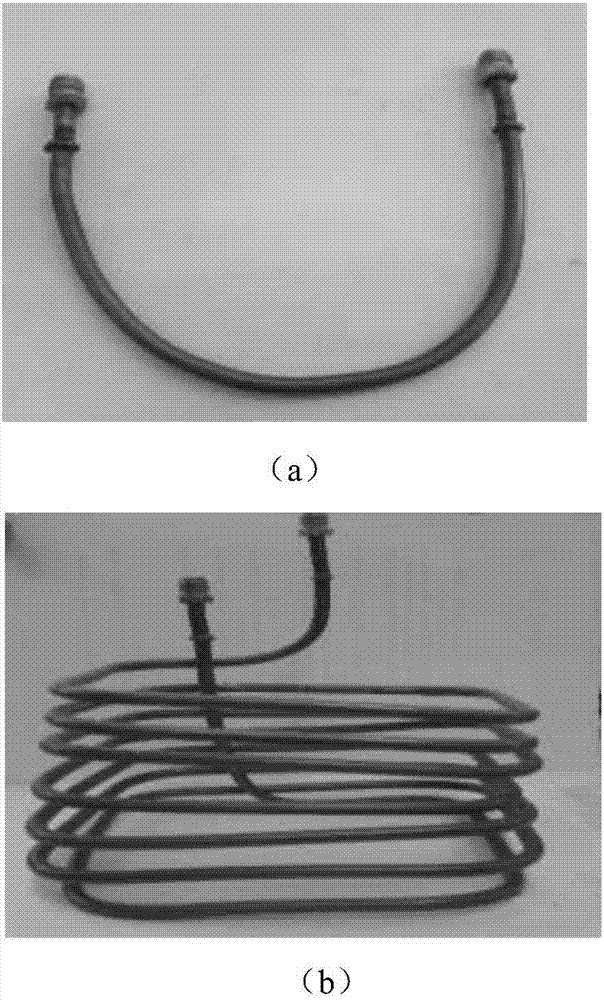
本发明涉及实验型微量液体加热装置领域,尤其是一种可用于微量液体样品加热的模拟uht处理系统及其应用。
背景技术:
:超高温瞬时灭菌(uht)是一种为达灭菌要求而升高液体温度为135-140℃,保温4-10s的杀菌工艺,整个灭菌过程是在高温状态下瞬间完成的,是鲜奶、谷物饮料、果汁等处理的一种常用灭菌工艺,灭菌后产品可在常温下保存,保质期可达1-6个月。目前市场上常温保存的液态产品如奶类、饮料类等食品几乎均采用uht杀菌工艺。实际生产中使用uht杀菌机进行液体的uht处理,但国内的uht杀菌机大多在企业的生产车间,其最大的特点是uht设备连续运转且设备处理量非常大。根据设备处理能力的不同分为大型、中试和小试uht设备,工厂一般为大型或中试uht灭菌机,小试uht处理机为实验室用。大型生产设备处理量高达5-6t/h,中试生产设备处理量为1.5-2t/h,即使实验室用小试设备处理量也要10-100l/h,小试uht设备相对较小,但实际操作时必须严格保证设备不能空转,因此单次进样量最少也要保证在5-10l左右。很多基础研究中经常涉及到不同的加热温度对产品稳定性、营养成分、风味、质构等的影响,而在进行此类研究时,样品量往往只需要很少,少至1升,甚至几百毫升。比如,实验材料为鲜奶时,为防止机器挤奶造成的奶样污染及影响,往往要求手工挤奶,因此多数情况下奶样数量不多。有的实验往往要综合考虑到对照组与实验组的设计以及各单因素对产品的性质、结构、风味等的影响,因此单个处理也只有几十毫升甚至几毫升的样品量。在样品量在几百毫升、几十毫升甚至几毫升这样微量的情况下,即使实验室用小型uht设备也很难完成uht处理。但从基础科学的角度又需要研究uht处理后样品的成分及结构变化以改进uht工艺使其更加适用于实际生产。而且,基础科学中研究加热温度和加热时间的影响时,往往需要根据样品性质和比对效果等安排不同的加热时间或加热温度,这就使得实验中可能会涉及到样品处理时采用任意加热温度或任意加热时间,而现今的加热杀菌设备并不能完全满足这项要求。此外目前实验室用微型uht杀菌机设备昂贵,在国内应用同样并不广泛,也使得处理样品极不方便。技术实现要素:针对上述现有技术的不足,发明人经过长期的技术与实践探索,结合uht杀菌机保持较高蒸汽压力及超高温状态以保证短时间快速杀菌的原理,提供一种基于微量液体样品加热的模拟uht处理系统,所述处理系统制备材料廉价易得,制备和使用方法简单,便于操作,将其应用于微量实验样品的uht处理可以大大简化实验,方便使用。具体的,本发明涉及以下技术方案:一种基于微量液体样品加热的模拟uht处理系统,所述处理系统由载液管、热源和降温源组成,所述热源为油浴锅,所述载液管管体由金属或合金制成,所述载液管主体两端设置有密封装置;所述降温源为冰浴锅;优选的,所述载液管管体呈u型管或盘状管;便于加热时固定,同时使待测液体在管内分布更为均匀;优选的,所述载液管管体的管壁厚度为0.1-1.5mm,进一步优选为0.7-0.8mm;所述管体外径为0.5-20mm,进一步优选为5-10mm;管体外径及管壁厚度的选择尤为重要,基于最大限度增大传热面积,使传热更为迅速之考虑,管体外径及管壁厚度应尽可能较小,然而由于所选载液管需要进行高温高压反应,加之承载待检的各种试样液体,金属或合金在此种环境下更易发生蠕变效应,从而因蠕变-断裂而失效;因此发明人通过不断试验摸索,最终确定上述管壁外径及厚度参数;优选的,所述金属或合金包括但不限于银、铜、金、铝、铁和不锈钢,进一步优选为铜,铜具有良好的热传导系数,在常用金属或合金材料中,其热传导系数极为突出,同时铜化学性质稳定,延展性好,具有良好的耐腐蚀能力;其轻便耐用,用其制备管体具有良好的导热效果。优选的,所述密封装置为单向阀,可起到良好的自密封效果;目前,单向阀主要使用在冷暖空调系统中,经常与毛细管配合使用;在制冷系统中,介质流经单向阀进入毛细管;在制热系统中,工况是逆向的,由于单向阀单向截止,它只能流入与单向阀并列的制热毛细管;本发明基于单向阀上述特点,因此在载液管管体两端采用单向阀的设计,其密封效果好;所述单向阀设置有密封盖,所述密封盖内设置有橡胶垫用于进一步进行密封;优选的,所述载液管管体两端设置有与管体密封连接的压力表和/或温度计,用以测定管体内部压力和温度,便于监控;进一步优选的,所述压力表和/或温度计上设置有紧固件(优选为螺母),便于与载液管密封连接;采用油浴加热的方式能够使得受热均匀,同时便于控制温度;其中,进一步优选的,所述油浴锅油浴介质为二甲基硅油,所述二甲基硅油无味、无毒、不易挥发,具有高导热性、耐高低温性、疏水性和热稳定性,发明人经过实验摸索,采用二甲基硅油介质同时使用上述铜制载液管能够最大程度模拟还原超高温瞬时灭菌,取得了良好的技术效果。优选的,所述降温源为冰浴锅,所述冰浴锅内为冰水混合物,其温度为0℃;经试验验证,加热处理完毕,把载液管迅速放入冰水混合物进行降温,可保证载液管内的样品于10s内降温至室温(20℃)以下,采用冰水混合物一方面是由于冰水混合物温度保持恒定,通过载液管的强大热交换效率,能够快速将微量液体样品降温冷却;另一方面发明人通过试验选用其他降温源,如液态水、冰盐水、液氮等,由于降温源温度过高或过低,无法满足试验要求,同时冰盐水、液氮等强制冷剂会强烈损害载液管结构性能,导致载液管易出现脆性破坏,严重影响载液管使用寿命。所述基于微量液体样品加热的模拟uht处理系统在模拟低温长时巴氏灭菌法(ltlt)、高温短时巴氏灭菌法(htst)、超高温巴氏杀菌法和超高温瞬时灭菌法(uht)灭菌工艺中的应用。具体的,所述应用方法,步骤如下:将待测液体注入模拟uht载液管中,加盖密封装置,置于热源中进行加热处理,加热处理完成后迅速置于降温源中进行降温处理;优选的,所述加热处理为油浴加热处理;所述降温源为为冰浴锅,所述冰浴锅内为冰水混合物;具体的,模拟低温长时巴氏灭菌法(ltlt,实际杀菌条件为62-65℃/30min),采用油浴处理,油浴处理温度为71℃,处理时间为32min;模拟高温短时巴氏灭菌法(htst,实际杀菌条件为75-90℃/15-40s),采用油浴处理,油浴处理温度为140℃,处理时间为30s;模拟超高温巴氏杀菌(实际杀菌条件120-125℃/4-15s),采用油浴处理,油浴处理温度为250℃,处理时间为18s;模拟超高温瞬时灭菌法(uht,实际杀菌条件135-140℃/4-15s),采用油浴处理,油浴处理温度为270℃,处理时间为20s。本发明有益效果:1.本发明通过合理选择管体材料,制备一种用于微量液体样品模拟uht的加热管,本发明本体的管体材料为铜,从热传导系数和成本等综合考量,最终选择铜作为管体材料。主体铜管的外径与材料厚度适宜,从而最大限度增大传热面积,使传热更为迅速,从而保证热交换效率最大化,实现待测液体样品的快速升温和降温,从而尽可能还原实际生产uht灭菌效果;2.本发明采用加液阀(单向阀)使管内空间密封,加热会使管内压力增大,进而使得管内样品沸点升高,样品的升温速度也随之增大。经试验验证,在管内空间中,样品可顺利升温至其常压沸点以上,因此即使对于常压沸点低于135℃的液体样品而言,此管也可以使其快速升温至135℃以上。如,常压下水的沸点为100℃,在非密封状态下其最高温度为100℃;在本发明的密封管中,压力的升高可以使水顺利升温至135℃及以上,因此,本发明可以对其进行模拟uht加热。3.本发明满足微量样品处理量的要求,单次处理量为3-50ml,操作简便,成本小。而传统的实验型uht设备单次进样量较大,操作复杂,设备昂贵,更加适合于企业的实际生产。本发明从样品处理量、操作和成本上进行优化,填补了现存的大型uht杀菌设备不适于进行微量液体样品处理的空白,为科学研究中微量液体样品的uht杀菌处理提供了便捷,实现了微量液体样品的uht处理,具有非常显著的实际应用性。4.本发明通过调整油浴温度和油浴时间,可以满足科学实验操作中涉及的任意加热时间及任意加热温度的要求。如,不同的油浴温度可以使管内液体在相同时间内分别达到65℃、85℃、105℃、125℃、135℃等梯度温度;同理也可以使管内液体达到相同温度(如125℃)所需时间呈梯度形式。因此,本发明可以处理一系列的不同加热温度及不同加热时间的样品进行科学研究,使科研实验设计更全面,分析结果更完善。5.本发明通过升高油浴温度以达到升温时间的缩短,使样品尽快达到理想温度,在理想温度范围内保持适宜时间,并采用冰水混合物进行降温,以保证载液管内的样品于10s内降温至室温(20℃)以下。由此更接近实际生产中相应的灭菌效果。附图说明图1为本申请u型载液管示意图;其中,1-加液阀,2-载液管管体;图2(a)为u型载液管实物图;图2(b)为盘状载液管实物图;图2(c)为加液阀细节展示图,其中a区域展示为加液阀螺纹结构;图3为设置在载液管上的压力表,其中图示b区域展示为紧固件螺帽结构,其能与图2(c)a区域进行螺栓连接;图4为设置在载液管上的温度计,其中图示c区域展示为温度计探测头,d区域展示为为紧固件螺帽结构,其能与图2(c)a区域进行螺栓连接;图5为实施例2升温曲线图;图6为实施例3升温曲线图;图7为实施例4升温曲线图;图8为实施例5升温曲线图;具体实施方式应该指出,以下详细说明都是例示性的,旨在对本申请提供进一步的说明。除非另有指明,本文使用的所有技术和科学术语具有与本申请所属
技术领域:
的普通技术人员通常理解的相同含义。需要注意的是,这里所使用的术语仅是为了描述具体实施方式,而非意图限制根据本申请的示例性实施方式。如在这里所使用的,除非上下文另外明确指出,否则单数形式也意图包括复数形式,此外,还应当理解的是,当在本说明书中使用术语“包含”和/或“包括”时,其指明存在特征、步骤、操作、器件、组件和/或它们的组合。正如
背景技术:
所介绍的,现有技术中尚不存在用于进行微量液体样品进行加热杀菌处理的设备;有鉴于此,本发明的一个具体实施方式中提供一种基于微量液体样品加热的模拟uht处理系统,所述处理系统由载液管、热源和降温源组成,所述热源为油浴锅,所述载液管管体由金属或合金制成,所述载液管主体两端设置有密封装置;所述降温源为冰浴锅;本发明的又一实施方式中,所述载液管管体呈u型管或盘状管;便于加热时固定,同时使待测液体在管内分布更为均匀;所述载液管管体的管壁厚度为0.1-1.5mm,进一步优选为0.7-0.8mm;所述管体外径为0.5-20mm,进一步优选为5-10mm;管体外径及管壁厚度的选择尤为重要,基于最大限度增大传热面积,使传热更为迅速之考虑,管体外径及管壁厚度应尽可能较小,然而由于所选载液管需要进行高温高压反应,加之承载待检的各种试样液体,金属或合金在此种环境下更易发生蠕变效应,从而因蠕变-断裂而失效;因此发明人通过不断试验摸索,最终确定上述管壁外径及厚度参数;本发明的又一实施方式中,所述金属或合金包括但不限于银、铜、金、铝、铁和不锈钢,进一步优选为铜,铜具有良好的热传导系数,在常用金属或合金材料中,其热传导系数极为突出,同时铜化学性质稳定,延展性好,具有良好的耐腐蚀能力;其轻便耐用,用其制备管体具有良好的导热效果。本发明的又一实施方式中,所述密封装置为单向阀,可起到良好的自密封效果;目前,单向阀主要使用在冷暖空调系统中,经常与毛细管配合使用;在制冷系统中,介质流经单向阀进入毛细管;在制热系统中,工况是逆向的,由于单向阀单向截止,它只能流入与单向阀并列的制热毛细管;本发明基于单向阀上述特点,因此在载液管管体两端采用单向阀的设计,其密封效果好;所述单向阀设置有密封盖,所述密封盖内设置有橡胶垫用于密封;本发明的又一实施方式中,所述载液管管体两端设置有与管体密封连接的压力表和/或温度计,用以测定管体内部压力和温度,便于监控;本发明的又一实施方式中,所述压力表和/或温度计上设置有紧固件(优选为螺母),便于与载液管密封连接;采用油浴加热的方式能够使得受热均匀,同时便于控制温度;其中,所述油浴锅油浴介质为二甲基硅油,所述二甲基硅油无味、无毒、不易挥发,具有高导热性、耐高低温性、疏水性和热稳定性,发明人经过实验摸索,采用二甲基硅油介质同时使用上述铜制载液管能够最大程度模拟还原超高温瞬时灭菌,取得了良好的技术效果。本发明的又一实施方式中,所述降温源为冰浴锅,所述冰浴锅内为冰水混合物,其温度在0℃;经试验验证,加热处理完毕,把载液管迅速放入冰水混合物进行降温,可保证载液管内的样品于10s内降温至室温(20℃)以下。本发明的又一实施方式中,提供所述基于微量液体样品加热的模拟uht处理系统在模拟低温长时巴氏灭菌法(ltlt)、高温短时巴氏灭菌法(htst)、超高温巴氏杀菌法和超高温瞬时灭菌法(uht)灭菌工艺中的应用。具体的,所述应用方法,步骤如下:将待测液体注入模拟uht载液管中,加盖密封装置加盖密封装置和/或温度计和/或压力表,置于热源中进行加热处理,而后置于降温源中快速降温;优选的,所述加热处理为油浴加热处理;所述降温源为冰浴锅,所述冰浴锅内为冰水混合物;具体的,模拟低温长时巴氏灭菌法(ltlt,实际杀菌条件为62-65℃/30min),采用油浴处理,油浴处理温度为71℃,处理时间为32min;模拟高温短时巴氏灭菌法(htst,实际杀菌条件为75-90℃/15-40s),采用油浴处理,油浴处理温度为140℃,处理时间为30s;模拟超高温巴氏杀菌(实际杀菌条件120-125℃/4-15s),采用油浴处理,油浴处理温度为250℃,处理时间为18s;模拟超高温瞬时灭菌法(uht,实际杀菌条件135-140℃/4-15s),采用油浴处理,油浴处理温度为270℃,处理时间为20s。需要说明的是,当今使用的食品杀菌程序种类繁多,不同种类的食品采用的杀菌工艺也不尽相同。综合考虑杀菌工艺的杀菌效果、对食品质量的影响以及杀菌工艺本身的实施性,生产上常采用低温长时巴氏灭菌法(ltlt)、高温短时巴氏灭菌法(htst)、超高温巴氏杀菌法和超高温瞬时灭菌法(uht)这四种灭菌工艺。基于此,为了使科学研究具有科研价值和应用价值并能够进一步指导生产,科研工作者在进行不同杀菌工艺对食品性质、结构的影响的研究时,多参考实际生产中的灭菌工艺进行样品热处理,生产中的常用灭菌工艺及加热条件见表1。表1实际生产中常用的杀菌工艺条件生产灭菌工艺加热条件低温长时巴氏灭菌法(ltlt)62-65℃/30min高温短时巴氏灭菌法(htst)75-90℃/15-40s超高温巴氏杀菌120-125℃/4-15s超高温瞬时灭菌法(uht)135-140℃/4-15s下面通过具体实例对本发明进行进一步的阐述,应该说明的是,下述说明仅是为了解释本发明,并不对其内容进行限定。实施例1:不同油浴温度条件下温升曲线的探索材料及设备:液体样品(鲜奶)35ml,注射器,模拟uht加热载液管(载液管管体的管壁厚度为0.8mm;所述管体外径为10mm,盘状管,最大载液量50ml),温度计,扳手,油浴锅(内置二甲基硅油)和冰浴锅(内置冰水混合物)。操作方法如下:(1)用注射器将液体样品缓缓注入模拟uht加热载液管中,加热管一端拧上单向阀,另一头拧上温度计并用扳手拧紧防止漏气,置于某相应温度的油浴锅中加热。(2)加热过程中,每隔5s测一次温度并记录,若油浴温度不合适则根据实际情况进行调整,直至满足条件为止。(3)根据记录的温度,绘制升温曲线图。实施例2:62-65℃/30min处理时油浴温度的探索材料及操作方法同实施例1。操作时温度保持在60℃-68℃范围即可。根据记录的温度,绘制升温曲线图,见图5。图5中,油浴温度为71℃,在此油浴条件下,管内液体样品升至60℃所需时间为2min,之后直至加热到30min为止,全过程中管内液体样品温度不超过68℃,符合巴氏杀菌工艺的加热要求。因此,油浴条件为71℃/32min即可达到巴氏杀菌工艺62-65℃/30min的条件要求。实施例3:75-90℃/15-40s处理时油浴温度的探索材料及操作方法同实施例1。操作时温度保持在70℃-95℃范围即可。根据记录的温度,绘制升温曲线图,见图6。图6中,油浴温度为140℃,在此油浴条件下,管内液体样品升至70℃所需时间为15s,继续加热至30s时管内液体样品温度已经升至90℃。综上,140℃/30s即可达到75-90℃/15-40s处理的加热要求。实施例4:120-125℃/4-15s处理时油浴温度的探索材料及操作方法同实施例1。操作时温度保持在118℃-128℃范围即可。根据记录的温度,绘制升温曲线图,见图7。图7中,油浴温度为250℃,在此油浴条件下,管内液体样品升至123℃所需时间为18s,继续加热至20s时管内液体样品温度已经升至128℃。综上,250℃/18s即可达到120-125℃/4-15s处理的加热要求。实施例5:135-140℃/4-15s处理时油浴温度的探索材料及操作方法同实施例1。操作时温度保持在130℃-138℃范围即可。根据记录的温度,绘制升温曲线图,见图8。图8中,油浴温度为270℃,在此油浴条件下,管内液体样品升至135℃所需时间为20s。因此,270℃/20s的油浴条件即可达到135-140℃/4-15s处理的加热要求。实施例6:四种加热工艺的油浴条件的探索汇总依照上述实施例2、实施例3、实施例4和实施例5的步骤操作,可探索出能够满足实际生产中杀菌条件的油浴温度及加热时间,其杀菌要求及条件见表2。表2实际生产中的杀菌工艺及相应的油浴条件杀菌工艺名称杀菌条件油浴温度油浴条件低温长时巴氏灭菌法(ltlt)62-65℃/30min71℃71℃/32min高温短时巴氏灭菌法(htst)75-90℃/15-40s140℃140℃/30s超高温巴氏杀菌120-125℃/4-15s250℃250℃/18s超高温瞬时灭菌法(uht)135-140℃/4-15s270℃270℃/20s实际生产中的加热处理要求的时间很短,一般为几十秒甚至几秒,若加热管升温时间过长,不仅会导致样品损失,而且会导致样品热处理的误差过大,影响后期对数据的分析处理,因此加热操作时要考虑到加热管内液体的升温时间。所以,通过升高油浴温度以达到升温时间的缩短,使样品尽快达到理想温度,在理想温度范围内保持适宜时间,并采用冰水混合物能够保证载液管内的样品于10s内降温至室温(20℃)以下。由此更接近实际生产中相应的灭菌效果。因此,实施例1-5探索出一系列油浴温度条件下的温升曲线以指导实际操作。实施例结果表明,本发明的加热管升温速度快,时间短,一般15秒内即可达到所需温度,实际进行加热操作时可忽略其升温时间,完全能够满足实际生产中的超高温巴氏杀菌和uht处理。本发明的加热管单次处理量为3-50ml,满足微量液体样品对低压高温热处理的要求,填补了现存的大型uht杀菌设备不适于微量液体样品处理的空白,为科学研究中微量液体样品的uht杀菌处理提供了便捷,实现了微量液体样品的uht处理,具有非常显著的实际应用性。实施例7:四种杀菌工艺条件下压力的测定材料及设备:液体样品(鲜奶),注射器,模拟uht加热载液管,压力表,扳手,油浴锅(内置二甲基硅油)和冰浴锅(内置冰水混合物)。操作方法如下:(1)用注射器将液体样品缓缓注入模拟uht加热载液管中,加热管一头拧上双层密封盖,另一头拧上压力表并用扳手拧紧防止漏气,置于某相应温度的油浴锅中加热。(2)加热过程中,每隔5s测一次压力并记录。(3)汇总记录下的不同温度、不同时间时的压力值。如表3。表3四种杀菌工艺条件下管内压力以上所述仅为本申请的优选实施例而已,并不用于限制本申请,对于本领域的技术人员来说,本申请可以有各种更改和变化。凡在本申请的精神和原则之内,所作的任何修改、等同替换、改进等,均应包含在本申请的保护范围之内。当前第1页12