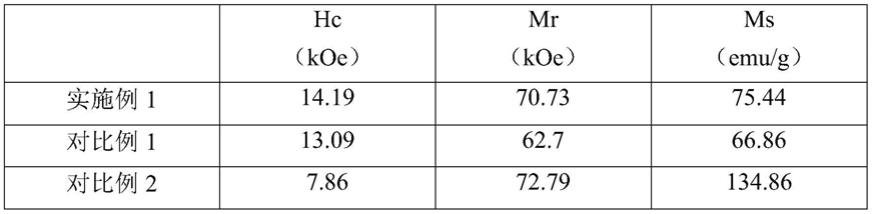
一种具有特殊结构的(nd,tb)2fe
14
b/co复合磁性材料的制备方法
技术领域
1.本发明涉及一种复合磁性材料的制备方法,具体涉及一种表面活性剂辅助高能球磨和化学沉淀制备具有特殊结构的(nd,tb)2fe
14
b/co复合磁性材料的制备方法,属于稀土磁性材料领域。
背景技术:2.当今社会,永磁材料在内燃机,能源汽车,计算机,航空航天,生物医学等领域应用广泛。社会的发展,也加速和放大了人们对永磁材料的需求。众所周知,第三代永磁材料nd2fe
14
b已经愈发的接近其理论磁能积,而且在地球上,稀土元素的含量有限,日渐稀少。于是,从可持续发展和降低成本的角度出发,人们将目光转向了纳米双相复合磁体,具有高的理论磁能积和更低的成本等优势。
3.目前关于纳米双相复合磁体的制备方法主要有两种,自下而上法和自上而下法。自上而下法是指通过加热或塑性变形等物理手段将宏观物质微型化的一种方法,所以又叫物理法。机械球磨法是物理法制备双相复合磁性材料的主要方法,是将铸锭破碎后,对软硬磁相的粉进行球磨,再烧结成型以获得双相磁性复合材料。该方法虽然可以大规模制备,但颗粒容易出现团聚和氧化,对磁性能造成影响。自下而上法是指以分子或原子为单元,通过一定的化学实验设计,对其形貌结构等进行调控,达到设计定向纳米复合材料的过程。液相合成与ca还原扩散相结合的方法作为自下而上法的代表之一,常作为磁体制备的主要手段。用该法制备出的纳米颗粒粒径均一,形貌可控,但是温度要求较高,无法实现大批量生产。因此,需要一种新的物理法和化学法相结合的方法制备纳米复合磁性材料。
技术实现要素:4.为了解决上述问题,本发明提供了一种具有特殊结构的(nd,tb)2fe
14
b/co复合磁性材料的制备方法。使用表面活性剂辅助球磨结合化学沉积法制备了不同(nd,tb)2fe
14
b/co质量比的纳米双相复合颗粒。通过化学沉积过程,所制得的(nd,tb)2fe
14
b/co复合磁性材料相组成是(nd,tb)2fe
14
b和co组成的复合相;所制得的(nd,tb)2fe
14
b/co复合磁性材料的显微结构是以(nd,tb)2fe
14
b为核心硬磁相,co纳米线组成的软磁相为外壳层;co纳米线对(nd,tb)2fe
14
b纳米片不同质量分数的包覆或在(nd,tb)2fe
14
b纳米片表面的生长负载;具有各向异性的(nd,tb)2fe
14
b纳米片的c轴(00l)方向与纳米片平面平行,这样的良性取向和分布状态有效的减小了形状对磁体磁性能的影响,使得软硬磁相在磁场取向后能够分布更均匀,交换耦合作用更有利,改善了磁性能,且在很大程度上减少了稀土(nd,tb)的消耗。为双各向异性纳米双相粘接磁体的制备奠定了基础,提供了新思路。
5.为实现上述目的,本发明的技术方案由以下步骤组成:
6.步骤1:.以cocl2·
6h2o粉末为原料,通过水热法制备出月桂酸钴前驱体;
7.步骤2:按nd:tb:fe:b=11.2:4.8:78:6的原子比分别称量nd:tb:fe:b原料;
8.步骤3:将配好的原料放入悬浮熔炼炉中,抽真空,在氩气保护下熔炼,获得合金锭;
9.步骤4:将熔炼好的合金锭在惰性气体保护下退火,之后进行快冷,制备出(nd,tb)2fe
14
b;
10.步骤5:将步骤4中(nd,tb)2fe
14
b进行机械破碎后加入表面活性剂进行高能球磨,得到(nd,tb)2fe
14
b纳米片;
11.步骤6:将步骤5中得到的(nd,tb)2fe
14
b纳米片和月桂酸钴、十六烷基胺、rucl3通过醇热法经去离子水离心超声后制备出(nd,tb)2fe
14
b/co复合磁性材料。
12.作为优选方案,步骤1月桂酸钴前驱体的制备过程为:向装有80ml去离子水的三颈烧瓶中加入80-85mmol naoh,水浴加热至60℃后加入85-90mmol月桂酸,机械搅拌使其充分溶解;取35-40mmol cocl2·
6h2o溶于20ml去离子水中逐滴加入三颈烧瓶,搅拌30-40分钟后溶液从紫色变成粉色,取出冷却到室温;随后用去离子水和甲醇超声离心洗涤3-4次后放入干燥箱,离心速度为6000-8000r/min,离心时间为3-5min,干燥时间为8-10h;将干燥后产物研磨即可得到月桂酸钴前驱体;上述物质用量关系根据需要同比增大或缩小;
13.作为优选方案,步骤3中(nd,tb)2fe
14
b合金锭的制备过程为:通过悬浮熔炼的方式,炼制nd-tb-fe-b合金铸锭;悬浮熔炼炉真空度达到5
×
10-2
pa后充入纯氩气,如此循环往复抽放气3-5次;对原料重复熔炼3-5次,使铸锭成分均匀;考虑到金属的烧损问题,按照相应的化学计量比配料,分别对nd、tb和feb合金配置额外烧损如对的烧损依次为3wt.%、3wt.%和5wt.%;最后将铸锭在惰性气体保护下的真空退火炉中均匀化退火。
14.作为优选方案,步骤4中(nd,tb)2fe
14
b的退火,真空度为5
×
10-2
pa,退火温度为1100-1200℃,退火时间为24h。
15.作为优选方案,步骤5中(nd,tb)2fe
14
b纳米片的制备过程为:将退火后的(nd,tb)2fe
14
b铸锭去氧化皮,研磨过100目筛子,过筛后的粉末按照球料比为20:1的比例放入球磨罐中,加入油胺和油酸作为表面活性剂,同时以正庚烷作为球磨介质放入高能球磨机进行不同时间不同能量球磨;球磨结束后,用酒精、丙酮、正庚烷等有机溶剂对样品进行反复超声和离心,去除表面活性剂;最后在真空条件下干燥,得到(nd,tb)2fe
14
b纳米片。
16.作为优选方案,步骤6中(nd,tb)2fe
14
b/co纳米复合磁性材料的制备过程为:将预先制备的(nd,tb)2fe
14
b纳米片和2-2.1g的月桂酸钴、0.5771-0.5819g的十六烷基胺(hda)、0.0035-0.004g rucl3和60ml 1,2-丁二醇加入到高压釜内衬中,通入氩气保护气体进行超声分散后放入高压釜中,使用马弗炉进行加热反应;升温速率为8-10℃/min,反应温度为250℃,保温时间为80-100min。冷却至室温后使用甲苯和正己烷离心洗涤3-5次,最后保存在正己烷中。由此制得(nd,tb)2fe
14
b/co纳米复合磁性材料。
17.步骤6中,每2-2.1g的月桂酸钴对应0.5771-0.5819g的十六烷基胺(hda)、0.0035-0.004g rucl3和60ml 1,2-丁二醇,制得co纳米线;根据加入不同量的(nd,tb)2fe
14
b纳米片可以制得不同包覆量或负载量co纳米线的(nd,tb)2fe
14
b/co纳米复合磁性材料。
18.作为优选方案,步骤6中(nd,tb)2fe
14
b纳米片是在球磨能量为50-60v,球磨时间为0.5-7h下进行的。
19.进一步优选:步骤6中(nd,tb)2fe
14
b纳米片和月桂酸钴的质量比为(0.5-2):1。
20.本发明与现有技术相比具有如下有益效果:
21.本发明提供了一种通过表面活性剂辅助球磨结合醇热法制备出具有特殊结构的(nd,tb)2fe
14
b/co复合磁性材料的制备方法,即以(nd,tb)2fe
14
b硬磁相为核心,以co软磁相为外壳层,使得软磁相能够均匀的分布于硬磁相周围。这一技术解决了现有技术中出现的软硬磁相分布不均匀的问题,通过该法制备的复合颗粒中的软硬磁相分布均匀,有利于软硬磁相间的交换耦合作用。改善了磁性能,且在很大程度上减少了稀土(nd,tb)的消耗。有利于双各向异性(nd,tb)2fe
14
b/co粘接磁体的制备。
附图说明
22.图1左图为实施例1与实施例2中制备的复合磁性材料的xrd测试的物相结果,右图为实施例1的磁测结果。
23.图2左图为实施例1制备的复合磁性材料的扫描电镜图,右图为实施例2制备的复合磁性材料的扫描电镜图。
24.图3左图为对比例1的xrd测试的物相结果,右图为对比例1的磁测结果。
25.图4左图为对比例2的xrd测试的物相结果,右图为对比例2的磁测结果。
具体实施方式
26.为详细说明本发明的技术内容、所实现目的及效果,以下结合实施方式予以说明。
27.实施例1
28.(1)向装有80ml去离子水的三颈烧瓶中加入84mmol naoh,水浴加热至60℃后加入88mmol月桂酸,机械搅拌使其充分溶解。取40mmol cocl2·
6h2o溶于20ml去离子水中逐滴加入三颈烧瓶,搅拌30分钟后溶液从紫色变成粉色,取出冷却到室温。随后用去离子水和甲醇超声离心洗涤4次后放入干燥箱,离心速度为8000r/min,离心时间为5min,干燥时间为10h。将干燥后产物研磨即可得到月桂酸钴前驱体。
29.(2)通过悬浮熔炼的方式,炼制nd-tb-fe-b合金铸锭。悬浮熔炼炉真空度达到5
×
10-2
pa后充入高纯氩气,如此循环往复抽放气5次。对原料重复熔炼3次,使铸锭成分均匀。考虑到金属的烧损问题,按照相应的化学计量比配料,分别对nd,tb和feb合金配置额外3wt.%、3wt.%和5wt.%的烧损。最后将铸锭在惰性气体保护下的真空退火炉中均匀化退火。
30.(3)将退火后的(nd,tb)2fe
14
b铸锭去氧化皮,研磨过100目筛子。过筛后的粉末按照球料比为20:1的比例放入球磨罐中,加入适量的油胺和油酸作为表面活性剂,同时以正庚烷作为球磨介质放入高能球磨机进行不同时间不同能量球磨。球磨结束后,用酒精、丙酮、正庚烷等有机溶剂对样品进行反复超声和离心,去除表面活性剂。最后在真空条件下干燥,得到(nd,tb)2fe
14
b纳米片。
31.(4)将步骤(3)中的2.16g(nd,tb)2fe
14
b纳米片和2.07g月桂酸钴,0.5809g十六烷基胺(hda),0.0037g rucl3,60ml 1,2-丁二醇加入到100ml高压釜内衬中。通入氩气保护气体进行超声分散后放入高压釜中,使用马弗炉进行加热反应。升温速率为10℃/min,反应温度为250℃,保温时间为80min。冷却至室温后使用甲苯和正己烷离心洗涤3次,最后保存在正己烷中。由此制得10%co含量的(nd,tb)2fe
14
b/co纳米复合磁性材料。
32.(5)采用xrd对产物的物相组成进行分析,结果如图1左图所示,样品由(nd,tb)2fe
14
b相和co相组成,说明在反应中生成了co,稀土在反应中有烧损。采用vsm对产物的磁性能进行测试,结果如图1右图所示。利用sem对产物的形貌进行了表征,结果如图2左图所示,co纳米线平行于纳米片表面。
33.实施例2
34.(1)向装有80ml去离子水的三颈烧瓶中加入84mmol naoh,水浴加热至60℃后加入88mmol月桂酸,机械搅拌使其充分溶解。取40mmol cocl2·
6h2o溶于20ml去离子水中逐滴加入三颈烧瓶,搅拌30分钟后溶液从紫色变成粉色,取出冷却到室温。随后用去离子水和甲醇超声离心洗涤4次后放入干燥箱,离心速度为8000r/min,离心时间为5min,干燥时间为10h。将干燥后产物研磨即可得到月桂酸钴前驱体。
35.(2)通过悬浮熔炼的方式,炼制nd-tb-fe-b合金铸锭。悬浮熔炼炉真空度达到5
×
10-2
pa后充入高纯氩气,如此循环往复抽放气5次。对原料重复熔炼3次,使铸锭成分均匀。考虑到金属的烧损问题,按照相应的化学计量比配料,分别对nd,tb和feb合金配置额外3wt.%、3wt.%和5wt.%的烧损。最后将铸锭在惰性气体保护下的真空退火炉中均匀化退火。
36.(3)将退火后的(nd,tb)2fe
14
b铸锭去氧化皮,研磨过100目筛子。过筛后的粉末按照球料比为20:1的比例放入球磨罐中,加入适量的油胺和油酸作为表面活性剂,同时以正庚烷作为球磨介质放入高能球磨机进行不同时间不同能量球磨。球磨结束后,用酒精、丙酮、正庚烷等有机溶剂对样品进行反复超声和离心,去除表面活性剂。最后在真空条件下干燥,得到(nd,tb)2fe
14
b纳米片。
37.(4)将步骤(3)中的0.96g(nd,tb)2fe
14
b纳米片和2.07g月桂酸钴,0.5809g十六烷基胺(hda),0.0037g rucl3,60ml 1,2-丁二醇加入到100ml高压釜内衬中。通入氩气保护气体进行超声分散后放入高压釜中,使用马弗炉进行加热反应。升温速率为10℃/min,反应温度为250℃,保温时间为80min。冷却至室温后使用甲苯和正己烷离心洗涤3次,最后保存在正己烷中。由此制得20%co含量的(nd,tb)2fe
14
b/co纳米复合磁性材料。
38.(5)采用xrd对产物的物相组成进行分析,结果如图1左图所示,样品由(nd,tb)2fe
14
b相和co相组成,稀土在反应中有烧损。co相峰强与实施例1相比相对增加,说明co含量在反应中发生了变化。利用sem对产物的形貌进行了表征,结果如图2右图所示,co纳米线含量增加,更均匀的分散在纳米片表面。
39.对比例1
40.(1)通过悬浮熔炼的方式,炼制nd-tb-fe-b合金铸锭。悬浮熔炼炉真空度达到5
×
10-2
pa后充入高纯氩气,如此循环往复抽放气5次。对原料重复熔炼3次,使铸锭成分均匀。考虑到金属的烧损问题,按照相应的化学计量比配料,分别对nd,tb和feb合金配置额外3wt.%、3wt.%和5wt.%的烧损。最后将铸锭在惰性气体保护下的真空退火炉中均匀化退火。
41.(2)将退火后的(nd,tb)2fe
14
b铸锭去氧化皮,研磨过100目筛子。过筛后的粉末按照球料比为20:1的比例放入球磨罐中,加入适量的油胺和油酸作为表面活性剂,同时以正庚烷作为球磨介质放入高能球磨机进行不同时间不同能量球磨。球磨结束后,用酒精、丙酮、正庚烷等有机溶剂对样品进行反复超声和离心,去除表面活性剂。最后在真空条件下干燥,得到(nd,tb)2fe
14
b纳米片。
42.(3)采用xrd对产物的物相组成进行分析,结果如图3左图所示,样品由(nd,tb)2fe
14
b相组成,稀土在反应中有烧损。采用vsm对产物的磁性能进行测试,结果如图3右图所示。
43.对比例2
44.(1)向装有80ml去离子水的三颈烧瓶中加入84mmol naoh,水浴加热至60℃后加入88mmol月桂酸,机械搅拌使其充分溶解。取40mmol cocl2·
6h2o溶于20ml去离子水中逐滴加入三颈烧瓶,搅拌30分钟后溶液从紫色变成粉色,取出冷却到室温。随后用去离子水和甲醇超声离心洗涤4次后放入干燥箱,离心速度为8000r/min,离心时间为5min,干燥时间为10h。将干燥后产物研磨即可得到月桂酸钴前驱体。
45.(2)将步骤(1)中的2.07g月桂酸钴,0.5809g十六烷基胺(hda),0.0037g rucl3,60ml 1,2-丁二醇加入到100ml高压釜内衬中,通入氩气保护气体进行超声分散后放入高压釜中,使用马弗炉进行加热反应。升温速率为10℃/min,反应温度为250℃,保温时间为80min,冷却至室温后使用甲苯和正己烷离心洗涤3次,超声分散后保存在正己烷中。由此制得co纳米线。
46.(3)采用xrd对产物的物相组成进行分析,结果如图4左图所示,样品由co相组成,说明在反应中生成了co。采用vsm对产物的磁性能进行测试,结果如图4右图所示。
47.将实施例1和对比例中磁性能结果进行比较,如表1所示。
48.表1:本发明实施例及对比例中磁性能测试结果
[0049][0050]
综上所述,本发明通过表面活性剂辅助球磨与醇热法结合纳米片与纳米线在外加磁场作用下的特殊结构,可成功制备出具有核壳结构的(nd,tb)2fe
14
b/co样品,硬磁相均匀的分布在软磁相周围,使得软硬磁相间可产生更有效地交换耦合作用。相对于对比例1,在3t磁场下的剩余磁化强度和饱和磁化强度均有所提高,相比于对比例2,其矫顽力得到了极大提升,减少了稀土的消耗,为双各向异性粘接磁体的制备奠定了基础,提供了新思路。