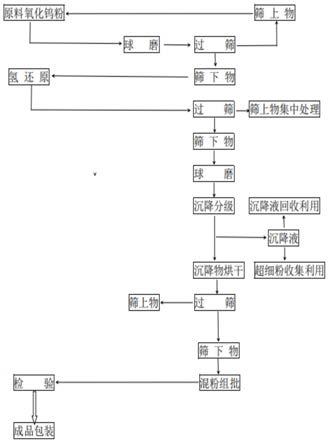
1.本发明涉及餐具技术领域,具体的说,是一种生产高温导体浆料用钨粉的方法。
背景技术:2.钨粉主要用于作碳化钨粉的原料或用于钨(烧结)制品以及加工产品的原料,生产厂商很多、产量很大,市场供应充足。但一些特殊用途的钨粉,因用量极少,市场产品又无法满足其特殊要求,而某些尖端技术领域又离不开它。例如,在高集成度的三维混合集成电路的mcm-c(陶瓷基板多芯片组装)技术中,高温导体(导电、导热)浆料用钨粉。
3.mcm-c是用丝网印刷技术,将高温导体钨浆料印制在陶瓷(如氮化铝、氧化铝等)生料带上形成各种电路图案,层间利用激光在生料带上打出的微孔并注入导体浆料形成电连通,将印有钨导体线路图案的生陶瓷片多层叠合,在高温(1600℃~2000℃)保护性气氛中共烧,形成多层布线htcc(高温共烧陶瓷)的三维电路基板,在其表面可以贴装ic和有源器件,制成无源/有源集成的功能模块,使电路小型化与高密度化,以适应航天、卫星通信、高机动雷达等高科技领域,对高端电子设备的整机小型化、轻量化,大功率、低功耗,多功能、高速、高可靠性的需求。氮化铝htcc高温共烧陶瓷多层布线基板,就是mcm-c(陶瓷基板多芯片组装)技术中、特别适合用于制作高频、大功率组件的应用之一。
4.用于htcc金属化的导体浆料,由钨粉、无机粘结相和有机载体混合而成,钨粉作为浆料主要功能相,含量占导电浆料的60~90%,以下将这种浆料简称“钨浆料”。该浆料中的钨粉纯度、粒度及粒度分布、形貌等,对电路印刷精度、烧结性能、导电膜的电性能有着至关重要的影响。
5.用于高温导体浆料的钨粉,要求纯度大于99.95%,粉末费氏粒度在1.0μm左右(0.5~1.5μm),粉末粒度分布曲线呈近似正态分布(以中位径为对称轴,小于和大于中位径的钨粉颗粒占比左右基本对称,粒度分布范围窄(粒径跨度span≤1.5),粒度波动范围为标称值
±
0.1μm(例如fsss:0.7
±
0.1μm、0.9
±
0.1μm等)。
6.工业化生产的市售钨粉,是以仲钨酸铵为原料,制成氧化钨(黄钨、蓝钨或紫钨)粉,然后将氧化钨粉在氢气中于一定温度下还原成钨粉。可以通过调整原料技术指标和还原工艺参数,制备各种用途的钨粉。例如用作碳化钨产品、钨(烧结)制品和钨深加工产品的生产原料。工业化批量生产钨粉的生产企业,设备都是长期每天24小时连续运行,单台设备日产量以吨计,年产量在数百吨至数千吨,这种规模化批量生产形式,虽能有效降低生产成本和稳定控制产品质量,但要在这种钨粉生产线上,专门生产年用量只有几公斤至十几公斤的钨浆料专用钨粉,其生产成本和生产周期是任何一家钨浆料生产商都无法承受的。
7.虽然也有用高能球磨法、溶胶凝胶法、冷冻干燥法、熔盐电解法、自蔓延高温还原法以及喷雾干燥-流化床法等方法制备细钨粉的技术研究,但这些技术要用于制备浆料用细钨粉,还是显得技术成熟度不够。即便这些技术中有些相对成熟,但要用这些技术专门建一条钨浆料用钨粉生产线并维持其运行,在经济上也是不现实的。
8.钨浆料生产商没有选择的余地,只能在有一定规模的钨粉生产企业中,随机购买
普通钨粉来制备钨浆料。随机购买的钨粉,非用户定制,其技术指标难以令用户满意,用户只能根据所购普通钨粉的技术指标,被动地调整钨浆料的制备工艺和后续高温共烧工艺来适应,这将导致钨浆料性能及后续高温共烧工艺的波动。这些不稳定因素,对可靠性要求极高的航天等高科技产品来说是难以接受的。
技术实现要素:9.本发明的目的在于提供一种生产高温导体浆料用钨粉的方法,以适应对钨粉有特殊技术要求、质量稳定性要求很高、用量极少但又不可或缺的特殊应用场景,满足高端技术所依赖的钨浆料对钨粉的需求。
10.本发明通过下述技术方案实现:
11.一种生产高温导体浆料用钨粉的方法,基于钨粉生产线,具体包括以下步骤:
12.步骤s1:制备原料氧化钨粉;将氧化钨粉球磨、过筛得到粒度fsss:0.5~5μm的原料氧化钨粉;
13.步骤s2:原料氧化钨粉在还原炉内还原为原始钨粉;还原工艺:舟皿料层厚度为1~6mm,炉管内的氢气流速为0.2~1.2m/s;
14.之所以控制炉管内的氢气流速而非流量,是因为不同型号的还原炉,炉管内径不同,炉管内截面面积也就不同,对于同样的氢气流量,管径小的炉管氢气流速大,管径大的炉管氢气流速小,而在相同的温度下,影响还原效果的重要因素之一,是氢气带走还原舟内还原所产生的水蒸汽的速度和补充新氢气的速度,因此用氢气流速比用氢气流量更能适应不同型号的还原炉。
15.步骤s3:原始钨粉过200目筛网,对筛下物进行团聚分散处理;
16.由于在研磨过程中将产生大量的大量超细钨粉,不利于钨浆料的质量控制;用大小颗粒的粉末在液体中沉降速度不同,将超细钨粉分离。步骤s4:将分散处理后的钨粉沉降分级,去除超细粉;
17.步骤s5:将沉降分级的钨粉烘干、过300目筛网,获得的筛下物即为高温导体浆料用钨粉。
18.上述步骤s4具体步骤如下:
19.步骤s41:将钨粉倒入装有沉降液的容器内,搅拌2~3分钟;
20.步骤s42:静置沉淀3~5分钟,将悬浮在沉降液中的超细粉随上清液倾出;
21.步骤s43:向容器中重新加入沉降液并依次搅拌、沉淀、倾出悬浮在液相中的超细粉;
22.步骤s44:重复步骤s43 1-3次。
23.进一步地,为了更好的实现本发明,所述步骤s2中,还原炉内最高温度为850℃~900℃,原料氧化钨粉在热区停留时间4~6小时,氢气露点-30℃~-50℃。
24.该设置与现有钨粉生产线中的参数设置一致,保证了在进行本发明中的钨粉制备时,也不影响其他钨粉的制备,进而使得不需要建造一条生产线来满足高温导体浆料用钨粉的制备,有效的降低了成本。
25.进一步地,为了更好的实现本发明,避免在对团聚粉分散时,钨粉中杂质含量的上升,从而影响产品的质量,将筛下物置于行星球磨机中球磨;球磨工艺:球磨前,用惰性气体
将罐内空气排出;转盘公转转速175~250转/分钟;磨罐自转350~500转/分,磨罐正转20分钟,停转15分钟,然后反转20分钟,上述正转、停转、反转步骤反复循环2~3次。
26.采用行星球磨机对过200目筛网的钨粉中的团聚粉进行分散,对于球磨罐内壁作衬钨处理,磨球采用钨材料制成,该设置将有效的降低球磨过程中,带入其他杂质,从而影响产品的质量;这里的球磨罐内壁作衬钨处理是指:为保证钨粉纯度,本发明采用等离子喷涂的方法,在不锈钢罐内壁(含盖子内表面)喷涂一层金属钨涂层,将钨粉与球磨罐内壁材质隔离,磨球用钨球或短钨杆,避免钨粉与球磨罐材质直接接触。也可用薄钨片贴合在球磨罐内壁作内衬。
27.球磨时,钨粉与磨球的体积总和不超过球磨罐有效容积的60%,球磨罐封盖之前,用氮气将罐内空气排出;
28.调节变频器频率,将转盘公转转速控制在175~250转/分钟,磨罐自转350~500转/分;其中正转20分钟,停转15分钟,然后反转20分钟;如此反复循环,直到团聚的钨粉全部分散。
29.所述步骤s41中的沉降液为酒精;酒精易于挥发去除,不会残留在钨粉中。
30.所述步骤s1具体包括以下步骤:取粒度fsss:10μm~20μm的氧化钨粉,装入玛瑙罐,每个玛瑙罐中装入2~4kg氧化钨粉,并在玛瑙罐中放入玛瑙球;
31.步骤s12:用惰性气体将玛瑙罐中的空气排出后盖上盖子密封;
32.步骤s13:在行星球磨机上一次对称装两罐或四罐进行球磨;
33.步骤s14:过筛,得到氧化钨粉粒度fsss:0.5~5μm,并将其作为原料氧化钨粉。
34.进一步的,所述步骤s1中原料氧化钨粉的粒度fsss:0.5~2.5μm。
35.进一步的,所述步骤s1中原料氧化钨粉的粒度fsss:2.5~5μm。
36.本发明与现有技术相比,具有以下优点及有益效果:
37.本发明能够有效的实现对于特殊技术要求、质量稳定性要求很高、用量极少但又不可或缺的特殊应用场景,满足高端技术所依赖的钨浆料对钨粉的需求;
38.本发明通过沉降分级有效的将超细钨粉进行分离;
39.本发明通过在现有钨粉生产线上在制备正常钨粉的情况下,制备高温导体浆料用钨粉,不需要增添专用生产设备,从而有效的降低生产加工的成本。
附图说明
40.图1为本发明的工作流程图;
41.图2为本发明制备的钨粉的激光粒度分布曲线的示意图;
42.图3为未经本发明处理的钨粉呈偏左的非不对称分布分布曲线示意图的;
43.图4为未经本发明处理的钨粉呈偏右的非不对称分布的分布曲线示意图;
44.图5为球磨过度且未经处理钨粉在细粉端呈双峰分布的分布曲线示意图;
45.图6为未经本发明处理钨粉在细粉端呈双峰分布的分布曲线示意图。
具体实施方式
46.下面结合实施例对本发明作进一步地详细说明,但本发明的实施方式不限于此。
47.实施例1:
48.本发明通过下述技术方案实现,图1所示,一种生产高温导体浆料用钨粉的方法,基于钨粉生产线,当采用粒度fsss:1μm~2μm的普通钨粉制备高温导体浆料时具体包括以下步骤:
49.步骤s1:制备原料氧化钨粉;具体是指:
50.采用行星球磨机磨成粒度fsss:2.5μm~5μm的蓝钨粉作为原料氧化钨粉;
51.取粒度fsss.:10μm~20μm的正常生产钨粉所用的蓝钨粉,装入玛瑙罐,每个玛瑙罐中装入2~4kg蓝钨粉,并在罐中放入玛瑙球,用惰性气体将罐中的空气排出后盖上盖子密封,在行星球磨机上一次对称装两罐或四罐进行球磨,球磨后过筛,得到蓝钨粉粒度fsss:2.5~5μm,将其作为制备浆料用钨粉的原料氧化钨粉。
52.步骤s2:在钨粉生产线中取一根炉管,向还原舟中装入原料氧化钨粉,其中舟皿料层厚度为3~5mm,在第一舟内放入钨块标记,跟随其他正常装料的还原舟推入该炉管;控制该炉管内的氢气流速为0.3~0.5m/s;在还原炉中随其它炉管按正常的钨还原工艺将原料氧化钨粉还原为原始钨粉;
53.将该炉管改变氢气流量、改变蓝钨粉性状及装舟量后还原的钨粉单独收集在一个容器中,作为制备浆料钨粉的原始钨粉;而该炉管在改变氢气流量期间,用正常蓝钨粉按正常装舟量还原出的钨粉与该还原炉正常生产的钨粉收集在一起,在生产线上正常流转。
54.这里其它炉管按正常的钨还原工艺即:温度梯度设置不变、炉内最高温度850℃~900℃,原料氧化钨粉在热区停留时间4~6小时,氢气露点-30℃~-50℃。这样有效的保证了其他钨粉产品的生产,同时也能满足本发明中高温导体浆料用钨粉。
55.由于还原过程中与钨粉接触的还原舟内壁难免会有富含舟皿材质的脱皮混入钨粉中成为有害杂质,且细粉通常会有聚团现象,粉越细聚团现象越严重。为达到浆料用钨粉的成分及粒度分布要求,需在保证钨粉纯度的前提下,去除原始钨粉的粗颗粒和超细粉,并将团聚的钨粉强行分散,使钨粉的纯度、粒度和粒度分布达到用户要求。对此处理方法如下:
56.步骤s3:对原始钨粉过筛,获得过200目筛网的钨粉,对于筛上物将集中处理,用于其他钨粉的生产,并对过200目筛网的钨粉中的团聚粉分散。
57.对于过200目筛网的钨粉中的团聚粉分散,优选的,采用行星球磨机进行,在处理之前对球磨罐内壁作衬钨处理,磨球材质换成钨,以避免球磨过程带入其它杂质;
58.在球磨时,每罐装入钨粉2000克,钨粉与磨球的体积总和不超过球磨罐有效容积的60%,球磨罐封盖之前,用氮气将罐内空气排出;每次球磨时在球磨机上装2个桶或4个桶,呈对称分布以保持设备运行的动平衡。
59.调节变频器频率,将转盘公转转速控制在175~250转/分钟,磨罐自转350~500转/分。控制正转20分钟,停转15分钟,然后反转20分钟。如此反复循环2~3次,直到团聚粉全部被分散。
60.由于在对过200目筛网的钨粉研磨过程不可避免会生大量超细钨粉,超细钨粉不利于钨浆料的质量控制。对此利用大小颗粒的粉末在液体中沉降速度不同,将超细钨粉分离。钨颗粒在沉降液中,粒径大的优先沉降到容器底部,超细粉悬浮在沉降液中,将沉降液倾出,重新向容器中加入沉降液进行沉降分离,如此反复操作几次,直至钨粉的粒度分布曲线呈正态分布,且粒径跨度span≤1.5。具体操作如下:
61.步骤s41:将2~3kg过200目筛网的钨粉边搅拌边倒入装有酒精的容器内,其中过200目筛网的钨粉在容器中的高度为溶液高度的1/3~1/5,过200目筛网的钨粉倒入完毕后搅拌2~3分钟;
62.步骤s42:待液面平静后,再静置沉降3~5分钟,将悬浮在液相中的超细粉随上清液倾出并回收处理;
63.步骤s43:向容器中重新加入酒精并搅拌、沉淀、倾出悬浮在液相中的超细粉;反复操作,循环2~3次,直至超细粉全部倾出;获得制备高温导体浆料用的钨粉。优选的,采用酒精作为沉降液;
64.步骤s5:对步骤s4中的钨粉烘干、过筛,获得过300目筛网的钨粉,对于筛下物合入该还原炉正常生产的钨粉使用;获得过300目筛网的钨粉即为生产高温导体浆料用钨粉,且粒度fsss:1μm~2μm;完成制备。
65.经对过300目筛网的钨粉进行分析检测,制成钨含量≥99.96%、粒度波动范围为
±
0.1μm、粒度呈正态分布且粒径跨度span≤1.5的浆料用钨粉。
66.步骤s6:对获得的过300目筛网的钨粉混粉组批、检测、包装。
67.混粉组批:将所有用同一批原料、用同一生产设备和同样的生产工艺、在同一个生产周期内生产并用同样的方法处理过的过300目筛网的钨粉混合在一起,组成一个生产批号。
68.检测、包装:经检测达到要求的钨粉,成为制备钨浆料的专用钨粉,并按用户要求进行产品包装
69.本实施例的其他部分与上述实施例相同,故不再赘述。
70.实施例2:
71.一种生产高温导体浆料用钨粉的方法,基于钨粉生产线,图1所示,当采用粒度fsss:0.5μm~1.0μm的超细钨粉制备高温导体浆料时,具体包括以下步骤:
72.步骤s1:制备原料氧化钨粉;具体是指:
73.采用将氧化钨粉用行星球磨机球磨、过筛得到粒度fsss:0.5μm~2.5μm的原料氧化钨粉;
74.步骤s2:在钨粉生产线中取一根炉管,正式开始投料生产超细钨粉前,在该炉管中先推入空舟,其中还原舟中不装料,以避免此前已装入该炉管的正常原料还原时产生的水蒸气使跟在其后的超细钨粉的原始粒度过度长大;待炉子的出料端见到空舟时,向还原舟中装入原料氧化钨粉,其中舟皿料层厚度为1~3mm,在第一舟皿内放入钨块标记,跟随其他正常装料的还原舟推入该炉管;控制该炉管内的氢气流速为0.5~1.0m/s;随该还原炉按正常的钨还原工艺。重复装料、推舟操作,并在最后一舟内放入钨块作标记。最后一舟料进炉后,该炉管后续装舟量及蓝钨粉都恢复原状。待装有钨标记的最后一舟料出炉后,将该炉管的氢气流量恢复到与其它炉管一致,整台炉子恢复正常生产。
75.将该炉管从推空舟开始,到恢复氢气流量期间生产的钨粉分类存放。将用球磨蓝钨粉还原的原始钨粉单独收集在一个容器中,作为浆料用钨粉的原始钨粉。其它钨粉收集在另一个容器内与正常钨粉一起流转。
76.过筛、球磨、沉降分离、烘干及分析检测等方法和参数,与实施例1浆料用普通钨粉的方法及参数基本一致,不再赘述。
77.这里其它炉管按正常的钨还原工艺即:温度梯度设置不变、炉内最高温度850℃~900℃,原料氧化钨粉在热区停留时间4~6小时,氢气露点-30℃~-50℃。这样有效的保证了其他钨粉产品的生产,同时也能满足本发明中高温导体浆料用钨粉。
78.其他步骤与实施例1中的步骤s2-步骤s5相同;此方法能够有效制备制备钨含量≥99.95%,粒度fsss:0.5~1.0μm,粒度在标称值的
±
0.1μm范围内波动,如:0.6μm的钨粉,其粒度范围为0.5~0.7μm.,粒度呈正态分布且粒径跨度span≤1.5的浆料用超细钨粉。
79.本实施例的其他部分与上述实施例相同,故不再赘述。
80.实施例3:
81.将上述实施例1和实施例2所制备的钨粉、正常制备的钨粉以及球磨过度的钨粉分别做激光粒度实验得到图2-图6所示的结果,其中图2为实施例1和实施例2所制备的高温导体浆料用钨粉的激光粒度分布曲线的示意图;图3和图4为未采用本发明处理的正常钨粉激光粒度分布曲线的示意图,图3为未经处理的正常钨粉,呈偏左的非不对称分布曲线示意图;图4为未经处理的正常钨粉,呈偏右的非不对称分布的分布曲线示意图;图5为球磨过度且未经处理钨粉在细粉端呈双峰分布的分布曲线示意图;图6为未经处理钨粉在细粉端呈双峰分布的分布曲线示意图;由此可知,采用本发明所制备的钨粉,纯度大于99.95%,粉末费氏粒度在1.0μm左右,粉末粒度分布曲线呈近似正态分布,粒度波动范围为标称值
±
0.1μm;符合生产高温导体浆料的钨粉的要求。
82.以上所述,仅是本发明的较佳实施例,并非对本发明做任何形式上的限制,凡是依据本发明的技术实质对以上实施例所作的任何简单修改、等同变化,均落入本发明的保护范围之内。