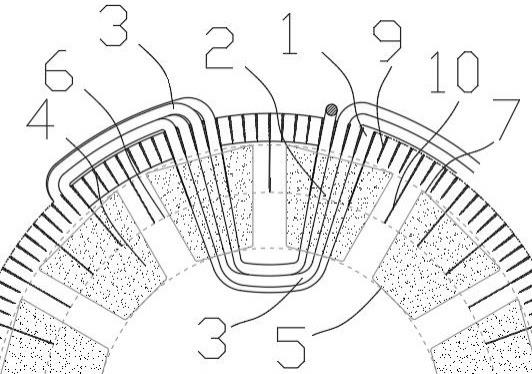
1.本发明涉及一种永磁盘式电机,具体涉及一种永磁盘式电机无铁芯电枢及其安装方法。
背景技术:2.盘式电机由于轴向尺寸短、结构紧凑,外形呈薄饼状,主要由定子和转子两部分组成。无刷电机的定子是电枢盘,转子是由铁轭盘和永磁体组成。
3.永磁盘式电机由于使用了永磁材料而无励磁损耗,定子没有铁芯,因此没有铁损耗,且定转子盘平行排列,使得电机效率比圆柱式电机高。现有技术中,永磁盘式电机的气隙长度空间受限,因为增加气隙长度会影响到气隙磁通密度减小的矛盾,提高电机绕组的槽满率是提高电机效率的有效途径。
4.盘式电机的内径和外径的差别比较大,造成外径处绕组空闲较多,而内径处绕组排线空间紧张,导致端部空间吃紧。每个线圈在端部互相叠压排列,而传统电机电枢外径处和内径处区域有富余空间未见加以利用。
5.以200w,3000r/min的电机为例,其电机效率只有不到80%左右。便携移动设备电机,如何提高电机效率,减少锂电池的用量,是亟待解决的技术问题。
技术实现要素:6.盘式电机电枢绕组的有效导体在空间沿径向呈辐射状分布,所以越靠近外径处绕组空闲的扇形区域越多,永磁体圈内、圈外有富余的空间可以利用。无铁芯结构的定子,是把线圈封装在绝缘材料内,压成盘状,制成无铁芯定子绕组盘。
7.本发明所采用的技术方案是:本发明的目的在于提供一种高功率密度盘式电机绕组线圈结构压延制备方法,以解决上述节约空间的技术问题,降低电枢电阻。
8.本发明采用圆铜线,漆包线绕制,成本低,选超大线径的漆包线,在线圈做功边,即有效边,经多次压延,变薄、变长,使之能够与气隙长度空间电枢的截面积匹配:如,一是在线圈做功边靠近永磁体外径处,绕组线圈空闲较多区域,在电机轴向看渐进变薄;二是在线圈做功边靠近永磁体内径处区域,在电机径向侧面看渐进变薄。平面看线圈做功边每个单根导体呈现扇面形状;侧向看线圈做功边呈现倒扇面形状。即永磁体外径处气隙短、内径处气隙长。
9.进一步地,所述永磁体内径处气隙增长到比理论值稍短,这样有利增加内径处磁密度,即所述内径处气隙导体的截面积比永磁体外径处截面积要有意稍小。
10.所述的线圈端部边截面积大于做功边截面积,至少在永磁体内圆至中心圆区域内的每根导体挤压使之自适应变形,填满槽截面。槽截面是指电枢盘做功边处的截面,满槽是指漆包线的漆包厚度加导线。
11.所述线圈内、外圈端部边的截面积大于永磁体外圆处导体截面积,永磁体外圆处
导体截面积大于永磁体内圆处导体截面积。
12.上述的卷绕压延制备方法,采用冗余设计工艺,得到的电枢线圈端部边截面积大于做功边截面积,是充分利用电枢线圈端部边空间冗余,采用超规格选大线径的漆包线来加工绕制,实际放大了线径,这样就能够大大降低电枢线圈电阻,提高电机效率。
13.所述内端部边定子绕组由各相绕组叠放,如a、b、c相叠放排列。三相做功边均布在一个平面上,以减少磁场区域的厚度,缩短气隙长度。
14.所述外端部边越过定子套壳体裸露在外,利用电机外部空气来散热。
15.所述定子套一端加工成环绕一周均布的齿。齿缝隙留给绕组导体通过。呈现梳子齿状的骨架。所述线圈每一根导体均被梳子齿夹持,一来给电枢提供稳固的骨架支撑,二来每一根导体的热量均利用梳子齿的定子套(9)散热。
16.进一步地,所述每一根绕组导体均平直延申出经过定子套外圆,在壳体外连接。壳体外的导体焊接、串联、并联工艺简单,容易操作,降低了生产成本,也方便电连控制器。以上导体串并联的灵活应用,可以自由调整电机的转速和功率。
17.进一步地,所述电枢线圈外端部边封装在定子套上,经壳体与轴承内圈固定连接。
18.本发明漆包线经绕制成线圈单元,再在做功边压延处理,使得槽满率更高、气隙平整、内径、外径空间利用率更高,对于高功率密度的电机设计和加工则非常有益。
19.本发明在永磁体内圆线到永磁体中心圆线区域内,导体槽满率为满槽状态,即导体被压制矩形或方形,绝缘层厚度小于0.1mm,每根导体相互无缝隙贴近。
20.进一步地,至少在永磁体的内圆至中心圆区域,每根导体相互无缝隙贴近,并且采用压延,挤压使之每根导体变成矩形,导体槽满率为满槽状态。并且采用挤压使之每根导体自适应变形,填满槽状态。至少在永磁体内圆至中心圆区域内的每根导体被挤压使之自适应变形,填满槽截面状态。满槽不是指绝对满槽,可以存在仅剩余的工艺角,方形或矩形的四个角,如r<0.2左右的圆角。
21.本发明电机无铁芯无骨架结构,在此基础上实现外圆区域有定子骨架式,用于导热散热、抗旋转扭矩,将一圈花瓣状线圈精确固定在平整的平面中,更加牢固。
22.盘式无铁芯电机,产生扭矩主要在永磁体外圆线到中心圆线区域,在此区域设置了抗旋转扭矩的骨架。
23.本发明在永磁体外圆处引入补强片,在花瓣状线圈外边缘,窄缝隙区域填充补强片。补强片为刚性体,如采用铝合金、不锈钢、陶瓷片、粉末烧结、热固性材料,模压后bmc封装。也可采用3d打印技术,实现定子骨架制作。
24.以200w,3000r/min的电机为例,其电机效率能够达到90%以上,在移动设备上使用可以节约10%锂电池的用量。
25.上述线圈在做功边靠近外径处渐进变薄,节约了气隙空间,气隙长度变短,外径处轭部靠近了一些,气隙磁通密度增加,提高了电机扭矩。
26.上述线圈做功边采用多次压延,在一定的空间内可以容纳的总导体数增加,提高了效率。
27.上述线圈做功边通过电枢拓扑几何或空间的变形处理,实现了线圈的不同部位的不同形状变形,来适应盘式电机在小气隙下,有效降低电枢绕组的电阻,从而提高了电机效率。
28.本发明提高绕组的空间利用率,同时在保证合理温升特性前提下,增大盘式电机的极限驱动电流、改善转矩特性及功率密度等。
29.本发明采用将圆铜线压延制备方法使做功边导体的结晶更加密实,导体变硬;结晶向电流方向变长,电阻降低。导体变硬有利于定子电枢盘提升刚性,抗变形,保证平整度。
30.下面结合附图和具体实施方式对本发明进一步说明:图1本发明实施例电枢a相一个线圈单元局部结构示意图;图2本发明实施例的电枢线圈剖视图和补强片示意图;图3本发明实施例的的盘式电机结构剖视图;图4本发明实施例的电枢内外圆处导体截面示意图;图5本发明实施例电枢三相绕组的a、b相示意图;图6本发明实施例的a、b、c相线圈示意图;图中:1、线圈;2、做功边;3、端部边;4、永磁体;5、内圆;6、中心圆;7、外圆;8、壳体;9、定子套;10、补强片;51、内圆处导体截面;71、外圆处导体截面。
31.如图1所示,本发明采用圆铜线或方形或矩形漆包线绕制,又以成本最低原则,优选圆漆包铜线,以波绕方式。以单层线电枢绕组为例:电枢线圈(1)在内圆端部边错位二层排列,做功边排列单层;如图2、4所示,以两层线电枢绕组为例:电枢线圈(1)在内圆端部边错位四层排列,做功边排列双层。
32.进一步地,所述线圈(1)采用多次多方向压延,指包含采用轧辊扎制,模具打遍,模具挤压等工艺,使电枢端部边截面积大于做功边截面积,大于1.5倍。如图3所示,靠近外圆(7)气隙长度变短。做功边(2)导体靠近外圆(7)变遍;体靠近内圆(5)变窄变厚。
33.所述的电枢端部边截面积大于做功边截面积,至少在永磁体内圆至中心圆区域内的每根导体被挤压使之自适应变形,填满槽截面。
34.进一步地,所述至少在永磁体内圆至中心圆区域内的每根导体被挤压使之自适应变形,包括在绕制前采用的如板材切割,冲压,整形工艺实现的方法。
35.如图2所示,本发明由永磁体构成的转子盘中间夹着定子电枢盘,永磁体下方即圈内空间冗余,线圈(1)内端部边采用多相叠放。
36.如图3、4所示,本发明永磁体对应处的导体线圈经过压延后形成的截面图,内圆处导体截面(51)、外圆处导体截面(71)。
37.如图1、5所示,定子套(9)靠近线圈(1)处,呈现梳子齿状,环绕一圈齿。定子套(9)右侧整的圈体与壳体(8)固定。所述线圈(1)每一根导体均被梳子齿夹持,一来给电枢提供稳固的骨架支撑,二来每一根导体的热量均利用梳子齿的定子套(9)散热。定子套(9)采用铝合金制作,散热性能更加好。
38.如图2、3所示,进一步地,线圈(1)每根导体的外端部边越过定子套(9)裸露在外,并且所述每一根导体均平直延申出经过定子套(9),在壳体外连接,如焊接、串联、并联。
39.所述一种盘式电机及定子线圈压延制造方法,包括线圈(1)、定子套(9),其特征在于,所述电枢线圈(1)外端部边封装在定子套(9)的外圈上,经壳体(8)与轴承内圈固定连接。
40.如图1、2所示,进一步地,所述电枢线圈单元缝隙夹持着复数个补强片(10),环绕均布,其厚度极薄,可以控制在只有0.2mm的厚度以下;可以控制在只有0.1mm的厚度以下。
41.图5本发明实施例电枢揭去一相的半片示意图,以6对极为例,在三相18个绕组单元的相互缝隙中,引入补强片(10),个数36片。引入片数是极对数乘以相数,再乘以2。
42.进一步地,所述补强片(10)为刚性体,如采用铝合金、不锈钢、陶瓷片、粉末烧结、热固性材料,模压后bmc封装,也可采用3d打印技术。所述补强片(10)竖直均布贴装在每个线圈(1)单元导体的外边侧,并经封装固定在定子套(9)上。补强片(10)内端口最大插入到永磁体(4)的中心圆(6)处。
43.如图2所示,所述电枢线圈a、b、c相密实均布,做功边(2)至少在永磁体内圆至中心圆区域内的每根导体填满槽截面。