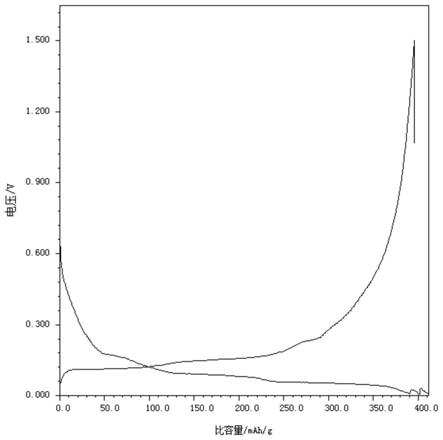
1.本发明属于电池技术领域,尤其涉及一种电池活性层的制备方法、电池极片和应用。
背景技术:2.随着新能源汽车的快速发展,对车用动力电池能量密度以及安全性能的要求不断提升。为实现动力电池能量密度的进一步突破,寻找高比容量正/负极材料成为动力电池开发的重点。但是目前锂离子电池主要以石墨作为负极,而石墨类负极材料的比容量极限约为372mah/g,基于这类负极材料已经难以进一步提高锂离子电池的能量密度,难以适应市场对更高能量密度锂离子电池的需求,因此越来越多的高比容量材料应用到极片中。
3.因此,负极预锂技术成为一种可以提高负极首效和容量的有效方式,目前越来越多的公司和科研院所在做这方面的研究和技术突破。但是常规负极预锂技术存在难度大,危险性高,或是成本太高等问题,目前难以大规模推广应用。
4.cn108288690a公开了一种锂固态电池的负极及其制备方法和应用,所述负极包括负极集流体和负载在该负极集流体上的负极材料,其中,所述负极材料包括:含金属锂的复合负极活性物质、导电添加剂和粘结剂。将该发明提供的负极用于锂固态电池中,可以提高锂离子电池的能量密度和安全性能,并且由于所述负极有效缓解了材料粉化和界面接触等问题,制备成的锂固态电池比使用纯金属锂作为负极的锂固态电池具有更好的循环性能。
5.cn112349956a公开了一种固态电池及其制作方法,包括如下步骤:将正极活性物质、导电剂、粘结剂、锂盐混合均匀后,溶解于有机溶剂中,得到正极浆料,采用磁力搅拌后,将浆料涂布于铝箔上,经过真空烘干、压片等步骤后得到正极;将锂盐加入到溶剂中,搅拌均匀后,依次加入聚合物材料、无机填料,搅拌均匀后得到混合浆料;将混合浆料涂覆于纳米纤维膜上,经过静置、真空干燥等步骤后得到复合电解质膜;将复合电解质浆料涂覆于负极表面,待溶剂烘干后得到负极。将正极、固态电解质、负极组装后得到固态电池。采用该方法制得的固态电池,能够有效的增加电解质与电极界面的相容性,且能够增加电解质的力学性能,有效的改善负极析锂问题。
6.现有技术中,固态电池的极片存在制备工艺复杂、成本高和安全性能低等问题,因此如何在保证固态电池的极片具有制备工艺简单的情况下,还能够保证成本低和安全性能高,成为目前迫切需要解决的问题。
技术实现要素:7.针对现有技术存在的不足,本发明的目的在于提供一种电池活性层的制备方法、电池极片和应用,利用干法混合的活性材料与导电剂混合后,再加入纤维化粘结剂进行纤维化处理,结合碳包覆的预锂材料,使极片具有柔软和平整的特点,提高电池的倍率性能。
8.为达此目的,本发明采用以下技术方案:
9.第一方面,本发明提供了一种电池活性层的制备方法,所述电池活性层的制备方
法包括:
10.将活性材料和导电剂干法混合后,加入纤维化粘结剂并进行纤维化处理,干法工艺得到的混合物料进行辊压成膜后,形成所述的电池活性层;所述活性材料中包括碳包覆的预锂材料。
11.本发明通过加入纤维化粘结剂,与活性材料和导电剂一起进行纤维化处理,结合碳包覆的预锂材料,由于预锂材料表面包覆了一层碳,表面光滑,利用粘结剂形成的纤维进一步地改善了锂硅合金的表面物理性能,制备的负极极片光滑柔软,表面平整,改善了极片的成膜效果,提高了补锂负极的倍率性能,避免了预锂材料颗粒大,硬度硬,锂析出后附在负极形成枝晶,导致表面局部变高,刺穿了隔膜,形成微短路,导致充电曲线异常的问题。此外,本发明无需惰性气体进行保护,在混料阶段加入碳包覆的预锂材料,操作简单,易于工业化,与石墨负极相比,具有首效高、容量高的特点,可用作高能量密度电池的制备。
12.需要说明的是,本发明对集流体的材质不做具体要求和特殊限定,本领域技术人员可根据设计要求合理选择集流体,例如为涂碳铜箔。
13.作为本发明的一个优选技术方案,所述制备方法在干燥环境下进行。
14.优选地,所述活性材料和导电剂干法混合过程中还加入非纤维化粘结剂。
15.优选地,所述非纤维化粘结剂包括聚偏氟乙烯、羧甲基纤维素或丁苯橡胶中的一种或至少两种的组合。
16.优选地,所述非纤维化粘结剂的质量为混合物料的0~10%,例如为0%、1%、2%、3%、4%、5%、6%、7%、8%、9%或10%,进一步优选为0.5~5%。
17.本发明通过采用非纤维化粘结剂与纤维化粘结剂进行配合使用,其中非纤维化粘结剂在热辊压时受热熔化变成熔融态覆盖在活性材料表面,改善活性材料的表面物理性能,能很好地粘住导电剂,形成良好的导电通路,提高导电率;纤维化粘结剂通过纤维化后形成丝状纤维能将不同的活性材料质和导电剂等粘接在一起,形成整体的块状或片状固体。通过两种粘结剂的不同粘接形式,实现均匀稳定的粘连效果,有效避免混合过程中黏连结块等问题的发生,进一步地提高极片的柔软性和成膜效果。并且与传统的只使用非纤维化粘结剂必须加入溶剂来促发粘结剂的粘接作用相比,加入纤维化粘结剂来起粘接作用,可以不用加入溶剂,省去了溶剂回收及烘干过程,简化了制备工艺,节约了成本。
18.优选地,所述纤维化粘结剂包括聚四氟乙烯、聚酰亚胺、聚丙烯或聚乙烯中的一种或至少两种的组合。
19.优选地,所述纤维化粘结剂的质量为混合物料的0.1~30%,例如为0.1%、1%、2%、4%、6%、8%、10%、12%、14%、16%、18%、20%、22%、24%、26%、28%或30%,进一步优选为0.5~10%。
20.本发明通过设置纤维化粘结剂的质量为混合物料的0.1~30%,进一步优选为0.5~10%,在保证极片柔软性和平整性的情况下,使极片具有良好成膜效果,若质量低于混合物料的0.1%,则纤维化粘结剂产生的纤维化拉丝不足,活性材料之间粘结效果差,导致极片的成膜效果不好;若质量高于混合物料的30%,则纤维化粘结剂加入量过高,影响活性材料占比,进而影响电池性能。
21.作为本发明的一个优选技术方案,所述纤维化处理包括研磨、球磨或脱泡中的一种或至少两种的组合,进一步优选为研磨,所述纤维化处理将纤维化粘结剂纤维化,并与活
性材料和导电剂形成块状或片状结构的混合物料。
22.本发明中纤维化处理方式为研磨,是一种比高速搅拌、气流粉碎等更简单容易,同时纤维化效果更好的方式。
23.作为本发明的一个优选技术方案,所述预锂材料包括锂硅合金、硅或氧化亚硅中的一种或至少两种的组合,进一步优选为锂硅合金。
24.本发明采用锂硅合金作为补锂添加剂,其理论容量达1800mah/g以上,但是锂硅合金比较活泼,容易与水发生剧烈反应,发生安全问题,本发明通过干法工艺有效避免了锂硅合金环境要求高和安全性差的问题。
25.优选地,所述活性材料中碳包覆的预锂材料的质量占比为0.1~60%,例如为0.1%、1%、5%、10%、20%、30%、40%、50%、60%,进一步优选为5~40%。
26.优选地,所述碳包覆的预锂材料中包覆碳的质量含量为0.5~50%,例如为0.5%、1%、5%、10%、15%、20%、25%、30%、35%、40%、45%或50%,进一步优选为1~10%。
27.优选地,所述锂硅合金中li:si的原子数量比为(0~4.4):1,例如为0.4:1、0.8:1、1.2:1、1.6:1、2.0:1、2.4:1、2.8:1、3.2:1、3.6:1、4.0:1或4.4:1。
28.优选地,所述锂硅合金包括li
4.4
si、li
3.25
si或li
1.71
si中的一种或至少两种的组合。
29.作为本发明的一个优选技术方案,所述活性材料为负极活性材料,所述负极活性材料中还包括石墨。
30.优选地,所述负极活性材料中石墨的质量占比为40~95%,例如为40%、45%、50%、55%、60%、65%、70%、75%、80%、85%、90%或95%。
31.本发明通过设置负极活性材料中石墨的质量占比为40~95%,从而具有降低锂硅合金的膨胀问题、提高极片能量密度的优点,若低于40%,则存在锂硅合金的膨胀问题;若高于95%,则存在能量密度提升不明显的问题。
32.作为本发明的一个优选技术方案,所述活性材料的质量为混合物料的25~99.9%,例如为25%、30%、35%、40%、45%、50%、55%、60%、65%、70%、75%、80%、85%、90%、95%或99.9%,进一步优选为87.5~98.5%。
33.优选地,所述导电剂的质量为混合物料的0~5%,例如为0%、0.5%、1.0%、1.5%、2.0%、2.5%、3.0%、3.5%、4.0%、4.5%或5.0%,进一步优选为1~2.5%。
34.优选地,所述导电剂包括乙炔黑、super
‑
p、碳纳米管、碳纤维、科琴黑、石墨导电剂、石墨烯、活性炭、多孔碳中的一种或至少两种的组合。
35.作为本发明的一个优选技术方案,所述辊压的方式包括热辊压,所述混合物料辊压后形成电池活性层。
36.优选地,所述热辊压的温度为25~200℃,例如为25℃、30℃、40℃、60℃、80℃、100℃、120℃、140℃、160℃、180℃或200℃,进一步优选为90~160℃。
37.作为本发明的一个优选技术方案,所述制备方法具体包括以下步骤:
38.(ⅰ)在干燥环境下,将活性材料、导电剂和非纤维化粘结剂干法混合后,再加入纤维化粘结剂进行研磨纤维化处理,使纤维化粘结剂纤维化,并与活性材料和导电剂研磨形成块状或片状结构的混合物料,其中,活性材料中碳包覆的锂硅合金的质量占比为0.1~100%,碳包覆的锂硅合金中包覆碳的质量含量为1~10%,锂硅合金的li:si原子数量比为
(0~4.4):1;非纤维化粘结剂的质量为混合物料的0.5~5%,纤维化粘结剂的质量为混合物料的0.5~10%,活性材料的质量为混合物料的87.5~98.5%,导电剂的质量为混合物料的1~2.5%;
39.(ⅱ)将混合物料在90~160℃下进行热辊压形成电池活性层。
40.第二方面,本发明提供了一种电池极片,所述电池极片包括集流体以及位于集流体至少一侧表面的电池活性层,所述电池活性层采用第一方面所述的电池活性层的制备方法制备得到。
41.需要说明的是,集流体与电池活性层的复合方式为热辊压,优选复合过程中热辊压的温度为25~200℃,例如为25℃、30℃、40℃、60℃、80℃、100℃、120℃、140℃、160℃、180℃或200℃。
42.作为本发明的一个优选技术方案,所述电池极片的厚度为30~500μm,例如为30μm、50μm、100μm、150μm、200μm、250μm、300μm、350μm、400μm、450μm或500μm。
43.第三方面,本发明提供了一种固态电池,所述固态电池包括正极、负极和隔膜,所述负极采用第二方面所述的电池极片。
44.本发明所述的数值范围不仅包括上述例举的点值,还包括没有例举出的上述数值范围之间的任意的点值,限于篇幅及出于简明的考虑,本发明不再穷尽列举所述范围包括的具体点值。
45.与现有技术相比,本发明的有益效果为:
46.本发明通过加入纤维化粘结剂,与活性材料和导电剂一起进行纤维化处理,结合碳包覆的预锂材料,由于预锂材料表面包覆了一层碳,表面光滑,利用粘结剂形成的纤维进一步地改善了锂硅合金的表面物理性能,制备的负极极片光滑柔软,表面平整,改善了极片的成膜效果,提高了补锂负极的倍率性能,避免了预锂材料颗粒大,硬度硬,锂析出后附在负极形成枝晶,导致表面局部变高,刺穿了隔膜,形成微短路,导致充电曲线异常的问题。此外,本发明无需惰性气体进行保护,在混料阶段加入碳包覆的预锂材料,操作简单,易于工业化,与石墨负极相比,具有首效高、容量高的特点,可用作高能量密度电池的制备。
附图说明
47.图1为实施例1在0.1c下充放电曲线图;
48.图2为对比例1在0.1c下充放电曲线图;
49.图3为实施例1在1c下充放电曲线图;
50.图4为对比例2在1c下充放电曲线图。
具体实施方式
51.为更好地说明本发明,便于理解本发明的技术方案,下面对本发明进一步详细说明。但下述的实施例仅是本发明的简易例子,并不代表或限制本发明的权利保护范围,本发明保护范围以权利要求书为准。
52.下面通过具体实施方式来进一步说明本发明的技术方案。
53.实施例1
54.本实施例提供了一种电池活性层的制备方法,所述的制备方法具体包括以下步
骤:
55.(ⅰ)在干燥环境下,将8.7g石墨、1g碳包覆的锂硅合金和0.1g聚偏氟乙烯干法混合后,再加入0.2g聚四氟乙烯进行研磨纤维化处理,使聚四氟乙烯纤维化,并与活性材料研磨形成块状或片状结构的混合物料,其中,活性材料中碳包覆的锂硅合金的质量占比为10.3%,碳包覆的锂硅合金中包覆碳的质量含量为5%,锂硅合金为li
3.25
si;聚偏氟乙烯的质量为混合物料的1%,聚四氟乙烯的质量为混合物料的2%,活性材料的质量为混合物料的97%;
56.(ⅱ)将混合物料在100℃下进行热辊压形成电池活性层。
57.本实施例还提供了一种电池极片,所述电池极片由上述电池活性层在100℃下与集流体热辊压复合形成200μm的电池极片。
58.实施例2
59.本实施例提供了一种电池活性层的制备方法,所述的制备方法具体包括以下步骤:
60.(ⅰ)在干燥环境下,将1g石墨、7.7g碳包覆的锂硅合金、0.2g乙炔黑和0.1g羧甲基纤维素干法混合后,再加入1g聚酰亚胺进行研磨纤维化处理,使聚酰亚胺纤维化,并与活性材料和导电剂研磨形成块状或片状结构的混合物料,其中,活性材料中碳包覆的锂硅合金的质量占比为88.5%,碳包覆的锂硅合金中包覆碳的质量含量为10%,锂硅合金为li
1.71
si;羧甲基纤维素的质量为混合物料的1%,聚酰亚胺的质量为混合物料的10%,活性材料的质量为混合物料的87%,导电剂的质量为混合物料的2%;
61.(ⅱ)将混合物料在90℃下进行热辊压形成电池活性层。
62.本实施例还提供了一种电池极片,所述电池极片由上述电池活性层在90℃下与集流体热辊压复合形成50μm所述的电池极片。
63.实施例3
64.本实施例提供了一种电池活性层的制备方法,所述的制备方法具体包括以下步骤:
65.(ⅰ)在干燥环境下,将9g碳包覆的锂硅合金、0.5g碳纳米管和0.5g聚偏氟乙烯干法混合后,再加入0.5g聚丙烯进行研磨纤维化处理,使聚丙烯纤维化,并与活性材料和导电剂研磨形成块状或片状结构的混合物料,其中,活性材料中碳包覆的锂硅合金的质量占比为100%,碳包覆的锂硅合金中包覆碳的质量含量为1%,锂硅合金为li
4.4
si;聚偏氟乙烯的质量为混合物料的5%,聚丙烯的质量为混合物料的5%,活性材料的质量为混合物料的90%,导电剂的质量为混合物料的5%;
66.(ⅱ)将混合物料在110℃下进行热辊压形成电池活性层。
67.本实施例还提供了一种电池极片,所述电池极片由上述电池活性层在110℃下与集流体热辊压复合形成500μm所述的电池极片。
68.实施例4
69.本实施例提供了一种电池活性层的制备方法,所述的制备方法具体包括以下步骤:
70.(ⅰ)在干燥环境下,将0.7g石墨、5g碳包覆的锂硅合金、0.3g石墨烯和1g聚偏氟乙烯干法混合后,再加入3g聚乙烯进行研磨纤维化处理,使聚乙烯纤维化,并与活性材料和导
电剂研磨形成块状或片状结构的混合物料,其中,活性材料中碳包覆的锂硅合金的质量占比为87.7%,碳包覆的锂硅合金中包覆碳的质量含量为40%,锂硅合金为li
2.2
si;聚偏氟乙烯的质量为混合物料的10%,聚乙烯的质量为混合物料的30%,活性材料的质量为混合物料的57%,导电剂的质量为混合物料的3%;
71.(ⅱ)将混合物料在110℃下进行热辊压形成电池活性层,
72.本实施例还提供了一种电池极片,所述电池极片由上述电池活性层在100℃下与集流体热辊压复合形成300μm所述的电池极片。
73.实施例5
74.本实施例提供了一种电池活性层的制备方法,所述的制备方法具体包括以下步骤:
75.(ⅰ)在干燥环境下,将8g石墨、0.5g碳包覆的锂硅合金、0.2g石墨烯和0.6g聚偏氟乙烯干法混合后,再加入0.7g聚乙烯进行研磨纤维化处理,使聚乙烯纤维化,并与活性材料和导电剂研磨形成块状或片状结构的混合物料,其中,活性材料中碳包覆的锂硅合金的质量占比为5.8%,碳包覆的锂硅合金中包覆碳的质量含量为20%,锂硅合金为li
2.8
si;聚偏氟乙烯的质量为混合物料的6%,聚乙烯的质量为混合物料的7%,活性材料的质量为混合物料的85%,导电剂的质量为混合物料的2%;
76.(ⅱ)将混合物料在110℃下进行热辊压形成电池活性层。
77.本实施例还提供了一种电池极片,所述电池极片由上述电池活性层在100℃下与集流体热辊压复合形成300μm所述的电池极片。
78.实施例6
79.本实施例提供了一种电池活性层的制备方法,与实施例1相比,其区别在于,不加入聚偏氟乙烯,其余加入量与实施例1完全相同。
80.实施例7
81.本实施例提供了一种电池活性层的制备方法,与实施例1相比,其区别在于,聚四氟乙烯的加入量为1.3g,即聚四氟乙烯的质量为混合物料的11.7%,其余加入量与实施例1完全相同。
82.实施例8
83.本实施例提供了一种电池活性层的制备方法,与实施例1相比,其区别在于,聚四氟乙烯的加入量为4.5g,即聚四氟乙烯的质量为混合物料的31.5%,其余加入量与实施例1完全相同。
84.实施例9
85.本实施例提供了一种电池活性层的制备方法,与实施例1相比,其区别在于,活性材料为3.7g石墨和6g碳包覆的锂硅合金,其余加入量与实施例1完全相同。
86.实施例10
87.本实施例提供了一种电池活性层的制备方法,与实施例1相比,其区别在于,活性材料为8.8g石墨和0.1g碳包覆的锂硅合金,其余加入量与实施例1完全相同。
88.对比例1
89.本对比例提供了一种电池活性层的制备方法,与实施例1相比,其区别在于,将1g碳包覆的锂硅合金替换为1g石墨,其余参数与实施例1完全相同。
90.对比例2
91.本对比例提供了一种电池活性层的制备方法,与实施例1相比,其区别在于,将1g碳包覆的锂硅合金替换为1g未经碳包覆的锂硅合金,其余参数与实施例1完全相同。
92.本发明还提供了一种固态电池,所述的固态电池中极片采用上述实施例制备得到的电池极片。
93.将上述实施例和对比例中的极片组装对锂扣电,隔膜为pe膜,电解液为lipf6(在电解液中浓度为1mol/l)溶于体积比为1:1:1的碳酸乙烯酯(ec)/碳酸二甲酯(dec)/碳酸甲乙酯(emc)的混合液中,在0.1c下进行充放电,然后在0.5c,1c下充放电,测试倍率性能。测试结果如表1所示。实施例1在0.1c下充放电曲线图如图1所示,对比例1在0.1c下充放电曲线图如图2所示,实施例1在1c下充放电曲线图如图3所示,对比例2在1c下充放电曲线图如图4所示。
94.表1
[0095][0096]
通过上表可以看出:
[0097]
(1)实施例1与实施例6相比,实施例1的测试数据优于实施例6,由此可以看出,本发明通过采用非纤维化粘结剂与纤维化粘结剂进行配合使用,其中非纤维化粘结剂在热辊压时受热熔化变成熔融态覆盖在活性材料表面,改善活性材料的表面物理性能,能很好地粘住导电剂,形成良好的导电通路,提高导电率;纤维化粘结剂通过纤维化后形成丝状纤维
能将不同的活性材料和导电剂等粘接在一起,形成整体的块状或片状固体。通过两种粘结剂的不同粘接形式,实现均匀稳定的粘连效果,有效避免混合过程中黏连结块等问题的发生,进一步地提高极片的柔软性和成膜效果。并且与传统的只使用非纤维化粘结剂必须加入溶剂来促发粘结剂的粘接作用相比,加入纤维化粘结剂来起粘接作用,可以不用加入溶剂,省去了溶剂回收及烘干过程,简化了制备工艺,节约了成本。
[0098]
(2)实施例1与实施例7、8相比,实施例1的测试数据优于实施例7、8,由此可以看出,本发明通过设置纤维化粘结剂的质量为混合物料的0.1~30%,进一步优选为0.5~10%,在保证极片柔软性和平整性的情况下,使极片具有良好成膜效果,若质量低于混合物料的0.1%,则纤维化粘结剂产生的纤维化拉丝不足,活性材料之间粘结效果差,导致极片的成膜效果不好;若质量高于混合物料的30%,则纤维化粘结剂加入量过高,影响活性材料占比,进而影响电池性能。
[0099]
(3)实施例1与实施例9、10相比,实施例1的测试数据优于实施例9、10,由此可以看出,本发明通过设置负极活性材料中石墨的质量占比为40~95%,从而具有降低锂硅合金的膨胀问题、提高极片能量密度的优点,若低于40%,则存在锂硅合金的膨胀问题;若高于95%,则存在能量密度提升不明显的问题。
[0100]
(4)实施例1与对比例1、2相比,实施例1的充电比容量、放电比容量和首效优于对比例1,实施例1的首效、0.5c/0.1c和1c/0.1c的性能优于对比例2,由此可以看出,本发明通过加入纤维化粘结剂,与活性材料和导电剂一起进行纤维化处理,结合碳包覆的预锂材料,由于预锂材料表面包覆了一层碳,表面光滑,利用粘结剂形成的纤维进一步地改善了锂硅合金的表面物理性能,制备的负极极片光滑柔软,表面平整,改善了极片的成膜效果,提高了补锂负极的倍率性能,避免了预锂材料颗粒大,硬度硬,锂析出后附在负极形成枝晶,导致表面局部变高,刺穿了隔膜,形成微短路,导致充电曲线异常的问题。此外,本发明无需惰性气体进行保护,在混料阶段加入碳包覆的预锂材料,操作简单,易于工业化,与石墨负极相比,具有首效高、容量高的特点,可用作高能量密度电池的制备。
[0101]
申请人声明,以上所述仅为本发明的具体实施方式,但本发明的保护范围并不局限于此,所属技术领域的技术人员应该明了,任何属于本技术领域的技术人员在本发明揭露的技术范围内,可轻易想到的变化或替换,均落在本发明的保护范围和公开范围之内。