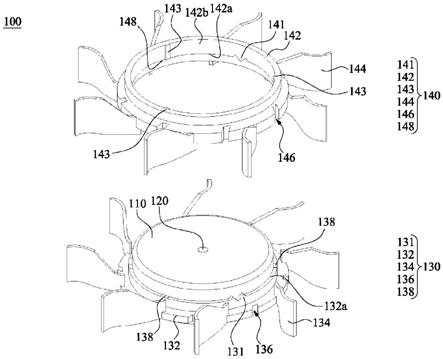
[0001]
本发明是关于一种风扇模块。
背景技术:[0002]
一般而言,风扇的转子有多个叶片连接在中央的轮毂上。考虑到生产成本及扇叶转子的平衡,目前常是由一套射出成型的模具来制造出扇叶转子。因为射出成型模具所产出的扇叶转子,通常都会有脱模的问题,以致于扇叶的结构设计有所局限。
[0003]
此外,随着电子产品的轻薄化,装设于电子产品内,用以散热电子元件的风扇体积也随之减小,叶片之间的间距也会因此缩小。间距缩小等同于模具此位置的结构也会缩小,提升了制作模具的难度,也提升了工艺难度。除了模块结构有一定缩小尺寸的限制之外,对于模具本体的耐用性也会有影响。
技术实现要素:[0004]
本发明的目的在于提供一种可克服生产制造时脱模的问题,减少扇叶结构设计上限制的风扇模块。
[0005]
依据本发明的一实施方式,一种风扇模块包含轮毂、第一扇叶体以及第二扇叶体。轮毂被配置成基于中心轴转动。第一扇叶体与轮毂的外壁连接。第二扇叶体套设于轮毂的外壁。第二扇叶体包含多个肋条。肋条设置于第二扇叶体的内壁,并与轮毂的外壁抵接。
[0006]
综上所述,本发明的风扇模块是将风扇转子叶片结构分拆成两个以上的元件,以利于各个叶片分别脱模生产。接着,再通过组装的方式,将这些分拆的扇叶体组合成预期的扇叶转子结构。如此,可克服生产制造时脱模的问题,减少扇叶结构设计上的限制。此外,在多个扇叶体上设置有肋条、凸台以及对位部等辅助对位结构。通过上述肋条、凸台以及对位部的辅助,组装风扇模块时,可有效提升多个扇叶体之间的对位精准度,以确保扇叶体组装后同心度的一致、扇叶体之间贴合的平整度,以及扇叶在旋转方向的角度方位正确对齐。
[0007]
以上所述仅用以阐述本发明所欲解决的问题、解决问题的技术手段、及其产生的功效等等,本发明的具体细节将在下文的实施方式及相关附图中详细介绍。
附图说明
[0008]
图1为本发明一实施方式的风扇模块的立体图。
[0009]
图2为图1中的风扇模块沿线段2-2的剖面分解图。
[0010]
图3为图1中的风扇模块的分解图。
[0011]
图4a为图1中的风扇模块沿线段4-4的剖面图。
[0012]
图4b为图1中的第二扇叶体的俯视图。
[0013]
图5为图1中的风扇模块的局部示意图。
[0014]
图6a为本发明另一实施方式的风扇模块的分解图。
[0015]
图6b为图6a的风扇模块的立体图。
[0016]
图7a为本发明又一实施方式的风扇模块的分解图。
[0017]
图7b为图7a的风扇模块的立体图。
具体实施方式
[0018]
以下将以附图公开本发明的多个实施方式,为明确说明起见,许多实务上的细节将在以下叙述中一并说明。然而,应了解到,这些实务上的细节不应用以限制本发明。也就是说,在本发明部分实施方式中,这些实务上的细节是非必要的。此外,为简化附图起见,一些已知惯用的结构与元件在附图中将以简单示意的方式示。
[0019]
请参照图1~3。图1为本发明一实施方式的风扇模块100的立体图。图2为图1中的风扇模块100沿线段2-2的剖面分解图。图3为图1中的风扇模块100的分解图。
[0020]
本实施方式的风扇模块100可以装设于电子装置中,以对电子装置中的电子元件进行散热,避免电子元件运作时温度过高而损坏的散热风扇。在一些实施方式中,电子装置可以是笔记本电脑、平板电脑、台式机等,本发明不应以此为限。
[0021]
如图1以及图2所示,风扇模块100包含轮毂110、转轴120、第一扇叶体130以及第二扇叶体140。轮毂110被配置成基于中心轴c转动。在此实施例中,转轴120与轮毂110一体成形地连接,且转轴120与中心轴c的位置重合。在另一实施例中,转轴120与轮毂110为两个不同的元件,并彼此固接。第一扇叶体130包含第一环状结构132以及多个第一叶片134(图中仅示例性地标示一个)。第一扇叶体130的第一环状结构132与轮毂110的外壁110a连接。多个第一叶片134连接第一环状结构132,并朝远离轮毂110的方向延伸。第二扇叶体140包含第二环状结构142以及多个第二叶片144(图中仅示例性地标示一个)。第二扇叶体140的第二环状结构142套设于轮毂110的外壁110a,并与第一环状结构132叠合。多个第二叶片144连接第二环状结构142,并朝远离轮毂110的方向延伸。在此实施例中,多个第一叶片134以及多个第二叶片144环绕着中心轴c交替排列。换言之,每个第一叶片134是位于相邻两第二叶片144之间,且每个第二叶片144是位于相邻两第一叶片134之间,但本发明不应以此为限。
[0022]
在一些实施方式中,转轴120、轮毂110以及第一扇叶体130是通过射出成型的方式结合成型,但本发明不应以此为限。
[0023]
如图3所示,第一扇叶体130还包含多个第一容置槽136(图中仅示例性地标示一个)、多个第一凸台138以及多个第一对位部131。在此实施例中举三个第一凸台138以及两个第一对位部131(有些第一凸台138及第一对位部131因角度关系,故未示于图中)为例进行说明。第一容置槽136形成于第一环状结构132的外缘。每个第一容置槽136设置于相邻两第一叶片134之间。具体而言,第一容置槽136是设置于与第二扇叶体140的多个第二叶片144相对应的位置。当第二扇叶体140套设于轮毂110外时,第一容置槽136可用以容纳第二叶片144,以使第一叶片134与第二叶片144更加密合。如此,为了避免因为叶片之间间距过小而难以脱模的问题,设计第一扇叶体130及第二扇叶体140的制作模具时,可使任两相邻第一叶片134之间或任两相邻第二叶片144之间的间距拉大。但在组装第一扇叶体130及第二扇叶体140后,风扇模块100也能具有密集的风扇叶片。换言之,风扇模块100便能具有更多数量的风扇叶片。叶片数量多,风扇模块100的出风量较大,散热效果也较好。第一凸台138以及第一对位部131设置于第一环状结构132的顶面132a,即第一扇叶体130面对第二扇
叶体140的表面。有关第一凸台138以及第一对位部131,将在下文有更详细的描述。
[0024]
第二扇叶体140还包含多个第二容置槽146(图中仅示例性地标示一个)、多个第二凸台148与多个第二对位部141与肋条143。在此举三个第二凸台148、两个第二对位部141(有些第二凸台148及第二对位部141因角度关系,故未示于图中)为例进行说明。类似地,第二容置槽146形成于第二环状结构142的外缘。每个第二容置槽146设置于相邻两个第二叶片144之间。当第二扇叶体140套设于轮毂110外时,第二容置槽146可用以容纳第一叶片134,以使第一叶片134与第二叶片144更加密合。第二凸台148以及第二对位部141设置于第二环状结构142的底面142a,即第二扇叶体140面对第一扇叶体130的表面。肋条143设置于第二扇叶体140的内壁142b,并朝第二环状结构142所围成的内部空间突出。有关肋条143、第二凸台148以及第二对位部141,将在下文有更详细的描述。
[0025]
请参照图4a以及图4b。图4a为图1中的风扇模块100沿线段4-4的剖面图。图4b为图1中的第二扇叶体140的俯视图。如图4a所示,当第二扇叶体140套设于轮毂110外时,第二扇叶体140的肋条143与轮毂110的外壁110a抵接。在本实施方式中,肋条143的数量有三个,但本发明不应以此为限。换言之,肋条143的数量可视实际操作情况而弹性调整。
[0026]
由于扇叶体多为塑料成型的方式所制成。然而,塑料成型的零件于制造过程中多少会有收缩、变形的现象,因此,在尺寸的控制上,塑料成型的零件的尺寸精准度不容易达到预期的要求,因而影响了零件组装时的精准度及风扇运转时的平稳度。因此,本发明通过肋条143的设置,即能忽略第二环状结构142于制造时真圆尺寸上精确度的问题,以确保第一扇叶体130以及第二扇叶体140组合后的同心度。
[0027]
具体而言,三个肋条143实质上是平均分布设置于第二环状结构142的内壁142b,但本发明不应以此为限。当第二扇叶体140套设于轮毂110上时,在垂直于中心轴c的剖面(如图4a所示的剖面)上,三个肋条143至中心轴c的距离l1、l2、l3实质上相等。换言之,三肋条143可形成一个虚拟的内切圆r(如图4b所示)。内切圆r的圆心i与中心轴c实质上重合。因此,三个肋条143至中心轴c的距离l1、l2、l3实质上即为内切圆r的半径。第一扇叶体130的第一环状结构132与轮毂110连接。因此,第一环状结构132的环心实质上是与中心轴c重合。也就是说,当第二扇叶体140套设于轮毂110上时,与三肋条143形成的内切圆r的圆心i及第一环状结构132的环心实质上是在平行中心轴c的方向上重合。
[0028]
在本发明中,“实质上”的意思意旨允许些微公差,例如约5%以内。本发明不应以此为限。
[0029]
如上述结构设计,制造、设计第二扇叶体140时,只要调整三肋条143的尺寸,使得与三肋条143内切的内切圆r的圆心i能与中心轴c重合,即能确保组装时第一扇叶体130与第二扇叶体140的同心度,以避免因扇叶体组装后中心位置不一致而导致风扇旋转不稳定的问题。此外,轮毂110与第二环状结构142的内壁142b之间会保有间隙g1。间隙g1在组装时可作为排气及填充固定用胶的容置空间。良好的排气及胶的容置空间可助于改善结构挤压变形的问题。
[0030]
在一些实施方式中,肋条143与轮毂110的外壁110a的抵接面可以是平面、凹弧面或凸弧面。在其他实施方式中,肋条143与轮毂110的外壁110a仅抵接于接触线或接触面。举例而言,肋条143与轮毂110的外壁110a的抵接面是凸弧面,且肋条143的凸弧面与轮毂110的外壁110a正切,使得肋条143与轮毂110的外壁110a仅抵接于接触线,但本发明不应以此
为限。
[0031]
请参照图5。图5为图1中的风扇模块100的局部示意图。具体而言,图5为第一凸台138、第二凸台148、第一对位部131以及第二对位部141的局部放大图。为了方便说明起见,图中是以平面的方式描绘第一环状结构132以及第二环状结构142,但本发明不应以图5所示为限。在下文中仅以一第一凸台138、第二凸台148、第一对位部131以及第二对位部141为例说明,然而其余第一凸台138、第二凸台148、第一对位部131以及第二对位部141也可参照下文说明。
[0032]
如图5所示,第一凸台138朝第二扇叶体140凸出。第二凸台148朝第一扇叶体130凸出。每个第一凸台138具有第一平面138a。第一平面138a面对第二扇叶体140。第一平面138a实质上平行第一环状结构132的顶面132a,且三个第一凸台138的三个第一平面138a实质上共平面。第二凸台148具有第二平面148a面对第一扇叶体130。第二平面148a实质上平行第二环状结构142的底面142a,且三个第二凸台148的三个第二平面148a实质上共平面。三个第一凸台138与三个第二凸台148对应设置。当第二扇叶体140套设于轮毂110上时,三个第一平面138a与对应的第二平面148a抵接。
[0033]
一般而言,塑料零件成形时会有收缩、变形的现象。因此,实际上第一环状结构132的顶面132a以及第二环状结构142的底面142a并非理想的平面。如此,在组装时容易造成上下扇叶体元件的歪斜。因此,通过第一凸台138以及第二凸台148的设置,仅需调整第一平面138a与第二平面148a的平整度,使多个第一平面138a或多个第二平面148a彼此共平面,再通过第一平面138a与第二平面148a抵接接触,即能克服顶面132a、底面142a凹凸不平整的问题,以确保组装后第一扇叶体130以及第二扇叶体140之间贴合的平整度。此外,由于第一凸台138与第二凸台148分别相对第一环状结构132的顶面132a及第二环状结构142的底面142a凸出,并互相抵接,因此,第一环状结构132的顶面132a及第二环状结构142的底面142a之间具有间隙g2。间隙g2在组装时可作为排气及填充固定用胶的容置空间。良好的排气及胶的容置空间可助于改善结构挤压变形的问题。
[0034]
在一些实施方式中,第一凸台138及第二凸台148的高度至少大于或等于顶面132a或底面142a上凹凸结构的最大高度。相关数据关联于制程所用的设备,在此并不加以限制。
[0035]
在本实施方式中,第一凸台138的宽度小于第二凸台148的宽度。于另一实施方式中,第一凸台138的宽度等于第二凸台148的宽度。在其他实施方式中,第一凸台138的宽度大于第二凸台148的宽度。本发明不应以此为限。
[0036]
在一些实施方式中,第一凸台138以及第二凸台148的数量及位置可视实际情况弹性调整,本发明不应以此为限。
[0037]
在一些实施方式中,多个第一平面138a的总面积约小于或等于顶面132a的面积的十分之一。多个第二平面148a的总面积也约小于或等于底面142a的面积的十分之一。本发明不应以此为限。
[0038]
请继续参照图5。如图5所示,第二对位部141设置于第二扇叶体140与第一对位部131对应的位置上。第一对位部131具有一个凹槽1312以及二个凸起1314,且凹槽1312位于二个凸起1314之间。凹槽1312相对第一环状结构132的顶面132a凹陷。二个凸起1314相对第一环状结构132的顶面132a凸出。进一步地,凹槽1312相对顶面132a的凹陷深度d1约等于二个凸起1314相对顶面132a的凸起高度h1。
[0039]
对应地,第二对位部141具有二个凹槽1412以及一个凸起1414,且凸起1414位于二个凹槽1412之间。二个凹槽1412相对第二环状结构142的底面142a凹陷。凸起1414相对第二环状结构142的底面142a凸出。凹槽1412相对底面142a的凹陷深度d2约等于二个凸起1414相对底面142a的凸起高度h2。进一步地,二个凹槽1412的凹陷深度d2大约等于二个凸起1314的凸起高度h1。凸起1414的凸起高度h2大约等于凹槽1312的凹陷深度d1。当第二扇叶体140叠合于第一扇叶体130上时,二个凹槽1412与二个凸起1314卡合,且凸起1414与凹槽1312卡合。
[0040]
组装时,通过第二对位部141与第一对位部131的卡合对位,可辅助导正第二扇叶体140以及第一扇叶体130于叶片的旋转方向上的叠合,以确保每个第二叶片144与每个第一叶片134之间的相对位置符合预期。此外,对于小尺寸的风扇而言,凹槽结构以及凸起结构的搭配设计,可在有限的结构空间内达到更明显有效的导引效果,使得风扇模块100于旋转方向上的组装对位更为精准。
[0041]
在一些实施方式中,第一对位部131包含一个凸起以及二个凹槽。对应地,第二对位部141包含两凸起以及一个凹槽,本发明不应以此为限。
[0042]
在一些实施方式中,第一对位部131及第二对位部141的形状以及数量可视实际操作情况而弹性调整,本发明不应以此为限。
[0043]
通过上述结构设计,本发明的多件式组合的风扇模块100在生产制造上可解决已知不能脱模的问题,以突破结构设计上的限制,使风扇模块100的尺寸更为缩小,以利电子产品的薄型化。此外,通过肋条143、第一凸台138、第二凸台148、第一对位部131以及第二对位部141的辅助对位、导引功能,可降低组装时的难度,并且提升组装的精准度,使风扇模块100可以达到良好的组装品质。进一步地,有别于已知转轴与塑料扇叶体连接的方式,在本实施方式中,转轴120与轮毂110一体成形地连接便可省略已知覆盖于轮毂110上承载转轴120的壳件。如此,有助于风扇模块100的薄型化。
[0044]
请参照图6a以及图6b。图6a为本发明另一实施方式的风扇模块200的分解图。图6b为图6a的风扇模块200的立体图。如图6a所示,在本实施方式中,风扇模块200包含轮毂110、转轴120、第一扇叶体230以及第二扇叶体240。第一扇叶体230包含第一环状结构232、多个第一叶片234、第一凸台138以及第一对位部131。第二扇叶体240包含第二环状结构242、多个第二叶片244、肋条143、第二凸台148以及第二对位部141。本实施方式中的轮毂110、转轴120、第一凸台138、第一对位部131、肋条143、第二凸台148以及第二对位部141皆与图1所示实施方式相同,因此可参照前述相关说明,在此不再赘述。本实施方式与图1所示的实施方式的差异处,在在本实施方式中,当第二扇叶体240套设于轮毂110外时,每个第二叶片244是与对应的第一叶片234叠合。换言之,第二叶片244是在平行于中心轴c的方向上与对应的第一叶片234对齐(如图6b所示)。
[0045]
在本实施方式中,因多个第一叶片234以及多个第二叶片244非环绕中心轴c交替排列,因此,前述实施方式中的第一容置槽136以及第二容置槽146可选择性地自第一环状结构232或第二环状结构242上省略。
[0046]
请参照图7a以及图7b。图7a为本发明又一实施方式的风扇模块300的分解图。图7b为图7a的风扇模块300的立体图。如图7a所示,在本实施方式中,风扇模块300包含轮毂110、转轴120、第一扇叶体230以及第二扇叶体340。第一扇叶体230包含第一环状结构232、多个
第一叶片234、第一凸台138以及第一对位部131。第二扇叶体340包含第二环状结构342、多个第二叶片244、肋条143、第二凸台148以及第二对位部141。本实施方式中的轮毂110、转轴120、第一环状结构232、第一凸台138、第一对位部131、第一叶片234、肋条143、第二凸台148、第二对位部141以及第二叶片244皆与第6a、6b图所示实施方式相同,因此可参照前述相关说明,在此不再赘述。本实施方式与第6a、6b图所示的实施方式的差异处,在在本实施方式中,风扇模块300还包含第三扇叶体350。第三扇叶体350套设于轮毂110外,叠合于第二扇叶体340之上(如图7b所示)。第三扇叶体350包含第三环状结构352、多个第三叶片354、第三凸台358、第三对位部351以及肋条353。
[0047]
类似于上述肋条143的结构设计,肋条353设置于第三环状结构352的内壁352b。相仿如前述,肋条353可用以辅助、调整第三扇叶体350于尺寸上真圆度的精准度,以确保第三扇叶体350与第一扇叶体130以及第二扇叶体340组合后的同心度。详细的设计及作用原理可参照前述肋条143的相关说明。
[0048]
第三凸台358以及第三对位部351设置在第三环状结构352的底面352a,即第三环状结构352面对第二扇叶体340的表面。对应地,第二环状结构342的顶面342c,即第二环状结构342面对第三扇叶体350的表面,设置有第四凸台348以及第四对位部341。当第三扇叶体350与第二扇叶体340套设于轮毂110外时,第三凸台358与第四凸台348抵接。第三对位部351与第四对位部341卡合。借此,可确保第二扇叶体340与第三扇叶体350之间贴合的平整度,以及第二扇叶体340与第三扇叶体350在风扇模块300旋转方向上的角度定位。由于第四凸台348、第三凸台358、第四对位部341以及第三对位部351与前述第一凸台138、第二凸台148、第一对位部131以及第二对位部141具有相同的构型及功能。因此,详细的设计及作用原理可参照前述第一凸台138、第二凸台148、第一对位部131以及第二对位部141的相关说明,在此不再赘述。
[0049]
在本实施方式中,当第三扇叶体350与第二扇叶体340套设于轮毂110外时,第一叶片234、第二叶片244以及第三叶片354是在平行于中心轴c的方向上对齐并叠合,如图7b所示。
[0050]
在一些实施方式中,第一叶片234、第二叶片244以及第三叶片354是环绕中心轴c交替排列,此实施例不应以此为限。
[0051]
在一些实施方式中,扇叶体的数量可为二个或二个以上,本发明不应以此为限。
[0052]
由以上对于本发明的具体实施方式的详述,可以明显地看出,本发明的风扇模块是将风扇转子叶片结构分拆成两个以上的元件,以利于各个叶片分别脱模生产。接着,再通过组装的方式,将这些分拆的扇叶体组合成预期的扇叶转子结构。如此,可克服生产制造时脱模的问题,减少扇叶结构设计上的限制。此外,在多个扇叶体上设置有肋条、凸台以及对位部等辅助对位结构。通过上述肋条、凸台以及对位部的辅助,组装风扇模块时,可有效提升多个扇叶体之间的对位精准度,以确保扇叶体组装后同心度的一致、扇叶体之间贴合的平整度,以及扇叶在旋转方向的角度定位。
[0053]
虽然本发明已以实施例公开如上,然其并非用以限定本发明,任何本领域技术人员,在不脱离本发明的精神和范围内,当可作些许的更动与润饰,故本发明的保护范围当视权利要求书所界定的为准。