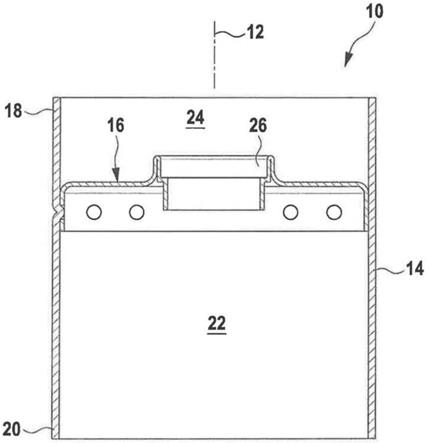
1.本发明涉及一种用于制造壳体的方法和装置,该壳体具有盖和围绕壳体的纵向轴线延伸的套筒形壳体壁,所述盖在壳体壁的纵向端部之间的预定位置处横向于纵向轴线地设置在壳体壁内。
背景技术:2.这样的壳体例如可以是用于电动马达的壳体。盖可以有一个用于马达轴的轴承法兰。盖位于壳体壁的内部,即在与壳体壁的两个纵向端部间隔开的位置处位于由壳体壁成型的空腔中。盖将壳体的内部划分为第一子空间,该第一子空间用于容纳电动马达的定子,而另一子空间例如可以容纳用于电动马达的控制电子装置。
3.由于盖位于壳体的空腔中,因此这种复杂的壳体不能使用诸如深拉的传统成型工艺由坯件一体制成。可以设想使用压铸工艺一体式或整体式制造这样的壳体。然而,通过压铸生产的壳体具有成本高的缺点。
4.还可以想到这样一种原理,其中,这种复杂的壳体由单独的零件制造,每个零件在成型过程中由坯件制成,这些零件在单独制造之后组装在一起。例如,套筒状的壳体壁和盖可以分别由一个坯件在深拉工艺中制造,然后可以将盖插入壳体壁内的预定位置。然而,在相应的分离装置上分别用一个工具生产单个零件在制造成本方面也是不利的。
技术实现要素:5.因此,本发明基于这样的目的:提供一种制造开头所述类型的壳体的方法,利用该方法可以以低制造成本制造这种壳体。
6.本发明还基于这样的目的:提供一种用于制造这种壳体的装置。
7.所述目的的实现在于根据本发明的方法,其包括:
[0008]-提供壳体的前体,其中,盖与壳体壁一体地成型并且盖设置在壳体壁的纵向端部之一处,
[0009]-将盖与壳体壁分离,
[0010]-使盖相对于壳体壁沿纵向轴线的方向从一个纵向端部移动到预定位置。
[0011]
因此,根据本发明的方法脱离了这种通过首先将壳体的各个部分单独制造然后将其组装来制造复杂壳体的构思。取而代之的是,首先提供壳体的前体,在前体中,盖与壳体壁一体成型,即整体地成型,并且盖被布置在壳体壁的纵向端部之一处。
[0012]
壳体的整体式前体可以有利地通过传统的成型工艺在成型装置中由单个坯件制成。在壳体的前体中,盖在横向于纵向轴线的方向上已经处于正确的位置,因此与单独制造盖和壳体壁相比,有利地不需要在这方面的定位过程。然而,盖尚未处于壳体壁内的纵向端部之间的轴向预定位置处。因此,根据本发明的方法还提供了在制造壳体的前体之后将盖与壳体壁分离并且用于将其相对于壳体壁沿壳体壁的纵向轴线从一个纵向端部(盖在壳体前体中所位于的端部)移动到预定位置(期望位置)并因此定位盖。在移动到所期望位置之
后,盖可以在期望位置与壳体壁结合。
[0013]
根据本发明的方法的特征在于,盖的分离和定位(移动)以及必要时壳体的前体的生产以及必要时的结合可以在一条生产线/一个生产设施上进行。在这种情况下,前体的生产、盖的分离和定位以及必要时的结合可以在压制循环中进行。同一生产线还可以包括一个结合站。
[0014]
根据本发明的用于执行根据本发明的方法的装置包括:
[0015]
用于将盖与壳体壁分离的分离装置,以及
[0016]
定位装置,其用于使盖相对于壳体壁沿纵向轴线移动到预定位置。
[0017]
优选地,该装置包括用于制造壳体的前体的制造装置。此外,该装置优选地包括用于在预定位置将盖结合到壳体壁的结合装置。
[0018]
优选地,壳体的前体的生产与盖的分离和移位在同一生产线的不同工作站中进行。为此,根据本发明的装置优选地具有用于制造壳体前体的制造装置。
[0019]
从而进一步减少了制造壳体的时间和成本。
[0020]
在根据本发明的方法中,提供壳体的前体优选地包括由同一坯件一体式地、即整体地成型壳体壁和盖。
[0021]
所有在一个或多个成型阶段中被执行的常规成型工艺,诸如深拉、反向拉伸(st
ü
lpziehen)、颈缩/收缩(einziehen),都可以用作成型工艺。
[0022]
为此,根据本发明的装置可以包括成型装置,用于在一个或多个成型阶段中将盖和壳体壁由同一的坯件一起一体地成型。
[0023]
在该方法的另一个优选实施例中,提供壳体的前体包括成型具有裙部的盖,该裙部沿壳体壁的纵向方向在壳体壁的部分长度上并周向地围绕纵向轴线延伸。
[0024]
该措施的优点在于,裙部提供了盖与壳体壁内侧的平坦/面状邻接,因此提供了用于将盖结合到壳体壁的足够的面。
[0025]
进一步优选地,裙部的外径对应于壳体壁的内径。
[0026]
在此有利的是,裙部无气隙地贴靠在壳体壁的内表面上,从而在盖移动进入期望位置后无需额外材料所述盖就可以通过裙部以压力密封的方式结合到壳体壁。裙部的外径可以与壳体壁的内径相适配,使得盖将其自身保持为抵靠在壳体壁的内表面的期望位置。
[0027]
在该方法的另一优选实施例中,所述盖以机械地、热力地(thermisch)和/或热力机械地(thermomechanisch)结合至壳体壁。
[0028]
如在进一步的实施例中可选地提供的,可以通过使壳体壁与盖的裙部中的孔接合、例如通过将壳体壁压入裙部中的孔中来实现机械结合。这里的另一个优点是,通过壳体壁接合在裙部的孔中,所述盖被防止相对于壳体壁旋转。代替将壳体壁压入盖的裙部的孔中,也可以完全无孔地进行机械结合,例如通过压接连接,例如弯折、钉入/咬合等。
[0029]
裙部的穿孔可以作为壳体的前体的生产的一部分来进行。因此,在优选实施例中,根据本发明的装置包括用于对盖的裙部进行穿孔的穿孔装置。在该装置的另一个实施例中,结合装置可以布置成将壳体壁与裙部的孔接合。
[0030]
热力结合可以包括例如将盖焊接到壳体壁。热力机械结合可以包括热力结合和机械结合的组合,例如,可以通过施加热来执行机械结合。
[0031]
优选地,盖与壳体壁的结合与盖的分离和移位在相同的装置中执行。
[0032]
在该方法的另一个优选实施例中,提供壳体的前体包括将盖成型为轴承法兰。
[0033]
轴承法兰可以设计成容纳轴。轴承法兰的中心开口可以在壳体壁和盖的一体成型期间引入,即在盖与壳体壁分离之前引入。
[0034]
在该装置的另一优选实施例中,分离装置具有分离柱塞和分离模具,带盖的壳体壁可以放置在分离柱塞上,分离模具被设计为将盖与壳体壁分离。
[0035]
分离模具可以例如具有周向切割边缘,该周向切割边缘作用在盖到壳体壁的过渡处并且通过切割模具和分离柱塞的相对运动将壳体壁从盖上剪断或切断。分离装置的这种设计的优点在于它可以以简单的方式集成到压力机中。
[0036]
定位装置优选地具有推动器,该推动器设计为使盖相对于壳体壁移位。
[0037]
这种推动器也可以容易地集成到压力机中。例如,推动器可以从上方作用于盖并且在盖已经与壳体壁分离之后将其相对于壳体壁移位到期望的位置。
[0038]
使用根据本发明的方法和装置,重量轻的复杂壳体能够在花费很少的时间和成本的情况下,在单个装置或生产线/生产设施中以很少的工具从单个坯件中生产处理。
[0039]
为了本发明的目的,“坯件(platine)”被理解为具有相同材料质量的板坯件(blechplatine),或所谓的拼装板坯(tailored blank),即可以由不同的材料质量和板材厚度构成的板坯件,或轧制板坯(walzplattierte blechplatine)。坯件的材料是金属的,例如钢或铝。由不同金属或由金属和塑料制成的可成型的复合材料也是可能的。
[0040]
进一步的优点和特征由以下描述和附图得出。
[0041]
应当理解,上述特征和下面要解释的特征不仅可以以在每种情况下指出的组合使用,而且可以以其他组合使用或单独使用,而不背离本发明的范围。
附图说明
[0042]
本发明的示例性实施例在附图中示出并且在下文中参考附图进行更详细的描述。其中:
[0043]
图1示出沿壳体的纵向轴线的剖视图。
[0044]
图2示出处于制造壳体的方法的工艺阶段中的图1中的壳体的前体;
[0045]
图2a示出生产前体的坯件;
[0046]
图3示出制造图1中的壳体的方法的另一个工艺阶段;
[0047]
图4示出制造图1中的壳体的方法的另一个工艺阶段;
[0048]
图5示出穿过用于制造图1中的壳体的装置的工作站的处于工作位置的一部分的纵向剖视图;
[0049]
图6示出穿过所述装置的所述工作站的纵向剖视图,其中所述工作站的另一部分处于另一工作位置;
[0050]
图7示出穿过图6中工作站的处于另一工作位置的纵向剖视图;
[0051]
图8示出穿过图6中工作站的处于另一工作位置的纵向剖视图;
[0052]
图9示出穿过图6中工作站的处于另一工作位置的纵向剖视图;
[0053]
图10示出穿过图6中工作站的处于另一工作位置的纵向剖视图;
[0054]
图11示出图5中的工作站处于另一个工作位置的一部分;和
[0055]
图12示出图5中的工作站处于又一个工作位置的一部分。
具体实施方式
[0056]
图1在沿着壳体的纵向轴线12的纵向剖视图中示出了用通用附图标记10标记的壳体。壳体10关于纵向轴线12是旋转对称的,尽管非旋转对称的几何形状也是可能的。
[0057]
壳体10具有盖16和围绕纵向轴线12延伸的套筒形壳体壁14。壳体10因此成型为多个部分。在本例中,在不限制通用性的情况下,壳体10由两部分构成,即壳体壁14和盖16。壳体10也可以具有多于两个的部分。然而,如稍后将描述的,盖16和壳体壁14没有被制造为分开的单独部件,而是由一个坯件(platine)一体地制造。
[0058]
盖16在壳体壁14内布置在第一纵向端部18和第二纵向端部16之间的预定位置处并且横向于壳体的纵向轴线12地延伸。盖16的预定位置与两个纵向端部间隔开。如后所述地,盖16与壳体壁14结合。
[0059]
壳体10整体由金属板(例如钢板或铝板)制成。其他可以在成型工艺中成型的材料,例如金属和塑料的混合材料,也是可能的。盖16的壁厚在图1中示出为不同于壳体壁的壁厚,但应当理解,盖16和壳体壁14的壁厚也可以相同。不同的壁厚例如可以通过使用所谓的拼装板坯(tailored blank)或轧制板坯(walzplattierte platine)作为起始坯件来实现。
[0060]
例如,壳体10可以是用于电动马达的壳体,其中,壳体10内部的第一子空间22用于接纳电动马达的定子,而壳体10内部的第二子空间24用于接纳马达的控制电子装置。盖16将两个区域22和24隔开。盖16可以构造为如图所示的轴承座,在这种情况下,盖16包括轴承法兰26。轴承法兰26可以用于接纳马达的轴承轴。
[0061]
盖16在壳体10的其他应用中也可以具有不同的几何形状,即,所述轴承法兰可以具有不同的构造或可以被省略。
[0062]
由于盖16布置在壳体壁14的内侧上,即布置在壳体壁14的纵向端部18和20之间的壳体10的内部空间中,壳体10可以被描述为复杂壳体。这种复杂的壳体可以一体地制造,即整体地制造,而不是制造为由单个坯件成型的部件。
[0063]
参照图2至图4,下面描述制造壳体10的方法。
[0064]
参考图2,提供了壳体10的前体28。在壳体10的前体28中,盖16与壳体壁14一体地成型并且布置在壳体壁14的纵向端部之一处,在这里其布置在纵向端部18处。
[0065]
由于盖16在前体28中布置在壳体壁14的纵向端部之一处,因此前体28可以在常规成型工艺中通过使壳体壁14和盖16由同一坯件一起成型而被一体地制造,即整体地制造。图2a(未按比例)示出坯件29。坯件29可以是单片的、拼装的坯件或轧制包覆的(walzplattiert)。
[0066]
作为成型壳体10的前体28的一部分,盖16成型有裙部30,裙部30沿壳体壁14的纵向方向在壳体壁14的部分长度上并且沿圆周方向围绕纵向轴线12延伸。裙部30通过前体28中的肩部32一体地,即整体地连接到壳体壁14。裙部具有对应于壳体壁14的内径d1的外径da。裙部30的外径da从而小于壳体壁14的外径。
[0067]
当由同一个坯件成型壳体10的前体28时,还成型轴承法兰26。为了由坯件29成型壳体10的前体28,可以应用成型工艺深拉、反向拉深、反向/翻边,以及机加工工艺穿孔(用于轴承法兰26的通孔),还可以对通孔的边缘进行切割(durchstellen)和校准。
[0068]
此外,裙部30可以作为制造壳体10的前体28的一部分被穿孔。在图2中示出示例性
的孔34、36、38、40、42。孔34-42可以围绕纵向轴线12围绕裙部30的外周均匀地间隔开。下面将描述对裙部30进行穿孔的功能。
[0069]
图3示出制造壳体10的方法的一个工艺阶段,在图2中的壳体10的前体28中盖16与壳体壁14分离。分离发生在肩部32处,即盖16到壳体壁14的过渡处。分离过程将在后面参考相应装置的实施例更详细地描述。
[0070]
在将盖16与壳体壁14分离之后,盖16根据箭头44沿纵向轴线12相对于壳体壁14移位到图1和图4所示的预定位置中。基于裙部30的外径相对于壳体壁14的内径的上述尺寸,裙部30的外表面紧贴壳体壁14的内表面,如图4所示。裙部30的外径相对于壳体壁14的内径的尺寸可以使得盖16基于相应的摩擦配合而即使不与壳体壁14结合也自己保持在根据图4的预定位置。
[0071]
在根据图4的下一工艺阶段中,盖16结合到壳体壁14。作为结合工艺可以使用机械结合工艺、热力机械结合工艺或热力结合工艺。例如,裙部30可以焊接到壳体壁14。周向焊接可以用于以压力密封的方式将裙部30结合到壳体壁14。盖16与壳体壁14的机械结合可以这样构建,即,使壳体壁14与穿孔(图2中的孔34-42)接合,如在位置46处所示。这可以例如通过将壳体壁14压入孔34-42中来实现,这具有壳体10对外部保持压力密封的优点。如果不需要壳体10的压力密封设计,壳体壁14也可以在裙部30的穿孔区域中被切割并且壳体壁14的材料可以折弯到孔34-42中。
[0072]
壳体壁14的材料的到裙部30的穿孔中的接合防止盖16相对于壳体壁14旋转。
[0073]
盖16与壳体壁14的机械结合也可以完全无孔地完成,例如诸如弯折(toxen)、咬合等的压接连接。
[0074]
盖16与壳体壁14的热力机械结合也是可以想到的。
[0075]
前述的由坯件29成型壳体10的前体28、将盖16与壳体壁14分离、将盖16移位到壳体壁14的内部空间中以及将盖16结合到壳体壁16的工艺可以全部在同一装置(其具有相应的多个工作站或阶段)中进行。这将在下面参考图5至图10更详细地描述。
[0076]
图5和图6示出用于制造图1中的壳体10的装置的工作站50。该装置在下文中参照将盖16与壳体壁14分离以及将盖16相对于壳体壁14定位的操作来描述。
[0077]
用于制造壳体10的整个装置还可包括用于在一个或多个成型阶段中将盖16和壳体壁14由同一坯件一体成型的成型装置,以及另外的工作站(例如穿孔、校准、切割),以便制造根据图2的壳体10的前体28。由于这种具有多个成型阶段的成型装置和加工装置是本领域技术人员所熟悉的,因此在附图中未示出并且在此不再赘述。
[0078]
图5示出工作站50的下部52。下部52包括固定的平台或底座54。下部52还包括可根据双箭头58竖直移动的可移动工作台56。下部52进一步包括具有缸体62和活塞64的气压或液压弹簧60。活塞64也可根据双箭头58竖直移动。此外,下部52具有分离柱塞66,分离柱塞也可以根据双箭头58竖直移动。分离柱塞66是用于将盖16与壳体壁14分离的分离装置的一部分。下部52具有向上移动器68(hochbringer),向上移动器68可以根据双箭头58竖直移动。
[0079]
装置50还包括上部70,该上部70在图6中与所述下部52一起示出。上部70包括框架或桥部72、74。桥部72、74(根据双箭头58)可竖直移动。上部70还包括切割模具78,其与分离柱塞66一起构成用于将盖16从壳体壁14分离的分离装置。切割模具74可根据双箭头58移
动。
[0080]
上部70还包括固定在桥部上的推动器或滑块80,用于在盖16已经与壳体壁14分离之后使盖16相对于壳体壁14移位。上部70还包括气压或液压弹簧82、84和间隔件86。
[0081]
根据图5,壳体10的前体28在其在装置的成型装置中制造之后被放置在分离柱塞66上。在这种情况下,分离柱塞66位于气压或液压弹簧60的活塞64上,其中活塞64处于其伸出位置。向上移动器68处于其升高位置。
[0082]
根据图6,装置50的上部70现在向下部52移动。通过进一步向下移动上部70,推动器80推动或挤压所述壳体的前体28整体在分离柱塞66上方进入图7所示的位置。在此过程中,向上移动器68同样通过间隔件86被下压。切割模具78也向下移动。
[0083]
在图7中,前体28现在完全位于分离柱塞66上,其中盖16的内侧贴靠在分离柱塞66的顶部上。向上移动器68和框架74贴靠在工作台56上。
[0084]
图7示出紧接在盖16与壳体10的前体28的壳体壁14分离之前的时刻。
[0085]
图8示出将盖16与壳体10的前体28的壳体壁14分离的分离过程。通过切割模具78和分离柱塞66之间的相对运动,盖16与壳体壁14的分离发生在盖10的裙部30和壳体壁14的纵向端部18之间的肩部32处。
[0086]
切割模具78保持在适当位置并且上部气压或液压弹簧82、84缩回。
[0087]
根据图9,通过进一步向下移动上部70,盖16与分离柱塞66一起被推动器80根据箭头88下压。在此过程中,壳体壁14保持固定。因此,通过根据箭头88向下移动上部70,盖16移位到由壳体壁14限定的内部空间中,直到盖16已经到达相对于壳体壁14的轴向预定位置,如图10所示。气压或液压弹簧60在盖16相对于壳体壁14移位期间缩回,气压或液压弹簧82和84也是如此。
[0088]
分离柱塞66现在处于下止点位置,装置50的上部70也是如此。气压或液压弹簧60被锁定在适当位置。然后将上部70从下部52移开,如图11所示。
[0089]
然后向上移动器68向上移动以从分离柱塞66上移除壳体10,如图12所示。现在,在装置的另一个周期中,壳体10可以被转移到该装置的结合装置(未示出),在结合装置中盖16结合到壳体壁14,如上面参照图4所描述的。
[0090]
然而,盖16与壳体壁14的结合也可以在图11中所示的工艺阶段执行,即在壳体10从分离柱塞66移除之前执行。
[0091]
盖16与壳体壁14的上述分离以及盖16相对于壳体壁14移位到壳体壁14的内部可以在装置的压制周期中进行。分离和定位过程之前是成型操作,也处于压制循环中。在同一装置中,在分离和定位操作之后可进行盖16与壳体壁的结合。以这种方式,可以在压制循环中以简单的方式并且使用很少的工具来生产壳体10。