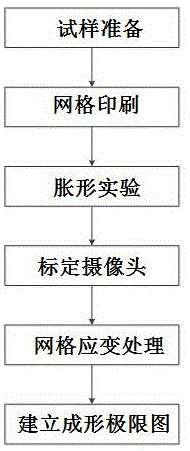
本发明涉及金属板料成形
技术领域:
,特别涉及一种基于光学非接触式的板料成形极限的测量方法。
背景技术:
:在板料成形领域,成形极限图(forminglimitdiagram,fld),用于确定板料在受到拉伸、胀形或拉伸胀形结合时能够达到的变形程度,反映了板料在发生塑性失稳时的极限应变。是对板料成形性能的一种定量描述,也是评价板料成形性能的重要方法,为方便地研究板料成形极限和评价拉伸失稳理论提供了基础。目前,板料成形极限的测定方法通常有两种:1、理论计算;2、实验确定。理论计算成形极限主要是通过采用不同的屈服准则和塑性本构关系,利用不同的拉伸失稳准则作为判断发生颈缩与破裂的条件来进行解析的。目前较常用的屈服准则包括hill系列屈服准则(hill48,hill1979,hill1990,hill1993),hosford屈服准则,barlat,gotoh屈服准则等。但理论推导只符合特定的线性或近似线性的应变路径,而实际板料的冲压,特别在是成形较复杂的零件或是多工序成形的情况下,往往偏离了线性应变路径,导致无法准确判断板料的失稳现象。且不同屈服准则的适用范围有限,所涉及的参数较多,计算精度受到诸多因素影响,应用不多。因此,迫切需要一种能简单、方便地构建板料成形极限图的实验方法。技术实现要素:本发明的目的在于提供一种基于光学非接触式的板料成形极限的测量方法,克服现有板料成形极限理论计算方法的不足。本发明可以高效准确的测量板料成形的极限应变,以建立板料的成形极限图。第一步,试样准备:采用线切割的方式将板料毛坯切割成符合标准要求的尺寸及几何形状的试件;第二步,网格印制:采用电解液腐蚀法对试件印制网格;第三步,胀形实验:在成形试验机上进行胀形实验直至试件发生颈缩或破裂;第四步,标定摄像头:利用光学应变测量设备对相机进行标定;第五步,网格应变处理:从多个角度记录试样表面的图像信息,分析处理获得试验件变形失稳部位的主次应变分布;第六步,建立成形极限图,将获得的极限应变点拟合成适当的曲线或构成条带形区域,以建立板料的的成形极限图。本明具有测量操作方便,自动化程度高,测量结果准确、可靠的特点,并且具有很好的普适性。本发明的上述目的通过以下技术方案实现:基于光学非接触式的板料成形极限的测量方法,包括如下步骤:1)试样准备:将板料毛坯切割成符合标准要求的尺寸及几何形状的试样,为减小压边圈处的应力集中,将小尺寸试样设计成中部稍窄的哑铃状,有效成形区域为由中心向两侧均匀过渡的弧形,并将大尺寸试样设计为矩形;2)网格印制:用有机溶剂清洗干净试样表面,并采用电解液腐蚀法在所需要测量的试样表面印制圆形网格,网格为直径1mm的实心圆点,且圆形网格的圆心距为2mm;3)胀形试验:在成形试验机上进行凸模胀形实验,为减小摩擦,在试样和冲头之间放置硅胶垫,将试样的网格面背向冲头,利用成形试验设备产生的压边力压紧试样材料的边部,在冲头的作用下试样中部发生胀形形变,胀形至试样发生颈缩或者开裂时,停止实验;4)标定摄像头:使用多个标定点确定测量过程中的三维空间坐标系;在光学测量过程中,改变摄像头的位置,从多个角度记录试样表面的图像信息,并保证试样上所有实心圆点都被摄像头记录通过摄像头获取变形后试样上的所有的实心圆点的相对位置;5)网格应变处理:将记录的试样图像信息导入到专用的处理软件中,二维影像图被处理成三维立体图像,并由软件将临近的实心圆点连接为四边形网格,通过图像匹配的方法对比分析变形前后各实心圆点的空间位置差异,并根据网格边长的变化自动计算断裂临界区的主次应变;6)建立成形极限按图:e1为工程主应变,e2为工程次应变,d1为临界网格圆长轴直径,d2为临界网格圆短轴直径,d0为网格圆初始直径;应变测量计算原理如下公式:e1=(d1-d0)/d0×100(%)(1)e2=(d2-d0)/d0×100(%)(2)以工程主应变e1为纵坐标,工程次应变e2为横坐标,建立应变坐标系;将求得的极限应变点拟合成适当的曲线或构成条带形区域,以建立板料的的成形极限图。步骤中1)所述的试样准备要求试样表面平整、边缘无裂纹,厚度在0.3~3mm,应至少准备5种不同尺寸的试样,且每种类型的试样不少于3个。步骤中2)所述的试样表面圆形网格制备清晰完整且制备范围大于所测量变形区域。步骤中3)所述的胀形实验在室温下进行成形,或者对试件高温加热后进行高温胀形。本发明采用的润滑物质为聚乙烯薄膜、硅胶垫或润滑油;有机溶剂为工业酒精或丙酮。本发明的有益效果在于:1、本发明克服现有板料成形极限理论计算方法的不足,提供了一种操作简单、可以高效准确的测量板料成形极限应变的方法。2、本发明以失稳区边界点所能达到的最大主应变数值作为板料的极限主应变,具有明确的物理意义。3、本发明使用网格圆点作为测量依据,测量范围可根据实际需求进行设定,适用范围广泛;且极限应变测量效率较高。4、本发明使用的是光学测量的方式,是一种非接触测量方法。附图说明此处所说明的附图用来提供对本发明的进一步理解,构成本申请的一部分,本发明的示意性实例及其说明用于解释本发明,并不构成对本发明的不当限定。图1为本发明的步骤流程图;图2为本发明的凸模胀形实验原理图;图3为本发明实施例中的实验件形状和尺寸图;图4为本发明实施例中的圆形网格形状尺寸示意图;图5为本发明实施例中的板料成形极限图。具体实施方式下面结合附图进一步说明本发明的详细内容及其具体实施方式。参见图1至图5所示,本发明的基于光学非接触式的板料成形极限的测量方法,包括如下步骤:第一步,试样准备,将厚度为0.2mm~3mm的板料毛坯切割成符合标准的尺寸和几何形状要求的试件,通过改变试样有效成形区域的宽度来实现不同应变路径;板料试样准备要求应保证制备的试样边缘无裂纹,且试样表面平整;不同尺寸和几何形状的试样至少准备5种,且每种类型的试样不少于3个。第二步,用有机溶剂将试样表面清洗干净,并采用电解液腐蚀法在所需要测量的试样表面区域印制网格;网格形式为均布的直径1mm实心圆点,且圆形网格的圆心距为2mm;圆形网格制备应清晰完整,且制备范围应大于所测量变形区域。第三步,对试样进行凸模胀形实验,为减小试样和冲头之间的摩擦,在两者间放置润滑物质,并将试样的网格面背向冲头,利用成形试验设备产生的压边力压紧试样材料的边部,在冲头的作用下试样中部产生胀形变形,胀形至试样发生颈缩或者开裂时,停止实验。上述润滑物质为聚乙烯薄膜、硅胶垫或润滑油。第四步,对摄像头进行标定,使用多个标定点确定测量过程中的三维空间坐标系。在光学测量过程中,改变摄像头的位置,从多个角度记录试样表面的图像信息。在测量过程中保证系统标定点始终处于摄像头的记录范围以内,并保证试样上所有实心圆点都被摄像头记录。第五步,将记录的试样图像信息导入到专用的处理软件中,二维影像图被处理成三维立体图像,并由软件将临近的实心圆点连接为四边形网格,并根据网格边长的变化自动计算断裂临界区的主次应变。应变测量计算原理如下公式:e1=(d1-d0)/d0×100(%)(1)e2=(d2-d0)/d0×100(%)(2)式中,e1为工程主应变,e2为工程次应变,d1为临界网格圆长轴直径,d2为临界网格圆短轴直径,d0为网格圆初始直径。第六步,建立板料的成形极限图,以工程主应变e1为纵坐标,工程次应变e2为横坐标,建立应变坐标系。根据第五步求得的极限应变点,拟合成适当的曲线或构成条带形区域,以建立板料的成形极限图。本发明的实验方法采用标准实验装置进行实验,能够对各种润滑条件下金属薄板材料的成形极限、以及在成形过程中发生破坏的位置和成形性能进行判断。实施例:以下结合附图和厚度为1mm的6016-t4铝合金板料的成形极限测定实验对本发明作进一步的详细说明。本发明提出一种基于光学非接触式板料成形极限的测量方法,具体操作步骤如图1所示。所采用的实验装置的硬件原理结构如图2所示,凸模胀形实验采用的是ec系列标准板料成形试验机。该设备主要参数为:压边力设定为1200kn,拉伸力设定为1500kn,冲头直径100mm,凹模圆角半径5mm,冲头上升速度为1mm/min,总电功率为5.5kw,外形尺寸为1510*1010*1700mm,总重量为1500kg,圆顶冲头由液压拉伸机构控制,可保证实验过程中匀速前进,并保证冲头对中性在0.05mm以内。将厚度为1mm的6016-t4铝合金板料毛坯切割成符合标准尺寸和几何形状要求的试样,为减小压边圈处的应力集中,将小尺寸试样设计成中部稍窄的哑铃状,有效成形区域为由中心向两侧均匀过渡的弧形,考虑加工的简易性和试验的可行性,将大尺寸试样设计为矩形,如图3及表1所示,其中h=90mm。通过改变试样宽度来实现不同应变路径,即从单向拉伸状态逐渐过渡到双向等拉状态。用有机溶剂如酒精将试样表面清洗干净,并采用电解液腐蚀法在所需要测量的试样表面印制圆形网格,且网格印制范围应大于所测变形区域;网格形式为均布的直径1mm实心圆点,且圆形网格的圆心距为2mm,如图4所示。表1123456789w/mm101520304050607080r/mm4037.535302520***l/mm4042.545505560***采用ec系列标准板料成形试验机对试样进行胀形实验,为减小摩擦,在试样和冲头之间放置硅胶垫,将试样的网格面背向冲头,利用成形试验设备产生的压边力压紧试样材料的边部,在冲头的作用下试样中部产生胀形变形,试件表面的圆形网格发生畸变,由圆形变为椭圆形。胀形至试样发生颈缩或者开裂时,停止实验。使用多个标定点确定测量过程中的三维空间坐标系对摄像头进行标定。在光学测量过程中,改变摄像头的位置,从多个角度记录试样表面的图像信息。在测量过程中保证系统标定点始终处于摄像头的记录范围以内,并保证试样上所有实心圆点都被摄像头记录。将记录的试样图像信息导入到专用的处理软件中,二维影像图被处理成三维立体图像,并由软件将临近的实心圆点连接为四边形网格,并根据网格边长的变化自动计算断裂临界区的主次应变。以工程主应变e1为纵坐标,以工程次应变e2为横坐标,建立平面应变坐标系,将所获得的局部表面极限应变值标绘在表面应变坐标系中,形成成形极限散点图,将分布的散点用一条光滑的曲线连接或构成条带形区域,以建立6016-t4铝合金的成形极限图,如图5所示。以上所述仅为本发明的优选实例而已,并不用于限制本发明,对于本领域的技术人员来说,本发明可以有各种更改和变化。凡对本发明所作的任何修改、等同替换、改进等,均应包含在本发明的保护范围之内。当前第1页12