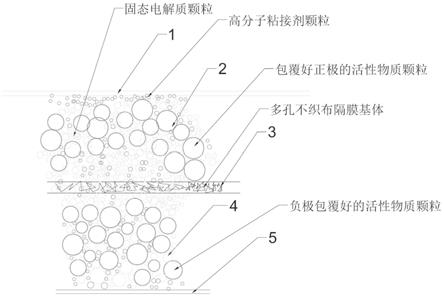
1.本发明涉及一种全固态锂离子电池制造工艺方法,属于新能源动力储能电池技术领域。
背景技术:2.动力锂离子电池作为一种储能装置在纯电动汽车中得到了推广应用。但是,动力电池的安全问题一直是行业的痛点,不能得到有效的解决,安全问题表现在汽车在充电过程、行驶中以及停放时自燃,其根本原因是目前动力电池还采用液态有机电解液,其闪点低,属极易燃烧物,同时,正极材料属于高氧化态,增强了了电池的燃烧程度。随着固态电解质材料的研发成功逐步应用到动力离子电池中,其应用原理与传统锂离子电池有了很大区别,因此,制造工艺完全区别于传统液态锂离子电池的制造工艺,尤其在极板制造方面。传统液态锂离子电池工序电极制造工艺包括合浆、涂布、滚压、分切等工序,其中,合浆工序是将颗粒活性物质、导电剂(炭黑、sp)、高分子粘接剂以及溶剂(nmp溶液或纯水)通过合浆机制成50%-70%左右的浆料供涂布使用;涂布工序是将浆料均匀涂敷在导电集流体上(铝箔或铜箔),经烘箱烘干,形成多孔电极;滚压工序是将涂覆好的电极压制成一定厚度,并调整极板孔率,以便电解液存在其中,形成离子通道、与活性物质交换锂离子。
3.而电子通道有导电剂与活性物质颗粒接触并在活性物质层形成导电(电子)网络,传递到集流体。
4.但上述现有技术,离子交换的效率很低,活性物质颗粒与外界传递电子通道存在问题;还影响锂离子的传输,烘干的能耗高。电池的安全性也较低。
技术实现要素:5.为了解决上述问题,本发明就是基于固态电解质取代传统液态电解液的基础上,采用全新的电极制造工艺及对应的制造设备。本发明提出了一种全固态锂离子电池制造工艺方法,全固态锂离子电池的全固态电池极片组由正极集流体、正极活性物质层、隔膜、负极活性物质层、负极集流体组成,所述正极活性物质层由正极活性物质颗粒、固态电解质、导电颗粒、高分子粘接剂组成,其中,大颗粒的正极活性物质颗粒已包覆小颗粒的固态电解质以及导电颗粒,并通过高分子粘接剂接触在一起。
6.在上述全固态锂离子电池制造工艺方法中,所述隔膜由不织布、固态电解质颗粒以及高分子粘接剂组成,其中高分子不织布形成骨架起到提供共强度支撑作用,通过碾压在一起。所述负极活性物质层由负极活性物质颗粒、固态电解质、导电颗粒、高分子粘接剂组成,其中大颗粒的负极活性物质颗粒已包覆小颗粒的固态电解质以及导电颗粒,并通过高分子粘接剂接触在一起。
7.另外,所述正极集流体可以是铝箔、铝拉网、穿孔铝箔,所述负极集流体可以是铜箔、铜切拉网、穿孔铜箔,然后将正极集流体与正极活性物层制成的正极片、隔膜、负极集流体与负极活性物质层制成的负极片,通过高温热压成一体。采用橡胶工业中捏合、混炼的工
艺及其设备。所述负极集流体为金属铜薄板,激光或光刻或者其他成孔工艺,在所述金属铜薄板上制备成微孔,将金属锂沉积在微孔的侧壁上形成锂金属层。
8.在上述全固态锂离子电池制造工艺方法中,所述金属铜薄板的厚度为50-300微米,所述微孔的孔率在10%-50%之间,所述锂金属层的厚度为10-150微米,然后将混炼后的固态电解质胶热压在复合电极的表面以及微孔中与锂金属层紧密接触,最后再将正极板也热合在在负极板上形成极组,这样固态电解质在正负间形成了离子通道。所述负极板还可以在微孔中留存液态电解液与固态电解质形成半固态电池。
9.此外,所述固态电解质为氧化物、硫化物,所述导电颗粒为super-p、乙炔黑、ks-6、vgcf、cnt分别使用或其混合使用,所述高分子粘接剂为pvdf或sbr或ptfe。所述正极活性物质颗粒为三元材料ncm、nca高能正极材料,其大小为微米级,d50在5—20微米,其表面已包覆小颗粒的直径30-200纳米的炭黑和小颗粒的30-200纳米的固态电解质颗粒,150-200纳米的碳黑或者碳纳米管纤维。
10.本发明具有如下的技术效果和优点:
11.1、活性物质颗粒表面混合包覆固态电解质与导电颗粒,不仅提高了锂离子活性物质颗粒与固态电解质固固界面的离子交换的效率,同时,又解决了活性物质颗粒与外界传递电子通道的问题;
12.2、采用橡胶工业中捏合、混炼的工艺及其设备,可以免溶剂化制备活性物质层,一方面减少了溶剂的使用成本以及带来的环境问题,而且,避免了因使用溶剂烘干,造成活性物质的多孔化,而活性物质层多孔造成固气两相界面,影响锂离子的传输。还减低了烘干的能耗。
13.3、金属锂负极板结构改变了传统锂金属负极平板结构,采用在薄铜板上打微孔、将锂沉积到孔壁上,改变了充放电过程中锂枝晶的生长方向,提高了电池的安全性。
附图说明
14.图1为本发明的全固态电池极片组的组成示意图。
15.图2为本发明的金属铜薄板与金属锂层紧密接触的示意图。
16.图3为本发明的活性物质颗粒包覆示意图。
具体实施方式
17.下面结合附图详细说明本发明的具体实施方式。以下实施例用于说明本发明,但不用来限制本发明的范围。
18.如图1所示,全固态电池极片组由正极集流体1、正极活性物质层2、隔膜3、负极活性物质层4、负极集流体5组成;其中正极集流体1可以是铝箔、铝拉网、穿孔铝箔等,正极活性物质层2由正极活性物质颗粒、固态电解质(氧化物、硫化物)颗粒、导电颗粒(super-p、乙炔黑、ks-6、vgcf、cnt等分别使用或其混合使用)、高分子粘接剂(pvdf或sbr或ptfe等)组成,其中大颗粒的正极活性物质颗粒已包覆小颗粒的固态电解质以及导电颗粒,并通过高分子粘接剂紧密接触在一起,尽量消除空隙。隔膜3由不织布、固态电解质颗粒以及高分子粘接剂组成,其中高分子不织布形成骨架起到提供共强度支撑作用,通过碾压在一起;负极活性物质层4由负极活性物质颗粒、固态电解质(氧化物、硫化物)颗粒、导电颗粒(super-p、
乙炔黑、ks-6、vgcf、cnt等分别使用或其混合使用)、高分子粘接剂(pvdf或sbr或ptfe等)组成,其中大颗粒的负极活性物质颗粒已包覆小颗粒的固态电解质以及导电颗粒,并通过高分子粘接剂紧密接触在一起,尽量消除空隙,负极集流体5可以是铜箔、铜切拉网、穿孔铜箔。然后将正极集流体1与正极活性物层2制成的正极片、隔膜3、负极集流体5与负极活性物质层4制成的负极片,通过高温热压成一体如图1所示。
19.如图2所示,金属铜薄板5其厚度50-300微米,激光或光刻或者其他成孔工艺,在铜薄板上制备成微孔6,其孔率在10%-50%之间,将金属锂沉积在微孔6的侧壁上形成厚度为10-150微米的锂金属层4,然后将混炼后的固态电解质胶热压在上述复合电极的表面以及微孔6中与金属锂层4紧密接触,最后再将上述正极板也热合在在负极板上形成极组,这样固态电解质在正负间形成了离子通道。另外,本负极板还可以在孔中留存液态电解液与固态电解质形成半固态电池。
20.活性物质颗粒包覆
21.如图3所示,包覆的正极或负极活性物质颗粒,由正极或者负极活性物质颗粒(大颗粒)微米级尺度,固态电解质颗粒,纳米尺度,经过包覆技术,使得小粒径的固态电解质颗粒与导电剂颗粒紧密包裹在大粒径的活性物质颗粒上,提高了锂离子、电子扩散进或出活性物质体相的效率,相当于形成了两个有效的对外物质交换的窗口。如图3所示,在充放电过程中,活性物质体相中的锂离子通过包覆层中固态电解质传递给活性物质层中的固态电解质从而到达对电极的活性物质颗粒的体相中完成,锂离子的传递;而活性物质颗粒体相传递出一个锂离子,必然要得到一个电子,而电子从集流体、活性物质层中的导电剂颗粒、传递到包覆在活性物质颗粒表面的导电颗粒,在传递到活性物质颗粒的体相中,完成电荷的平衡。
22.实施例1
23.如图1所示,正极活性物质层包括正极活性物质(三元材料ncm、nca等高能正极材料)颗粒,其大小为微米级,d50在5—20微米,其表面已包覆小颗粒的炭黑(直径30-200纳米)和小颗粒的固态电解质颗粒(30-200纳米),碳黑150-200纳米或者碳纳米管纤维等,pvdf、固态电解质颗粒其粒径d50在2-9微米。
24.先将pvdf在捏合设备中加热融化,温度控制范围100-250摄氏度(℃),然后加进小颗粒的炭黑、固态电解质、活性物质进行捏合,其活性物质配比占70%-98%,pvdf占1.5%-15%、导电剂1%-2%、固态电解质颗粒2%-10%;然后,在混炼机中进行混炼,形成均匀的塑性胶态,在高温辊轧机上,碾压成条片状其过程中冷却到常温,并辅助于pet膜收卷。
25.然后,成卷的铝箔,与上述制成的卷装的活性物质层经过热辊,热压复合在一起,制成正极片卷料,以备装配成电池使用。
26.负极活性物质层由负极活性物质(人造石墨、硅碳负极材料等高能负极材料)颗粒,其大小为微米级,d50在5—30微米,其表面已包覆小颗粒的炭黑(直径30-200纳米)和小颗粒的固态电解质颗粒(30-200纳米),碳黑150-200纳米或者碳纳米管纤维等,pvdf或sbr、固态电解质颗粒其粒径d50在2-9微米。
27.先将pvdf或sbr在捏合设备中加热融化,温度控制范围100-250
°
c,然后加进小颗粒的炭黑、固态电解质、活性物质进行捏合,其活性物质配比占70%-98%,pvdf或sbr占1.5%-15%、导电剂1%-2%、固态电解质颗粒2%-10%;然后,在混炼机中进行混炼,形成
均匀的塑性胶态,在高温辊轧机上,碾压成条片状其过程中冷却到常温,并辅助于pet膜收卷。
28.然后,成卷的铜箔,与上述制成的卷装的活性物质层经过热辊,热压复合在一起,制成负极片卷料,以备装配成电池使用。
29.隔膜制备:固体电解质颗粒、高分子粘接剂混练,碾压成薄片状与隔膜基体(聚乙烯、聚丙烯、pvdf不织布)复合,辊压成所需厚度;
30.将上述正极片、隔膜、负极片,热压成三明治装,将三个材料中的固态电解质热合在一起,制成极组。然后根据需求制成不同大小的电池
31.实施例2
32.正极活性物质层包括正极活性物质(三元材料ncm、nca等高能正极材料)颗粒,其大小为微米级,d50在5—20微米,其表面已包覆小颗粒的炭黑(直径30-200纳米)和小颗粒的固态电解质颗粒(30-200纳米),碳黑150-200纳米或者碳纳米管纤维等,pvdf、固态电解质颗粒其粒径d50在2-9微米。
33.先将pvdf在捏合设备中加热融化,温度控制范围100-250℃,然后加进小颗粒的炭黑、固态电解质、活性物质进行捏合,其活性物质配比占70%-98%,pvdf占1.5%-15%、导电剂1%-2%、固态电解质颗粒2%-10%;然后,在混炼机中进行混炼,形成均匀的塑性胶态,在高温辊轧机上,碾压成条片状其过程中冷却到常温,并辅助于pet膜收卷。
34.然后,成卷的铝箔,与上述制成的卷装的活性物质层经过热辊,热压复合在一起,制成正极片卷料,以备装配成电池使用。
35.金属锂复合负极制备
36.使用厚度150微米的铜板,在其上加工微孔,其直径为20微米,其孔率为21%,然后经金属锂沉积在微孔壁内,其厚度50微米,然后,将上述实施例制备的隔膜,热合到复合负极板上,并使固态电解质颗粒热压进微孔中,最后,将上述正极片热合到负极板。制成电池极组。
37.以上所述,仅为本发明的具体实施方式,但本发明的保护范围并不局限于此,任何熟悉本技术领域的技术人员在本发明揭露的技术范围内,可轻易想到变化或替换,都应涵盖在本发明的保护范围之内。