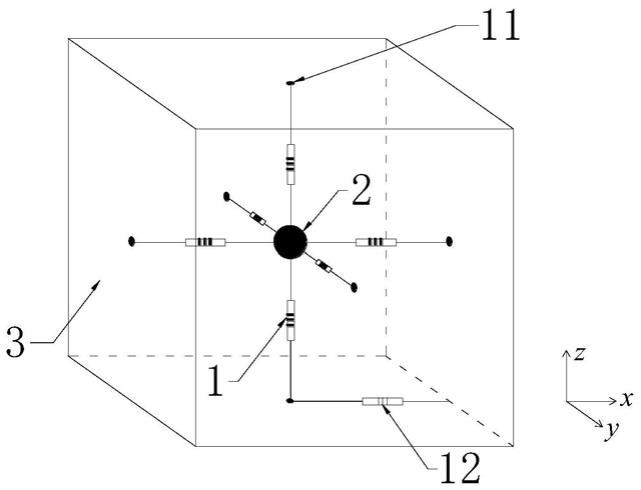
[0001]
本发明涉及煤矿设备技术领域,特别是涉及一种用于采煤机滚筒光纤光栅智能识别煤岩装置。
背景技术:[0002]
随着采煤工艺进入智能化阶段,煤岩界面识别是采煤机自动控制的基础,也是实现智能化开采的先决条件。由于煤矿井下工作环境恶劣,工作人员对采煤机的截割状态极易造成误判,导致无法及时调节采煤机滚筒高度。当采煤机滚筒高度调节过高,滚筒截割岩石时,导致滚筒的截齿磨损加速,采煤机的寿命缩短,造成煤矸石落入煤中,增加后期选煤成本,同时造成高粉尘、高噪声的工作环境,对工作人员生命安全造成危害;当采煤机滚筒高度调节过低,顶、底煤剩余过厚,采煤工作面回采率过低,降低经济效率。目前已有20多种方法对此展开研究,包括人工γ射线法、自然γ射线法、机械振动法、雷达探测法、红外反射和记忆截割法等。根据采煤机是否需截割岩石,将煤岩界面自动识别技术分为非接触式技术和接触式技术。非接触式技术,如机器视觉技术、电磁探测技术等;接触式技术,如振动探测技术、扭矩探测技术等。现在最常用的煤岩识别技术有:机器视觉技术、电磁探测技术、伽马射线探测技、振动探测技术四种。
[0003]
机器视觉技术是通过人工制造光源,利用工业相机获得采煤机滚筒前方的图像,再利用各类特征提取方法和识别算法进行煤岩界面的识别。机器视觉技术与人眼识别煤岩界面的过程一致,可以直观地判断,具有高可靠性和通用性,在技术方面也容易实现。但是机器视觉技术的图像质量容易受到环境的影响,比如粉尘浓度过高、光照强度不够稳定、工作面需要喷水处理等都会影响到相机的图像获取质量。
[0004]
电磁探测技术包括雷达探测技术和电子自旋共振技术。电磁探测技术是采用脉冲生成器生成电磁脉冲,利用天线发射装置发射电磁波,反射回来的电磁波被接收装置接收,通过这一个过程会将各个对电磁波反射性质不同的材料加以识别。这种技术适用的范围广,不受环境光照、工作面粉尘以及水雾的影响限制。但电磁探测技术也有局限之处,比如:容易受到天线放大器溢出、天线环时响应等的干扰,导致识别精度不能满足要求。电子自旋共振技术是在顶煤下方放置线圈,当线圈形成磁场与天线发射的电磁波发生共振时,电磁波会被顶煤吸收,根据接收到的电磁波强度可推算出煤层厚度,信号强度越弱,煤层越厚,目前测煤厚度可达13~152mm。该技术对煤岩的物理性质没有要求,但是波长与穿透介质厚度有关,顶煤厚度越大,衰减越严重,影响识别精度。而且这种技术探测的范围较小。
[0005]
伽马射线探测技术是利用射线传感器提取射线强度信号理论来推测煤层厚度。这种技术适用于高瓦斯矿井,提升了适用的范围,同时不需要提供放射源,减小了技术成本。射线的探测范围较大,放顶煤厚度可以控制在500mm以内。但这种技术要求井下顶底板中含有放射性元素,否则射线传感器将不能接收到信号。射线探测的精度容易受到矸石的影响,若煤层中夹矸太多,识别精度会大大下降。
[0006]
当煤岩的普氏系数较大时,可以采用振动探测技术来识别煤岩界面。振动探测技
术是将振动传感器放置在采煤机的合适位置,通过后期的信号放大和数据处理得到振动曲线,进而判断煤岩界面。但现有的振动传感器容易受到环境的干扰,降低识别精度,同时参数处理不够迅速会使采煤机的反应迟滞。
[0007]
现今煤岩识别技术都会受到工作面环境的影响,尤其是一些非接触式识别技术,当粉尘浓度高、喷水降尘等因素会极大地影响识别精度。接触式煤岩识别技术需要研发抗干扰能力强、能获得稳定参数的传感器,尽可能的提高煤岩识别精度。因此,需要通过研制一种不受工作环境干扰的传感器进行煤岩界面识别以及成套的采煤机滚筒自动升降系统显得尤为重要。
技术实现要素:[0008]
本发明的目的是提供一种用于采煤机滚筒光纤光栅智能识别煤岩装置,以解决上述现有技术存在的问题。
[0009]
为实现上述目的,本发明提供了如下方案:本发明提供一种用于采煤机滚筒光纤光栅智能识别煤岩装置,包括采煤机滚筒,所述采煤机滚筒上固定设置有光纤光栅加速度传感器,所述光纤光栅加速度传感器电性连接有光纤光栅解调仪,所述光纤光栅解调仪电性连接有计算机,所述计算机电性连接有信号接收器,所述信号接收器连接有控制所述滚筒运动的油泵电机。
[0010]
优选的,所述光纤光栅加速度传感器包括壳体,所述壳体内部设置有圆形振子,所述圆形振子的周向固定连接有六根光纤bragg光栅,所述六根光纤bragg光栅分别与壳体的六个端面固定连接,所有所述光纤bragg光栅的端头汇集成束后与光纤光栅解调仪电性连接。
[0011]
优选的,所述光纤bragg光栅靠近所述圆形振子的一侧贯穿有光纤固定支架,所述光纤固定支架的内部设置有预紧柱,所述光纤bragg光栅贯穿预紧柱且与预紧柱固定连接;所述光纤固定支架的外侧套接有保护套,所述保护套与壳体固定连接,所述保护套内设置有隔板,所述隔板与光纤固定支架之间设置有阻尼弹簧和阻尼器。
[0012]
优选的,所述预紧柱为“l”形结构,所述阻尼弹簧套接在预紧柱的外侧,所述光纤固定支架的侧壁上开设有容纳所述阻尼器的凹槽,所述阻尼弹簧与阻尼器之间设置有间隙。
[0013]
优选的,所述光纤bragg光栅与预紧柱通过固定螺丝固定连接,所述固定螺丝设置在隔板与保护套之间。
[0014]
优选的,所述壳体为正方体,所述圆形振子设置在壳体的中心位置,所述光纤bragg光栅垂直于所述壳体的六个端面。
[0015]
优选的,所述壳体内部固定设置有光纤光栅温度传感器,所述光纤光栅温度传感器与光纤光栅解调仪电性连接。
[0016]
优选的,所述光纤光栅解调仪为矿用本安型光纤光栅解调仪,在光纤光栅受到轴向应变时及时解调信号并传输给外部计算机。
[0017]
本发明公开了以下技术效果:
[0018]
(1)实时监测,精度高。本发明设计并使用了光纤光栅加速度传感器,光纤光栅的光波反射变化迅速,能够将振动信号及时有效的传输到计算机数据处理系统并生成曲线
图,给采煤机自动升降提供良好的环境。
[0019]
(2)不会受到采煤工作面恶劣环境的干扰。井下采煤工作面粉尘浓度高,环境湿度大并且会出现地下电磁波干扰。现有的加速度传感器很难排除上述因素影响,本发明能够克服上述问题,给采煤机升降控制系统提供稳定的实时数据。
[0020]
(3)容易部署和维护,成本低。光纤光栅技术成熟,制作成本低,在部署时比其他类型的加速度传感器方便,使用年限可达5年及以上。
附图说明
[0021]
为了更清楚地说明本发明实施例或现有技术中的技术方案,下面将对实施例中所需要使用的附图作简单地介绍,显而易见地,下面描述中的附图仅仅是本发明的一些实施例,对于本领域普通技术人员来讲,在不付出创造性劳动性的前提下,还可以根据这些附图获得其他的附图。
[0022]
图1为本发明光纤bragg光栅、圆形振子和壳体位置示意图;
[0023]
图2为本发明光纤光栅加速度传感器结构示意图;
[0024]
图3为光纤光栅加速度传感器力学模型示意图;
[0025]
图4为本发明结构示意图;
[0026]
图5为滚筒割煤状态时,光纤光栅加速度传感器测得的振动加速度与工作时间的线性关系图;
[0027]
图6为滚筒割岩状态时,光纤光栅加速度传感器测得的振动加速度与工作时间的线性关系图;
[0028]
图7为滚筒空转状态时,光纤光栅加速度传感器测得的振动加速度与工作时间的线性关系图。
[0029]
其中,1为光纤bragg光栅,2为圆形振子,3为壳体,4为固定螺丝,5为保护套,6为预紧柱,7为阻尼弹簧,8为光纤固定支架,9为阻尼器,10为光纤光栅解调仪,11为壳体中心点,12为光纤光栅温度传感器,13为信号接收器,14为计算机,15为滚筒,16为油泵电机,17为光纤光栅加速度传感器。
具体实施方式
[0030]
下面将结合本发明实施例中的附图,对本发明实施例中的技术方案进行清楚、完整地描述,显然,所描述的实施例仅仅是本发明一部分实施例,而不是全部的实施例。基于本发明中的实施例,本领域普通技术人员在没有做出创造性劳动前提下所获得的所有其他实施例,都属于本发明保护的范围。
[0031]
为使本发明的上述目的、特征和优点能够更加明显易懂,下面结合附图和具体实施方式对本发明作进一步详细的说明。
[0032]
参照图1-7,本发明提供一种用于采煤机滚筒光纤光栅智能识别煤岩装置,包括采煤机滚筒15,采煤机滚筒15上固定设置有光纤光栅加速度传感器17,光纤光栅加速度传感器17电性连接有光纤光栅解调仪10,光纤光栅解调仪10电性连接有计算机14,计算机14电性连接有信号接收器13,信号接收器13连接有控制滚筒15运动的油泵电机16。当采煤机工作时,光纤光栅加速度传感器17会将收集到的振动信号以波形传输到光纤光栅解调仪10,
经过计算机14的数据处理后将信号传输给信号接收器13,判断该采煤机滚筒15的切割状态,油泵电机16对此做出相应的反应。
[0033]
光纤光栅加速度传感器17包括壳体3,壳体3内部设置有圆形振子2,圆形振子2的周向固定连接有六根光纤bragg光栅1,六根光纤bragg光栅1分别与壳体3的六个端面固定连接,壳体3为正方体,圆形振子2设置在壳体3的中心位置,光纤bragg光栅1垂直于壳体3的六个端面。能够准确地获得滚筒15的运动状态。所有光纤bragg光栅1的端头汇集成束后与光纤光栅解调仪10电性连接。
[0034]
光纤bragg光栅1靠近圆形振子2的一侧贯穿有光纤固定支架8,光纤固定支架8靠近圆形振子2的一侧为弧形结构,每个光纤固定支架8与圆形振子2之间均存在一定的距离,光纤固定支架8组成了一个运动腔,圆形振子2可以在该运动腔内运动。光纤固定支架8的内部设置有预紧柱6,光纤bragg光栅1贯穿预紧柱6且与预紧柱6固定连接,光纤bragg光栅1与预紧柱6通过固定螺丝4固定连接,固定螺丝4设置在隔板与保护套5之间。光纤固定支架8的外侧套接有保护套5,保护套5与壳体3固定连接,保护套5内设置有隔板,隔板与光纤固定支架8之间设置有阻尼弹簧7和阻尼器9。预紧柱6为“l”形结构,阻尼弹簧7套接在预紧柱6的外侧,光纤固定支架8的侧壁上开设有容纳阻尼器9的凹槽,阻尼弹簧7与阻尼器9之间设置有间隙。光纤固定支架8会限制圆形振子2的运动范围,当圆形振子2撞击到光纤固定支架8时,阻尼弹簧7和阻尼器9会对圆形振子2进行缓冲,防止与圆形振子2固定连接的光纤bragg光栅1受到损害。
[0035]
图3位光纤光栅加速度传感器的力学模型,将阻尼弹簧7和光纤光栅1简化为两根具有不同弹性模量的弹簧,光纤光栅1末端与具有一定质量m的圆形振子2连接,根据分析可以得到加速度传感器的固有频率和频率响应范围。当外部振动时圆形振子2响应并产生位移,光纤光栅发生轴向应变后转化为波长的变化量。
[0036]
壳体3内部固定设置有光纤光栅温度传感器12,光纤光栅温度传感器12与光纤光栅解调仪10电性连接。在振动监测过程中,采用相同温度条件下的光纤光栅温度传感器12进行温度补偿,防止温度变化对监测结果产生干扰,以剔除温度所产生的干扰,使得监测的数据可靠性更高。
[0037]
光纤光栅解调仪10为矿用本安型光纤光栅解调仪10,在光纤光栅受到轴向应变时及时解调信号并传输给外部计算机14。光纤光栅解调仪10与计算机14构成的数据处理模块为现有技术,其中光纤光栅解调仪10包括光电转换模块、数据采集模块、波长计算模块和数据分析模块。
[0038]
工作过程:滚筒15振动(信号输出)
→
光纤光栅加速度传感器17响应(信号响应)
→
光纤光栅解调仪10和计算机14(信号处理)
→
信号接收器13(信号接收)
→
控制器(信号输出)
→
油泵电机16(信号响应)
→
滚筒15调节高度(信号响应)。
[0039]
光纤光栅加速度传感器17安装在采煤机滚筒15的测点上,当采煤机工作时,光纤光栅加速度传感器17会将收集到的振动信号以波形传输到光纤光栅解调仪10,经过计算机14的数据处理后将信号传输给信号接收器13,判断该采煤机滚筒15的切割状态,分为以下几种:
[0040]
若判断采煤机滚筒15是割煤状态,信号接收器13将信号传输给控制器,控制器判断后传输信号至控制滚筒15运动的油泵电机16,油泵电机16调节采煤机滚筒15按设定的轨
迹继续运行,光纤光栅加速度传感器测得的振动加速度与工作时间的线性关系如图5所示。
[0041]
若判断采煤机滚筒15是割岩状态,信号接收器13将信号传输给控制器,控制器判断并传输信号至控制滚筒15运动的油泵电机16,油泵电机16将自动调节采煤机滚筒15高度,光纤光栅加速度传感器会检测最新的振动状态,并进行判断,以此循环,直至采煤机滚筒15保持割煤状态。图6中为光纤光栅振动传感器17监测到的信号经光纤光栅解调仪10和计算机14处理后得到振动曲线图像,可以看出在5s时采煤机滚筒15处于割岩状态,通过采煤机自动升降系统在10s后采煤机滚筒15处于割煤状态。
[0042]
若判断采煤机滚筒15是空转状态,信号接收器13将信号传输给控制器,控制器判断并传输信号至控制滚筒15运动的油泵电机16,油泵电机16将自动调节采煤机滚筒15高度,光纤光栅加速度传感器会检测最新的振动状态,并进行判断,以此循环,直至采煤机滚筒15保持割煤状态。图7为光纤光栅振动传感器17监测到的信号经光纤光栅解调仪10和计算机14处理后得到振动曲线图像,可以看出在7.5s时采煤机滚筒15处于空转,通过采煤机自动升降系统在13s后采煤机滚筒15处于割煤状态。
[0043]
在本发明的描述中,需要理解的是,术语“纵向”、“横向”、“上”、“下”、“前”、“后”、“左”、“右”、“竖直”、“水平”、“顶”、“底”、“内”、“外”等指示的方位或位置关系为基于附图所示的方位或位置关系,仅是为了便于描述本发明,而不是指示或暗示所指的装置或元件必须具有特定的方位、以特定的方位构造和操作,因此不能理解为对本发明的限制。
[0044]
以上所述的实施例仅是对本发明的优选方式进行描述,并非对本发明的范围进行限定,在不脱离本发明设计精神的前提下,本领域普通技术人员对本发明的技术方案做出的各种变形和改进,均应落入本发明权利要求书确定的保护范围内。