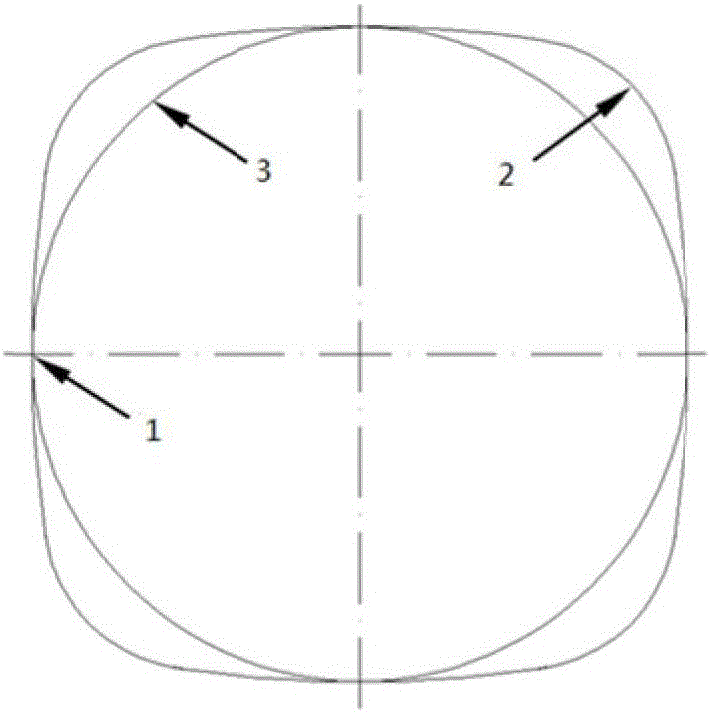
本发明属于航空发动机涡轮转子部件的结构优化设计,尤其涉及涡轮盘双轴对称异型螺栓孔的轮廓形状的多目标优化设计模型。
背景技术:
:航空发动机高压涡轮盘长期工作环境恶劣,其前安装边上螺栓圆孔常因应力集中现象,产生孔边裂纹,成为轮盘失效的一个重要原因。专利“多圆弧异型孔”(专利号:ZL201310287309.9)提出了可采用一种八圆弧异型孔结构。但仍存在如下不足:1.已有的优化模型中的目标函数的最优值存在过度优化现象(即孔边应力下降幅超过设计要求)。2.优化设计结果过分依赖于设计变量取值范围的设定,实际设计中,需不断试算以确定合理的设计变量取值范围,设计效率低。3.优化设计结果鲁棒性差,优化过程收敛速度较慢。技术实现要素:发明目的:为了克服现有技术中存在的不足,本发明提供一种基于最小轮廓变化的两参量异型螺栓孔稳健设计方法,该方法可避免优化设计时繁琐、低效的边界试算,提高设计的合理性及稳定性,同时大大提高设计效率。技术方案:为实现上述目的,本发明采用的技术方案为:一种基于最小轮廓变化的两参量异型螺栓孔稳健设计方法,包括以下步骤:步骤1.根据任务给定目标值、主圆弧半径、过渡圆弧半径以应力下降目标、异型孔主圆弧尺寸变化目标以及过渡圆弧尺寸变化目标建立异型孔多目标优化模型。步骤2.根据主圆弧半径上界、过渡圆弧半径下界确定步骤1中的异型孔多目标优化模型的尺寸约束。步骤3.引用加权系数,将异型孔多目标优化模型转化为异型孔单一综合目标优化模型。步骤4.根据定轮廓变化值和允许的误差对异型孔单一综合目标优化模型进行优化,获得异型孔各设计变量,完成异型孔的设计。所述步骤1中异型孔多目标优化模型建立方法包括以下步骤:步骤11,根据任务给定目标值、主圆弧半径、过渡圆弧半径建立无量纲应力下降幅目标函数。步骤12,根据原螺栓通孔半径、主圆弧半径建立主圆弧半径无量纲异型孔轮廓控制目标函数。步骤13,根据原螺栓通孔半径、过渡圆弧半径建立过渡圆弧半径无量纲异型孔轮廓控制目标函数。步骤14,根据步骤11建立的无量纲应力下降幅目标函数、步骤12建立的主圆弧半径无量纲异型孔轮廓控制目标函数、步骤13建立的过渡圆弧半径无量纲异型孔轮廓控制目标函数建立异型孔多目标优化模型。所述步骤11中无量纲应力下降幅目标函数的表达式如下:f1(σmax)=min{|σmax-σo|σ0}.]]>f1(σmax)为无量纲应力下降幅目标函数,σmax为孔边最大主应力,σmax=σmax(R1,R2),R1为主圆弧半径,R2为过渡圆弧半径,σo表示任务给定目标值。所述步骤12中主圆弧半径无量纲异型孔轮廓控制目标函数的表达式如下:f2(R1)=min|R1-R*|R*.]]>其中,f2(R1)主圆弧半径无量纲异型孔轮廓控制目标函数,R1为主圆弧半径,R*表示原螺栓通孔半径。所述步骤13中过渡圆弧半径无量纲异型孔轮廓控制目标函数的表达式如下:f3(R2)=min|R*-R2|R*.]]>其中,f3(R2)为过渡圆弧半径无量纲异型孔轮廓控制目标函数,R2为过渡圆弧半径,R*表示原螺栓通孔半径。所述步骤14中异型孔多目标优化模型的表达式如下:minf{y1=f1(σmax),y2=f2(R1),y3=f3(R2)}。所述步骤2中建立的尺寸约束为:s.t.R*<R1<R1maxR2min<R2<R*]]>其中,R1max为主圆弧半径上界,R2min为过渡圆弧半径下界,R1为主圆弧半径,R2为过渡圆弧半径,R*表示原螺栓通孔半径。所述步骤3中的异型孔单一综合目标优化模型为:f(f1,f2,f3)=k1·f1(σmax)+k2·f2(R1)+k3·f3(R2)。其中,k1为量纲应力下降幅目标函数的加权系数,f1(σmax)为无量纲应力下降幅目标函数,k2为主圆弧半径无量纲异型孔轮廓控制目标函数的加权系数,f2(R1)主圆弧半径无量纲异型孔轮廓控制目标函数,k3为过渡圆弧半径无量纲异型孔轮廓控制目标函数的加权系数,f3(R2)为过渡圆弧半径无量纲异型孔轮廓控制目标函数。所述步骤3中加权系数的确定方法如下:量纲应力下降幅目标函数的加权系数k1、主圆弧半径无量纲异型孔轮廓控制目标函数的加权系数k2、过渡圆弧半径无量纲异型孔轮廓控制目标函数的加权系数k3随R1主圆弧半径的取值范围以及σo应力目标值的不同而动态变化,其中:主圆弧半径R1和过渡圆弧半径R2取值范围变化时,对孔边应力的影响不同。R1max变化时:k2=0.008~0.012k2和k3之间满足:k3=g1(k2,R1max)=(1.25~2.1)·k2·R1maxk1与k2,k3之间满足:k1=g2(k2,k3,σ0)=σ0(σ1r-σ0)·[k2·f2(R1)+k3·f3(R2)].]]>其中,σ1r为原圆形螺栓通孔孔边最大主应力值。所述步骤4中对异型孔单一综合目标优化模型进行优化时,只有在优化后的异型孔孔边应力达到既定要求,即|σmax-σo|≤ε,ε为允许误差。且异型螺栓孔与原螺栓圆形通孔相比,轮廓变化小于给定轮廓变化值时,设计参数或变量才是满足要求的优化值。有益效果:本发明提供的一种基于最小轮廓变化的两参量异型螺栓孔稳健设计方法,相比现有技术,具有以下有益效果:1.完善了两变量异型孔优化问题的优化目标,使得到的优化解可按预期目标降低孔边应力。2.优化设计获得的异型孔轮廓尺寸既可满足应力下降到规定值,又不至偏离原有轮廓过大,因而设计更加稳健。3.克服了原优化结果对设计变量取值范围的过分依赖的问题,无需再优化设计中反复调整异型孔各圆弧尺寸(R1,R2)的设计范围,从而提高了优化设计点的稳定性,使得最终设计方案更加合理,设计效率也明显提高。附图说明图1是加权系数k1,k2,k3的动态确定流程图;图2是基于多目标两变量优化模型下得到的异型孔轮廓;其中:1-两变量异型孔主圆弧R1;2-两变量异型孔过渡圆弧R2;3-传统螺栓通孔(基圆)。具体实施方式下面结合附图和具体实施例,进一步阐明本发明,应理解这些实例仅用于说明本发明而不用于限制本发明的范围,在阅读了本发明之后,本领域技术人员对本发明的各种等价形式的修改均落于本申请所附权利要求所限定的范围。一种基于最小轮廓变化的两参量异型螺栓孔稳健设计方法,该模型针对航空发动机高压涡轮盘上的异型螺栓通孔(以下简称异型孔)轮廓优化问题,提出了一种稳健设计方法,即在优化设计中,采用(a)减小孔边应力至任务规定值和(b)控制异型孔轮廓变化幅度(即避免异型孔轮廓与原圆形轮廓差异过大)等优化目标,以此来获得合理、稳健的设计方案。在优化模型中,通过对每个优化目标进行合理的加权求和处理,建立了异型孔综合优化设计模型。在综合优化模型中,由于每个目标的权重将随异型孔设计变量取值范围的变化而变化,为此专利发明者设计了一种可保持不同设计目标对综合优化目标贡献均衡的权重系数动态调整方法,使得与应力控制目标有关的权重系数(k1)与异型孔轮廓设计变量取值范围相关联,在后者发生变化时,k1可自动调整,因而获得了多目标条件下的异型孔均衡优化设计效果,从根本上消除了异型孔各设计变量(即圆弧尺寸)优化结果对设计变量取值范围的依赖性,可快速优化得到满足强度设计任务要求条件且的轮廓尺寸变化最小的最佳异型孔轮廓。本发明使得两变量异型孔轮廓设计可按任务给出的孔边应力目标值进行优化设计,同时无需对异型孔各设计变量尺寸取值范围反复试探调整,设计结果具有较好的一致性。具体包括以下步骤:步骤1.根据任务给定目标值、主圆弧半径、过渡圆弧半径以应力下降目标、异型孔主圆弧尺寸变化目标以及过渡圆弧尺寸变化目标建立异型孔多目标优化模型。具体包括以下步骤:步骤11,根据任务给定目标值、主圆弧半径、过渡圆弧半径建立无量纲应力下降幅目标函数,f1(σmax)为无量纲应力下降幅目标函数,需保证异型孔孔边最大主应力足够逼近于事先设定(任务给定)的某一目标值σo。其表达式如下:f1(σmax)=mindd表示f1(R)所描述的孔边最大主应力σmax与事先设定的应力目标值σo的无量纲差值。f1(σmax)=min{|σmax-σo|σ0}.]]>f1(σmax)为无量纲应力下降幅目标函数,σmax为孔边最大主应力,σmax=σmax(R1,R2),R1为主圆弧半径,R2为过渡圆弧半径,σo表示任务给定目标值。在具体实施时,σo应力目标值需根据设计任务目标及工作条件确定步骤12,根据原螺栓通孔半径、主圆弧半径建立主圆弧半径无量纲异型孔轮廓控制目标函数,该目标函数将使得优化获得的异型孔轮廓与原轮廓差异尽可能小,从而得到更加稳健的设计点。以原螺栓通孔半径R*为基准。其表达式如下:f2(R1)=min|R1-R*|R*]]>其中,f2(R1)主圆弧半径无量纲异型孔轮廓控制目标函数,R1为主圆弧半径,R*表示原螺栓通孔半径。而目标函数f2(R1),f3(R2)保证满足目标f1(R)的前提下,获得的异型孔轮廓尺寸R(R1,R2)尽可能接近传统设计螺栓通孔轮廓,从而获得更加稳健的设计点。f2(R1)=minδ1,f3(R2)=minδ2;其中,δ1,δ2分别表征异型孔主圆弧R1和过渡圆弧半径R2与圆螺栓孔基圆半径的无量纲差,具体如下。步骤13,根据原螺栓通孔半径、过渡圆弧半径建立过渡圆弧半径无量纲异型孔轮廓控制目标函数,该目标函数将使得优化获得的异型孔轮廓与原轮廓差异尽可能小,从而得到更加稳健的设计点。以原螺栓通孔半径R*为基准。其表达式如下:f3(R2)=min|R*-R2|R*]]>其中,f3(R2)为过渡圆弧半径无量纲异型孔轮廓控制目标函数,R2为过渡圆弧半径,R*表示原螺栓通孔半径。优化设计中,确定设计变量取值范围时,R1max(主圆弧半径上界)可根据实际螺栓孔直径取为8~20R*(R*为基圆半径);R2min为过渡圆弧半径下界,取决于实际加工条件下的最小半径,可取实际用最小直径刀具半径。步骤14,根据步骤11建立的无量纲应力下降幅目标函数、步骤12建立的主圆弧半径无量纲异型孔轮廓控制目标函数、步骤13建立的过渡圆弧半径无量纲异型孔轮廓控制目标函数建立异型孔多目标优化模型,其表达式如下:minf{y1=f1(σmax),y2=f2(R1),y3=f3(R2)}求解具体优化问题时,所有设计点Ri(R1,R2)对应目标函数的f1,f2,f3可构成一个判据空间,用F表示,如下:F={fi(f1,f2,f3)∈R3|f1=f1(σmaxi),f2=f2(R1),f3=f3(R2)}fi=(f1,f2,f3)为三个目标函数值组成的向量。寻优过程即为对判据空间中所有向量fi的评估过程。σmax=σmax(R1,R2),R1,R2分别代表主圆弧和过渡圆弧,它们代表了设计点R;f1(σmax)为与设计点R(R1,R2)对应的应力下降幅目标函数;f2(R1)为主圆弧R1变化控制目标函数;f3(R2)为过渡圆弧R2变化控制目标函数。R*为基圆(即传统设计螺栓通孔)半径,R1max为主圆弧半径上界,R2min为过渡圆弧半径下界。异型孔多目标优化模型满足:(1)降低孔边应力至强度设计任务给定目标;(2)孔轮廓尺寸改变最小;(3)有效降低优化所得的异型孔轮廓尺寸对设计变量取值范围的依赖性,提高设计的鲁棒性。步骤2.根据主圆弧半径上界、过渡圆弧半径下界确定步骤1中的异型孔多目标优化模型的尺寸约束。其尺寸约束为:s.t.R*<R1<R1maxR2min<R2<R*]]>其中,R1max为主圆弧半径上界,可在合理范围内任意取值,R2min为过渡圆弧半径下界,R1为主圆弧半径,R2为过渡圆弧半径,R*表示基圆,即传统设计(原)螺栓通孔半径。步骤3.引用加权系数,将异型孔多目标优化模型转化为异型孔单一综合目标优化模型,即对目标f1(σmax)、f2(R1)和f3(R2)进行加权求和处理,将多目标优化问题简化为单一综合目标。异型孔单一综合目标优化模型为:f(f1,f2,f3)=k1·f1(σmax)+k2·f2(R1)+k3·f3(R2)。其中,k1为量纲应力下降幅目标函数的加权系数,f1(σmax)为无量纲应力下降幅目标函数,k2为主圆弧半径无量纲异型孔轮廓控制目标函数的加权系数,f2(R1)主圆弧半径无量纲异型孔轮廓控制目标函数,k3为过渡圆弧半径无量纲异型孔轮廓控制目标函数的加权系数,f3(R2)为过渡圆弧半径无量纲异型孔轮廓控制目标函数。本发明由三个新目标函数构成的多目标优化设计模型,可以同时对孔边最大主应力下降幅和异型孔轮廓尺寸变化进行控制,使得孔边应力降低幅满足既定目标,孔型设计更为稳健,孔型参数更为稳定。通过加权系数k1,k2,k3可调整三个单一优化目标对综合优化目标的贡献。如附图1所示,加权系数的确定方法如下:量纲应力下降幅目标函数的加权系数k1、主圆弧半径无量纲异型孔轮廓控制目标函数的加权系数k2、过渡圆弧半径无量纲异型孔轮廓控制目标函数的加权系数k3随R1主圆弧半径的取值范围以及σo应力目标值的不同而动态变化,其中:主圆弧半径R1和过渡圆弧半径R2取值范围变化时,对孔边应力的影响不同。R1max变化时:k2=0.008~0.012k2和k3之间满足:k3=g1(k2,R1max)=(1.25~2.1)·k2·R1maxk1与k2,k3之间满足:k1=g2(k2,k3,σ0)=σ0(σ1r-σ0)·[k2·f2(R1)+k3·f3(R2)].]]>其中,σ1r为原圆形螺栓通孔孔边最大主应力值。生成的加权系数k1,k2,k3可使得各设计参量变化更为均衡,获得稳健的设计点。步骤4.根据定轮廓变化值和允许的误差对异型孔单一综合目标优化模型进行优化,获得异型孔各设计变量,完成异型孔的设计。对异型孔单一综合目标优化模型进行优化时,只有在优化后的异型孔孔边应力达到既定要求,即|σmax-σo|≤ε,ε为允许误差。且异型螺栓孔与原螺栓圆形通孔相比,轮廓变化小于给定轮廓变化值时,设计参数或变量才是满足要求的优化值,在所给的多目标优化模型中,要求三个单一目标对综合设计结果贡献均衡。由于加权系数k1,k2,k3与设计变量的取值范围相关,为此给出了加权系数k1,k2,k3动态生成办法,使得k1,k2,k3值可随R1max取值范围的不同,调整取值,以满足三个单一优化目标之间的均衡,最终得到满足强度设计要求、且更为稳健、稳定的设计点,保证三者具有恰当的影响因数,从而保证了最终最优解的鲁棒性。本发明中提出的多目标优化设计方法可在满足应力设计目标(任务值)的基础上,获得孔轮廓改变更小、更加稳健的孔型设计方案;此外,优化设计中,在异型孔圆弧尺寸允许变化范围明显变化时,仍能保持稳定的优化解,使得最终优化设计结果摆脱了对圆弧设计变量设定范围值的依赖,提高了设计效率。该多目标优化模型下得到的两参量异型孔结构如附图2所示。本发明提供了一种新的多目标优化设计模型,可按任务规定的孔边应力下降幅给出稳健、稳定的设计方案。该多目标优化模型由(a)应力下降目标、(b)异型孔主圆弧尺寸R1变化目标和(c)过渡圆弧尺寸R2变化目标构成;多目标优化模型中,三个单一目标(即(a)、(b)和(c))对综合目标的贡献应满足均衡条件;所提供的新模型及算法可避免优化设计时繁琐、低效的边界试算,提高设计的合理性及稳定性,同时大大提高设计效率。以上所述仅是本发明的优选实施方式,应当指出:对于本
技术领域:
的普通技术人员来说,在不脱离本发明原理的前提下,还可以做出若干改进和润饰,这些改进和润饰也应视为本发明的保护范围。当前第1页1 2 3