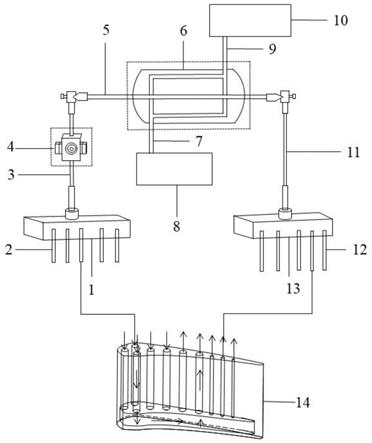
1.本申请涉及用于航空发动机涡轮导向器叶片,特别涉及一种用于航空发动机涡轮导向器叶片的高效冷却装置。
背景技术:2.航空发动机作为飞机的“心脏”,被誉为“工业皇冠上的明珠”,它的性能指标,直接影响着飞机的安全性、可靠性和经济性。在航空燃气涡轮发动机的发展中,为提高发动机的热效率和推重比,压气机的增压比和涡轮进口温度不断被提高。装配在第四代战斗机中推重比达到10一级的发动机,其压气机增压比已经达到30以上,涡轮前温也接近2000k。预计在2030年左右可能出现推重比超过20的战斗机发动机,与f119发动机相比,耗油率降低25%,全寿命期成本降低64%,能力/成本指数为11.5倍。面对如此高性能的标准,对涡轮叶片材料的耐热性和冷却技术就提出了更高的要求。
3.涡轮中导向器叶片,它的工作条件十分恶劣,被高温燃气包围,表面温度高且分布不均匀,在设计时必须综合考虑材料、结构、冷却方式。传统的冷却方式主要有气膜冷却、冲击冷却、发散冷却、肋壁强化换热、扰流柱强化换热等,上述冷却方式中的冷却工质选用来自压气机或燃烧室的空气,但是空气的散热能力有限是不争的事实。为了满足未来更高的推重比要求,需要寻求一种换热系数更高的流动工质,结合现有的技术,开发出一种新型高效的冷却装置。
技术实现要素:4.发明人为了解决上述问题,提出如下设想:将涡轮导向器叶片原有内部冷却通道中的流动工质换为低熔点的液态金属,并加上电磁泵用于驱动液态金属的流动,为了达到更为高效的冷却和综合利用热量,将采用换热器装置,用机载燃油为冷源来降低来自叶片内部冷却通道的液态金属,然后整体用管道连接,构成了循环装置。这样既可以降低叶片表面的温度,延长叶片的使用寿命,还可以将原有的冷气省下,提高发动机的热效率和做功能力,甚至使得航空煤油在燃烧室中燃烧更充分,达到理想的高效冷却、综合利用的目的。基于以上综合考虑,本申请提出一种用在航空发动机涡轮导向器叶片上能够带走大量热、利用热并高效冷却的循环装置。
5.本申请一种用于航空发动机涡轮导向器叶片的高效冷却装置,叶片内部布置多条冷却通道,以低熔点金属或其合金作为流动工质,内部每条冷却通道流经导向器叶片底部预留的腔室,所述多条冷却通道中的部分冷却通道为流入叶片冷却通道、其余部分的冷却通道为流出叶片冷却通道,所述高效冷却装置包括:
6.分流器,其内部开有流通通道,且流通通道内装有流动工质,所述分流器的一侧布置有多根分流器管道,多根分流器管道的数量、尺寸及形状与所述流入叶片冷却通道的数量、尺寸及形状相匹配,所述分流器通过所述多根分流器管道与所述导向器叶片内部的流入叶片冷却通道对应连接;
7.收集器,其内部开有流通通道,且流通通道内装有流动工质,所述收集器的一侧布置有多根收集器管道,多根收集器管道的数量与形状与所述流出叶片冷却通道的数量与形状相匹配,所述收集器通过所述多根收集器管道与所述导向器叶片内部的流出叶片冷却通道对应连接;
8.电磁泵,通过第一连接管道与所述分流器连通,用于驱动所述流动工质流动;和
9.换热器,通过第二连接管道和第五连接管道对应连通所述电磁泵和所述收集器,所述第二连接管道穿过所述换热器并与所述第五连接管道连通,用于对由所述导向器叶片中流出的带有热量的流动工质进行快速散热降温,换热器中还布有蛇形管道,一端通过第四连接管道连通油箱,由燃油泵通过燃油管输送航空煤油到换热器的蛇形管道中,另一端通过第三连接管道连通到燃烧室,将升温后的航空煤油输送到燃烧室,提高其燃烧效率;
10.在所述导向器叶片前缘和尾缘部分涂抹陶瓷涂层,防止局部温度过高而冷却通道数量不足带来的叶片表面受热不均,
11.其中,每一流动工质均为液态的低熔点金属或其合金,所述分流器、所述导向器叶片、所述收集器、所述换热器、所述电磁泵形成闭环回路,所述电磁泵驱动所述流动工质在闭环回路中流动。
12.可选地,所述分流器和所述收集器的截面形状为正方形、长方形、三角形或者圆形。
13.可选地,所述分流器和所述收集器由金属或耐高温合金材料制成。
14.可选地,所述换热器的截面形状为正方形、长方形、椭圆形。
15.可选地,所述换热器由高导热金属或者半导体硅材料制成。
16.可选地,所述换热器内部的蛇形管道的截面形状为正方形、长方形、三角形或圆形。
17.可选地,所述第一连接管道、所述第二连接管道、所述第三连接管道、所述第四连接管道和所述第五连接管道的截面形状为正方形、长方形、三角形或圆形。
18.可选地,所述第一连接管道、所述第二连接管道、所述第三连接管道、所述第四连接管道和所述第五连接管由金属或耐高温合金材料制成。
19.可选地,每一流动工质为在室温下可熔化的低熔点金属镓,或者是金属镓与以锡、铋或铟为基组成的合金。
20.可选地,所述导向器叶片中的每条冷却通道为带肋的冷却通道。
21.可选地,所述导向器叶片中的每条冷却通道的截面形状为正方形、长方形、三角形或圆形。
22.可选地,所述导向器叶片的内部前端的冷却通道为流入叶片冷却通道,所述导向器叶片的内部后端的冷却通道为流出叶片冷却通道,所述多条冷却通道通过所述腔室构成流动工质的逆时针闭合流动空间。
23.可选地,所述导向器叶片的腔室的尺寸稍大于所述导向器叶片的多条冷却通道的尺寸,以将流入叶片冷却通道和流出叶片冷却通道的流动工质汇集于此,形成逆时针闭合回路。
24.本申请的用于航空发动机涡轮导向器叶片高效冷却装置,不同于现行的冷却气体在导向器叶片外部流动的气膜冷却和在导向器叶片内部加扰流器强化换热、冲击冷却等方
式的传统冷却,本申请包括分流器、收集器、电磁泵和换热器,本申请与导向器叶片形成闭环回路,本申请采用液态的低熔点金属或其合金作为流动工质,通过电磁泵驱动流动工质在导向器叶片内部的多条冷却通道流通的冷却方式,充分利用金属或其合金所具有远高于非金属类材料热导率的特性,同时该流动工质可以在闭合回路中循环流动,然后通过与换热器中设有蛇形管道内的航空煤油进行热交换,快速带走导向器叶片中大量热,并将热量传递给航空煤油,这样既能达到高效冷却导向器叶片的效果,还能对航空煤油进行预热,增加燃烧效率,从而提高冷却工质的品质。本申请没有采用空气冷却,故节省下原有从压气机引出的冷却空气,增加飞机的推进动力,减少因冷热空气掺混带来的不稳定性;本申请的冷却效果远优于传统的空气冷却方式,传热效率高,导向器叶片温降更大,利于延长导向器叶片的使用寿命;本申请的导向器叶片外表面无需开设气膜孔,内部无复杂结构,提高叶片的强度,降低加工工艺成本;本申请的换热器采用液态金属
‑
航空煤油换热器,带走热量的能力远优于单靠空气的翅片散热,带走叶片的热量也没有直接排放到大气中,而是传递给航空煤油,对其提前预热,提高它的燃烧效率;本申请整个过程循环封闭,低熔点金属或其合金重复循环利用,对环境无影响。
25.根据下文结合附图对本申请的具体实施例的详细描述,本领域技术人员将会更加明了本申请的上述以及其他目的、优点和特征。
附图说明
26.后文将参照附图以示例性而非限制性的方式详细描述本申请的一些具体实施例。附图中相同的附图标记标示了相同或类似的部件或部分。本领域技术人员应该理解,这些附图未必是按比例绘制的。附图中:
27.图1是根据本申请一个实施例的航空发动机涡轮导向器叶片的高效冷却装置的示意性逻辑控制图;
28.图2是航空发动机涡轮导向器叶片的高效冷却装置的示意性结构图;
29.图3是导向器叶片的示意性透视图。
30.图中各符号表示含义如下:
31.1分流器,2分流器管道,3第一连接管道,4电磁泵,5第二连接管道,6换热器,7第三连接管道,8燃烧室,9第四连接管道,10油箱,11第五连接管道,12收集器管道,13收集器,14导向器叶片,15流入叶片冷却通道,16流出叶片冷却通道,17腔室。
具体实施方式
32.图1是根据本申请一个实施例的航空发动机涡轮导向器叶片的高效冷却装置的示意性逻辑控制图。图2是航空发动机涡轮导向器叶片的高效冷却装置的示意性结构图。图3是导向器叶片的示意性透视图。
33.如图3所示,本实施例中,导向器叶片14中根据叶型布置多条冷却通道。导向器叶片14内的底部位置处预留有腔室17。每条冷却通道均与所述腔室17连通。所述多条冷却通道中的部分冷却通道为流入叶片冷却通道15,所述多条冷却通道中其余部分的冷却通道为流出叶片冷却通道16。如图1所示,还可参见图2
‑
3,本实施例提供了一种以低熔点金属或其合金作为流动工质的航空发动机涡轮导向器叶片的高效冷却装置,一般性可以包括分流器
1、收集器13、换热器6和电磁泵4。分流器1的内部开有流通通道,且流通通道内装有流动工质。所述分流器1的一侧布置有多根分流器管道2。每根分流器管道2与分流器1的流通通道连通。多根分流器管道2的数量、尺寸及形状与所述流入叶片冷却通道15的数量、尺寸及形状相匹配。所述分流器1通过所述多根分流器管道2与所述导向器叶片14内部的流入叶片冷却通道15对应连接。收集器13的内部开有流通通道,且流通通道内装有流动工质。所述收集器13的一侧布置有多根收集器管道12。每根收集器管道12与收集器13的流通通道连通。多根收集器管道12的数量与形状与所述流出叶片冷却通道16的数量、尺寸与形状相匹配。所述收集器13通过所述多根收集器管道12与所述导向器叶片14内部的流出叶片冷却通道16对应连接。电磁泵4通过第一连接管道3与所述分流器1连通,主要用于驱动整个装置中冷却工质流动。换热器6通过第二连接管道5和第五连接管道11对应连通所述电磁泵4和所述收集器9。所述第二连接管道5穿过所述换热器6并与所述第五连接管道11连通。换热器6主要用于对由所述导向器叶片14中流出的带有热量的流动工质与来自油箱10内通过所述第四连接管道9流进的航空煤油进行热交换,以达到快速换热降温的效果,此时外涵道的空气对其也起到一定的散热作用;携带有热量的航空煤油通过所述第三连接管道7流到燃烧室8中,完成后续燃烧,冷却后的流动工质通过所述第五连接管11,流经收集器13再次进入导向器叶片14,开始下一周期流动。其中,每一流动工质即分流器1与收集器13中的流动工质均为液态的低熔点金属或其合金。流动工质经所述分流器1、所述导向器叶片14、所述收集器13、所述换热器6、所述电磁泵4回到所述分流器1,从而形成闭环回路,所述电磁泵4驱动所述流动工质在闭环回路中流动。
34.具体实施时,电磁泵4安装在第二连接管道5上,以便驱动第二连接管道5内以低熔点金属或者其合金为流动工质的流动。电磁泵4主要用于驱动低熔点金属或其合金工质在整个闭环回路的流动,形状未定,只需满足体积尽可能小,适合安装在外涵道的空间中。第二连接管道5制作时形状未定,尺寸大小一段与电磁泵4端口匹配即可,之后第二连接管道5的另一端与换热器6连接。根据需要,第二连接管道5及第一连接管道3的长度可以按照外涵道空间进行调整,在满足需求的情况下尽可能短,减轻整体重量。
35.具体实施时,换热器6安装在第二连接管道5上,以便以低熔点金属或者其合金为流动工质实现更高效的温降,实现下一步的回流循环。制作时,可通过机加工其他方式两端做成与第二连接管道5、第五连接管道11的管径相同的接口,以便与第二连接管道5、第五连接管道11连接,上下两端口也需要和第三连接管道7、第四连接管道9配套连接。换热器6的形状未定,外部由大量翅片组包裹,内部设置蛇形管道,上面一端通过第四连接管道9将来自油箱10的航空煤油输送到蛇形管道中,下面一段通过第三连接管道7将携带有热量的航空煤油输送到燃烧室8中,第三连接管道7、第四连接管道9长度需要满足管道输送的要求,翅片所用材质为常规材料。使用时,通过外涵道的冷气经过于此,翅片与空气发生对流换热,带走部分热量,而流经此处第二连接管道5内的低熔点金属或合金中的绝大部分热量通过与蛇形管道中低温的航空煤油交换热量,进而实现高效冷却作用,随后流到下一个装置中。根据需要,第二连接管道5及第五连接管道11的长度可以按照外涵道空间进行调整,在满足需求的情况下尽可能短。
36.本申请的工作过程:
37.如图2所示,在实际启动时,以低温的低熔点金属或其合金作为流动工质,该流动
工质从分流器1内的流通通道经过分流器管道2流入导向器叶片14的流入叶片冷却通道15,低温的低熔点金属或其合金迅速将高温的导向器叶片14的热量转移到并携带,随后汇集在导向器叶片14底部预留的腔室17内,之后从导向器叶片14的流出叶片冷却通道16流出导向器叶片14,通过多根收集器管道12进入收集器13。再通过第五连接管道11、第二连接管道5到达换热器6,低熔点金属或其合金的热量小部分通过换热器6的翅片被外涵道的空气带走,大部分热量由来自油箱10的航空煤油流经第四连接管道9在换热器内部的蛇形管道带走,被降温的低熔点金属或其合金继续流经电磁泵4、从第一连接管道3中到达分流器1,构成整个闭合循环回路,准备进入下一个循环,周而复始。这种方法对导向器叶片14冷却的效果很好,低熔点金属或其合金的引入相当于将导向器叶片14的热量直接转移到航空煤油中,不仅对导向器叶片14的冷却效果明显,同时航空煤油也在预热中燃烧充分,因此提高了以低熔点金属或其合金作为流动工质的冷却品质,达到高效冷却的作用。
38.本申请的工作原理:
39.本申请提供的航空发动机涡轮导向器叶片的高效冷却装置在流动工质上的选择与传统冷却装置有着实质性差别,即它首次采用以低熔点金属或其合金作为冷却导向器叶片14的流动工质(至今国内外文献和专利均无相同方法的报道)。当涡轮导向器叶片冷却装置与叶片连接时,由于低熔点金属或其合金具有远高于非金属流体的热导率和扩散率,因而传热是高效而快速的,其流动可致使快速将所吸收的热量通过流动传输走。于此同时,所有流经导向器叶片14内部的多条冷却通道的低熔点金属或其合金汇流于收集器12中,通过收集器12的流通通道经过第五连接管道11到达换热器6,换热器6因为其外部翅片的结构、内部蛇形管道通有来自油箱10的低温航空煤油,进而使得携带有大量热的低熔点金属或其合金在外涵道空间的空气和内部蛇形管道的低温航空煤油双重换热作用下,热量被空气耗散并大多数被携带转移到航空煤油中。总之,低熔点金属或其合金流动工质极高的换热系数可以保证将导向器叶片14本身的热量传递出去,而相比较以往的空气冷却或者用其他液体如水等非低熔点金属,则会出现温降效果不明显,高温下工质不稳定等问题,所以低熔点金属或其合金流动工质的引入使得低熔点金属或其合金为流动工质的换热方式将导向器叶片14热量带走高效而可行。此外,换热器6进一步加强与外涵道空气及蛇形管道中航空煤油的热量交换,大大增强了冷却效率;而电磁泵4的存在,可在流通通道中造成一定的压差,在压差作用下,实现低熔点金属或其合金作为流动工质在整个闭合回路中循环流动,经过一次循环后的低熔点金属或其合金流动工质将来自携带叶片内部热量释放给外涵道空气及航空煤油后,又成为低温的流动工质,从而继续新的热量输运,形成周而复始的流动。
40.综上,本申请的航空发动机涡轮导向器叶片的高效冷却装置,不同于现行的冷却气体在叶片外部流动的气膜冷却和在叶片内部加扰流器强化换热、冲击冷却等方式的传统冷却,本申请包括分流器1、收集器13、换热器6和电磁泵4,本申请与导向器叶片14形成闭环回路,本申请采用液态的低熔点金属或其合金作为流动工质,通过电磁泵4驱动流动工质在导向器叶片14内部的多条冷却通道流通的冷却方式,充分利用金属或其合金所具有远高于非金属类材料热导率的特性,同时该工质可以在闭合回路中循环流动,通过换热器6快速带走导向器叶片14中大量热的能力,达到高效冷却导向器叶片14的效果。本申请没有采用空气冷却,故节省下原有从压气机引出的冷却空气,增加飞机的推进动力,减少因冷热空气掺混带来的不稳定性;本申请的冷却效果远优于传统的空气冷却方式,传热效率高,导向器叶
片温降更大,利于延长导向器叶片的使用寿命;本申请的导向器叶片14外表面无需开设气膜孔,内部无复杂结构,提高叶片的强度,降低加工工艺成本;本申请的所述装置换热器6采用液态金属
‑
航空煤油换热器,带走热量的能力远优于单靠空气的翅片散热,带走叶片的热量也没有直接排放到大气中,而是传递给航空煤油,对其提前预热,提高它的燃烧效率;本申请整个过程循环封闭,低熔点金属或其合金重复循环利用,对环境无影响。
41.如图2所示,具体地,所述分流器1和所述收集器13的外部形状多样化,截面形状可为正方形、长方形、三角形或者圆形。更具体地,分流器1、收集器13主要用途是分配进入导向器叶片14内部流入叶片冷却通道15的流动工质以及收集来自导向器叶片14内部流出叶片冷却通道16的流动工质,再次经过换热器6和电磁泵4后构成闭合回路,准备下一次循环流动,原则上现行所有的流通通道均可作为其结构。流通通道的结构形式可根据需要加以制备,并可实现多种形式组合。整套装置的形式最好为环状,以适应外涵道的空间结构。
42.如图2所示,具体地,所述分流器1和所述收集器13由金属或耐高温合金材料制成。
43.如图2所示,具体地,所述第一连接管道3、所述第二连接管道5、所述第三连接管道7、所述第四连接管道9和所述第五连接管道11的截面形状可为正方形、长方形、三角形或圆形。
44.如图2所示,具体地,所述第一连接管道3、所述第二连接管道5、所述第三连接管道7、所述第四连接管道9和所述第五连接管道11由金属或耐高温合金材料制成。
45.如图2所示,具体地,所述换热器6的截面形状为正方形、长方形、椭圆形。
46.如图2所示,具体地,所述换热器6由高导热金属或者半导体硅材料制成。
47.如图2所示,具体地,所述换热器6内部的蛇形管道的截面形状为正方形、长方形、三角形或圆形。
48.更具体地,如图3所示,所述导向器叶片14中的每条冷却通道为带肋的冷却通道。
49.进一步地,所述导向器叶片14中的每条冷却通道的截面形状可为正方形、长方形、三角形或圆形。
50.更具体地,所述导向器叶片14的内部前端的冷却通道为流入叶片冷却通道15,所述导向器叶片14的内部后端的冷却通道为流出叶片冷却通道16,所述多条冷却通道通过所述腔室17构成流动工质的逆时针闭合流动空间。
51.更具体地,所述的导向器叶片14内底部预留的腔室17形状不做限定,所述导向器叶片14的腔室17的尺寸稍大于所述导向器叶片14的多条冷却通道的尺寸,以将流入叶片冷却通道15和流出叶片冷却通道16的流动工质汇集于此,形成逆时针闭合回路。具体是指腔室17的上表面积是要大于多条冷却通道的截面所形成的外表面积,腔室17的外表面圆弧与导向器叶片14的形状呈比例缩小,但腔室14的外表面圆弧的最小缩小弧长特别是前缘位置得略大于前三条冷却通道的外切圆。
52.更具体地,所述导向器叶片14前缘和尾缘部分涂抹陶瓷涂层,防止局部温度过高而冷却通道数量不足带来的叶片表面受热不均。(涂层太薄,图例未显示)。
53.为了达到高效冷却,一般用作本申请的低熔点金属或其合金流动工质应满足如下要求:低熔点,在应用范围25℃~2000℃仍然保持液态,以减少或避免启动时的熔化过程;高沸点,高温下不蒸发,维持液态,以避免产生气液两相,易于流体管理;高导热率,以增强换热、降低热阻、减小热梯度;热容大,以提高传热能力,降低泵流量需求;高导电性,以提高
电磁泵的效率;无毒,对所接触材料腐蚀小、没有化学作用,在高温下化学反应缓慢,整体安全性高;便于获取;该低熔点金属或其合金流动工质应与结构材料相容,低熔点金属或其合金流动工质应不能造成对冷却装置部件产生腐蚀和锈化等影响使用寿命的不利因素。比如,同样作为液体金属的钠,即使其熔点97.82℃,钾的熔点为63.2℃,它们均不适合于导向器叶片冷却用,主要因为钠和钾极易与水发生化学反应,金属活性太强;另外,再比如,水银的熔点虽然很低,为
‑
38.87℃,但因有毒性,也不宜考虑作为本申请的工质。
54.具体地,如图2所示,每一流动工质即在分流器1、收集器13及第一连接管道3、第二连接管道5、第五连接管道11内流动的流动工质为在室温下可熔化的低熔点纯金属镓、铟,或者是金属镓与以锡、铟为基组成的合金。如液态金属ga
68
in
20
sn
12
从10.7℃~2200℃皆保持液态,具有较宽泛的单相温区。导热方面,液态金属的导热系数很高,是水的65倍,空气的1600倍,使其具有很好的换热能力。流动性方面,液态金属的粘性系数和水在一个量级,大约是水的2倍,因此也具有较好的流动能力。比热容方面,尽管水的质量比热容远大于液态金属,但是液态金属密度较大,因此液态金属的体积热容也与水在一个量级,约为水的1/2。此外液态金属的最大特点是其拥有很高的电导率,其电导率仅仅比常用高导电材料铜低一个量级,因此可以将其考虑作为本申请的工质。
55.本申请的关键之处在于引入了低熔点金属或其合金作为传输热量的流动工质,即在导向器叶片14内部的多条冷却通道及及第一连接管道3、第二连接管道5、第五连接管道11内流动的流动工质并非常规所用的水或者其他液体,而是在很大温度范围都可以保持液体状态的金属如镓或其合金ga
68
in
20
sn
12
等,由于低熔点金属具有远高于非金属的热导率和热扩散率,且具有流动性,因而可以快速而高效的运输热量,这相对于以往使用气体或者非金属液体作为流动工质的做法是一个革新。目前,尽管很多金属如汞等的熔点均比较低,但是考虑安全性和稳定性,比较合适的低熔点纯金属为镓,镓是柔软的银白色金属,它在大气环境下的熔点很低,仅为29.77℃,在熔点时的导热系数为29.4w/(m
·
℃),远高于空气和水;液态镓的绝对粘度在52.9℃时为1.89g/(m
·
s),在301℃时为1.03g/(m
·
s);在32.38℃时的液态镓密度为6.093g/cm3;这些热特性表明将镓作为导向器叶片高效冷却装置的流动介质是十分合适的。在常温下,镓在空气中是稳定的,当温度在260℃以上时,干燥的氧可使镓金属氧化,但生成的氧化膜可防止它继续氧化;值得指出的是,镓可与许多金属如铋、锡、铟等生成熔点低的合金,例如,含锡8%的镓合金熔点为20℃,含铟25%镓合金在l6℃时即熔化。进一步地,采用多元混合物,还可获得熔点更广泛的金属流体,比如62.5%ga,21.5%in,16%sn的熔点为10.7℃,而三元低共熔混合物:69.8%ga,17.6%in,12.6%sn的熔点为10.8℃。而其合金如ga、in、sn三种金属构成的合金熔点更低,gain
25
sn
13
低至5℃,同样可以作为冷却介质,甚至性能表现更优。它们均可作为本申请的工作介质。上述表明,低熔点金属或其合金换热能力远大于传统的甲醇、水等导热剂,是新一带的理想传热介质。只要在连接管道中设置一个电磁泵4,即可驱动导向器叶片14内部流入叶片冷却通道15、流出叶片冷却通道16及第一连接管道3、第二连接管道5及第三连接管道11内的低熔点金属或其合金流动;另外,为了使得从导向器叶片14中携带热量的低熔点金属或其合金快速散热进行下次循环,在第二连接管道5中还设置换热器6,因为其外部翅片的结构、内部蛇形管道通有来自油箱10的低温航空煤油,进而使得携带有大量热的低熔点金属或其合金在外涵道空间的空气和内部蛇形管道的低温航空煤油双重换热作用下,热量被空气耗散并多数被携带转移到
航空煤油中,最终达到高效冷却作用。而且,即使低熔点金属或其合金停止流动,利用低熔点金属或其合金高的导热率,将热量从导向器叶片14传递到换热器6部位,也能够充分实现换热的功能,从而降低导向器叶片14本身的温度,延长其使用寿命。
56.目前,面对航空燃气涡轮发动机年增20℃涡轮进口温度相比,每年提高8℃导向器叶片14材料的耐热性能仍不能满足燃气初温提高的要求,原有的空气冷却方式终将达到发展瓶颈,导向器叶片14冷却方式的改变迫在眉睫。本申请提供的以低熔点金属或其合金作为流动工质以及结合电磁泵4和换热器6为一体的循环回路装置是一种概念新颖的技术,能够快速带走导向器叶片14的大量热,使导向器叶片14维持一个正常的工作温度,同时给燃烧室8中航空煤油提前预热,提高航空煤油的燃烧效率,是高效冷却导向器叶片10的突破口,是提高其冷却品质的技术。
57.需要注意的是,除非另有说明,本申请使用的技术术语或者科学术语应当为本申请所属领域技术人员所理解的通常意义。
58.在本申请的描述中,需要理解的是,术语“中心”、“纵向”、“横向”、“长度”、“宽度”、“厚度”、“上”、“下”、“前”、“后”、“左”、“右”、“竖直”、“水平”、“顶”、“底”“内”、“外”、“顺时针”、“逆时针”、“轴向”、“径向”、“周向”等指示的方位或位置关系为基于附图所示的方位或位置关系,仅是为了便于描述本申请和简化描述,而不是指示或暗示所指的装置或元件必须具有特定的方位、以特定的方位构造和操作,因此不能理解为对本申请的限制。
59.此外,术语“第一”、“第二”等仅用于描述目的,而不能理解为指示或暗示相对重要性或者隐含指明所指示的技术特征的数量。在本申请的描述中,“多个”的含义是两个以上,除非另有明确具体的限定。
60.在本申请中,除非另有明确的规定和限定,术语“安装”、“相连”、“连接”、“固定”等术语应做广义理解,例如,可以是固定连接,也可以是可拆卸连接,或成一体;可以是机械连接,也可以是电连接;可以是直接相连,也可以通过中间媒介间接相连,可以是两个元件内部的连通或两个元件的相互作用关系。对于本领域的普通技术人员而言,可以根据具体情况理解上述术语在本申请中的具体含义。
61.在本申请中,除非另有明确的规定和限定,第一特征在第二特征“上”或“下”可以是第一和第二特征直接接触,或第一和第二特征通过中间媒介间接接触。而且,第一特征在第二特征“之上”、“上方”和“上面”可是第一特征在第二特征正上方或斜上方,或仅仅表示第一特征水平高度高于第二特征。第一特征在第二特征“之下”、“下方”和“下面”可以是第一特征在第二特征正下方或斜下方,或仅仅表示第一特征水平高度小于第二特征。
62.以上所述,仅为本申请较佳的具体实施方式,但本申请的保护范围并不局限于此,任何熟悉本技术领域的技术人员在本申请揭露的技术范围内,可轻易想到的变化或替换,都应涵盖在本申请的保护范围之内。因此,本申请的保护范围应该以权利要求的保护范围为准。