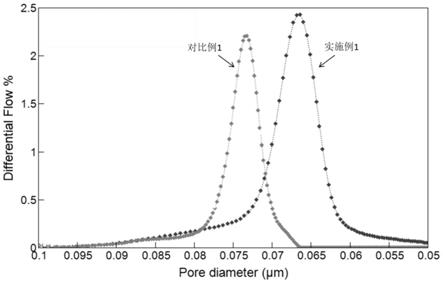
1.本发明涉及一种全聚合物耐高温隔膜及其制备方法。
背景技术:2.目前,锂离子电池在绿色能源领域有着举足轻重中的地位,广泛应用在电能存储, 3c以及动力电池等领域。作为锂离子电池的重要组成部件,隔膜起着隔绝正负极,防止电池内短路的作用,同时贯穿隔膜的微孔为锂离子的传输提供了通道。目前,商业化的锂离子电池隔膜多采用聚烯烃为原料,聚烯烃材料具有较高的强度和良好的化学稳定性,但其作为一种热塑性材料,在高温条件下变形严重。当锂离子电池温度在外部或者内部因素作用下升高,隔膜会发生热收缩,这是就有可能造成正负极短路,导致事故的发生。
3.为了解决上述问题,中国专利cn1969407a、cn102306726a提出用pvdf
‑
hfp 作为胶黏剂和al2o3、batio3等无机填料配成浆料涂覆在聚烯烃隔膜上,大大提高了隔膜的耐热性和吸收保持电解液的能力。
4.中国专利cn103000848a公开了一种含水性胶黏剂、无机分体和其他水性助剂的涂覆层的复合隔膜。能有效的提高聚烯烃隔膜的耐热性。
5.上述方式均能很好的提高隔膜的耐热性能,但是同时也大大提升了隔膜的重量和厚度。
技术实现要素:6.本发明所要解决的技术问题是克服现有技术的缺陷,提供一种全聚合物耐高温隔膜,它在提高其耐热性能的基础上,使得隔膜厚度增加较小,避免了电池体积的过大增加。
7.为了解决上述技术问题,本发明的技术方案是:一种全聚合物耐高温隔膜,它包括隔膜本体,所述隔膜本体是在具有微孔结构的基膜中涂覆耐高温树脂材料形成的,所述基膜的厚度为3μm~20μm,形成的所述隔膜本体的厚度与基膜的厚度之间的增加量≤ 0.2μm,形成的所述隔膜本体在130℃时的热收缩率≤8%。
8.进一步,所述基膜由聚烯烃材质制成。
9.进一步,所述聚烯烃为聚乙烯、聚丙烯、聚丁烯、聚己烯、乙烯
‑
丙烯共聚物、乙烯
‑
丁烯共聚物、乙烯
‑
己稀共聚物的至少一种。
10.进一步,所述基膜的参数被配置为:透气值≤200s/100cc;和/或微孔曲折度为 1.0
‑
2.5;和/或孔径大于45nm;和/或130℃热收缩率≤30%。
11.进一步,所述隔膜本体的参数还被配置为:透气值≤400s/100cc;和/或面密度相较于基膜的面密度增加量≥25%。
12.进一步,所述耐高温树脂材料为聚酰亚胺、聚醚酰亚胺,聚砜以及纤维素中的至少一种。
13.进一步,所述耐高温树脂材料涂覆于所述基膜的至少一表面上和/或所述基膜的微孔结构中。
14.进一步,所述耐高温树脂材料是通过溶液状态转移到基膜中的。
15.进一步,所述溶液状态中,混合所述耐高温树脂材料的溶剂为低沸点溶剂。
16.进一步,所述溶剂为甲醇、乙醇、二氯甲烷、氯仿、丙酮、乙醚、石油醚、正己烷、四氢呋喃中的至少一种。
17.进一步,溶液质量浓度≥3%。
18.为了简化工艺步骤,本发明还提供了一种全聚合物耐高温隔膜的制备方法,方法的步骤中含有:
19.制备耐高温树脂溶液和具有微孔结构的基膜;
20.将基膜在耐高温树脂溶液中浸涂,然后干燥,即得到全聚合物耐高温隔膜;其中,
21.制备耐高温树脂溶液的步骤为:将耐高温树脂材料溶解于溶剂中,得到耐高温树脂溶液。
22.进一步,制备具有微孔结构的基膜的步骤为:将聚烯烃与石蜡油混合后进行密炼、挤出、冷却铸片、拉伸、萃取,制得基膜。
23.采用了上述技术方案后,本发明制备得到的全聚合物耐高温隔膜,在膜厚增加较小,甚至不增加的条件下,保持较低的透气值,较低的热收缩率,一方面可减少电池短路的风险,另一方面避免了现有技术中为了提高耐热性能而导致的电池的体积过多增加的现象,并且原料易得,工艺简单。
附图说明
24.图1为本发明的对比例1和实施例1的孔径分布图;
25.图2为本发明的对比例1和实施例1的tma数据图;
26.图3为本发明的对比例1的sem图;
27.图4为本发明的实施例1的sem图。
具体实施方式
28.为了使本发明的内容更容易被清楚地理解,下面根据具体实施例并结合附图,对本发明作进一步详细的说明。
29.实施例1
30.s1、将pe与石蜡油(质量比为3:1)混合后进行密炼,230℃混炼10min,挤出,冷却铸片,制得含油基片,含油基片经过第一次双向拉伸(拉伸倍率为双向各7倍)制得含油基膜,二氯甲烷萃取,干燥,进行第二次双向拉伸(拉伸倍率为双向各2.5倍) 制得面密度为3.5g/m2,孔径为73.2nm,透气值为25s/100cc,微孔曲折度为1.1的基膜;
31.s2、将聚醚酰亚胺与二氯甲烷按照质量比为5:95混合,搅拌溶解,得到浸涂溶液;
32.s3、将步骤s1中得到的基膜在步骤s2中得到的浸涂溶液中浸涂,干燥后即得到隔膜。
33.制得的隔膜的面密度为5.8g/m2,面密度增加65.7%。
34.基膜厚度为8.7μm,浸涂后隔膜厚度为8.7μm,厚度几乎没有增加,符合设计要求。
35.实施例2
36.与实施例1不同的是,第二次双拉倍率为双向各2倍,基膜面密度为4.0g/m2,孔径
为63.2nm,微孔曲折度为1.5,制得隔膜。
37.制得的隔膜的面密度为6.0g/m2,面密度增加50%。
38.基膜厚度为8.7μm,浸涂后隔膜厚度为8.8μm,厚度增加了0.1μm,符合设计要求。
39.实施例3
40.与实施例1不同的是,第二次双拉倍率为双向各1.5倍,基膜面密度为4.3g/m2,孔径为58.7nm,微孔曲折度为1.8,制得隔膜。
41.制得的隔膜的面密度为6.3g/m2,面密度增加46.5%。
42.基膜厚度为8.7μm,浸涂后隔膜厚度为8.8μm,厚度增加了0.1μm,符合设计要求。
43.实施例4
44.与实施例1不同的是,耐高温树脂材料为聚砜,制得隔膜。
45.制得的隔膜的面密度为5.5g/m2,面密度增加57.1%。
46.基膜厚度为8.7μm,浸涂后隔膜厚度为8.9μm,厚度增加了0.2μm,符合设计要求。
47.实施例5
48.与实施例1不同的是,耐高温树脂材料为聚芳砜,制得隔膜。
49.制得的隔膜的面密度为5.6g/m2,面密度增加60%。
50.基膜厚度为8.7μm,浸涂后隔膜厚度为8.8μm,厚度增加了0.1μm,符合设计要求。
51.对比例1
52.将pe与石蜡油(质量比为3:1)混合后进行密炼,230℃混炼10min,挤出,冷却铸片,制得含油基片,所述含油基片经过第一次双向拉伸(拉伸倍率为双向各7倍)制得含油基膜,二氯甲烷萃取,干燥,进行第二次双向拉伸(拉伸倍率为双向各2.5倍) 制得面密度为3.5g/m2,孔径为73.2nm,微孔曲折度为1.2的隔膜。
53.对比例2
54.与实施例1不同的是,聚醚酰亚胺与二氯甲烷的质量比为1:99,制得隔膜。
55.对比例3
56.s1、将pe与石蜡油(质量比为3:1)混合后进行密炼,230℃混炼10min,挤出,冷却铸片,制得含油基片,所述含油基片经过第一次双向拉伸(拉伸倍率为双向各7倍) 制得含油基膜,二氯甲烷萃取,干燥,制得面密度为5.5g/m2,孔径为42nm,微孔曲折度为2.3的隔膜;
57.s2、将聚醚酰亚胺与二氯甲烷按照质量比为5:95混合,搅拌溶解,得到浸涂溶液;
58.s3、将步骤s1中得到的基膜在步骤s2中得到的浸涂溶液中浸涂,干燥后即得到隔膜。
59.下面对按照实施例1
‑
6及对比例1
‑
3方法制得的隔膜进行测试,结果如下:
[0060][0061]
通过上述表格数据可知,实施例1与对比例1相比,膜厚基本相同,面密度增加, sem显示表面微孔结构清晰可见,表明浸涂后耐高温树脂材料存在在微孔内部,同时孔径整体向小孔方向移动,表明耐高温树脂材料对隔膜经络进行包覆,造成孔径变小,透气有所增加。130℃热收缩下降明显,达到5.3%,tma数据也表明收缩改善明显,并且破膜温度也有所提升。其中,对比例1和实施例1的孔径分布具体参见图1;对比例1和实施例1的tma数据具体参见图2;对比例1的sem图具体参见图3;实施例 1的sem图具体参见图4。
[0062]
对比例2数据表明,当溶液浓度较低时,面密度增加较小,热收缩改善效果不明显。
[0063]
对比例3数据表明,对于孔径较小的隔膜,浸涂后虽然热收缩改善,但耐高温树脂材料完全填充微孔,透气增加过大,造成堵孔的发生。
[0064]
在本实施例中,热收缩率:将纵/横(纵向md,沿隔膜长度方向;横向td,指与 md水平垂直方向)方向上具有一定尺寸的隔膜样品置入恒温箱加热至特定温度,测量加热前后隔膜纵/横(md/td)方向上尺寸变化率即为热收缩率。
[0065]
透气值:指隔膜允许气体通过的程度,采用测量单位气体体积(100cc)在特定压力(0.05mpa)下透过隔膜所需时间来获得。
[0066]
孔径:指聚烯烃微孔膜中微孔的直径,通过孔径分析仪进行测试。
[0067]
微孔曲折度:指聚烯烃微孔膜中微孔通道的曲折程度,通过电化学工作站进行测试,并计算得到。
[0068]
厚度:采用gb/t 6672
‑
2001iso 4593:1993标准,使用三丰测厚仪进行厚度测试,多次测试取平均值,三丰测厚仪的精度可达0.1μm。
[0069]
面密度:指单位面积隔膜的重量,单位为g/m2,通过精密天平进行测试并计算得到。
[0070]
以上所述的具体实施例,对本发明解决的技术问题、技术方案和有益效果进行了进一步详细说明,所应理解的是,以上所述仅为本发明的具体实施例而已,并不用于限制本发明,凡在本发明的精神和原则之内,所做的任何修改、等同替换、改进等,均应包含在本发明的保护范围之内。