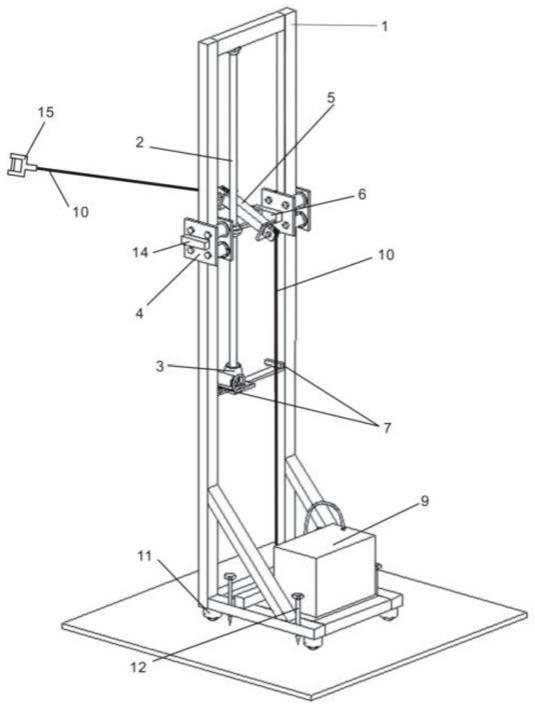
1.本发明涉及车辆行李架强度试验的检测装置,具体涉及一种车身行李架静态及动态强度试验装置,既满足法规的静态检验要求,同时满足开发试验的需求。
技术背景
2.汽车车顶行李架及雪橇架静态载荷是测量汽车车顶行李架总成承重能力的一项重要试验,针对此试验,国家标准gb11566已经规定了静态载荷的强制性要求,要求行李架及雪橇架试验过程中其承受纵向及横向的水平作用力,力值不低于制造厂商规定的最大垂直承载能力,对于按照厂家规定安装的行李架及雪橇架试验,试验载荷不能作用在一个点上。
3.相同载荷情况下,行李架及雪橇架相对车身中心线宽度安放间距的不同,其行李架支撑点与车身受力也会出现很大区别;反之选择不同间距的安装点,行李架的最大承重也会有很大区别,行李架相对车顶位置间距的选择,关系到整车工艺、风阻、造型、成本等方面如何优化,所以试验时宽度方向的受力中心需要与车辆中心线一致,但目前的试验装置存在车身中心线找正困难。
4.同时法规未对整车开发条件下行李架及雪橇架强度试验的需求进行规定,由于在行车中会遇到不同的车况,行李架及雪橇架会承受不同方向共同的作用力,因此在车辆的开发环节,各车企不仅需要对新开发车型的行李架及雪橇架做静态载荷试验,同时需要做动态交变载荷与行李架纵向及横向非水平静态及动态载荷试验,但目前的试验装置仅能完成法规要求的静态荷载的测试,并不能完成其他几种试验。同时现有的试验装置不能自由匹配不同车型的高度,辅助工时长,不能便携,无法分析行李架在加载时的受力状态,不能满足乘用车及商用车开发的要求。
5.技术方案本发明的目的在于解决上述现有技术的不足,从而提供一种车身行李架静态及动态强度试验装置,能满足不同车辆行李架强度的试验。
6.一种车身行李架静态及动态强度试验装置,包括:车顶固定板,所述车顶固定板与待测试车身的行李架连接成刚性整体,车顶固定板沿待测试车身的宽度方向的中心线与待测试车身的中心线平齐,车顶固定板上端均布有z个应力片;用于对车顶固定板施加外荷载的加力模块,所述加力模块至少为四个,四个加力模块分别放置于待测车身的四个面上,且待测车身前、后侧的两个加力模块的中心线与待测车身的中心线平齐,待测车身左、右测的两个加力模块的中心线与车顶固定板长度方向的中心线平齐,所述加力模块包括支撑框架、用于施加拉力的钢丝绳,钢丝绳一端与用于施力的液压马达连接、另一端与挂钩连接,挂钩固定在车顶固定板上,钢丝绳中部固定在滑轮托架,滑轮托架下端部可旋转的连接在电动旋转台的旋转中心上,滑轮托架位于加力模块的中心线上,电动旋转台固定在升降装置的升降横杆上,升降横杆可沿支撑框架上下移动;
用于标定待测试车辆中心线的中心线标定装置,所述中心线标定装置安装在待测试车身的前后车牌照框内。
7.所述支撑框架为由底架及立在底架一侧的立架组成的l型框架结构,立架为由两个横杆和两个立杆焊接成的长方形框架结构,两个立杆上预设有对称用于与中心线标定装置配合定位加力模块位置的标定点;底架的底部四角均装有一个万向轮,底架上还装有四个用于调平的地脚螺栓,四个地脚螺栓两两对称分设在底架两端面上;底架与立架之间焊接有倾斜的支撑杆。
8.所述升降装置包括螺旋升降机、升降横杆,螺旋升降机底部固定在水平横杆上,水平横杆固定在立架的两个立杆之间;升降横杆套装在螺旋升降机上丝杆的外部,升降横杆用于穿过丝杆的通孔内设有与丝杆配合的牙销,升降横杆上设有水平仪;升降横杆的两端部分别与一个导向装置连接,两个导向装置可沿立架的两个立杆升降,两个导向装置上分别装有一个激光测距仪,两个激光测距仪关于升降横杆中线对称,车顶固定板的四个侧边线上分别预设有两个标定块,左、右两个侧边线的同一侧边上的两个标定块之间的距离与两个激光测距仪之间的距离一致。
9.所述导向装置包括平行设置的竖板,两个竖板经两组滚轮组相互连接,两组滚轮组分别与立杆的前、后侧面滚动接触,两个竖板与立杆的左、右侧面平行相对。
10.z个所述应力片排布成一个m行n列的矩阵,z=m
×
n。
11.还包括用于为液压马达提供液压油的液压泵站,液压泵站及液压马达均设于底架上,液压泵站的底部装有配重块。
12.所述中心线标定装置包括车辆基准参考装置、激光校准测距装置;所述车辆基准参考装置包括设于待测车身前后车牌照框里的前部参考装置、后部参考装置;前部参考装置、后部参考装置均包括车牌架、设在车牌架上的三轴云台、装在三轴云台上的角度编码盘、伸缩杆,车牌架安装在待测车辆的车牌照框内,伸缩杆立在角度编码盘旋转中心上、可随角度编码盘一起同轴旋转,前部参考装置、后部参考装置的伸缩杆顶端的中心连线与待测车身位于同一竖直平面内;所述激光校准测距装置包括激光扫描测距仪及光电传感器,光电传感器设在后部参考装置的伸缩杆顶端,激光扫描测距仪设置在前部参考装置的角度编码盘上、可随该角度编码盘一起旋转,前部参考装置的伸缩杆为空心结构、且在两端头开设有窗口,两个窗口处分设有一个等腰直角三棱镜,上、下两个等腰直角三棱镜的斜边相对平行布置、且斜边中点的连线与伸缩杆的中轴线同轴心,光电传感器与上部等腰直角三棱镜斜边中心的连线与水平面平齐,激光扫描测距仪发射出的激光水平照射在下部等腰直角三棱镜斜边的中心点上,用于将激光扫描测距仪发射出的激光通过上、下两个等腰直角三棱镜反射后从上部等腰直角三棱镜斜边中心点水平射出。
13.所述车牌架包括底板、连接于底板一侧的立板,立板上设有两个用于与车牌照框内螺栓安装孔对应固定的通过孔;角度编码盘上设有两个可随角度编码盘一起旋转的激光发射器,伸缩杆顶端侧壁经连接杆连接有与两个激光发射器垂直对应的激光接收器;伸缩杆采用碳纤维材质;底板两端部上分设有两个螺孔,每个螺孔内均装有地脚固定螺栓。
14.还包括校准装置,校准装置包括设置在前部参考装置、后部参考装置的伸缩杆上
的标定靠板、两组标定方箱组,每组标定方箱组由两个标定方箱组成,每组内的两个标定方箱分设在对应的前部参考装置/后部参考装置的两侧,每组内的一个标定方箱与水平工作台面的纵边平齐、另一标定方箱与水平工作台面的横边平齐,且每组内的两个标定方箱上平面高于对应的前部参考装置和后部参考装置的标定靠板上平面,前部参考装置和后部参考装置的标定靠板上设有两组激光测距组,两组激光测距组分别沿标定靠板的x轴方向、y轴方向发射激光,每组激光测距组包括两个激光测距仪。
15.还包括控制器,控制器与无线通讯模块经信号线连接;每个所述加力模块上设用于与控制器经无线通讯模块信号互通的无线接收器二及无线发射器二;所述中心线标定装置的前部参考装置的三轴云台上装有无线接收器一,后部参考装置的三轴云台装有无线发射器一,无线接收器一、无线发射器一也与控制器经过无线通讯模块信号互通。
16.与现有技术相比本技术1.能满足不同车辆行李架强度的试验;2.能完成行李架动态交变载荷模拟,行李架纵向及横向非水平作用力状态下的静态和动态开发试验;3.具有较好的便携性,能快速完成乘用车、商用车的开发试验;4.本装置车身中心线对中速度快、精度高;5.通过预先放置的应力传感器可以进行车顶行李架及顶棚力学有限元实时分析,提供开发所需的数据。
附图说明
17.图1为本发明加力模块的结构图一;图2为本发明加力模块的结构图二;图3为本发明中心线标定装置的结构图;图4为本发明中心线标定装置的俯视图;图5为前部参考装置的结构图;图6为前部参考装置的部分结构图;图7为激光折射角度原理图;图8为后部参考装置的结构图;图9为后部参考装置的立体图;图10为车顶固定板与行李架的装配图;图11为加力模块及车顶固定板布置位置的校准原理图;图12为图11的局部放大图;图13为水平静态载荷试验俯视图;图14为水平静态载荷试验图;图15为非水平静态载荷试验图一;图16为非水平静态载荷试验图二;图中:1、支撑框架,101、反光贴,2、丝杠,3、螺旋升降机,4、升降装置,5、滑轮托架,6、电动旋转台,7、水平仪,8、液压马达,9、液压泵站,10、前部参考装置,11、万向轮,12、地脚螺栓,13、车顶固定板,131、标定块,14、激光测距仪,15、挂钩,16、应力片,17、配重块,18、钢丝绳,19、激光束,20、后部参考装置;21、行李架,22、紧固板,23、行李架横梁,24、螺栓,25、
螺帽;301、标定方箱一,302、标定方箱二,303、标定方箱三,304、标定方箱四;1011、前车牌架,1012、地脚固定螺栓一,1013、三轴云台一,1014、角度编码盘一,1016、前标定靠板,1017、前伸缩杆,1021、激光扫描测距仪,1022、高容量锂电池一,1051、激光发射器一,1052、激光发射器二,1081、激光接收器一,1091、下部等腰直角三棱镜,1092、上部等腰直角三棱镜,1020、无线接收器一;2011、后车牌架,2012、地脚固定螺栓二,2013、角度编码盘二,2014、三轴云台二,2016、后标定靠板,2017、后伸缩杆,2019、光电传感器,2021、高容量锂电池二,2051、激光发射器三,2052、激光发射器四,2081、激光接收器二,2082、激光接收器三。
具体实施方案
18.实施例一:图1~2中,加力模块包括用于施加拉力的钢丝绳18,钢丝绳18一端与液压马达8连接、另一端与挂钩15连接,挂钩15固定在车顶固定板13上,液压马达8放置在支撑框架1上、用于提供拉力,支撑框架1是l型框架结构,l型框架结构由底架及立在底架一侧的立架组成,底架与立架之间焊接有倾斜的支撑杆,立架为由两个横杆和两个立杆焊接成的长方形框架结构,两个立杆上预设有对称用于与中心线标定装置配合定位加力模块位置的标定点,标定点采用反光贴。在底架的底部四角均装有一个万向轮11,底架上还装有四个地脚螺栓12,四个地脚螺栓12两两对称分设在底架两端面上,通过四个地脚螺栓12可以调节底架的水平;钢丝绳18的伸缩方向与两个立杆平行、且到两个立杆的垂直距离一致,钢丝绳18中部固定在滑轮托架5,滑轮托架5下端部可旋转的连接在电动旋转台6的旋转中心上,并带动滑轮托架5同步旋转,滑轮托架5可绕电动旋转台6的旋转中心在立架竖直方向的中心线上进行俯仰动作,电动旋转台6固定在升降装置4的升降横杆上,升降装置4的螺旋升降机3底部固定在水平横杆上,水平横杆固定在立架的两个立杆之间,升降横杆套装在螺旋升降机3的丝杆2的外部,升降横杆上设有用于穿过丝杆2的通孔,通孔内壁设与丝杆2配合的牙销,丝杆2为往复丝杆。升降横杆的两端部分别与一个导向装置连接,两个导向装置可沿立架的两个立杆升降,导向装置包括平行设置的竖板,两个竖板经两组滚轮组相互连接,两组滚轮组分别与立杆的前、后侧面滚动接触,两个竖板与立杆的左、右侧面平行相对。通过设置导向装置可以使升降横杆水平升降。水平横杆的两端分别设有一个水平仪7,通过观察水平仪7,调节地脚螺栓2,使加力模块处于水平。用于为液压马达8提供液压油的液压泵站9均设于底架上,液压泵站9的底部装有配重块17,在给待测车身施加拉力时,确保加力模块不会出现移动现象,影响试验的准确性。将用于提供外荷载的加力模块整体模块化,测试时只用根据试验的要求,加力模块可以准确快速的放置在对应的点位上,然后进行测试,不仅有效的节省试验时间,同时也提高试验的准确性,为开发车辆提供便利。
19.图3中,中心线标定装置包括由前部参考装置10、后部参考装置20组成的车辆基准参考装置,以及激光校准测距装置;前部参考装置10、后部参考装置20分装在待测车身前后车牌照框里。
20.图4中,用于校准前部参考装置10、后部参考装置20校准装置包括四个标定方箱,四个标定方箱均为六面体,其4条边与水平工作台面的x方向和y方向平行,4条边所在的立
面与水平工作台面的水平面垂直;四个标定方箱分别是标定方箱一301、标定方箱二302、标定方箱三303、和标定方箱四304,其中标定方箱一301、标定方箱二302为一组,标定方箱一301、标定方箱二302与前部参考装置1的前标定靠板1016上的两组激光测距组配合、用于校准的角度编码盘一1014的初始位置,标定方箱一301、标定方箱二302分设在前部参考装置10的两侧,标定方箱一301左侧边与水平水平工作台面的纵边平齐,且右侧边与左侧边相互平行;标定方箱二302后侧边与水平水平工作台面的横边平齐,且后侧边与前侧边相互平行,标定方箱一301、标定方箱二302上平面高于前部参考装置10的前标定靠板1016上平面,前标定靠板1016上平面的两组激光测距组分别向水平工作台面的x轴方向、y轴方向发射激光,每组激光测距组包括两个激光测距仪;标定方箱三303和标定方箱四304为一组,标定方箱三303和标定方箱四304与后部参考装置20的后标定靠板2016上的两组激光测距组配合、用于校准的角度编码盘二2013的初始位置,标定方箱三303和标定方箱四304分设在后部参考装置20的两侧,标定方箱三303右侧边与水平水平工作台面的纵边平齐,且右侧边与左侧边相互平行;标定方箱四304后侧边与水平水平工作台面的横边平齐,且后侧边与前侧边相互平行,标定方箱三303和标定方箱四304上平面高于后部参考装置20的后标定靠板2016上平面,后标定靠板2016上平面的两组激光测距组分别向水平工作台面的x轴方向、y轴方向发射激光,每组激光测距组包括两个激光测距仪。
21.前部参考装置10、后部参考装置20的校准原理:前部参考装置10、后部参考装置20的角度编码盘旋转,前标定靠板1016上放置有激光测距仪,其中x轴方向两个激光测距仪测量标定箱一301,y轴方向两个激光测距仪测量标定箱二302,当满足x轴方向两个激光测距仪测到标定箱一301两端部的距离一致、且y轴方向两个激光测距仪测到标定箱二302两端部的距离一致时,前标定靠板1016的x轴、y轴方向与水平工作台面的x轴、y轴方向平行;同理后标定靠板2016上放置有激光测距仪,其中x轴方向两个激光测距仪测量标定箱三303,y轴方向两个激光测距仪测量标定箱四304,当满足x轴方向两个激光测距仪测到标定箱三303两端部的距离一致、且y轴方向两个激光测距仪测到标定箱四304两端部的距离一致时,前标定靠板1016的x轴、y轴方向与水平工作台面的x轴、y轴方向平行;设备通电后角度编码器的初始0位会有误差,通过此过程来初始化前部参考装置10、后部参考装置20的角度编码盘,排除其误差。
22.图5~6中,前部参考装置10包括前车牌架1011、地脚固定螺栓一1012、三轴云台一1013、角度编码盘一1014、前标定靠板1016、前伸缩杆1017,前车牌架1011包括底板、连接于底板一侧的立板,立板上设有两个用于与车牌照框内螺栓安装孔对应固定的通过孔,底板两端部上分设有两个螺孔,每个螺孔内均装有地脚固定螺栓一1012,地脚固定螺栓一1012安放在前车牌架1011上一端支撑在试验平台上,与车牌照固定螺栓形成了一个平稳支撑面,1012前车牌架与汽车前保险杠通过螺栓孔里的螺栓固定,由于前车牌架1011及上面的测量装置整体总量较重,车牌照预留螺栓孔无法长时间承受此重量,会出现变形,导致前车牌架1011出现倾斜,为此安装地脚固定螺栓一1012可以有效的分担前保险杠螺栓孔的重量,确保前车牌架1011的垂直状态;三轴云台一1013安装在底板上,角度编码盘一1014安装在三轴云台一1013上,前伸缩杆1017立在角度编码盘一1014的旋转中心上、可随角度编码盘一1014起同轴旋转,三轴云台一1013上装有无线接收器一1020;安置在角度编码盘一1014上的激光发射器一1051、激光发射器二1052向上发射垂直校准激光束与两个激光接收
器一1081,确定前伸缩杆1017是否垂直水平面;如果不垂直重新更换前伸缩杆1017,其中,前伸缩杆1017是垂直基准标定杆,前伸缩杆1017采用碳纤维材质。
23.前伸缩杆1017上放置有前标定靠板1016,前标定靠板1016上x轴和y轴方向各有两个激光测距仪;无线接收器一1020放置在三轴云台一1013上,接收信号并把信号发送给角度编码盘一1014;高容量锂电池1022给角度编码盘一1014、激光扫描测距仪1021、无线接收器1020提供电源。
24.激光校准测距装置的激光扫描测距仪1021设置在前部参考装置10的角度编码盘一1014上、可随角度编码盘一1014一起旋转,前伸缩杆1017为空心结构、且在两端头开设有窗口,两个窗口处分设有上部等腰直角三棱镜1092、下部等腰直角三棱镜1091。
25.图7中,上部等腰直角三棱镜1092、下部等腰直角三棱镜1091的斜边相对平行布置、且斜边中点的连线与伸缩杆的中轴线同轴心,激光扫描测距仪1021发射的水平激光束射入下部等腰直角三棱镜1091斜边的中心点上改变90
°
角,变成垂直光束之后射入上部等腰直角三棱镜1092的中心点上再次改变90
°
角变成水平方向。改变激光发射装置的安装位置,不用在前部参考装置顶端设置较多的结构完成激光发射装置的安装固定,防止前部参考装置的不稳造成的测量度降低问题。
26.图8~9中,后部参考装置20与前部参考装置10的结构大致相同,后部参考装置20包括后车牌架2011、地脚固定螺栓二2012、三轴云台二2014、角度编码盘二2013、激光发射器三2051、激光发射器一四2052、激光接收器二2081、激光接收器三2082、高容量锂电池2021的功能与前部参考装置10功能、结构都相同。后车牌架2011包括底板、连接于底板一侧的立板,立板上设有两个用于与车牌照框内螺栓安装孔对应固定的通过孔,底板两端部上分设有两个螺孔,每个螺孔内均装有地脚固定螺栓二2012,地脚固定螺栓二2012安放在后车牌架2011上;三轴云台二2014安装在底板上,角度编码盘二2013安装在三轴云台二2014上,后伸缩杆2017立在角度编码盘二2013的旋转中心上、可随角度编码盘二2013起同轴旋转;安置在角度编码盘二2013上的激光发射器一三2051、激光发射器四2052向上发射垂直校准激光束,与激光接收器二2081、激光接收器三2082进行标定,确定后伸缩杆2017是否垂直水平面;如果不垂直重新更换后伸缩杆2017,其中,后伸缩杆2017是垂直基准标定杆,后伸缩杆2017采用碳纤维材质。不同的是,激光校准测距装置的光电传感器2019装在后伸缩杆2017的顶端,且光电传感器2019与上部等腰直角三棱镜1092的斜边中心的连线与水平面平齐;无线发射器2020将光电传感器2019的信号发射给前部参考装置10的无线接收器一1020。无线接收器一1020、无线发射器2020与控制器经过无线通讯模块信号互通。
27.图10中,试验前需要把车顶固定板13与待测试车身的行李架21连接成刚性整体。把两个行李架横梁23(购买的成品,其两端有对应车型行李架的夹持装置)平行放置在待测车身顶部两个行李架21之间并固定好;车顶固定板13上预留有腰型孔,螺栓24穿过预留腰型孔与行李架横梁23上的紧固板22通过螺帽25固定,使车顶固定板13牢固的与行李架21成为一个刚性体。
28.图11中,车顶固定板13固定前,需将车顶固定板13沿待测试车身的宽度方向的中心线与待测试车身的中心线对齐。车顶固定板13四侧面预留均预留有两个对称的标定块131,通过中心线标定装置的三轴云台一1031旋转,带激光扫描测距仪1021发射激光束19扫
描车顶固定板13前侧两个标定块131,测量激光扫描测距仪1021发射点到车顶固定板13前侧两个标定块131之间的距离h3、h4,当h3=h4时,认为车顶固定板13沿待测试车身的宽度方向的中心线与待测试车身的中心线对齐,如果距离不对,松开螺帽25调整车顶固定板13相对行李架21的位置,直至测得的距离h3=h4。
29.试验总共需要四个加力模块,四个加力模块分别放置于待测车身的四个面上,待测车身前、后侧的两个加力模块的中心线与待测车身的中心线平齐,待测车身左、右测的两个加力模块的中心线与车顶固定板13长度方向的中心线平齐。通过中心线标定装置的三轴云台一1031旋转,带激光扫描测距仪1021发射激光束19扫描待测车尾部的加力模块两个立柱上预留的对称反光贴,测量激光扫描测距仪1021到两个反光贴的距离h9、h10,当距离h9=h10时,车辆尾部的加力模块中心与车辆y0重合,尾部的加力模块标定结束,保证待测车身尾部的加力模块的拉力方向位于车身的中心线上;同理用此方法测量待测车身前方的加力模块两个立柱上预留的对称反光贴与测量激光扫描测距仪1021之间的距离h1、h2,当h1=h2时,待测车身前方的加力模块的拉力中心与车辆中心线重合,前部的加力模块标定结束;待测车身两侧面放置的两个加力模块,两个导向装置上分别装有一个激光测距仪14,两个激光测距仪14关于升降横杆中线对称,利用其两个立柱上的激光测距仪14随着升降装置4调整到与车顶固定板13的等高,测量与车顶固定板13左、右两个侧边线上的两个标定块131之间的距离,当测得的距离h6=h8,h5=h7时,左右两侧部的的加力模块标定结束。车顶固定板13左、右两个侧边线的同一侧边上的两个标定块131之间的距离与两个激光测距仪14之间的距离一致。
30.图12中,车顶固定板13上端均布有36个应力片,36个所述应力片排布成一个6行6列的矩阵,通过采集均布的应力片可以进行车顶行李架及顶棚力学有限元实时分析。
31.实施例二:通过控制器控制加力模块、中心线标定装置的动作,控制器采用plc。每个加力模块上设用于与控制器经无线通讯模块信号互通的无线接收器二及无线发射器二;中心线标定装置的前部参考装置10的三轴云台上装有无线接收器一1020,后部参考装置20的三轴云台装有无线发射器一2020,无线接收器一1020、无线发射器一2020也与控制器经过无线通讯模块信号互通。
32.试验前试验装置的安装布置过程为:a-1、在试验车辆前、后车牌架处安装前部参考装置10、后部参考装置20,标定好车身中心y0线;a-2、把两个行李架横梁23(购买的成品,其两端有对应车型行李架的夹持装置)平行放置在两个行李架21之间固定好;螺栓24穿过预留腰型孔的车顶固定板13,与紧固板22通过螺帽25固定,使车顶固定板13牢固的与汽车行李架21成为一个刚性体;a-4、把四个加力模块利用各自万向轮11推到试验车辆前方后方及两个侧面放置,利用自带的水平仪7结合地脚螺栓12可以调平;a-3、利用前部参考装置10上的激光扫描测距仪1021,测量到车顶固定板13前侧两个标定块131的距离,使h3=h4,如果距离不对,松开螺帽25调整车顶固定板13相对行李架21的位置,直至测得的距离h3=h4;a-5、用车辆前牌照处的y0对前部参考装置10上的激光扫描测距仪1021,分别测量
车辆尾部的加力模块两个立柱预留的对称反光贴,当测量的距离h9=h10时,车辆尾部的加力模块中心与车辆中心线y0重合,尾部加力模块标定结束;同理用此方法测量车前方加力模块两个立柱预留的对称反光贴101,当测量的距离h1=h2时,车辆前部的加力模块中心与车辆中心线y0重合,车辆前部加力模块标定结束;a-6、由于车顶固定板13四周预留有对称的标定块131,同一侧面的两个标定块131的距离与加力模块上两个激光测距仪14的中心距一致;车辆侧面放置的两个加力模块,利用其加力模块上两个激光测距仪14随着升降装置4调整到与车顶固定板13的等高,测量与车顶固定板1侧面两个标定块131之间的距离,当测得h6=h8,h5=h7,此时左右两侧部的的加力模块标定结束。
33.图13中,将试验车辆前后侧的两个加力模块的挂钩15与车顶固定板13前后侧的中点连接,将试验车辆左右侧的两个加力模块的挂钩15与车顶固定板13左右侧的中点连接。完成后可以开始进行试验。
34.图14中,静态载荷试验过程:1、将试验车辆前后左右四个方向放置的加力模块的电动旋转台6调至初始零位,此时连接在电动旋转台6旋转中心上的滑轮托架5处于水平;2、利用各自的升降装置4将滑轮托架5的顶端与车顶固定板13调至等高的位置上,使从滑轮托架5引出的钢丝绳18水平伸出,末端的挂钩15连接车顶固定板13;3、试验车辆前端的加力模块对车顶固定板13向+x方向施加拉力,其他三个方向上的加力模块处于泄力状态,并通过控制器采集此过程中车顶固定板13上各应力片16在加力过程中应力;4、试验车辆后端的加力模块对车顶固定板13向-x方向施加拉力,其他三个方向上的加力模块处于泄力状态,并通过控制器采集此过程中车顶固定板13上各应力片16在加力过程中应力;5、试验车辆左端的加力模块对车顶固定板13向+y方向施加拉力,其他三个方向上的加力模块处于泄力状态,并通过控制器采集此过程中车顶固定板13上各应力片16在加力过程中应力;6、试验车辆右端的加力模块对车顶固定板13向-y方向施加拉力,其他三个方向上的加力模块处于泄力状态,并通过控制器采集此过程中车顶固定板13上各应力片16在加力过程中应力;7、控制器通过放置在13车顶固定板上的16应力片,可以实时采集到车顶固定板13所受到的应力,并将采集到的数据输入有限元力学分析软件对试验实施力学分析数据,至此试验过程结束。
35.步骤3~6的没有先后顺序要求,步骤3~6之间的间隔时间与法规要求的一致。
36.动态交变载荷试验过程:1、将试验车辆前后左右四个方向放置的加力模块的电动旋转台6调至初始零位,此时连接在电动旋转台6旋转中心上的滑轮托架5处于水平;2、利用各自的升降装置4将滑轮托架5的顶端与车顶固定板13调至等高的位置上,使从滑轮托架5引出的钢丝绳18水平伸出,末端的挂钩15连接车顶固定板13;3、试验车辆前端的加力模块对车顶固定板13向+x方向施加拉力,同时试验车辆左
端的加力模块对车顶固定板13向+y方向施加拉力,其他两个方向上的加力模块处于泄力状态,并通过控制器采集此过程中车顶固定板13上各应力片16在加力过程中应力;4、试验车辆前端的加力模块对车顶固定板13向+x方向施加拉力,同时试验车辆右端的加力模块对车顶固定板13向-y方向施加拉力,其他两个方向上的加力模块处于泄力状态,并通过控制器采集此过程中车顶固定板13上各应力片16在加力过程中应力;5、试验车辆后端的加力模块对车顶固定板13向-x方向施加拉力,同时试验车辆左端的加力模块对车顶固定板13向+y方向施加拉力,其他两个方向上的加力模块处于泄力状态,并通过控制器采集此过程中车顶固定板13上各应力片16在加力过程中应力;6、试验车辆后端的加力模块对车顶固定板13向-x方向施加拉力,同时试验车辆右端的加力模块对车顶固定板13向-y方向施加拉力,其他两个方向上的加力模块处于泄力状态,并通过控制器采集此过程中车顶固定板13上各应力片16在加力过程中应力;7、控制器通过放置在13车顶固定板上的16应力片,可以实时采集到车顶固定板13所受到的应力,并将采集到的数据输入有限元力学分析软件对试验实施力学分析数据,至此试验过程结束。
37.步骤3~6的没有先后顺序要求,步骤3~6之间的间隔时间可根据车企的要求进行更改。
38.图15~16中,非水平静态载荷试验:1、将试验车辆前后左右四个方向放置的加力模块的电动旋转台6调至初始零位,此时连接在电动旋转台6旋转中心上的滑轮托架5处于水平;2、利用各自的升降装置4将滑轮托架5的顶端与车顶固定板13调至等高的位置上;3、利用各自的电动旋转台6旋转带动滑轮托架5旋转俯仰,使从滑轮托架5引出的钢丝绳18与车顶固定板13之间形成夹角a;4、试验车辆前端的加力模块对车顶固定板13向+x方向施加拉力,其他三个方向上的加力模块处于泄力状态,并通过控制器采集此过程中车顶固定板13上各应力片16在加力过程中应力;5、试验车辆后端的加力模块对车顶固定板13向-x方向施加拉力,其他三个方向上的加力模块处于泄力状态,并通过控制器采集此过程中车顶固定板13上各应力片16在加力过程中应力;6、试验车辆左端的加力模块对车顶固定板13向+y方向施加拉力,其他三个方向上的加力模块处于泄力状态,并通过控制器采集此过程中车顶固定板13上各应力片16在加力过程中应力;7、试验车辆右端的加力模块对车顶固定板13向-y方向施加拉力,其他三个方向上的加力模块处于泄力状态,并通过控制器采集此过程中车顶固定板13上各应力片16在加力过程中应力;8、控制器通过放置在13车顶固定板上的16应力片,可以实时采集到车顶固定板13所受到的应力,并将采集到的数据输入有限元力学分析软件对试验实施力学分析数据,至此试验过程结束。
39.步骤4~7的没有先后顺序要求,步骤3~6之间的间隔时间可根据车企的要求进行更改。
40.非水平动态及载荷试验1、将试验车辆前后左右四个方向放置的加力模块的电动旋转台6调至初始零位,此时连接在电动旋转台6旋转中心上的滑轮托架5处于水平;2、利用各自的升降装置4将滑轮托架5的顶端与车顶固定板13调至等高的位置上;3、利用各自的电动旋转台6旋转带动滑轮托架5旋转俯仰,使从滑轮托架5引出的钢丝绳18与车顶固定板13之间形成夹角a;4、试验车辆前端的加力模块对车顶固定板13向+x方向施加拉力,同时试验车辆左端的加力模块对车顶固定板13向+y方向施加拉力,其他两个方向上的加力模块处于泄力状态,并通过控制器采集此过程中车顶固定板13上各应力片16在加力过程中应力;5、试验车辆前端的加力模块对车顶固定板13向+x方向施加拉力,同时试验车辆右端的加力模块对车顶固定板13向-y方向施加拉力,其他两个方向上的加力模块处于泄力状态,并通过控制器采集此过程中车顶固定板13上各应力片16在加力过程中应力;6、试验车辆后端的加力模块对车顶固定板13向-x方向施加拉力,同时试验车辆左端的加力模块对车顶固定板13向+y方向施加拉力,其他两个方向上的加力模块处于泄力状态,并通过控制器采集此过程中车顶固定板13上各应力片16在加力过程中应力;7、试验车辆后端的加力模块对车顶固定板13向-x方向施加拉力,同时试验车辆右端的加力模块对车顶固定板13向-y方向施加拉力,其他两个方向上的加力模块处于泄力状态,并通过控制器采集此过程中车顶固定板13上各应力片16在加力过程中应力;8、控制器通过放置在13车顶固定板上的16应力片,可以实时采集到车顶固定板13所受到的应力,并将采集到的数据输入有限元力学分析软件对试验实施力学分析数据,至此试验过程结束。
41.步骤4~7的没有先后顺序要求,步骤3~6之间的间隔时间可根据车企的要求进行更改。