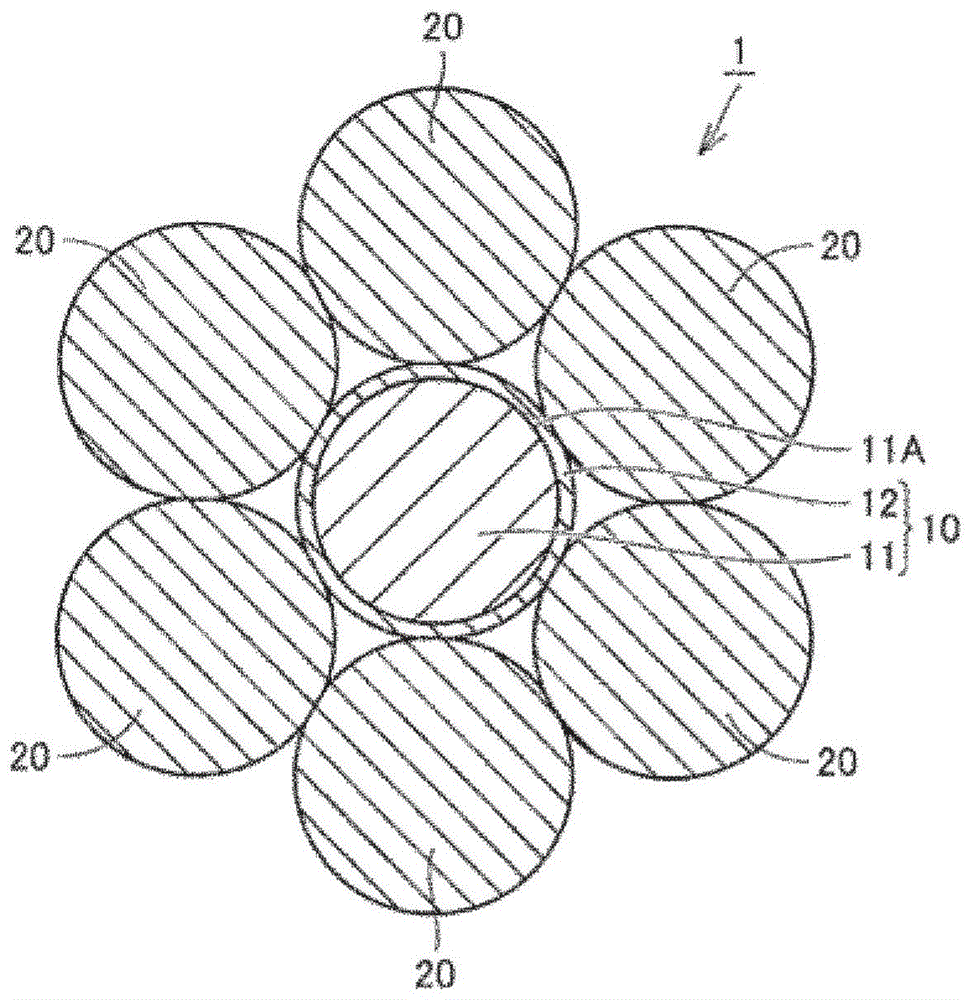
本发明涉及一种线束用线股和线束。本申请要求2016年11月16日提交的日本专利申请第2016-222989号的优先权,该日本专利申请的全部内容以引用的方式并入到本文中。
背景技术:
:线束被用于在例如车辆这样的机械设备能够进行供电、传输等。例如,线束具有这样的结构:其中,连接器被设置在作为导电体的、由铜制成的导线部的端部处。线束的导线部不仅需要低电阻,还需要能够确保耐久性的强度。使用铜或铜合金作为导线部的材料提供了具有低电阻的导线部。然而,为了使得导线部具有足够的强度,由铜或铜合金制成的导线部需要稍微粗一些。这增加了铜的用量。为了解决这个问题,已经提出了通过将由不锈钢制成的第一元件线和由铜或铜合金制成的第二元件线绞合在一起而获得的线束用线股(例如,参见专利文献1和专利文献2)。这些能够提供减少铜用量并同时获得强度和导电率的线束用线股。现有技术文献专利文献专利文献1:日本未审查专利申请公开第2004-281241号专利文献:国际公开第2005/024851号技术实现要素:根据本发明的线束用线股包括第一元件线和第二元件线,所述第二元件线绞合在所述第一元件线周围,并且由铜(cu)或铜合金制成。所述第一元件线包括由不锈钢制成的芯部以及覆盖所述芯部并由铜或铜合金制成的覆层。附图说明[图1]图1是垂直于根据第一实施例的线束用线股的纵向方向的截面的示意性截面图。[图2]图2是芯部与覆层之间的边界部分附近的结构的示意性截面图。[图3]图3是垂直于根据第二实施例的线束用线股的纵向方向的截面的示意性截面图。[图4]图4是垂直于根据第三实施例的线束用线股的纵向方向的截面的示意性截面图。[图5]图5是垂直于根据第四实施例的线束用线股的纵向方向的截面的示意性截面图。[图6]图6是概括用于生产线束用线股和线束的方法的流程图。[图7]图7是示出用于生产线束用线股和线束的方法的示意性截面图。[图8]图8是示出用于生产线束用线股和线束的方法的示意图。[图9]图9是示出用于生产线束用线股和线束的方法的示意图。[图10]图10是沿着图9中的x-x线截取的示意性截面图。具体实施例[本公开要解决的问题]在生产线束时,一个导线部和另一个导线部可以接合(拼接接合法)以形成分支。导线部的接合能够例如通过超声波焊接来进行。然而,如果专利文献1和专利文献2中公开的线束用线股用作导线部,则其不利之处在于,难以通过超声波焊接而接合。因此,本发明的目的是提供一种线束用线股和一种线束,该线束用线股能够减少铜的用量,同时获得强度和导电率,并且有助于通过超声波焊接而接合。[本公开的有益效果]上述线束用线股能够减少铜的用量,同时获得强度和导电率,并有助于通过超声波焊接进行接合。[本发明实施例的描述]首先,将按顺序描述本发明的实施例。本申请的线束用线股包括第一元件线和第二元件线,第二元件线绞合在第一元件线周围并由铜或铜合金制成。第一元件线包括由不锈钢制成的芯部,以及覆盖芯部并由铜或铜合金制成的覆层。本发明人研究了通过超声波焊接而接合专利文献1和专利文献2中公开的线束用线股的困难的原因和解决方案。研究表明,通过超声波焊接进行接合是困难的,因为由不锈钢制成的第一元件线和由铜或铜合金制成的第二元件线之间的粘附力较弱,因此由于超声波焊接引起的振动使得元件线彼此分离(脱离)。本申请的线束用线股具有这样的结构,其中,包括由不锈钢制成的芯部的第一元件线和由铜或铜合金制成的第二元件线绞合在一起。因此,本申请的线束用线股1能够减少铜的用量,并实现强度和导电率两者。在本申请的线束用线股中,由铜或铜合金制成的覆层被形成以覆盖第一元件线的芯部。这改善了第一元件线与由铜或铜合金制成的第二元件线之间的粘附。结果,抑制了由于超声波焊接引起的振动所导致的元件线的彼此分离(脱离),以有助于通过超声波焊接进行接合。因此,本申请的线束用线股能够减少铜的用量,实现强度和导电率两者,并有利于通过超声波焊接进行接合。在线束用线股中,多个第二元件线可以被绞合以包围第一元件线的外周。这种构造有助于减少铜的用量,并实现强度和导电率两者。在线束用线股中,多个第一元件线和多个第二元件线可以绞合在一起。这种构造也有助于减少铜的用量,并实现强度和导电率两者。在线束用线股中,构成芯部的不锈钢可以是奥氏体不锈钢。这种构造能够提高线束用线股的耐腐蚀性、耐电解腐蚀性和可加工性。在线束用线股中,奥氏体不锈钢可能具有-400℃或更低的ms点,ms点是马氏体转变开始温度,ms点由公式(1)计算。ms=1032-1667×(%c+%n)-27.8×%si-33×%mn-61×%ni-41.7×%cr···(1)这能够抑制在生产线束用线股的过程期间,在构成第一元件线的芯部的奥氏体不锈钢中形成应变诱发马氏体相。结果,能够更可靠地提高线束用线股的耐腐蚀性、耐电解腐蚀性和可加工性。为了更可靠地抑制应变诱发马氏体相的形成,由公式(1)计算的ms点优选为-700℃或更低。在公式中,奥氏体不锈钢中碳、氮、硅、锰、镍和铬的平均含量(单位:质量%)分别为%c、%n、%si、%mn、%ni和%cr。ms点以摄氏度为单位表示。在线束用线股中,第一元件线还可以包括设置在芯部与覆层之间的ni(镍)层。这种构造能够改善芯部与覆层之间的粘附。在线束用线股中,ni层可以具有0.05μm或更大和5μm或更小的厚度。为了可靠地实现改善芯部与覆层之间的粘附性的功能,ni层的厚度优选为0.05μm或更大,更优选为0.2μm或更大,更优选为0.3μm或更大,以便防止诸如针孔之类的缺陷。ni层能够例如通过电镀形成。在这种情况下,电镀期间水电解而形成的氢可能使材料脆化。为了缩短电镀时间以防止这种脆化,ni层的厚度优选为5μm或更小,更优选为2μm或更小,更优选为1μm或更小。在线束用线股中,第一元件线在覆层的表面上还可以包括选自由au(金)层、ag(银)层和sn(锡)层所组成的组中的至少一个。这种构造能够减小第一元件线的外周表面处的接触电阻。在线束用线股中,au层、ag层和sn层可以各自具有0.3μm或更大和20μm或更小的厚度。为了减小厚度的变化,au层、ag层和sn层的厚度各自优选为0.3μm或更大。然而,如果au层、ag层和sn层比必需的厚,则效果达到极限,导致生产成本增加。为了降低生产成本,au层、ag层和sn层的厚度各自优选为20μm或更小,更优选为5μm或更小,更优选为0.7μm或更小。在线束用线股中,在芯部表面上的钝化膜可以具有5nm或更小的厚度。这种构造允许覆层容易地形成在芯部的表面上。芯部表面上钝化膜的厚度能够通过测量五个不同点处的钝化膜的厚度来确定,例如,使用tem(透射电子显微镜)并计算平均值。在线束用线股中,覆层的厚度可以为1μm或更大和20μm或更小。为了更可靠地产生覆层形成的上述效果,覆层的厚度优选为1μm或更大。然而,如果覆层比必需的厚,效果会达到极限,导致生产成本增加。为了降低生产成本,覆层的厚度优选为20μm或更小。在线束用线股中,第二元件线和覆层可以由黄铜、磷青铜、科森合金或铍铜制成。这些材料适合作为构成第二元件线和覆层的铜合金。在线束用线股中,第二元件线和覆层可以由相同的材料制成。这种构造进一步改善了第一元件线与第二元件线之间的粘附。在垂直于线束用线股的纵向方向的截面中,第一元件线与第二元件线的面积比可以是7:3至2:8。这种构造有助于减少铜的用量,并实现强度和导电率两者。线束用线股可以具有50%iacs(国际退火铜标准)或更高和90%iacs或更小的导电率。为了确保线束的导线部具有足够的导电率,线束用线股的导电率优选为50%iacs或更高。为了确保足够的强度,线束用线股的导电率优选为90%iacs或更小,更优选为70%iacs或更小。线束用线股可以具有600mpa或更高和1000mpa或更小的拉伸强度。为了提供具有足够耐久性的线束(特别是信号线束),线束用线股的拉伸强度优选为600mpa或更高。为了改善冲击断裂特性,线束用线股的拉伸强度优选为750mpa或更高。为了确保足够的导电率,线束用线股的拉伸强度优选为1000mpa或更小。为了确保足够的柔性,线束用线股的拉伸强度更优选为900mpa或更小。本申请的线束包括第一线股和被焊接到第一线股的第二线股。第一线股和第二线股各自是用于本申请的线束的线股。第一线股的第二元件线和第二线股的第二元件线电连接在一起。本申请的线束具有这样的结构:其中,通过超声波焊接容易接合的第一线股和第二线股被焊接在一起。这种结构能够提供这样一种线束:该线束减少了铜的用量,实现强度和导电率两者,并且包括具有高接合强度的分支部分。[本发明实施例的细节]接下来,下面将参照附图描述根据本发明的线束用线股和线束的实施例。在下面的附图中,相同或相应的部分由相同的附图标记表示,并且不再重复对其的描述。(第一实施例)首先,将参照图1和图2描述根据第一实施例的线束用线股。参照图1,作为根据第一实施例的线束用线股的线股1包括第一元件线10和第二元件线20,第二元件线20绞合在第一元件线10周围并且由铜或铜合金制成。第一元件线10包括由不锈钢制成的芯部11以及覆盖芯部11并由铜或铜合金制成的覆层12。覆层12覆盖芯部11的外周表面11a,从而与外周表面11a接触。多个(在本实施例中为六个)第二元件线被绞合在一起,以包围第一元件线10的外周。覆层12具有例如1μm或更大和20μm或更小的厚度。第二元件线20和覆层12可以由铜(纯铜)制成,或者可以由铜合金制成,例如黄铜、磷青铜、科森合金或铍铜。第二元件线20和覆层12可以由相同的材料制成。根据该实施例的线股1具有这样的结构:其中,包括由不锈钢制成的芯部11的第一元件线10和由铜或铜合金制成的第二元件线20绞合在一起。因此,根据该实施例的线股1是这样一种线股:该线股减少了线束的铜的用量,并且实现了强度和导电率两者。在根据本实施例的线股1中,由铜或铜合金制成的覆层12被形成为覆盖第一元件线10的芯部11。这改善了第一元件线10与由铜或铜合金制成的第二元件线20之间的粘附。结果,抑制了由于超声波焊接引起的振动导致的元件线的彼此分离(脱离),以有助于通过超声波焊接进行接合。因此,线股1是如下所述的线束用线股:该线束用线股能够减少线束的铜的用量,实现强度和导电率两者,并且有助于通过超声波焊接进行接合。在该实施例中,构成芯部11的不锈钢是jis标准中定义的奥氏体不锈钢。构成芯部11的奥氏体不锈钢的ms点优选为-400℃或更低,更优选为-700℃或更低,ms点由公式(1)计算。ms=1032-1667×(%c+%n)-27.8×%si-33×%mn-61×%ni-41.7×%cr···(1)这能够抑制构成芯部11的奥氏体不锈钢中应变诱发马氏体相的形成。由于芯部11由不锈钢制成,所以在芯部11的表面上形成钝化膜。参照图2,钝化膜19位于芯部11的外周表面11a上(在芯部11与覆层12之间)。在根据该实施例的线股1中,钝化膜19具有5nm或更小的厚度。这允许覆层12容易地形成在芯部11的外周表面11a上。在垂直于线股1的纵向方向的截面中,第一元件线10与第二元件线20的面积比优选为7:3至2:8。这有助于减少铜的用量,实现强度和导电率两者。线股1优选具有50%iacs或更高和90%iacs或更小的导电率。为了确保线束的导线部具有足够的导电率,线股1的导电率优选为50%iacs或更高。为了确保足够的强度,线股1的导电率优选为90%iacs或更小,更优选70%iacs或更小。线股1优选具有600mpa或更高和1000mpa或更小的拉伸强度。为了提供具有足够耐久性的线束(特别是信号线束),线股1的拉伸强度优选为600mpa或更高。为了改善冲击断裂特性,线股1的拉伸强度优选为750mpa或更高。为了确保足够的导电率,线股1的拉伸强度优选为1000mpa或更小。为了确保足够的柔韧性,线股1的拉伸强度更优选为900mpa或更小。(第二实施例)接下来,将描述根据另一实施例,即,第二实施例的线束用线股。参照图3和图1,作为根据第二实施例的线束用线股的线股1基本上具有与根据第一实施例的线束相同的构造并产生相同的效果。然而,根据第二实施例的线股1在第一元件线10的结构上不同于根据第一实施例的线股1。参照图3,根据第二实施例的线股1的第一元件线10还包括被布置在芯部11与覆层12之间的ni层13。在该实施例中,ni层13具有0.2μm或更大和1μm或更小的厚度。在根据该实施例的线股1中,由于第一元件线10中存在ni层13,芯部11与覆层12之间的粘附性得到改善。(第三实施例)接下来,将描述根据又一实施例,即第三实施例的线束用线股。参照图4和图3,作为根据第三实施例的线束用线股的线束1基本上具有与根据第二实施例的线束相同的构造并产生相同的效果。然而,根据第三实施例的线股1在第一元件线10的结构上不同于根据第二实施例的线股1。参照图4,根据第三实施例的线股1的第一元件线10还包括在覆层12的表面上的第二覆层14,第二覆层14由选自由au层、ag层和sn层所组成的组中的至少一个形成。构成第二覆层14的au层、ag层和sn层各自具有0.3μm或更大和20μm或更小的厚度。在根据该实施例的线股1中,由于第一元件线10中存在第二覆层14,在第一元件线10的外周表面处的接触电阻减小。(第四实施例)接下来,将描述根据又一实施例,即,第四实施例的线束用线股。参照图5和图1,作为根据第四实施例的线束用线股的线股1基本上具有与根据第一实施例的线束相同的构造并产生相同的效果。然而,根据第四实施例的线股1与根据第一实施例的线股1的不同之处在于第一元件线10的数量与第二元件线20的数量之比以及它们如何绞合在一起。参照图5,在根据第四实施例的线股1中,多根(四根)第一元件线10和多根(三根)第二元件线20绞合在一起。具体地,在垂直于纵向方向的截面中,一个第一元件线10被布置在中心处。总共六条第一元件线10和第二元件线20交替地被布置在圆周方向上,以在中心处包围第一元件线10的外周。具有这种结构的根据第四实施例的线股1也能够产生与根据第一实施例的线股相同的效果。(第五实施例)接下来,将描述包括根据第一实施例的线股1的线束和用于生产线束的方法。图6是概括用于生产线束的方法的流程图,该线束具有两个线股1接合在一起的结构。参照图6,在根据本实施例的用于生产线束的方法中,首先执行步骤(s10),即,元件线提供步骤。在步骤(s10)中,参照图1,提供了第一元件线10和第二元件线20。所提供的第二元件线20例如是直径为0.1mm至0.3mm的纯铜线。所提供的第一元件线10例如是包括直径为0.1mm至0.3mm的奥氏体不锈钢线(芯部11)和形成在奥氏体不锈钢线表面上的镀铜层(覆层12)的线。奥氏体不锈钢线(芯部11)可以在进行镀铜之前进行酸洗,使得芯部11的表面上的钝化膜变薄(例如,5nm或更小)。接下来,执行步骤(s20),即绞合步骤。在步骤(s20)中,将步骤(s10)中提供的第一元件线10和第二元件线20绞合在一起。具体地,参照图1,用作芯线的第一元件线10被布置在中心处,并且六个第二元件线20被布置成包围第一元件线10的外周。然后,六条第二元件线20被绞合,使得六条第二元件线20在第一元件线10的外周表面上螺旋延伸。结果,获得了根据第一实施例的线股1。接下来,执行步骤(s30),即,压接步骤。在步骤(s30)中,径向压缩在步骤(s20)中获得的线股1。具体地,例如,使用模具对在步骤(s20)中获得的线股1进行径向压缩处理。模具的内孔被调整为稍微小于线股1的外径。虽然步骤(s30)不是必需的,但是通过执行该步骤将第二元件线20和第一元件线的覆层12压接在一起。结果,更可靠地改善了第一元件线10与第二元件线20之间的粘附。接下来,执行步骤(s40),即绝缘树脂层形成步骤。在步骤(s40)中,参照图1和图7,形成由绝缘树脂制成的绝缘树脂层40,以覆盖通过执行步骤(s10)至(s30)获得的线股1的外周表面。结果,获得了在径向方向上与外部绝缘的线股1。接下来,执行步骤(s50),即剥离步骤。在步骤(s50)中,剥离通过执行步骤(s10)至(s40)而获得的在线股1上形成的绝缘树脂层40的一部分。具体地,首先提供要彼此接合的两个线股(线股50和线股60)(见图8)。线股50和线股60各自是通过执行步骤(s10)至(s40)获得的线股1。参照图8,线股50包括导线部51和覆盖导线部51的绝缘树脂层52。线股60包括导线部61和覆盖导线部61的绝缘树脂层62。导线部51和导线部61各自对应于图1所示的线股1。绝缘树脂层52和绝缘树脂层62各自对应于绝缘树脂层40。然后,剥离线股50和线股60的部分,即,绝缘树脂层52和绝缘树脂层62的部分,其中线股50和线股60将会彼此接合。在该实施例中,线股50的中间部分和线股60的末端部分接合在一起。因此,在线股50的中间部分处的绝缘树脂层52的一部分和在线股60的末端部分处的绝缘树脂层62的一部分被剥离。结果,如图8所示,导线部51和导线部61分别在线股50的、已经剥离了绝缘树脂层52的部分处和线股60的已经剥离了绝缘树脂层62的部分处露出。接下来,执行步骤(s60),即超声波焊接步骤。在步骤(s60)中,在步骤(s50)中通过剥离绝缘树脂层52和绝缘树脂层62而已经暴露的导线部51和导线部61通过超声波焊接被接合在一起。具体地,参照图8,通过剥离绝缘树脂层52和绝缘树脂层62而已经暴露的导线部51和导线部61保持彼此接触,同时导线部51与导线部61之间的接触区域经受超声波振动。结果,如图9所示,焊接部70被形成为将线股50与线股60接合在一起。参照图10,焊接部70具有这样的结构,其中,由来自第二元件线20和覆层12的铜制成的铜区域25包围线股50的芯部11和线股60的芯部11。在焊接部70中,第二元件线20和覆层12可以是完全集成的,或者可以被接合到这样的程度:即,第二元件线20与覆层12在被接合之前是可区分的。然后,可选地安装连接器等,以完成根据该实施例的线束100。根据该实施例的线束100包括线股50和被焊接到线股50的线股60。线股50和线股60各自是例如根据第一实施例的线束用线股的线股1。通过在焊接部70中形成铜区域25,线股50的第二元件线20和线股60的第二元件线20电连接在一起。根据该实施例的线束100具有这样的结构:其中,作为易于通过超声波焊接而接合的线束1的线股50和线股60被焊接在一起。因此,线束100是这样的线束:该线束减少了铜用量、实现了强度和导电率两者、并且具有高接合强度的分支部分(焊接部70)。虽然在第一至第四实施例中已经描述了一条第一元件线10和六条第二元件线20绞合在一起的情况以及四条第一元件线10和三条第二元件线20绞合在一起的情况,但是任何其它数量的第一元件线10和第二元件线20可以绞合在一起,并且绞合在一起的第一元件线10和第二元件线20的数量可以根据预期用途所需的强度和导线性质自由地选择。虽然在第二实施例中已经描述了形成ni层13的情况,并且在第三实施例中已经描述了形成ni层13和第二覆层14的情况,但是可以在不形成ni层13的情况下形成第二覆层14。示例类似于根据第五实施例的线束100,制备了包括通过超声波接合而被接合在一起的两个线股1的样品,并且进行了用于评估接合强度的实验。实验程序如下所述。提供了包括直径为0.15mm的奥氏体不锈钢线(芯部11)和通过电镀形而成在奥氏体不锈钢线表面上的纯铜层(覆层12)的第一元件线10和直径为0.15mm的由纯铜制成的第二元件线20。如在第一实施例中,六条第二元件线20被布置在用作芯线的一条第一元件线10周围,并且进行绞合。然后,通过使所得产品通过具有直径为0.42mm的通孔的模具,径向压缩该产品,从而获得线股1。以这种方式获得两个线股1,并如第五实施例中那样通过超声波焊接而接合以制备样品。焊接部70的长度约为4.0mm,厚度约为0.8mm。对于超声波焊接,使用schunk(示例)制造的minic系列焊接机进行同轴拼焊。为了比较,除了省略覆层12的形成以外,通过执行相同的程序制备了样品(比较例)。然后进行拉伸测试,使得拉伸应力沿纵向方向作用在焊接部70上,以确定断裂负荷,由此评估接合强度。(实验1)首先,通过上述实验研究覆层12的厚度对接合强度的影响。实验的条件和结果在表1中示出。[表1]覆层厚度(μm)拉伸断裂负荷(n)示例1111.3示例2312.6示例3514.3示例41018.0示例52017.6比较例109.1参照表1,形成有覆层12的示例1至5的拉伸断裂强度明显高于未形成有覆层12的比较例1。在比较例1的焊接部中,观察到由于超声波焊接引起的振动而导致元件线彼此分离。这表明,在形成有铜或铜合金制成的覆层的本申请的线股中,改善了第一元件线与第二元件线之间的粘附,并且抑制了元件线彼此的分离,因此导致接合强度增加。覆层12的厚度为1μm的示例1的接合强度明显高于比较例1的接合强度。因此,能够说覆层12的厚度优选为1μm或更大。尽管拉伸断裂强度随着覆层12的厚度增加而增加,但是在10μm至20μm厚度时,拉伸断裂强度的增加已经达到极限。比所需的厚度更厚的覆层12会导致生产成本增加。因此,能够说覆层12的厚度优选为20μm或更小。(实验2)接下来,通过上述实验研究了芯部11表面上钝化膜19的厚度对接合强度的影响。钝化膜19的厚度通过使用tem研究每个芯部11表面上的多个点并计算平均值来确定。实验的条件和结果在表2中示出。[表2]参考表2,在钝化膜19的厚度为5nm或更小的示例1和6中不能发现对接合强度的影响。然而,在钝化膜19的厚度大于5nm的实施例7至9中,接合强度趋于降低。这表明钝化膜19的厚度优选为5nm或更小。(实验3)接下来,通过上述实验研究了ni层13和第二覆层14的形成对接合强度的影响。实验的条件和结果在表3中示出。在表3中的“第二覆层厚度”列中给出的括号中的元素名称表示构成第二覆层14的元素。ni层13和第二覆层14通过电镀形成。[表3]参照表3,形成ni层13或第二覆层14的示例10至13的拉伸断裂负荷与没有形成这些层的示例1的拉伸断裂负荷相当。这表明,即使在形成ni层13或第二覆层14时,也提供了足够的接合强度。应该理解,这里公开的实施例和示例在所有方面都是说明性的,而不是以任何方式进行限制。本发明的范围由权利要求限定,而不是由前面的描述限定,并且在权利要求等同物的含义和范围内的所有变化都包括在其中。附图标记列表1线股10第一元件线11芯部11a外周表面12覆层13ni层14第二覆层19钝化膜20第二元件线25铜区域40绝缘树脂层50线股51导线部52绝缘树脂层60线股61导线部62绝缘树脂层70焊接部100线束当前第1页12