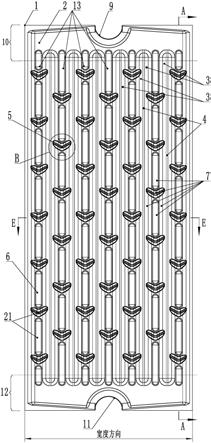
1.本实用新型涉及变压器用散热器加工制造技术领域,特别提供一种散热器用非能动三维均混扰流型散热片。
背景技术:2.运行中的油浸式变压器、电抗器在绕组及铁芯等部件中会产生一定的能量损耗,并转化为热能。该部分热能仅有一小部分会通过变压器以热传导和热对流的方式传递给油箱壁并散发到空气中。而绝大部分热能无法通过变压器自身油箱平壁结构快速有效地散发出去,直接导致变压器油温升提高,进而降低了其绝缘寿命,所以,不得不考量其他更为有效的散热措施来解决油浸式变压器的散热问题。经过近半个世纪的实践和发展,片式散热器已成为解决油浸式变压器、电抗器散热问题的主流措施。特别在低噪声,以onan为主的产品上应用更加广泛。但基于其结构原因,片式散热器总传热系数k 值较低,为此,为了达到散热量要求,往往需要配置大量散热片组。如大型变压器67mva/500kv需要选用片散pc2800-28/520(32)组才能满足散热要求,而该散热片组自身结构尺寸占用了变压器较大周围空间,且成本较高,造成了空间占用和成本较大。因此,在不增加散热器材料成本或在降低其材料成本的前提下,提高散热片的有效散热能力,对现有油浸式变压器用片式散热器应用在变压器行业上具有十分重要的意义,但是,由于片式散热器散热原理中提高散热能力和减小散热片尺寸或减少散热器数量之间本身就是一对矛盾,所以这一瓶颈问题的突破将成为变压器用散热器设计生产的重要技术环节,本实用新型将有效的解决上述技术瓶颈。
技术实现要素:3.本实用新型目的在于提供一种散热器用非能动三维均混扰流型散热片。这种散热器用非能动三维均混扰流型散热片的板材为钢或铝材质薄板,其薄板由动力系统及支撑机械结构驱动成对轧辊模滚压方法制出散热单片的气侧扰流结构和油侧混流结构,再由冲压轧制系统使用平板模制出与多个混流油流通腔对应且过渡连接的分流腔、汇流腔部分的散热单片,由板料输送系统将板料传输到以上工位,完成非能动三维均混扰流型散热片轧制工艺,本实用新型利用带有外侧的气侧扰流结构和内侧的油侧混流结构的散热片制成的变压器用散热器能够在非能动冷却(onan)条件下,使散热片内外部形成三维均混流和扰流状态,同时使散热片内外部的油侧混流场、片间气侧扰流场中的流体进行不断掺混和扰动起到强化传热的作用,继而达到本实用新型散热片比现有散热片的散热能力大幅提高,实现了减少变压器用散热器组数或片数的效果,并且减少散热器占用变压器油箱周围的横向空间,同时减少变压器用油量,降低了变压器制造成本,并且在风机冷却(onaf)条件下同时可以减少风机数量。
4.本实用新型在仅依靠密度差和位置差使介质流动的前提下,设计出散热片外侧的气侧扰流结构,使散热器气侧形成至下而上的分段导向扰流;气侧表面向外散热过程中,散
热片表面的散热气流会从下部向上部在叠加状态中上升散热,在这种情况下,上部散热片表面在散热的同时还会受到来自于散热片下部热气流的影响;在气侧扰流结构的作用下形成分段阻断向上的传热气流,各分段中的传热气流在纵向上两半环形气流导向波峰之间会产生脱离散热器气侧表面的效果,从而避免散热片表面热气流至下而上的在其表面形成温度叠加来提高散热效率,各散热段都在同样的接近环境温度的条件下进行散热,减少了由于温度叠加造成的上部环境温度比下部环境温度高的现象,并且气侧扰流结构中半环形气流导向波峰横向干扰了全部油流散热面气流,使干扰效果发挥最大,在半环形气流导向波峰对上升的表面气流的分流导向作用下,按中华人民共合国机械行业标准jb/t 5347《变压器用片式散热器》规定“自冷式的片间距离不应小于45mm”实际应用中片间距离多以45mm为标准,由于相邻散热片距离较近,所以多个散热片在这种间距条件下的气侧扰流结构,会使相邻散热片气侧之间的气流相互产生干扰,形成散热片间气侧扰流场和油侧混流场,其两者相互作用产生利于散热的流场效应;同时设计出散热器油侧油流通腔的腔体截面和形状都不变的情况下会产生层流状的缓慢对流散热,采用油侧混流结构将层流状改变成混流状,通过对散热器油侧油流通腔在纵向上分段设置了油侧混流结构,使油流通腔上的混流结构处油流流向发生改变、油流通腔内的层外流与层内流出现不断掺混、油流通腔内的各油流层的油流温度通过改变油流方向得到充分掺混、油流内层与外层在混流的状态下通过散热片表面进行散热,从而提高了散热效率;在油流通腔上设计出两半环形对接的环形油流腔,因使油流腔截面积徒增,在重力作用下使油流外层不能继续依附油流腔内壁向下流动、而是脱离腔内壁向下流入油流内层得到内外层的混流,并且在混流结构的环形油流腔作用下使油流腔内的层流几乎全部得到多次混流;在环形油流腔出、入口分别设计有减容混流油流腔使油流方向得到充分掺混,也使内层油流与外层油流得到多次混流,通过以上均混扰流方案来实现散热器对油流通腔内变压器热油快速散热的效果;本实用新型技术方案在不改变现有板料成本的前提下可以大幅增加了油侧几何散热面积9%以上。
5.本实用新型提出在变压器用油浸式散热器的气侧和油测上优化结构设计,增加混、扰流结构,对散热器传热空气层、油流层形成均混扰流,分段阻断了气侧热边界层向上叠加将段内的热气层流导出散热器气侧表面,使传热气层温度降低;同时分段改变散热器油侧油流通腔容积和形状,使变压器油流动方向及流速改变且无规则,从而对散热器油侧分段扰流达到高效散热的目的,并且油侧散热面积增加将使散热器onan有效散热面积增加,则散热能力增加。
6.为解决上述技术问题,本实用新型采用的技术方案是:一种散热器用非能动三维均混扰流型散热片,其散热片1由两个散热单片2对置焊接组成,散热单片2的散热面为多个大弧形散热面3 组成、两个大弧形散热面3之间设有焊接通道4、大弧形散热面3上设有半环形气流导向波峰5、混流减容槽6,其组合构成了散热片1外侧的气侧扰流结构7和内侧的油侧混流结构8;
7.所述散热片1包括:带有进油口9的分流腔10、出油口11的汇流腔12和由焊接通道4分隔开的多个大弧形散热面3的混流油流通腔13,及其大弧形散热面3的混流油流通腔13内侧设有的油侧混流结构8、其大弧形散热面3外侧设有的气侧扰流结构7;
8.所述进油口9为半圆弧形口状敞开式,且与分流腔10相通;出油口11区别于进油口9的是与汇流腔12相通;
9.所述散热单片2的大弧形散热面3上的气侧扰流结构7和油侧混流结构8设置成与散热单片2不同交错排列构成a型散热单片14;
10.所述散热单片2与a型散热单片14焊接组成a型散热片15;a型散热片15区别于散热片 1厚度方向的两侧混流减容槽6与半环形气流导向波峰5交错设置。
11.所述散热单片2的大弧形散热面3上的气侧扰流结构7和油侧混流结构8中的半环形气流导向波峰5设置成两侧或单侧穿过焊接通道、延伸至相邻混流油流通腔13内部且与其相通;其半环形气流导向波峰5的曲线方向设置成不同方向构成b型散热单片16;
12.所述两b型散热单片16焊接组成b型散热片17;b型散热片17区别在于散热片1和a型散热片15混流油流通腔13与其相邻的半环形气流导向波峰5相互连通,且半环形气流导向波峰5 之间通过混流油流通腔13相互连通,以上相互连通使散热片16内的变压器油全部得到掺混和扰动。
13.优选的,所述进油口9为半圆弧形口状敞开式,且与分流腔10相通;出油口11区别于进油口9的是与汇流腔12相通;
14.所述分流腔10、汇流腔12上设有与多个混流油流通腔13过渡连接的大弧形散热面3和混流减容槽6形状,其形状分别与多个混流油流通腔13两端相连通;
15.所述焊接通道4为平面条状,多个焊接通道4分隔成多个混流油流通腔13;
16.所述大弧形散热面3为弧面形状,其大弧形散热面3上设有半环形气流导向波峰5、混流减容槽6。
17.优选的,所述散热单片2的大弧形散热面3从气侧面向外隆起成山峰状,从油侧面向外隆起成山谷状,其山峰状为半环形气流导向波峰5、其山谷状为半环形混流油流腔18,半环形气流导向波峰5和半环形混流油流腔18有曲线弧形19和直线弧形20;
18.所述为使半环形气流导向波峰阻断层间气流、实现干扰气流和导向气流的效果达到最大化,其半环形气流导向波峰5从油腔外侧平面向外隆起形成半环;
19.所述半环形气流导向波峰5展长度可达到60-70mm左右,宽度可达到10-30mm左右,高度可达到8mm左右;
20.所述上下两个半环形气流导向波峰5之间垂直方向间隔可按测试结果优选,推荐为 100-200mm之间。
21.优选的,所述散热单片2的多个大弧形散热面3上的上下两半环形气流导向波峰5之间设有向混流油流通腔13方向隆起的长圆弧形混流减容槽6,半环形气流导向波峰5和混流减容槽6构成容积对冲结构21;
22.所述混流减容槽6为长圆弧形并向散热片油腔内侧隆起,隆起高度小于内腔厚度的1/2,其长度为40-120mm,宽度6-16mm,深3-4mm。相比于目前行业内片式散热器,该散热器片的混流减容槽6向内隆起部分能够与更为中心部位的导热油接触,基于现有散热片内部导热油温度场分布可知:同一高度截面的油层温度场,中心温度高于边缘温度。
23.因此基于傅里叶定律热流率方程(heat transfer rate equation)可知:
[0024][0025]
式中:
[0026]
1)q为热流密度,即在与传递方向相垂直的单位面积上单位时间内通过的热流量
(w/
㎡
);
[0027]
2)λ为热导率;
[0028]
3)δ为热量通过的壁厚;
[0029]
4)t1、t2分别为温度场中的高温和低温;
[0030]
在导热材料不改变,壁厚不变的前提下,单位时间内通过同一壁厚的热流量与其温度场的温差成正比,因此,本实用新型所设计混流减容槽6通过提高导热壁厚两侧温差,从而提高了热流密度,起到了提高散热效果的作用;
[0031]
所述为使半环形气流导向波峰5高,对层间气流干扰作用很大,但高波峰导向会同时使散热片1油腔容积出现很多增加量,会使变压器装油量增加成本增高,本实用新型在纵向的两半环形气流导向波峰5之间混流减容槽6的设计,使半环形气流导向波峰6高增加的容积与混流减容槽6两者构成容积对冲,使散热片1容积不变。
[0032]
优选的,所述混流油流通腔13设置在两焊接通道4间,混流油流通腔13中设置五种混流油流通腔13截面形状:
[0033]
所述混流油流通腔13截面形状,其一为减容混流油流腔22截面形状,由两混流减容槽6 部分对置组成;
[0034]
所述混流油流通腔13截面形状,其二为环形混流油流腔23截面形状,由两半环形混流油流腔18部分对置组成;
[0035]
所述混流油流通腔13截面形状,其三为大弧形混流油流腔24截面形状,由两大弧形散热面3部分对置组成;
[0036]
所述混流油流通腔13截面形状,其四为双半环形混流油流腔25截面形状,由混流减容槽 6部分与半环形混流油流腔18部分对置组成;
[0037]
所述混流油流通腔13截面形状,其五为大弧形减容混流油流腔26截面形状,由混流减容槽6部分与大弧形散热面3部分对置组成。
[0038]
所述本设计减容混流油流腔22比环形混流油流腔23截面积小2.7倍左右,环形混流油流腔23比大弧形混流油流腔24截面积大2.1倍左右,由于散热片1的混流油流通腔13内油流方向先通过减容混流油流腔22、再通过环形混流油流腔23、再通过大弧形混流油流腔24、又通过减容混流油流腔22,且以上油流路径多次往复通过,所以混流油流通腔13内的油流方向及油流速度在减容混流油流腔22、环形混流油流腔23和大弧形混流油流腔24之间不断发生改变,使混流油流通腔13内的变压器油形成不断掺混和扰动,从而起到强化传热的作用。
[0039]
优选的,所述多个大弧形散热面3上的气侧面向外隆起的半环形气流导向波峰5纵向设有上下两个长圆弧形混流减容槽6,大弧形散热面3上的长圆弧形混流减容槽6向混流油流通腔13隆起,混流减容槽6的槽底隆起深度浅于焊接通道4底处深度,以上设置构成气侧扰流结构7;
[0040]
所述为使散热片1气侧层间气流产生横向干扰,本设计采用了气侧扰流结构交错排列,构成带有多个气侧扰流结构7的多个混流油流通腔13的散热片1;
[0041]
所述散热片1宽度方向交错排列的气侧扰流结构7和有一定片间距的多个散热片1相邻排列,组成散热片1的片间气侧扰流场27;
[0042]
所述a型散热片15宽度、厚度方向交错排列的多个气侧扰流结构7和有一定片间距
的a 型散热片15相邻排列,组成a型散热片15的a型片间气侧扰流场28。
[0043]
优选的,所述大弧形散热面3上的上下两半环形气流导向波峰5之间设有向混流油流通腔 13方向隆起的两长圆弧形混流减容槽6对置形成的减容混流油流腔22、大弧形散热面3上从油侧面向外隆起成山谷状的两半环形混流油流腔18对置形成的环形混流油流腔23、弧面形状的两大弧形散热面3对置形成的大弧形混流油流腔24,以上三者构成散热片1的油侧混流结构8,且混流减容槽6 隆起的容积与半环形混流油流腔18容积相等。
[0044]
所述大弧形散热面3上的上下两半环形气流导向波峰5之间设有向混流油流通腔13方向隆起的两长圆弧形混流减容槽6部分对置形成的减容混流油流腔22、混流减容槽6部分与半环形混流油流腔18部分对置形成的双半环形混流油流腔25、混流减容槽6部分与大弧形散热面3部分对置形成的大弧形减容混流油流腔26以上三者构成a型散热片15的油侧混流结构8;
[0045]
所述b型散热片17的油侧混流结构8区别在于散热片1油侧混流结构8的混流油流通腔 13间通过半环形气流导向波峰5相互连通,且半环形气流导向波峰5之间通过混流油流通腔13相互连通;
[0046]
所述散热片1宽度方向交错排列的多个油侧混流结构8和有一定片间距的多个散热片1相邻排列,组成油侧混流场29;
[0047]
所述a型散热片15宽度、厚度方向交错排列的多个油侧混流结构8和有一定片间距的a 型散热片15相邻排列,组成a型油侧混流场30。
[0048]
优选的,带有进油口9的分流腔10、出油口11的汇流腔12和由焊接通道4分隔开的多个大弧形散热面3的混流油流通腔13构成c型散热单片51;
[0049]
所述c型散热单片51与散热片1对置焊接组成c型散热片52。
[0050]
综上所述散热单片2、a型散热单片14、b型散热单片16、c型散热单片51及与本实用新型精神实质所作的等效变化或修饰的单片片型同种或异种两两对置焊接组成非能动三维均混扰流型散热片,不同组合且有一定片间距的多个相邻排列,均会对混流油流通腔13内和散热器用非能动三维均混扰流型散热片外的液相与气相物体得到不同的掺混和扰动,同时形成不同的油侧混流场29和片间气侧扰流场27。
[0051]
一种散热器用非能动三维均混扰流型散热片的制造方法,所述制成散热片1的板材采用钢或铝材质薄板,在轧辊模上按照大弧形散热面3、半环形气流导向波峰5和混流减容槽6的图样加工成相适应的成对轧辊模;再按分流腔10、汇流腔12的图样加工成相适应的平板模;在半环形油流腔上轧辊模31和半环形气流导向波峰下轧辊模32完全啮合时,确定其轴端键槽位置33,且轴端键槽位置33与其啮合处34为竖直中心线位置上;上轧辊模齿轮35和下轧辊模齿轮36完全啮合确定其齿轮键槽位置37,且齿轮键槽位置37与其啮合处34为竖直中心线位置上;通过对轴上齿轮键槽位置 37和轴端键槽位置33的确定,可以使轧辊模上的半环形油流腔上轧辊模31和半环形气流导向波峰下轧辊模32压合及其上轧辊模齿轮35、下轧辊模齿轮36啮合共同满足轧辊模滚压轧制条件;
[0052]
所述轧辊模按大弧形散热面3、半环形气流导向波峰5和混流减容槽6的结构形状分为两种:
[0053]
所述第一种轧辊模按照大弧形散热面3的弧面形状图样制作成与其相适应的大弧形上轧辊模38和大弧形下轧辊模39;
[0054]
所述第二种轧辊模按气侧扰流结构7和油侧混流结构8形状图样制作成与其相适应的半环形油流腔上轧辊模31和半环形气流导向波峰下轧辊模32;
[0055]
所述散热片1的加工方法:由动力系统及支撑机械结构驱动成对轧辊模滚压方法制出散热单片2的气侧扰流结构7和油侧混流结构8;再由冲压轧制系统使用平板模制出与多个混流油流通腔 13对应且过渡连接的分流腔10、汇流腔12部分的散热单片2,由板料输送系统将板料传输到以上工位,完成非能动三维均混扰流型散热片轧制工艺;
[0056]
所述非能动三维均混扰流型散热片轧制工艺为以下三种方法:
[0057]
所述轧制工艺方法一,当进油口9与出油口11的中心距与纵向两半环形气流导向波峰5 的中心距成整数倍数关系时,先将半环形油流腔上轧辊模31和半环形气流导向波峰下轧辊模32在非工作状态使其分离,确保其两轧辊模最大外径之间分离的缝隙宽度应大于由多个大弧形散热面3和焊接通道4组成的大弧形散热面成型片40的厚度,其缝隙宽度应满足大弧形上轧辊模38和大弧形下轧辊模39轧制时,大弧形散热面成型片40从半环形油流腔上轧辊模31和半环形气流导向波峰下轧辊模32间的大弧形散热面成型片40在轧辊分离状态下通过时所处的位置41通过;再施加于大弧形上轧辊模38轴端42旋转动力,通过其下轧辊模齿轮36使大弧形下轧辊模39旋转,施加于大弧形下轧辊模39两轴端42向上压力使其两轧辊模压合,平板材在大弧形上轧辊模38、大弧形下轧辊模39旋转和压合当中通过,当轧制到分流腔10、汇流腔12时,平板材上需预留分流腔、汇流腔位置43,此时上轧辊模齿轮35和下轧辊模齿轮36保持啮合,将施加于大弧形下轧辊模39两轴端42相对压力解除并使大弧形上轧辊模38和大弧形下轧辊模39最大外径分离,且大弧形上轧辊模38和大弧形下轧辊模39最大外径之间分离的缝隙宽度应大于平板材厚度,使平板上分流腔10、汇流腔12位置未经大弧形上轧辊模38、大弧形下轧辊模39、半环形油流腔上轧辊模31和半环形气流导向波峰下轧辊模 32滚压即输送到分流腔10、汇流腔12平板模压制成型位置44,进行分流腔10、汇流腔12与大弧形散热面成型片40部分相连接的压制,在以上过程中两套轧辊其轴端42的上轧辊模齿轮35和下轧辊模齿轮36一直处在轧制时啮合状态45和轧辊分离时齿轮啮合状态46,完成散热单片2或a型散热单片14轧制成型工艺;
[0058]
所述轧制工艺方法二,区别于轧制工艺方法一的是当进油口9与出油口11的中心距与纵向两半环形气流导向波峰5的中心距成非整数倍数关系时,与平板模干涉的半环形气流导向波峰47位置由大弧形上轧辊模38、大弧形下轧辊模39滚压轧制成型的大弧形散热面成型片40部分替代,且与分流腔10、汇流腔12进行过渡连接段48的滚压轧制;
[0059]
所述轧制工艺方法三,区别于轧制工艺方法一的是当进油口9与出油口11的中心距与纵向两半环形气流导向波峰5的中心距成整数倍数关系时,且动力系统及支撑机械结构的驱动力足够大时,先将大弧形上轧辊模38和大弧形下轧辊模39设置在轧辊分离时齿轮啮合状态46,再由半环形油流腔上轧辊模31和半环形气流导向波峰下轧辊模32完成滚压轧制;
[0060]
所述c型散热单片51的轧制工艺方法,区别于轧制工艺方法一的是先将半环形油流腔上轧辊模31和半环形气流导向波峰下轧辊模32设置在轧辊分离时齿轮啮合状态46,再由大弧形上轧辊模38和大弧形下轧辊模39完成c型散热单片51的滚压轧制;
[0061]
完成散热单片2、a型散热单片14、b型散热单片16、c型散热单片51轧制成型工艺后,将散热单片2、a型散热单片14、b型散热单片16、c型散热单片51异种或同种两两对置后
的四周边缘为平面的周边焊道49和焊接通道4在混流油流通腔13侧对向重合对齐,两散热单片2或两a型散热单片14四周边缘采用行业现有焊接工艺制成;将合片焊接完成的散热片1或a型散热片15的四周边缘余料剪切完毕转入散热器50制造流程的下道工序。
[0062]
本实用新型具有以下有益的效果:
[0063]
散热片的油侧面积用三维软件测得数据表明比现有的散热片油侧面积增加9%左右,散热片的气侧扰流结构对气侧层换热所起的作用和油侧混流结构对油侧层换热所起的作用,以及散热片内外部的油侧混流场、片间气侧扰流场中的流体进行不断掺混和扰动所起的作用,推算本设计在非能动冷却(onan)条件下的散热片比现有散热片的散热效果增加15%左右,在风机冷却(onaf)条件下的散热片比现有散热片的散热效果增加20%左右。
[0064]
在散热片材料成本没有增加前提下,提高了散热器的散热效率,从而实现了单位散热功率下散热器材料成本降低,由于散热器散热效率提高变压器配用散热器数量发生减少,从而使变压器装油量降低,降低了变压器的制造成本,也能减少一定数量的散热器冷却风机,由于变压器配用散热器数量的减少,使变压器外形尺寸减小节省设备使用空间。
[0065]
在非能动三维均混扰流型散热片的制造方法中,采用轧制工艺方法一先滚压轧制大弧形散热面成型片、再先滚压轧制气侧扰流结构和油侧混流结构的两次成型的轧制方法轧制散热单片时,有利于散热单片的气侧扰流结构和油侧混流结构中半环形气流导向波峰和半环形油流腔的成型,继而达到设计所需的最佳成型效果。
[0066]
在非能动三维均混扰流型散热片的制造方法中,采用轧制工艺方法二,区别于用轧制工艺方法一的是仅滚压轧制与分流腔、汇流腔进行过渡连接段的大弧形散热面成型片,此轧制工艺方法提高工作效率且能够达到中心距可调控的效果。
[0067]
在非能动三维均混扰流型散热片的制造方法中,采用轧制工艺方法三,区别于用轧制工艺方法二和轧制工艺方法一的是仅使用半环形油流腔上轧辊模和半环形气流导向波峰下轧辊模滚压轧制散热单片的气侧扰流结构和油侧混流结构部分,此轧制工艺方法能够最高效的制作出散热单片。
附图说明
[0068]
图1为散热片的正视图;
[0069]
图2为散热片的a-a剖视图;
[0070]
图3为散热片的俯视图;
[0071]
图4为半环形气流导向波峰b放大局部视图;
[0072]
图5为半环形气流导向波峰c-c剖放大视图;
[0073]
图6为图4d-d剖截面放大视图;
[0074]
图7为散热片的e-e剖视图;
[0075]
图8为散热单片的气侧扰流结构局部剖轴测视图;
[0076]
图9为散热单片的油侧混流结构局部剖轴测视图;
[0077]
图10为散热片的气侧扰流结构和油侧混流结构的局部阶梯剖轴测视图;
[0078]
图11为a型散热片的正视图;
[0079]
图12为a型散热片的f-f剖视图;
[0080]
图13为b型散热片的正视图;
[0081]
图14为b型散热片的g-g剖视图;
[0082]
图15为图14的i放大视图;
[0083]
图16为b型散热片的h-h剖视图;
[0084]
图17为b型散热片的轴测视图;
[0085]
图18为图17的j-j剖视图;
[0086]
图19为直线弧形半环形气流导向波峰散热片的正视图;
[0087]
图20为图19的m-m剖视图;
[0088]
图21为图17的k放大视图;
[0089]
图22为曲线弧形半环形气流导向波峰b放大局部轴测视图;
[0090]
图23为直线弧形半环形气流导向波峰l放大局部轴测视图;
[0091]
图24为散热片在单个混流油流腔上的气侧扰流结构示意图;
[0092]
图25为图24厚度方向的气侧扰流结构剖视示意图;
[0093]
图26为图24的n-n放大剖视图;
[0094]
图27为图24的p-p放大剖视图;
[0095]
图28为图24的q-q放大剖视图;
[0096]
图29为图24的r放大局部阶梯剖视图;
[0097]
图30为a型散热片单个混流油流腔示意图;
[0098]
图31为图30厚度方向的气侧扰流结构剖视示意图;
[0099]
图32为图30的s-s放大剖视图;
[0100]
图33为图30的t-t放大剖视图;
[0101]
图34为图30的u-u放大剖视图;
[0102]
图35为散热片片间气侧扰流场和油侧混流场的纵向剖示意图;
[0103]
图36为图35的油侧混流结构v放大局部视图;
[0104]
图37为a型散热片片间气侧扰流场和油侧混流场的纵向剖示意图;
[0105]
图38为图37的油侧混流结构w放大局部视图;
[0106]
图39为轧制时啮合状态正视示意图;
[0107]
图40为轧辊分离时齿轮啮合状态及大弧形散热面成型片在轧辊分离状态下通过时所处的位置正视示意图;
[0108]
图41为图39的左视图;
[0109]
图42为图39的x-x剖视图;
[0110]
图43为图40的左视图;
[0111]
图44为图40的轧辊y-y剖视图;
[0112]
图45为轧制工艺方法一轴测示意图;
[0113]
图46为轧制工艺方法二轴测示意图;
[0114]
图47为轧制工艺方法三轴测示意图;
[0115]
图48为与平板模干涉的半环形气流导向波峰示意图;
[0116]
图49为大弧形散热面成型片截面示意图;
[0117]
图50为非能动三维均混扰流型散热片制成的散热器轴测示意图;
[0118]
图51为c型散热片正视图;
[0119]
图52为c型散热片z-z剖视图;
[0120]
图53为c型散热单片轧制方法示意图。
[0121]
图中:1,散热片;2,散热单片;3,大弧形散热面;4,焊接通道;5,半环形气流导向波峰;6,混流减容槽;7,气侧扰流结构;8,油侧混流结构;9,进油口;10,分流腔;11,出油口; 12,汇流腔;13,混流油流通腔;14,a型散热单片;15,a型散热片;16,b型散热单片;17,b 型散热片;18,半环形混流油流腔;19曲线弧形;20,直线弧形;21,容积对冲结构;22,减容混流油流腔;23,环形混流油流腔;24,大弧形混流油流腔;25,双半环形混流油流腔;26,大弧形减容混流油流腔;27,片间气侧扰流场;28,a型片间气侧扰流场;29油侧混流场;30,a型油侧混流场;31,半环形油流腔上轧辊模;32,半环形气流导向波峰下轧辊模;33,轴端键槽位置;34,啮合处;35,上轧辊模齿轮;36,下轧辊模齿轮;37,齿轮键槽位置;38大弧形上轧辊模;39大弧形下轧辊模;40,大弧形散热面成型片;41,轧辊分离状态下通过时所处的位置;42,轴端;43,分流腔、汇流腔位置;44,平板模压制成型位置;45轧制时啮合状态;46,轧辊分离时齿轮啮合状态;47,与平板模干涉的半环形气流导向波峰;48,过渡连接段;49,周边焊道;50,散热器;51,c型散热单片;52,c型散热片。
具体实施方式
[0122]
下面结合附图和实施例对本实用新型进行详细描述。
[0123]
如图1、2所示,一种散热器用非能动三维均混扰流型散热片,其散热片1由两个散热单片 2对置焊接组成,散热单片2的散热面为多个大弧形散热面3组成、两个大弧形散热面3之间设有焊接通道4、散热单片2上分布若干半环形气流导向波峰5、混流减容槽6,其组合构成散热片1外侧的如图8、24、25、30、31所示,气侧扰流结构7和内侧的如图9、35~38所示,油侧混流结构8。
[0124]
如图1、2、8、9所示,所述散热片1包括:带有进油口9的分流腔10、出油口11的汇流腔12;由焊接通道4分隔开的多个大弧形散热面3的混流油流通腔13;混流油流通腔13内侧设有的油侧混流结构8;大弧形散热面3外侧设有的气侧扰流结构7;
[0125]
如图1、11所示,所述散热单片2的大弧形散热面3上的气侧扰流结构7和油侧混流结构 8设置成与散热单片2不同交错排列构成a型散热单片14;
[0126]
所述散热单片2与a型散热单片14焊接组成a型散热片15;a型散热片15区别于散热片 1厚度方向的两侧混流减容槽6与半环形气流导向波峰5交错设置。
[0127]
如图1、11、13~18、21所示,所述散热单片2的大弧形散热面3上的气侧扰流结构7和油侧混流结构8中的半环形气流导向波峰5设置成两侧或单侧穿过焊接通道、延伸至相邻混流油流通腔13内部且与其相通;其半环形气流导向波峰5的曲线方向设置成不同方向构成b型散热单片16;
[0128]
所述两b型散热单片16焊接组成b型散热片17;b型散热片17区别在于散热片1和a型散热片15混流油流通腔13与其相邻的半环形气流导向波峰5相互连通,且半环形气流导向波峰5 之间通过混流油流通腔13相互连通。
[0129]
如图1、3所示,所述进油口9为半圆弧形口状敞开式,且与分流腔10相通;出油口11 区别于进油口9的是与汇流腔12相通;
[0130]
所述分流腔10、汇流腔12上设有与多个混流油流通腔13过渡连接的大弧形散热面
3和混流减容槽6形状,其形状分别与多个混流油流通腔13两端相连通;
[0131]
如图8~10、17所示,所述焊接通道4为平面条状,多个焊接通道4分隔成多个混流油流通腔13;
[0132]
如图1、6~9、28所示,所述大弧形散热面3为弧面形状,其大弧形散热面3上设有半环形气流导向波峰5、混流减容槽6。
[0133]
如图8~10、17~23、29所示,所述散热单片2的大弧形散热面3从气侧面向外隆起成山峰状,从油侧面向外隆起成山谷状,其山峰状为半环形气流导向波峰5、其山谷状为半环形混流油流腔18,半环形气流导向波峰5和半环形混流油流腔18有曲线弧形19和直线弧形20。
[0134]
如图1、8、10所示,所述散热单片2的多个大弧形散热面3上的上下两半环形气流导向波峰5之间设有向混流油流通腔13方向隆起的长圆弧形混流减容槽6,半环形气流导向波峰5和混流减容槽6构成容积对冲结构21。
[0135]
如图24~34所示,所述混流油流通腔13设置在两焊接通道4间,混流油流通腔13中设置五种混流油流通腔13截面形状:
[0136]
所述混流油流通腔13截面形状,其一为减容混流油流腔22截面形状,由两混流减容槽6 部分对置组成;
[0137]
所述混流油流通腔13截面形状,其二为环形混流油流腔23截面形状,由两半环形混流油流腔18部分对置组成;
[0138]
所述混流油流通腔13截面形状,其三为大弧形混流油流腔24截面形状,由两大弧形散热面3部分对置组成;
[0139]
所述混流油流通腔13截面形状,其四为双半环形混流油流腔25截面形状,由混流减容槽 6部分与半环形混流油流腔18部分对置组成;
[0140]
所述混流油流通腔13截面形状,其五为大弧形减容混流油流腔26截面形状,由混流减容槽6部分与大弧形散热面3部分对置组成。
[0141]
如图8、26所示,所述多个大弧形散热面3上的气侧面向外隆起的半环形气流导向波峰5 纵向设有上下两个长圆弧形混流减容槽6,大弧形散热面3上的长圆弧形混流减容槽6向混流油流通腔13隆起,混流减容槽6的槽底隆起深度浅于焊接通道4深度,以上设置构成气侧扰流结构7;
[0142]
如图35所示,所述散热片1宽度方向交错排列的气侧扰流结构7和有一定片间距的多个散热片1相邻排列,组成散热片1的片间气侧扰流场27;
[0143]
如图37所示,所述a型散热片15宽度、厚度方向交错排列的多个气侧扰流结构7和有一定片间距的a型散热片15相邻排列,组成a型散热片15的a型片间气侧扰流场28。
[0144]
如图9、10、26~29所示,所述大弧形散热面3上的上下两半环形气流导向波峰5之间设有向混流油流通腔13方向隆起的两长圆弧形混流减容槽6对置形成的减容混流油流腔22、大弧形散热面3上从油侧面向外隆起成山谷状的两半环形混流油流腔18对置形成的环形混流油流腔23、弧面形状的两大弧形散热面3对置形成的大弧形混流油流腔24,以上三者构成散热片1的油侧混流结构8,且混流减容槽6隆起的容积与半环形混流油流腔18容积相等。
[0145]
如图9、10、24~34所示,所述大弧形散热面3上的上下两半环形气流导向波峰5之
间设有向混流油流通腔13方向隆起的两长圆弧形混流减容槽6部分对置形成的减容混流油流腔22、混流减容槽6部分与半环形混流油流腔18部分对置形成的双半环形混流油流腔25、混流减容槽6部分与大弧形散热面3部分对置形成的大弧形减容混流油流腔26以上三者构成a型散热片15的油侧混流结构8;
[0146]
如图1、11、13~18所示,所述b型散热片17的油侧混流结构8区别在于散热片1油侧混流结构8的混流油流通腔13间通过半环形气流导向波峰5相互连通,且半环形气流导向波峰5之间通过混流油流通腔13相互连通;
[0147]
如图35~38所示,所述散热片1宽度方向交错排列的多个油侧混流结构8和有一定片间距的多个散热片1相邻排列,组成油侧混流场29;
[0148]
所述a型散热片15宽度、厚度方向交错排列的多个油侧混流结构8和有一定片间距的a 型散热片15相邻排列,组成a型油侧混流场30。
[0149]
如图51、52所示,带有进油口9的分流腔10、出油口11的汇流腔12和由焊接通道4分隔开的多个大弧形散热面3的混流油流通腔13构成c型散热单片51;
[0150]
所述c型散热单片51与散热片1对置焊接组成c型散热片52。
[0151]
如图35~38所示,综上所述散热单片2、a型散热单片14、b型散热单片16、c型散热单片51及与本实用新型精神实质所作的等效变化或修饰的单片片型同种或异种两两对置焊接组成非能动三维均混扰流型散热片,不同组合且有一定片间距的多个相邻排列,均会对混流油流通腔13内和散热器用非能动三维均混扰流型散热片外的液相与气相物体得到不同的掺混和扰动,同时形成不同的油侧混流场29和气侧扰流场27。
[0152]
如图39~50所示,所述的一种散热器用非能动三维均混扰流型散热片的制造方法,制成散热片1的板材采用钢或铝材质薄板,在轧辊模上按照大弧形散热面3、半环形气流导向波峰5和混流减容槽6的图样加工成相适应的成对轧辊模;再按分流腔10、汇流腔12的图样加工成相适应的平板模;在半环形油流腔上轧辊模31和半环形气流导向波峰下轧辊模32完全啮合时,确定其轴端键槽位置33,且轴端键槽位置33与其啮合处34为竖直中心线位置上;上轧辊模齿轮35和下轧辊模齿轮36 完全啮合确定其齿轮键槽位置37,且齿轮键槽位置37与其啮合处34为竖直中心线位置上;通过对轴上齿轮键槽位置37和轴端键槽位置33的确定,可以使轧辊模上的半环形油流腔上轧辊模31和半环形气流导向波峰下轧辊模32压合及其上轧辊模齿轮35、下轧辊模齿轮36啮合共同满足轧辊模滚压轧制条件;
[0153]
如图45~47所示,所述轧辊模按大弧形散热面3、半环形气流导向波峰5和混流减容槽6 的结构形状分为两种:
[0154]
所述第一种轧辊模按照大弧形散热面3的弧面形状图样制作成与其相适应的大弧形上轧辊模38和大弧形下轧辊模39;
[0155]
所述第二种轧辊模按气侧扰流结构7和油侧混流结构8形状图样制作成与其相适应的半环形油流腔上轧辊模31和半环形气流导向波峰下轧辊模32;
[0156]
所述散热片1的加工方法:由动力系统及支撑机械结构驱动成对轧辊模滚压方法制出散热单片2的气侧扰流结构7和油侧混流结构8;再由冲压轧制系统使用平板模制出与多个混流油流通腔13对应且过渡连接的分流腔10、汇流腔12部分的散热单片2,由板料输送系统将板料传输到以上工位,完成非能动三维均混扰流型散热片轧制工艺;
[0157]
所述非能动三维均混扰流型散热片轧制工艺为以下三种方法:
[0158]
如图45所示,所述轧制工艺方法一,当进油口9与出油口11的中心距与纵向两半环形气流导向波峰5的中心距成整数倍数关系时,先将半环形油流腔上轧辊模31和半环形气流导向波峰下轧辊模32在非工作状态使其分离,确保其两轧辊模最大外径之间分离的缝隙宽度应大于由多个大弧形散热面3和焊接通道4组成的大弧形散热面成型片40的厚度,其缝隙宽度应满足大弧形上轧辊模 38和大弧形下轧辊模39轧制时,大弧形散热面成型片40从半环形油流腔上轧辊模31和半环形气流导向波峰下轧辊模32间的大弧形散热面成型片40在轧辊分离状态下通过时所处的位置41通过;再施加于大弧形上轧辊模38轴端42旋转动力,通过其下轧辊模齿轮36使大弧形下轧辊模39旋转,施加于大弧形下轧辊模39两轴端42向上压力使其两轧辊模压合,平板材在大弧形上轧辊模38、大弧形下轧辊模39旋转和压合当中通过,当轧制到分流腔10、汇流腔12时,平板材上需预留分流腔、汇流腔位置43,此时上轧辊模齿轮35和下轧辊模齿轮36保持啮合,将施加于大弧形下轧辊模39两轴端42相对压力解除并使大弧形上轧辊模38和大弧形下轧辊模39最大外径分离,且大弧形上轧辊模38和大弧形下轧辊模39最大外径之间分离的缝隙宽度应大于平板材厚度,使平板上分流腔10、汇流腔12位置未经大弧形上轧辊模38、大弧形下轧辊模39、半环形油流腔上轧辊模31和半环形气流导向波峰下轧辊模32滚压即输送到分流腔10、汇流腔12平板模压制成型位置44,进行分流腔10、汇流腔12与大弧形散热面成型片40部分相连接的压制,在以上过程中两套轧辊其轴端42的上轧辊模齿轮35和下轧辊模齿轮36一直处在轧制时啮合状态45和轧辊分离时齿轮啮合状态46,完成散热单片2或a型散热单片14轧制成型工艺;
[0159]
如图46所示,所述轧制工艺方法二,区别于轧制工艺方法一的是当进油口9与出油口11 的中心距与纵向两半环形气流导向波峰5的中心距成非整数倍数关系时,与平板模干涉的半环形气流导向波峰47位置由大弧形上轧辊模38、大弧形下轧辊模39滚压轧制成型的大弧形散热面成型片40 部分替代,且与分流腔10、汇流腔12进行过渡连接段48的滚压轧制;
[0160]
如图47所示,所述轧制工艺方法三,区别于轧制工艺方法一的是当进油口9与出油口11 的中心距与纵向两半环形气流导向波峰5的中心距成整数倍数关系时,且动力系统及支撑机械结构的驱动力足够大时,先将大弧形上轧辊模38和大弧形下轧辊模39设置在轧辊分离时齿轮啮合状态46,再由半环形油流腔上轧辊模31和半环形气流导向波峰下轧辊模32完成滚压轧制;
[0161]
如图53所示,所述c型散热单片51的轧制工艺方法,区别于轧制工艺方法一的是先将半环形油流腔上轧辊模31和半环形气流导向波峰下轧辊模32设置在轧辊分离时齿轮啮合状态46,再由大弧形上轧辊模38和大弧形下轧辊模39完成c型散热单片51的滚压轧制;
[0162]
完成散热单片2、a型散热单片14、b型散热单片16、c型散热单片51轧制成型工艺后,将散热单片2、a型散热单片14、b型散热单片16、c型散热单片51异种或同种两两对置后的四周边缘为平面的周边焊道49和焊接通道4在混流油流通腔13侧对向重合对齐,两散热单片2或两a型散热单片14四周边缘采用行业现有焊接工艺制成;将合片焊接完成的散热片1或a型散热片15的四周边缘余料剪切完毕转入散热器50制造流程的下道工序。
[0163]
上述实施例只为说明本实用新型的技术构思及特点,其目的在于让熟悉此项技术的人士能够了解本实用新型的内容并据以实施,并不能以此限制本实用新型的保护范围。凡根据本实用新型精神实质所作的等效变化或修饰,都应涵盖在本实用新型的保护范围之内。