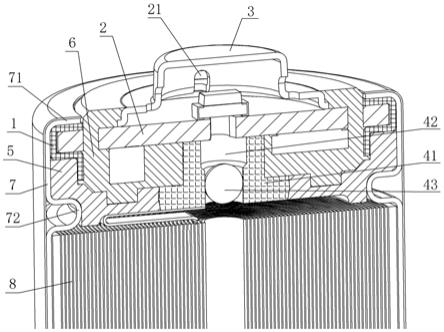
1.本发明涉及电池,特别是涉及一种电池盖帽的结构以及采用该种电池盖帽的锂电池结构。
背景技术:2.在现代化的发展之中,电池被越来越广泛地应用于各类用电器具,人们对电池的性能要求也越来越高。为了提高电池的性能和安全性,中国专利公开号为cn112201839a的发明专利申请公开了一种锂电池结构,如图1所示,其在电池的盖帽组件101上设置有电路板102、金属环103、防爆阀104,并在金属环内侧与防爆阀之间填充塑胶以形成胶块105,通过该胶块包裹电路元件。该锂电池结构可以利用贯通孔向钢壳内的卷芯进行抽真空和注电解液,从而更充分地利用电池空间和提高电池容量。但另一方面,胶块虽然能够保护电路元件并提高各零部件的安装稳定性和连接强度,但其底部直接与电池的卷芯106相对,使得其会与电池内部的电解液接触,而两者长时间的接触下很可能会产生化学反应,导致胶块被腐蚀、电解液变质,从而破坏锂电池的安全性和稳定性。另外,现有的锂电池结构中,钢壳与盖帽之间通过焊接固定,其工艺要求较高,且若焊接不到位,有可能会引发电池内部的电解液泄漏,从而影响电池的安全性。
技术实现要素:3.本发明的目的在于提供一种可避免胶块与电池内部电解液接触的电池盖帽结构,以及一种采用该种电池盖帽并可提高钢壳与盖帽之间连接稳定性的锂电池结构,以提高锂电池的工作稳定性和安全性。
4.本发明所述的电池盖帽结构,包括环形且中空的金属环,金属环内设有具备电源管理功能的电路板,电路板的外侧连接有用于导电的电极端子、内侧处设置有防爆阀;所述金属环的外侧端包覆于电路板的外侧边缘并与电路板电路电连通,金属环位于电路板内侧的末端背向电路板向外延伸,金属环的延伸端外侧套有密封圈,密封圈的内侧与防爆阀外壁相接触,电路板内侧与金属环、密封圈、防爆阀之间灌有胶块。
5.所述的电池盖帽结构可以设置于电池的正极端,电极端子是作为电池正极连接端的正极帽;除此之外,电池盖帽结构也可以设置于电池的负极端,电极端子是电池底部的负极连接片。
6.本发明所述的锂电池结构,包括钢壳及设置于钢壳内的卷芯,钢壳的开口端连接有环形且中空的金属环,金属环内设有具备电源管理功能的电路板,电路板的外侧连接有用于导电的电极端子、内侧处设置有防爆阀;所述金属环的外侧端包覆于电路板的外侧边缘并与电路板电路电连通,金属环位于电路板内侧的末端背向电路板向外延伸;钢壳的末端边缘向内弯折为翻边并抵于金属环的外侧,钢壳位于金属环延伸端与卷芯之间处设有向内凸起的钢壳凸台;另有密封圈,密封圈的外侧端设置于金属环与钢壳凸台之间,密封圈的内侧与防爆阀外壁相接触,电路板内侧与金属环、密封圈、防爆阀之间灌有胶块。
7.本发明所述的电池盖帽结构及锂电池结构,假设将电池盖帽结构安装于电池的正极端,电池盖帽结构上的金属环可以作为负极连接件使电路板负极端与钢壳电连接,钢壳即可作为电池的负极端连接于用电设备上,金属环的设置还可以作为散热连接件,快速地将电路板、电子元件等零件产生的热量导向钢壳,从而提高散热效率;而金属环与防爆阀之间设置密封圈,密封圈的外侧端、内侧端分别用以与金属环、防爆阀密封;在此情况下,通过塑料填充而形成的胶块将被阻挡于密封圈和防爆阀朝向电路板的一侧,由此隔绝了胶块与电池内部的电解液,由此有效地隔绝胶块与电解液,从而防止胶块与电解液相互之间产生化学反应,也避免了因此而导致的锂电池工作稳定性和安全性问题;同时,该种电池盖帽结构还可以作为单独的零部件进行制造和出售,使其独立于传统的电池之外,极大地提高了其应用和使用范围。而钢壳上设置有滚槽状的钢壳凸台,可以将整体化制造的电池盖帽结构放入钢壳内,然后再将钢壳的末端进行翻边弯折,将电池盖帽结构固定的同时,也通过金属环实现了与电路板负极端的连接。该种锂电池结构,钢壳通过钢壳凸台和翻边夹紧固定电池盖帽组件,避免了传统焊接操作而带来的泄漏和安全性问题,且制造极为方便,有利于降低生产难度和提高生产效率。同样地,若将电池盖帽结构安装于电池的负极端,金属环将作为正极连接件与钢壳、正极帽连接,电极端子则作为电池的负极端使用,且该种电池同样可以有效隔绝胶块与电解液,从而防止胶块与电解液相互之间产生化学反应,且作为电极负极端的盖帽结构可以降低正极电路所带来的高电阻问题,提高电池的制造方便性,降低制造成本和电能能耗。
附图说明
8.图1是现有锂电池结构的结构示意图。
9.图2、3是本发明所述电池盖帽结构及锂电池结构的结构示意图。
10.图4是去除外层包装后的锂电池结构的结构示意图。
11.图5是密封圈的结构示意图。
12.图6是电池盖帽结构及锂电池结构实施例二的结构示意图。
13.图7是电池盖帽结构及锂电池结构实施例三的结构示意图。
14.图8是电池盖帽结构及锂电池结构实施例四的结构示意图。
具体实施方式
15.实施例一,如图2
‑
5所示。电池盖帽结构10设置于锂电池20的正极端,作为电池正极使用。
16.一种电池盖帽结构,包括环形且中空的金属环1,金属环内设有具备电源管理功能的电路板2,电路板的外侧连接有用于导电的电极端子3、内侧处设置有防爆阀;所述电极端子3是正极帽,所述金属环的外侧端包覆于电路板的外侧边缘并与电路板电路的负极端电连通,金属环位于电路板内侧的末端背向电路板向外延伸,金属环的延伸端外侧套有密封圈5,密封圈的内侧与防爆阀外壁相接触,电路板内侧与金属环、密封圈、防爆阀之间灌有胶块6。
17.电池盖帽结构上的金属环可以作为负极连接件使电路板负极端与钢壳电连接,钢壳即可作为电池的负极端连接于用电设备上,金属环的设置还可以作为散热连接件,快速
地将电路板、电子元件等零件产生的热量导向钢壳,从而提高散热效率;而金属环与防爆阀之间设置密封圈,密封圈的外侧端、内侧端分别用以与金属环、防爆阀密封;在此情况下,通过塑料填充而形成的胶块将被阻挡于密封圈和防爆阀朝向电路板的一侧,由此隔绝了胶块与电池内部的电解液,由此有效地隔绝胶块与电解液,从而防止胶块与电解液相互之间产生化学反应,也避免了因此而导致的锂电池工作稳定性和安全性问题;同时,该种电池盖帽结构还可以作为单独的零部件进行制造和出售,使其独立于传统的电池之外,极大地提高了其应用和使用范围。而钢壳上设置有滚槽状的钢壳凸台,可以将整体化制造的电池盖帽结构放入钢壳内,然后再将钢壳的末端进行翻边弯折,将电池盖帽结构固定的同时,也通过金属环实现了与电路板负极端的连接。
18.所述的电池盖帽结构,密封圈5朝向电路板2一侧的中部设有向内凹陷的凹台51,若干个凹台沿密封圈环形间隔设置,胶块6设有延伸至凹台内的塑胶凸台相啮合,从而进一步提高零部件之间的连接强度和密封性。
19.所述的电池盖帽结构,电路板2上设置有连通内外两侧的过胶孔,胶块6从外侧穿过电路板并延伸至电路板内侧以覆盖电路板上的电路元件,这可以使注胶时能够从电路板的外侧流入内侧并最终形成所需形状的胶块,由此保证生产质量并简化工艺,同时降低加工成本和提高生产效率。另外,正极帽3与电路板2相邻的边缘处沿电池的径向向外延伸,胶块6的外侧端覆盖于正极帽向外延伸的边缘处;在将电池盖帽结构安装至钢壳内之后,注入塑胶以形成胶块,胶块不仅能够保护电路板上的电路元件和使内部形成密封,还可以覆盖正极帽的边缘以提高其固定强度,保证电池的工作稳定性。
20.现有的锂电池结构中,防爆金属管的管孔为直径一致的光滑直管,当电池异常而使防爆珠从防爆金属管喷出时,防爆珠很容易冲破正极帽而喷出电池外,从而危害用电器具和使用人员的安全。为此,本发明所述的电池盖帽结构,防爆阀包括防爆金属管41和设置于防爆金属管的管孔42内的防爆珠43;所述管孔包括以台阶状设置的大管孔和小管孔,防爆珠设于小管孔内且密封相抵,大管孔设于与电路板2相邻的一端,电路板上相对大管孔处设有透气孔21,且透气孔的直径小于防爆珠。所述透气孔(21)为椭圆形孔,其短直径的尺寸小于防爆珠(43)的直径,且长直径的尺寸大于防爆珠的直径。由此使得电路板的外侧可以经透气孔、管孔通向电池内部;在正常使用情况下,防爆珠固定于直径较小的小管孔一端,对小管孔形成密封;若锂电池内部发生异常或产生高热而造成电解液气化时,锂电池内部将会充斥大量气体而导致气压增加,增加气压将会对防爆珠形成推动力,当该推动力达到设定值后,防爆珠被推离小管孔而进入大管孔,并通过电路板的阻挡而留在大管孔内,而多余的气体将通过大管孔和电路板透气孔排出以形成泄压,从而使电池内部的气压下降,由此防止锂电池因内部气压过大而爆炸;透气孔为椭圆形,其一方面可以防止防爆珠喷出,一方面又可以供气体排出,避免防爆珠堵塞透气孔。故而,通过该结构可以使防爆珠从小管孔喷出后停留于大管孔内,避免其喷出至电池之外而危害使用者。
21.一种锂电池结构,包括钢壳7及设置于钢壳内的卷芯8,钢壳的开口端连接有环形且中空的金属环1,金属环内设有具备电源管理功能的电路板2,电路板的外侧连接有用于导电的电极端子3、内侧处设置有防爆阀;所述金属环的外侧端包覆于电路板的外侧边缘并与电路板电路电连通,金属环位于电路板内侧的末端背向电路板向外延伸;钢壳的末端边缘向内弯折为翻边71并抵于金属环的外侧,钢壳位于金属环延伸端与卷芯之间处设有向内
凸起的钢壳凸台72;另有密封圈5,密封圈的外侧端设置于金属环与钢壳凸台之间,密封圈的内侧与防爆阀外壁相接触,电路板内侧与金属环、密封圈、防爆阀之间灌有胶块6。
22.所述的锂电池结构,钢壳凸台72由钢壳7向内弯曲过渡而成,形成滚槽状,以便于加工制作,降低制造难度和制造成本。
23.所述的锂电池结构,钢壳上设置有滚槽状的钢壳凸台,可以将整体化制造的电池盖帽结构放入钢壳内,然后再将钢壳的末端进行翻边弯折,将电池盖帽结构固定的同时,也通过金属环实现了与电路板负极端的连接。该种锂电池结构,钢壳通过钢壳凸台和翻边夹紧固定电池盖帽组件,避免了传统焊接操作而带来的泄漏和安全性问题,且制造极为方便,有利于降低生产难度和提高生产效率。
24.实施例二,如图6所示。
25.所述的电池盖帽结构及锂电池结构,电池盖帽结构设置于锂电池结构的负极端,作为电池负极使用,电极端子3是电池底部的负极连接片;负极连接片设于电路板2外侧并与电路板电路的负极端电连通;其余与实施例一相同。
26.该电池盖帽结构除了可以安装于电池正极之外,还可以安装于电池负极,作为电池负极的连接端,这样可以降低正极电路所带来的高电阻问题,提高电池的制造方便性,降低制造成本和电能能耗。
27.实施例三,如图7所示。
28.所述的电池盖帽结构及锂电池结构,防爆金属管41的外壁上连接有导电环44,导电环与电路板2的内侧固定连接并电连通;所述防爆金属管41采用镍材料制作而成,导电环44采用铜材料制作而成;其余与实施例一相同。
29.为了提高防爆金属管的耐腐蚀性,避免其与电池内部的电解液接触而产生化学反应,防爆金属管采用镍材料制作而成,但该种材料难以与制作电路板的pcb相互焊接,为此,在防爆金属管外由铜材料制作而成的导电环,通过该导电环可以更为稳定、牢固地与电路板连接,从而保证电池工作的稳定性。
30.实施例四,如图8所示。
31.所述的电池盖帽结构及锂电池结构,导电环44朝向电路板2的一端覆盖于防爆金属管41的外侧端,导电环背向电路板的一端设有内扣45,防爆金属管外壁上设有与内扣相配合的扣槽46,导电环通过内扣卡入扣槽内与防爆金属管相互固定;其余与实施例五相同。
32.通过内扣和扣槽的相互定位,可以有效保证其导电端的连接,并提高安装方便性和准确性。