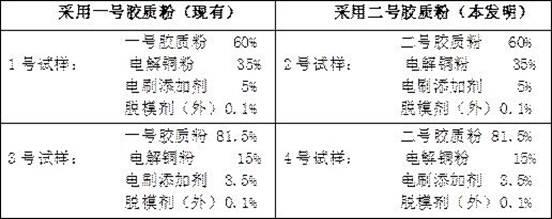
1.本发明涉及电刷技术领域,具体涉及电刷的制备方法。涉及包含电碳制品生产中各类机电用碳,以及机械用碳混合工序中的碳石墨材料表面涂覆处理工艺和方法、步骤。
背景技术:2.电刷是用于电机中与换向器或滑环接触而形成电连接的一种导电部件,作为导入导出电流的滑动接触体,其导电、导热及润滑性能良好,有一定的机械强度,具有抑制换向火花的本能。
3.通常的机电用电刷碳制品,其工艺方法基本上是用沥青或人造树脂粘结剂对石墨粉进行涂覆处理,以确保材料的成型性,达到改善石墨粉材料的可成型性的目的。但是,随着市场需求的变化,对电刷性能要求越来越高,同时由于市场竞争激烈,对产品成本要求也越来越低。传统的工艺方法很难满足要求。
4.中国专利公告公开了申请号为201210415962.4、申请日为2012.10.26、发明为一种电刷的制作方法的专利申请,包含以下步骤:步骤一:选取原材料,分别为二硫化铜、石墨粉、树脂、酒精、粘结剂、润滑剂;步骤二:将二硫化铜、石墨粉、树脂、酒精、粘结剂、润滑剂按照重量比为1:5:3:2:1:1的比例放在搅拌机中混合;步骤三:将上述混合物放在粉碎机中粉碎成粉末状,筛选出精细的粉末,然后放在锅炉中焙烧,制成半成品,所述温度为200℃
‑
300℃;步骤四:将半成品经过石墨化处理,检测合格品;步骤五:机械加工,得到成品。因此本发明方法简单、易操作抗电子干扰能力强。上述方法制备的电刷仍然存在性能与成本方面的问题。
技术实现要素:5.针对现有技术中存在的问题,本发明的一个目的在于提供一种用中温沥青对碳石墨原料涂覆处理的方法进行改进,使得涂覆效果更好,成本低,同时制成的碳刷使用性能更优异的制备方法。
6.为达到以上目的,本发明采用如下技术方案。
7.体步骤如下。
8.一种电刷的制备方法,其特征在于,它包括如下步骤。
9.a、首先制备一阶段胶质粉,其步骤为:(一)混合。
10.a,将195石墨粉、cpc7599石墨粉、二硫化钼、氧化铈按顺序加入,搅拌50
‑
80分钟;同时加热料温至135
±
5℃;其中按质量份比例配比。
11.195石墨粉58
‑
63%。
12.二硫化钼4
‑
6%。
13.氧化铈0.5
‑
1.5%。
14.中温沥青粉30
‑
35%备用。
15.b,开盖,均匀加入备用的沥青粉;闭盖继续搅拌70
‑
100分钟,同时加热料温至165
±
5℃。
16.c,开盖,继续搅拌1
‑
3小时;然后停止加热,搅拌至物料呈5~15cm粒径颗粒后,卸料。
17.(二)烘干。
18.将物料放入烘箱,240
±
10℃烘干7
‑
9小时。
19.(三)打粉、过筛、混均。
20.a,将物料用万能打粉机打粉,过70目筛。
21.b,将筛下料粉混均45~60分钟。
22.b、制备二阶段胶质粉,其步骤为。
23.(一)混合。
24.a,将干粉按顺序加入,闭盖搅拌70
‑
100分钟;同时加热料温至145
±
5℃;其中。
25.一阶段胶质料粉70
‑
75%。
26.cpc7599石墨粉15
‑
18%。
27.碳化硅粉0.2
‑
0.4%。
28.中温沥青粉8
‑
12%。
29.b,开盖,继续搅拌。加热料温至155
±
5℃,维持1
‑
2.5小时;然后卸料,冷却7
‑
9小时。
30.(二)打粉、过筛、混均。
31.a,用万能打粉机打粉,过70目筛。
32.b,筛下料粉混均45~60分钟。
33.制备金属石墨压粉:按质量份配制压粉,并充分混均。
34.二阶段胶质粉55
‑
86%。
35.电解铜粉13
‑
40%。
36.电刷添加剂3
‑
6%上述组份之和为100%。
37.另外增加脱模剂0.08
‑
0.12%。
38.d、高温烧结炉烧结成型。
39.优先的,所述制备一阶段胶质粉步骤a的混合步骤a中。
40.195石墨粉61.8%。
41.二硫化钼5%。
42.氧化铈1.2%。
43.中温沥青粉32%。
44.优先的,所述制备二阶段胶质粉步骤b的混合(一)步骤a中。
45.一阶段料粉73%。
46.cpc7599石墨粉16.7%。
47.碳化硅粉0.3%。
48.中温沥青粉10%。
49.优先的,所述制备步骤c中。
50.二阶段胶质粉60%。
51.电解铜粉35%。
52.电刷添加剂5%。
53.另外增加脱模剂0.1%。
54.所述制备步骤a的混合(一)的第b步骤中闭盖继续搅拌时间为90分钟;第a步骤中闭盖搅拌时间为60分钟。
55.所述制备步骤b的混合(一)的第a步骤中闭盖搅拌时间为90分钟。
56.本发明的有益效果是。
57.本发明立足于使用普通石墨原料,控制材料成本;结合使用少量高端材料,帮助提升产品的性能。通过改变生产工艺方法(主要是混合处理方法),采用制备第一阶段胶质粉和第二阶段胶质粉的两步法制备,使制得的产品比传统工艺方法的产品寿命、电气性能等更优越。
具体实施方式
58.下面结合说明书,对本发明的具体实施方式作进一步的描述,使本发明的技术方案及其有益效果更加清楚、明确。下面通过参考描述实施例是示例性的,旨在解释本发明,而不能理解为对本发明的限制。
59.本发明的附加方面和优点将在下面的描述部分中变得明显,或通过本发明的实践了解到。
60.以下结合现有的实施方法和步骤和本发明的方法进行对比,以进一步说明本发明的特点。
61.(一)、传统工艺方法(对照组):一号胶质粉。
62.1、混合。
63.原材料及配比。
64.195石墨粉45.41%。
65.cpc7599石墨粉16.7%。
66.二硫化钼3.65%。
67.氧化铈0.88%。
68.中温沥青粉33.36%。
69.具体操作步骤。
70.a,将195石墨粉、cpc7599石墨粉、二硫化钼、氧化铈按顺序加入,搅拌90分钟。同时加热料温至120~130℃。
71.b,开盖,均匀加入沥青粉。闭盖继续搅拌90分钟,同时加热料温至165
±
5℃。
72.c,开盖,继续搅拌2小时。然后停止加热,搅拌至物料呈5~15cm粒径颗粒后卸料。
73.2、打粉,过筛。
74.a,用万能打粉机打粉。
75.b,料粉过70目筛。
76.(二)、本发明的改进工艺方案:二号胶质粉。
[0077] 1、混合(一阶段)。
[0078]
原材料及配比。
[0079]
195石墨粉61.8%可在58
‑
63%范围内选取。
[0080]
二硫化钼5%可在4%及6%范围内选取。
[0081]
氧化铈1.2%0.5%及1.5%范围内选取。
[0082]
中温沥青32%;中温沥青粉30%及35%范围内选取。
[0083]
具体操作步骤。
[0084]
a,将石墨粉、二硫化钼、氧化铈依次加入,闭盖搅拌60分钟。同时加热料温至135
±
5℃。
[0085]
b,开盖,均匀加入沥青粉,闭盖继续搅拌70
‑
100分钟,本实施例为90分钟。同时加热料温至165
±
5℃。
[0086]
c,开盖,继续搅拌1
‑
3小时2小时。然后停止加热,继续搅拌,至物料呈5~15cm粒径的颗粒,卸料。
[0087]
2、烘干。
[0088]
将物料放入烘箱,240℃烘干7
‑
9小时,本实施例为8小时。
[0089]
3、打粉、过筛、混均。
[0090]
a,将物料用万能打粉机打粉,过70目筛。
[0091]
b,将筛下料粉混均45~60分钟。
[0092]
4、混合(二阶段)。
[0093]
原材料及配比。
[0094]
一阶段胶质料粉73%。
[0095]
cpc7599石墨粉16.7%。
[0096]
碳化硅粉0.3%。
[0097]
中温沥青粉10%。
[0098]
操作步骤。
[0099]
a,将干粉按顺序加入,闭盖搅拌90分钟。同时加热料温至145
±
5℃。
[0100]
b,开盖,继续搅拌。加热料温至155
±
5℃,维持2小时。然后卸料,冷却8小时。
[0101]
5、打粉、过筛、混均。
[0102]
a,用万能打粉机打粉,过70目筛。
[0103]
b,筛下料粉混均45~60分钟。
[0104]
(三),制备金属石墨压粉。
[0105]
需要说明的是,利用二阶段胶质粉制备金属石墨压粉是采用现有技术中的其它组份的常用配方,其配方构成按重量份为。
[0106]
二阶段胶质粉55
‑
86%,电解铜粉13
‑
40%。
[0107]
电刷添加剂3
‑
6%上述组份之和为100%。
[0108]
另外增加脱模剂0.08
‑
0.12%;下面采用具体的组份对比进行详细说明本发明材料性能。
[0109]
1、两组电刷工艺配比方案:
。
[0110]
按照1~4号分组,分别配制压粉,并充分混均。
[0111]
2、采用同一套6x13mm压制模具,压制压力6.5mpa,各压制20只。压制后成型密度如下:。
[0112]
3、将样品用高温烧结炉烧结成型。取样检测理化参数。
[0113]
a,体积密度检查结果(g/cm
³
):。
[0114]
b,电阻率检测结果(ω.m):。
[0115]
c,洛氏硬度检测结果(hr10/392):
。
[0116]
4、理化检测结果。
[0117]
在原材料配比基本相同,烧结工艺一致的情况下,采用普通胶质粉工艺的1号和3号试样、与改变胶质粉制作工艺方法的2号和4号试样,通过对烧结成型后的样品进行理化检测,得到如下结论。
[0118]
a,体积密度。
[0119]
1号试样平均值2.276;2号试样平均值2.35。2号试样的密度比1号试样平均高3.25%。
[0120]
3号试样平均值1.893;4号试样平均值2.016。4号试样的密度比3号试样平均高约6.5%。
[0121]
b,电阻率。
[0122]
1号试样平均值10.116,2号试样平均值2.643。1号试样是2和试样的3.83倍。
[0123]
3号试样平均值15.075,4号试样平均值4.799。3号试样是4号试样的3.14倍。
[0124]
c,洛氏硬度hr10/392。
[0125]
1号试样平均值83.625,2号试样平均值97.25。2号试样比1号试样高16.29%。
[0126]
3号试样平均值68.625,4号试样平均值75.5。4号比3号高10.02%。
[0127]
5、样品实际动态测试结果。
[0128]
我们选取一款两台12v的直流电机,分别装配1号试样碳刷和2号碳刷试样,进行500小时动态实机负载测试;选取一款两台24v直流电机,分别装配3号试样碳刷和试样号碳刷,进行500小时动态实机负载测试,实际结果如下。
[0129]
1号试样,最大磨损:1.26mm,按有效使用长度8mm计算,理论寿命3174小时。
[0130]
2号试样,最大磨损:0.72mm,按有效使用长度8mm计算,理论寿命5555小时。
[0131]
相同试验条件下,2号试样理论寿命比1号试样延长了75%。
[0132]
3号试样,最大磨损:1.05mm,按有效使用长度8mm计算,理论寿命3809小时。
[0133]
4号试样,最大磨损:0.58mm,按有效使用长度8mm计算,理论寿命6896小时。
[0134]
相同试验条件下,4号试样理论寿命比3号试样延长了81%。
[0135]
6、通过以上对比实验,可以得出如下结论。
[0136]
通过工艺方法的改变和革新,我们得出的结果是:在原材料基本相同的条件下,采用新的工艺方法,可以有效的提升电刷材料的性能:一方面,电刷材料的强度提高了,使得材料的磨损大幅降低;另一方面,电刷的电阻率大幅降低,提高电刷的电气性能,同时能有效的抑制因电阻损耗产生的温升。另外,由于新的工艺方法能够有效的降低电刷体的电阻率,因此可以相应的降低金属铜的使用量,增加石墨粉的比例。而石墨粉的自润滑性远优于金属铜,进而对电刷材料自身的减磨起到帮助作用,又有效的提高了电刷的使用寿命,因此
本发明工艺采用现有材料不同工艺,取得了明显的技术效果。
[0137]
需要说明的是,本发明中电刷添加剂、脱模剂均为常规市购,与现有电刷制备中所采用的没有区别,申请人在此不作详述。
[0138]
针对上述利用二阶段胶质粉制备金属石墨压粉的配方中,我们采用二阶段胶质粉55%或86% ,电解铜粉 13%或40% ,电刷添加剂 3%或6% ,与现有技术中的相应试样进行对比,均能得到基本相同的结论。
[0139]
在本发明中,术语“第一”、“第二”仅用于描述目的,而不能理解为指示或暗示相对重要性或隐含指明技术特征的数量。由此,限定有“第一”、“第二”特征可以明示或者隐含包括一个或者多个该特征,在本发明描述中,“至少”的含义是一个或一个以上,除非另有明确具体的限定。
[0140]
通过上述的结构和原理的描述,所属技术领域的技术人员应当理解,本发明不局限于上述的具体实施方式,在本发明基础上采用本领域公知技术的改进和替代均落在本发明的保护范围,本发明的保护范围应由各权利要求项及其等同物限定之。具体实施方式中未阐述的部分均为现有技术或公知常识。