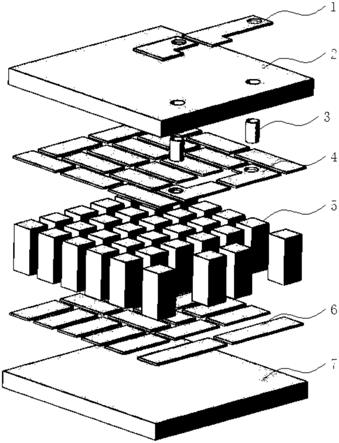
1.本实用新型涉及热电技术领域,尤其是涉及一种带导电通孔的热电模块。
背景技术:2.目前随着互联网行业的飞速发展,数据业务产品中巨大的用量以及更小封装尺寸的要求,孕育出了新的产品形式。为此我们发明了一种同样封装尺寸下,更大热流密度的带导电通孔的热电模块,以满足客户对尺寸及性能的要求。
3.中国专利公开号cn203192863u,申请日2013年04月27日,发明创造的名称为半导体热电模块,该申请案包括热端基板、冷端基板,热端基板与冷端基板之间设置p
‑
n型电偶对和导流条,p
‑
n型电偶对与导流条之间焊接,其中,该热端基板的传导热阻小于冷端基板的传导热阻。该申请方案中不能进一步提高电偶对的布置密度从而达到提高整体热电模块效率的问题。
技术实现要素:4.本实用新型是为了克服现有技术的因内部布局不合理造成空间利用率不高的问题,提供一种内部布局合理并提高空间利用率的带导电通孔的热电模块。
5.为了实现上述目的,本实用新型采用以下技术方案:
6.本实用新型解决其技术问题所采用的技术方案是:一种带导电通孔的热电模块,包括上基板、热电半导体颗粒和下基板,模块上基板开有若干导线孔,导线孔内壁溅射一层导体材料,并且在导线孔内壁形成穿透导体,穿透导体用于给热电半导体供电。本实用新型在上基板开有若干导线孔,并在导线孔内做金属溅射和电镀,使得上基板陶瓷片两面的电极可以联通并通电。使得原本部分空出用于打金线的区域可以排布上热电半导体颗粒充分利用空间,从而在相同封装尺寸下增加产品的制冷功率,产品比较于相同面积常规热电产品制冷量增加5
‑
20%。在常规热电制冷器中,约5
‑
20%的下基板面积会被用于设计焊盘,用于产品供电,本设计可以充分利用这部分面积,在相同尺寸下可以放下更多的半导体颗粒。
7.作为优选,所述是上基板上设置有第一焊盘,热电半导体第一端焊接在第一焊盘上,第一焊盘与穿透导体连接。通过在上下基板之间设置有p型半导体元件和n型半导体元件组成的热电半导体颗粒,通过焊锡的方式进行连接固定。通过激光对陶瓷片进行打孔,并在孔内做金属溅射和电镀,使得上基板陶瓷片两面的电极可以联通并通电。使得原本部分空出用于打金线的区域可以排布上半导体pn节充分利用空间,从而在相同封装尺寸下增加产品的制冷功率。
8.作为优选,所述下基板上设置有第二焊盘,热电半导体第二端焊接在第二焊盘上。通过在上下基板之间设置有p型半导体元件和n型半导体元件组成的热电半导体颗粒,通过焊锡的方式进行连接固定。通过激光对陶瓷片进行打孔,并在孔内做金属溅射和电镀,使得上基板陶瓷片两面的电极可以联通并通电。使得原本部分空出用于打金线的区域可以排布上半导体pn节充分利用空间,从而在相同封装尺寸下增加产品的制冷功率。
9.作为优选,所述上基板远离下基板一面设置有导线焊层,导线焊层用于焊接外部导线,外部导线连接穿透导线。产品可以在上基板表面打金线,很多产品放置在通信类的管壳中,管壳深度较深,打金线的劈刀需要深入到下基板面才能进行打金线作业。此设计的可以较大幅度提升工艺可行性,方便操作。
10.作为优选,所述导线孔呈锥状,在导线孔的第一锥面附着有导体材料,并且在导线孔的第一锥面形成第一穿透导体。在导线孔内做金属溅射时,由于导线孔呈锥状,金属溅射时的金属粒子的运动方向与第一锥面的夹角远大于0度,这样使得金属溅射时的金属粒子更容易附着在第一锥面上,若导线孔为圆柱形,则金属溅射时的金属粒子运动方向与导线孔的内壁的夹角在0度附近,这样使得金属溅射时的金属粒子附着效果不好,容易脱落,造成产品质量下降。
11.作为优选,所述导线孔内壁上还设有若干第二螺旋面,第二螺旋面附着有导体材料,并且在导线孔的第二螺旋面形成第二穿透导体。在导线孔内做金属溅射时,金属溅射时的金属粒子的运动方向与第二螺旋面的夹角在第二螺旋面螺旋角的余角附近,这使得金属溅射时的金属粒子的运动方向与第二螺旋面的夹角大于金属溅射时的金属粒子的运动方向与第一锥面的夹角,也既使得金属溅射时的金属粒子与第二螺旋面的结合更加紧密,不易脱落,提高产品质量。
12.作为优选,所述第一穿透导体连接第二穿透导体。
13.作为优选,所述导线孔圆柱状,在导线孔内壁设有若干第二螺旋面,第二螺旋面附着有导体材料,并且在导线孔的第二螺旋面形成穿透导体。在导线孔内做金属溅射时,金属溅射时的金属粒子的运动方向与第二螺旋面的夹角在第二螺旋面螺旋角的余角附近,这使得金属溅射时的金属粒子的运动方向与第二螺旋面的夹角大于金属溅射时的金属粒子的运动方向与导线孔圆柱内壁的夹角,也既使得金属溅射时的金属粒子与第二螺旋面的结合更加紧密,不易脱落,提高产品质量。
14.因此,本实用新型具有如下有益效果:(1)本实用新型在上基板开有若干导线孔,并在导线孔内做金属溅射和电镀,使得上基板陶瓷片两面的电极可以联通并通电。使得原本部分空出用于打金线的区域可以排布上热电半导体颗粒充分利用空间,从而在相同封装尺寸下增加产品的制冷功率,产品比较于相同面积常规热电产品制冷量增加5
‑
20%。在常规热电制冷器中,约5
‑
20%的下基板面积会被用于设计焊盘,用于产品供电,本设计可以充分利用这部分面积,在相同尺寸下可以放下更多的半导体颗粒;
15.(2)通过在上下基板之间设置有p型半导体元件和n型半导体元件组成的热电半导体颗粒,通过焊锡的方式进行连接固定。通过激光对陶瓷片进行打孔,并在孔内做金属溅射和电镀,使得上基板陶瓷片两面的电极可以联通并通电。使得原本部分空出用于打金线的区域可以排布上半导体pn节充分利用空间,从而在相同封装尺寸下增加产品的制冷功率;
16.(3)产品可以在上基板表面打金线,很多产品放置在通信类的管壳中,管壳深度较深,打金线的劈刀需要深入到下基板面才能进行打金线作业。此设计的可以较大幅度提升工艺可行性,方便操作;
17.(4)在导线孔内做金属溅射时,若导线孔为圆柱形,则金属溅射时的金属粒子运动方向与导线孔的内壁的夹角在0度附近,这样使得金属溅射时的金属粒子附着效果不好,容易脱落,造成产品质量下降,但由于本实用新型中导线孔呈锥状,金属溅射时的金属粒子的
运动方向与第一锥面的夹角远大于0度,这样使得金属溅射时的金属粒子更容易附着在第一锥面上;
18.(5)在导线孔内做金属溅射时,金属溅射时的金属粒子的运动方向与第二螺旋面的夹角在第二螺旋面螺旋角的余角附近,这使得金属溅射时的金属粒子的运动方向与第二螺旋面的夹角大于金属溅射时的金属粒子的运动方向与第一锥面的夹角,也既使得金属溅射时的金属粒子与第二螺旋面的结合更加紧密,不易脱落,提高产品质量。
附图说明
19.图1是本实用新型的一种结构爆炸图
20.图2是本实用新型的一种导线孔俯视图
21.图3是本实用新型的一种导线孔剖视图
22.图中:1. 导线焊层, 2.上基板,21.导线孔,211.第一圆锥面,212.第二螺旋面,3.穿透导体,4.第一焊盘, 5. 热电半导体颗粒, 6.第二焊盘,7. 下基板。
具体实施方式
23.下面结合附图与具体实施方式对本实用新型做进一步的描述。
24.实施例1:一种带导电通孔的热电模块,如图1所示,包括上基板2、热电半导体颗粒5和下基板7,热电半导体颗粒设置在上基板和下基板之间,上基板开有若干导线孔21,导线孔内壁附着一层导体材料,并且在导线孔内壁形成穿透导体,穿透导体用于给热电半导体供电。上基板上设置有第一焊盘4,热电半导体第一端焊接在第一焊盘上,第一焊盘与穿透导体连接。下基板上设置有第二焊盘6,热电半导体第二端焊接在第二焊盘上。上基板远离下基板一面设置有导线焊层1,导线焊层用于焊接外部导线,外部导线连接穿透导线。如图1和图2所示,导线孔呈锥状,在导线孔的第一锥面211附着有导体材料,并且在导线孔的第一锥面形成第一穿透导体。导线孔内壁上还设有若干第二螺旋面212,第二螺旋面附着有导体材料,并且在导线孔的第二螺旋面形成第二穿透导体。第一穿透导体连接第二穿透导体。
25.本实用新型在上基板开有若干导线孔,并在导线孔内做金属溅射和电镀,使得上基板陶瓷片两面的电极可以联通并通电。使得原本部分空出用于打金线的区域可以排布上热电半导体颗粒充分利用空间,从而在相同封装尺寸下增加产品的制冷功率,产品比较于相同面积常规热电产品制冷量增加5
‑
20%。在常规热电制冷器中,约5
‑
20%的下基板面积会被用于设计焊盘,用于产品供电,本设计可以充分利用这部分面积,在相同尺寸下可以放下更多的半导体颗粒。
26.通过在上下基板之间设置有p型半导体元件和n型半导体元件组成的热电半导体颗粒,通过焊锡的方式进行连接固定。通过激光对陶瓷片进行打孔,并在孔内做金属溅射和电镀,使得上基板陶瓷片两面的电极可以联通并通电。使得原本部分空出用于打金线的区域可以排布上半导体pn节充分利用空间,从而在相同封装尺寸下增加产品的制冷功率。
27.通过在上下基板之间设置有p型半导体元件和n型半导体元件组成的热电半导体颗粒,通过焊锡的方式进行连接固定。通过激光对陶瓷片进行打孔,并在孔内做金属溅射和电镀,使得上基板陶瓷片两面的电极可以联通并通电。使得原本部分空出用于打金线的区域可以排布上半导体pn节充分利用空间,从而在相同封装尺寸下增加产品的制冷功率。
28.产品可以在上基板表面打金线,很多产品放置在通信类的管壳中,管壳深度较深,打金线的劈刀需要深入到下基板面才能进行打金线作业。此设计的可以较大幅度提升工艺可行性,方便操作。
29.在导线孔内做金属溅射时,由于导线孔呈锥状,金属溅射时的金属粒子的运动方向与第一锥面的夹角远大于0度,这样使得金属溅射时的金属粒子更容易附着在第一锥面上,若导线孔为圆柱形,则金属溅射时的金属粒子运动方向与导线孔的内壁的夹角在0度附近,这样使得金属溅射时的金属粒子附着效果不好,容易脱落,造成产品质量下降。
30.在导线孔内做金属溅射时,金属溅射时的金属粒子的运动方向与第二螺旋面的夹角在第二螺旋面螺旋角的余角附近,这使得金属溅射时的金属粒子的运动方向与第二螺旋面的夹角大于金属溅射时的金属粒子的运动方向与第一锥面的夹角,也既使得金属溅射时的金属粒子与第二螺旋面的结合更加紧密,不易脱落,提高产品质量。
31.实施例2:采用与实施例1基本相同的技术方案,其不同之处在于导线孔21呈圆柱状,在导线孔内壁设有若干第二螺旋面212,第二螺旋面附着有导体材料,并且在导线孔的第二螺旋面形成穿透导体。在导线孔内做金属溅射时,金属溅射时的金属粒子的运动方向与第二螺旋面的夹角在第二螺旋面螺旋角的余角附近,这使得金属溅射时的金属粒子的运动方向与第二螺旋面的夹角大于金属溅射时的金属粒子的运动方向与导线孔圆柱内壁的夹角,也既使得金属溅射时的金属粒子与第二螺旋面的结合更加紧密,不易脱落,提高产品质量。