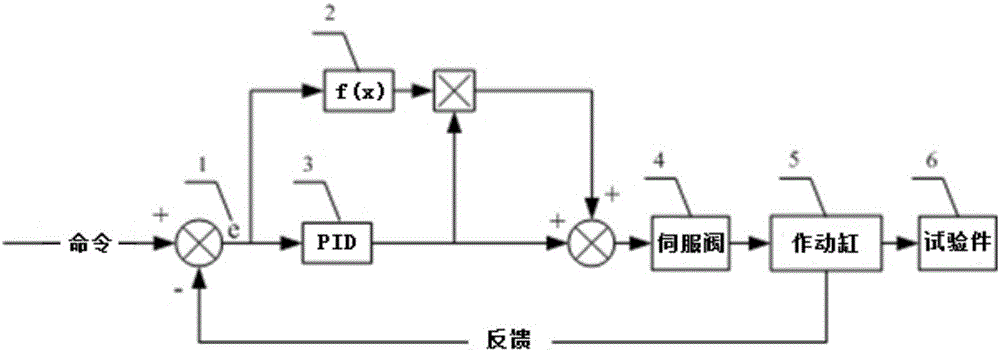
本发明属于结构试验控制领域,特别涉及航空试验加载控制系统,具体涉及一种伺服控制信号补偿方法。
背景技术:
:飞机结构强度试验采用经典比例、积分、微分(PID)控制进行试验载荷控制。试验中受商业控制设备的限制,PID参数整定后难以自适应实时更改,如图1所示。对于这种常规控制,一般是在低载情况下整定PID控制参数,整定后在整个试验过程中PID都不会再改变,所以当试验进入高载阶段时,试验件刚度、液压流量、油管压降、机械连接等情况都可能发生改变,控制误差变化较大,不可变PID参数难以适应时刻改变的试验状态,导致加载点误差增大,影响试验运行,试验成本和风险增大,而实时改变的PID参数研究又难以适用于商业控制设备(存在技术封锁,开放度较低)。技术实现要素:本发明的目的在于提供一种伺服控制信号补偿方法,利用伺服阀控制信号自补偿技术控制载荷误差。本发明的目的通过如下技术方案实现:一种伺服控制信号补偿方法,包括如下步骤:步骤一,建立结构强度试验系统仿真模型,包括:伺服阀控制补偿模型,包括用于判断是否进行伺服阀控制信号补偿的控制部分、用于处理所述控制误差的PID控制设备模型部分,以及为伺服阀控制信号进行补偿的补偿规则部分;试验件模型,为结构强度试验对象;液压系统模型,用于接收所述PID控制设备模型输出的信号,并且对所述试验件模型进行施加载荷;步骤二,对所述结构强度试验系统仿真模型进行模拟仿真结构强度试验;步骤三,仿真得到伺服阀控制信号的补偿规则;步骤四,将步骤三仿真得到的补偿规则写入PID控制设备输出的信号控制通道中,对结构强度试验系统进行实际结构强度试验。优选地是,所述步骤三中的补偿规则为其中,x为控制对象误差,a为补偿系数,b为补偿条件,a与b通过仿真确定。优选地是,所述液压系统模型包括伺服阀模型和作动模型,所述伺服阀模型用于接收所述PID控制设备模型输出的信号控制所述作动缸模型,所述作动缸模型用于执行所述PID控制设备模型的命令对所述试验件模型进行施加载荷。本发明所提供的伺服控制信号补偿方法的有益效果在于,该方法不试图去实时改变PID参数,而是实时补偿经PID控制设备输出的信号,即伺服阀控制信号,以适应时刻变化的试验状态,降低载荷控制误差。不受商业控制设备限制;试验外界影响因素都可反映到载荷控制误差上,所以只对载荷误差控制即可,无需逐个考虑影响因素;对于需要补偿的任意一个加载点,其只占用一个控制通道,不浪费设备资源;本方法在设备上可以通过编程实现。附图说明图1为现有常规结构强度试验系统示意图;图2为本发明伺服控制信号补偿方法中结构强度试验系统框图;图3为常规结构强度试验系统仿真模型示意图;图4为本发明伺服控制信号补偿方法中结构强度试验系统仿真模型示意图;图5为常规结构强度试验系统仿真模型命令和反馈仿真曲线(未补偿);图6为本发明伺服控制信号补偿方法中结构强度试验系统仿真模型命令和反馈仿真曲线(补偿后);图7为常规结构强度试验系统仿真模型和本发明伺服控制信号补偿方法中结构强度试验系统仿真模型的控制误差仿真曲线;图8为常规结构强度试验系统仿真模型和本发明伺服控制信号补偿方法中结构强度试验系统仿真模型的伺服控制信号仿真曲线。附图标记:1-载荷控制误差、2-补偿函数、3-PID控制设备、4-伺服阀、5-作动缸、6-试验件。具体实施方式为使本发明实施的目的、技术方案和优点更加清楚,下面将结合本发明实施例中的附图,对本发明实施例中的技术方案进行更加详细的描述。在附图中,自始至终相同或类似的标号表示相同或类似的元件或具有相同或类似功能的元件。所描述的实施例是本发明一部分实施例,而不是全部的实施例。下面通过参考附图描述的实施例是示例性的,旨在用于解释本发明,而不能理解为对本发明的限制。基于本发明中的实施例,本领域普通技术人员在没有作出创造性劳动前提下所获得的所有其他实施例,都属于本发明保护的范围。下面结合附图对本发明伺服控制信号补偿方法做进一步详细说明。先对图2中标号做详细说明:1-载荷控制误差,为控制部分,用于判断是否进行伺服阀控制信号补偿,由于试验件6加载情况,刚度情况、载荷情况、液压流量、油管压降情况等影响结构强度试验的因素都会被反映到控制误差上,所以本发明只对载荷误差进行控制即可,无需逐个考虑结构强度试验的外界影响因素;2-补偿函数,为伺服阀控制信号的补偿规则;3-PID控制设备,用于处理控制误差;4-伺服阀,用于接收PID控制设备输出的信号控制作动缸5;5-作动缸,执行PID控制设备的命令,对试验件6进行施加载荷;6-试验件,结构强度试验对象。其中,伺服阀4和作动缸5都是液压系统中的一部分。伺服控制信号补偿方法,通过如下步骤实现:步骤一:选用AMESim软件建立如图2所示的结构强度试验系统仿真模型,包括伺服控制补偿模型、液压系统模型中的伺服阀模型和作动缸模型以及试验件模型。伺服阀控制补偿模型包括控制部分、PID控制设备模型部分、伺服阀控制信号的补偿规则部分,其中,控制部分模拟仿真实际结构强度试验中的载荷控制误差1,用来判断是否进行伺服阀控制信号补偿,PID控制设备模型部分模拟仿真实际结构强度试验中的PID控制设备3,用于处理控制误差,伺服阀控制信号的补偿规则部分为补偿函数2,用于为伺服阀控制信号进行补偿。伺服阀模型模拟仿真实际结构强度试验中的伺服阀4,用于接收PID控制设备模型输出的信号控制作动缸模型。作动缸模型模拟仿真实际结构强度试验中的作动缸5,用于执行PID控制设备模型的命令对试验件模型进行施加载荷。试验件模型模拟仿真实际结构强度试验中的试验件6,为结构强度试验对象。步骤二,将伺服阀4、作动缸5、试验件6等各组件的参数编辑录入结构强度试验系统仿真模型中,进行模拟仿真结构强度试验。步骤三,在模拟仿真结构强度试验的低载情况下,并且伺服阀控制信号无补偿时,得到低载整定的PID控制参数。在高载情况下,由于外界因素影响,载荷控制误差1增大,通过模拟仿真将载荷控制误差1降低到低载情况时水平,得到伺服阀控制信号的补偿规则,即补偿函数2被确定。f(x)=a(|x|≥b)0(|x|<b)---(1)]]>其中,x为控制对象误差,a为补偿系数,b为补偿条件,a与b通过仿真确定;当补偿系统a=0,为伺服阀控制信号低载无补偿情况。步骤四,以低载情况下的整定试验系统的PID控制设备的控制参数为基础,将步骤三仿真得到的补偿函数2编程写入PID控制设备输出的信号控制通道中,进行实际结构强度试验。下面举例如下:基于AMESim仿真软件,在AMESim草图模式下,构建常规结构强度试验系统仿真模型和本实施例的结构强度试验系统仿真模型,如图3和图4所示,两仿真模型均采用PID控制器控制;液压系统中的伺服阀模型选择穆格型号伺服阀;液压系统中的作动缸模型采用非对称缸;机械部分由质量弹簧阻尼系统构成;油压部分利用液压泵实现,外接一个溢流阀和减压装置,其中,机械部分、油压部分、溢流阀和减压装置都统称试验件模型。图3和图4的唯一区别在于图4中用控制误差判断,用伺服控制信号自补偿,而图3伺服阀无补偿。仿真参数见表1所示,伺服阀选择穆格3002B型阀,作动缸为吨位2t,行程1m的非对称缸,供油压力恒定为21MPa,弹簧阻尼系统的刚度和阻尼由验证试验的试验件悬臂框架一阶模态计算而得。仿真中,先进行无补偿试验系统的仿真,即PID调试后试验中不发生改变,然后进行试验系统伺服阀补偿控制仿真研究,并总结伺服阀补偿规律。表1无补偿情况,只利用调节PID参数来控制载荷误差。注意到,调节PID时,由于微分增益对试验影响较大,实际结构试验中一般设置为0,本仿真遵从这条经验。利用图3所示的试验系统,调试P=5,I=1.5,D=0。无补偿情况下信号跟踪性能较差,反馈信号发生相位滞后和过冲现象,如图5所示;载荷误差达到0.7%左右,如图7所示;伺服控制信号大约在0.2,如图8所示。由于作动缸输出力在P>5时起振,如图5所示,所以P只能调到5。可见,无补偿情况在高载阶段控制载荷误差还是偏大的,达到了0.7%,而低载时载荷误差为0.4%。若要降低高载误差只能牺牲试验系统的稳定性,但是试验系统不稳定可能对试验件和设备造成损伤。下面利用伺服控制信号补偿技术以降低高载控制误差,使误差恢复到低载情况。利用图4所示的结构强度试验系统仿真模型进行伺服控制信号补偿研究,保持P=5,I=1.5,D=0不变。当a=0.4,b=0.025%时,可得图6~图8所示仿真曲线。很明显,伺服控制信号获得补偿后,反馈信号的过冲和相位滞后明显降低,如图6所示;高载阶段载荷控制误差达到0.4%左右,如图7所示,相对无补偿情况载荷误差得到了有效控制;如图8所示,两图线相重合的部分未进行伺服控制信号补偿,未重合部分在进行补偿,补偿后的伺服控制信号大约在0.3,相对无补偿情况,其明显增大,补偿了高载阶段伺服控制信号的损失,这种伺服控制信号的损失是载荷误差降低的主要原因,而引起伺服控制信号损失的原因是高载阶段试验外界条件的变化,包括载荷变化,试验件刚度变化,油液变化等。可见,当a=0.4,b=0.025%时,本文伺服阀补偿控制能够有效控制高载阶段载荷误差,并将误差控制到0.4%附近。所以最终伺服阀补偿公式可写成式(2)。f(x)=0.4(|x|≥0.025%)0(|x|<0.025%)---(2)]]>得到a=0.4,b=0.025%。a和b的取值会根据设备参数不同而改变,a和b的取值通过仿真确定。然后再将得到的补偿规则即式(2)方程,通过编程写入PID控制设备输出的信号控制通道中,进行实际结构强度试验。本方法不试图去实时改变PID参数,而是实时补偿经PID控制设备输出的信号,即伺服阀控制信号,以适应时刻变化的试验状态,降低载荷控制误差,同时试验外界影响因素都可反映到载荷控制误差上,所以只对载荷误差控制即可,无需逐个考虑影响因素。以上所述,仅为本发明的具体实施方式,但本发明的保护范围并不局限于此,任何熟悉本
技术领域:
的技术人员在本发明揭露的技术范围内,可轻易想到的变化或替换,都应涵盖在本发明的保护范围之内。因此,本发明的保护范围应以所述权利要求的保护范围为准。当前第1页1 2 3