中空催化剂膜芯元件,每个中空催化剂膜芯元件设有5个并联的中空催化剂膜芯,如图4,其中物料的流向是由中空催化剂膜芯外向中空通道扩散。本发明实施例采用的原料的性质见表1。表1原料的性质原料密度(20℃),g/cm30.998残炭,wt%24.6金属(v+ni)含量,μg/g760硫,wt%5.24氮,μg/g5320本发明实施例中,对每个膜芯反应器产物的残炭含量进行监测,以反应初始的脱残炭率为基础,切出脱残炭率降低5个百分点的膜芯式反应器,对其中的中空催化剂膜芯进行再生,再生后再切入继续进行反应。其中反应初始的脱残炭率为反应器每次重新进原料后反应稳定时(即反应器切入原料运转大约在200h时)测得的脱残炭率。实施例1原料(性质见表1)与氢气混合,进入膜芯式反应器进行加氢处理反应,所得的产物经分离得到的加氢重馏分油(沸点在350℃以上)的性质见表4。由表4可见,加氢重馏分油特别适宜作为船用燃料。所用膜芯式反应器如图3所示,即4个膜芯式反应器串联,相邻反应器间设置气液分离器,气液分离器出来的气体进入氢氧化钠碱液中吸收硫化氢,进入硫酸溶液中吸收氨气,提纯后的气体作为循环氢继续使用。每个膜芯式反应器内设置由5个中空催化剂膜芯并联组成一个膜芯元件如图4。每个中空催化剂膜芯为同心环状圆柱体,膜芯的外直径为430mm,高为1000mm,中空通道内直径为30mm。所用的每个中空催化剂膜芯a组成如下:加氢活性金属为mo和ni,以氧化物计,mo+ni为48wt%,mo:ni以氧化物计的重量之比为4:1,载体采用氧化铝,催化剂性质见表2。加氢处理的操作条件如下:液时体积空速为0.22h-1,氢油体积比为800:1,反应温度为385℃,反应压力为15.5mpa。该反应器正常运转一定天数后,沉积金属含量参见表3。实施例2将实施例1中所用的中空催化剂膜芯a替换为中空催化剂膜芯b,并对操作条件作了调整。所述中空催化剂膜芯b组成如下:加氢活性金属为mo和ni,以氧化物计,mo+ni为55wt%,mo:ni以氧化物计的重量之比为5:1,载体采用氧化铝,其它同中空催化剂膜芯a,催化剂性质见表2。加氢处理的操作条件如下:液时体积空速为0.24h-1,氢油体积比为800:1,反应温度为385℃,反应压力为15.0mpa。所得的产物经分离得到的加氢重馏分油(沸点在350℃以上)的性质见表4。由表4可见,加氢重馏分油特别适宜作为船用燃料。该反应器正常运转一定天数后,沉积金属含量参见表3。实施例3将实施例1中所用的中空催化剂膜芯a替换为中空催化剂膜芯c,并对操作条件作了调整。中空催化剂膜芯c组成如下:加氢活性金属为mo和ni,以氧化物计,mo+ni为60wt%,mo:ni以氧化物计的重量之比为4:1,载体采用氧化铝,其它同中空催化剂膜芯a,催化剂性质见表2。加氢处理的操作条件如下:液时体积空速为0.25h-1,氢油体积比为1000:1,反应温度为385℃,反应压力为14.5mpa。所得的产物经分离得到的加氢重馏分油(沸点在350℃以上)的性质见表4。由表4可见,加氢重馏分油特别适宜作为船用燃料。该反应器正常运转一定天数后,沉积金属含量参见表3。实施例4将实施例1中所用的中空催化剂膜芯a替换为中空催化剂膜芯d,并将中空催化剂膜芯d放置于由不锈钢网板制备成中空构件中以保护膜芯增加其强度。同时对操作条件作了调整。中空催化剂膜芯d组成如下:加氢活性金属为mo和ni,以氧化物计,mo+ni为40wt%,mo:ni以氧化物计的重量之比为4:1,载体采用氧化铝,其它同中空催化剂膜芯a,催化剂性质见表2。加氢处理的操作条件如下:液时体积空速为0.24h-1,氢油体积比为800:1,反应温度为385℃,反应压力为15.5mpa。所得的产物经分离得到的加氢重馏分油(沸点在350℃以上)的性质见表4。由表4可见,加氢重馏分油特别适宜作为船用燃料。该反应器正常运转一定天数后,沉积金属含量参见表3,所得加氢重馏分油的性质和收率见表4。表2本发明实施例所用中空催化剂膜芯的性质催化剂样品实施例1实施例2实施例3实施例4孔容,cm3/g0.720.630.650.70比表面积,m2/g102105106105平均孔直径,nm60514858孔分布,%10nm以下724610-30nm2320342830-100nm61655149100nm以上9131117体积密度,g/cm30.570.580.620.52侧压强度,n/mm27252824表3本发明实施例加氢处理催化剂的评价结果沉积金属含量*,wt%运转天数实施例163255实施例264260实施例358262实施例465263注:*沉积金属含量是废加氢处理催化剂中沉积的v和ni占废加氢处理催化剂的重量百分比,其中v和ni的量采用等离子发射光谱法测定(icp)的。表4加氢重馏分油的性质和收率收率,wt%硫,wt%v+ni,μg/g残炭,wt%原料-5.2476024.6实施例1680.45425.5实施例2690.42384.8实施例3690.39394.0实施例4680.41405.3综上,采用本发明的方法,能够将劣质重油全馏分转化为轻质燃料油和重质燃料油,且重质燃料油性质良好,运转周期长,这是其它工艺所不能实现的。需要说明的是,以上实施例仅用以举例说明本发明的技术方案,而非对本发明的技术方案进行限制;尽管参照前述实施例对本发明进行了详细的说明,本领域的技术人员应当理解:在不偏离权利要求及其等同形式限定的精神和范围下可对以上实施例在形式和细节上作出各种变化。当前第1页1 2 3