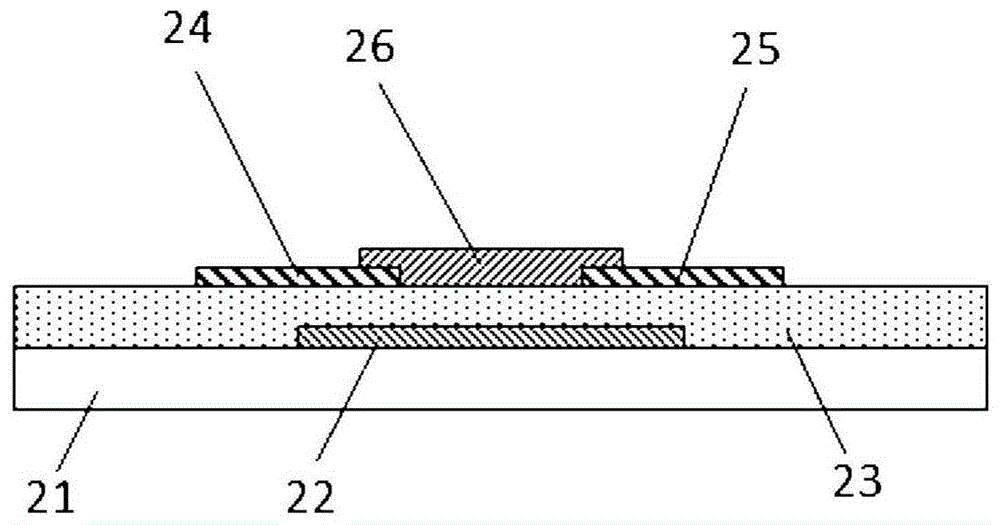
本发明涉及用于形成氧化物的涂覆液(以下可以称为“氧化物形成涂覆液”)、用于制造氧化物膜的方法和用于制造场效应晶体管的方法。
背景技术:
:场效应晶体管(fet)是基于利用沟道电场将电场施加到栅极以在电子流或空穴流中提供栅极的原理来控制源极和漏极之间电流的晶体管。由于其特性,fet被用作例如开关元件和放大元件等。与双极晶体管相比,fet的栅极电流低、结构平坦、易于生产和集成。由于这些原因,fet是用于现有电子器件中的集成电路的基本元件。例如,fet作为薄膜晶体管(fet)已经应用于有源矩阵显示器。近年来,平板显示器(fpd)、液晶显示器、有机电致发光(el)显示器和电子纸等得到了广泛的应用。这些fpd由包含在有源层中使用非晶硅或多晶硅的tft的驱动电路驱动。要求fpd具有增加的尺寸、改善的清晰度和图像质量以及增加的驱动速度。为此,需要具有高载流子迁移率、高开/关比、随时间特性的变化小以及元件之间变化小的tft。然而,非晶硅或多晶硅各有优缺点。因此,很难同时满足上述所有要求。为了响应这些要求,已经在tft上积极地进行开发,在有源层中使用氧化物半导体(其迁移率可以预期高于非晶硅)。例如,公开了在半导体层中使用ingazno4的tft(参见例如非专利文献1)。一般而言,构成tft的半导体层和栅极绝缘膜是通过气相方法如溅射法或cvd(化学气相沉积)法形成的。然而,溅射法和cvd法需要真空设备,并且所需的设备昂贵,这就带来了成本方面的问题。因此,近年来,液相法如狭缝涂覆法受到关注,因为它们不需要这样的真空装置。在液相法中,诸如狭缝涂布和模头涂布以及旋涂等涂布方法使用涂布液。专利文献1公开了一种多组分氧化物半导体的前体涂覆溶液。专利文献1公开了一种前体涂覆液,该前体涂覆液可以通过要求具有高到中等粘度的涂覆液的印刷方法来形成图案,并且可以通过煅烧获得具有半导体电特性的氧化物半导体膜。专利文献2公开了一种半导体层,所述半导体层包括使用含有氧化物半导体前体的溶液或分散液而形成的膜。在专利文献2中,栅极或源极和漏极以及栅极绝缘膜也都通过涂覆来形成。引用文献列表专利文献专利文献1:日本未审查专利申请公开号2014-143403专利文献2:日本未审查专利申请公开号2010-283190非专利文献非专利文献1:k.nomura以及其他5人,“使用非晶氧化物半导体的透明柔性薄膜晶体管的室温制造”,《自然》,第432卷,2004年11月25日,第488至492页(k.nomura,and5others“room-temperaturefabricationoftransparentflexiblethinfilmtransistorsusingamorphousoxidesemiconductors”,nature,vol.432,25,november,2004,pp.488to492)技术实现要素:技术问题本发明的目的是提供一种氧化物形成涂覆液,该涂覆液能够形成抑制其性能劣化的氧化物膜。解决问题的技术方案解决上述问题的手段如下。即,本发明的氧化物形成涂覆液包括:硅(si)和b元素,所述b元素是选自碱土金属中的至少一种。当si元素的浓度由camg/l(毫克每升)表示,并且所述b元素的总浓度由cbmg/l表示时,所述氧化物形成涂覆液中钠(na)和钾(k)的总浓度为(ca+cb)/(1×102)mg/l或更低,并且所述氧化物形成涂覆液中铬(cr)、钼(mo)、锰(mn)、铁(fe)、钴(co)、镍(ni)和铜(cu)的总浓度为(ca+cb)/(1×102)mg/l或更低。本发明的有益效果本发明可以提供一种氧化物形成涂覆液,该氧化物形成涂覆液可以形成具有抑制其性能退化的氧化物膜。附图说明图1a是示出本发明的场效应晶体管的一个示例(底部接触/底栅)的图。图1b是示出本发明的场效应晶体管的一个示例(顶部接触/底栅)的图。图1c是示出本发明的场效应晶体管的一个示例(底部接触/顶栅)的图。图1d是示出本发明的场效应晶体管的一个示例(顶部接触/顶栅)的图。图2a是示出本发明的场效应晶体管的一个示例(底部接触/底栅)的图。图2b是示出本发明的场效应晶体管的一个示例(顶部接触/底栅)的图。图2c是示出本公开的场效应晶体管的一个示例(底部接触/顶栅)的图。图2d是示出本公开的场效应晶体管的一个示例(顶部接触/顶栅)的图。图3a是示出在实施例1和比较例1中制造的场效应晶体管的示意图。图3b是示出在实施例3和比较例3中制造的场效应晶体管的示意图。图3c是示出在实施例5中制造的场效应晶体管的示意图。图4a是示出在实施例2和比较例2中制造的场效应晶体管的示意图。图4b是示出在实施例4和比较例4中制造的场效应晶体管的示意图。图4c是示出实施例6中制造的场效应晶体管的示意图。图5是示出在实施例1~6和比较例1~4中制造的电容器的示意图。具体实施方式本发明人对在形成用于例如场效应晶体管的氧化物膜中应用氧化物形成涂覆液进行了广泛的研究。在研究过程中,本发明人发现在氧化物形成涂覆液的涂覆步骤中产生异物以及在通过涂覆氧化物形成涂覆液形成的氧化物膜的图案化步骤中出现图案缺陷的问题。此外,他们还发现,通过涂覆氧化物形成涂覆液而形成的氧化物膜的性能会发生退化。为了解决上述问题,本发明人继续进行了广泛的研究,发现在氧化物形成涂覆液中含有一定浓度或更高浓度的na、k、cr、mo、mn、fe、co、ni、cu等元素时,出现上述问题。需要注意的是,作为本发明人检索现有技术的结果,本发明人没有发现任何现有技术研究例如氧化物形成涂覆液的原料的纯度以及所述涂覆液的制备条件,以便将在氧化物形成涂覆液的诸如na、k、cr、mo、mn、fe、co、ni和cu等元素控制为在所形成的氧化物膜中以一定或更低的浓度存在。(氧化物形成涂覆液)本发明的氧化物形成涂覆液包括si(硅)和b元素,优选包括c元素,并且必要时包括其它组分。所述b元素是至少一种碱土金属。所述碱土金属的实例包括be(铍)、mg(镁)、ca(钙)、sr(锶)和ba(钡)。所述c元素是选自al(铝)和b(硼)所组成的组中的至少一种。在氧化物形成涂覆液中,当si元素的浓度由camg/l表示,并且所述b元素的总浓度由cbmg/l表示时,所述氧化物形成涂覆液中的钠(na)和钾(k)的总浓度为(ca+cb)/(1×102)mg/l或更低,并且所述氧化物形成涂覆液中铬(cr)、钼(mo)、锰(mn)、铁(fe)、钴(co)、镍(ni)和铜(cu)的总浓度为(ca+cb)/(1×102)mg/l或更低。更优选地,在所述氧化物形成涂覆液中,当si元素的浓度由camg/l表示,并且所述b元素的总浓度由cbmg/l表示时,所述氧化物形成涂覆液中钠(na)和钾(k)的总浓度为(ca+cb)/(1×102)mg/l或以下,并且所述氧化物形成涂覆液中铬(cr)、钼(mo)、锰(mn)、铁(fe)、钴(co)、镍(ni)和铜(cu)的总浓度为(ca+cb)/(1×102)mg/l或更低。可以通过例如电感耦合等离子体光发射光谱(icp-oes)、电感耦合等离子体质谱(icp-ms)、原子吸收光谱(aas)或x射线荧光分析(xrf)来测量所述氧化物形成涂覆液中si元素的浓度ca和所述b元素的浓度cb。可以通过例如电感耦合等离子体光发射光谱(icp-oes)、电感耦合等离子体质谱(icp-ms)、原子吸收光谱(aas)或x射线荧光分析(xrf)来测量所述氧化物形成涂覆液中na、k、cr、mo、mn、fe、co、ni和cu的浓度。所述氧化物形成涂覆液中si和所述b元素之间的组成比没有特别地限制,并且可以根据预期目的适当地选择,但优选在以下范围内。就相应的氧化物(sio2、beo、mgo、cao、sro和bao)而言,在所述氧化物形成涂覆液中si和所述b元素之间的组成比(si:b元素)优选为50.0mol%到90.0mol%:10.0mol%到50.0mol%。所述氧化物形成涂覆液中si、所述b元素和所述c元素之间的组成比没有特别地限制,并且可以根据预期目的适当地选择,但优选在以下范围内。就相应的氧化物(sio2、beo、mgo、cao、sro、bao、al2o3和b2o3)而言,所述氧化物形成涂覆液中si、所述b元素和所述c元素之间的组成比(si:b元素:c元素)优选为50.0mol%到90.0mol%:5.0mol%到20.0mol%:5.0mol%到30.0mol%。所述氧化物形成涂覆液至少包括例如含硅化合物和含碱土金属化合物(含b元素化合物),优选地包括含c元素化合物,并且如果需要,还包括其它成分如溶剂。所述氧化物形成涂覆液包括例如选自所述硅的无机盐、氧化物、氢氧化物、卤化物、金属络合物和有机盐所组成的组中的至少一种。所述氧化物形成涂覆液包括例如选自所述b元素的无机盐、氧化物、氢氧化物、卤化物、金属络合物和有机盐所组成的组中的至少一种。所述氧化物形成涂覆液包括例如选自所述c元素的无机盐、氧化物、氢氧化物、卤化物、金属络合物和有机盐所组成的组中的至少一种。所述无机盐包括例如选自硝酸盐、硫酸盐、碳酸盐、乙酸酯和磷酸盐所组成的组中的至少一种。所述卤化物包括例如选自氟化物、氯化物、溴化物和碘化物所组成的组中的至少一种。例如,所述有机盐包括选自羧酸盐、石碳酸、以及它们的衍生物所组成的组中的至少一种。-含硅化合物-所述含硅化合物是含有硅的化合物。所述含硅化合物的实例包括四氯硅烷、四溴硅烷、四碘硅烷、四甲氧基硅烷、四乙氧基硅烷、四异丙氧基硅烷、四丁氧基硅烷、1,1,1,3,3,3-六甲基二硅氮烷(hmds)、双(三甲基甲硅烷基)乙炔、三苯基硅烷、2-乙基己酸硅和四乙酰氧基硅烷。-含碱土金属化合物(含b元素化合物)-含碱土金属化合物(含b元素的化合物)是含有碱土金属的化合物。含碱土金属化合物(含b元素化合物)的实例包括硝酸镁、硝酸钙、硝酸锶、硝酸钡、硫酸镁、硫酸钙、硫酸锶、硫酸钡、氯化镁、氯化钙、氯化锶、氯化钡、氟化镁、氟化钙、氟化锶、氟化钡、溴化镁、溴化钙、溴化锶、溴化钡、碘化镁、碘化钙、碘化锶、碘化钡、氧化镁、氧化钙、氧化锶、氧化钡、氢氧化镁、氢氧化钙、氢氧化锶、氢氧化钡、氢氧化镁、甲醇镁、乙醇镁、二乙基镁、醋酸镁、甲酸镁、乙酰丙酮镁、2-乙基己酸镁、乳酸镁、环烷酸镁、柠檬酸镁、水杨酸镁、苯甲酸镁、草酸镁、三氟甲烷磺酸镁、甲醇钙、乙醇钙、乙酸钙、甲酸钙、乙酰丙酮钙、二新戊酰基甲烷钙(calciumdipivaloylmethanate)、2-乙基己酸钙、乳酸钙、环烷酸钙、柠檬酸钙、水杨酸钙、新癸酸钙、苯甲酸钙、草酸钙、异丙醇锶、乙酸锶、甲酸锶、乙酰丙酮锶、2-乙基己酸锶、乳酸锶、环烷酸锶、水杨酸锶、草酸锶、乙醇钡、异丙醇钡、乙酸钡、甲酸钡、乙酰丙酮钡、2-乙基己酸钡、乳酸钡、环烷酸钡、新癸酸钡、草酸钡、苯甲酸钡、三氟甲烷磺酸钡。-含c元素化合物-所述含c元素的化合物是含有所述c元素的化合物。所述含c元素化合物的实例包括硝酸铝、硫酸铝、硫酸铝铵、氧化硼、硼酸、氢氧化铝、磷酸铝、氟化铝、氯化铝、溴化硼、溴化铝、碘化铝、异丙醇铝、仲丁醇铝、三乙基铝、二乙基乙醇铝、乙酸铝、乙酰丙酮铝、六氟乙酰丙酮铝、2-乙基己酸铝、乳酸铝、苯甲酸铝、二(仲丁氧基)乙酰乙酸铝酯螯合物、三氟甲基磺酸铝、(r)-5,5-二苯基-2-甲基-3,4-丙-1,3,2-噁唑硼烷、硼酸三异丙酯、2-异丙氧基-4,4,5,5-四甲基-1,3,2-二氧硼杂环戊烷、双(己烯甘醇酸)二硼、4-(4,4,5,5-四甲基-1,3,2-二氧硼杂环戊烷-2-基)-1h-吡唑、(4,4,5,5-四甲基-1,3,2-二氧硼杂环戊烷-2-基)苯、叔丁基-n-[4-(4,4,5,5-四甲基-1,2,3-二氧硼杂环戊烷-2-基)苯基]氨基甲酸酯、苯硼酸、3-乙酰苯基硼酸、三氟化硼乙酸络合物、三氟化硼环丁砜络合物、2-噻吩硼酸和三(三甲基硅基)硼酸酯。-溶剂-所述溶剂的实例包括有机酸、有机酸酯、芳香族化合物、二醇、乙二醇醚、极性非质子溶剂、烷烃化合物、烯烃化合物、醚、醇和水。可以单独使用或组合使用这些溶剂。所述氧化物形成涂覆液中溶剂的量没有特别地限制,并且可以根据预期目的适当地选择。所述溶剂没有特别地限制,并且可以根据预期目的适当地选择,只要它是稳定地溶解或分散上述各种金属源的溶剂。所述溶剂的实例包括甲苯、二甲苯、均三甲苯、异丙苯、戊基苯、十二烷基苯、双环己基、环己基苯、癸烷、十一烷、十二烷、十三烷、十四烷、十五烷、四氢萘、十氢萘、异丙醇、苯甲酸乙酯、n,n-二甲基甲酰胺、碳酸亚丙酯、2-乙基己酸、矿物油,二甲基丙烯脲、4-丁内酯、甲醇、乙醇、1-丁醇、1-丙醇、1-戊醇、2-甲氧基乙醇和水。(氧化物形成涂覆液的生产方法)与本发明有关的用于生产氧化物形成涂覆液的方法没有特别地限制,并且可以根据预期目的适当地选择。所述方法包括,例如,测量含有硅和所述b元素的氧化物形成涂覆液中na、k、cr、mo、mn、fe、co、ni和cu的浓度。可以通过例如电感耦合等离子体光发射光谱法(icp-oes)、电感耦合等离子体质谱法(icp-ms)、原子吸收光谱法(aas)或x射线荧光分析法(xrf)来测量氧化物形成涂覆液中na、k、cr、mo、mn、fe、co、ni和cu的浓度。(氧化物形成涂层液的评价方法)与本发明有关的用于评价氧化物形成涂覆液体的方法没有特别地限制,并且可以根据预期目的适当地选择。所述方法包括,例如,测量含有硅和所述b元素的氧化物形成涂覆液中na、k、cr、mo、mn、fe、co、ni和cu的浓度。可以通过例如电感耦合等离子体光发射光谱法(icp-oes)、电感耦合等离子体质谱法(icp-ms)、原子吸收光谱法(aas)或x射线荧光分析法(xrf)来测量氧化物形成涂覆液中na、k、cr、mo、mn、fe、co、ni和cu的浓度。在上述评价方法中,例如,当氧化物形成涂覆液中的硅(si)元素的浓度由camg/l表示,并且氧化物形成涂覆液中的所述b元素的总量由cbmg/l表示时,以及当所述氧化物形成涂覆液中的na和k的总浓度为(ca+cb)/(1×102)mg/l或以下,并且所述氧化物形成涂覆液中cr、mo、mn、fe、co、ni和cu的总浓度为(ca+cb)/(1×102)mg/l或更低时,评价认定已获得本发明的氧化物形成涂覆液。(氧化物膜的生产方法)将描述使用氧化物形成涂覆液来生产氧化物膜的方法的一个示例。在生产氧化物膜的方法中,涂覆并且热处理所述氧化物形成涂覆液以获得所述氧化物膜。制备氧化物膜的方法包括,例如,涂覆步骤和热处理步骤;如有必要,还包括其他步骤。所述涂覆步骤没有特别地限制,并且可以根据预期目的适当地选择,只要涂覆步骤是将氧化物形成涂覆液涂覆到待涂覆的对象上的步骤。涂覆方法没有特别地限制,并且可以根据预期目的适当地选择。所述方法的实例包括:通过溶液工艺形成膜以及通过光刻对该膜进行图案化的方法;以及通过印刷如喷墨印刷、纳米压印或凹印来直接形成具有所需形状的膜的方法。所述溶液工艺的实例包括浸涂、旋涂、模涂和喷嘴印刷。所述热处理步骤没有特别地限制,并且可以根据预期目的适当地选择,只要热处理步骤是热处理涂覆在待涂覆的对象上的氧化物形成涂覆液的步骤。需要注意的是,在所述热处理步骤中,可以通过例如空气干燥来干燥涂覆在待涂覆的对象上的氧化物形成涂覆液。例如,通过所述热处理,干燥溶剂并烘烤氧化物。在所述热处理步骤中,优选在不同温度下进行溶剂的干燥(以下称为“干燥处理”)和氧化物的烘烤(以下称为“烘烤处理”)。具体而言,优选在溶剂干燥之后升高温度以烘烤所述氧化物。例如,在烘烤氧化物时,发生选自含硅化合物、含b元素化合物和含c元素化合物所组成的组中的至少一种化合物的分解。所诉干燥处理的温度没有特别地限制,并且可以根据所包含的溶剂来适当地选择。例如,干燥处理的温度为80℃~180℃。至于干燥,例如,使用真空烘箱来降低所需温度是有效的。干燥处理的时间没有特别地限制,可以根据预期目的适当选择。例如,干燥处理的时间为30秒至1小时。烘烤处理的温度并没有特别地限制,可以根据预期用途适当选择。然而,烘烤处理的温度优选为100℃或更高但低于450℃,更优选为200℃至400℃。烘烤处理的时间并没有特别地限制,可以根据预期用途适当选择。例如,烘烤处理的时间为30分钟至5小时。需要注意的是,在热处理步骤中,可以连续地进行干燥处理和烘烤处理,或者可以以多个步骤的分割方式进行。所述热处理方法并没有特别地限制,可以根据预期用途适当选择。所述热处理方法的示例包括加热待涂覆的对象的方法。所述热处理中的大气并没有特别地限制,可以根据预期用途适当选择。然而,所述大气优选为空气或氧气气氛。当在大气或氧气气氛中进行所述热处理时,分解产物可以迅速排放到系统外部,并且可以加速氧化物的生成。在所述热处理中,考虑到生成处理的反应加速,在干燥处理后,将波长为400nm或更短的紫外光应用于材料是有效的。使用波长为400nm或更短的紫外光,可以使在例如干燥处理后的材料中所包含的无机材料和所述有机材料的化学键断裂,并且可以分解无机材料和有机材料。因此,可以有效地形成氧化物。波长为400nm或更短的紫外射线并没有特别地限制,并且可以根据预期用途适当地选择。紫外射线的例子包括从准分子灯发射的波长为222nm的紫外射线。此外,优选使用臭氧取代紫外射线,或者臭氧与紫外线结合使用。干燥处理后,将臭氧应用于所述材料,可以加速氧化物的生成。在形成氧化物涂覆液中,溶质均匀溶解在所述溶剂中。因此,使用所述氧化形成涂覆液形成的氧化物膜是均匀的。例如,所形成的氧化物膜可以是用作栅极绝缘膜时具有低泄漏电流的氧化物膜。所形成的氧化物膜可以是用作钝化层时具有阻挡性(例如,阻挡空气中的水分和氧气)的氧化物膜。在所述形成氧化物涂覆液中,当硅(si)元素的浓度由camg/l表示,并且所述b元素的总浓度由cbmg/l表示时,所述形成氧化物涂覆液中na和k的总浓度为(ca+cb)/(1×102)mg/l或以下。因此,当使用所述形成氧化物涂覆液形成的氧化物膜为绝缘体膜时,由于na和k而产生的泄漏电流低。可以提供优良的绝缘膜。类似地,在所述形成氧化物涂覆液中,当硅(si)元素的浓度由camg/l表示,并且所述b元素的总浓度由cbmg/l表示时,所述形成氧化物涂覆液中na和k的总浓度为(ca+cb)/(1×102)mg/l或以下。因此,当使用形成氧化物涂覆液形成的氧化物膜是钝化层时,由于na和k在阻挡性能(例如,阻挡空气中的水分和氧)上的劣化降低。可以提供优良的钝化膜。此外,在所述形成氧化物涂覆液中,当硅(si)元素的浓度由camg/l表示,并且所述b元素的总浓度由cbmg/l表示时,所述形成氧化物涂覆液中cr、mo、mn、fe、co、ni和cu的总浓度为(ca+cb)/(1×102)mg/l或以下。因此,在蚀刻使用所述氧化形成涂覆液形成的氧化物膜时,由于cr、mo、mn、fe、co、ni和cu而产生的刻蚀残留物较少。优良图案的氧化物膜是可能的。(生产场效应晶体管的方法1)下面是使用所述氧化物膜(栅极绝缘膜)生产场效应晶体管的情况的一个实例,所述氧化物膜是使用所述氧化物形成涂覆液而生产的。所述场效应晶体管至少包括栅极绝缘膜;并且如有必要,还包括诸如栅极、源极、漏极和半导体层等其他组件。-栅极-栅极例如与栅绝缘膜接触并且经由栅极绝缘膜面对半导体层。栅极没有特别地限制,并且只要栅极是被配置为向场效应晶体管施加栅极电压的电极,就可以根据预期目的适当地选择栅极。栅极的材料没有特别地限制,并且可以根据预期目的适当地选择。所述材料的实例包括:金属(例如,mo、ti、al、au、ag和cu)和这些金属的合金;透明导电氧化物,例如,氧化铟锡(ito)和掺锑氧化锡(ato);有机导体,例如,聚乙烯二氧噻吩(pedot)和聚苯胺(pani)。--栅极的形成方法--栅极的形成方法没有特别地限制,并且可以根据预期目的适当地选择。所述形成方法的实例包括:(i)通过溅射或浸涂形成膜并且通过光刻形成图案的方法;以及(ii)通过印刷工艺如喷墨印刷、纳米压印或凹印来直接形成具有所需形状的膜的方法。栅极的平均膜厚度没有特别地限制,并且可以根据预期目的适当地选择。然而,栅极的平均膜厚度优选为20nm至1微米,更优选为50nm至300nm。-源极和漏极-源极和漏极没有特别地限制,并且可以根据预期目的适当地选择,只要它们是配置成从场效应晶体管中取出电流的电极。源极和漏极的材料没有特别地限制,并且可以根据预期目的适当地选择。所述材料的实例包括:金属(例如,mo、al、au、ag和cu)和这些金属的合金;透明导电氧化物如氧化铟锡(ito)和掺锑氧化锡(ato);有机导体如聚乙烯二氧噻吩(pedot)和聚苯胺(pani)。--源极和漏极的形成方法--源极和漏极的形成方法没有特别地限制,并且可以根据预期目的适当地选择。形成方法的实例包括:(i)通过溅射或浸涂形成膜并通过光刻形成图案的方法;以及(ii)通过印刷工艺如喷墨印刷、纳米压印或凹印来直接形成具有所需形状的膜的方法。源极和漏极的平均膜厚度没有特别地限制,并且可以根据预期目的适当地选择。然而,平均膜厚度优选地为20nm至1微米,更优选地为50nm至300nm。-半导体层-所述半导体层例如设置与源极和漏极相邻。所述半导体层包括沟道形成区、源极区和漏极区。所述源极区与所述源极接触。所述漏极区域与漏极接触。所述源极区和所述漏极区的比电阻优选地低于沟道形成区的比电阻。所述半导体层的材料没有特别地限制,并且可以根据预期目的适当地选择。这种材料的例子包括硅半导体和氧化物半导体。所述硅半导体的例子包括非晶硅和多晶硅。所述氧化物半导体的实例包括in-ga-zn-o、in-zn-o和in-mg-o。在这些实例中,氧化物半导体是优选的。--半导体层的形成方法—所述半导体层的形成方法没有特别地限制,并且可以根据预期目的适当地选择。所述形成方法的实例包括:通过真空工艺(例如,溅射、脉冲激光沉积(pld)、化学气相沉积(cvd)或原子层沉积(ald))或溶液工艺(例如,浸涂、旋涂或模涂)形成膜并且通过光刻来对所述膜进行图案化的方法;以及通过诸如喷墨打印、纳米压印或凹印等打印方法直接形成具有所需形状的膜的方法。所述半导体层的平均膜厚度没有特别地限制,并且可以根据预期目的适当地选择。然而,所述半导体层的平均膜厚度优选为5nm至1微米,更优选为10nm至0.5微米。-栅极绝缘膜-栅极绝缘膜例如设置在栅极和半导体层之间。--使用氧化物形成涂覆液形成栅极绝缘膜的方法--栅极绝缘膜的形成方法没有特别地限制,并且可以根据预期目的适当地选择。如以上部分(氧化物膜的生产方法)所述的,优选使用氧化物形成涂覆液的涂覆方法如旋涂、模涂或喷涂。所述栅极绝缘膜的平均膜厚度没有特别地限制,并且可以根据预期目的适当地选择。然而,所述栅极绝缘膜的平均膜厚度优选为50nm至3微米,更优选为100nm至1微米。所述场效应晶体管的结构没有特别地限制,并且可以根据预期目的适当地选择。所述场效应晶体管的结构实例包括以下结构:(1)场效应晶体管,包括衬底、形成在衬底上的栅极、形成在栅极上的栅极绝缘膜、形成在栅极绝缘膜上的源极和漏极以及形成在源极和漏极之间的半导体层;和(2)场效应晶体管,包括衬底;形成在衬底上的源极和漏极;形成在源极和漏极之间的半导体层;形成在源极、漏极和半导体层上的栅极绝缘膜;以及形成在栅极绝缘膜上的栅极。具有上述(1)中所述的结构的场效应晶体管是,例如,底部接触/底栅类型(图1a)和顶部接触/底栅类型(图1b)。具有上述(2)中所述的结构的场效应晶体管是,例如,底部接触/顶栅类型(图1c)和顶接触/顶栅类型(图1d)。在图1a至图1d中,附图标记21表示衬底,附图标记22表示栅极,附图标记23表示栅极绝缘膜,附图标记24表示源极,附图标记25表示漏极,附图标记26表示氧化物半导体层。(生产场效应晶体管的方法2)下面是使用氧化物膜(钝化层)生产场效应晶体管的情况的一个实例,所述氧化物膜是使用氧化物形成涂覆液来生产的。所述场效应晶体管至少包括钝化层;如有必要,还包括诸如栅极、源极、漏极和半导体层的其它组件。-栅极-所述栅极例如与栅极绝缘膜接触并且经由栅极绝缘膜面对半导体层。所述栅极没有特别地限制,并且只要栅极是被配置为向场效应晶体管施加栅极电压的电极,就可以根据预期目的适当地选择栅极。所述栅极的材料没有特别地限制,并且可以根据预期目的适当地选择。所述材料的实例包括:金属(例如,mo、ti、al、au、ag和cu)和这些金属的合金;透明导电氧化物如氧化铟锡(ito)和掺锑氧化锡(ato);有机导体如聚乙烯二氧噻吩(pedot)和聚苯胺(pani)。--栅极的形成方法--所述栅极的形成方法没有特别地限制,并且可以根据预期目的适当地选择。所述形成方法的实例包括:(i)通过溅射或浸涂形成膜并且通过光刻使所述膜图案化的方法;以及(ii)通过印刷工艺如喷墨印刷、纳米压印或凹印来直接形成具有所需形状的膜的方法。所述栅极的平均膜厚度没有特别地限制,并且可以根据预期目的适当地选择。然而,所述栅极的平均膜厚度优选为20nm至1微米,更优选为50nm至300nm。--源极和漏极的形成方法--源极和漏极的形成方法没有特别地限制,并且可以根据预期目的适当地选择。所述形成方法的实例包括:(i)通过溅射或浸涂形成膜并且通过光刻使所述膜图案化的方法;以及(ii)通过印刷工艺如喷墨印刷、纳米压印或凹印来直接形成具有所需形状的膜的方法。所述源极和所述漏极的平均膜厚度没有特别地限制,并且可以根据预期目的适当地选择。然而,平均膜厚度优选地为20nm至1微米,更优选地为50nm至300nm。-半导体层-所述半导体层例如设置与所述源极和所述漏极相邻。所述半导体层包括沟道形成区、源极区和漏极区。所述源极区与源极接触。所述漏极区域与漏极电极接触。所述源极区和所述漏极区的比电阻优选地低于沟道形成区的比电阻。所述半导体层的材料没有特别地限制,并且可以根据预期目的适当地选择。这种材料的实例包括硅半导体和氧化物半导体。所述硅半导体的实例包括非晶硅和多晶硅。所述氧化物半导体的实例包括in-ga-zn-o、in-zn-o和in-mg-o。在这些示例中,氧化物半导体是优选的。--半导体层的形成方法--所述半导体层的形成方法没有特别地限制,并且可以根据预期目的适当地选择。所述形成方法的实例包括:通过真空工艺(例如,溅射、脉冲激光沉积(pld)、化学气相沉积(cvd)或原子层沉积(ald))或溶液工艺(例如,浸涂、旋涂或模涂)形成膜并且通过光刻使所述膜图案化的方法;以及通过诸如喷墨打印、纳米压印或凹印等打印方法来直接形成具有所需形状的膜的方法。所述半导体层的平均膜厚度没有特别地限制,并且可以根据预期目的适当地选择。然而,所述半导体层的平均膜厚度优选为5nm至1微米,更优选为10nm至0.5微米。-栅极绝缘膜-所述栅极绝缘膜例如设置在栅极和半导体层之间。栅极绝缘膜的材料没有特别地限制,可以根据预期用途适当地选择。该材料的实例包括已经用于大规模生产的材料,例如,sio2、sinx和al2o3、高介电常数材料(如la2o3和hfo2)以及有机材料如聚酰亚胺(pi)和氟树脂。或者,使用本发明的氧化物形成涂覆液生产的氧化物膜可以用作栅极绝缘膜。-栅极绝缘膜的形成方法-栅极绝缘膜的形成方法没有特别地限制,并且可以根据预期目的适当地选择。所述形成方法的实例包括:通过真空工艺(例如溅射、化学气相沉积(cvd)或原子层沉积(ald))或印刷工艺(例如,旋涂、模涂或喷墨打印)来形成膜的方法。栅极绝缘膜的平均膜厚度没有特别地限制,并且可以根据预期目的适当地选择。然而,栅极绝缘膜的平均膜厚度优选为50nm至3微米,更优选为100nm至1微米。-钝化层-所述钝化层通常设置在所述衬底上方。--使用氧化形成涂料液形成钝化层的方法--所述钝化层的形成方法并没有特别地限制,并且可以根据预期目的适当选择。如以上部分(氧化物膜的生产方法)所述的,优选使用氧化物形成涂覆液的涂覆方法如旋涂、模涂或喷墨涂覆。所述钝化层的平均膜厚度没有特别地限制,可以根据预期用途适当地选择。然而,所述钝化层的平均膜厚度优选为50nm至3微米,更优选地为100nm至1微米。所述场效应晶体管的结构没有特别地限制,并且可以根据预期目的适当地选择。所述场效应晶体管的结构实例包括以下结构:(3)场效应晶体管,包括衬底、在衬底上形成的栅极、在栅极上形成的栅极绝缘膜、在栅极绝缘膜上形成的源极和漏极、在源极与漏极之间形成的半导体层、以及在源极、漏极和半导体层上形成的钝化层;和(4)场效应晶体管,包括衬底、在衬底上形成的源极与漏极、在所述源极与所述漏极之间形成的半导体层、在所述源极、所述漏极和所述半导体层上形成的栅极绝缘膜、在栅极绝缘膜上形成的栅极、以及在栅极绝缘膜和所述栅极上形成的钝化层。具有上述(3)中描述的结构的场效应晶体管例如是底部接触/底栅类型(图2a)和顶部接触/底栅类型(图2b)。具有上述(4)中所述的结构的场效应晶体管是,例如,底部接触/顶栅类型(图2c)和顶部接触/顶栅类型(图2d)。在图2a至图2d中,附图标记21表示衬底,附图22表示栅极,附图23表示栅极绝缘膜,附图标记24表示源极,附图25表示漏极,附图标记26表示氧化物半导体层,附图27表示钝化层。实施例将通过实例描述本发明,但这些实施例不应解释为以任何方式限制本发明。(实施例1)-氧化物形成涂覆液的制备-将1.50ml的环己基苯(cica特级,纯度97.0%,产品编号07670-00,可从关东化学有限公司(kantochemicalco.,inc.)获得)、0.55ml的四丁氧基硅烷(产品编号t5702,可从西格玛-奥德里奇公司(sigma-aldrich)获得)和0.28ml的2-乙基己酸镁(产品编号12-1260,可从strem公司获得)在1.50ml的甲苯(primepure级,纯度99.9%,产品编号40180-79,可从关东化学有限公司获得)中混合,以获得氧化物形成涂覆液。在1000级洁净室中制备实施例1中的氧化物形成涂覆液。1000级洁净室是指在0.028m3的体积中含有小于等于1000个0.5微米或以上的颗粒的环境。接着,生产如图3a中所示的底部接触/底栅场效应晶体管。<场效应晶体管的生产>-栅极的形成-首先,在玻璃衬底(衬底91)上形成栅极92。具体地,通过直流溅射在玻璃衬底(衬底91)上形成mo(钼)膜,从而获得约100nm的平均膜厚度。此后,在其上涂覆光致抗蚀剂,并且将所获得物经受预烘烤、由曝光装置进行曝光、以及显影,从而形成具有与待形成的栅极92的图案相同的图案的抗蚀剂图案。此外,通过反应离子刻蚀(rie)去除了无抗蚀剂图案区的mo膜。此后,还移除抗蚀剂图案以形成由mo膜形成的栅极92。-栅极绝缘膜的形成-接着,将0.6ml的氧化物形成涂覆液滴到衬底91和栅极92上,并且在预定条件下旋涂(以500rpm旋转5秒,然后以3000rpm旋转20秒,并且停止旋转以便在5秒内为0rpm)。随后,将所获得的产物在120℃下在大气中干燥1小时,然后在400℃下在o2气氛中烘烤3小时,从而形成氧化物膜。此后,在氧化物膜上涂覆光致抗蚀剂,并且对所得物进行预烘烤、通过曝光装置进行曝光、以及进行显影,从而形成与待形成的栅极绝缘膜93具有相同图案的抗蚀剂图案。此外,通过湿法刻蚀去除了无抗蚀剂图案区的氧化物膜。此后,还移除抗蚀剂图案以形成栅极绝缘膜93。栅极绝缘膜的平均膜厚为约35nm。-源极和漏极的形成-接着,在栅极绝缘膜93上形成源极94和漏极95。具体地,通过直流溅射在栅极绝缘膜93上形成mo(mo)膜,使得平均膜厚度约为100nm。此后,在mo膜上涂覆光致抗蚀剂,并且对所得物进行预烘烤、由曝光装置进行曝光、以及进行显影,从而形成具有与待形成的源极94和漏极95的图案相同的图案的抗蚀剂图案。此外,通过rie去除了无抗蚀剂图案区的mo膜。此后,还移除了抗蚀剂图案以形成源极94和漏极95,其中每个电极均由mo膜形成。-氧化物半导体层的形成-接着,形成氧化物半导体层96。具体地,通过直流溅射形成mg-in基氧化物(in2mgo4)膜,使得平均膜厚度约为100nm。此后,在mg-in基氧化物膜上涂覆光致抗蚀剂,并且对所获得物进行预烘烤、通过曝光装置进行曝光、以及进行显影,以形成具有与待形成的氧化物半导体层96的图案相同的图案的抗蚀剂图案。通过湿法刻蚀去除无抗蚀剂图案区的镁铟基氧化物膜。此后,还移除抗蚀剂图案以形成氧化物半导体层96。其结果是,以在源极94和漏极95之间形成沟道的方式来形成氧化物半导体层96。最后,作为后处理的热处理,将所获得产物在大气中在300℃下进行热处理1小时,从而完成场效应晶体管。<用于介电常数评估的电容器的生产>接下来,生产具有图5所示结构的电容器。具体地,使用在待形成下电极102的区域中具有开口的金属掩膜,通过真空气相沉积方法在玻璃衬底(衬底101)上形成al(铝)膜,以使得平均膜厚度约为100nm。通过在实施例1中的场效应晶体管的栅极绝缘膜的形成中所描述的方法,形成平均薄膜厚度为约35nm的绝缘体薄膜103。最后,使用在待形成上电极104的区域中具有开口的金属掩膜,通过真空气相沉积方法形成al膜,以使得平均膜厚度为约100nm,从而完成电容器。(实施例2)-氧化物形成涂覆液的制备-将0.17ml的hmds(1,1,1,3,3,3-六甲基二硅氮烷,可从东京应化工业有限公司(tokyoohkakogyoco.,ltd)获得)、0.01g的硝酸钙(产品编号032-00747,可从华科纯化工有限公司获得)和0.02g的乳酸钡(产品号021-00272)在2.50ml的超纯水(产品编号95305-1l,可从西格玛奥德里奇(sigmaaldrich)公司获得)中混合,以获得氧化形成涂覆液。在1000级洁净室中制备了实施例2中氧化形成涂覆液。接下来,生产如图4a所示的底部接触/底栅型场效应晶体管。<场效应晶体管的生产>-栅极的形成-首先,在玻璃衬底(衬底91)上形成栅极92。具体地,通过直流溅射在玻璃衬底(衬底91)上形成mo(钼)膜,从而具有约100nm的平均膜厚度。此后,在其上涂覆光致抗蚀剂,并且将所获得物经受预烘烤、由曝光装置进行曝光、以及进行显影,从而形成具有与待形成的栅极92的图案相同的图案的抗蚀剂图案。此外,通过反应离子刻蚀(rie)去除了无抗蚀剂图案区的mo膜。此后,还移除抗蚀剂图案以形成由mo膜形成的栅极92。-栅极绝缘膜的形成-接着,在衬底91和栅极92上形成栅极绝缘膜93。具体地,通过直流溅射在其上形成sio2薄膜,使其平均薄膜厚度为约120nm。此后,在其上涂覆光致抗蚀剂,并且将所获得物预焙烤、由曝光装置进行曝光、以及显影,从而形成具有与待形成的栅极绝缘膜93相同图案的抗蚀图案。此外,通过湿法刻蚀去除了无抗蚀剂图案区的sio2膜。此后,还去除了所述抗蚀图案,以形成由sio2膜形成的栅极绝缘膜93。-源极和漏极的形成-接着,在栅极绝缘膜93上形成源极94和漏极95。具体地,通过直流溅射在栅极绝缘膜93上形成mo(mo)膜,使得平均膜厚度为约100nm。此后,在mo膜上涂覆光致抗蚀剂,对所获得物进行预烘烤、由曝光装置曝光、以及进行显影,从而形成具有与待形成的源极94和漏极95的图案相同的图案的抗蚀剂图案。此外,用rie去除了无抗蚀剂图案区的mo膜。此后,还移除抗蚀剂图案以形成源极94和漏极95,其中每个电极均由mo膜形成。-氧化物半导体层的形成-接着,形成氧化物半导体层96。具体地,通过直流溅射形成mg-in基氧化物(in2mgo4)膜,使得平均膜厚度为约100nm。此后,在mg-in基氧化物膜上涂覆光致抗蚀剂,对所获得物进行预烘烤、通过曝光装置进行曝光、以及进行显影,以形成具有与待形成的氧化物半导体层96的图案相同的图案的抗蚀剂图案。通过湿法刻蚀去除了无抗蚀剂图案区的镁铟基氧化物膜。此后,还移除抗蚀剂图案以形成氧化物半导体层96。其结果是,以在源极94和漏极95之间形成沟道的方式形成氧化物半导体层96。-钝化层的形成-接下来,将0.6ml的氧化形成涂覆液滴到衬底上,在预定条件下旋涂(以500rpm旋转5秒,然后以3000rpm旋转20秒,停止旋转以在5秒内为0rpm)。随后,将所获得物在120℃下在大气中干燥1小时,然后在400℃下在o2气氛中烘烤3小时,从而形成氧化物膜。此后,在氧化物膜上涂覆光致抗蚀剂,将所得产物进行预焙烤、由曝光装置曝光、进行显影,从而形成具有与待形成钝化层97相同图案的抗蚀图案。此外,由湿法刻蚀去除了无抗蚀剂图案区的氧化物膜。此后,还去除了该抗蚀图案以形成钝化层97。钝化层平均膜厚为约50nm。最后,作为后处理的热处理,将所获得物在大气中在300℃下进行1小时的热处理,从而完成场效应晶体管。<用于介电常数评估的电容器的生产>接下来,生产具有图5所示结构的电容器。具体地,使用在形成下电极102的区域中具有开口的金属掩膜,通过真空气相沉积方法在玻璃衬底(衬底101)上形成al(铝)膜,以便使平均膜厚度约为100nm。通过在实施例2中的场效应晶体管的钝化层的形成中所述描述的方法,形成平均膜厚度为约41nm的绝缘体薄膜103。最后,使用在待形成上电极104的区域中具有开口的金属掩膜,通过真空气相沉积方法形成al膜,使平均膜厚度为约100nm,从而完成电容器。(实施例3)-氧化物形成涂覆液的制备-将0.51ml的四丁烷氧基硅烷(产品编号t5702,可从西格玛奥德里奇(sigmaaldrich)公司获得)、0.16ml的2-乙基己酸钙(产品编号36657,可从阿法埃莎(alfaaesar)公司获得)、0.83ml的2-乙基己酸锶(产品编号195-09561,可从华科纯化工有限公司获得)和0.16ml的2-乙基己酸钡(产品编号021-09471,可从华科纯化工有限公司获得)在1.00ml的环己基苯(cica特殊等级,纯度97.0%,产品编号07560-00,可从关东化学株式会社获得)中混合,从而获得所述形成氧化物涂覆液。在1000级洁净室中制备了实施例3中的氧化物形成涂覆液。将作为溶剂的环己烷通过pfa管进行了给料。接下来,生产了如图3b所示的底部接触/顶栅型场效应晶体管。<场效应晶体管的生产>-源极和漏极的形成-首先,在玻璃衬底(衬底91)上形成源极94和漏极95。具体地,在衬底上通过直流溅射形成mo(钼)膜,使其平均薄膜厚度为约100nm。此后,在mo膜上涂覆光致抗蚀剂,对所获得物进行预烘烤、由曝光装置曝光、并且进行显影,从而形成具有与待形成的源极94和漏极95的图案相同的图案的抗蚀剂图案。此外,通过刻蚀去除了无抗蚀剂图案区的mo膜。此后,还移除抗蚀剂图案以形成源极94和漏极95,其中每个电极均由mo膜形成。-氧化物半导体层的形成-接着,形成氧化物半导体层96。具体地,通过直流溅射形成了in-ga-zn基氧化物膜,使得平均膜厚度为约100nm。此后,在in-ga-zn基氧化物膜上涂覆光刻胶,并且将所获得的产物进行预烘烤、由曝光装置曝光、并且进行显影,以形成与待形成的氧化物半导体层96相同的图案的抗蚀图案。此外,通过刻蚀去除了无抗蚀剂图案区的in-ga-zn基氧化物膜。此后,还移除抗蚀剂图案以形成氧化物半导体层96。其结果是,以在源极94和漏极95之间形成沟道的方式形成氧化物半导体层96。-栅极绝缘膜的形成-接下来,将0.25ml的氧化形成涂覆液滴到所述衬底、氧化物半导体层、源极、漏极上,并且在预定条件下旋涂(在500rpm下旋转5秒,然后在2000rpm下旋转20秒,并且停止旋转以在5秒内为0rpm)。随后,将所获得物在120后下在大气中干燥1小时,然后在400然下在o2气氛中烘烤3小时,从而形成氧化物膜。此后,在氧化物膜上涂覆光致抗蚀剂,并且对所获得物进行预烘烤、通过曝光装置进行曝光、并且进行显影,从而形成与待形成的栅极绝缘膜93具有相同图案的抗蚀剂图案。此外,通过湿法刻蚀去除了无抗蚀剂图案区的氧化物膜。此后,还移除抗蚀剂图案以形成栅极绝缘膜93。栅极绝缘膜的平均厚度为约51nm。-栅极的形成-接着,在栅极绝缘膜上形成栅极92。具体地,通过直流溅射在栅极绝缘膜上形成mo(钼)膜,使其平均膜厚为约100nm。此后,在mo膜上涂覆光刻胶,并且将所获得物进行预烘烤、由曝光装置曝光、并且进行显影,从而形成具有与待形成的栅极92相同图案的抗蚀图案。此外,通过刻蚀去除了无抗蚀剂图案区的mo膜。此后,还移除抗蚀剂图案以形成由mo膜形成的栅极92。最后,作为后处理的热处理,将所获得物在大气中在300℃下进行热处理1小时,从而完成场效应晶体管。<用于介电常数评估的电容器的生产>接下来,生产如图5所示结构的电容器。具体地,使用在形成下电极102的区域中具有开口的金属掩膜,通过真空气相沉积法在玻璃衬底(衬底101)上形成al(铝)膜,以便使平均膜厚度为约100nm。通过在实施例3中的场效应晶体管的栅极绝缘膜的形成中所描述的方法,形成平均膜厚为约32nm的绝缘体薄膜103。最后,使用在待形成上电极104的区域中具有开口的金属掩膜,通过真空气相沉积方法形成al膜,以使得平均膜厚度为约100nm,从而完成电容器。(实施例4)-氧化物形成涂覆液的制备-将0.50ml的乙醇(电子工业级,纯度99.5%,可从关东化学有限公司获得)、0.09ml的hmds(1,1,1,3,3,3-六甲基二硅氮烷,可从东京应化工业有限公司获得)、0.02mg的硫酸铝(产品编号018-09745,可从华科纯化工有限公司获得)、0.01g的硼酸(产品编号025-02193,可从华科纯化工有限公司获得)、0.01g的硝酸钙(产品编号032-00747,可从华科纯化工有限公司获得)和0.01g的氯化锶(产品编号193-04185,可从华科纯化工公司获得)在1.60ml超纯水(产品编号95305-1l,可从西格玛奥德里奇(sigmaaldrich)公司获得)中混合,从而获得氧化形成涂覆液。在1000级洁净室中制备了实施例4中的氧化物形成涂覆液。作为溶剂的乙醇和超纯水通过pfa管进行了给料。接下来,生产如图4b所示的底部接触/顶栅型场效应晶体管。<场效应晶体管的生产>-源极和漏极的形成-首先,在玻璃衬底(衬底91)上形成源极94和漏极95。具体地,通过直流溅射在所述衬底上形成mo(钼)膜,使得平均膜厚度为约100nm。此后,在mo膜上涂覆光致抗蚀剂,将所获得物进行预烘烤、由曝光装置进行曝光、并进行显影,从而形成具有与待形成的源极94和漏极95相同的图案的抗蚀剂图案。此外,通过刻蚀去除了无抗蚀剂图案区的钼膜。此后,还移除抗蚀剂图案以形成源极94和漏极95,其中每个电极均由mo膜形成。-氧化物半导体层的形成-接着,形成氧化物半导体层96。具体地,通过直流溅射形成in-ga-zn基氧化物膜,使得平均膜厚为约100nm。此后,在in-ga-zn基氧化物膜上涂覆光致抗蚀剂,并且所获得物进行预烘烤、通过曝光装置进行曝光、并且进行显影,以形成具有与待形成的氧化物半导体层96相同图案的抗蚀剂图案。此外,通过刻蚀去除了无抗蚀剂图案区的铟镓锌基氧化物膜。此后,还移除抗蚀剂图案以形成氧化物半导体层96。其结果是,以在源极94和漏极95之间形成沟道的方式形成氧化物半导体层96。-栅极绝缘膜的形成-接着,在衬底91和栅极92上形成栅极绝缘膜93。具体地,通过直流溅射在其上形成sio2膜,使得其具有约120nm的平均膜厚度。此后,在其上涂覆光致抗蚀剂,将所获得物经受预烘烤、由曝光装置进行曝光、并且进行显影,从而形成具有与待形成的栅极绝缘膜93相同图案的抗蚀剂图案。此外,通过湿法刻蚀去除了无抗蚀剂图案区的sio2膜。此后,还移除抗蚀剂图案以形成由sio2膜形成的栅极绝缘膜93。-栅极的形成-接着,在栅极绝缘膜93上形成栅极92。具体地,通过直流溅射在栅极绝缘膜93上形成mo(mo)膜,使得平均膜厚度为约100nm。此后,在mo膜上涂覆光致抗蚀剂,对所获得物进行预烘烤、由曝光装置进行曝光、并且进行显影,从而形成具有与待形成的栅极92相同图案的抗蚀剂图案。此外,通过刻蚀去除了无抗蚀剂图案区的钼膜。此后,还移除抗蚀剂图案以形成由mo膜形成的栅极92。-钝化层的形成-接着,将0.6ml的氧化物形成涂覆液滴到衬底上并在预定条件下旋涂(以500rpm旋转5秒,然后以3000rpm旋转20秒,停止旋转以便在5秒内为0rpm)。随后,将所获得物在120后下在大气中干燥1小时,然后在400然下在o2气氛中烘烤3小时,从而形成氧化物膜。此后,在氧化物膜上涂覆光致抗蚀剂,并且将所获得物经受预烘烤、由曝光装置进行曝光、并且进行显影,从而形成具有与待形成的钝化层97相同图案的抗蚀剂图案。此外,通过湿法刻蚀去除了无抗蚀剂图案区的氧化物膜。此后,还移除抗蚀剂图案以形成钝化层97。钝化层的平均膜厚为约43nm。最后,作为后处理的热处理,将所获得物在大气中在300气下热处理1小时,从而完成场效应晶体管。<介电常数评估用电容器的生产>接着,生产如图5所示结构的电容器。具体地,使用在要形成下电极102的区域中具有开口的金属掩模,通过真空气相沉积方法在玻璃衬底(衬底101)上形成al(铝)膜,以使其具有约100nm的平均膜厚度。通过实施例4中的场效应晶体管的栅极绝缘膜的形成中所描述的方法,形成平均膜厚度为约35nm的绝缘体膜103。最后,使用在要形成上电极104的区域中具有开口的金属掩模,通过真空气相沉积方法形成al膜以使其具有约100nm的平均膜厚度,从而完成电容器。(实施例5)-氧化物形成涂覆液的制备-将0.52ml的四丁氧基硅烷(可从西格玛奥德里奇(sigma-aldrich)公司获得)、0.06ml的二(仲丁氧基)乙酰乙酸铝酯螯合物(产品编号89349,可从阿法埃莎(alfaaesar)公司获得)和0.53ml的2-乙基己酸钡(产品编号021-9471)在2.00ml的甲苯(cica一级,纯度99.0%,产品编号40180-01,可从关东化学株式会社获得)中混合,从而获得所述氧化物形成涂覆液。在1000级洁净室中制备实施例5中的氧化物形成涂覆液。接着,生产如图3c所示的顶部接触/顶栅型场效应晶体管。<场效应晶体管的生产>-氧化物半导体层的形成-首先,在玻璃衬底(衬底91)上形成氧化物半导体层96。具体地,通过直流溅射形成mg-in基氧化物(in2mgo4)膜,使得平均膜厚度为约100nm。此后,在mg-in基氧化物膜上涂覆光致抗蚀剂,对所获得物进行预烘烤、通过曝光装置进行曝光、并进行显影,以形成具有与要形成的氧化物半导体层96相同图案的抗蚀剂图案。此外,通过刻蚀去除了无抗蚀剂图案区的镁铟基氧化物膜。此后,还移除抗蚀剂图案以形成氧化物半导体层96。-源极和漏极的形成-接着,在衬底和氧化物半导体层上形成源极94和漏极95。具体地,通过直流溅射在衬底和氧化物半导体层上形成mo(mo)膜,从而使其具有约100nm的平均膜厚度。此后,在mo膜上涂覆光致抗蚀剂,并且对所获得物进行预烘烤、由曝光装置进行曝光、并且进行显影,从而形成具有与要形成的源极94和漏极95相同图案的抗蚀剂图案。此外,通过刻蚀去除了无抗蚀剂图案区的钼膜。此后,还移除抗蚀剂图案以形成源极94和漏极95,其中每个电极均由mo膜形成。-栅极绝缘膜的形成-接着,将0.25ml的氧化物形成涂覆液滴到衬底、氧化物半导体层、源极和漏极上,并且在预定条件下(以500rpm旋转5秒,然后以2000rpm旋转20秒,停止旋转以便在5秒内为0rpm)进行旋涂。随后,将所获得物在120旋下在大气中干燥1小时,然后在400然下在o2气氛中烘烤3小时,从而形成氧化物膜。此后,在氧化物膜上涂覆光致抗蚀剂,并且对所获得物进行预烘烤、通过曝光装置进行曝光、并且进行显影,从而形成与要形成的栅极绝缘膜93具有相同图案的抗蚀剂图案。此外,通过湿法刻蚀去除了无抗蚀剂图案区的氧化物膜。此后,还移除抗蚀剂图案以形成栅极绝缘膜93。栅极绝缘膜的平均膜厚为约43nm。-栅极的形成-接着,在栅极绝缘膜上形成栅极92。具体地,通过直流溅射在栅极绝缘膜上形成mo(mo)膜,使得平均膜厚度为约100nm。此后,在mo膜上涂覆光致抗蚀剂,并且对所获得物进行预烘烤、由曝光装置进行曝光、并且进行显影,从而形成具有与要形成的栅极电极92相同图案的抗蚀剂图案。此外,通过刻蚀去除了无抗蚀剂图案区的钼膜。此后,还移除抗蚀剂图案以形成由mo膜形成的栅极92。最后,作为后处理的热处理,将所获得物在大气中在300℃下进行热处理1小时,从而完成场效应晶体管。<介电常数评价用电容器的生产>接着,制造如图5所示结构的电容器。具体地,使用在要形成下电极102的区域中具有开口的金属掩模,通过真空气相沉积方法在玻璃衬底(衬底101)上形成al(铝)膜,以使其具有约100nm的平均膜厚度。通过实施例5中场效应晶体管的栅极绝缘膜的形成中所描述的方法,形成平均膜厚度为约20nm的绝缘体薄膜103。最后,使用在要形成上电极104的区域中具有开口的金属掩模,通过真空气相沉积方法形成al膜以使其具有约100nm的平均膜厚度,从而完成电容器。(实施例6)-氧化物形成涂覆液的制备-将0.50ml的甲醇(cica一级,纯度99.5%,产品编号25183-01,可从关东化学株式会社获得)、1.00ml的乙二醇单异丙基醚(无等级,纯度99.0%,产品编号40180-80,可从关东化学株式会社获得)、0.13ml的hmds(1,1,1,3,3,3-六甲基二硅氮烷,可从东京大阪工业株式会社获得)、0.02ml的硫酸铝(产品编号018-09745,可从华科纯化学工业有限公司获得)、0.01mg的硼酸(产品编号025-02193,可从华科纯化学工业有限公司获得)、0.01mg的氯化镁(136-03995,可从华科纯化学工业有限公司获得)和0.02mg的乳酸钡(产品编号021-00272)在0.75ml的纯水(可从一般实验室获得)中混合,由此获得氧化物形成涂覆液。在1000级洁净室中制备实施例6的氧化物形成涂覆液。接着,生产如图4c所示的顶部接触/顶栅型场效应晶体管。-氧化物半导体层的形成-首先,在玻璃沉底(沉底91)上形成氧化物半导体层96。具体地,通过直流溅射形成mg-in基氧化物(in2mgo4)膜,使得平均膜厚度为约100nm。此后,在mg-in基氧化物膜上涂覆光致抗蚀剂,对所获得物进行预烘烤、通过曝光装置进行曝光、并且进行显影,以形成具有与要形成的氧化物半导体层96相同图案的抗蚀剂图案。此外,通过刻蚀去除了无抗蚀剂图案区的镁铟基氧化物膜。此后,还移除抗蚀剂图案以形成氧化物半导体层96。-源极和漏极的形成-接着,在所述衬底和所述氧化物半导体层上形成源极94和漏极95。具体地,通过直流溅射在衬底和氧化物半导体层上形成mo(mo)膜,从而使其具有约100nm的平均膜厚度。此后,在mo膜上涂覆光致抗蚀剂,对所获得物进行预烘烤、通过曝光装置进行曝光、并且进行显影,从而形成具有与要形成的源极94和漏极95的图案相同的图案的抗蚀剂图案。此外,通过刻蚀去除了无抗蚀剂图案区的钼膜。此后,还移除抗蚀剂图案以形成源极94和漏极95,其中每个电极均由mo膜形成。-栅极绝缘膜的形成-接着,在所述沉底和所述栅极上形成栅极绝缘膜93。具体地,通过直流溅射在其上形成sio2膜,使得其具有约120nm的平均膜厚度。此后,在其上涂覆光致抗蚀剂,对所获得物经受预烘烤、通过曝光装置进行曝光、并且进行显影,从而形成具有与要形成的栅极绝缘膜93的图案相同的图案的抗蚀剂图案。此外,通过湿法刻蚀去除了无抗蚀剂图案区的sio2膜。此后,还移除抗蚀剂图案以形成由sio2膜形成的栅极绝缘膜93。-栅极的形成-接着,在栅极绝缘膜上形成栅极92。具体地,通过直流溅射在栅极绝缘膜上形成mo(mo)膜,使得平均膜厚度为约100nm。此后,在mo膜上涂覆光致抗蚀剂,对所获得物进行预烘烤、通过曝光装置进行曝光、并且进行显影,从而形成具有与要形成的栅极电极92的图案相同的图案的抗蚀剂图案。此外,通过刻蚀去除了无抗蚀剂图案区的钼膜。此后,还移除抗蚀剂图案以形成由mo膜形成的栅极电极92。-钝化层的形成-接着,将0.6ml的氧化物形成涂覆液滴到所述沉底上并在预定条件下进行旋涂(以500rpm旋转5秒,然后以3000rpm旋转20秒,停止旋转以便在5秒内为0rpm)。随后,将所获得物在120后下在大气中干燥1小时,然后在400然下在o2气氛中烘烤3小时,从而形成氧化物膜。此后,在氧化物膜上涂覆光致抗蚀剂,并且将所获得物经受预烘烤、通过曝光装置进行曝光、并且进行显影,从而形成具有与要形成的钝化层97的图案相同的图案的抗蚀剂图案。此外,通过湿法刻蚀去除了无抗蚀剂图案区的氧化物膜。此后,还移除抗蚀剂图案以形成钝化层97。钝化层的平均膜厚为约45nm。最后,作为后处理的热处理,将所获得产物在大气中在300在下进行热处理1小时,从而完成场效应晶体管。<介电常数评价用电容器的生产>接着,生产如图5所示结构的电容器。具体地,使用在要形成下电极102的区域中具有开口的金属掩模,通过真空气相沉积方法在玻璃沉底(沉底101)上形成al(铝)膜,以使其具有约100nm的平均膜厚度。通过实施例6的场效应晶体管的栅极绝缘膜的形成中所描述的方法,形成平均薄膜厚度为约31nm的绝缘体薄膜103。最后,使用在要形成上电极104的区域中具有开口的金属掩模,通过真空气相沉积方法形成al膜,以使其具有约100nm的平均膜厚度,从而完成电容器。(比较例1)-氧化物形成涂覆液的制备-将1.50ml的环己基苯(cica特级,纯度97.0%,产品编号07670-00,可从关东化学公司获得)、0.55ml的四丁氧基硅烷(产品编号t5702,可从西格玛奥德里奇(sigma-aldrich)公司获得)和0.28ml的2-乙基己酸镁(产品编号12-1260,可从strem公司获得)在1.50ml的甲苯(primepure级,纯度99.9%,产品编号40180-79,可从关东化学公司获得)中混合,以获得氧化物形成涂覆液。在通用实验室中进行了比较例1的氧化物形成涂覆液的制备。通用实验室是在0.028m3的体积具有0.5微米或以上的粒度的颗粒有6×105个的环境。<场效应晶体管的生产>接下来,以与实施例1相同的方式使用氧化物形成涂覆液,从而生产如图3a所示的底部接触/底栅型场效应晶体管。<介电常数评价用电容器的生产>接下来,以与实施例1相同的方式使用氧化物形成涂覆液,从而生产具有图5所示结构的电容器。(比较例2)-氧化物成型涂布液的制备-将0.17ml的hmds(1,1,1,3,3,3-六甲基二硅氮烷,可从东京应化工业有限公司获得)、0.01g的硝酸钙(产品编号032-00747,可从华科纯化学工业株式会社获得)和0.02g的乳酸钡(产品编号021-00272)在2.50ml的超纯水(产品编号95305-1l,可从西格玛奥德里奇(sigma-aldrich)公司获得)中混合,以获得氧化物形成涂覆液。比较例2的氧化物形成涂覆液的制备是通用实验室中进行的。通用实验室是在0.028m3的体积具有0.5微米或以上的粒度的颗粒有6×105个的环境。<场效应晶体管的生产>接下来,以与实施例2相同的方式使用氧化物形成涂覆液,从而生产如图4a所示的底部接触/底栅型场效应晶体管。<介电常数评价用电容器的生产>接下来,以与实施例2相同的方式使用氧化物形成涂覆液,从而生产具有图5所示结构的电容器。(比较例3)-氧化物形成涂覆液的制备-将0.51ml的四丁氧基硅烷(产品编号t5702,可从西格玛奥德里奇(sigmaaldrich)公司获得)、0.16ml的2-乙基己酸钙(产品编号36657,可从阿法埃莎(alfaaesar)公司获得)、0.83ml的2-乙基己酸锶(产品编号195-09561,可从华科纯化学工业公司(wakopurechemicalindustries,ltd)获得)和0.16ml的2-乙基己酸钡(产品编号021-09471,从华科纯化学工业有限公司)在1.00ml的环己基苯(cica特级,纯度97.0%,产品编号07560-00,从关东化学株式会社获得)中混合,由此获得氧化物形成涂覆液。比较例3的氧化物形成涂覆液的制备在1000级洁净室中进行的。将用作溶剂的环己基苯通过sus304管供给,以确认重金属(例如,cr、fe和ni)对氧化物形成涂覆液的影响。<场效应晶体管的生产>接下来,以与实施例3相同的方式使用氧化物形成涂覆液,从而生产如图3b所示的顶部接触/顶栅型场效应晶体管。<介电常数评估用电容器的生产>接下来,以与实施例3相同的方式使用氧化物形成涂覆液,从而生产如图5所示结构的电容器。(比较例4)-氧化物形成涂覆液的制备-将0.50ml的乙醇(电子工业级,纯度99.5%,可从关东化学株式会社获得)、0.09ml的hmds(1,1,1,3,3-六甲基二硅氮烷,可从东京应化工业有限公司获得)、0.02mg的硫酸铝(产品编号018-09745,可从华科纯化学工业株式会社获得)、0.01g的硼酸(产品编号025-02193,可从华科纯化学工业有限公司获得)、0.01g的硝酸钙(产品编号032-00747,可从华科纯化学工业有限公司获得)和0.01g的氯化锶(产品编号193-04185,可从华科纯化学工业有限公司获得)在1.60ml的超纯水(产品编号95305-1l,可从西格玛奥德里奇(sigma-aldrich)公司获得)中混合,从而获得氧化物形成涂覆液。比较例4的氧化物形成涂覆液的制备是在1000级洁净室中进行的。将作为溶剂的乙醇和超纯水通过sus304管给料,以确认重金属(例如,cr、fe和ni)对氧化物形成涂覆液的影响。<场效应晶体管的生产>接下来,以与实施例4相同的方式使用氧化物形成涂覆液,从而生产如图4b所示的顶部接触/顶栅型场效应晶体管。<介电常数评估用电容器的生产>接下来,以与示例4相同的方式使用氧化形成涂覆液,从而生产如图5所示结构的电容器。<氧化形成涂覆液的杂质浓度的评价>使用原子吸收光谱仪(产品编号za3300,可从日立高新技术集团(hitachihightechsciencecorporation)获得),评估实例1~6和比较例1~4所制备的氧化物形成涂覆液中的na和k的浓度。使用icp-oes装置(产品号6300-duo,可从赛默飞费舍尔科学公司(thermofisherscience)获得)评估实施例1~6和比较例1~4所制备的氧化物形成涂覆液中的cr、mo、mn、fe、co、ni和cu的浓度。其结果示于表1中。使用icp-oes装置(产品号6300-duo,可从赛默飞费舍尔科学公司获得)评估实施例1~6和比较例1~4所制备的氧化物形成涂覆液中的si元素的浓度(ca)和所述b元素的总浓度(cb)。其结果示于表2中。由表2可知,从实施例1~6和比较例3和4的每个氧化物形成涂覆液中检测到的na和k的总浓度为(ca+cb)/(1×102)mg/l或更低,作为根据si元素浓度(camg/l(毫克/升))和b元素的总浓度(cbmg/l)计算的值。同时,由比较例1和2的每个氧化物形成涂覆液中检测到的na和k的总浓度大于(ca+cb)/(1×102)mg/l。此外,由表2可知,从实施例1~6和比较例1~2的每个氧化物形成涂覆液中检测到的cr、mo、mn、fe、co、ni和cu的总浓度为(ca+cb)/(1×102)mg/l或更低。同时,比较例3和4的每个氧化物形成涂覆液中的cr、mo、mn、fe、co、ni和cu的总浓度大于(ca+cb)/(1×102)mg/l。由表2可知,从实施例1~4和比较例3~4的每个氧化物形成涂覆液中检测到的na和k总浓度为(ca+cb)/(1×104)mg/l或更低,作为根据si元素浓度(camg/l(毫克/升))和所述b元素总浓度(cbmg/l)计算的值。同时,从实施例5~6和比较例1~2的每个氧化物形成涂覆液中检测到的na和k的总浓度大于(ca+cb)/(1×104)mg/l。此外,由表2可知,从实施例1~4的每个氧化物形成涂覆液中检测到的cr、mo、mn、fe、co、ni和cu的总浓度为(ca+cb)/(1×104)mg/l或更低。同时,从实施例5~6和比较例1~4的每个氧化物形成涂覆液中检测到的cr、mo、mn、fe、co、ni和cu的总浓度大于(ca+cb)/(1×104)mg/l。<由氧化物形成涂覆液形成的氧化物膜的异物和刻蚀刻残留物的评价>关于在实施例1、3和5以及比较例1和3中生产的每个场效应晶体管,在形成栅极绝缘膜后,在显微镜(产品号dm8000m,可从莱卡公司(leica)获得)下评价由氧化物形成涂覆液形成的氧化物膜中的异物和由氧化物形成涂覆液形成的氧化物膜的蚀刻部分中的蚀刻残留物。关于在实施例2、4和6以及比较例2和4中生产的每个场效应晶体管,在钝化层形成之后,在上述显微镜下评价由氧化物形成涂覆液形成的氧化物膜中的异物和由氧化物形成涂覆液形成的氧化物膜的蚀刻部分中的蚀刻残留物。显微镜下观察条件为:对于一个样品,在明场观察模式下以50倍放大倍率观察10个部分;并且在暗场观察模式下以50倍放大倍率观察10个部分。对于实施例1~6和比较例1~4中的每个,生产了12个场效应晶体管(12个衬底)样品,并且在显微镜下观察。表3给出了通过在实施例1~6和比较例1~4的每个中所生产的12个场效应晶体管样品的氧化物膜中进行显微观察而确认的具有异物和蚀刻残留物的样品的数量。由表3可知,在由实施例1~6和比较实施例3~4的氧化物形成涂覆液形成的氧化物膜中,在明场观察模式下未观察到异物。同时,在比较例1~2的氧化物形成涂覆液形成的氧化物膜中,在明场观察模式下观察到异物。由表3可知,在由实施例1~6以及比较例1~2的氧化物形成涂覆液所形成的氧化物膜的蚀刻部分中,在明场观察模式下未发现蚀刻残留物。同时,在比较例3~4所形成的氧化物膜的蚀刻部分中,在明场观察模式下确认有蚀刻残留物。该蚀刻残留物意味着该膜等保留在非预期的部分中。即,观察到蚀刻残留物的样品可以说涉及图案化失效。<由氧化物形成涂覆液形成的氧化物膜的绝缘性能和介电常数的评估>使用lcr计(产品编号4284a,可从安捷伦公司(agilentco.)获得)对实施例1~6和比较例1~4中生产的电容器进行电容测量。表4给出了根据测量的电容值计算的介电常数ε和在1khz频率下的介质损耗tanδ。由表4可知,在实施例1~6中所生产的电容器在1khz下的介质损耗tan耗较小;即:0.02(2×.0-2)或更小,并且它们表现出优异的绝缘性能。同时,在比较例1~4中生产的电容器的介电损耗tanδ较大;即:0.02(2×10-2)或更大,并且它们表现出差的绝缘性能。<场效应晶体管的晶体管特性的评估>使用半导体器件参数分析器(b1500a,可从安捷伦公司获得)评估实施例1~6和比较例1~4中生产的场效应晶体管的晶体管特性。通过测量如下关系来评估晶体管特性:即,当在漏极95与源极94之间的电压(vds)为+1v时,在栅极92和源极94之间的电压(vgs)与在漏极95和源极94之间的电流(ids)之间的关系(vgs-ids);以及栅极92和源极94之间的电压(vgs)与在栅极92和源极94之间的电流(igs)之间的关系(vgs-igs)。此外,通过在-5v和+5v之间改变vgs来测量vgs-ids和vgs-igs。根据晶体管特性(vgs-ids)的评价结果,计算了饱和区内的场效应迁移率。评估了在vgs为-5v下的栅极电流(igs)值。计算晶体管的导通状态(vgs=+5v)与关闭状态(vgs=-5v)的ids比率(开/关比)。计算阈值摆幅(ss)作为在应用vgs时ids上升的锐度指标。此外,阈值电压(vth)被计算为在应用vgs时ids上升时的电压值。由表4可知,实施例1~6中生产的场效应晶体管具有3.0cm2/vs或更高的高迁移率、低于1.0×10-12a的低栅极电流、3.0比电流7或更高的高开关比、1.0或更低的低ss、以及在±±低范围内的vth,表现出良好的晶体管特性。同时,在比较实施例1和3中生产的场效应晶体管具有高于1.0×.0-10a的栅极电流,小于1.0比流体5的低开关比,因此没有表现出足够的晶体管特性。<场效应晶体管的晶体管可靠性评估>在大气(温度:23℃,相对湿度:50%)中对实施例2、4和6以及比较例2和4所生产的每个场效应晶体管进行100小时的偏置温度应力(bts)测试。应力条件如下:vgs=+5v,vds=+1v。每次bts测试进行一段时间,测量vds=+1v时vgs和ids之间的关系(vgs-ids)。根据该结果,计算了阈值电压(vth)。表4列出了相对于在对实施例2、4和6以及比较例2和4的每个场效应晶体管执行的bts测试中100小时的应力时间的δvth。此处“δvth”表示vth从0小时的应力时间到100小时的应力时间的变化值。从表4可以发现,实施例2、4和6中生产的场效应晶体管具有小的δ场th变化;即在100小时的应力时间下为3.0v或更低,并且在bts测试中表现出优异的可靠性。另一方面,已经发现在比较例2和4中生产的场效应晶体管具有大的δ定th变化;即:-20v或更高,并且在bts测试中表现出低的可靠性。[表1]nakcrmomnfeconicumg/lmg/lmg/lmg/lmg/lmg/lmg/lmg/lmg/l实施例10.8130.151<0.001<0.0010.3100.520<0.0010.010<0.001实施例20.3520.1880.0160.0130.0680.1000.0150.030<0.001实施例30.7300.221<0.0010.0310.1760.470<0.0010.130<0.001实施例40.080<0.003<0.001<0.0010.0380.020<0.0010.050<0.001实施例525.21011.0551.3561.1013.9983.2602.0151.5303.105实施例61.4003.0150.4800.1600.3550.9000.1350.1560.096比较例1300.500189.1000.3310.8811.2453.9500.5310.2220.510比较例2189.30050.4800.6420.5130.6810.9000.1530.1770.531比较例30.8400.02030.3204.18210.530234.7007.39020.5305.314比较例40.2000.005153.4003.69453.550428.5008.21683.61015.550[表2]ca+cb(ca+cb)/(1×102)(ca+cb)/(1×104)na+kcr+mo+mn+fe+co+ni+cumg/lmg/lmg/lmg/lmg/l实施例11.3×104130.81.31.00.8实施例21.8×104183.11.80.50.2实施例32.8×104264.92.61.00.8实施例41.6×104143.01.40.10.1实施例52.6×104194.21.936.316.4实施例61.5×104109.91.14.42.3比较例11.3×104130.81.3489.67.7比较例21.8×104183.11.8239.83.6比较例32.8×104264.92.60.9313.0比较例41.6×104143.01.40.2746.5[表3][表4]本发明的技术方案为例如如下。<1>一种用于形成氧化物的涂覆液,所述涂覆液包括:硅(si);和b元素,所述b元素为至少一种碱土金属,其中,当si元素的浓度由camg/l表示,并且所述b元素的总浓度由cbmg/l表示时,所述涂覆液中钠(na)和钾(k)的总浓度为(ca+cb)/(1×102)mg/l或更低,并且所述涂覆液中铬(cr)、钼(mo)、锰(mn)、铁(fe)、钴(co)、镍(ni)和铜(cu)的总浓度为(ca+cb)/(1×102)mg/l或更低。<2>根据<1>所述的用于形成氧化物的涂覆液,其中,当si元素的浓度由camg/l表示,并且所述b元素的总浓度由cbmg/l表示时,所述涂覆液中钠(na)和钾(k)的总浓度为(ca+cb)/(1×102)mg/l或更低,并且所述涂覆液中铬(cr)、钼(mo)、锰(mn)、铁(fe)、钴(co)、镍(ni)和铜(cu)的总浓度为(ca+cb)/(1×102)mg/l或更低。<3>根据<1>或<2>所述的用于形成氧化物的涂覆液,其中,所述涂覆液还包括c元素,所述c元素是选自铝(al)和硼(b)所组成的组中的至少一种元素。<4>根据<1>至<3>中任一项所述的用于形成氧化物的涂覆液,其中,所述涂覆液包括选自si或所述b元素的无机盐、si或所述b元素的氧化物、si或所述b元素的氢氧化物、si或所述b元素的卤化物、硅或所述b元素的金属络合物、以及硅或所述b元素的有机盐中的至少一种。<5>根据<4>所述的用于形成氧化物的涂覆液,其中,所述无机盐包括选自硝酸盐、硫酸盐、碳酸盐、乙酸盐和磷酸盐所组成的组中的至少一种。<6>根据<4>所述的用于形成氧化物的涂覆液,其中,所述卤化物包括选自氟化物、氯化物、溴化物和碘化物所组成的组中的至少一种。<7>根据<4>所述的用于形成氧化物的涂覆液,其中,所述有机盐包括选自羧酸盐、石碳酸盐、以及它们的衍生物所组成的组中的至少一种。<8>一种用于制备氧化物膜的方法,所述方法包括:涂覆并且热处理根据<1>至<7>中任一项所述的用于形成氧化物的涂覆液,以获得氧化物膜。<9>一种用于生产场效应晶体管的方法,所述方法包括:使用根据<1>至<7>中任一项所述的用于形成氧化物的涂覆液来形成氧化物膜,其中,所述场效应晶体管包括栅极绝缘膜,所述栅极绝缘膜包括所述氧化物膜。<10>一种用于生产场效应晶体管的方法,所述方法包括:使用根据<1>至<7>中任一项所述的用于形成氧化物的涂覆液来形成氧化物膜,其中,所述场效应晶体管包括:栅极;源极和漏极;半导体层;栅极绝缘层;以及钝化层,所述钝化层包括所述氧化物膜。上述<1>至<7>的氧化物形成涂覆液可以提供形成具有抑制其性能退化的氧化物膜的氧化物形成涂覆液。上述<8>所述的用于制备氧化物膜的方法可以提供具有抑制其性能退化的氧化物膜。上述<9>和<10>所述的用于生产场效应晶体管的方法可以提供使用具有抑制其特性退化的氧化物膜的场效应晶体管。[附图符号列表]21衬底22栅极23栅极绝缘膜24源极25漏极26半导体层91衬底92栅极93栅极绝缘膜94源极95漏极96半导体层101衬底102下电极103栅极绝缘膜104上电极当前第1页12