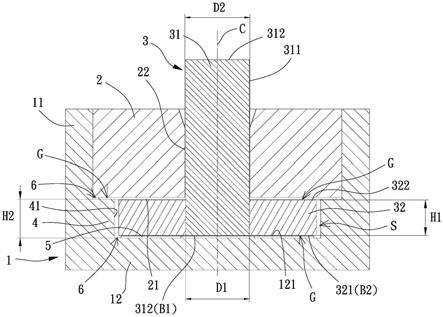
[0001]
本发明是关于一种马达或风扇的构件,尤其是一种可安装于马达或风扇中的轴承系统。
背景技术:[0002]
请参照图1,其是一种现有的风扇9,该现有的风扇9具有一轴座91、一轴承系统92、一转子93及一定子94。该轴承系统92具有一轴筒921组装结合于该轴座91,一含油轴承922组装在该轴筒921内部,一密封塞923封闭该轴筒921的底部,一耐磨垫924设于该密封塞923内。该转子93具有一轴杆931贯穿该含油轴承922,该轴杆931的底端抵接该耐磨垫924,该轴杆931外周面结合有一扣片932,该扣片932位于该含油轴承922下方,该轴杆931顶端结合有一轮毂933,该轮毂933的外周面连接有多个扇叶934,该轮毂933的内周面则连接有一磁性件935。该定子94结合于该轴筒921的外周并与该磁性件935径向相对,以驱动该转子93旋转。类似于该现有的风扇9的一实施例已公开于中国台湾公告第m247713号专利案当中。
[0003]
上述现有的风扇9运作时,其轴杆931若有向上飘移的现象,将可借由该扣片932挡在该含油轴承922底端而限制该轴杆931的轴向位移;但是,该扣片932会反复碰撞该含油轴承922底端,使该转子93的旋转因振动而不平稳,同时也会产生噪音。
[0004]
有鉴于此,现有风扇的轴承系统确实仍有加以改善的必要。
技术实现要素:[0005]
为解决上述问题,本发明的目的是提供一种轴承系统,可限制转轴的轴向位移,并大幅减少转轴碰撞轴承的轴向端面的状况。
[0006]
本发明的次一目的是提供一种轴承系统,其转轴的底部可以维持腾空而不摩擦其他构件。
[0007]
本发明的又一目的是提供一种轴承系统,其转轴与轴承之间可以产生更平均的油膜。
[0008]
本发明的再一目的是提供一种轴承系统,可以简化所需组装的构件,以提升组装便利性及效率。
[0009]
本发明全文所述方向性或其近似用语,例如“前”、“后”、“左”、“右”、“上(顶)”、“下(底)”、“内”、“外”、“侧面”等,主要是参考附图的方向,各方向性或其近似用语仅用以辅助说明及理解本发明的各实施例,非用以限制本发明。
[0010]
本发明全文所记载的元件及构件使用“一”或“一个”的量词,仅是为了方便使用且提供本发明范围的通常意义;于本发明中应被解读为包括一个或至少一个,且单一的概念也包括复数的情况,除非其明显意指其他意思。
[0011]
本发明全文所述“结合”、“组合”或“组装”等近似用语,主要包括连接后仍可不破坏构件地分离,或是连接后使构件不可分离等型态,本领域中普通技术人员可以依据欲相连的构件材质或组装需求予以选择。
[0012]
本发明的轴承系统,包括:一第一轴承,内部中空而具有一第一内表面;一第二轴承,位于该第一轴承内部,该第二轴承具有一第二内表面与该第一内表面轴向相对,且该第二内表面与该第一内表面之间形成一间隔空间;及一转动件,具有一外凸部连接一转轴,该外凸部位于该间隔空间中,该外凸部能够在转动时分别与该第一内表面及该第二内表面之间形成一动压间隙。
[0013]
由此,本发明的轴承系统,其转动件旋转时,可以在该外凸部与该两个轴承之间分别因动压而产生一油膜,不仅能让转轴维持顺畅旋转,还能由该油膜抑制转轴的轴向位移,及防止该外凸部碰撞该两个轴承,故可有效减少运作噪音及振动,具有提升装有该轴承系统的风扇或马达品质的功效。
[0014]
该轴承系统可以另外包括一支撑部,该支撑部位于该第一内表面与该第二内表面之间,以于该第一内表面、该第二内表面与该支撑部的一内周面之间形成该间隔空间。如此,可以由该支撑部准确控制该间隔空间的大小,具有提升组装便利性及产品合格率等功效。
[0015]
其中,该转轴贯穿该第二轴承的一轴孔,该第一轴承具有一环墙连接一轴向端部,该第一内表面位于该轴向端部并朝向该轴孔,该支撑部可以一体连接该第一内表面并供该第二内表面抵接,或是该支撑部可以一体连接该第二内表面并抵接该第一内表面。如此,将该第二轴承组装入该第一轴承内部时,只要压抵该第二轴承至该支撑部抵接该第一内表面或该第二内表面,即可确保该间隔空间符合预定尺寸,且需组装的构件极少,具有提升组装便利性及效率等功效。
[0016]
其中,该转轴的外径较佳略小于该轴孔的孔径。如此,具有提升该转轴的旋转顺畅度等功效。
[0017]
其中,该第一轴承的第一内表面可以凹设有一容槽,该容槽连通该间隔空间,该转轴的底部可以伸入该容槽且维持腾空而不接触该容槽的一底面。如此,该转轴转动时将不会摩擦到该容槽的底面,具有提升转轴旋转顺畅度、降低运作噪音及延长轴承系统使用寿命等功效。
[0018]
其中,该转轴的外径小于该容槽的径宽。如此,具有提升该转轴的旋转顺畅度等功效。
[0019]
其中,该第一轴承具有一环墙连接一轴向端部,该第一内表面位于该轴向端部,一轴孔设于该轴向端部并贯穿该第一内表面,该转轴贯穿该轴孔,该支撑部可以一体连接该第一内表面并供该第二内表面抵接,或是该支撑部可以一体连接该第二内表面并抵接该第一内表面。如此,将该第二轴承组装入该第一轴承内部时,只要压抵该第二轴承至该支撑部抵接该第一内表面或该第二内表面,即可确保该间隔空间符合预定尺寸,且需组装的构件极少,具有提升组装便利性及效率等功效。
[0020]
其中,该转轴的外径小于该轴孔的孔径。如此,具有提升该转轴的旋转顺畅度等功效。
[0021]
其中,该第二轴承可以具有一容槽凹设于该第二内表面,该容槽连通该间隔空间,该转轴的底部可以伸入该容槽且维持腾空而不接触该容槽的一底面。如此,该转轴转动时将不会摩擦到该容槽的底面,具有提升转轴旋转顺畅度、降低运作噪音及延长轴承系统使用寿命等功效。
[0022]
其中,该转轴的外径小于该容槽的径宽。如此,具有提升该转轴的旋转顺畅度等功效。
[0023]
其中,该转轴的底部可以与该外凸部的底端齐平。如此,具有简化结构以便制造的功效。
[0024]
其中,该转轴具有一环周面及两个端面,该外凸部可以对位在该转轴的两个端面之间。如此,具有提升该转动件的旋转稳定度的功效。
[0025]
其中,该第一轴承具有一环墙,该第二轴承可以紧配结合该第一轴承的环墙。如此,具有提升结合稳固性的功效。
[0026]
其中,该第一轴承具有一环墙,该第二轴承可以雷射焊接结合该环墙。如此,具有提升结合稳固性的功效。
[0027]
其中,该外凸部可以一体连接该转轴的一环周面,并自该环周面呈径向朝外延伸。如此,该外凸部在该转轴的环周面上的位置可维持固定不变,能够降低组装误差或后续相对位移而对油膜形成效果所造成的影响,具有提升轴承系统的运作稳定度的功效。
[0028]
其中,该外凸部可以结合于该转轴的一环周面,并自该环周面呈径向朝外延伸。如此,具有提升制造及组装便利性的功效。
[0029]
其中,该外凸部可以雷射焊接结合该转轴的环周面。如此,具有提升结合稳固性的功效。
[0030]
其中,该第一轴承与该第二轴承的材质可以为磷青铜合金。如此,该第一轴承与该第二轴承将具有足够的结构强度而可以直接与风扇的基座结合,且不会渗漏润滑油的现象,具有简化构件而提升组装便利性及效率等功效。
[0031]
其中,该外凸部可以呈盘状以完整圈围该转轴的一环周面。如此,该外凸部与该第一轴承及该第二轴承之间所产生的油膜可更为平均,具有提升转轴旋转顺畅度的功效。
[0032]
其中,该外凸部具有一第一轴向表面与该第一轴承的第一内表面相对,该第一内表面及该第一轴向表面中的至少一个可以凹设有多个动压沟,该外凸部具有一第二轴向表面与该第二轴承的第二内表面相对,该第二内表面及该第二轴向表面中的至少一个可以凹设有另外多个动压沟。如此,具有更进一步地提升该轴承系统运作时所产生的动压效果的功效。
[0033]
该轴承系统可以另外包括一环沟,该环沟位于该多个动压沟的外周并与该多个动压沟连通。如此,具有提升润滑油的循环顺畅度的功效。
附图说明
[0034]
图1:一种现有风扇的剖视结构图;图2:本发明第一实施例的分解立体图;图3:本发明第一实施例的组合剖视图;图4:本发明第二实施例的分解立体图;图5:本发明第二实施例的组合剖视图;图6:本发明其他实施例呈现支撑部连接于第二轴承的组合剖视图;图7:本发明第三实施例的组合剖视图;图8:本发明的另一形式转轴的立体图。
[0035]
附图标记说明1
ꢀꢀꢀꢀꢀꢀꢀꢀꢀꢀꢀꢀ
第一轴承11
ꢀꢀꢀꢀꢀꢀꢀꢀꢀꢀꢀ
环墙12
ꢀꢀꢀꢀꢀꢀꢀꢀꢀꢀꢀ
轴向端部121
ꢀꢀꢀꢀꢀꢀꢀꢀꢀꢀ
第一内表面13
ꢀꢀꢀꢀꢀꢀꢀꢀꢀꢀꢀ
轴孔14
ꢀꢀꢀꢀꢀꢀꢀꢀꢀꢀꢀ
容槽141
ꢀꢀꢀꢀꢀꢀꢀꢀꢀꢀ
底面2
ꢀꢀꢀꢀꢀꢀꢀꢀꢀꢀꢀꢀ
第二轴承21
ꢀꢀꢀꢀꢀꢀꢀꢀꢀꢀꢀ
第二内表面22
ꢀꢀꢀꢀꢀꢀꢀꢀꢀꢀꢀ
轴孔23
ꢀꢀꢀꢀꢀꢀꢀꢀꢀꢀꢀ
容槽231
ꢀꢀꢀꢀꢀꢀꢀꢀꢀꢀ
底面3
ꢀꢀꢀꢀꢀꢀꢀꢀꢀꢀꢀꢀ
转动件31
ꢀꢀꢀꢀꢀꢀꢀꢀꢀꢀꢀ
转轴311
ꢀꢀꢀꢀꢀꢀꢀꢀꢀꢀ
环周面312
ꢀꢀꢀꢀꢀꢀꢀꢀꢀꢀ
端面32
ꢀꢀꢀꢀꢀꢀꢀꢀꢀꢀꢀ
外凸部321
ꢀꢀꢀꢀꢀꢀꢀꢀꢀꢀ
第一轴向表面322
ꢀꢀꢀꢀꢀꢀꢀꢀꢀꢀ
第二轴向表面4
ꢀꢀꢀꢀꢀꢀꢀꢀꢀꢀꢀꢀ
支撑部41
ꢀꢀꢀꢀꢀꢀꢀꢀꢀꢀꢀ
内周面5
ꢀꢀꢀꢀꢀꢀꢀꢀꢀꢀꢀꢀ
动压沟6
ꢀꢀꢀꢀꢀꢀꢀꢀꢀꢀꢀꢀ
环沟b1
ꢀꢀꢀꢀꢀꢀꢀꢀꢀꢀꢀ
底部b2
ꢀꢀꢀꢀꢀꢀꢀꢀꢀꢀꢀ
底端c
ꢀꢀꢀꢀꢀꢀꢀꢀꢀꢀꢀꢀ
旋转轴线d1
ꢀꢀꢀꢀꢀꢀꢀꢀꢀꢀꢀ
外径d2、d3
ꢀꢀꢀꢀꢀꢀꢀꢀ
孔径d4、d5
ꢀꢀꢀꢀꢀꢀꢀꢀ
径宽g
ꢀꢀꢀꢀꢀꢀꢀꢀꢀꢀꢀꢀ
动压间隙h1、h2
ꢀꢀꢀꢀꢀꢀꢀꢀ
轴向高度s
ꢀꢀꢀꢀꢀꢀꢀꢀꢀꢀꢀꢀ
间隔空间﹝现有技术﹞9
ꢀꢀꢀꢀꢀꢀꢀꢀꢀꢀꢀꢀ
风扇91
ꢀꢀꢀꢀꢀꢀꢀꢀꢀꢀꢀ
轴座92
ꢀꢀꢀꢀꢀꢀꢀꢀꢀꢀꢀ
轴承系统921
ꢀꢀꢀꢀꢀꢀꢀꢀꢀꢀ
轴筒922
ꢀꢀꢀꢀꢀꢀꢀꢀꢀꢀ
含油轴承
923
ꢀꢀꢀꢀꢀꢀꢀꢀꢀꢀ
密封塞924
ꢀꢀꢀꢀꢀꢀꢀꢀꢀꢀ
耐磨垫93
ꢀꢀꢀꢀꢀꢀꢀꢀꢀꢀꢀ
转子931
ꢀꢀꢀꢀꢀꢀꢀꢀꢀꢀ
轴杆932
ꢀꢀꢀꢀꢀꢀꢀꢀꢀꢀ
扣片933
ꢀꢀꢀꢀꢀꢀꢀꢀꢀꢀ
轮毂934
ꢀꢀꢀꢀꢀꢀꢀꢀꢀꢀ
扇叶935
ꢀꢀꢀꢀꢀꢀꢀꢀꢀꢀ
磁性件94
ꢀꢀꢀꢀꢀꢀꢀꢀꢀꢀꢀ
定子。
具体实施方式
[0036]
为使本发明的上述及其他目的、特征及优点能更明显易懂,下文特根据本发明的较佳实施例,并配合附图,作详细说明如下:请参照图2、3所示,其是本发明轴承系统的第一实施例,包括一第一轴承1、一第二轴承2及一转动件3,该第二轴承2位于该第一轴承1内,该转动件3可相对于该第一轴承1与该第二轴承2旋转。
[0037]
该第一轴承1具有一环墙11连接一轴向端部12,使该第一轴承1概形成内部中空的杯状而可容置该第二轴承2。在本实施例中,该轴向端部12可以位于该环墙11的底侧,并与该环墙11一体成型相连接,使该第一轴承1的底端可完全封闭以有效避免该第一轴承1内的润滑油渗漏。其中,该轴向端部12具有一第一内表面121,该第一内表面121可以朝向该环墙11的顶端。
[0038]
该第二轴承2位于该第一轴承1内部,该第二轴承2具有一第二内表面21与该第一内表面121轴向相对,并于该第二内表面21与该第一内表面121之间形成一间隔空间s。其中,该第二轴承2可以紧配结合该第一轴承1的环墙11,且较佳在相接处的外端予以雷射焊接。更进一步地,本实施例的轴承系统还可以另外包括一支撑部4,该支撑部4位于该第一内表面121与该第二内表面21之间,用以间隔该第一内表面121与该第二内表面21,使该第二轴承2组装入该第一轴承1内部后,该第二内表面21可与该第一内表面121保持预定间距,从而达到提升组装便利性及准确控制该间隔空间s的大小等效果。
[0039]
具体而言,该支撑部4可以一体连接该第一内表面121,并凸出于该第一内表面121之上,组装该第二轴承2时,只要压抵该第二轴承2至该第二内表面21抵接于该支撑部4,即可限制该第二轴承2的结合深度,并于该第一内表面121、该第二内表面21与该支撑部4的一内周面41之间形成前述的间隔空间s,同时确保该间隔空间s符合预定尺寸,且需组装的构件极少而可快速完成组装。在其他实施例中,也可以与前述设置相反,使该支撑部4一体连接该第二内表面21,并于组装该第二轴承2时,由该支撑部4抵接该第一内表面121;或者,该支撑部4还可以拆成两部分,一部分一体连接该第一内表面121,另一部分一体连接该第二内表面21,并于组装时相对抵接,均可达到上述效果。
[0040]
此外,本实施例的第二轴承2可以具有贯穿状的一轴孔22,以由该轴孔22连通该间隔空间s与外部。其中,该轴孔22贯穿该第二内表面21并朝向该第一内表面121;较佳地,该轴孔22至少有局部沿轴向呈由下往上渐扩的形态,使得不慎溢流至该轴孔22的润滑油较不
易继续朝外部流出。
[0041]
该转动件3具有可受驱动旋转的一转轴31,该转轴31具有一环周面311及两个端面312,该转轴31可以贯穿该第二轴承2的轴孔22,且该转轴31的其中一端面312位于该第一轴承1外部,该转轴31的另一端面312则位于该第一轴承1内部;其中,该转轴31的外径d1较佳略小于该轴孔22的孔径d2,以提升该转轴31的旋转顺畅度。该转动件3具有一外凸部32连接该转轴31并位于该间隔空间s中,该转轴31可带动该外凸部32同步旋转;在本实施例中,该外凸部32可以连接于该转轴31的环周面311,且该外凸部32概呈自该环周面311径向朝外延伸地设于该间隔空间s中,使该外凸部32具有相对的一第一轴向表面321及一第二轴向表面322,该第一轴向表面321与该第一轴承1的第一内表面121相对,该第一轴向表面322与该第二轴承2的第二内表面21相对,第二轴承的第二内表面。本发明不限制该外凸部32的形态,该外凸部32的轴向高度h1小于该间隔空间s的轴向高度h2,并以该外凸部32能够在转动时分别与该第一内表面121及该第二内表面21之间形成一动压间隙g为原则;本实施例的外凸部32可选择设为盘状,以完整圈围该转轴31的环周面311。
[0042]
在具有前述支撑部4的实施例中,该外凸部32应与该支撑部4的内周面41相间隔以维持不接触,避免影响该转动件3的旋转顺畅度。此外,该外凸部32可以一体成型连接于该转轴31的环周面311(如图7所示),或例如以雷射焊接或紧配结合等方式结合于该转轴31的环周面311,本发明也不加以限制。另外地,本实施例的转动件3,可选择设为使该转轴31的底部b1与该外凸部32的底端b2齐平的形态;也即,该转轴31位于该第一轴承1内部的端面312可以与该外凸部32的第一轴向表面321共平面,使该转动件3概呈倒t形。
[0043]
为能更进一步地提升该轴承系统运作时所产生的动压效果,还可选择在该第一内表面121及该第一轴向表面321中的至少一个凹设有多个动压沟5,另外在该第二内表面21及该第二轴向表面322中的至少一个凹设有另外多个动压沟5;例如,本实施例可选择使该第一轴承1的第一内表面121及该第二轴承2的第二内表面21分别具有多个动压沟5,但不以此为限。
[0044]
详言之,位于同一表面上的该多个动压沟5可选择以该转轴31的旋转轴线c为中心呈放射状分布,或选择沿一参考圆的切线延伸形成,该多个动压沟5可以呈同向的弯弧状,且各动压沟5的深度约为0.02-0.04 mm。其中,该轴承系统较佳另外具有一环沟6位于该多个动压沟5的外周并与该多个动压沟5连通,以提升润滑油的循环顺畅度。设于该第二内表面21的该多个动压沟5则可以连通或不连通至该轴孔22,另外也可以具有一环沟6位于设在该第二内表面21的该多个动压沟5的外周并与该多个动压沟5连通。
[0045]
根据前述结构,将上述的轴承系统应用于一风扇中时,该第一轴承1可以结合于一扇框,一定子设于该第一轴承的外周,一扇轮则结合于该转动件3的转轴31。该风扇运作时,该定子可以驱动该扇轮旋转,从而连动该转动件3相对于该第一轴承1及该第二轴承2旋转。在该转动件3旋转的过程中,位于该外凸部32与该第一内表面121之间的动压间隙g中的润滑油可产生一油膜,位于该外凸部32与该第二内表面21之间的动压间隙g中的润滑油可产生另一油膜,使该转动件3可维持顺畅旋转,并由两个油膜防止该外凸部32碰撞该第一轴承1或该第二轴承2,故本实施例的轴承系统运作时,不易有碰撞该第一轴承1或该第二轴承2所产生的噪音及振动。此外,该外凸部32与该第一内表面121之间所产生的动压,以及该外凸部32与该第二内表面21之间所产生的动压,均具有抑制该转轴31产生轴向位移的效果。
[0046]
值得一提的是,该第一轴承1与该第二轴承2可以是采用磷青铜合金车制而成的轴承,不但具有足够的结构强度,且相较于以金属粉末烧结而成的含油轴承,或称多孔质轴承(porous bearing),磷青铜轴承质密而不会有润滑油因毛细现象从内部往外部流动所造成的漏油现象。因此,本发明的轴承系统可以直接与风扇的基座结合,而不需在该第一轴承1与该第二轴承2的外部再设置硬质且可防漏油的衬套,具有简化构件而提升组装便利性及效率等功效。
[0047]
请参照图4、5所示,其是本发明轴承系统的第二实施例。在本实施例中,该第一轴承1的轴向端部12可以位于该环墙11的顶端,使该第一轴承1的底端呈开放状以便结合该第二轴承2。
[0048]
详言之,该第一轴承1的轴向端部12具有一第一内表面121,该第一内表面121可以朝向该环墙11的底侧。该第一轴承1具有一轴孔13设于该轴向端部12并贯穿该第一内表面121,以由该轴孔13连通该间隔空间s与外部;该转动件3的转轴31贯穿该轴孔13,使该外凸部32的第一轴向表面321得以朝向该第一内表面121;其中,该转轴31的外径d1较佳略小于该轴孔13的孔径d3,以提升该转轴31的旋转顺畅度。
[0049]
此外,该支撑部4可以一体连接该第一内表面121,并凸出于该第一内表面121之下,组装该第二轴承2时,只要压抵该第二轴承2至该第二内表面21抵接于该支撑部4,即可限制该第二轴承2的结合深度,并于该第一内表面121、该第二内表面21与该支撑部4的一内周面41之间形成前述的间隔空间s,同时确保该间隔空间s符合预定尺寸,且需组装的构件极少而可快速完成组装。在其他实施例中,也可以相反设置,使该支撑部4一体连接该第二内表面21,并于组装该第二轴承2时,由该支撑部4抵接该第一内表面121(如图6所示);或者,该支撑部4还可以拆成两部分,一部分一体连接该第一内表面121,另一部分一体连接该第二内表面21,并于组装时相对抵接。
[0050]
请再参照图4、5所示,本实施例的转动件3,可选择使该外凸部32对位在该转轴31的两个端面312之间,使该转动件3大概呈十字形。为此,本实施例的第二轴承2可以另外设有一容槽23,该容槽23凹设于该第二内表面22,且该容槽23连通该转动空间s;如此,即可由简易的结构,使该转轴31的底部b1可以伸入该容槽23,且该转轴31底部b1的端面312较佳维持腾空而不接触该容槽23的一底面231,使该转轴31转动时不会摩擦该底面231。其中,该转轴31的外径d1较佳略小于该容槽23的径宽d4,以提升该转轴31的旋转顺畅度。
[0051]
请参照图7所示,其是本发明轴承系统的第三实施例。在本实施例中,该第一轴承1的轴向端部12可以位于该环墙11的底侧,使该第一轴承1的顶端呈开放状以便结合该第二轴承2,且该转动件3也大概呈十字形。
[0052]
详言之,本实施例的支撑部4可以一体连接该第二内表面22,并凸出于该第二内表面22之下,组装该第二轴承2时,只要压抵该第二轴承2至该第一内表面121抵接于该支撑部4,即可限制该第二轴承2的结合深度,并于该第一内表面121、该第二内表面21与该支撑部4的内周面41之间形成前述的间隔空间s,同时确保该间隔空间s符合预定尺寸,且需组装的构件极少而可快速完成组装。另外地,本实施例的第一轴承1可以设有一容槽14,该容槽14凹设于该第一内表面121,且该容槽14连通该转动空间s;如此,该转轴31的底部b1可以伸入该容槽14,且该转轴31底部b1的端面312较佳维持腾空而不接触该容槽14的一底面141,使该转轴31转动时不会摩擦该底面141。其中,该转轴31的外径d1较佳略小于该容槽14的径宽
d5,以提升该转轴31的旋转顺畅度。
[0053]
请参照图8所示,在前述的各实施例中,也可以选择使该转动件3的外凸部32的第一轴向表面321及第二轴向表面322均设有多个动压沟5,而位于上端的多个动压沟5可以与位于下端的多个动压沟5轴向相对位或错位,本发明不加以限制。换言之,在前述的各实施例中,可以使该第一轴承1的第一内表面121、该第二轴承2的第二内表面21及该外凸部32的二轴向表面321都分别具有多个动压沟5。或者,也可以使该第一轴承1的第一内表面121及该第二轴承2的第二内表面21不具有该多个动压沟5,仅该外凸部32的第一轴向表面321及第二轴向表面322分别具有多个动压沟5。以上结构本领域普通技术人员可以依照需求选用与变更,故不以本发明的附图为限。其中,相较于对该第一轴承1的第一内表面121加工成型该多个动压沟5,在该外凸部32的第一轴向表面321加工成型该多个动压沟5更容易进行,可借以提升加工便利性及效率。
[0054]
综上所述,本发明的轴承系统,其转动件旋转时,可以在该外凸部与该两个轴承之间分别因动压而产生一油膜,不仅能让转轴维持顺畅旋转,还能由该两个油膜抑制转轴的轴向位移,及防止该外凸部碰撞该两个轴承,故可有效减少运作噪音及振动,具有提升装有该轴承系统的风扇或马达品质的功效。
[0055]
值得一提的是,本发明的轴承系统还可以预先完成组装,以便后续能快速地组装至风扇或马达的基座,并由其转动件的转轴结合风扇或马达的转子,以提升组装风扇或马达的效率。
[0056]
虽然本发明已利用上述较佳实施例进行说明,然其并非用以限定本发明,任何本领域技术人员在不脱离本发明的精神和范围之内,相对上述实施例进行各种更动与修改仍属本发明所保护的技术范畴,因此本发明的保护范围当视权利要求书为准。