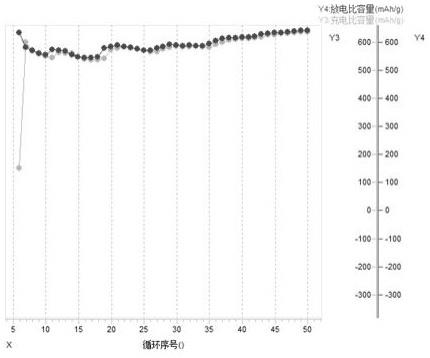
[0001]
本发明涉及锂电池负极领域,公开了一种磁性包覆球磨生产锂电池硅碳负极活性材料的方法。
背景技术:[0002]
近年来新能源发电领域的快速发展对与之匹配的储能系统提出了新的要求。而在储能电池的更新换代中,锂离子电池由于其自身所具备的各种优点,已成为重点研究领域,并在大量的储能项目中获得了实际应用,取得了一定的成效。锂离子电池的容量决定于正极材料的活性锂离子以及负极材料的可嵌脱锂能力,正负极在各种环境下的稳定性决定了电池的性能发挥,甚至严重影响电池的安全性,因此,电极的性能在一定程度上决定了锂离子电池的综合性能。
[0003]
锂离子电池作为现有新能源汽车的主要动力来源之一,经过几十年来的发展,已经逐渐实现商业化,但续航里程和充电时间仍然是电动汽车的短板。为了提高续航里程,电池的正极材料由磷酸铁锂过渡到ncm三元体系,然而传统的石墨负极容量已经难以匹配高容量的正极材料,因此硅碳负极应运而生。硅碳负极材料因其低嵌锂电位、低原子质量、高能量密度和在li-si合金中的高li摩尔分数,被认为是碳负极材料的替代性产品。
[0004]
硅基负极材料虽然具有优异的性能和良好的而应用前景,但循环性能和稳定性方面尚有欠缺,主要是因为实际应用的脱/嵌锂过程中,存在着较大的体积膨胀效应,这种结构上的膨胀收缩变化破坏了电极结构的稳定性,导致硅颗粒破裂粉化,造成电极材料结构的坍塌和剥落,使电极材料失去电接触,最终导致负极的比容量迅速衰减,使锂电池循环性能变差。现有技术中,可以利用碳包覆等改性技术解决上述问题,商业化的硅碳负极容量普遍在400~450mah/g,循环次数为200~500次,基本可以达到现有负极性能需求。
[0005]
中国发明专利申请号201910511082.9公开了一种硅碳复合粉体材料的制备方法,其包括以下步骤:将硅粉、石墨粉混合均匀后加入球磨机中,将球磨机的研磨仓体抽真空并通入惰性气体,再向球磨机冷却套中通入循环冷却水,设定球磨工艺参数进行球磨,球磨结束得到硅碳复合粉体材料;其中,所述硅粉与石墨粉的质量比为1:1~1:9。
[0006]
中国发明专利申请号201810743893.7公开了一种高容量硅碳负极材料、制备方法及应用,制备方法包括以下步骤:将硅源、石墨粉和球磨介质混合,进行湿法球磨处理,抽滤,烘干,得到一种高容量硅碳负极材料。此发明先将硅粉、石墨和乙醇混合,再利用湿法球磨的方法,进行两次球磨即得到高容量硅碳负极材料。
[0007]
根据上述,现有方案中用于锂电池的硅基负极材料存在循环性能和稳定性较差的缺陷,而利用碳包覆改性得到的硅碳负极具有较佳的性能,但目前的硅碳负极生产方案大多较为复杂,通常需要高能球磨和高温碳化工艺,而且硅碳复合的效果较差,本发明提出了一种磁性包覆球磨生产锂电池硅碳负极活性材料的方法,可有效解决上述技术问题。
技术实现要素:[0008]
目前应用较广的锂电池硅碳负极材料的制备工艺通常需要高能球磨和高温碳化等工艺,制备过程较为复杂,而且硅碳复合效果差,影响了硅碳负极材料的性能和发展应用。
[0009]
本发明通过以下技术方案解决上述问题:一种磁性包覆球磨生产锂电池硅碳负极活性材料的方法,生产的具体过程为:(1)先将硅粉、铁粉混合均匀,然后加入球磨助剂并置于保护气氛为氮气的球磨机中,以转速为40~120r/min、球料比为2-3:1球磨1~6h,再将球磨后的浆料置于真空炉中进行真空退火,收集产物,得到粉末a;(2)先将多孔碳粉置于过量的阴离子表面活性剂中以频率为30~40khz、功率为200~350w的超声波处理30~40min,得到改性多孔碳粉,然后将得到的改性多孔碳粉与铁氧体前驱体、去离子水、无水乙醇混合均匀配制为悬浊液,再将悬浊液置于超声震荡仪中以频率为20~40khz、功率为180~540w分散30~60min,过滤收集滤渣置于真空炉中进行烧结,得到负载铁氧体的多孔碳,最后将负载铁氧体的多孔碳置于定向磁场下进行磁化,收集产物,得到粉末b;(3)先将步骤(1)中得到的粉末a与步骤(2)中得到的粉末b加入去离子水中混合配制为悬浊液,然后向悬浊液中加入少量ptfe乳液,以频率为30~50khz、功率为200~500w的超声波分散60~120min,再静置待自然沉降,离心分离收集底部的沉降物并进行造粒,最后将造粒获得的颗粒退火处理,经研磨、筛分,即得锂电池硅碳负极活性材料。
[0010]
本发明首先以硅粉、铁粉为原料,以分散剂、粘接剂、溶剂组成的混合物为球磨助剂,在保护气氛下进行球磨,控制球磨的转速和球料比等参数,然后将球磨浆料真空退火,硅粉通过粘接剂附着在铁粉表面,利用简单工艺制得硅铁复合材料。
[0011]
作为本发明的优选,步骤(1)所述硅粉的平均粒度为50~200nm。
[0012]
作为本发明的优选,步骤(1)所述铁粉的平均粒度为100~500nm。
[0013]
作为本发明的优选,步骤(1)所述球磨助剂包括分散剂、粘接剂、溶剂,各原料配比为,按重量份计,分散剂15~20重量份、粘接剂3~10重量份、溶剂100~200重量份。
[0014]
作为本发明的进一步优选,所述分散剂为nmp、pvp、六偏磷酸钠中的一种,所述粘接剂为sbr、pvdf、硬脂酸中的一种,所述溶剂为无水乙醇、nmp、去离子水中的至少一种。
[0015]
作为本发明的优选,步骤(1)所述真空退火的温度为100~150℃,时间为30~40min。
[0016]
作为本发明的优选,步骤(1)所述各原料配比为,按重量份计,硅粉5~50重量份、铁粉10~50重量份、球磨助剂100~300重量份。
[0017]
本发明利用阴离子表面活性剂改性多孔碳粉,改变了多孔碳粉表面的界面性,然后与磁性材料铁氧体前驱体混合,改性后的多孔碳粉与磁性材料具有良好的界面结合性,再利用超声振荡,使得负载铁氧体的多孔碳粉,之后进行过滤、烧结,使磁性材料进一步牢固负载到多孔碳粉,最后磁化处理,得到磁性碳材料。
[0018]
作为本发明的优选,步骤(2)所述多孔碳粉的平均粒度为1~3μm,孔隙率为30~70%。
[0019]
作为本发明的优选,步骤(2)所述阴离子表面活性剂为磺酸盐、硫酸酯盐中的一种。
[0020]
作为本发明的优选,步骤(2)所述铁氧体前驱体为硝酸铁与硝酸铜、硝酸锌、硝酸
镍、硝酸钴中至少一种组成的混合物,平均粒度为0.1~1μm。
[0021]
作为本发明的优选,步骤(2)所述烧结的温度为900~950℃,烧结时间为1~2h,烧结气氛为氮气。
[0022]
作为本发明的优选,步骤(2)所述定向磁场的磁场强度为0.3~0.4t。
[0023]
作为本发明的优选,步骤(2)所述各原料配比为,按重量份计,改性多孔碳粉50~95重量份、铁氧体前驱体10~50重量份、去离子水80~180重量份、无水乙醇90~160重量份。
[0024]
本发明将硅铁复合材料和磁性碳材料加入去离子水中,加入少量ptfe乳液后进行超声处理,通过磁性材料对金属粉末的吸附能力,通过磁性作用使碳粉和硅粉在悬浊液中自发复合,得到硅/碳复合材料,再通过后续的造粒工艺使小颗粒的复合颗粒团聚形成大颗粒,实现碳粉对硅粉的宏观包覆,最后经简单的低温热处理,得到复合效果极佳的硅碳活性材料。
[0025]
本发明整个过程利用超声分散、简易球磨和低温热处理实现,工艺简单,创造性地利用通过磁性材料对金属的吸附能力,有效提高了复合材料中硅粉和碳粉的均匀性和复合能力,不仅制备工艺简单可控,而且复合材料性能优异。
[0026]
作为本发明的优选,步骤(3)所述ptfe乳液的重量分数为5~8wt%。
[0027]
作为本发明的优选,步骤(3)所述造粒采用喷雾造粒、挤出造粒中的一种。
[0028]
作为本发明的优选,步骤(3)所述退火处理的温度为200~300℃,时间为30~120min,保护气氛为氮气、氩气中的一种。
[0029]
作为本发明的优选,步骤(3)所述各原料配比为,按重量份计,粉末a 5~50重量份、粉末b 50~95重量份、去离子水100~300重量份、ptfe乳液1~10重量份由上述方法制备得到的锂电池硅碳负极活性材料,其中硅和碳的复合效果好,显著提升了循环性能。通过测试,制备的硅碳负极活性材料制成扣式电池的首次放电容量为644~646 mah/g,循环50圈后放电容量保持在635~638 mah/g。
[0030]
本发明提供的一种磁性包覆球磨生产锂电池硅碳负极活性材料的方法,将硅粉与铁粉混合均匀,并加入球磨助剂置于球磨机中球磨,将球磨后的浆料置于真空炉中退火,收集产物记为粉末a;将多孔碳粉置于阴离子表面活性剂中超声处理,获得改性多孔碳粉,之后将铁氧体前驱体与改性多孔碳粉、去离子水和无水乙醇混合均匀配置为悬浊液,将悬浊液置于超声震荡仪中分散,过滤收集滤渣置于真空炉中烧结,获得负载铁氧体的多孔碳,之后将烧结产物置于定向磁场下进行磁化,收集产物记为粉末b;将粉末a与粉末b在去离子水中混合配置为悬浊液,将悬浊液中加入少量ptfe乳液进行超声分散,静置待其自然沉降,离心分离收集底部的沉降物进行造粒,将造粒获得的颗粒退火,经研磨、筛分,即可。
[0031]
本发明提供了一种磁性包覆球磨生产锂电池硅碳负极活性材料的方法,与现有技术相比,其突出的特点和优异的效果在于:1、提出了采用硅铁复合材料和负载铁氧体的多孔碳实现磁性包覆球磨生产锂电池硅碳负极活性材的方法。
[0032]
2、通过磁性材料对金属吸附能力,可以有效提高硅碳复合材料中硅粉和碳粉的均匀性和复合能力,制备获得的硅碳负极活性材料具有优异的循环性能。
[0033]
3、本发明的制备工艺简单,操作方便,具有大规模生产潜力。
附图说明
[0034]
图1为本发明实施例6制得的硅碳负极材料制衡扣式电池的循环50圈容量曲线。
[0035]
图2为本发明对比例1制得的硅碳负极材料制衡扣式电池的循环50圈容量曲线。
[0036]
图3为本发明对比例2制得的硅碳负极材料制衡扣式电池的循环50圈容量曲线。
[0037]
图4为本发明实施例6和对比例1制得的硅碳负极材料的扫描电镜照片,其中,a为实施例6,b为对比例1。
[0038]
图5为本发明实施例6和对比例2制得的硅碳负极材料在去离子水中超声处理后的分散情况照片,其中,c为实施例6,d为对比例2。
具体实施方式
[0039]
以下通过具体实施方式对本发明作进一步的详细说明,但不应将此理解为本发明的范围仅限于以下的实例。在不脱离本发明上述方法思想的情况下,根据本领域普通技术知识和惯用手段做出的各种替换或变更,均应包含在本发明的范围内。
[0040]
实施例1(1)先将硅粉、铁粉混合均匀,然后加入球磨助剂并置于保护气氛为氮气的球磨机中,以转速为920r/min、球料比为2.6:1球磨3h,再将球磨后的浆料置于真空炉中进行真空退火,收集产物,得到粉末a;硅粉的平均粒度为110nm;铁粉的平均粒度为250nm;球磨助剂包括分散剂、粘接剂、溶剂,各原料配比为,按重量份计,分散剂17重量份、粘接剂6重量份、溶剂160重量份;其中,分散剂为nmp,粘接剂为sbr,溶剂为无水乙醇;真空退火的温度为130℃,时间为36min;各原料配比为,按重量份计,硅粉30重量份、铁粉40重量份、球磨助剂190重量份;(2)先将多孔碳粉置于过量的阴离子表面活性剂中以频率为36khz、功率为270w的超声波处理34min,得到改性多孔碳粉,然后将得到的改性多孔碳粉与铁氧体前驱体、去离子水、无水乙醇混合均匀配制为悬浊液,再将悬浊液置于超声震荡仪中以频率为28khz、功率为350w分散50min,过滤收集滤渣置于真空炉中进行烧结,得到负载铁氧体的多孔碳,最后将负载铁氧体的多孔碳置于定向磁场下进行磁化,收集产物,得到粉末b;多孔碳粉的平均粒度为2μm,孔隙率为50%;阴离子表面活性剂为磺酸盐表面活性剂;铁氧体前驱体为硝酸铁与硝酸铜组成的混合物,平均粒度为0.6μm;烧结的温度为930℃,烧结时间为1.5h,烧结气氛为氮气;定向磁场的磁场强度为0.36t;各原料配比为,按重量份计,改性多孔碳粉65重量份、铁氧体前驱体40重量份、去离子水130重量份、无水乙醇120重量份;(3)先将步骤(1)中得到的粉末a与步骤(2)中得到的粉末b加入去离子水中混合配制为悬浊液,然后向悬浊液中加入少量ptfe乳液,以频率为38khz、功率为360w的超声波分散80min,再静置待自然沉降,离心分离收集底部的沉降物并进行造粒,最后将造粒获得的颗粒退火处理,经研磨、筛分,即得锂电池硅碳负极活性材料;ptfe乳液的重量分数为7wt%;造粒采用喷雾造粒;退火处理的温度为260℃,时间为100min,保护气氛为氮气;各原料配比为,按重量份计,粉末a 30重量份、粉末b 65重量份、去离子水180重量份、ptfe乳液5重量份。
[0041]
实施例2
(1)先将硅粉、铁粉混合均匀,然后加入球磨助剂并置于保护气氛为氮气的球磨机中,以转速为60r/min、球料比为2:1球磨5h,再将球磨后的浆料置于真空炉中进行真空退火,收集产物,得到粉末a;硅粉的平均粒度为100nm;铁粉的平均粒度为200nm;球磨助剂包括分散剂、粘接剂、溶剂,各原料配比为,按重量份计,分散剂16重量份、粘接剂5重量份、溶剂180重量份;其中,分散剂为pvp,粘接剂为pvdf,溶剂为nmp;真空退火的温度为1150℃,时间为38min;各原料配比为,按重量份计,硅粉10重量份、铁粉20重量份、球磨助剂250重量份;(2)先将多孔碳粉置于过量的阴离子表面活性剂中以频率为32khz、功率为250w的超声波处理38min,得到改性多孔碳粉,然后将得到的改性多孔碳粉与铁氧体前驱体、去离子水、无水乙醇混合均匀配制为悬浊液,再将悬浊液置于超声震荡仪中以频率为25khz、功率为220w分散50min,过滤收集滤渣置于真空炉中进行烧结,得到负载铁氧体的多孔碳,最后将负载铁氧体的多孔碳置于定向磁场下进行磁化,收集产物,得到粉末b;多孔碳粉的平均粒度为1μm,孔隙率为40%;阴离子表面活性剂为硫酸酯盐表面活性剂;铁氧体前驱体为硝酸铁与硝酸锌组成的混合物,平均粒度为0.3μm;烧结的温度为910℃,烧结时间为2h,烧结气氛为氮气;定向磁场的磁场强度为0.32t;各原料配比为,按重量份计,改性多孔碳粉55重量份、铁氧体前驱体20重量份、去离子水150重量份、无水乙醇130重量份;(3)先将步骤(1)中得到的粉末a与步骤(2)中得到的粉末b加入去离子水中混合配制为悬浊液,然后向悬浊液中加入少量ptfe乳液,以频率为35khz、功率为300w的超声波分散100min,再静置待自然沉降,离心分离收集底部的沉降物并进行造粒,最后将造粒获得的颗粒退火处理,经研磨、筛分,即得锂电池硅碳负极活性材料;ptfe乳液的重量分数为6wt%;造粒采用挤出造粒;退火处理的温度为220℃,时间为100min,保护气氛为氩气;各原料配比为,按重量份计,粉末a 10重量份、粉末b 55重量份、去离子水250重量份、ptfe乳液3重量份。
[0042]
实施例3(1)先将硅粉、铁粉混合均匀,然后加入球磨助剂并置于保护气氛为氮气的球磨机中,以转速为100r/min、球料比为3:1球磨1h,再将球磨后的浆料置于真空炉中进行真空退火,收集产物,得到粉末a;硅粉的平均粒度为150nm;铁粉的平均粒度为400nm;球磨助剂包括分散剂、粘接剂、溶剂,各原料配比为,按重量份计,分散剂19重量份、粘接剂9重量份、溶剂120重量份;其中,分散剂为六偏磷酸钠,粘接剂为硬脂酸,溶剂为去离子水;真空退火的温度为140℃,时间为33min;各原料配比为,按重量份计,硅粉40重量份、铁粉40重量份、球磨助剂150重量份;(2)先将多孔碳粉置于过量的阴离子表面活性剂中以频率为38khz、功率为320w的超声波处理32min,得到改性多孔碳粉,然后将得到的改性多孔碳粉与铁氧体前驱体、去离子水、无水乙醇混合均匀配制为悬浊液,再将悬浊液置于超声震荡仪中以频率为35khz、功率为500w分散40min,过滤收集滤渣置于真空炉中进行烧结,得到负载铁氧体的多孔碳,最后将负载铁氧体的多孔碳置于定向磁场下进行磁化,收集产物,得到粉末b;多孔碳粉的平均粒度为3μm,孔隙率为60%;阴离子表面活性剂为磺酸盐表面活性剂;铁氧体前驱体为硝酸铁与硝酸镍组成的混合物,平均粒度为0.8μm;烧结的温度为930℃,烧结时间为1h,烧结气氛为
氮气;定向磁场的磁场强度为0.38t;各原料配比为,按重量份计,改性多孔碳粉92重量份、铁氧体前驱体45重量份、去离子水100重量份、无水乙醇100重量份;(3)先将步骤(1)中得到的粉末a与步骤(2)中得到的粉末b加入去离子水中混合配制为悬浊液,然后向悬浊液中加入少量ptfe乳液,以频率为40khz、功率为300w的超声波分散100min,再静置待自然沉降,离心分离收集底部的沉降物并进行造粒,最后将造粒获得的颗粒退火处理,经研磨、筛分,即得锂电池硅碳负极活性材料;ptfe乳液的重量分数为7wt%;造粒采用喷雾造粒;退火处理的温度为280℃,时间为50min,保护气氛为氮气;各原料配比为,按重量份计,粉末a 40重量份、粉末b 90重量份、去离子水150重量份、ptfe乳液8重量份。
[0043]
实施例4(1)先将硅粉、铁粉混合均匀,然后加入球磨助剂并置于保护气氛为氮气的球磨机中,以转速为40r/min、球料比为2:1球磨6h,再将球磨后的浆料置于真空炉中进行真空退火,收集产物,得到粉末a;硅粉的平均粒度为50nm;铁粉的平均粒度为100nm;球磨助剂包括分散剂、粘接剂、溶剂,各原料配比为,按重量份计,分散剂15重量份、粘接剂3重量份、溶剂200重量份;其中,分散剂为nmp,粘接剂为sbr,溶剂为无水乙醇;真空退火的温度为100℃,时间为40min;各原料配比为,按重量份计,硅粉5重量份、铁粉10重量份、球磨助剂300重量份;(2)先将多孔碳粉置于过量的阴离子表面活性剂中以频率为30khz、功率为200w的超声波处理40min,得到改性多孔碳粉,然后将得到的改性多孔碳粉与铁氧体前驱体、去离子水、无水乙醇混合均匀配制为悬浊液,再将悬浊液置于超声震荡仪中以频率为20khz、功率为180w分散60min,过滤收集滤渣置于真空炉中进行烧结,得到负载铁氧体的多孔碳,最后将负载铁氧体的多孔碳置于定向磁场下进行磁化,收集产物,得到粉末b;多孔碳粉的平均粒度为1μm,孔隙率为30%;阴离子表面活性剂为硫酸酯盐表面活性剂;铁氧体前驱体为硝酸铁与硝酸钴组成的混合物,平均粒度为0.1μm;烧结的温度为900℃,烧结时间为2h,烧结气氛为氮气;定向磁场的磁场强度为0.3t;各原料配比为,按重量份计,改性多孔碳粉50重量份、铁氧体前驱体10重量份、去离子水180重量份、无水乙醇160重量份;(3)先将步骤(1)中得到的粉末a与步骤(2)中得到的粉末b加入去离子水中混合配制为悬浊液,然后向悬浊液中加入少量ptfe乳液,以频率为30khz、功率为200w的超声波分散120min,再静置待自然沉降,离心分离收集底部的沉降物并进行造粒,最后将造粒获得的颗粒退火处理,经研磨、筛分,即得锂电池硅碳负极活性材料;ptfe乳液的重量分数为5wt%;造粒采用挤出造粒;退火处理的温度为200℃,时间为30min,保护气氛为氩气;各原料配比为,按重量份计,粉末a 5重量份、粉末b 50重量份、去离子水300重量份、ptfe乳液1重量份。
[0044]
实施例5(1)先将硅粉、铁粉混合均匀,然后加入球磨助剂并置于保护气氛为氮气的球磨机中,以转速为120r/min、球料比为3:1球磨1h,再将球磨后的浆料置于真空炉中进行真空退火,收集产物,得到粉末a;硅粉的平均粒度为200nm;铁粉的平均粒度为500nm;球磨助剂包括分
散剂、粘接剂、溶剂,各原料配比为,按重量份计,分散剂20重量份、粘接剂10重量份、溶剂100重量份;其中,分散剂为pvp,粘接剂为pvdf,溶剂为nmp;真空退火的温度为150℃,时间为30min;各原料配比为,按重量份计,硅粉50重量份、铁粉50重量份、球磨助剂100重量份;(2)先将多孔碳粉置于过量的阴离子表面活性剂中以频率为40khz、功率为350w的超声波处理30min,得到改性多孔碳粉,然后将得到的改性多孔碳粉与铁氧体前驱体、去离子水、无水乙醇混合均匀配制为悬浊液,再将悬浊液置于超声震荡仪中以频率为40khz、功率为540w分散30min,过滤收集滤渣置于真空炉中进行烧结,得到负载铁氧体的多孔碳,最后将负载铁氧体的多孔碳置于定向磁场下进行磁化,收集产物,得到粉末b;多孔碳粉的平均粒度为3μm,孔隙率为70%;阴离子表面活性剂为磺酸盐表面活性剂;铁氧体前驱体为硝酸铁与硝酸铜组成的混合物,平均粒度为1μm;烧结的温度为950℃,烧结时间为1h,烧结气氛为氮气;定向磁场的磁场强度为0.4t;各原料配比为,按重量份计,改性多孔碳粉95重量份、铁氧体前驱体50重量份、去离子水80重量份、无水乙醇90重量份;(3)先将步骤(1)中得到的粉末a与步骤(2)中得到的粉末b加入去离子水中混合配制为悬浊液,然后向悬浊液中加入少量ptfe乳液,以频率为50khz、功率为500w的超声波分散60min,再静置待自然沉降,离心分离收集底部的沉降物并进行造粒,最后将造粒获得的颗粒退火处理,经研磨、筛分,即得锂电池硅碳负极活性材料;ptfe乳液的重量分数为8wt%;造粒采用喷雾造粒;退火处理的温度为300℃,时间为30min,保护气氛为氮气;各原料配比为,按重量份计,粉末a 50重量份、粉末b 95重量份、去离子水100重量份、ptfe乳液10重量份。
[0045]
实施例6(1)先将硅粉、铁粉混合均匀,然后加入球磨助剂并置于保护气氛为氮气的球磨机中,以转速为80r/min、球料比为2.5:1球磨4h,再将球磨后的浆料置于真空炉中进行真空退火,收集产物,得到粉末a;硅粉的平均粒度为120nm;铁粉的平均粒度为300nm;球磨助剂包括分散剂、粘接剂、溶剂,各原料配比为,按重量份计,分散剂18重量份、粘接剂8重量份、溶剂150重量份;其中,分散剂为六偏磷酸钠,粘接剂为硬脂酸,溶剂为去离子水;真空退火的温度为125℃,时间为35min;各原料配比为,按重量份计,硅粉30重量份、铁粉30重量份、球磨助剂200重量份;(2)先将多孔碳粉置于过量的阴离子表面活性剂中以频率为35khz、功率为280w的超声波处理35min,得到改性多孔碳粉,然后将得到的改性多孔碳粉与铁氧体前驱体、去离子水、无水乙醇混合均匀配制为悬浊液,再将悬浊液置于超声震荡仪中以频率为30khz、功率为360w分散45min,过滤收集滤渣置于真空炉中进行烧结,得到负载铁氧体的多孔碳,最后将负载铁氧体的多孔碳置于定向磁场下进行磁化,收集产物,得到粉末b;多孔碳粉的平均粒度为2μm,孔隙率为50%;阴离子表面活性剂为硫酸酯盐表面活性剂;铁氧体前驱体为硝酸铁与硝酸钴组成的混合物,平均粒度为0.6μm;烧结的温度为925℃,烧结时间为1.5h,烧结气氛为氮气;定向磁场的磁场强度为0.35t;各原料配比为,按重量份计,改性多孔碳粉75重量份、铁氧体前驱体30重量份、去离子水130重量份、无水乙醇120重量份;
(3)先将步骤(1)中得到的粉末a与步骤(2)中得到的粉末b加入去离子水中混合配制为悬浊液,然后向悬浊液中加入少量ptfe乳液,以频率为40khz、功率为350w的超声波分散90min,再静置待自然沉降,离心分离收集底部的沉降物并进行造粒,最后将造粒获得的颗粒退火处理,经研磨、筛分,即得锂电池硅碳负极活性材料;ptfe乳液的重量分数为6wt%;造粒采用挤出造粒;退火处理的温度为250℃,时间为75min,保护气氛为氩气;各原料配比为,按重量份计,粉末a 30重量份、粉末b 80重量份、去离子水200重量份、ptfe乳液6重量份。
[0046]
实施例6制得的硅碳负极活性材料制成扣式电池,循环50圈的容量曲线如图1所示。
[0047]
对比例1对比例1不加入铁粉与磁性材料,其他制备条件与实施例6相同,制得的硅碳负极活性材料制成扣式电池,其循环50圈的容量曲线如图2所示。
[0048]
对比例2对比例2不加入退火工艺,其他制备条件与实施例6相同,制得的硅碳负极活性材料制成扣式电池,其首次放电容量及循环50圈后放电容量如表2所示,循环50圈的容量曲线如图3所示。
[0049]
上述性能指标的测试方法为:循环容量测试:将本发明实施例和对比例制得的硅碳负极材料与super-p导电剂、pvdf粘接剂按照8:1:1的质量混合配置为浆料,浆料涂布在铜箔表面作为正极,以锂片为负极,六氟磷酸锂和碳酸酯作为电解液制备扣式电池,使用新威bts4000系列电池充放电测试仪对电池进行测试。记录初始充放电容量及循环50圈后的充放电容量,放电容量如表2所示,其中实施例6、对比例1和对比例2容量曲线分别如图1、图2和图3所示。
[0050]
扫描电镜观察:利用扫描电镜分别观察实施例6和对比例1制得的硅碳负极材料,所得扫描电镜照片如图4所示。
[0051]
分散性观察:将实施例6和对比例2制得的硅碳负极材料加入去离子水中分散,分散情况如如图5所示。
[0052]
由图1、图2及图3可见:实施例的硅碳负极材料制成的扣式电池循环50圈后容量高于对比例,这是由于通过磁性材料的互相吸附使碳粉对硅粉形成宏观包覆结构,提高硅粉与碳粉的复合能力。对比例1的扣式电池容量曲线如图2所示,在循环10圈后容量明显下降,这是由于未加入磁性材料,硅粉通过粘接剂与碳粉进行复合,在循环过程中从碳粉表面脱落,导致容量迅速衰减;对比例2由于未加入退火工艺,粘接剂难以使硅粉和碳粉有效复合,在浆料配置过程中硅粉与碳粉分离,,导致硅粉难以有效发挥容量。
[0053]
由图4可见:实施例6制得的硅碳负极材料颗粒形成较大粒径的团聚体,如图4a所示;而对比例1制得的硅碳负极材料硅粉通过粘接剂与碳粉进行复合,如图4b所示,影响循环性能。
[0054]
由图5可见:实施例6制得的硅碳负极材料在去离子水中结合紧密,如图5c所示;而对比例2制得的硅碳负极材料在浆料去离子水中硅粉与碳粉分离,如图5d所示,复合效果差。