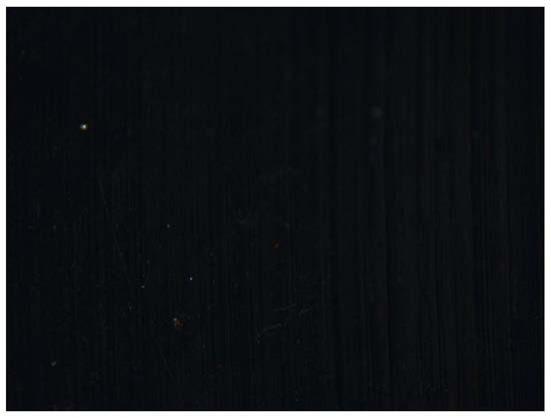
1.本发明涉及一种制备中间相沥青的方法,使用催化裂化油浆为原料通过两步法来制备中间相沥青,属于石油沥青领域。
背景技术:2.催化裂化油浆,是指原油在炼化过程中经过催化裂化装置后排出来的富含芳烃的废油浆,是催化裂化工艺的主要副产物,而催化裂化工艺是重质油轻质化主要的炼制过程之一。我国每年催化裂化装置生产出的副产物油浆可达到一千万吨以上。在石油化工行业,催化裂化油浆是一种重要的低附加值副产物,主要用作燃料油的调和组分或者直接作为重质燃料油来使用,这样限制了其使用范围,也没有带来较高的经济效益,造成了一定的资源浪费。因此探索和开发催化裂化油浆的新用途,加强其在石油化工行业的应用,是当前具有经济效益和社会效益的任务,目的是提高催化裂化油浆的附加值,实现原油价值最大化,从而实现我国石油化工行业的可持续发展目标。
3.目前,催化裂化油浆在石油化工行业的应用主要有以下几方面,作为软化剂对橡胶的软化有一定作用,可以改变塑料的可塑性,降低塑料粘度;可以作为沥青质量改善的溶剂,提高沥青的品质;通过复杂的过程生产出高质量的石油焦;还可以作为废油蒸馏过程中的活化剂;作为生产炭黑的原料等等。
4.中间相沥青是制备一系列优质碳材料的前驱体,其原料通常为煤焦油沥青和石油沥青。合成中间相沥青的传统方法包括直接热缩聚法,该方法虽然工艺简单但是对原料的要求较高,获得的产物的软化点相对较高;催化热缩聚法通过加入alcl3、超强酸、固体酸等催化剂合成软化点相对较低的中间相沥青,alcl3的缺点是很难与产物分离,对中间相沥青后续制备的碳材料性能有一定的影响,超强酸固体酸等具有很强的腐蚀性;共炭化法是将一种或多种共炭化添加剂加入到原料沥青中,添加剂一般包括有机和无机添加剂两大类,其中有机添加剂包含聚乙烯、聚苯乙烯等高分子颗粒;无机添加剂包含炭黑、石墨、石墨烯等,通过升温和保温的方式获得中间相沥青;卤素诱导法是通过卤素原子的引入打开芳烃侧链,使芳烃分子发生齐聚反应,从分子层面实现对反应的设计与调控。
5.众所周知,催化裂化油浆中含有大量的饱和烃以及饱和侧链官能团,这些饱和侧链需要在极高的温度下才能芳环化,而且成环后的芳烃分子(即石油沥青组分)具有较多侧链,不利于反应生成规整的高性能中间相沥青。所以如何获得侧链基团少,规整性好的石油沥青是制备优质石油基中间相沥青的关键。
技术实现要素:6.针对上述内容,本发明利用催化裂解油浆这种低附加值副产物作为原料,提出一种两步法来制备中间相沥青的方法,在原料催化裂化油浆中直接添加石墨烯,有助于改变催化裂化油浆聚合过程的分子量小、分子量分布宽、侧链多、分子结构不规整的问题,在获得高软化点、高规整性的石油沥青后进行第二步热缩聚反应,最终制备中间相沥青。
7.本发明所提供的制备中间相沥青的方法,是以催化裂化油浆作为原料,主要包括下述步骤:
8.步骤(1)以催化裂化油浆为原料,根据其分子结构特点分析,将一定量的石墨烯与催化裂化油浆混合,通过热缩聚反应制备出高软化点、分子量分布窄、高规整性的石油沥青;
9.步骤(2)将所得石油沥青通过直接热缩聚反应制备出高性能中间相沥青。
10.上述方法步骤(1)中采用的催化裂化油浆是一种重质油,含有20%~60%的饱和烃。
11.所述的石墨烯为不同含氧量(≤60%)的氧化石墨烯、还原氧化石墨烯,为单层石墨烯、双层石墨烯、少层石墨烯(<5层)或多层石墨烯(5
‑
10层)其中的一种或几种的组合,所述石墨稀尺寸为10~400nm,所述石墨烯添加剂占催化裂化油浆质量百分比为0.001wt%~2wt%。
12.所述热缩聚过程中始终保持氮气气氛,且以1~10℃/min的速率升温至100~300℃并强力搅拌(300~600rpm)20min以上,使石墨烯在油浆中分散均匀。然后再以2~10℃/min的速率从室温升至380~450℃,保温2~10h,压力为自升压,转速为100~600rpm,获得软化点为100~160℃、分子量分布为1.50~1.90、晶体层间距为0.3470~0.3499nm的石油沥青。
13.上述方法步骤(2)中将获得的石油沥青置于高温高压反应釜中,通入氮气置换空气后,以2℃~10℃/min的升温速率从室温升至350℃~450℃,然后保温3~30h,反应过程中压力为0.1~10mpa,搅拌速率为100~600rpm。
14.所述中间相沥青的软化点(260℃~330℃)较低,中间相含量不低于80%。
15.按照上述任一方法制备得到的中间相沥青均可用来制备导热率大于800w/(m
·
k)、模量大于400gpa的高导热或高模量的碳纤维,以及导热率大于80w/(m
·
k)的高导热泡沫炭。
16.本发明具有以下优点:
17.(1)采用催化裂化油浆为原料,在我国含量丰富,容易获得。
18.(2)本方法开发了催化裂化油浆制备中间相沥青的新方法,可以提高原料催化裂化油浆的附加值,带来更大的经济效益,减少资源的浪费。
19.(3)本方法制备中间相沥青,工艺过程比较简单,对设备要求相对较低,可以实现大规模工业化生产。
20.(4)本方法制备中间相沥青的过程中未采用难以去除的催化剂,制备过程不会产生有毒物质,比较安全环保。
21.(5)本方法采用石墨烯添加到催化裂化油浆中来制备石油沥青,在热缩聚过程中,利用石墨烯的片层结构提供平整的反应场所,通过分子间相互作用使得催化裂化油浆聚合成高软化点(分子量较高)、分子量分布窄、高规整性的石油沥青分子,使其更容易通过热缩聚反应来形成高品质的中间相沥青。
22.(6)本方法采用施加适当的压力和搅拌的方式来促进中间相的快速形成。
23.(7)本方法制备出的中间相沥青杂质含量少,软化点相对较低。
附图说明
24.为了更清楚的说明本实施例中的技术方案,下面将实施例描述中所使用的附图作简单的介绍,描述中的附图仅仅是本发明的一些实施例,对于本领域内的普通技术人员来讲,在不付出创造性劳动的前提下,还可以根据这些附图获得其他的附图。
25.图1为实施例1制备出的石油沥青的偏光图。
26.图2为实施例11制备出的中间相沥青产物的偏光图。
具体实施方式
27.为使本发明的目的、技术方案更加清楚,下面结合具体实施例,进一步阐述本发明,但不构成对本发明的限制。
28.利用所述方法制备出的中间相沥青来制备碳纤维的工艺是以5℃/min的升温速率升高到350℃条件下熔融纺丝、在230℃温度下进行不熔化处理、施加少量张力(20g砝码)进行碳化,碳化温度1000℃。制备泡沫炭的过程是将中间相沥青以5℃/min的升温速率升高到预发泡温度320℃保温2h,再以10℃/min的速率升至480℃保温2h,压力为恒压3mpa。将生料泡沫以10℃/min升到200℃再以5℃/min升高到300℃保温6h进行预氧化,再经过1000℃碳化,最后在3000℃条件下进行石墨化处理。
29.实施例1:
30.第一步将0.01g尺寸为30nm的少层还原氧化石墨烯组合(含氧量为1%)和400g催化裂化油浆加入到高温高压反应釜内,通入氮气吹扫置换空气后密闭,以5℃/min的速率升温至150℃并强力搅拌(500rpm)1h,使石墨烯在油浆中分散均匀。然后再以2℃/min的速率升至430℃,搅拌(300rpm)保温3h,反应过程中压力为自升压。当保温过程结束时,释放釜内压力,氮气吹扫30min去除轻组分,停止搅拌装置,使反应釜冷却至室温,获得300g石油沥青,其软化点为120℃,分子量分布为1.72,晶体层间距为0.3483nm。
31.第二步将上述300g石油沥青粉碎后再置于高温高压反应釜中,通入氮气吹扫置换空气后密闭,以3℃/min的速率升温,当温度高于180℃时开始搅拌,搅拌转速为400rpm,直至温度达到400℃时保温7h。反应过程中,保持反应釜内恒压2mpa,持续匀速搅拌。当保温过程结束时,释放釜内压力,氮气吹扫30min去除轻组分,停止搅拌装置,使反应釜冷却至室温,获得软化点为270℃的中间相沥青,中间相含量达93%。
32.使用该中间相沥青制备的泡沫炭热导率为100w/(m
·
k);碳纤维的模量为502gpa,热导率为970w/(m
·
k)。
33.实施例2
34.将还原氧化石墨烯添加量由0.01g提高到0.04g,其他条件同实施例1,获得的石油沥青软化点为135℃、分子量分布为1.70、晶体层间距为0.3481nm,最终制备出的中间相沥青的软化点为265℃,中间相含量为95%。使用该中间相沥青制备的泡沫炭热导率为106w/(m
·
k);碳纤维的模量为510gpa,热导率为983w/(m
·
k)。
35.实施例3
36.将还原氧化石墨烯添加量由0.01g提高到0.08g,其他条件同实施例1,获得的石油沥青软化点为142℃、分子量分布为1.66、晶体层间距为0.3479nm,最终制备出的中间相沥青的软化点为261℃,中间相含量为97%。使用该中间相沥青制备的泡沫炭热导率为115w/
(m
·
k);碳纤维的模量为550gpa,热导率为1008w/(m
·
k)。
37.实施例4
38.将还原氧化石墨烯的尺寸由30nm替换成50nm,其他条件同实施例1,获得的石油沥青软化点为127℃、分子量分布为1.68、晶体层间距为0.3480nm,最终制备出的中间相沥青的软化点为267℃,中间相含量为97%。使用该中间相沥青制备的泡沫炭热导率为108w/(m
·
k);碳纤维的模量为512gpa,热导率为1003w/(m
·
k)。
39.实施例5
40.将还原氧化石墨烯的尺寸由30nm替换成100nm,其他条件同实施例1,获得的石油沥青软化点为138℃、分子量分布为1.64、晶体层间距为0.3472nm,最终制备出的中间相沥青的软化点为262℃,中间相含量为99%。使用该中间相沥青制备的泡沫炭热导率为113w/(m
·
k);碳纤维的模量为579gpa,热导率为1125w/(m
·
k)。
41.实施例6
42.将还原氧化石墨烯(含氧量为1%)替换成氧化石墨烯(含氧量为60%),其他条件同实施例1,获得的石油沥青软化点为135℃、分子量分布为1.71、晶体层间距为0.3494nm,最终制备出的中间相沥青的软化点为292℃,中间相含量为97%。使用该中间相沥青制备的泡沫炭热导率为98w/(m
·
k);碳纤维的模量为469gpa,热导率为837w/(m
·
k)。
43.实施例7
44.将少层还原氧化石墨烯替换成多层还原氧化石墨烯,其他条件同实施例1,获得的石油沥青软化点为123℃、分子量分布为1.75,、晶体层间距为0.3484nm,最终制备出的中间相沥青的软化点为272℃,中间相含量为92%。使用该中间相沥青制备的泡沫炭热导率为99w/(m
·
k);碳纤维的模量为500gpa,热导率为966w/(m
·
k)。
45.实施例8
46.将少层还原氧化石墨烯(含氧量为1%)替换成少层还原氧化石墨烯(含氧量为4%),其他条件同实施例1,获得的石油沥青软化点为122℃、分子量分布为1.72,、晶体层间距为0.3483nm,最终制备出的中间相沥青的软化点为274℃,中间相含量为90%。使用该中间相沥青制备的泡沫炭热导率为97w/(m
·
k);碳纤维的模量为499gpa,热导率为967w/(m
·
k)。
47.实施例9
48.将第一步中150℃下的强力搅拌由500rpm降到300rpm,其他条件同实施例1,获得的石油沥青软化点为121℃、分子量分布为1.83、晶体层间距为0.3485nm,最终制备出的中间相沥青的软化点为275℃,中间相含量为90%。使用该中间相沥青制备的泡沫炭热导率为93w/(m
·
k);碳纤维的模量为470gpa,热导率为864w/(m
·
k)。
49.实施例10
50.将第一步保温温度由430℃升高到450℃,其他条件同实施例1,获得的石油沥青软化点为150℃、分子量分布为1.64、晶体层间距为0.3479nm,最终制备出的中间相沥青的软化点为273℃,中间相含量为98%。使用该中间相沥青制备的泡沫炭热导率为110w/(m
·
k);碳纤维的模量为528gpa,热导率为1137w/(m
·
k)。
51.实施例11
52.将第一步保温时间由3h增加到4h,其他条件同实施例3,获得的石油沥青软化点为
149℃、分子量分布为1.75、晶体层间距为0.3477nm,最终制备出的中间相沥青的软化点为289℃,中间相含量为99%。使用该中间相沥青制备的泡沫炭热导率为101w/(m
·
k);碳纤维的模量为517gpa,热导率为968w/(m
·
k)。
53.实施例12
54.将第一步保温时间由3h增加到5h,其他条件同实施例3,获得的石油沥青软化点为152℃、分子量分布为1.84、晶体层间距为0.3472nm,最终制备出的中间相沥青的软化点为293℃,中间相含量为98%。使用该中间相沥青制备的泡沫炭热导率为99w/(m
·
k);碳纤维的模量为511gpa,热导率为957w/(m
·
k)。
55.实施例13
56.将第二步保温温度由400℃提高到410℃,其他条件同实施例1,获得的石油沥青软化点为120℃、分子量分布为1.72、晶体层间距为0.3483nm,最终制备出的中间相沥青的软化点为276℃,中间相含量为95%。使用该中间相沥青制备的泡沫炭热导率为113w/(m
·
k);碳纤维的模量为546gpa,热导率为1169w/(m
·
k)。
57.实施例14
58.将第二步保温温度由400℃提高到430℃,其他条件同实施例1,获得的石油沥青软化点为120℃、分子量分布为1.72、晶体层间距为0.3483nm,最终制备出的中间相沥青的软化点为300℃,中间相含量为100%。使用该中间相沥青制备的泡沫炭热导率为87w/(m
·
k);碳纤维的模量为425gpa,热导率为752w/(m
·
k)。
59.实施例15
60.将第二步保温时间由7h增加到10h,其他条件同实施例1,获得的石油沥青软化点为120℃、分子量分布为1.72、晶体层间距为0.3483nm,最终制备出的中间相沥青的软化点为275℃,中间相含量为97%。使用该中间相沥青制备的泡沫炭热导率为116w/(m
·
k);碳纤维的模量为538gpa,热导率为1045w/(m
·
k)。
61.实施例16
62.将第二步保温时间由7h增加到15h,其他条件同实施例1,获得的石油沥青软化点为120℃、分子量分布为1.72、晶体层间距为0.3483nm,最终制备出的中间相沥青的软化点为288℃,中间相含量为99%。使用该中间相沥青制备的泡沫炭热导率为120w/(m
·
k);碳纤维的模量为541gpa,热导率为1132w/(m
·
k)。
63.实施例17
64.将第二步的搅拌转速由400rpm提高到500rpm,其他条件同实施例1,获得的石油沥青软化点为120℃、分子量分布为1.72、晶体层间距为0.3483nm,最终制备出的中间相沥青的软化点为265℃,中间相含量为98%。使用该中间相沥青制备的泡沫炭热导率为117w/(m
·
k);碳纤维的模量为539gpa,热导率为1012w/(m
·
k)。
65.实施例18
66.将第二步的反应压力由2mpa增加到3mpa,其他条件同实施例1,获得的石油沥青软化点为120℃、分子量分布为1.72、晶体层间距为0.3483nm,最终制备出的中间相沥青的软化点为267℃,中间相含量为94%。使用该中间相沥青制备的泡沫炭热导率为106w/(m
·
k);碳纤维的模量为526gpa,热导率为1004w/(m
·
k)。
67.以上已对本发明的较佳实施例进行了具体说明,但本发明并不限于所述实施例,
熟悉本领域的技术人员在不违背本发明精神的前提下还可作出种种的等同的变型或替换,这些等同的变型或替换均包含在本技术权利要求所限定的范围内。