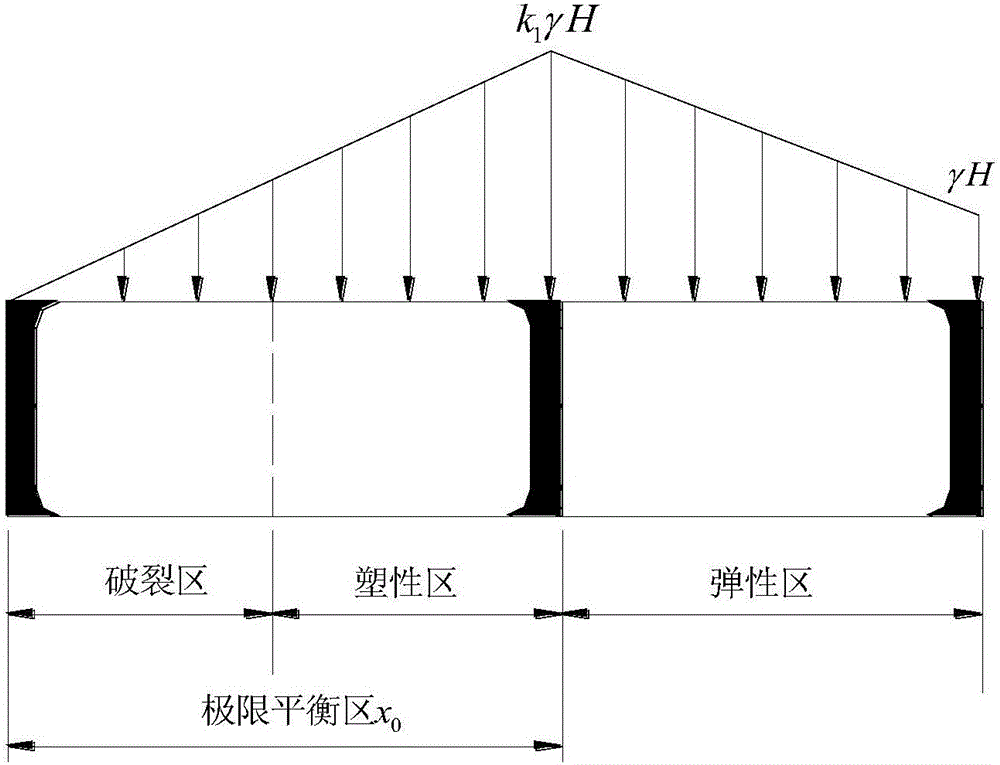
本发明属于巷道施工
技术领域:
,尤其是涉及一种近距离煤层巷道底臌病害防治方法。
背景技术:
:近年来,随着中厚煤层资源的逐步枯竭,近距离薄煤层群开采(也称为近距离煤层开采)成为当今煤炭资源发展的必然趋势之一。通常认为煤层层间距很近,开采时具有显著相互影响的煤层;一般指煤层间距小于30m的煤层。由于近距离煤层中煤层间距较小,受上部煤层开采后遗留煤柱形成的集中压力的影响,围岩变形剧烈,其中巷道两帮的煤体强度通常较顶底板的煤体强度软弱,巷道两帮煤体的变形量大已成为下部回采巷道支护工作的重点和难点,并且诸多专家和现场工程技术人员对此进行了深入研究。其中,张炜通过对近距离煤层巷道变形进行现场实测发现下部煤层的回采巷道布置在应力降低区,依然出现了巷道一帮变形大于另一帮的情形;胡敏军等认为由于下煤层巷道两帮所受的水平应力大小不等,巷道靠近煤柱侧的帮部变形和破坏区大于靠近实体煤侧;张继华等运用数学计算软件分析了近距离下部煤层巷道帮部变形失稳出现的非对称现象,指出靠近煤柱侧的变形情况远远超过靠近实体煤侧;杨智文提出从巷道布置、支护措施、预爆破上覆煤柱等来解决极近距离煤层多采空区下巷道的稳定问题;方新秋采用现场实测、理论分析及数值模拟,通过设计顶板及两帮不同支护参数,分析了不同计算模型下巷道煤帮及顶底板的位移。此外,还有一些文献也通过数值模拟和理论分析对近距离下部煤层巷道围岩的变形及支护技术进行了探讨。由上述内容可知,现如今对近距离下煤层回采巷道变形及其支护的研究取得了较多的成果,但都是采用数值模拟和现场实测来开展的,而基于工程类比或施工经验来确定的开挖、支护方案及参数具有很大的随意性和盲目性。由于近距离采空区下回采巷道的受力环境较单一煤层巷道具有显著的差异,现有单一煤层巷道变形及支护的研究成果并不适用于近距离采空区下的回采巷道。另外,现如今对回采巷道底臌的形成机理及其控制措施进行了深入探讨。但由于煤矿巷道应力状况和围岩性质的复杂性,对底臌机理至今尚没有统一的认识,进而导致现场底臌控制措施的确定大多采用工程类比法和施工人员的经验法,具有相当大的盲目性和对经验的依赖性,底臌治理效果并不理想。工程实际中巷道开挖后,对底板而言,两帮岩体起着传递应力的作用,底臌的发生及发展与两帮支承压力的分布是密切相关的。但目前治理底臌的方法主要集中在底板的处理上,一是加固法,即底板注浆、底板锚杆或封闭式支架;二是卸压法,即底板切缝、底板卸压钻孔或松动爆破;三是巷旁充填法,即把回采巷道两帮一定范围内的煤采出,再填入既有一定的支护阻力又有一定的让压性能的充填材料,使巷帮应力向深部转移。技术实现要素:本发明所要解决的技术问题在于针对上述现有技术中的不足,提供一种近距离煤层巷道底臌病害防治方法,其方法步骤简单、设计合理且实现方便、使用效果好,根据近距离下部煤层巷道的围岩变形情况对巷道两帮预留开挖量分别进行确定,并采用注浆锚杆与巷道支护单元配合对巷道进行有效支护,能有效解决近距离下部煤层巷道的底臌问题。为解决上述技术问题,本发明采用的技术方案是:一种近距离煤层巷道底臌病害防治方法,其特征在于:沿巷道纵向延伸方向由后向前分多个节段对近距离煤层巷道进行开挖及巷道围岩支护施工;所述近距离煤层巷道的横断面为矩形且其为在下部煤层内开采的巷道,所述近距离煤层巷道位于上煤层巷道的一侧下方,所述上煤层巷道为在上部煤层内开采的巷道,所述上部煤层位于下部煤层上方,且上部煤层与下部煤层之间通过夹层进行分隔;所述近距离煤层巷道与上煤层巷道呈平行布设;所述上煤层巷道的一侧为采空区且其另一侧为预留的保护煤柱,所述近距离煤层巷道位于采空区下方;所述近距离煤层巷道靠近上煤层巷道的一侧巷道帮部为煤柱下压侧煤帮,近距离煤层巷道的另一侧巷道帮部为上覆岩层下压侧煤帮;对近距离煤层巷道进行开挖及巷帮围岩支护施工时,多个所述节段的开挖及巷道围岩支护施工方法均相同;对于近距离煤层巷道的任一节段进行开挖及巷道围岩支护施工时,包括以下步骤:步骤一、围岩基本力学参数确定:通过对现场所取岩样进行室内试验,对当前所施工节段的围岩基本力学参数进行测试,并对测试结果进行同步记录;步骤二、巷道两帮预留开挖量确定:根据步骤一中所确定的围岩基本力学参数,对当前施工节段的两侧巷道帮部的预留开挖量分别进行确定;对当前施工节段的上覆岩层下压侧煤帮的预留开挖量进行确定时,根据开挖完成后当前施工节段的上覆岩层下压侧煤帮的向内位移理论值S1进行确定;其中(1);公式(1)中,h为近距离煤层巷道(1)的净高,且a和h单位均为m;Δh为开挖完成后当前所施工节段的顶板最大下沉量;E为当前所施工节段两帮岩体的综合弹性模量且其单位为Pa;P1为当前所施工节段两帮岩体弹塑性界面上的水平压力且P1=λ·k1·γH(2),公式(2)中k1为当前所施工节段两帮岩体弹塑性界面上的应力集中系数,γ为当前所施工节段上覆岩层的平均容重且其单位为N/m3,H为当前所施工节段的埋深且其单位为m,λ为当前所施工节段中弹性地基梁的弹性特征值,所述弹性地基梁为当前所施工节段的两帮岩体;l1=x0+le(3),公式(3)中le为当前所施工节段两帮岩体弹性区的宽度且le=h±Δh',Δh'=0m~0.3m;x0为当前所施工节段的巷帮极限平衡区宽度且(4),公式(4)中c为当前所施工节段巷道两帮岩体的粘聚力,为当前所施工节段巷道两帮岩体的内摩擦角;(5),公式(5)中Ks为当前所施工节段的巷道两帮岩体与顶底板间交界面的切向刚度系数;对当前施工节段的煤柱下压侧煤帮的预留开挖量进行确定时,根据开挖完成后当前施工节段的煤柱下压侧煤帮的向内位移理论值S2进行确定;其中(6);公式(6)中l2为保护煤柱的宽度,P2=λ·k2·γH(8),公式(8)中k2为当前所施工节段的煤柱下压侧煤帮内侧且位于保护煤柱正下方的岩体的应力集中系数;步骤三、巷道开挖:根据步骤二中所确定的当前施工节段的两侧巷道帮部的预留开挖量,由后向前对当前施工节段进行开挖;步骤四、巷道支护结构确定:所采用的巷道支护结构包括多个巷道支护单元和多根注浆锚杆,多个所述巷道支护单元沿近距离煤层巷道的巷道纵向延伸方向由后向前布设,多根所述注浆锚杆沿近距离煤层巷道的巷道纵向延伸方向由后向前布设,且所述巷道支护单元与注浆锚杆呈交错布设;多个所述巷道支护单元的结构均相同;所述巷道支护单元包括布设在近距离煤层巷道底板上的底板支护体系和布设在近距离煤层巷道左右两侧巷道帮上的巷道帮部支护体系,所述底板支护体系和所述巷道帮部支护体系均布设在近距离煤层巷道的同一个巷道断面上;对所述巷道支护单元的支护结构进行确定时,需对所述底板支护体系和所述巷道帮部支护体系的支护结构分别进行确定;其中,所述巷道帮部支护体系所采用的支护结构根据当前所施工节段的巷帮极限平衡区宽度x0进行确定;对所述底板支护体系所采用的支护结构进行确定时,先根据步骤一中所确定的围岩基本力学参数,且根据公式(8-1),计算得出当前所施工节段的巷道底板岩体最大破坏深度hmax;并根据公式(8-2),计算得出当前所施工节段底部左右两侧的巷道底板岩体最大破坏深度处距相邻巷道帮壁的水平距离l0;式(8-1)和(8-2)中,为当前所施工节段巷道底板岩体的内摩擦角;之后,根据所确定的巷道底板最大破坏深度hmax和巷道底板最大破坏深度处至巷道帮壁的水平距离l0,对所述底板支护体系所采用的支护结构进行确定;多根所述注浆锚杆均呈平行布设且其均与当前所施工节段的煤柱下压侧煤帮呈垂直布设;所述注浆锚杆位于当前所施工节段的煤柱下压侧煤帮的中部且其布设在当前所施工节段的一个横断面上;步骤五、巷道围岩支护施工:根据步骤四中所确定的巷道支护结构,对当前所施工节段进行支护施工;步骤六、下一节段开挖及巷道围岩支护施工:重复步骤一至步骤五,对下一节段进行开挖及巷道围岩支护施工;步骤七、多次重复步骤六,直至完成近距离煤层巷道的全部开挖及巷道围岩支护施工过程。上述一种近距离煤层巷道底臌病害防治方法,其特征是:所述近距离煤层巷道为回采巷道且其净高与下部煤层的净高相同;步骤三中进行巷道开挖时,按照常规矿山回采巷道开挖的施工方法,对当前所施工节段进行开挖。上述一种近距离煤层巷道底臌病害防治方法,其特征是:多个所述节段的纵向长度均为10m~50m,所述近距离煤层巷道与上煤层巷道之间的水平间距为8m~12m;所述近距离煤层巷道的煤柱下压侧煤帮内侧岩体由外至内分为第一变形区、第二变形区和第三变形区,所述第一变形区位于采空区下方,第二变形区位于上煤层巷道下方,第三变形区位于保护煤柱下方;所述第二变形区与上煤层巷道的宽度相同,所述第三变形区的宽度与保护煤柱的宽度相同;步骤二中所述的l1为第一变形区的宽度,所述第一变形区由内至外分为破裂区、塑性区和弹性区;所述的k2为当前所施工节段的煤柱下压侧煤帮内侧的第三变形区内岩体的应力集中系数。上述一种近距离煤层巷道底臌病害防治方法,其特征是:步骤二中根据开挖完成后当前施工节段的上覆岩层下压侧煤帮的向内位移理论值S1,对当前施工节段的上覆岩层下压侧煤帮的预留开挖量进行确定时,根据公式Δd1=S1+Δd1(9)进行确定;公式(9)中,Δd1=0.05m~0.12m;根据开挖完成后当前施工节段的煤柱下压侧煤帮的向内位移理论值S2,对当前施工节段的煤柱下压侧煤帮的预留开挖量进行确定时,根据公式Δd2=S2+Δd2(10)进行确定;公式(10)中,Δd2=0.05m~0.12m。上述一种近距离煤层巷道底臌病害防治方法,其特征是:步骤三中进行巷道开挖之前,先根据步骤二中所确定的当前施工节段的两侧巷道帮部的预留开挖量,并结合近距离煤层巷道的设计宽度B,对当前施工节段的上覆岩层下压侧煤帮一侧的实际开挖宽度b1和煤柱下压侧煤帮一侧的实际开挖宽度b2分别进行确定;其中,b1=b+Δd1,b2=b+Δd2,且b和B的单位均为m;当前施工节段的实际开挖宽度b'=b1+b2;步骤三中进行巷道开挖时,根据预先设计的当前所施工节段的巷道中心线,并结合所确定的b1和b2,对当前所施工节段进行开挖。上述一种近距离煤层巷道底臌病害防治方法,其特征是:步骤四中所述注浆锚杆的长度为rm';其中rm'=rm-b2,(11),rm的单位为m;公式(11)中,r0为近距离煤层巷道的等效圆半径且B为近距离煤层巷道的设计宽度,r0、a、b和B的单位均为m;l=2·r0。上述一种近距离煤层巷道底臌病害防治方法,其特征是:步骤四中所述底板支护体系所采用的支护结构为预应力锚杆支护结构;对所述底板支护体系所采用的支护结构进行确定时,根据当前所施工节段的实际开挖宽度b'进行确定:当b'<3m时,所述底板支护体系包括左右两根底板锚杆,两根所述底板锚杆均呈竖直向布设,两根所述底板锚杆分别为第一左侧底板锚杆和第一右侧底板锚杆,所述第一左侧底板锚杆与当前所施工节段左侧巷帮之间的间距以及所述第一右侧底板锚杆与当前所施工节段右侧巷帮之间的间距均为l0;当b'≥3m时,所述底板支护体系包括四根底板锚杆,四根所述底板锚杆均呈竖直向布设,四根所述底板锚杆包括两根第二左侧底板锚杆和两根第二右侧底板锚杆,两根所述第二左侧底板锚杆之间的中心位置与当前所施工节段左侧巷帮之间的水平距离为l0,两根所述第二右侧底板锚杆之间的中心位置与当前所施工节段右侧巷帮之间的水平距离为l0;所述第一左侧底板锚杆、所述第一右侧底板锚杆、两根所述第二左侧底板锚杆和两根所述第二右侧底板锚杆的长度均不小于hmax;所述巷道帮部支护体系所采用的支护结构为预应力锚杆支护结构;所述巷道帮部支护体系所采用的支护结构包括两个分别对称布设在近距离煤层巷道左右两侧巷道帮上的帮部支护结构,两个所述帮部支护结构的结构相同;所述帮部支护结构包括布设在近距离煤层巷道的巷道帮上且呈水平向布设的巷道帮部锚杆;所述巷道帮部锚杆的长度等于l1'+x0+l2',其中l1'=10cm~20cm,l2'=30cm~50cm。上述一种近距离煤层巷道底臌病害防治方法,其特征是:所述底板支护体系所采用的支护结构还包括两个分别对称布设在近距离煤层巷道底板左右两端的帮角锚杆;所述第一左侧底板锚杆、所述第一右侧底板锚杆、两根所述第二左侧底板锚杆和两根所述第二右侧底板锚杆的长度均等于l1'+K·hmax+l2',两个所述帮角锚杆的长度均为L1且l1'=10cm~20cm,l2'=30cm~50cm;K为安全系数且K=1~1.5。上述一种近距离煤层巷道底臌病害防治方法,其特征是:步骤四中前后相邻两根所述注浆锚杆之间的间距为0.8m~1.2m,前后相邻两个所述巷道支护单元之间的间距为0.8m~1.2m。上述一种近距离煤层巷道底臌病害防治方法,其特征是:步骤四中所述巷道帮部支护体系和所述底板支护体系所采用的支护结构均为预应力锚杆支护结构;步骤五中对当前所施工节段进行支护施工时,先由后向前对多根所述注浆锚杆进行施工,再由后向前对多个所述巷道帮部支护体系所采用的支护结构进行施工,之后再由后向前对多个所述底板支护体系所采用的支护结构进行施工。本发明与现有技术相比具有以下优点:1、防治方法步骤简单、实现方便且投入成本低。2、设计合理且实现方便,为确保开挖效果,沿巷道纵向延伸方向由后向前分多个节段对近距离煤层巷道进行开挖;并且,对近距离煤层巷道的任一个节段进行开挖时,先确定围岩基本力学参数,再根据所确定的围岩基本力学参数对当前施工节段的两侧巷道帮部的预留开挖量分别进行确定,最后根据所确定的当前施工节段的两侧巷道帮部的预留开挖量由后向前对当前施工节段进行开挖,施工简便且施工过程易于控制,可操性强。3、所采用的当前施工节段两侧巷道帮部的预留开挖量的确定方法简单、实现简便且使用效果好,所确定的预留开挖量合理、准确,能有效保证确保成型后的近距离煤层巷道内部空间符合设计要求。所确定的预留开挖量分别与上覆岩层下压侧煤帮的向内位移理论值S1和煤柱下压侧煤帮的向内位移理论值S2对应,并且考虑到实际施工中近距离煤层巷道的复杂变形因素,并对上覆岩层下压侧煤帮的向内位移理论值S1和煤柱下压侧煤帮的向内位移理论值S2分别叠加一定的调整量(即Δd1和Δd2)。并且,上覆岩层下压侧煤帮的向内位移理论值S1和煤柱下压侧煤帮的向内位移理论值S2的确定方法简单、合理且精度高,能简便、快速且准确地对上覆岩层下压侧煤帮的向内位移理论值S1和煤柱下压侧煤帮的向内位移理论值S2进行确定。4、所采用的巷道支护结构设计合理且设计过程简单、实现方便,包括多个巷道支护单元和多根注浆锚杆,多个巷道支护单元沿近距离煤层巷道的巷道纵向延伸方向由后向前布设,多根注浆锚杆沿近距离煤层巷道的巷道纵向延伸方向由后向前布设,且巷道支护单元与注浆锚杆呈交错布设,施工简便且施工质量易控。针对近距离煤层巷道的巷帮(也称煤帮)存在的非对称变形情况,开挖完成后在煤柱下压侧煤帮中部布设多根注浆锚杆进行加固,注浆锚杆的长度设计合理,通过多根注浆锚杆能对煤柱下压侧煤帮的整个破裂区进行有效加固,并且省工省料省时。同时,通过合理设计巷道帮部支护体系和底板支护体系所采用的支护结构,对近距离煤层巷道的巷道帮部和底板进行有效加固,能有效解决复杂条件下矩形回采巷道的挤压流动性底臌问题。其中巷道帮部支护体系所采用的支护结构根据巷帮极限平衡区宽度进行确定,且底板支护体系所采用的支护结构根据巷道底板最大破坏深度和巷道底板最大破坏深度处至相邻巷道帮壁的水平距离确定,并辅以巷道帮部支护体系的加固作用来控制回采巷道底臌,在满足支护稳定、可靠且安全的前提下,达到节约成本的目的,具有经济、投入施工成本较低、安全可靠等优点,因而能为矿山正常生产提供有力保障。5、使用效果好且实用价值高,能有效解决煤帮非对称变形后侵入巷道净空并影响巷道正常使用的问题,巷道开挖时两帮预留不同的开挖量,确保成型后的近距离煤层巷道内部空间符合设计要求。首先,根据近距离下部煤层巷道的围岩变形情况对巷道两帮预留开挖量分别进行确定,能有效解决煤帮非对称变形后侵入巷道净空并影响巷道正常使用的问题;同时,采用注浆锚杆与巷道支护单元配合对巷帮和底板进行有效加固、支护,避免了近距离下部煤层巷道的返修工作,且施工成本低。本发明针对采空区下回采巷道煤帮(即近距离煤层巷道煤帮)在上覆岩层及煤柱的支承压力下易产生非对称变形,煤帮破裂厚度及其位移大小直接影响巷道开挖方案及其支护效果。针对现有煤帮破裂范围理论研究的不足和现场实测的客观困难,采用合理的煤帮破裂区厚度确定方法,并根据所确定的破裂区厚度对在煤帮上布置注浆锚杆,并分别考虑上覆岩层与煤柱支承压力及顶底板相对移动对煤帮变形的影响,建立了下煤层巷道两帮不同的位移计算模型,提出了非对称预留开挖方案。由于多数情况下,巷道底臌的发生与两帮岩体的挤压流动有关,因而对支承压力下巷道煤帮的荷载分布规律及其极限平衡区宽度进行研究,进而确定挤压流动条件下巷道底板的破坏深度,并提出相应的底板支护方案及其参数。并且,本发明专利申请所采用的技术方案中运行弹性地基梁理论,在综合考虑巷帮两侧岩体变形以及极限平衡区和弹性区上方支承压力对极限平衡区内岩体变形破坏影响的基础上,对两帮极限平衡区岩体和底板岩体的变形过程进行全面系统的分析,并求得巷帮极限平衡区宽度,进而确定巷道底板岩体在煤帮挤压下产生塑性流动时的最大剪切破坏深度及其与相应煤帮的距离,在此基础上设计两帮及底板的锚杆支护参数,从根本上防治巷道底臌,并且由于巷道顶底板及两帮的变形相互影响,相互制约,本发明所采用的支护方案合理设计巷道底板及两帮的锚杆支护参数,使巷道底板的变形控制在规范允许的范围内,避免底板过度变形破坏后形成底臌灾害,为煤矿的高效高产提供有力的技术保障。综上所述,本发明方法步骤简单、设计合理且实现方便、使用效果好,根据近距离下部煤层巷道的围岩变形情况对巷道两帮预留开挖量分别进行确定,并采用注浆锚杆与巷道支护单元配合对巷道进行有效支护,能有效解决近距离下部煤层巷道的底臌问题,避免了近距离下部煤层巷道的返修工作,且施工成本低。下面通过附图和实施例,对本发明的技术方案做进一步的详细描述。附图说明图1为本发明所建立近距离煤层巷道的巷帮应力计算模型的结构示意图。图2为本发明所建立近距离煤层巷道的巷道两帮岩体弹塑性界面应力计算模型的结构示意图。图3为本发明的巷道开挖方法流程框图。图4为本发明注浆锚杆的布设位置示意图。图5为本发明巷道支护单元所采用支护结构的结构示意图。图6为巷道底板出现挤压流动性底鼓时的力学模型示意图。图7为本发明所建立巷道底板破坏深度计算模型的结构示意图。图8为本发明所建立巷道底板塑性破坏模型的结构示意图。附图标记说明:1—近距离煤层巷道;1-1—第一变形区;1-2—第二变形区;1-3—第三变形区;2—下部煤层;3—上煤层巷道;4—上部煤层;5—夹层;6—采空区;7—保护煤柱;8—注浆锚杆;9—巷道帮部锚杆;10—帮角锚杆;11—竖向底板锚杆。具体实施方式如图3所示一种近距离煤层巷道底臌病害防治方法,其特征在于:沿巷道纵向延伸方向由后向前分多个节段对近距离煤层巷道1进行开挖及巷道围岩支护施工;所述近距离煤层巷道1的横断面为矩形且其为在下部煤层2内开采的巷道,所述近距离煤层巷道1位于上煤层巷道3的一侧下方,所述上煤层巷道3为在上部煤层4内开采的巷道,所述上部煤层4位于下部煤层2上方,且上部煤层4与下部煤层2之间通过夹层5进行分隔;所述近距离煤层巷道1与上煤层巷道3呈平行布设;所述上煤层巷道3的一侧为采空区6且其另一侧为预留的保护煤柱7,所述近距离煤层巷道1位于采空区6下方;所述近距离煤层巷道1靠近上煤层巷道3的一侧巷道帮部为煤柱下压侧煤帮,近距离煤层巷道1的另一侧巷道帮部为上覆岩层下压侧煤帮;对近距离煤层巷道1进行开挖及巷帮围岩支护施工时,多个所述节段的开挖及巷道围岩支护施工方法均相同;对于近距离煤层巷道1的任一节段进行开挖及巷道围岩支护施工时,包括以下步骤:步骤一、围岩基本力学参数确定:通过对现场所取岩样进行室内试验,对当前所施工节段的围岩基本力学参数进行测试,并对测试结果进行同步记录;步骤二、巷道两帮预留开挖量确定:根据步骤一中所确定的围岩基本力学参数,对当前施工节段的两侧巷道帮部的预留开挖量分别进行确定;对当前施工节段的上覆岩层下压侧煤帮的预留开挖量进行确定时,根据开挖完成后当前施工节段的上覆岩层下压侧煤帮的向内位移理论值S1进行确定;其中(1);公式(1)中,h为近距离煤层巷道1的净高,且a和h单位均为m;Δh为开挖完成后当前所施工节段的顶板最大下沉量;E为当前所施工节段两帮岩体的综合弹性模量且其单位为Pa;P1为当前所施工节段两帮岩体弹塑性界面上的水平压力且P1=λ·k1·γH(2),公式(2)中k1为当前所施工节段两帮岩体弹塑性界面上的应力集中系数,γ为当前所施工节段上覆岩层的平均容重且其单位为N/m3,H为当前所施工节段的埋深且其单位为m,λ为当前所施工节段中弹性地基梁的弹性特征值,所述弹性地基梁为当前所施工节段的两帮岩体;l1=x0+le(3),公式(3)中le为当前所施工节段两帮岩体弹性区的宽度且le=h±Δh',Δh'=0m~0.3m;x0为当前所施工节段的巷帮极限平衡区宽度且(4),公式(4)中c为当前所施工节段巷道两帮岩体的粘聚力,为当前所施工节段巷道两帮岩体的内摩擦角,c的单位为Pa;(5),公式(5)中Ks为当前所施工节段的巷道两帮岩体与顶底板间交界面的切向刚度系数;对当前施工节段的煤柱下压侧煤帮的预留开挖量进行确定时,根据开挖完成后当前施工节段的煤柱下压侧煤帮的向内位移理论值S2进行确定;其中(6);公式(6)中l2为保护煤柱7的宽度,P2=λ·k2·γH(8),公式(8)中k2为当前所施工节段的煤柱下压侧煤帮内侧且位于保护煤柱7正下方的岩体的应力集中系数;步骤三、巷道开挖:根据步骤二中所确定的当前施工节段的两侧巷道帮部的预留开挖量,由后向前对当前施工节段进行开挖;步骤四、巷道支护结构确定:所采用的巷道支护结构包括多个巷道支护单元和多根注浆锚杆8,多个所述巷道支护单元沿近距离煤层巷道1的巷道纵向延伸方向由后向前布设,多根所述注浆锚杆8沿近距离煤层巷道1的巷道纵向延伸方向由后向前布设,且所述巷道支护单元与注浆锚杆8呈交错布设;多个所述巷道支护单元的结构均相同;所述巷道支护单元包括布设在近距离煤层巷道1底板上的底板支护体系和布设在近距离煤层巷道1左右两侧巷道帮上的巷道帮部支护体系,所述底板支护体系和所述巷道帮部支护体系均布设在近距离煤层巷道1的同一个巷道断面上;对所述巷道支护单元的支护结构进行确定时,需对所述底板支护体系和所述巷道帮部支护体系的支护结构分别进行确定;其中,所述巷道帮部支护体系所采用的支护结构根据当前所施工节段的巷帮极限平衡区宽度x0进行确定;对所述底板支护体系所采用的支护结构进行确定时,先根据步骤一中所确定的围岩基本力学参数,且根据公式(8-1),计算得出当前所施工节段的巷道底板岩体最大破坏深度hmax;并根据公式(8-2),计算得出当前所施工节段底部左右两侧的巷道底板岩体最大破坏深度处距相邻巷道帮壁的水平距离l0;式(8-1)和(8-2)中,为当前所施工节段巷道底板岩体的内摩擦角;之后,根据所确定的巷道底板最大破坏深度hmax和巷道底板最大破坏深度处至巷道帮壁的水平距离l0,对所述底板支护体系所采用的支护结构进行确定;多根所述注浆锚杆8均呈平行布设且其均与当前所施工节段的煤柱下压侧煤帮呈垂直布设;所述注浆锚杆8位于当前所施工节段的煤柱下压侧煤帮的中部且其布设在当前所施工节段的一个横断面上;步骤五、巷道围岩支护施工:根据步骤四中所确定的巷道支护结构,对当前所施工节段进行支护施工;步骤六、下一节段开挖及巷道围岩支护施工:重复步骤一至步骤五,对下一节段进行开挖及巷道围岩支护施工;步骤七、多次重复步骤六,直至完成近距离煤层巷道1的全部开挖及巷道围岩支护施工过程。如图1所示,所述近距离煤层巷道1的煤柱下压侧煤帮内侧岩体由外至内分为第一变形区1-1、第二变形区1-2和第三变形区1-3,所述第一变形区1-1位于采空区6下方,第二变形区1-2位于上煤层巷道3下方,第三变形区1-3位于保护煤柱7下方;所述第二变形区1-2与上煤层巷道3的宽度相同,所述第三变形区1-3的宽度与保护煤柱7的宽度相同;步骤二中所述的l1为第一变形区1-1的宽度;结合图2,所述第一变形区1-1由内至外分为破裂区、塑性区和弹性区;所述的k2为当前所施工节段的煤柱下压侧煤帮内侧的第三变形区1-3内岩体的应力集中系数。其中,所述第一变形区1-1为破裂区、塑性区和弹性区的宽度之和。本实施例中,将当前所施工节段两帮岩体作为弹性地基梁进行分析。如图1所示,所述上煤层巷道3为已开挖完成的回采巷道,待上部煤层4中的上煤层巷道3开挖完成后,对对应的工作面回采结束后,采空区6的顶板完全垮落并充填采空区6,该上煤层巷道3的另一侧为一定支承压力作用下的保护煤柱7;当下部煤层回采巷道(即近距离煤层巷道1)掘进后,近距离煤层巷道1的两帮在上覆岩层及采空区6内矸石自重应力作用下发生变形或破坏;此外,上部煤柱(即保护煤柱7)的支承压力通过上下煤层之间的夹层(即夹层5,也称中间煤层)传递至下部煤层3。本实施例中,所述近距离煤层巷道1位于上煤层巷道3的左侧下方,所述上煤层巷道3的左侧为采空区6且其右侧为保护煤柱7,由于近距离煤层巷道1的左右帮受力的非对称性,出现了右帮变形破裂较左帮严重的非对称现象。结合图2,所建立的近距离煤层巷道的巷道两帮岩体弹塑性界面应力计算模型为基于弹性地基梁理论建立的应力计算模型,且所建立的巷道两帮岩体界面应力计算模型为在无支护情况下的力学模型,所建立的力学模型中所述第一变形区1-1由近距离煤层巷道1的帮壁向内依次形成破裂区、塑性区和弹性区,其中破裂区和塑性区的岩体处于应力极限平衡状态,所述破裂区和塑性区组成极限平衡区。所述近距离煤层巷道1开挖初期,煤帮处于弹塑性状态,其表面部分的弹性变形能很快消失,塑性区进一步扩展至弹塑性边界。煤帮表面的煤体在垂直压力的作用下持续地向巷道空间内产生径向变形,直至在煤帮塑性区的某个界面上产生离层后形成破裂区。本实施例中,步骤二中根据开挖完成后当前施工节段的上覆岩层下压侧煤帮的向内位移理论值S1,对当前施工节段的上覆岩层下压侧煤帮的预留开挖量进行确定时,根据公式Δd1=S1+Δd1(9)进行确定;公式(9)中,Δd1为当前施工节段的上覆岩层下压侧煤帮的预留开挖量,Δd1=0.05m~0.12m;根据开挖完成后当前施工节段的煤柱下压侧煤帮的向内位移理论值S2,对当前施工节段的煤柱下压侧煤帮的预留开挖量进行确定时,根据公式Δd2=S2+Δd2(10)进行确定;公式(10)中,Δd2为当前施工节段的煤柱下压侧煤帮的预留开挖量,Δd2=0.05m~0.12m。本实施例中,步骤三中进行巷道开挖之前,先根据步骤二中所确定的当前施工节段的两侧巷道帮部的预留开挖量,并结合近距离煤层巷道1的设计宽度B,对当前施工节段的上覆岩层下压侧煤帮一侧的实际开挖宽度b1和煤柱下压侧煤帮一侧的实际开挖宽度b2分别进行确定;其中,b1=b+Δd1,b2=b+Δd2,且b和B的单位均为m;当前施工节段的实际开挖宽度b'=b1+b2;步骤三中进行巷道开挖时,根据预先设计的当前所施工节段的巷道中心线,并结合所确定的b1和b2,对当前所施工节段进行开挖。本实施例中,步骤四中所述注浆锚杆8的长度为rm';其中rm'=rm-b2,(11),rm的单位为m;公式(11)中,r0为近距离煤层巷道1的等效圆半径且B为近距离煤层巷道1的设计宽度,r0、a、b和B的单位均为m;l=2·r0。本实施例中,所述注浆锚杆8呈水平布设。并且,前后相邻两根所述注浆锚杆8之间的间距为0.8m~1.2m。本实施例中,前后相邻两根所述注浆锚杆8之间的间距为1m。实际施工时,可根据具体需要,对前后相邻两根所述注浆锚杆8之间的间距进行相应调整。通过对从当前所施工节段的煤柱下压侧煤帮中部向内布设的注浆结构的变形情况进行分析发现:该注浆结构长度方向上煤体在支承压力下产生的径向变形量并不相同,越靠近煤帮表面,其周围煤体的碎胀变形越大,径向位移量也越大。对整个注浆结构而言,由于其长度方向上各点周围煤体的径向位移速率不同,该注浆结构与其周围煤体之间必将产生相对位移而引起摩阻剪应力。所述注浆结构靠近煤帮表面的一个注浆段具有阻止周围煤体向巷道内径向变形的趋势,该注浆段表面产生指向巷道内的摩阻力;所述注浆结构的其余注浆段则在自身拉拔作用下产生指向煤帮深部的摩阻力。因而,所述注浆结构上存在一个表面摩阻力指向相反的分界点,该分界点为所述注浆结构与其周围煤体相对位移为零的中性点,该点摩阻力为零。但该分界点处,所述注浆结构的轴向拉力达到最大且由该分界点向注浆结构的两端轴向拉力逐渐减少并趋于零。所述注浆结构为从当前所施工节段的煤柱下压侧煤帮中部向内水平钻孔,并在所成型钻孔内注浆而成。而煤帮岩体的位移则由所述注浆结构的孔口至孔底呈逐步递减的分布规律。由公式(11)可知,随着近距离煤层巷道1的等效圆半径r0的增加,所述砂浆结构的长度相应增大,其中性点(即所述分界面)逐渐向巷道深部延伸,表明巷道帮部的破裂区宽度也相应增大。本实施例中,采用注浆锚杆8对当前所施工节段的煤柱下压侧煤帮进行加固,并且注浆锚杆8的长度为rm'。其中,rm'=Ls,Ls为当前所施工节段的煤柱下压侧煤帮的破裂区宽度。并且,所述的rm为当前所施工节段的巷道中心线至所述分界点的水平间距。所述分界点位于所述第一变形区1-1中破裂区和塑性区之间的分界面上。所述注浆锚杆8的直径为Φ0.02m。因而,本发明将注浆锚杆8的长度设定为rm',能有效满足对煤柱下压侧煤帮破裂区的加固需求,并且不会造成材料浪费,省工省时。根据公式(1)可知,当前施工节段的上覆岩层下压侧煤帮的向内位移理论值S1为煤体自身变形产生的煤帮表面向巷道内的位移与顶底板发生相对移动而产生的煤帮位移之和,其中煤体自身变形产生的煤帮表面向巷道内的位移为顶底板发生相对移动而产生的煤帮位移为根据公式(6)可知,当前施工节段的煤柱下压侧煤帮的向内位移理论值S2为煤体自身变形产生的煤帮表面向巷道内的位移、顶底板发生相对移动而产生的煤帮位移与第三变形区1-3内煤体自身变形产生的煤帮表面向巷道内的位移之和,其中第三变形区1-3内煤体自身变形产生的煤帮表面向巷道内的位移为(7)。由公式(1)和公式(6)能看出,下煤层回采巷道(即近距离煤层巷道1)的帮部将出现严重的非对称位移现象,靠近煤柱侧煤体的变形后产生的位移远大于靠近实体煤侧(即煤柱下压侧煤帮一侧的变形量远大于上覆岩层下压侧煤帮一侧的变形量),这与大量的现场实测结果高度吻合。因此,在设计巷道开挖宽度时,两帮需预留不同的开挖量,以避免煤帮非对称变形后侵入净空,影响巷道正常使用。本实施例中,步骤一中进行围岩基本力学参数确定之前,先从当前所施工节段中选取一个节段作为测试段,所述测试段位于当前所施工节段后端且其长度为1m。步骤一中进行围岩基本力学参数确定时,从所述测试段取岩样进行室内试验,且所获得的试验结果为开挖后当前所施工节段的围岩基本力学参数。并且,鉴于回采巷道(即近距离煤层巷道1)围岩的非均质、非连续及各向异性等特性,其力学参数必须在试验的基础上来确定,以确保数据准确可靠,减小计算误差。本实施例中,陕西澄合百良旭升煤矿主采煤层为4号煤层(即上部煤层4)和5号煤层(即下部煤层2)。其中,4号煤层的平均厚度为1.5m,大部分可采,平均埋深为487.3m;5号煤层的平均厚度5.37m,全部可采,平均埋深为380.6m(即H=380.6m)。两个煤层的平均层间距为4.05m(即夹层5的平均层厚为4.05m),属于典型的近距离煤层,采用下行开采方式,即先采4号煤层,预留宽度为20m的保护煤柱7(即l2=20m),再开采5号煤层。4号煤层回采后,5号煤层工作面的运输顺槽(即近距离煤层巷道1)布置在4号煤层的采空区6下并与4号煤区段的保护煤柱7内错8m处,巷道断面为4.0m×3.5m,即h=2a=3.5m,B=4.0m;原设计采用“锚杆+锚索+网”的对称支护方案。由于忽略了巷道帮部受力及变形的非对称性,尽管5号煤层的运输顺槽布置在应力降低区,巷道帮部依然出现了严重的非对称变形,帮部锚杆(索)不同程度地“翻盘”,严重影响5号煤层的正常开采。本实施例中,步骤二中所述的当前所施工节段中弹性地基梁的弹性特征值其中k3为当前所施工节段两帮岩体的反力系数,E和I分别为当前所施工节段两帮岩体的综合弹性模量和惯性矩;b'=1m。本实施例中,步骤一中进行围岩基本力学参数确定时,所确定的围岩基本力学参数至少应包括近距离煤层巷道1的净高h(即近距离煤层巷道1的内部高度)、开挖完成后当前所施工节段的顶板最大下沉量Δh(具体是为对试验段顶板进行监测得到的实际监测值)、当前所施工节段两帮岩体的综合弹性模量E、当前所施工节段两帮岩体弹塑性界面上的应力集中系数k1、当前所施工节段上覆岩层的平均容重γ、当前所施工节段的埋深H、当前所施工节段的巷道两帮岩体的粘聚力c(也称粘结力)、当前所施工节段的巷道两帮岩体的内摩擦角当前所施工节段的巷道两帮岩体与顶底板间交界面的切向刚度系数Ks、保护煤柱7的宽度l2、当前所施工节段的煤柱下压侧煤帮内侧且位于保护煤柱7正下方的岩体的应力集中系数k2、当前所施工节段两帮岩体的反力系数k3、当前所施工节段两帮岩体的惯性矩I和近距离煤层巷道1的设计宽度B。并且,还需相应对当前所施工节段两帮岩体的弹性特征值λ和当前所施工节段的巷帮极限平衡区宽度x0分别进行确定。本实施例中,所确定的围岩基本力学参数详见表1:表1围岩基本力学参数表本实施例中,将利用matlab软件且根据式(4),计算得出巷帮极限平衡区宽度x0=3.53m。所述的且并且,le=h+0.18m=3.68m。所述的l1=x0+le=7.21m。所述近距离煤层巷道1的等效圆半径r0=2.66m,本实施例中,Δh'=0.18m。实际施工时,可根据具体需要,对Δh'的取值大小进行相应调整。本实施例中,经现场实测得煤帮表面处的顶板最大下沉量(即开挖完成后当前所施工节段的顶板最大下沉量)Δh=0.15m,根据公式(1),求得S1=P1l12aEβcosh(βl1)sinh(βl1)+Δh2a-Δhl1=0.5×1.3×25×1000×380.6×7.213.5×2.8×109×0.1cosh(0.1×7.21)sinh(0.1×7.21)+0.153.5-0.15×7.21=0.4m.]]>而则由上述内容可知,开挖完成后当前施工节段的上覆岩层下压侧煤帮的向内位移理论值S1=0.4m,开挖完成后当前施工节段的煤柱下压侧煤帮的向内位移理论值S2=0.53m。考虑到煤柱支承压力引起的上煤层巷道3底板最大破坏深度波及下部煤层2和由于上煤层巷道3开挖卸载而引起的下部煤层2中第三变形区1-3的影响,当前施工节段的上覆岩层下压侧煤帮的预留开挖量Δd1=S1+Δd1=0.4m+0.1m,当前施工节段的煤柱下压侧煤帮的预留开挖量Δd2=S2+Δd2=0.53m+0.07m=0.6m。本实施例中,Δd1=0.1m,Δd2=0.07m。实际施工时,可根据具体需要,对Δd1和Δd2的取值大小进行相应调整。本实施例中,所述近距离煤层巷道1为回采巷道且其净高与下部煤层2的净高相同;步骤三中进行巷道开挖时,按照常规矿山回采巷道开挖的施工方法,对当前所施工节段进行开挖。实际施工过程中,多个所述节段的纵向长度均为10m~50m。本实施例中,多个所述节段的纵向长度为30m左右。实际施工时,所述近距离煤层巷道1与上煤层巷道3之间的水平间距为8m~12m。实际施工时,前后相邻两个所述巷道支护单元之间的间距为0.8m~1.2m。本实施例中,前后相邻两个所述巷道支护单元之间的间距为1m,相邻两个所述巷道支护单元之间的中部均设置有一根所述注浆锚杆8。本实施例中,步骤五中对当前所施工节段进行支护施工时,先由后向前对多根所述注浆锚杆8进行施工,再由后向前对多个所述巷道帮部支护体系所采用的支护结构进行施工,之后再由后向前对多个所述底板支护体系所采用的支护结构进行施工。因而,对巷道底板进行支护加固之前,要先对近距离煤层巷道1的两帮进行支护,充分发挥巷道帮部围岩的承载作用,减小底板压力,以防止由于两帮围岩过度下沉,导致底板破裂而形成严重底臌。本实施例中,所述巷道帮部支护体系所采用的支护结构为预应力锚杆支护结构。对所述巷道帮部支护体系所采用的预应力锚杆支护结构进行确定时,主要是根据当前所施工节段的巷帮极限平衡区宽度x0,对巷道帮部支护时所采用预应力锚杆的数量和锚杆长度进行确定。如图5所示,所述巷道帮部支护体系所采用的支护结构包括两个分别对称布设在近距离煤层巷道1左右两侧巷道帮上的帮部支护结构,两个所述帮部支护结构的结构相同;所述帮部支护结构包括布设在近距离煤层巷道1的巷道帮上且呈水平向布设的巷道帮部锚杆9;所述巷道帮部锚杆9的长度等于l1'+x0+l2',其中l1'=10cm~20cm,l2'=30cm~50cm。实际施工时,所述帮部支护结构中巷道帮部锚杆9的数量为一个或多个;且当巷道帮部锚杆9的数量为一个时,该巷道帮部锚杆9布设在所述需防治回采巷道的巷道帮中部;当所述巷道帮部锚杆9的数量为多个时,多个所述巷道帮部锚杆9呈均匀布设且相邻两个所述巷道帮部锚杆9之间的间距为0.8m~1m。本实施例中,所述巷道帮部锚杆9的数量为三个。实际施工时,可根据具体需要,对所述帮部支护结构中巷道帮部锚杆9的数量进行相应调整。本实施例中,所述巷道帮部锚杆9的长度Lbang=l1'+x0+l2'=0.1+3.53+0.33=3.96m。此处,取所述巷道帮部锚杆9的长度为4.2m,两帮各三根Φ18×6500mm的左旋螺纹钢锚杆,间排距为800×1000mm,设计锚固长度取为1200mm,每根锚杆采用2节Z2360型中速树脂锚固剂。其中l1'=10cm,l2'=33cm,所述巷道帮部锚杆9的有效长度为3.53m,巷道帮部锚杆9的外露长度为0.1m且其锚入稳定岩层内的长度为0.33m。实际施工时,当巷道整体处于软弱破碎为岩体时,由于开采造成应力重新分布和构造应力的不断释放,使破碎底板岩体变形逐渐增大,产生挤压流变底鼓随时间不断发展的时间效应。其中,挤压流动性底鼓主要发生在巷道底板为软弱破碎岩体的岩层内,在垂直地应力作用下,以巷道底板为沿空自由面,底板软弱破碎岩体受水平应力挤压流动到巷道内,形成巷道底鼓,其力学模型详见图6。本实施例中,步骤四中所述底板支护体系所采用的支护结构为预应力锚杆支护结构。实际对所述底板支护体系所采用的支护结构进行确定时,由于近距离煤层巷道1的底板左右两侧会分别出现一个深度为hmax的巷道底板最大破坏深度处,因而实际对巷道底板进行支护时,主要是参照巷道底板最大破坏深度处的深度hmax以及巷道底板最大破坏深度处距离巷道帮壁之间的水平距离l0,对近距离煤层巷道1底板最大破坏深度处进行处理。因而,对所述底板支护体系所采用的预应力锚杆支护结构进行确定时,主要是根据近距离煤层巷道1底部左右两侧的巷道底板最大破坏深度处的深度hmax和巷道底板最大破坏深度处距离巷道帮壁之间的水平距离l0,对底板支护所采用预应力锚杆的数量和锚杆长度进行确定。本实施例中,对所述底板支护体系所采用的支护结构进行确定时,根据当前所施工节段的实际开挖宽度b'进行确定:当b'<3m时,所述底板支护体系包括左右两根底板锚杆,两根所述底板锚杆均呈竖直向布设,两根所述底板锚杆分别为第一左侧底板锚杆和第一右侧底板锚杆,所述第一左侧底板锚杆与当前所施工节段左侧巷帮之间的间距以及所述第一右侧底板锚杆与当前所施工节段右侧巷帮之间的间距均为l0;当b'≥3m时,所述底板支护体系包括四根底板锚杆,四根所述底板锚杆均呈竖直向布设,四根所述底板锚杆包括两根第二左侧底板锚杆和两根第二右侧底板锚杆,两根所述第二左侧底板锚杆之间的中心位置与当前所施工节段左侧巷帮之间的水平距离为l0,两根所述第二右侧底板锚杆之间的中心位置与当前所施工节段右侧巷帮之间的水平距离为l0;所述第一左侧底板锚杆、所述第一右侧底板锚杆、两根所述第二左侧底板锚杆和两根所述第二右侧底板锚杆的长度均不小于hmax。本实施例中,当前所施工节段的巷道宽度b'大于4m,并且所述底板支护体系包括四根底板锚杆。同时,所述底板支护体系所采用的支护结构还包括两个分别对称布设在近距离煤层巷道1底板左右两端的帮角锚杆10;所述第一左侧底板锚杆、所述第一右侧底板锚杆、两根所述第二左侧底板锚杆和两根所述第二右侧底板锚杆的长度均等于l1+K·hmax+l2,两个所述帮角锚杆10的长度均为L1且l1=10cm~20cm,l2=30cm~50cm;K为安全系数且K=1~1.5。其中,所述帮角锚杆10由外至内逐渐向下倾斜且其与水平方向之间的夹角为35°~55°。本实施例中,所述帮角锚杆10与水平方向之间的夹角为45°。本实施例中,K=1.2。所述第一左侧底板锚杆、所述第一右侧底板锚杆、两根所述第二左侧底板锚杆和两根所述第二右侧底板锚杆均为竖向底板锚杆11,并且所述竖向底板锚杆11的有效长度为:ldi=K·hmax,锚杆外露长度l1'=0.1m,锚入底板稳定岩层的长度l2'=0.3m,具体采用四根Φ18×7000mm的左旋螺纹钢锚杆,间排距为840×1000mm,设计锚固长度取为1200mm,每根锚杆采用2节Z2360型中速树脂锚固剂。所述帮角锚杆10的有效长度为锚杆外露长度l1'=0.1m,锚入底板稳定岩层的长度l2'=0.3m。步骤四中对当前所施工节段的巷道底板岩体最大破坏深度hmax进行确定之前,还需先建立回采巷道底板破坏深度计算模型,详见图7。并且,建立巷道底板塑性破坏模型,详见图8。如图7所示,对近距离煤层巷道1的底板岩体变形破坏过程进行分析:所述近距离煤层巷道1开挖后,围岩应力发生重分布并在顶板与帮部界面上形成支承压力区,两帮岩体形成宽度为x0的极限平衡区,并且巷道两帮岩体在垂直应力作用下挤压底板,使得底板发生塑性破坏。并且,底板发生塑性破坏后,产生的塑性破坏带分为1区、2区和3区三种类型的破坏区,其中3区位于近距离煤层巷道1的正下方,1区位于极限平衡区正下方,2区位于1区和3区之间,其中巷道底板岩体最大破坏深度处位于2区内。结合图7,当顶帮围岩为较坚硬岩石而底板处于软弱岩层中时,巷道底板在高垂直应力的强烈作用下发生隆起现象,上部软弱底板则被挤压流动,形成底臌。当支承压力达到或超过底板主动区岩体(1区,与极限平衡区对应)的极限强度时,该部分岩体在垂直方向上受压缩,岩体将变形破坏;同时,在水平方向上主动区岩体必然会膨胀,进而挤压过渡区岩体(2区),并将应力传递到这一区;过渡区岩体继续挤压被动区(3区)。由于只有被动区具有向回采巷道空间内的自由临空面,从而过渡区及被动区的岩体在主动区高支承压力的作用下将向回采巷道空间内移动并逐渐形成一个连续的滑移面,最后被动区的回采巷道底板岩体向上隆起,此时巷道底板岩体最大塑性区破坏深度为hmax。为科学评价本发明所采用支护方案的实际效果,需对试验段支护后的围岩变形情况进行系统监测。其中,围岩深部变形监测主要是通过对支护加固后不同深度岩体的变形情况的测试,以了解巷道围岩各部分不同深度围岩的弱化和松动范围,包括破碎区、塑性区的分布及其离层情况,以准确评估支护效果,修正支护参数;围岩表面位移监测可较好地判断围岩的运动情况,分析围岩是否进入稳定状态。监测结果表明:采用本发明进行支护后,所述近距离煤层巷道1的左右两侧巷道帮部的最大变形量分别为0.065m和0.08m,巷道顶底板相对移近量仅为0.09m,因而煤帮变形得到有效控制,同时显著提高了顶底板的稳定性。以上所述,仅是本发明的较佳实施例,并非对本发明作任何限制,凡是根据本发明技术实质对以上实施例所作的任何简单修改、变更以及等效结构变化,均仍属于本发明技术方案的保护范围内。当前第1页1 2 3