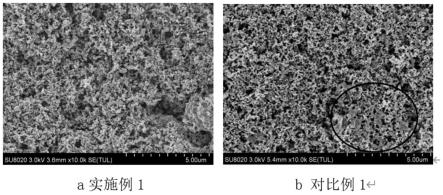
1.本发明属于燃料电池技术领域,具体涉及一种微孔层浆料,更进一步地,还涉及该微孔层浆料的制备方法,特别地,还涉及一种气体扩散层,更特别地,还涉及一种膜电极。
背景技术:2.质子交换膜燃料电池存在工作温度低、噪音小、无污染的优点,备受广大专家与学者的青睐。膜电极通常由质子交换膜、催化剂及气体扩散层组成,是质子交换膜燃料电池的关键组成部分。其中气体扩散层主要起到催化剂载体、支撑电极结构、排水传气、导电等作用,决定了燃料电池在高电流密度下的性能,决定了其性能的上限。随着双碳目标的提出,氢燃料电池应用场景的多元化,更高的功率密度已经明确纳入国家的氢燃料电池补贴标准,高性能的气体扩散层产品的需求迫在眉睫。
技术实现要素:3.本发明是基于发明人对以下事实和问题的发现和认识做出的:现有的微孔层制浆工艺中,普遍采用ptfe乳液、pvdf乳液或其混合物等乳液类物质作为疏水剂和粘结剂,乳液类物质原有的体系在分散过程中很容易被破坏,并且很难和导电碳基材料混合均匀,导致浆料不稳定、颗粒团聚、ptfe和碳粉分散不均匀等现象,另外,乳液类物质中的表面活性剂对微孔层浆料的状态及性能也会产生负面的影响。
4.本发明旨在至少在一定程度上解决相关技术中的技术问题之一。为此,本发明的实施例提出一种微孔层浆料及其制备方法,制得的微孔层浆料粒度小,分散均匀,稳定性好,长期存放而不易沉降和团聚。
5.本发明实施例的微孔层浆料的制备方法,包括如下步骤:
6.a、将导电碳基材料和乙烯-四氟乙烯共聚物纳米微球混合,在砂磨机中进行纳米研磨,形成导电碳基材料/乙烯-四氟乙烯共聚物纳米粉末;
7.b、将溶剂、表面活性剂和所述步骤a得到的导电碳基材料/乙烯-四氟乙烯共聚物纳米粉末混合,球磨,制得微孔层浆料;
8.c、将上述微孔层浆料进行边搅拌边真空脱泡,消除浆料中的气泡。
9.本发明实施例的微孔层浆料的制备方法带来的优点和技术效果,1、本发明实施例的方法中,先将导电碳基材料和乙烯-四氟乙烯共聚物纳米微球两种干料混合在砂磨机中进行干磨处理,由于碳基材料的吸附性,两者能充分均匀混合,形成导电碳基材料/乙烯-四氟乙烯共聚物纳米粉末,有效解决了现有技术中直接将导电材料与疏水剂乳液混合而导致的混合不均匀从而使浆料不稳定、颗粒团聚的问题;2、本发明实施例的方法中,采用乙烯-四氟乙烯共聚物纳米微球作为疏水剂和粘结剂,相比于乳液类物质,采用的原料便于储存和运输;3、本发明实施例的方法中,采用先干磨后湿磨的混合方式,在导电碳基材料和乙烯-四氟乙烯共聚物纳米微球充分吸附混合均匀的基础上,引入溶剂和表面活性剂等液体类物质,进行湿磨,制备得到的微孔层浆料粒度较小、分散均匀、较为稳定,能够存放较长时
间而不易发生沉降和团聚;4、本发明实施例制备的方法,得到浆料碳基材料和乙烯-四氟乙烯包覆性好,用于制备气体扩散层后,在使用过程中f元素流失少,有效延长了燃料电池组件的使用寿命;5、本发明实施例制备的微孔层浆料无气泡,利于涂布;6、本发明实施例的方法,工艺简单,易于工业化推广应用。
10.在一些实施例中,所述步骤a中,所述导电碳基材料包括导电炭黑、乙炔黑、导电石墨及碳纳米管中的至少一种。
11.在一些实施例中,所述步骤a中,所述导电碳基材料与乙烯-四氟乙烯共聚物纳米微球的质量比为2-4:1。
12.在一些实施例中,所述步骤a中,所述研磨机的转速为1000-8000r/min,研磨时间为10-60min。
13.在一些实施例中,所述步骤b中,所述溶剂包括水、乙醇、异丙醇、正丙醇、乙二醇、丙三醇中的一种或多种混合液;所述表面活性剂包括聚乙烯基吡咯烷酮或x-100中的至少一种。
14.在一些实施例中,还包括步骤c,将步骤b制得的微孔层浆料进行真空脱泡处理,同时进行搅拌。
15.在一些实施例中,所述步骤c中,所述真空脱泡处理的真空度为-0.05~-0.095mpa,搅拌速度为:50-500r/min,搅拌时间为30-60min。
16.本发明实施例还提供了一种微孔层浆料,采用本发明实施例的方法制得。本发明实施例的微孔层浆料,导电碳基材料和乙烯-四氟乙烯共聚物纳米微球充分吸附混合均匀,浆料粒度小、分散均匀并且稳定,能够长时间存放而不易发生沉降和团聚,并且,浆料中碳基材料和乙烯-四氟乙烯包覆性好,用于制备气体扩散层后,在使用过程中f元素流失少,有效延长了燃料电池组件的使用寿命。
17.本发明实施例还提供了一种气体扩散层,采用本发明实施例的微孔层浆料制得。本发明实施例的气体扩散层,具备本发明实施例微孔层浆料能够带来的所有优点,在此不再赘述。
18.本发明实施例还提供了一种膜电极,包括本发明实施例的气体扩散层。本发明实施例的膜电极,具备本发明实施例气体扩散层能够带来的所有优点,在此不再赘述。
附图说明
19.图1是实施例和对比例1制得的气体扩散层的sem图,其中,a为实施例1,b为对比例1;
20.图2是实施例和对比例1制得的单电池性能测试图;
21.图3是实施例1-3制得的单电池的性能测试图。
具体实施方式
22.下面详细描述本发明的实施例,所述实施例的示例在附图中示出。下面通过参考附图描述的实施例是示例性的,旨在用于解释本发明,而不能理解为对本发明的限制。
23.本发明实施例的微孔层浆料的制备方法,包括如下步骤:
24.a、将导电碳基材料和乙烯-四氟乙烯共聚物纳米微球混合,在砂磨机中进行纳米
研磨,形成导电碳基材料/乙烯-四氟乙烯共聚物纳米粉末;
25.b、将溶剂、表面活性剂和所述步骤a得到的导电碳基材料/乙烯-四氟乙烯共聚物纳米粉末混合,球磨,制得微孔层浆料。
26.本发明实施例的微孔层浆料的制备方法,先将导电碳基材料和乙烯-四氟乙烯共聚物纳米微球两种干料混合在砂磨机中进行干磨处理,由于碳基材料的吸附性,两者能充分均匀混合,形成导电碳基材料/乙烯-四氟乙烯共聚物纳米粉末,有效解决了现有技术中直接将导电材料与疏水剂乳液混合而导致的混合不均匀从而使浆料不稳定、颗粒团聚的问题;本发明实施例的方法中,采用乙烯-四氟乙烯共聚物纳米微球作为疏水剂和粘结剂,相比于乳液类物质,采用的原料便于储存和运输;本发明实施例的方法中,采用先干磨后湿磨的混合方式,在导电碳基材料和乙烯-四氟乙烯共聚物纳米微球充分吸附混合均匀的基础上,引入溶剂和表面活性剂等液体类物质,进行湿磨,制备得到的微孔层浆料粒度较小、分散均匀、较为稳定,能够存放较长时间而不易发生沉降和团聚;本发明实施例制备的方法,得到浆料碳基材料和乙烯-四氟乙烯包覆性好,用于制备气体扩散层后,在使用过程中f元素流失少,有效延长了燃料电池组件的使用寿命;本发明实施例的方法,工艺简单,易于工业化推广应用。
27.在一些实施例中,所述步骤a中,所述导电碳基材料包括导电炭黑、乙炔黑、导电石墨及碳纳米管中的至少一种,导电碳黑优选为xc-72r或bp2000;进一优选地,所述导电碳基材料与乙烯-四氟乙烯共聚物纳米微球的质量比为2-4:1,优选为3:1。本发明实施例中对导电碳基材料没有特别的限制,常用于微孔层浆料中的碳基材料都可以采用。本发明实施例进一步优选了导电碳基材料与乙烯-四氟乙烯共聚物纳米微球的配比,有利于进一步提高由微孔层浆料制得的气体扩散层的性能。
28.在一些实施例中,所述步骤a中,所述研磨机的转速为1000-8000r/min,研磨时间为10-60min。本发明实施例中优选了干磨过程中研磨机的转速和研磨时间,转速太低或者研磨时间过短会使乙烯-四氟乙烯共聚物纳米微球无法充分的吸附到导电碳基材料上,两者无法充分混合,转速过高、研磨时间过长会导致研磨机内部温度偏高,造成研磨机内粉末原有结构发生变化。
29.在一些实施例中,所述步骤b中,所述溶剂包括水;所述表面活性剂包括聚乙烯基吡咯烷酮或x-100中的至少一种。本发明实施例中,对溶剂和表面活性剂没有特别要求,微孔层浆料中常用的溶剂和表面活性剂都可以采用。
30.在一些实施例中,还包括步骤c,将步骤b制得的微孔层浆料进行真空脱泡处理,同时进行搅拌。优选地,所述真空脱泡处理的真空度为-0.05~-0.095mpa,这里的真空度指表压,搅拌速度为:50-500r/min,搅拌时间为30-60min。本发明实施例的方法中,对制得的微孔层浆料进一步进行真空脱泡处理,能够有效除去微孔层浆料中的气泡,有利于改善微孔层涂布的表观,提高了微孔层表面的平整度,增加了气体扩散层和催化层的接触,降低了接触电阻,从而提升了电池的性能。本发明实施例中进一步优选了真空脱泡处理的真空度和搅拌速度,真空度过高也即绝对压力过低,会导致微孔层浆料搅拌不充分,无法完全去除微孔层浆料中的气泡;真空度过低也即绝对压力过高或者搅拌速度过低,会使微孔层浆料中的气泡去除不够彻底;搅拌速度过快,会导致微孔层浆料的气泡二次产生,脱泡效果不理想。
31.本发明实施例还提供了一种微孔层浆料,采用本发明实施例的方法制得。本发明实施例的微孔层浆料,导电碳基材料和乙烯-四氟乙烯共聚物纳米微球充分吸附混合均匀,浆料粒度小、分散均匀并且稳定,能够长时间存放而不易发生沉降和团聚,并且,浆料中碳基材料和乙烯-四氟乙烯包覆性好,用于制备气体扩散层后,在使用过程中f元素流失少,有效延长了燃料电池组件的使用寿命。
32.本发明实施例还提供了一种气体扩散层,采用本发明实施例的微孔层浆料制得。本发明实施例的气体扩散层,具备本发明实施例微孔层浆料能够带来的所有优点,在此不再赘述。
33.本发明实施例还提供了一种膜电极,包括本发明实施例的气体扩散层。本发明实施例的膜电极,具备本发明实施例气体扩散层能够带来的所有优点,在此不再赘述。
34.下面结合实施例和附图详细描述本发明。
35.实施例1
36.一、微孔层浆料的制备
37.将质量比为2:1的导电炭黑xc-72r和乙烯-四氟乙烯共聚物纳米微球混合,在纳米研磨机中纳米研磨30min,控制研磨机转速为7000r/min,之后将研磨后的混合粉末、溶剂超纯水以及表面活性剂聚乙烯基吡咯烷酮在烧杯中磁力搅拌20min进行预混合,最后放入球磨机中球磨2h,将球磨后得到的浆料进行真空脱泡处理,控制真空度为-0.9mpa,同时进行搅拌,搅拌速度为400r/min,搅拌时间为60min,经真空脱泡处理后得到均一稳定的亮黑色油墨状微孔层浆料。
38.二、气体扩散层的制备
39.微孔层的涂布:采用刮刀涂布的方式将本实施例制得的微孔层浆料凃敷至碳纸基材上,在80℃下烘干,制得气体扩散层;
40.热处理:将涂布后得到的气体扩散层进行高温热处理,热处理温度为360℃,热处理时间为20min。
41.本实施例制得的气体扩散层的sem图见图1a,由图中可以看出导电碳基材料和乙烯-四氟乙烯共聚物疏水材料包覆的均一性优异。
42.三、膜电极的制备
43.将本实施例制得的气体扩散层与ccm组合制成膜电极。
44.四、单电池组装与测试
45.将本实施例制得的膜电极组装成单电池,采用燃料电池测试系统进行电池性能测试,测试条件:电池温度:t=80℃,加湿度:rh=40%/40%,背压:bp=100kpa/100kpa,过量系数:sto=1.5/2.0。测试结果见图2和图3,电池的性能为0.65v@1410ma/cm2。
46.本实施例制得的微孔层浆料在室温下存放一周不沉降,不团聚,浆料仍呈现亮黑色油墨状。
47.实施例2
48.与实施例1的制备方法相同,不同之处在于导电炭黑xc-72r和乙烯-四氟乙烯共聚物纳米微球的质量比为3:1。
49.将本实施例制得的膜电极组装成单电池,进行性能测试,测试条件与实施例1相同,测试结果见图3,电池的性能为0.65v@1600ma/cm2。
50.本实施例制得的微孔层浆料在室温下存放一周不沉降,不团聚,浆料仍呈现亮黑色油墨状。
51.实施例3
52.与实施例1的制备方法相同,不同之处在于导电炭黑xc-72r和乙烯-四氟乙烯共聚物纳米微球的质量比为4:1。
53.将本实施例制得的膜电极组装成单电池,进行性能测试,测试条件与实施例1相同,测试结果见图3,电池的性能为0.65v@1505ma/cm2。
54.本实施例制得的微孔层浆料在室温下存放一周不沉降,不团聚,浆料仍呈现亮黑色油墨状。
55.实施例4
56.与实施例1的制备方法相同,不同之处在于取消真空脱泡处理步骤。
57.将本实施例制得的膜电极组装成单电池,进行性能测试,测试条件与实施例1相同,电池的性能为0.65v@1350ma/cm2,与实施例1相比,电池的性能略低,这主要是由于本实施例未进行真空消泡处理,微孔层表观平整度不如实施例1,电池接触电阻大导致了性能呈现下降。
58.本实施例制得的微孔层浆料在室温下存放一周不沉降,不团聚,浆料仍呈现亮黑色油墨状。
59.实施例5
60.与实施例1的制备方法相同,不同之处在于真空脱泡处理中,控制真空度为-0.05mpa。
61.将本实施例制得的膜电极组装成单电池,进行性能测试,测试条件与实施例1相同,电池的性能为0.65v@1380ma/cm2。
62.本实施例制得的微孔层浆料在室温下存放一周不沉降,不团聚,浆料仍呈现亮黑色油墨状。
63.实施例6
64.与实施例1的制备方法相同,不同之处在于真空脱泡处理中,控制搅拌速度为100r/min。
65.将本实施例制得的膜电极组装成单电池,进行性能测试,测试条件与实施例1相同,电池的性能为0.65v@1400ma/cm2。
66.本实施例制得的微孔层浆料在室温下存放一周不沉降,不团聚,浆料仍呈现亮黑色油墨状。
67.实施例7
68.与实施例1的方法相同,不同之处在于研磨机转速为3000r/min。
69.将本实施例制得的膜电极组装成单电池,进行性能测试,测试条件与实施例1相同,电池的性能为0.65v@1330ma/cm2。
70.本实施例制得的微孔层浆料在室温下存放一周不沉降,不团聚,浆料仍呈现亮黑色油墨状。
71.对比例1
72.与实施例1的方法相同,不同之处在于取消干磨步骤,导电炭黑xc-72r和乙烯-四
氟乙烯共聚物纳米微球混合后不在纳米研磨机中进行纳米研磨,而是直接与水和表面活性剂聚乙烯基吡咯烷酮进行预混合,之后球磨,真空脱泡处理,制得微孔层浆料。
73.采用与实施例1相同的方法制备气体扩散层和膜电极,制得的气体扩散层的sem图见图1。
74.将对比例1制得的膜电极组装成单电池,进行性能测试,测试条件与实施例1相同,测试结果见图2,电池的性能为0.65v@1300ma/cm2。
75.通过图2可以看出,实施例1明显优于对比例1的电池性能,尤其是高电流密度下(传质极化区),实施例1的电池性能优势愈加明显,这主要是由于实施例的微孔层浆料对导电碳基材料和乙烯-四氟乙烯共聚物纳米微球先采用了干磨处理,使微孔层浆料中导电碳基材料和乙烯-四氟乙烯共聚物疏水材料包覆的均一性更好,有利于提升电池的水气管理能力,尤其是大电流密度下,电池水产生较多时,具有更明显的优势。
76.对比例1制得的微孔层浆料室温下存放一周,发生明显沉降,溶剂和碳粉分相。
77.对比例2
78.与实施例1的方法相同,不同之处在于研磨机转速为500r/min。
79.将对比例2制得的膜电极组装成单电池,进行性能测试,测试条件与实施例1相同,电池的性能为0.65v@1200ma/cm2。
80.对比例2制得的微孔层浆料室温下存放一周,未发生明显沉降。
81.对比例3
82.与实施例1的方法相同,不同之处在于研磨机转速为15000r/min。
83.将对比例3制得的膜电极组装成单电池,进行性能测试,测试条件与实施例1相同,电池的性能为0.65v@1050ma/cm2。
84.对比例3制得的微孔层浆料室温下存放一周,未发生明显沉降。
85.对比例4
86.与实施例1的方法相同,不同之处在于真空脱泡处理过程中,控制搅拌的转速为800r/min。
87.将对比例4制得的膜电极组装成单电池,进行性能测试,测试条件与实施例1相同,电池的性能为0.65v@1100ma/cm2。
88.对比例4制得的微孔层浆料室温下存放一周,未发生明显沉降。
89.在本发明中,术语“一个实施例”、“一些实施例”、“示例”、“具体示例”、或“一些示例”等意指结合该实施例或示例描述的具体特征、结构、材料或者特点包含于本发明的至少一个实施例或示例中。在本说明书中,对上述术语的示意性表述不必须针对的是相同的实施例或示例。而且,描述的具体特征、结构、材料或者特点可以在任一个或多个实施例或示例中以合适的方式结合。此外,在不相互矛盾的情况下,本领域的技术人员可以将本说明书中描述的不同实施例或示例以及不同实施例或示例的特征进行结合和组合。
90.尽管上面已经示出和描述了本发明的实施例,可以理解的是,上述实施例是示例性的,不能理解为对本发明的限制,本领域的普通技术人员在本发明的范围内可以对上述实施例进行变化、修改、替换和变型。