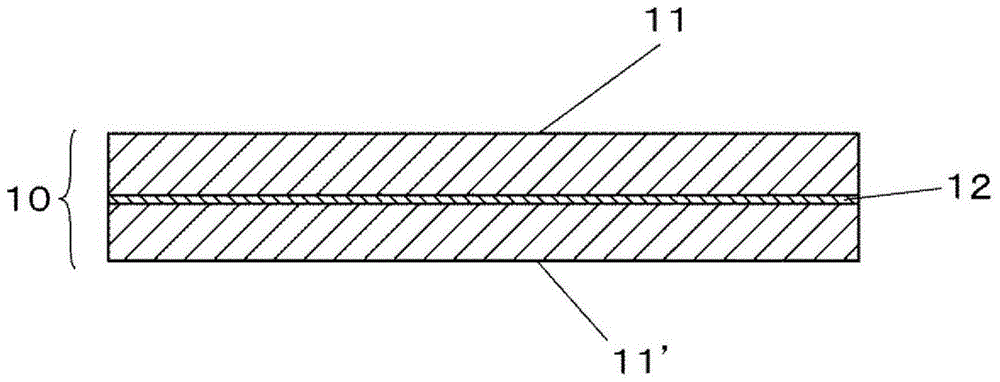
本发明涉及一种镀铝膜及用于制备镀铝膜的方法。本申请要求享有基于在2017年5月16日提交的日本专利申请第2017-097138号的优先权,其全部内容通过引用并入本文。
背景技术:
:专利文献1公开了一种由绝缘材料形成的多孔板,该多孔板设置在衬底和阳极之间。沿着衬底移动的方向对专利文献1中所描述的多孔板的开孔率进行调整,使电流密度均匀地分布于衬底的移动方向上。因此,可以形成厚度均匀的镀铝膜。专利文献2公开了一种镀铝膜,该镀铝膜是通过使用一种连续电处理装置在衬底上形成的。所述连续电处理装置包括电镀槽、导辊和供电辊,其中电镀槽具有腔室结构,腔室中有一个上储槽和一个下储槽,两个储槽通过位于两者之间的两个通道相互连接,导辊设置于下储槽,供电辊设置于电镀槽外、上储槽之上。根据专利文献2中所描述的连续电处理装置,通过使衬底在供电辊和导辊之间多次往复移动可在衬底表面形成多层镀铝膜。引用列表专利文献专利文献1:日本未经审查的专利申请公开第10-317195号专利文献2:日本未经审查的专利申请公开第11-117089号技术实现要素:本公开的镀铝膜是一种包含铝作为主要成分的镀铝膜,所述镀铝膜具有位于所述镀铝膜厚度方向上的两端的涂层表面之间的中间层,所述中间层包含具有比铝低的离子化倾向的金属,或者所述中间层包含铝和具有比铝低的离子化倾向的金属的合金。本公开的用于制备镀铝膜的方法为用于制备本公开所述的镀铝膜的方法,所述方法包括如下步骤:第一电解处理步骤:通过在第一电解液中使衬底经历电解处理以在所述衬底的表面电沉积铝来形成预镀铝膜,所述衬底的至少一个表面是导电的;置换步骤:在第一电解处理步骤之后,通过将所述预镀铝膜浸入包含所述第一电解液和具有比铝低的离子化倾向的金属的置换溶液中,以使用所述具有比铝低的离子化倾向的金属置换所述预镀铝膜的表面来形成置换镀膜;第二电解处理步骤:在置换步骤之后,通过在第二电解液中使所述置换镀膜经历电解处理以在所述置换镀膜的表面上电沉积铝来形成镀铝膜。所述第一电解液和所述第二电解液各自为包含至少氯化铝的熔盐。附图说明图1为示意地示出根据本公开的一个实施方式的镀铝膜的实例的截面的放大图。图2为示意地示出根据本公开的一个实施方式的镀铝膜的另一实例的截面的放大图。图3为示意性地示出根据本公开的一个实施方式的镀铝膜的另一实例的部分截面的放大图。图4为示意性地示出沿着图3中的a-a线截取的截面放大图。图5为包含具有三维网络结构的骨架的树脂成型体的实例的聚氨酯发泡树脂的照片。图6为示意性地示出在包含具有三维网络结构的骨架的树脂成型体的骨架的表面上形成导电层的状态的实例的部分截面放大图。图7为显示在实施例3中所制备的3号镀铝膜的截面的扫描电子显微镜观察的结果的照片。图8为显示在实施例4中制备的4号镀铝膜的截面的扫描电子显微镜观察的结果的照片。图9为在对比例2中制备的7号镀铝膜的截面的扫描电子显微镜观察的结果的照片。附图标记列表10-镀铝膜11-涂层表面11’-涂层表面12-中间层20-镀铝膜21-涂层表面21’-涂层表面22-中间层30-镀铝膜31-涂层表面31’-涂层表面32-中间层33-骨架34-骨架的内部35-孔65-孔66-树脂成型体67-导电层71-涂层表面71’-涂层表面72-中间层81-涂层表面81’-涂层表面82-中间层具体实施方式【本公开所要解决的问题】熔盐浴被用于实施电镀铝。但由于熔盐浴具有低导电性,所以在高速下无法形成镀铝膜。尤其是,在细长的衬底的情况下,如钢带,除非降低传输速度,否则在电镀浴中无法形成具有足够厚度的镀铝膜。根据专利文献1中所描述的方法,可以使得镀铝膜的厚度均一。但是,在镀铝膜厚度增加的情况下,除了降低传输速度外别无他法,这样会导致生产效率下降。当衬底是片状时如钢带,无法使用专利文献2中所描述的连续电处理装置进行处理。在专利文献2中所描述的连续电处理装置中,由于衬底是线材,所以衬底可以在供电辊和导辊之间多次往复移动。在衬底是片状的情况下,所述衬底不能在供电辊和导辊之间多次往复移动的。此外,在电镀浴中与导辊接触的衬底的部分表面上没有电沉积铝,而因此,所得的镀铝膜的厚度不均匀。鉴于此,本发明的发明人已经验证了如下过程:为了高效率地形成厚度大的镀铝膜,在水平方向传输衬底时使用多个被构造以形成镀铝膜的电镀装置以多阶段形成镀铝膜,从而提高传输速度。但是,发现如下情况。由于铝是一种很容易被氧化的金属,当将衬底从熔盐浴中被拉起时,形成了氧化物膜。因此,当以多阶段进行镀铝时,在各自的电镀装置中形成的镀铝膜之间就会插入类似年轮的氧化物膜。即使在氮气氛围(n2:99.99%以上)或氩气氛围(ar:99.99%以上)中进行熔盐镀铝,镀铝膜的表面也会由于所述氛围中含有的非常少量的氧气而形成氧化物膜。还发现,由于镀铝膜表面所形成的氧化物膜非常致密和牢固,并且电流不能被允许均匀地传输,以多阶段形成的镀铝膜之间的附着力差,可能会导致起泡等缺陷。因此,本公开的目的在于提供一种厚度大且能够在短时间内以低成本地制备的镀铝膜,以及用于制备所述镀铝膜的方法。[本发明的有益效果]根据本公开,可以提供一种厚度大且能够在短时间内以低成本地制备的镀铝膜,以及用于制备所述镀铝膜的方法。[本发明的实施例描述]首先,将列举并描述本公开的实施方式。(1)根据本公开的一个实施方式的镀铝膜为包含铝作为主要成分的镀铝膜。所述镀铝膜具有位于所述镀铝膜厚度方向上的两端的涂层表面之间的中间层,所述中间层包含具有比铝低的离子化倾向的金属,或者所述中间层包含铝和具有比铝低的离子化倾向的金属的合金。根据上述(1)的本发明的实施方式,可以提供了一种厚度大且能够在短时间内、低成本地制备的镀铝膜。(2)在根据上述(1)所述的镀铝膜中,所述镀铝膜优选具有细长片状的形状。根据上述(2)的本发明的实施方式,可以提供一种厚度大且能够在短时间内、低成本地在具有细长片状的形状的衬底的表面上制备的镀铝膜。(3)在根据上述(1)所述的镀铝膜中,所述镀铝膜优选形成金属多孔体的骨架,所述骨架具有三维网络结构。根据上述(3)的本发明的实施方式,可以提供一种形成多孔体的骨架的镀铝膜,所述骨架厚度大并且能够在短时间内、低成本地制备。(4)在根据上述(3)所述的镀铝膜中,所述金属多孔体优选具有细长片状的形状。根据上述(4)的本发明的实施方式,可以提供一种镀铝膜,该镀铝膜形成作为整体的具有细长片状形状的金属多孔体的骨架,所述镀铝膜厚度大并且能够在短时间内、低成本地制备。(5)在根据上述(1)至(4)中的任一项所述的镀铝膜中,所述镀铝膜优选具有在所述镀铝膜的厚度方向上的多层中间层。根据上述(5)的本发明的实施方式,可以提供了一种厚度大并且能够在短时间内、低成本地制备的镀铝膜。(6)在根据上述(1)至(5)中的任一项所述的镀铝膜中,所述具有比铝低的离子化倾向的金属优选为选自由铁(fe)、锌(zn)、锆(zr)、锰(mn)、镍(ni)和铜(cu)组成的组中的至少一种。根据上述(6)的本发明的实施方式,可以提供一种具有足够高的电导率的镀铝膜。(7)在根据上述(1)至(6)中的任一项所述的镀铝膜中,所述镀铝膜优选具有10μm以上且1000μm以下的厚度。根据上述(7)的本发明的实施方式,可以提供一种具有更大的厚度且能够在短时间内、低成本地制备的镀铝膜。(8)根据本公开的实施方式的用于制备镀铝膜的方法为用于制备根据上述(1)所述的镀铝膜的方法,所述方法包括如下步骤:第一电解处理步骤:通过在第一电解液中使衬底经历电解处理以在所述衬底的表面上电沉积铝来形成预镀铝膜,所述衬底的至少一个表面是导电的;置换步骤:在第一电解处理步骤之后,通过使所述预镀铝膜浸入包含所述第一电解液和具有比铝低的离子化倾向的金属的置换溶液中,以使用所述具有比铝低的离子化倾向的金属置换所述预镀铝膜的表面来形成置换镀膜;第二电解处理步骤:在置换步骤之后,通过在第二电解液中使所述置换镀膜经历电解处理以在所述置换镀膜的表面上电沉积铝来形成镀铝膜。所述第一电解液和所述第二电解液各自为包含至少氯化铝的熔盐。根据上述(8)的本发明的实施方式中,可以提供一种用于制备镀铝膜的方法,所述方法能够在短时间内、低成本地制备厚度大的镀铝膜。(9)根据上述(8)所述的用于制备镀铝膜的方法,所述衬底优选为包含具有三维网络结构的骨架的树脂成型体。根据上述(9)的本发明的实施方式,可以提供一种厚度大且能够在短时间内、低成本地在包含具有三维网络结构的骨架的衬底的表面上制备的镀铝膜的制备方法。(10)根据上述(8)或(9)所述的用于制备镀铝膜的方法优选包括在所述第二电解处理步骤后的去除衬底的去除步骤。根据上述(10)的本发明的实施方式,可以提供一种制备镀铝膜的方法,该方法能够制备根据上述(3)所述的镀铝膜。[实施方式的详细描述]下面将描述根据本发明的实施方式的镀铝膜及用于制备所述镀铝膜的方法的具体实例。本公开不受限于这些实例,而是由附加的权利要求所限定的,并且意欲涵盖与权利要求的含义和范围等同的含义和范围内的所有修改。<镀铝膜>根据本公开的一个实施方式的镀铝膜包含铝作为主要成分,并且具有位于厚度方向上的两端的涂层表面之间的中间层。此处“包含铝作为主要成分”表示在镀铝膜中铝的含量为50重量%以上。图1是根据本发明的一个实施方式的镀铝膜的实例的截面的放大示意图。如图1所示,镀铝膜10具有位于厚度方向上的两端的涂层表面11和11’之间的中间层12。镀铝膜10可以形成于没有示出的衬底的表面上。当镀铝膜10形成于衬底表面时,涂层表面11和11’的一个涂层表面与衬底表面紧密接触。当衬底是细长片状的衬底时,形成于衬底表面上的镀铝膜10也具有细长片状的形状。中间层12为包含具有比铝低的离子化倾向的金属的层,或包含铝和具有比铝低的离子化倾向的金属的合金的层。中间层12形成于大致平行于镀铝膜10的涂层表面11和11’上。当镀铝膜10为形成于平板型衬底的表面上的镀铝膜时,大致在镀铝膜10的整体上,中间层12大致平行于涂层表面11和11’。当镀铝膜10为形成于具有复杂三维形状的衬底表面上的镀铝膜时,中间层12通常大致部分平行于镀铝膜的涂层表面11和11’。中间层12的厚度优选尽可能地小,以及中间层12可以为单原子层(one-atomiclayer)。中间层12的厚度上限不做特别地限定,但是上限为约500nm以下。随着中间层12厚度的减小,在中间层12两侧上形成的铝层的附着力增强,由此可以防止镀铝膜的电导率的下降。中间层12的厚度更优选为1nm以上且400nm以下,进一步更优选为10nm以上且200nm以下。包括于根据本公开的实施方式的镀铝膜中的中间层可以通过例如使用扫描电子显微镜(sem)或透射电子显微镜(tem)来观察镀铝膜的截面进行确认。在中间层的厚度为约50nm以上的情况下,采用sem可以确认中间层。在中间层的厚度小于约50nm的情况下,采用tem进行元素映射可以确认中间层。图2是根据本公开的一个实施方式的镀铝膜的另一实例的截面的放大示意图。如图2所示,镀铝膜20优选具有位于厚度方向上的两端的涂层表面21和21’之间的多层中间层22。由于镀铝膜20具有多层中间层22,所以可以在更短时间内低成本地制备镀铝膜20。当镀铝膜具有多层中间层时,这些中间层也大致相互平行。组成中间层且具有比铝低的离子化倾向的金属优选为选自由铁(fe)、锌(zn)、锆(zr)、锰(mn)、镍(ni)和铜(cu)组成的组中的至少一种。由于这些金属具有足够高的电导率,所以即使当这些金属存在作为镀铝膜的中间层时,它们也不会降低镀铝膜的电导率。当具有比铝低的离子化倾向的金属为fe、zn、cu或ni时,可以相对较低的成本地制备镀铝膜。当具有比铝低的离子化倾向的金属为zr时,可以进一步加强中间层的两侧形成的铝层之间的附着力。当具有比铝低的离子化倾向的金属为mn时,由于锰具有高的耐腐蚀性,镀铝膜也可以适当地用作非水电解液电池等的集流体。具有比铝低的离子化倾向的金属可以在中间层与铝形成合金。当镀铝膜形成于衬底的表面时,从保护衬底的角度来看,镀铝膜的厚度优选尽可能地大。镀铝膜的厚度优选为约10μm以上。当镀铝膜的厚度优选为10μm以上时,镀铝膜的抗裂强度可以得到增强。从制备成本和减轻重量的角度来看,镀铝膜的厚度优选为约1000μm以下。综合考虑,镀铝膜的厚度更优选为15μm以上且700μm以下,进一步更优选为20μm以上且500μm以下。在相关领域中,需要耗费大量时间来制备具有10μm以上的厚度的镀铝膜。并且,形成具有细长片状形状且具有10μm以上厚度的镀铝膜是非常困难的。相比之下,根据本公开的一个实施方式的镀铝膜,即使当镀铝膜的厚度为10μm以上时,也可以在短时间内低成本地制备镀铝膜,并且也可以容易地制备具有细长片状形状的镀铝膜。此外,根据本公开的一个实施方式的镀铝膜在膜中无间隙并且是致密的。因此,即使镀铝膜的厚度增加,电导率也不会下降,镀铝膜的电导率大致与轧制箔的电导率相同。如图3所示,根据本公开的一个实施方式的镀铝膜可以形成金属多孔体的骨架33,骨架33具有三维网络结构。在图3所示的实例中,骨架33的内部34是中空的。可选地,衬底可以存在于骨架33的内部34中。金属多孔体具有连续的孔,孔35是由骨架33形成的。图4为示意性地示出沿图3中线a-a截取的截面的放大图。如图4所示,形成金属多孔体的骨架33的镀铝膜30具有位于厚度方向上的两端部分的涂层表面31和31’之间的中间层32。理想地,如图4所示,中间层32与涂层表面31和31’大致平行。然而,在具有复杂形状骨架的镀铝膜中,如在包含具有三维网络结构的骨架的金属多孔体中,中间层32处于部分大致平行于涂层表面31和31’的状态。由于骨架是由根据本公开的一个实施方式的镀铝膜形成的,因此即使当金属多孔体整体上具有细长片状的形状时,也可以在短时间内低成本地制备镀铝膜。根据金属多孔体的应用情况,可以适当地选择金属多孔体的孔隙率、平均孔径和厚度。例如,当金属多孔体作为电池的电极(集流体)时,优选具有小的平均孔径和小的厚度的金属多孔体。当金属多孔体用于散热时,优选具有大的平均孔径和大的厚度的金属多孔体。金属多孔体的孔隙率是指金属多孔体的内部空间(孔)与表观体积的比率。金属多孔体的平均孔径是指金属多孔体的骨架所形成的腔室(腔室/英寸)数值的倒数。<用于制备镀铝膜的方法>根据本公开的一个实施方式的用于制备镀铝膜的方法为用于制备根据本公开的一个实施方式的镀铝膜的方法,并且包括第一电解处理步骤、置换步骤和第二电解处理步骤。在制备具有较大厚度的镀铝膜的情况下,在第二电解处理步骤之后可以进一步重复地实施一组置换步骤和第一电解处理步骤。因此,可以制备在镀铝膜中具有多层中间层的镀铝膜。进一步地,在根据本公开的一个实施方式的用于制备镀铝膜的方法中,如果需要,还可以实施去除衬底的去除步骤。将详细地描述各步骤。-第一电解处理步骤-第一电解处理步骤为在第一电解液中使衬底经历电解处理以在衬底的表面上沉积铝来形成预镀铝膜的步骤。电解处理(熔盐电解)可以通过如下方式实施:设置衬底和铝从而在电解液中彼此面对,使衬底与整流器的阴极侧连接,使铝与阳极侧连接,以及在两个电极处施加电压。第一电解处理步骤在惰性氛围中实施,如氩气氛围或氮气氛围。(衬底)衬底不受特殊的限制,只要所述衬底需要具有在其上的镀铝膜即可。例如,铜板、钢带、铜线、钢线、或者经过导电处理的树脂成型体都可以被用作衬底。相关领域中,在细长片状的衬底上形成具有大厚度的镀铝膜是非常困难的,并且需要耗费大量的时间和高成本。相比之下,根据本公开的一个实施方式的用于制备镀铝膜的方法,即使当衬底具有细长片状的形状时,也可以在短时间内低成本地制备具有大的厚度的镀铝膜。例如,具有已经经历导电处理的表面的聚氨酯、三聚氰胺树脂、聚丙烯、聚乙烯等可以被用作已经经历导电处理的树脂成型体。已经经过导电处理的树脂成型体可具有任何形状。但是,通过使用包含具有三维网络结构的骨架的树脂成型体,可以最终制备应用于过滤器、催化剂载体、电池电极等的显示良好性能的金属多孔体。作为包含具有三维网络结构的骨架的树脂成型体,优选使用树脂发泡体。树脂发泡体可以是任意多孔树脂发泡体。可以使用已知或商用的树脂发泡体。例如,可以使用聚氨酯泡沫或苯乙烯泡沫。在这些树脂发泡体中,从高孔隙率的角度来看,特别优选聚氨酯泡沫。图5显示了聚氨酯发泡树脂的图片。类似的,通过使用具有类似无纺布骨架的树脂成型体,可以最终制备具有类似无纺布骨架且优选应用于过滤器、催化剂载体、电池电极等的金属多孔体。图6显示了示意性地示出通过使包含具有三维网络结构的骨架的树脂成型体经历导体处理而制备的衬底的实例的部分截面的放大图。如图6所示,包含具有三维网络结构的骨架的树脂成型体66具有连续的孔,以及孔65是由骨架形成的。由于金属多孔体的骨架是通过在树脂成型体66的骨架上的表面上形成镀铝膜而形成的,所以金属多孔体的孔隙率、平均孔径和厚度与树脂成型体66的孔隙率、平均孔径和厚度大致相同。因此,根据所要制备的目标金属多孔体的孔隙率、平均孔径和厚度可以适当地选择树脂成型体66的孔隙率、平均孔径和厚度。与在金属多孔体的孔隙率和平均孔径的相同的方式定义树脂成型体66的孔隙率和平均孔径。用于使树脂成型体66的骨架的表面经历导电处理的方法不受特别限制,只要在树脂成型体66的骨架的表面上可以形成导电层67即可。构成导电层67的材料的实例包括:金属,如镍、钛,不锈钢;碳粉,如石墨、无定形碳,如碳黑。其中,优选为碳粉,更优选为碳黑。在导电层67是由除金属之外的无定形碳或碳粉形成时,当需要时,去除树脂成型体时也同时去除导电层67。例如,在使用镍的情况下,导电处理的特别优选的实例为非电解电镀处理和溅射处理。在使用如钛或不锈钢的金属,碳黑或石墨的材料的情况下,优选方法的实例为将通过向任意的这些材料的细粉末中加入粘合剂而制备的混合物涂布到树脂成型体66的骨架的表面上的处理。例如,在使用镍的非电解电镀处理中,将树脂成型体66浸入已知的非电解镀镍浴中,如含有次磷酸钠作为还原剂的硫酸镍水溶液。例如,在浸入电镀浴前,根据需要,将树脂成型体66可以被浸入含有少量钯离子的活化液(清洗液,由日本kanigen有限责任公司生产)中。例如,使用镍的溅射处理可以按照如下步骤实施。在将树脂成型体66附着在衬底支架上之后,在衬底支架和目标物(镍)之间施加直流电压的同时引入惰性气体,从而导致电离的惰性气体与镍发生碰撞。所得的溅射镍粒子沉积在树脂成型体66的骨架的表面上。导电层67是连续形成的,以便覆盖树脂成型体66的骨架的表面。导电层67的涂层的重量优选为,但不是必须的,1.0g/m2以上且30g/m2以下,更优选为5.0g/m2以上且20g/m2以下,进一步更优选为7.0g/m2以上且15g/m2以下。导电层的涂层的重量是指在包含每表观单位面积的在骨架的表面上形成的导电层的树脂成型体的导电层的质量。(电解液)作为电解液,可以使用能够在衬底的表面上电沉积铝的熔盐(离子液体)。具体地,电解液可以为含有卤化铝的熔盐,也可以选择性包含添加剂。卤化铝包括氯化铝(alcl3)、溴化铝(albr3)和碘化铝(ali3)。其中,最优选为氯化铝。例如,氯化物熔盐或氟化物熔盐可以优选被用作熔盐。可以使用的氯化物熔盐的实例包括kcl、nacl、cacl2、licl、rbcl、cscl、srcl2、bacl2、mgcl2及它们的共融盐。可以使用的氟化物熔盐的实例包括lif、naf、kf、rbf、csf、mgf2、caf2、srf2、baf2及它们的共融盐。在上述熔盐中,从低成本和易得性的角度来看,优选使用kcl、nacl、或cacl2。从降低熔点的角度来看,熔盐优选包含选自由烷基咪唑鎓卤化物、烷基吡啶鎓卤化物和脲类化合物中的至少一种形成熔融盐的化合物。当与卤化铝混合时,在约110℃以下形成熔盐的化合物可以适当地被用于形成熔融盐的化合物。烷基咪唑鎓卤化物的实例包括在1-和3-位上具有烷基基团(各自具有1至5个碳原子)的氯化咪唑鎓、在1-、2-和3-位上具有烷基基团(各自具有1至5个碳原子)的氯化咪唑鎓、在1-和3-位上具有烷基基团(各自具有1至5个碳原子)的碘化咪唑鎓。它们具体的实例包括氯化1-乙基-3-甲基咪唑鎓(emic)、氯化1-丁基-3-甲基咪唑鎓(bmic)和氯化1-甲基-3-丙基咪唑鎓(mpic)。其中,最优选使用氯化1-乙基-3-甲基咪唑鎓(emic)。烷基吡啶鎓卤化物的实例包括氯化1-丁基吡啶鎓(bpc)、氯化1-乙基吡啶鎓(epc)和氯化1-丁基-3-甲基吡啶鎓(bmpc)。其中,最优选为氯化1-丁基吡啶鎓。脲类化合物指的是尿素或其衍生物,以及例如,可以优选使用由式(1)表示的化合物。[化学式1]式1在式(1)中,r各自表示氢原子、具有1至6个碳原子的烷基基团或苯基,以及r可以彼此相同或不同。在上述化合物中,特别地优选使用尿素和二甲脲作为脲类化合物。在使用上述形成熔盐化合物的情况下,通过调整卤化铝与形成熔盐的化合物的摩尔比范围至1:1至3:1来获得适合在衬底表面上电沉积铝的电解液。添加剂的实例包括平滑剂,该平滑剂能够使在衬底表面上电沉积的预镀铝膜变得平整。例如,选自由氯化1,10-菲咯啉一水合物、1,10-菲咯啉一水合物和1,10-菲咯啉组成的组中的至少一种化合物可以优选被用作平滑剂。当电解液含有任意的这些平滑剂时,就可以形成平整的、镜面般的预镀铝膜。-置换步骤-置换步骤为将在第一电解处理步骤中在衬底的表面上形成的预镀铝膜浸入置换溶液中以使用除铝以外的金属置换预镀铝膜的表面的步骤。置换溶液是一种含有具有比铝低的离子化倾向的金属的溶液。因此,将预镀铝膜和衬底一起浸入置换溶液中,用具有比铝低的离子化倾向的金属可以置换预镀铝膜的表面。当在第一电解处理步骤之后从第一电解液中取出预镀铝膜时,由于氛围中非常少量存在的氧气,在预镀铝膜的表面上形成了氧化物膜。在置换步骤中,预镀铝膜表面上的铝和氧化物膜一起溶解于置换溶液中,相反地,置换溶液中包含的金属沉积于预镀铝膜的表面上来形成置换镀膜。具体地,在预镀铝膜的表面上的铝(包括氧化物膜)被置换溶液中的金属置换,而因此,在预镀铝膜的表面上形成了由置换溶液中包含的金属制成的层。由置换溶液中包含的金属制成的层起到根据本公开的一个实施方式的镀铝膜中的中间层的作用。与铝相比,在置换溶液中包含的金属不会形成致密的氧化物膜。因此,紧随置换步骤之后实施的在第二电解处理步骤电沉积的铝对由第二电解液中包含的金属制成的层具有高的附着力。实施置换步骤的时间不受特别限制,以及实施置换步骤从而充分去除在预镀铝膜表面上的氧化物膜。从使中间层的厚度尽可能小的角度看,优选实施置换步骤不超过必要的时间。根据置换溶液中所包含的金属,在约1秒以上且约1小时以下的范围内实施置换步骤。在需要时间以用在置换溶液中包含的金属来置换铝的情况下,可以通过提供电流来缩短时间。在置换步骤中,置换溶液的温度为约20℃以上且200℃以下。在置换步骤中,预镀铝膜的表面被在置换溶液中所包含的金属均匀地置换。因此,以大致平行于衬底的表面(预镀铝膜的涂层表面)来形成由在置换溶液中包含的金属制成的层,只要在第一电解处理步骤中在衬底的表面上均匀地形成预镀铝膜即可。(置换溶液)置换溶液是将具有比铝低的离子化倾向的金属加入到在第一电解处理步骤中使用的第一电解液中得到的溶液。由于该金属具有比铝低的离子化倾向,所以可以优选使用选自由铁(fe)、锌(zn)、锆(zr)、锰(mn)、镍(ni)和铜(cu)组成的组中的至少一种金属。通过将具有比铝低的离子化倾向的金属的氯化物溶解于在第一电解处理步骤使用的第一电解液中,可以容易地制备置换溶液。例如,fecl4、zncl2、zrcl4、mncl2、nicl2或cucl2可以被用作具有比铝低的离子化倾向的金属的氯化物。在置换溶液中,具有比铝低的离子化倾向的金属的氯化物的浓度可以为约10mmol/l以上且1mol/l以下。-第二电解处理步骤-第二电解处理步骤为在第二电解液中使在置换步骤后的置换镀膜经历电解处理以在置换镀膜的表面上电沉积铝来形成镀铝膜的步骤。在相关领域中,以多阶段形成镀铝膜时,由于将镀铝膜从电解液中拉起时在镀铝膜的表面上形成氧化物膜的影响,所以在各阶段形成的镀铝膜之间的附着力不会增加。相反地,在根据本公开的实施方式的用于制备镀铝膜的方法中,在第二电解处理步骤中使用的置换镀膜的表面上没有形成致密的铝的氧化物膜,因此可以增加在各阶段形成的镀铝膜之间的附着力。第二电解处理步骤可以在与第一电解处理步骤的相同的条件下实施。具体地,在第一电解处理步骤中,除了使用置换步骤后的置换镀膜来代替使用衬底之外,可以与与第一电解处理步骤相同的方式实施第二电解处理步骤。在第二电解处理步骤中使用的第二电解液不必具有与在第一电解处理步骤中使用的第一电解液的相同的组分。然而,从防止其他成分进入的角度来看,在第一电解处理步骤和第二电解处理步骤中优选使用具有相同组分的电解液。当第一电解液和第二电解液具有相同组分时,优选分别制备各自的电镀浴。然而,从节省空间的角度来看,在第一电解处理步骤中已经使用的电镀浴可以在第二电解处理步骤中再次使用。在第二电解处理步骤中,当铝均匀地电沉积于置换镀膜的表面上时,由置换溶液中包含的金属制成的层和镀铝膜的表面(涂层表面)大致相互平行。-去除步骤-通过第一电解处理步骤、置换步骤和第二电解处理步骤在衬底的表面上可以形成根据本公开的一个实施方式的镀铝膜。然而,在不需要衬底时,可以实施去除衬底的去除步骤。用于去除衬底的方法不受特别限制。例如,当衬底为平板型衬底时,可以通过将镀铝膜从衬底上分离来去除衬底。当衬底为树脂成型体时,可以通过例如热处理去除衬底。例如,在通过热处理去除衬底的情况下,例如,在空气氛围中将镀铝膜加热到约400℃以上且680℃以下。在实施热处理的情况下,制备了中间层中的金属与铝合金化的铝镀膜。[实施例]尽管将在以下实施例的基础上更加详细地描述本公开,但这些实施例是说明性的,本发明的镀铝膜以及用于制备镀铝膜的方法不限于此。本公开的保护范围是由附加的权利要求所限定的,并且涵盖与本发明的权利要求的范围和含义等同的范围和含义内的所有的修改。实施例1<第一电解处理步骤>(衬底)制备平板状的铜板(50mm×80mm×1mm)作为衬底。(电解液)电解液的制备如下。将氯化铝(alcl3)与氯化1-乙基-3-甲基咪唑鎓(emic)以2:1的摩尔比率混合制备熔盐,将氯化1,10-菲咯啉一水合物作为平滑剂加入到熔盐中以具有0.5g/l的浓度。(熔盐电解)在铜板被用作阴极以及具有99.99%纯度的铝板被用作阳极的方式在如上所述的制备的电解液中实施熔盐电解。在铜板的表面上电沉积铝以形成预镀铝膜。电解液的温度为45℃。电流密度调整为3.0a/dm2。<置换步骤>(置换溶液)将fecl4加入在第一电解处理步骤中制备的电解液中以具有20mmol/l的浓度来制备置换溶液。(置换条件)将上面形成有预镀铝膜的铜板浸入如上所述制备的置换溶液中。浸入时间为10秒,以及置换溶液的温度为40℃。因此,得到其中预镀铝膜的表面被fe置换的置换镀膜。<第二电解处理步骤>在第一电解处理步骤中,除了在上面形成有置换镀膜的铜板来代替铜板之外,与在第一电解处理步骤相同的方式实施第二电解处理步骤。因此,制备了具有由fe制成且位于厚度方向上的两端的涂层表面之间的中间层的1号镀铝膜。1号镀铝膜具有约15μm的厚度。实施例2在实施例1中,除了在第二电解处理步骤之后加入通过将所得的2号镀铝膜浸入硝酸中来去除用作衬底的铜板的步骤之外,以与实施例1相同的方式制备2号镀铝膜。2号镀铝膜具有约17μm的厚度。实施例3<第一电解处理步骤>(衬底)制备已经经过导电处理的树脂成型体作为衬底。所使用的树脂成型体为具有1.0mm的厚度且包含具有三维网络结构的骨架的聚氨酯板(50mm×80mm)。所述树脂成型体具有96%的孔隙率和450μm的平均孔径。将聚氨酯板浸入碳悬浮液中,干燥后所得的聚氨酯板以所述聚氨酯板的骨架的表面上形成导电层来实施导电处理。碳悬浮液包含:25%含量的石墨和碳黑,树脂粘合剂,渗透剂和消泡剂作为组分。碳黑的粒径为0.5μm。(电解液)制备与在实施例1中的第一电解处理步骤中使用的电解液相同的电解液作为电解液。(熔盐电解)在已经经历导电处理的聚氨酯板被用作阴极以及具有99.99%纯度的铝板被用作阳极的方式在如上所述的制备的电解液中实施熔盐电解。因此,在已经经历导电处理的聚氨酯板的表面上电沉积铝以形成预镀铝膜。电解液的温度为45℃。电流密度调整为6.0a/dm2。<置换步骤>在与实施例1相同的条件下实施置换步骤。因此,在聚氨酯板的骨架的表面上形成置换镀膜。<第二电解处理步骤>在第一电解处理步骤中,除了使用其上形成有置换镀膜的聚氨酯板来代替已经经历导电处理的聚氨酯板之外,以与第一电解处理步骤相同的方式实施第二电解处理步骤。因此,形成了具有由fe制成且位于厚度方向上的两端的涂层表面之间的中间层的镀铝膜。<去除步骤>将上述所制备的镀铝膜在空气氛围下加热至600℃,通过燃烧去除聚氨酯板。因此,制备了3号镀铝膜,3号镀铝膜形成了金属多孔体的骨架,该金属多孔体包含具有三维网络结构的骨架。3号镀铝膜的厚度为约15μm。实施例4在实施例3中,除了使用如下述的置换溶液之外,以与实施例3相同的方式制备4号镀铝膜。4号镀铝膜的厚度为约18μm。(置换溶液)将zncl2加入到在实施例1的第一电解处理步骤中所使用的电解液中以具有40mmol/l的浓度来制备置换溶液。实施例5在实施例3中,除了使用如下述的置换溶液之外,以与实施例3相同的方式制备5号镀铝膜。5号镀铝膜的厚度为约16μm。(置换溶液)将zrcl2加入到在实施例1的第一电解处理步骤中使用的电解液中以具有100mmol/l浓度来制备置换溶液。对比例1在实施例2中,除了实施第二电解处理步骤而不实施置换步骤之外,以与实施例2相同的方式制备6号镀铝膜。6号镀铝膜的厚度为约16μm。对比例2在实施3中,除了实施第二电解处理步骤而不实施置换步骤之外,以与实施例3相同的方式制备7号镀铝膜。7号镀铝膜的厚度为约18μm。-评价-对上述所制备的1号至7号镀铝膜进行了如下评价。表1显示了评价结果。<电导率测试>使用电阻率计对2号至7号镀铝膜中的每一个的电阻率进行了测量,从而测量终端的距离为60mm。表1显示了测量结果。表1镀铝膜编号镀铝膜厚度(μm)电阻率(μω·m)115-2170.0383151.824181.785161.886160.0627182.09如表1所示,比较实施例2的2号镀铝膜和对比例1的6号镀铝膜,两者都是通过用于在铜板表面上形成镀铝膜的方法制备的,2号镀铝膜具有更低的电阻率。通过轧制而制备且厚度为18μm的镀铝膜的电阻率为0.031μω·m。这说明实施例2的2号镀铝膜的具有与通过轧制而制备的膜的电阻率相当的低电阻率。比较实施例3至5的3号至5号镀铝膜和对比例2的7号镀铝膜,它们都是通过用于在聚氨酯板的骨架的表面上形成镀铝膜的方法制备的,3号至5号镀铝膜中的每一个具有更低的电阻率。<镀铝膜的截面的观察>用扫描电子显微镜(sem)对3号、4号和7号镀铝膜中的每一个的截面进行观察。图7至9显示了观察结果。如图7和8所示,根据本公开的实施方式的3号和4号镀铝膜分别具有位于厚度方向上的两端的涂层表面之间的中间层72和82。此外,中间层两侧上的铝层彼此无间隙地紧密接触。相比之下,如图9所示,其中没有实施置换步骤的对比例2的7号镀铝膜具有位于在第一电解处理步骤中形成的镀铝膜和第二电解步骤中形成的镀铝膜之间的间隙,而具有差的附着力。此外,在第二电解处理步骤中形成的镀铝膜部分脱落。当前第1页12