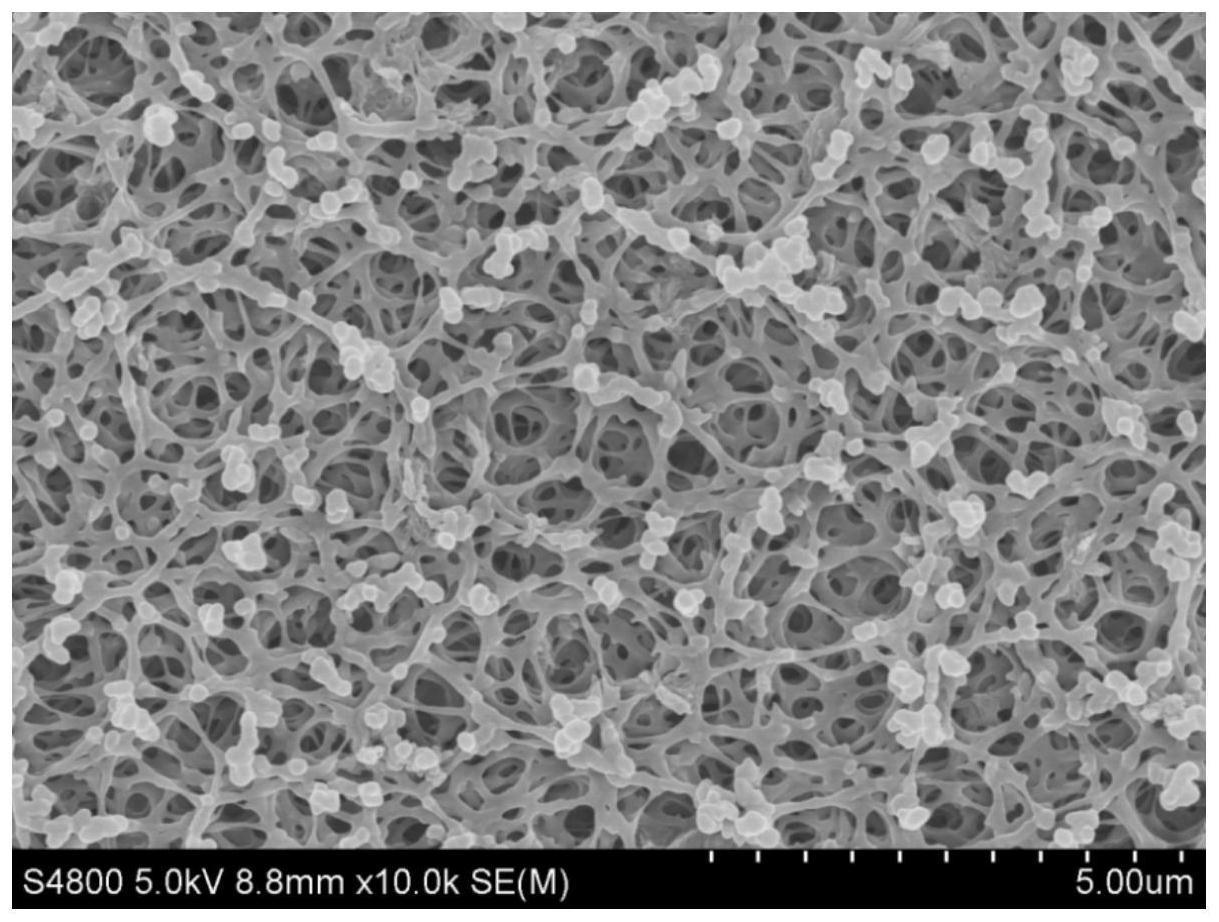
zhang a,tiange xu,et al.poly(m
‑
phenylene isophthalamide)separator for improving the heat resistance and power density of lithium
‑
ion batteries[j].journal of power sources,2016,329:8
‑
16.),但隔膜的循环稳定性还可进一步提升,在循环50圈后,容量保留率为91.8%,衰减了8.2%。
技术实现要素:[0006]
本发明的目的是克服现有技术的不足,提供一种利用优化后的非溶剂致相分离法制备多孔间位芳纶锂离子电池隔膜的方法,即采用梯度凝固浴的方式,通过调节相分离过程中铸膜液组成和成型条件,来控制相分离的传质过程,实现无致密皮层、结构均匀的多孔隔膜的制备。
[0007]
本发明具体通过如下技术方案予以实现:
[0008]
一种非溶剂致相分离法制备多孔间位芳纶锂离子电池隔膜的方法,包括如下步骤:
[0009]
(1)配制铸膜液:将锂盐或钙盐溶解在水和偶极溶剂中,得到溶液a;之后将溶液a和醇类溶剂分批次缓慢的加入到pmia原液中,搅拌6
‑
12h,得到均相溶液体系b,所述溶液b中pmia的质量分数为15%~19%,锂盐或钙盐的比例为1%~5%,水的比例为0.5%~3%,醇类溶剂的比例为0.5%~1.5%;之后对溶液b进行脱泡处理;
[0010]
(2)配制凝固浴:使用偶极溶剂和含有羟基类溶剂中的一种或多种溶液混合物作为凝固浴,将上述物质进行混合,得到凝固浴溶液c1和c2,所述溶液c1中v(偶极溶剂):v(含有羟基类溶剂)=8:2~5:5;所述溶液c2中v(偶极溶剂):v(含有羟基类溶剂)=3:7~0:10;
[0011]
(3)将步骤(1)制备的溶液b倒于成型基板上,并利用50
‑
150μm的刮刀将其刮涂成膜,控制涂布速度为20
‑
100m/min;之后将其一起放入凝固浴中,即先于凝固浴c1中10s~120s;后于凝固浴c2中30s~120s;最后将其放入纯水中12h~24h用于去除多孔膜内的残余溶剂,在凝固过程中pmia薄膜与成型基膜自动剥离;
[0012]
(4)将步骤(3)得到的pmia薄膜用去离子水冲洗,之后放入真空烘箱中在60~100℃下干燥后,得到可以用于锂离子电池的多孔间位芳纶锂离子电池隔膜。
[0013]
本发明上述方法中,其中优选所述的锂盐或钙盐为氯化锂、溴化锂、氯化钙、溴化钙中的一种或多种。
[0014]
所述的偶极溶剂为二甲基乙酰胺、二甲基甲酰胺、二甲亚砜和氮甲基吡咯烷酮中的一种或多种。
[0015]
步骤(1)中所述的醇类溶剂为甲醇、乙醇、异丙醇、乙二醇、丙二醇、丙三醇中的一种或多种。
[0016]
步骤(1)中所述的脱泡处理为真空脱泡或离心脱泡中的一种或多种,其中,真空脱泡温度为60℃~100℃,离心脱泡的转速为5000r/min~8000r/min。
[0017]
步骤(2)中所述的偶极溶剂优选为二甲基乙酰胺、二甲基甲酰胺、二甲亚砜和氮甲基吡咯烷酮中的一种或多种,且与步骤(1)中保持一致。
[0018]
步骤(2)中所述的含有羟基类溶剂优选为水、甲醇、乙醇、异丙醇、乙二醇、丙二醇、丙三醇中的一种或多种。
[0019]
步骤(3)中所述凝固浴优选为梯度凝固浴。
[0020]
本发明还提供了一种上述制备方法制得的多孔间位芳纶隔膜组装的电池。
[0021]
本发明提出的利用优化后的非溶剂致相分离法制备多孔间位芳纶锂离子电池隔膜方法与现有制备方法相比,其有益效果在于:本发明采用的非溶剂致相分离法,通过对铸膜液组成、凝固浴组成及成型条件进行调节,采用阶梯凝固浴,制备得到的耐热性间位芳纶电池隔膜具有优异的表皮孔结构和内部孔结构,无致密皮层生成,孔径在亚微米级别且可调,具有孔隙率高,结构均匀等特点,同时具有较好的力学性能和对电解液的浸润性,从而有效降低锂离子传输内阻,使电池获得较好的电化学性能。本发明采用的非溶剂致相分离法,制备过程简单,成型时间短,制备工艺易调节,能耗低,适合大规模工业化生产。
附图说明
[0022]
图1为本发明实施例1制备的间位芳纶锂离子电池隔膜的表面形貌图。
[0023]
图2为本发明实施例1制备的间位芳纶锂离子电池隔膜的截面形貌图。
[0024]
图3为本发明实施例1制备的间位芳纶锂离子电池隔膜的孔径分布图。
[0025]
图4为本发明实施例1制备的间位芳纶锂离子电池隔膜在热处理前后的尺寸变化图。
[0026]
图5为本发明实施例1制备的间位芳纶锂离子电池隔膜对碳酸酯类电解液的接触角。
[0027]
图6为本发明实施例1制备的间位芳纶锂离子电池隔膜的应力
‑
应变曲线。
[0028]
图7为本发明实施例1制备的间位芳纶隔膜用于锂离子电池中的循环性能图。
具体实施方式
[0029]
下面结合具体实施实例对本发明做进一步说明。需要说明的是,仅仅是对本发明所作的举例和说明,所属本技术领域的技术人员对所描述的具体实施例做各种各样的修改或补充或采取类似的方式替代,只要不偏离发明的构思或者超越本权利要求书所定义的范围,均应视为落入本发明的保护范围。
[0030]
实施例1
[0031]
配制铸膜液:将相对于整个铸膜液体系的溴化锂3%,水1%和二甲基乙酰胺进行共混,之后将其缓慢滴加到pmia原液中,搅拌,加入丙三醇0.5%,搅拌12h至得到均匀溶液;之后将其在6000r/min下进行离心脱泡,得到均相透明铸膜液。配制凝固浴:使用v(二甲基乙酰胺):v(丙三醇)=7:3配制凝固浴溶液c1;使用v(二甲基乙酰胺):v(水)=3:7配制凝固浴溶液c2;将制备的铸膜液倒于成型基板上,并利用100μm的刮刀将其刮涂成膜,之后放于凝固浴c1中30s;于凝固浴c2中30s;最后将其放入纯水中12h。将去除残余溶剂后的pmia隔膜用去离子水冲洗3次,之后放入真空烘箱中在60℃下干燥12h,得到可以用于锂离子电池的pmia隔膜。以钴酸锂为正极,石墨为负极,以1mol/l的六氟磷酸锂为电解液,按正极壳/正极/隔膜/负极/垫片/簧片/负极壳的顺序将制备的pmia隔膜组装成2032型纽扣电池,并进行隔膜形貌测试(附图1和2)、热稳定性测试(附图4)、浸润性测试(附图5)、拉伸强度测试(附图6)和电池循环性能测试(附图7),最终测得pmia隔膜组装的电池初始放电比容量为143.7mah/g,充放电循环50圈后,容量保留率为95.8%,衰减了4.2%。
[0032]
实施例2
[0033]
配制铸膜液:将相对于整个铸膜液体系的溴化锂1%,水3%和二甲基甲酰胺进行共混,之后将其缓慢滴加到pmia原液中,搅拌10h至得到均匀溶液;之后将其在8000r/min下进行离心脱泡,得到均相透明铸膜液。配制凝固浴:使用v(二甲基甲酰胺):v(丙三醇)=5:5配制凝固浴溶液c1;使用v(二甲基甲酰胺):v(水)=2:8配制凝固浴溶液c2;将制备的铸膜液倒于成型基板上,并利用150μm的刮刀将其刮涂成膜,之后放于凝固浴c1中120s;于凝固浴c2中120s;最后将其放入纯水中12h。将去除残余溶剂后的pmia隔膜用去离子水冲洗3次,之后放入真空烘箱中在60℃下干燥12h,得到可以用于锂离子电池的pmia隔膜。以钴酸锂为正极,石墨为负极,以1mol/l的六氟磷酸锂为电解液,按正极壳/正极/隔膜/负极/垫片/簧片/负极壳的顺序将制备的pmia隔膜组装成2032型纽扣电池,并进行电池循环性能测试。充放电循环50圈后,测得的容量保留率为94.6%,衰减了5.4%。
[0034]
实施例3
[0035]
配制铸膜液:将相对于整个铸膜液体系的氯化钙4.5%和二甲亚砜进行共混,之后将其缓慢滴加到pmia原液中,搅拌,加入丙三醇1%,搅拌6h至得到均匀溶液;之后将其在6000r/min下进行离心脱泡,得到均相透明铸膜液。配制凝固浴:使用v(二甲亚砜):v(水)=6:4配制凝固浴溶液c1;使用纯水作为凝固浴溶液c2;将制备的铸膜液倒于成型基板上,并利用80μm的刮刀将其刮涂成膜,之后放于凝固浴c1中30s;于凝固浴c2中12h。将去除残余溶剂后的pmia隔膜用去离子水冲洗3次,之后放入真空烘箱中在60℃下干燥12h,得到可以用于锂离子电池的pmia隔膜。以钴酸锂为正极,石墨为负极,以1mol/l的六氟磷酸锂为电解液,按正极壳/正极/隔膜/负极/垫片/簧片/负极壳的顺序将制备的pmia隔膜组装成2032型纽扣电池,并进行电池循环性能测试。充放电循环50圈后,测得的容量保留率为94.0%,衰减了6.0%。
[0036]
实施例4
[0037]
配制铸膜液:将相对于整个铸膜液体系的氯化锂3%,水2%和氮甲基吡咯烷酮进行共混,之后将其缓慢滴加到pmia原液中,搅拌,加入丙三醇1.5%,搅拌12h至得到均匀溶液;之后将其在8000r/min下进行离心脱泡,得到均相透明铸膜液。配制凝固浴:使用v(氮甲基吡咯烷酮):v(乙醇)=7:3配制凝固浴溶液c1;使用v(氮甲基吡咯烷酮):v(水)=2:8配制凝固浴溶液c2;将制备的铸膜液倒于成型基板上,并利用100μm的刮刀将其刮涂成膜,之后放于凝固浴c1中60s;于凝固浴c2中60s;最后将其放入纯水中12h。将去除残余溶剂后的pmia隔膜用去离子水冲洗3次,之后放入真空烘箱中在60℃下干燥12h,得到可以用于锂离子电池的pmia隔膜。以钴酸锂为正极,石墨为负极,以1mol/l的六氟磷酸锂为电解液,按正极壳/正极/隔膜/负极/垫片/簧片/负极壳的顺序将制备的pmia隔膜组装成2032型纽扣电池,并进行电池循环性能测试。充放电循环50圈后,测得的容量保留率为96.5%,衰减了3.5%。