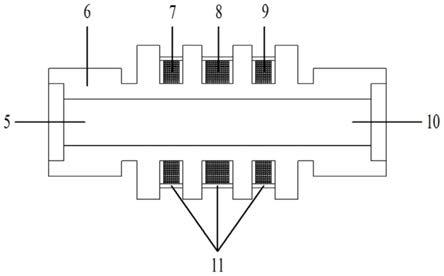
1.本发明涉及一种设备油液系统故障检测领域,特别是关于一种基于高磁导率铁芯的金属磨损颗粒检测传感器及检测方法。
背景技术:2.在机械设备的运行过程中,摩擦导致的磨损现象是不可避免的,因设备过度磨损而导致的机械故障是影响机械设备正常运行的主要障碍之一。在机械设备长时间的运行过程中产生的磨损颗粒中包含着设备当前阶段的磨损状态信息,通过对润滑油液中磨粒信息的实时检测,可以有效的获取当前的设备磨损状态。研究表明机械设备正常运行时润滑系统内的磨损颗粒直径集中于20μm;当设备磨损加剧时,油液内的磨损颗粒直径将增加到50μm
‑
150μm,而50
‑
150μm区间的颗粒又会导致设备发生更大的磨损。因此对润滑油内磨损颗粒的检测研究应尽可能提高对50
‑
150μm左右磨损颗粒的检测能力。现阶段的油液磨粒在线检测方法主要有光学检测、电学检测、声学检测、电感检测等。其中电感式金属磨损颗粒检测传感器具有结构形式简单可靠、温度稳定性好、抗背景噪声能力强的优点,但其对微小磨粒的检测能力较弱的缺点仍然限制了其得到广泛应用。如何提高电感式金属磨损颗粒检测传感器对微小磨粒的检测能力是目前对电感式磨粒检测传感器的主要研究方向。
技术实现要素:3.针对上述金属磨损颗粒检测传感器对微小磨粒检测能力不足的问题,本发明的目的是提供一种基于高磁导率铁芯的金属磨损颗粒检测传感器及检测方法,其能有效提高对于微小磨粒的检测能力。
4.为实现上述目的,本发明采取以下技术方案:一种基于高磁导率铁芯的金属磨损颗粒检测传感器,其包括:油管通道入口、检测单元、油管通道出口和传感器外壳;所述检测单元设置在所述传感器外壳内,所述油管通道入口与所述检测单元的第一端连接,所述油管通道出口与所述检测单元的第二端连接;所述检测单元包括检测单元入口、陶瓷骨架、第一激励线圈、感应线圈、第二激励线圈、检测单元出口和高磁导率铁芯;所述陶瓷骨架的一端为所述检测单元入口,所述检测单元入口与所述油管通道入口连通,所述陶瓷骨架的另一端为所述检测单元出口,所述检测单元出口与所述油管通道出口连通;所述陶瓷骨架的外侧间隔设置有三个线圈凹槽,位于中部的所述线圈凹槽内设置有所述感应线圈,位于所述感应线圈两侧的所述线圈凹槽内分别设置有所述第一激励线圈和第二激励线圈;位于所述感应线圈、第一激励线圈和第二激励线圈的径向外侧以及轴向两侧设置有所述高磁导率铁芯。
5.进一步,所述第一激励线圈和第二激励线圈绕制方向相反。
6.进一步,所述高磁导率铁芯采用导磁胶分别与所述感应线圈、第一激励线圈和第二激励线圈的外侧及轴向两侧固定连接。
7.进一步,所述第一激励线圈、第二激励线圈和感应线圈都采用漆包线绕制而成。
8.进一步,所述高磁导率铁芯的相对磁导率为5000
‑
20000。
9.进一步,所述高磁导率铁芯采用相对磁导率为5000的铍镆合金制成。
10.一种基于高磁导率铁芯的金属磨损颗粒检测传感器的检测方法,该方法采用上述金属磨损颗粒检测传感器,包括以下步骤:
11.1)带有金属磨损颗粒的润滑油液进入传感器后,磨损颗粒在传感器背景磁场的作用下被磁化,并在磨损颗粒位置处分别产生外部磁化场和内部磁化场,得到磨损颗粒处的合磁场;
12.2)根据磨损颗粒处的合磁场得到磨损颗粒内部的磁化强度;
13.3)根据颗粒内部磁化强度得到颗粒内部磁感应强度b和传感器中磁化场的总磁链,进而得到感器输出感应电动势,通过该感应电动势实现对微小金属磨损颗粒进行检测。
14.进一步,磨损颗粒处的合磁场h为:
15.h=h0+h
in
=h0‑
nm,
16.式中,h
in
为磨损颗粒内部退磁场,h0为线圈内部磁场强度,m为磨损颗粒的磁化强度,n为退磁因子。
17.进一步,颗粒内部磁化强度m'为:
[0018][0019]
式中,μ
r
为相对导磁率,h'为添加高磁导率铁芯后空间磁场的总磁场强度,h'=h0+h1,h0为线圈内部磁场强度,h1为磁场增量。
[0020]
进一步,传感器输出感应电动势e为:
[0021][0022]
式中,i为通过线圈的电流;为激励电压;r
s
为单个线圈电阻;l为线圈电感;
△
l为传感器线圈电感增量,磨损颗粒通过引起的传感器总磁链变化量为
△
ψ,
△
l=
△
ψ/l。
[0023]
本发明由于采取以上技术方案,其具有以下优点:本发明通过在激励线圈ⅰ/激励线圈ⅱ和感应线圈的轴向两侧及径向外侧添加高磁导率铁芯,将感应磁场引导向轴芯方向,同时避免了磁场向无效方向泄露,增加了传感器线圈内部磁场强度,增加了磨粒通过传感器时产生的磁化涡流效应,提升了传感器输出电压幅值。对于微小磨粒,提升后的电压幅值更容易达到检测识别标准,有助于提升电感式传感器对微小磨粒的检测能力。
附图说明
[0024]
图1为本发明基于高磁导率铁芯的金属磨损颗粒检测传感器结构示意图。
[0025]
图2为本发明检测单元结构图。
[0026]
图3为添加高磁导率铁芯前后金属磨损颗粒检测传感器轴线磁通密度对比图。
[0027]
图4为添加高磁导率材料前后金属磨损颗粒检测传感器输出感应电压对比图。
[0028]
图中,1:油管通道入口,2:电感式检测单元,3:油管通道出口,4:传感器外壳,5:检测单元入口,6:陶瓷骨架,7:第一激励线圈,8:感应线圈,9:第二激励线圈,10:检测单元出口,11:高磁导率铁芯。
具体实施方式
[0029]
在本发明的描述中,需要理解的是,术语“上”、“下”“内”、“外”等指示的方位或位置关系为基于附图所示的方位或位置关系,仅是为了便于描述本发明和简化描述,而不是指示或暗示所指的装置或元件必须具有特定的方位、以特定的方位构造和操作,因此不能理解为对本发明的限制。下面结合附图和实施例对本发明进行详细的描述。
[0030]
如图1所示,本发明提供一种基于高磁导率铁芯的金属磨损颗粒检测传感器,其包括油管通道入口1、检测单元2、油管通道出口3和传感器外壳4。检测单元2设置在传感器外壳4内,油管通道入口1与检测单元2的第一端连接,油管通道出口3与检测单元2的第二端连接。其中:
[0031]
如图2所示,检测单元2包括检测单元入口5、陶瓷骨架6、第一激励线圈7、感应线圈8、第二激励线圈9、检测单元出口10和高磁导率铁芯11。
[0032]
陶瓷骨架6的一端为检测单元入口5,检测单元入口5与油管通道入口1连通;陶瓷骨架6的另一端为检测单元出口10,检测单元出口10与油管通道出口3连通。陶瓷骨架6的外侧间隔设置有三个线圈凹槽,位于中部的线圈凹槽内设置有感应线圈8,位于感应线圈8两侧的线圈凹槽内分别设置有第一激励线圈7和第二激励线圈9。位于感应线圈8、第一激励线圈7和第二激励线圈9的径向外侧以及轴向两侧设置有高磁导率铁芯11。
[0033]
上述实施例中,第一激励线圈7和第二激励线圈9绕制方向相反。
[0034]
使用时,带有金属磨损颗粒的润滑油液通过油管通道入口1和检测单元入口5进入传感器,磨粒先后经过第一激励线圈7、感应线圈8和第二激励线圈9,最后经检测单元出口10和油管通道出口3流出传感器。由于第一激励线圈7和第二激励线圈9绕制方向相反,施加高频激励电流,使其在中间感应线圈8上产生的磁通相互抵消为零,磨粒通过时因激励线圈产生的磁场发生磁化,引起感应线圈失衡,其内部磁场发生变化,磁场变化的幅值转换成电压信号,该信号的相位和幅值分布代表磨粒的材质和大小。
[0035]
上述实施例中,高磁导率铁芯11采用导磁胶分别与感应线圈8、第一激励线圈7和第二激励线圈9的外侧及轴向两侧固定连接。
[0036]
上述各实施例中,第一激励线圈7、第二激励线圈9和感应线圈8都采用漆包线绕制而成。该漆包线直径为0.1
‑
1毫米,匝数为60
‑
160匝;第一激励线圈7、第二激励线圈9和感应线圈8的内径为3
‑
9毫米。
[0037]
上述各实施例中,高磁导率铁芯11相对磁导率为5000
‑
20000,可以使用相对磁导率为5000的铍镆合金制成,厚度为0.1
‑
1毫米。
[0038]
本发明还提供一种基于高磁导率铁芯的金属磨损颗粒检测传感器对金属磨损颗粒的检测方法,其包括以下步骤:
[0039]
1)带有金属磨损颗粒的润滑油液进入传感器后,磨损颗粒会在传感器背景磁场的作用下被磁化,并在磨损颗粒位置处分别产生外部磁化场和内部磁化场,得到磨损颗粒处的合磁场h;
[0040]
磨损颗粒的外部磁化场可以等效为一个磁偶极子,其磁偶极矩p为:
[0041]
p=μm=μmv
[0042]
式中,m为磁化强度,m为磨损颗粒的整体磁矩,v为磨损颗粒的体积,μ为磨损颗粒的磁导率;磨损颗粒的内部磁化场可表征为:
[0043]
h
in
=
‑
nm(0<n<1)
[0044]
b
in
=μ0h
in
+μ0m
[0045]
式中,h
in
为磨损颗粒内部退磁场,b
in
为磨损颗粒内部磁感应强度,n为退磁因子;假设电场稳定,则线圈内部磁场强度为h0,则磨损颗粒处的合磁场h为:
[0046]
h=h0+h
in
=h0‑
nm。
[0047]
2)根据磨损颗粒处的合磁场h得到磨损颗粒内部的磁化强度;
[0048]
由于传感器管路中的油液是线性介质,其不会影响传感器内磁场分布,故磨损颗粒磁化强度可表征为:
[0049]
m=χ
m
h
[0050]
式中,χ
m
=μ
r
‑
1为油液的磁化系数,μ
r
为相对导磁率,可得磁化强度m为:
[0051][0052]
由上述公式可知,磨损颗粒的磁化程度和线圈内部磁场h0有关。当铁磁性磨损颗粒经过磁场区域并被磁化时,颗粒位置处会产生与原磁场方向相同的内磁化场,即h
in
与原磁场h0方向相同,表现为线圈电感值增加。当非铁磁性磨损颗粒经过检测区域(非均匀磁场)时,颗粒内部会产生电涡流,其产生的附加磁场会减小原磁场强度h0,表现为线圈电感值减小。
[0053]
当为传感器添加高磁导率铁芯时,会增强激励线圈所产生的磁场(磁场增量为h1),此时空间磁场的总磁场强度h'可表征为:
[0054]
h'=h0+h1[0055]
此时颗粒内部磁化强度m'为:
[0056][0057]
3)根据颗粒内部磁化强度得到颗粒内部磁感应强度b和传感器中磁化场的总磁链,进而得到传感器输出感应电动势。无磨粒通过时,传感器输出感应电动势小于2mv,当金属磨损颗粒通过传感器时,传感器输出感应电动势高于2mv,且根据电动势幅值可以判断出通过金属磨损颗粒的尺寸,从而实现对微小金属磨损颗粒进行检测;
[0058]
由于高磁导率铁芯引起的总磁场增加,使得磨损颗粒磁化强度有所增大。此时,线圈中磨损颗粒内部磁感应强度如式所示,可见颗粒内部磁感应强度b也随之增强。
[0059]
b'=μ0[ni+m'(1
‑
n)]
[0060]
此外,传感器中磁化场的总磁链ψ可表征为:
[0061][0062]
式中,b为线圈半径;n为线圈单位长度上的匝数;l为线圈长度;
[0063]
可见,当为传感器线圈增加高磁导率铁芯时,由于磨损颗粒磁化强度的增强,传感器中总磁链ψ也随之增加(磨损颗粒引起的总磁链变化量为
△
ψ)。根据式
△
l=
△
ψ/l可得,磨损颗粒引起的传感器线圈电感增量
△
l也显著提高。此时,传感器输出感应电动势e为:
[0064][0065]
式中,i为通过线圈的电流;为激励电压;r
s
为单个线圈电阻;l为线圈电感;j为虚数单位;ω为交流电相位。
[0066]
因此,添加高磁导率铁芯能有效提高传感器的输出感应电动势、增强传感器检测灵敏度。
[0067]
本发明还提供一种基于高磁导率铁芯的金属磨损颗粒检测传感器的制作方法,其包括以下步骤:
[0068]
步骤s1:在传感器骨架线圈槽的轴向两侧添加高磁导率铁芯,使用导磁胶进行连接处固定;
[0069]
步骤s2:在轴向两侧添加过高磁导率铁芯的线圈槽中分别进行激励线圈ⅰ/激励线圈ⅱ和感应线圈的绕制;
[0070]
步骤s3:在线圈轴向外侧包裹高磁导率铁芯,其与轴向两侧高磁导率铁芯直接使用导磁胶进行粘合。
[0071]
综上,本发明在使用时,如图3所示,将本发明添加高磁导率铁芯11后与未添加高磁导率铁芯的金属磨损颗粒检测传感器轴线磁通密度对比图,可以看出,添加高磁导率铁芯后提升了轴线上的磁感应强度,高的磁感应强度有利于传感器对微小磨粒进行检测。如图4所示,将本发明添加高磁导率铁芯后与未添加高磁导率铁芯的金属磨损颗粒检测传感器对100微米磨粒的检测电压对比图,可以看出,添加高磁导率铁芯之后,传感器对金属磨粒产生的检测电压得到了提高。
[0072]
上述各实施例仅用于说明本发明,各部件的结构、尺寸、设置位置及形状都是可以有所变化的,在本发明技术方案的基础上,凡根据本发明原理对个别部件进行的改进和等同变换,均不应排除在本发明的保护范围之外。