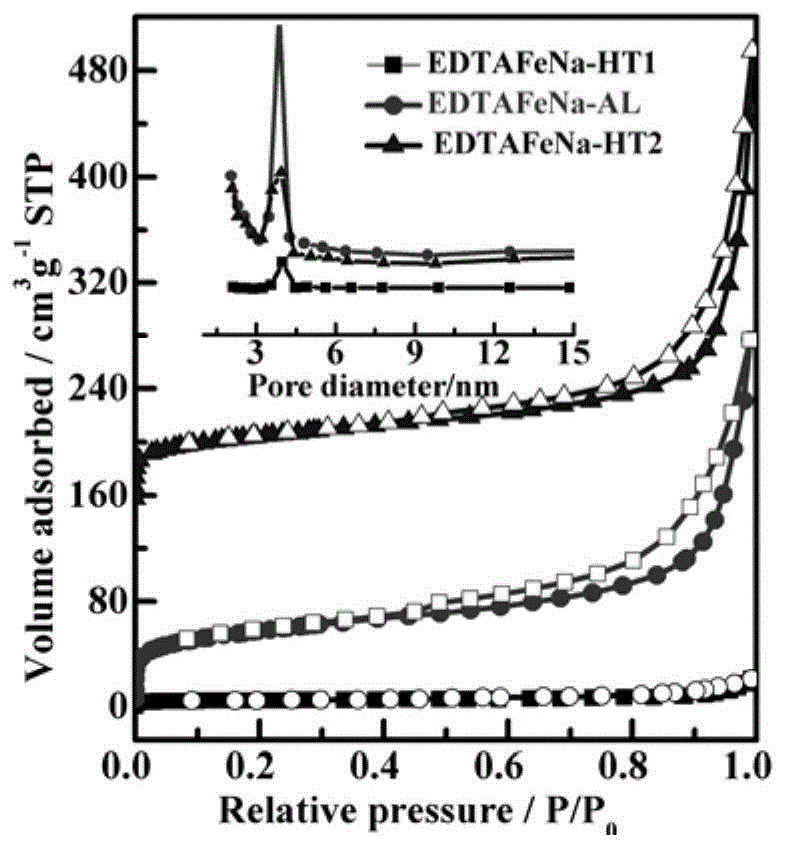
本发明属于电催化中非贵金属催化剂
技术领域:
,具体涉及一种edtafena衍生的自负载fe-n-c氧还原催化剂及其制备方法。
背景技术:
:燃料电池可以直接高效地将燃料分子中蕴含的化学能转化为电能,并且仅生成对环境没有污染的水,为现有化石能源的有效利用提供了一种新的途径。由于其具有质轻、高效、快速启动、寿命长、低腐蚀性、环境友好等特点,在电动汽车电源、移动电源、便携式电源以及电站应用等方面将具有非常大的应用前景。尽管如此,在短期内实现燃料电池在世界范围内民用化、商业化和产业化应用仍然面临巨大挑战,其中阻碍其商业化进程的关键因素之一则是燃料电池目前所用的电极材料(pt或pt基催化剂)资源贫乏、价格昂贵,导致燃料电池成本过高。为了解决此问题,开发能够替代pt用于燃料电池阴极氧还原(orr)的廉价非贵金属催化剂(npmcs)是科研者们一直追求的重要目标之一。技术实现要素:为了解决上述问题,本发明的目的在于提供一种edtafena衍生的自负载fe-n-c氧还原催化剂,该催化剂既有介孔结构、很大的比表面积同时又具有高程度且均匀的氮掺杂。本发明的目的之二是提供了所述自负载fe-n-c氧还原催化剂的制备方法,该方法合成路线灵活、弹性空间大、操作可控、成本相对低廉、易于规模化生产。本发明是通过以下技术方案来实现的:一种自负载fe-n-c氧还原催化剂,所述自负载fe-n-c氧还原催化剂的介孔孔径为3.9±0.2nm,比表面积为385±2m2g-1,fe元素含量为0.4±0.02at.%,n元素含量为2.6±0.2at.%,c元素含量为93±2at.%;所述自负载fe-n-c氧还原催化剂包括介孔分子筛和乙二胺四乙酸铁钠(edtafena),所述介孔分子筛与乙二胺四乙酸铁钠的质量比为1:1~20;所述介孔分子筛为sba-15、mcm-41、mcm-48或kit-6中的一种或几种组合物。其中介孔分子筛作为自牺牲硬模板,edtafena兼具铁、氮和碳前驱体。自负载fe-n-c氧还原催化剂的制备方法,包括如下步骤:1)先将介孔分子筛加入到去离子水中,再加入乙二胺四乙酸铁钠分散均匀,然后将上述悬浮物进行蒸发、干燥、研磨,得到固体粉末a;2)将步骤1)中所得到的a在流动惰性气体保护下,以10±2℃/min升温至650~750℃保持1-3h,接着自然冷却至室温后研磨均匀,得到催化剂前体,标记为edtafena-ht1(mms);3)将步骤2)中所得到的催化剂前体edtafena-ht1(mms)用酸或碱的乙醇水溶液进行刻蚀获得脱硅的前体edtafena-et(mms);4)将步骤3)中所得到的edtafena-et(mms)在70~90℃、0.5~2m的进行酸处理0.5~24h,完毕进行抽滤、干燥,得到去除了部分铁物种的前体edtafena-al(mms);5)将步骤4)中所得到的edtafena-al(mms),在180~220mlmin-1流动气体保护下,以10±2℃/min升温至600~1000℃并保持0.5~3h,然后自然冷却至室温,此阶段产品标记为edtafena-al-ht2(mms),即所述的自负载fe-n-c催化剂。其中,edtafena-al-ht2(mms)中的al是自命名,表明是酸处理,是英文acid-leaching的缩写。较佳地,所述的介孔分子筛和乙二胺四乙酸铁钠加入到去离子水中分散可以是超声分散或通过固相机械混合。较佳地,步骤1)中,还可以同时加入其它含氮小分子化合物;所述含氮小分子化合物为三聚氰胺、尿素、吡咯、乙二胺中的一个或几个组合物。较佳地,步骤1)中,还可以同时加入激活剂koh、k2co3、(nh4)2co3、znco3中的一个或几个组合物。较佳地,所述流动惰性气体为n2或he。较佳地,步骤3)中,用酸或碱的乙醇水溶液进行刻蚀,具体为:将edtafena-ht1(mms)加入到摩尔浓度为1.5~2.5m的naoh的乙醇-水溶液中,在55~65℃搅拌20~25h,然后用去离子水和乙醇重复洗涤3次、抽滤、干燥;所述乙醇-水溶液中乙醇与水的体积比为1:1。用酸的乙醇水溶液进行刻蚀时,优选hf。较佳地,步骤4)中所述酸处理中酸为hcl、h2so4或hno3溶液。较佳地,步骤5)中,所述流动气体为惰性气体或活性气体nh3。传统的基于碳载体、含氮前驱体和金属盐的fe-n-c材料制备方法,由于在热处理过程中,含氮前驱体降解并碳化,除了对碳载体进行不均匀的n掺杂,同时也不可避免地会不同程度地堵塞碳载体的孔道,因此在影响orr的几个关键因素如孔径、比表面积、活性位密度及分布之间,总是存在一个权衡折中。本发明采用有序介孔分子筛为牺牲硬模板,目的是利用其介观结构裁剪出具有大比表面积的介孔fe-n-c材料,有利于活性位的暴露和底产物的传质扩散,提升电子转移速率,另一个目的是其丰富的孔道与edtafena的相互作用能够提高碳化得率,同时减少n元素的损失;选择唯一廉价的有机-无机化合物edtafena兼具fe、n和c前驱体,目的是能够降低原材料成本,也能避免像多组分前驱体相互作用导致的结构复杂性;另外仅通过裂解edtafena一种前驱体就能得到fe、n共掺杂的碳材料,这种自掺杂将被期待能够获得更均匀分布的活性位和提高其密度;利用酸处理能够除去非活性fe物种和进一步调控材料的介观结构;从而协同出具有优异orr活性的非贵金属催化剂。本发明与现有技术相比,具有以下有益效果:1)所述制备过程仅使用廉价的有机-无机化合物edtafena兼具fe、n和c前驱体;2)所述制备过程使用sba-15为硬模板并结合酸处理,能够有效提高n掺杂和石墨化程度,创造窄分布的介孔和大的比表面积,去除非活性或促使orr发生2e-选择性反应途径的晶态fe物种,从而能为orr过程的物质和电子的快速传输提供通道;3)碱性条件下,该自负载介孔fe-n-c材料催化orr的起始和半波电位以及高电势下动力学电流密度接近于商品化pt/c催化剂,且催化orr以高能量转化效率的4e-反应途径进行;4)该催化剂实用范围广,可用作各种燃料电池的阴极氧还原催化剂。本发明所述制备edtafena衍生的自负载fe-n-c催化剂的方法,制备过程所需试剂毒性小、安全环保、组分少、原料成本低廉,制备工艺灵活、弹性空间大、操作可控、产率高,易于规模化生产。附图说明图1为edtafena-ht2、edtafena-ht1和edtafena-al的n2吸/脱附等温线和孔径分布。图2为edtafena-ht2、edtafena-ht1和edtafena-al的磁滞回曲线。图3为edtafena-ht2的tem照片。图4为edtafena-ht2的tem照片中fe物种尺寸统计分布图。图5为edtafena-ht2(sba-15)和edtafena-al-ht2(sba-15)的小角xrd谱图。图6为edtafena-ht2(sba-15)和edtafena-al-ht2(sba-15)的广角xrd谱图。图7为edtafena-ht2(sba-15)和edtafena-al-ht2(sba-15)的n2吸/脱附等温线和孔径分布。图8为edtafena-ht2(sba-15)和edtafena-al-ht2(sba-15)的xps全谱。图9为edtafena-ht2(sba-15)和edtafena-al-ht2(sba-15)的磁滞回曲线。图10为在o2饱和的0.1mkoh中edtafena-ht2(sba-15)、edtafena-al-ht2(sba-15)和pt/c催化orr的极化曲线(室温、扫速10mvs-1、转速1600rpm)。图11为不同转速下edtafena-ht2(sba15)催化orr的极化曲线和不同电势下每个o2分子发生反应转移的电子数。图12为不同转速下edtafena-al-ht2(sba15)催化orr的极化曲线和不同电势下每个o2分子发生反应转移的电子数。具体的实施方式下面结合具体实施方式对本发明作进一步的详细说明,以助于本领域技术人员理解本发明。实施例11)取2gedtafena放入石英舟中并置于管式炉,在200mlmin-1n2保护下,以10℃/min升温至700℃保持2h,自然冷却至室温,然后研磨均匀,此阶段产品命名为edtafena-ht1。2)取0.25gedtafena-ht1在80℃、30ml0.5m的h2so4溶液中进行酸处理0.5h,完毕进行抽滤、干燥,此阶段产品命名为edtafena-al。3)取0.15gedtafena-al继续在200mlmin-1n2保护下,以10℃/min升温至900℃并保持2h,然后自然冷却至室温,研磨均匀后备用,此阶段获得的样品标记为edtafena-ht2。此制备过程没有使用sba-15作为硬模板,但使用了酸处理步骤,将作为对照催化剂,与下述使用sba-15作为硬模板,同时进行了酸处理制备的催化剂进行比较。本实施例合成的edtafena-ht2的n2吸/脱附等温线和孔径分布以及磁滞回曲线如图1、2所示;tem(透射电镜)及fe物种尺寸统计分布如图3、4所示。实施例21)取0.4g自制的sba-15加入到45ml去离子水中,再加入7.88gedtafena,磁力搅拌0.5h,超声分散2h,然后将上述悬浮物进行蒸发、干燥、研磨,得到固体粉末a。2)取1ga样品,在200mlmin-1n2保护下,以10℃/min升温至700℃保持1-3h,接着自然冷却至室温后研磨均匀,得到催化剂前体,命名为edtafena-ht1(sba-15)。3)取0.25gedtafena-ht1(sba-15)加入到25ml2mnaoh的乙醇-水(1:1,v:v)溶液中,在60℃搅拌24h,然后用去离子水和乙醇重复洗涤3次、抽滤、干燥,此碱刻蚀过程是为了移除样品中的sba-15模板,获得脱硅的前体c,命名为edtafena-et(sba-15)。4)取0.15gedtafena-et(sba-15),在200mlmin-1n2保护下,以10℃/min升温至900℃并保持2h,然后自然冷却至室温,此阶段产品标记为edtafena-ht2(sba-15)。此制备过程使用了sba-15作为硬模板,但没有使用h2so4溶液进行酸处理,仍将作为对照催化剂,与下述使用sba-15作为硬模板,同时进行了酸处理制备的催化剂进行比较。实施例3实验步骤与实施例2相同,区别在于在实验步骤3)和4)之间增加了一步酸处理,其实验方法同实施例1中的实验步骤2),最终获得的样品命名为edtafena-al-ht2(sba-15)。本实施例合成的edtafena-al-ht2(sba-15)及实施例2合成的edtafena-ht2(sba-15)的小角、广角xrd谱图如图5、6所示;n2吸/脱附等温线、孔径分布和织构参数如图7和表1所示;xps全谱及表面元素组成如图8和表2所示;磁滞回曲线如图9所示。实施例4称取3mg实施例1、2、3制备的自负载fe-n-c催化剂,分散到0.5ml5wt%nafion和去离子水(1/9,v/v)的混合溶液中,超声分散1h,然后移取15μl上述均匀分散的催化剂悬浊液涂覆至已抛光好的玻碳电极表面,在红外灯下干燥,待溶剂完全挥发后作为工作电极,然后以铂丝作为对电极,ag/agcl电极作为参比电极通过cv,lsv电化学方法测试材料在0.1mkoh中的orr活性。实施例5一种自负载fe-n-c氧还原催化剂,由以下方法制备而得:1)取0.4g的sba-15加入到45ml去离子水中,再加入7.88gedtafena,磁力搅拌0.5h,超声分散2h,然后将上述悬浮物进行蒸发、干燥、研磨,得到固体粉末a。2)取1ga样品,在200mlmin-1n2保护下,以5℃/min升温至700℃保持2.5h,接着自然冷却至室温后研磨均匀,得到催化剂前体,标记为edtafena-ht1(sba-15)。3)取0.25gedtafena-ht1(sba-15)加入到25ml2mnaoh的乙醇-水(1:1,v:v)溶液中,在60℃搅拌24h,然后用去离子水和乙醇重复洗涤3次、抽滤、干燥,此碱刻蚀过程是为了移除样品中的sba-15模板,获得脱硅的前体c,命名为edtafena-et(sba-15)。4)取0.25gedtafena-et(sba-15)在80℃、30ml0.5m的h2so4溶液中进行酸处理0.5h,完毕进行抽滤、干燥,此阶段产品命名为edtafena-al(sba-15)。5)取0.15gedtafena-al(sba-15),在200mlmin-1n2保护下,以10℃/min升温至900℃并保持2h,然后自然冷却至室温,此阶段产品标记为edtafena-al-ht2(sba-15),即所述的自负载fe-n-c催化剂。实施例6一种自负载fe-n-c氧还原催化剂,由以下方法制备而得:1)取0.4g的mcm-48加入到45ml去离子水中,再加入6gedtafena,磁力搅拌2h,固相机械混合分散2h,然后将上述悬浮物进行蒸发、干燥、研磨,得到固体粉末a。2)取1ga样品,在200mlmin-1he保护下,以15℃/min升温至650℃保持3h,接着自然冷却至室温后研磨均匀,得到催化剂前体,标记为edtafena-ht1(mcm-48)。3)取0.25gedtafena-ht1(mcm-48)加入到25ml2mnaoh的乙醇-水(1:1,v:v)溶液中,在55℃搅拌24h,然后用去离子水和乙醇重复洗涤3次、抽滤、干燥,此碱刻蚀过程是为了移除样品中的mcm-48模板,获得脱硅的前体c,命名为edtafena-et(mcm-48)。4)取0.25gedtafena-et(mcm-48)在75℃、30ml2m的hno3溶液中进行酸处理0.5h,完毕进行抽滤、干燥,此阶段产品命名为edtafena-al(mcm-48)。5)取0.15gedtafena-al(mcm-48),在200mlmin-1nh3保护下,以10℃/min升温至950℃并保持2h,然后自然冷却至室温,此阶段产品标记为edtafena-al-ht2(mcm-48),即所述的自负载fe-n-c催化剂。实施例7一种自负载fe-n-c氧还原催化剂,由以下方法制备而得:1)取0.4g的kit-6加入到45ml去离子水中,再加入7.88gedtafena,磁力搅拌0.5h,超声分散2h,然后将上述悬浮物进行蒸发、干燥、研磨,得到固体粉末a。2)取1ga样品,在200mlmin-1n2保护下,以10℃/min升温至750℃保持1h,接着自然冷却至室温后研磨均匀,得到催化剂前体,标记为edtafena-ht1(kit-6)。3)取0.25gedtafena-ht1(kit-6)加入到25ml2mnaoh的乙醇-水(1:1,v:v)溶液中,在70℃搅拌24h,然后用去离子水和乙醇重复洗涤3次、抽滤、干燥,此碱刻蚀过程是为了移除样品中的kit-6模板,获得脱硅的前体c,命名为edtafena-et(kit-6)。4)取0.25gedtafena-et(kit-6)在75℃、30ml0.5m的hc1溶液中进行酸处理0.5h,完毕进行抽滤、干燥,此阶段产品命名为edtafena-al(kit-6)。5)取0.15gedtafena-al(kit-6),在200mlmin-1n2保护下,以10℃/min升温至900℃并保持2h,然后自然冷却至室温,此阶段产品标记为edtafena-al-ht2(kit-6),即所述的自负载fe-n-c催化剂。本发明的实施例中,用于对比的商业20%pt/c为johnsonmatthey公司产。如无特别说明,实施例中所采用的表征及电化学测试手段均为本领域常规的技术手段。表1自负载fe-n-c氧还原催化剂的结构性质参数samplesbet(m2g-1)v(cm3g-1)dp(nm)edtafena-ht1170.034.0edtafena-al2250.413.9edtafena-ht22950.513.9edtafena-ht2(sba-15)930.303.9edtafena-al-ht2(sba-15)3850.833.9表2自负载fe-n-c氧还原催化剂的表面元素组成表3自负载fe-n-c氧还原催化剂在0.1mkoh中催化orr的活性参数由表1-3可见,自负载fe-n-c催化剂窄的介孔孔径分布(~3.9nm),大的比表面积(385m2g-1),高的石墨化程度,较高的n含量和低的表面fe元素含量(<0.5at.%)。起始和半波电势都仅比商业pt/c催化剂(jm,20wt%pt)低10mv。实施例1、2、3制备的系列自负载fe-n-c催化剂和pt/c催化剂催化orr的极化曲线及获得的起始电势(eonset)、半波电势(e1/2)、极限电流密度(jl)和动力学电流密度(jk)如图10和表3所示;不同转速下orr在实施例2制备的edtafena-ht2(sba-15)和实施例3制备的edtafena-al-ht2(sba-15)上的极化曲线及相应的不同电势下的k-l方程拟合线(内置图)分别如图11和图12所示。图1、2示出了实施例1三个阶段产物edtafena-(ht1,al,ht2)的n2吸脱附曲线、孔径分布和磁滞回曲线,结合表1中织构参数,表明了酸处理能够有效除去大量磁性fe物种,同时调控样品的介观结构,获得具有较大比表面积(>220m2g-1)的微-介孔材料。图3、4示出了实施例1产物edtafena-ht2的tem照片及生产的fe物种尺寸统计分布,可以看出剩余的fe物种被包裹在石墨烯或石墨结构中,其颗粒尺寸为纳米级,表明仅裂解edtafena一种前驱体结合酸处理能够在一定程度抑制生成的fe物种聚集导致的颗粒尺寸增大和除掉表面fe物种。图5、6、7、8和9分别示出了实施例2和实施例3合成的edtafena-ht2(sba-15)和edtafena-al-ht2(sba-15)的小角、广角xrd谱图,n2吸/脱附等温线、孔径分布,xps全谱和磁滞回曲线,结合表1和2的数据,结果证明了采用有序介孔分子筛sba-15为牺牲硬模板同时借助酸处理,能够裁剪出具有一定有序度、大比表面积、窄孔径分布、高的石墨化程度和较高n含量的介孔fe-n-c材料,并且几乎所有的晶态铁物种如α-fe、fe3c和fe3o4能够被除掉。图10、11、12和表3分别示出了实施例1、2和3合成的最终阶段的3个样品和pt/c催化剂在o2饱和的0.1mkoh中催化orr的电化学性能,结果显示实施例3合成的edtafena-al-ht2(sba-15)对orr具有最高的催化性能,其eonset、e1/2、jl和jk(0.87v)分别高达0.96v、0.83v、4.20macm-2和1.32macm-2,仅与pt/c的eonset和e1/2相差10mv,并且催化orr以4电子反应途径进行,揭示了以sba-15为硬模板,廉价的有机-无机化合物edtafena兼具fe、n和c前驱体,获得的edtafena-al-ht2(sba-15)的介观结构、高的石墨化程度、较高的n含量有利于活性位的暴露、底产物的传质扩散和活性位密度的增加,从而提升电子转移速率,导致orr活性的提高;另外通过对比实施例2和3合成的edtafena-ht2(sba-15)和edtafena-al-ht2(sba-15)催化orr的所述合成方法能够降低原材料成本,且具有工艺路线灵活、弹性空间大、操作可控等特点,在优化的制备条件下,非常有潜力协同出对orr具有更优异活性的非贵金属催化剂。当前第1页12