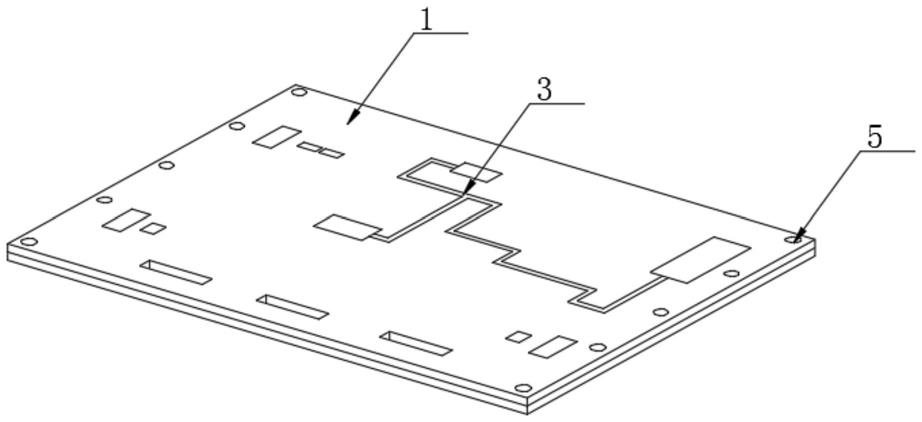
1.本发明涉及线路板技术领域,具体为一种全新锡导通工艺线路板及其制作工艺。
背景技术:2.电路板的名称有:陶瓷电路板,氧化铝陶瓷电路板,氮化铝陶瓷电路板,线路板,pcb板,铝基板,高频板,厚铜板,阻抗板,pcb,超薄线路板,超薄电路板,印刷(铜刻蚀技术)电路板等,电路板使电路迷你化、直观化,对于固定电路的批量生产和优化用电器布局起重要作用,电路板可称为印刷线路板或印刷电路板,英文名称为pcb、fpc线路板(fpc线路板又称柔性线路板柔性电路板是以聚酰亚胺或聚酯薄膜为基材制成的一种具有高度可靠性,绝佳的可挠性印刷电路板,具有配线密度高、重量轻、厚度薄、弯折性好的特点)和软硬结合板fpc与pcb的诞生与发展,催生了软硬结合板这一新产品,因此,软硬结合板,就是柔性线路板与硬性线路板,经过压合等工序,按相关工艺要求组合在一起,形成的具有fpc特性与pcb特性的线路板。
3.线路板的制作过程中,会将其表面进行镀锡,一般的操作都是在镀锡之前进行打孔,对于喷锡板,非塞孔的导通孔往往会藏锡,表现为导通孔不透光,藏锡的直接危害就是它可能跑出来黏附在焊盘上,形成锡珠,影响焊膏的印刷,更隐蔽的危害就是锡珠飞出来,对可靠性构成威胁。
技术实现要素:4.针对现有技术的不足,本发明提供了一种全新锡导通工艺线路板及其制作工艺,解决了在镀锡之前进行打孔,会造成通孔内藏锡的问题。
5.为实现以上目的,本发明通过以下技术方案予以实现:一种全新锡导通工艺线路板,包括正板与背板,该正板为单面板且背面涂覆一层热固胶,背板为铜(铝等金属类)箔,所述正板的背面与背板的正面通过正面或反面背胶相粘合,并且正板的表面和背板的底部均丝印有线路层,所述背板底部的两侧均设置有铜箔,并且正板与背板的表面均开设有通孔。
6.本发明还公开了一种全新锡导通工艺线路板的制作工艺,具体包括以下步骤:
7.s1、正板的加工:挑选合适的基板作为正板,然后在正板的背面粘贴背胶,对正板的表面进行线路丝印,丝印网板目数为90
‑
110t/cm2,丝印速度为2.5
‑
3.5m/min,丝印压力为0.6
‑
1mpa,然后对正板进行蚀刻操作,在正板上涂覆感光涂层后,在真空条件下进行曝光操作,去除正板上未被曝光部分的感光涂层,得到待蚀刻板,在25℃
‑
50℃的温度条件下,然后将其放置进蚀刻液中进行蚀刻操作,形成线路图案,然后运用高速高精度视觉处理技术自动检测pcb板上各种不同贴装错误及焊接缺陷;
8.s2、背板的加工:将背板的底部通过微粘膜贴附铜箔,然后对背板的底部进行线路丝印,丝印网板目数为90
‑
110t/cm2,丝印速度为2.5
‑
3.5m/min,丝印压力为0.6
‑
1mpa,然后对背板进行蚀刻操作,在背板上涂覆感光涂层后,在真空条件下进行曝光操作,去除背板上
未被曝光部分的感光涂层,得到待蚀刻板,在25℃
‑
50℃的温度条件下,然后将其放置进蚀刻液中进行蚀刻操作,形成线路图案,然后运用高速高精度视觉处理技术自动检测pcb板上各种不同贴装错误及焊接缺陷;
9.s3、整体加工:对正板和背板的正面都进行钻孔操作,然后通过正板背面的背胶将其与背板粘接在一起,然后将正板与背板之间进行冷压,冷压压力为10
‑
35mpa,挤压成型时间为15
‑
30s,然后自然晾干或者20
‑
50℃鼓风烘干,然后在正板的表面贴附白膜,然后利用热压机将白膜紧贴附在正板的表面,在背板底部不需焊接的线路和基材上涂上一层防焊阻剂,然后在正板的表面通过丝印的方式形成文字,然后在洁净的裸铜表面上,以化学的方法长出一层有机皮膜,然后将成型的线路板外形进行整理,最后对线路板本身的品质状况,包括:外观检验、尺寸/孔径的量测、性能测试等进行全面且最后一次的检验与测试,确保产品符合出货规格要求,进行包装之后就可以出厂。
10.优选的,所述s1中使用的背胶采用导热硅胶,导热硅胶是在硅橡胶的基础上添加了特定的导电填充物所形成的一类硅胶。
11.优选的,所述s1中,在去除所述覆合基材上未被曝光部分的感光涂层后,采用等离子设备去除所述待蚀刻板上的保留的感光涂层边缘处形成的毛边。
12.优选的,所述s3中对正板与背板进行钻孔的时候,其孔径一致。
13.有益效果
14.本发明提供了一种全新锡导通工艺线路板及其制作工艺。与现有技术相比具备以下有益效果:该全新锡导通工艺线路板,该正板为单面板且背面涂覆一层热固胶,背板为铜(铝等金属类)箔,所述正板的背面与背板的正面通过正面或反面背胶相粘合,并且正板的表面和背板的底部均丝印有线路层,所述背板底部的两侧均设置有铜箔,并且正板与背板的表面均开设有通孔,全新锡导通工艺线路板的制作工艺,具体包括以下步骤:s1、正板的加工,s2、背板的加工和s3、整体加工,通过在制作线路板的时候,正反面丝印线路、反面微粘膜铜箔,然后再进行正板与背板的分开打孔,之后再进行正板与背面的粘合,而且在正板与背面分来进行丝印线路之后,都会先分别进行自动光学检测,运用高速高精度视觉处理技术自动检测pcb板上各种不同贴装错误及焊接缺陷,与传统差别最大的是另外一面线路以转移贴合的方式生产,本设计可以通用双面smd/smt/com/倒装等封装后制造流程工艺,可以及时避免后续操作的失误,也可以提前发现问题并解决问题。
附图说明
15.图1为本发明结构的立体图;
16.图2为本发明背板底部的结构示意图;
17.图3为本发明的工艺流程图。
18.图中:1
‑
正板、2
‑
背板、3
‑
线路、4
‑
铜箔、5
‑
通孔。
具体实施方式
19.下面将结合本发明实施例中的附图,对本发明实施例中的技术方案进行清楚、完整地描述,显然,所描述的实施例仅仅是本发明一部分实施例,而不是全部的实施例。基于本发明中的实施例,本领域普通技术人员在没有做出创造性劳动前提下所获得的所有其他
实施例,都属于本发明保护的范围。
20.请参阅图1
‑
3,本发明提供三种种技术方案:一种全新锡导通工艺线路板,包括正板1与背板2,该正板1为单面板且背面涂覆一层热固胶,背板2为铜(铝等金属类)箔,正板1的背面与背板2的正面通过正面或反面背胶相粘合,并且正板1的表面和背板2的底部均丝印有线路层3,背板2底部的两侧均设置有铜箔4,并且正板1与背板2的表面均开设有通孔5。
21.其制作工艺包括以下实施例:
22.实施例一
23.s1、正板的加工:挑选合适的基板作为正板,然后在正板的背面粘贴背胶,对正板的表面进行线路丝印,丝印网板目数为100t/cm2,丝印速度为3m/min,丝印压力为0.8mpa,然后对正板进行蚀刻操作,在正板上涂覆感光涂层后,在真空条件下进行曝光操作,去除正板上未被曝光部分的感光涂层,得到待蚀刻板,在37℃的温度条件下,然后将其放置进蚀刻液中进行蚀刻操作,形成线路图案,然后运用高速高精度视觉处理技术自动检测pcb板上各种不同贴装错误及焊接缺陷;
24.s2、背板的加工:将背板的底部通过微粘膜贴附铜箔,然后对背板的底部进行线路丝印,丝印网板目数为100t/cm2,丝印速度为3m/min,丝印压力为0.8mpa,然后对背板进行蚀刻操作,在背板上涂覆感光涂层后,在真空条件下进行曝光操作,去除背板上未被曝光部分的感光涂层,得到待蚀刻板,在37℃的温度条件下,然后将其放置进蚀刻液中进行蚀刻操作,形成线路图案,然后运用高速高精度视觉处理技术自动检测pcb板上各种不同贴装错误及焊接缺陷;
25.s3、整体加工:对正板和背板的正面都进行钻孔操作,然后通过正板背面的背胶将其与背板粘接在一起,然后将正板与背板之间进行冷压,冷压压力为22mpa,挤压成型时间为22s,然后自然晾干或者35℃鼓风烘干,然后在正板的表面贴附白膜,然后利用热压机将白膜紧贴附在正板的表面,在背板底部不需焊接的线路和基材上涂上一层防焊阻剂,然后在正板的表面通过丝印的方式形成文字,然后在洁净的裸铜表面上,以化学的方法长出一层有机皮膜,然后将成型的线路板外形进行整理,最后对线路板本身的品质状况,包括:外观检验、尺寸/孔径的量测、性能测试等进行全面且最后一次的检验与测试,确保产品符合出货规格要求,进行包装之后就可以出厂。
26.实施例二
27.s1、正板的加工:挑选合适的基板作为正板,然后在正板的背面粘贴背胶,对正板的表面进行线路丝印,丝印网板目数为90t/cm2,丝印速度为2.5m/min,丝印压力为0.6mpa,然后对正板进行蚀刻操作,在正板上涂覆感光涂层后,在真空条件下进行曝光操作,去除正板上未被曝光部分的感光涂层,得到待蚀刻板,在25℃的温度条件下,然后将其放置进蚀刻液中进行蚀刻操作,形成线路图案,然后运用高速高精度视觉处理技术自动检测pcb板上各种不同贴装错误及焊接缺陷;
28.s2、背板的加工:将背板的底部通过微粘膜贴附铜箔,然后对背板的底部进行线路丝印,丝印网板目数为90t/cm2,丝印速度为2.5m/min,丝印压力为0.6mpa,然后对背板进行蚀刻操作,在背板上涂覆感光涂层后,在真空条件下进行曝光操作,去除背板上未被曝光部分的感光涂层,得到待蚀刻板,在25℃的温度条件下,然后将其放置进蚀刻液中进行蚀刻操作,形成线路图案,然后运用高速高精度视觉处理技术自动检测pcb板上各种不同贴装错误
及焊接缺陷;
29.s3、整体加工:对正板和背板的正面都进行钻孔操作,然后通过正板背面的背胶将其与背板粘接在一起,然后将正板与背板之间进行冷压,冷压压力为10mpa,挤压成型时间为15s,然后自然晾干或者20℃鼓风烘干,然后在正板的表面贴附白膜,然后利用热压机将白膜紧贴附在正板的表面,在背板底部不需焊接的线路和基材上涂上一层防焊阻剂,然后在正板的表面通过丝印的方式形成文字,然后在洁净的裸铜表面上,以化学的方法长出一层有机皮膜,然后将成型的线路板外形进行整理,最后对线路板本身的品质状况,包括:外观检验、尺寸/孔径的量测、性能测试等进行全面且最后一次的检验与测试,确保产品符合出货规格要求,进行包装之后就可以出厂。
30.实施例三
31.s1、正板的加工:挑选合适的基板作为正板,然后在正板的背面粘贴背胶,对正板的表面进行线路丝印,丝印网板目数为110t/cm2,丝印速度为3.5m/min,丝印压力为1mpa,然后对正板进行蚀刻操作,在正板上涂覆感光涂层后,在真空条件下进行曝光操作,去除正板上未被曝光部分的感光涂层,得到待蚀刻板,在50℃的温度条件下,然后将其放置进蚀刻液中进行蚀刻操作,形成线路图案,然后运用高速高精度视觉处理技术自动检测pcb板上各种不同贴装错误及焊接缺陷;
32.s2、背板的加工:将背板的底部通过微粘膜贴附铜箔,然后对背板的底部进行线路丝印,丝印网板目数为110t/cm2,丝印速度为3.5m/min,丝印压力为1mpa,然后对背板进行蚀刻操作,在背板上涂覆感光涂层后,在真空条件下进行曝光操作,去除背板上未被曝光部分的感光涂层,得到待蚀刻板,在50℃的温度条件下,然后将其放置进蚀刻液中进行蚀刻操作,形成线路图案,然后运用高速高精度视觉处理技术自动检测pcb板上各种不同贴装错误及焊接缺陷;
33.s3、整体加工:对正板和背板的正面都进行钻孔操作,然后通过正板背面的背胶将其与背板粘接在一起,然后将正板与背板之间进行冷压,冷压压力为35mpa,挤压成型时间为30s,然后自然晾干或者50℃鼓风烘干,然后在正板的表面贴附白膜,然后利用热压机将白膜紧贴附在正板的表面,在背板底部不需焊接的线路和基材上涂上一层防焊阻剂,然后在正板的表面通过丝印的方式形成文字,然后在洁净的裸铜表面上,以化学的方法长出一层有机皮膜,然后将成型的线路板外形进行整理,最后对线路板本身的品质状况,包括:外观检验、尺寸/孔径的量测、性能测试等进行全面且最后一次的检验与测试,确保产品符合出货规格要求,进行包装之后就可以出厂。
34.该产品的材料为:1、一面(下称a面)材料为:单面背胶基材(即在传统单面板背后用涂布机的方式涂覆一层专用特殊的热固胶),且背后一层离型保护膜。金属层可以纯铜、铝、铜包铝等用于导电类的金属即可。2、另一面材料(下称b面)为:单面铜箔背面黏贴一种承载膜。3、常规覆盖膜或白油。4、绝缘层材料包含:pi、pet等电子级绝缘材料。
35.通过在制作线路板的时候,正反面丝印线路、反面微粘膜铜箔,然后再进行正板与背板的分开打孔,之后再进行正板与背面的粘合,而且在正板与背面分来进行丝印线路之后,都会先分别进行自动光学检测,运用高速高精度视觉处理技术自动检测pcb板上各种不同贴装错误及焊接缺陷,可以及时避免后续操作的失误,也可以提前发现问题并解决问题。
36.可以理解的,1、该全新锡导通工艺线路板背面材料可以是承载膜铜,就是一种微
粘膜和铜箔贴合在一起,金属铜箔的厚度为5um以上;2、上述生产制程中需要进行承载膜转移制程,转移过程中需要撕掉承载膜,而承载膜只是制作过程中一个辅助物料;3、反面的线路制作工艺为:直接丝印线路、曝光线路、模冲线路和模切线路等线路制作工艺;4、锡导通位置可以设置在正面和可以设置在反面,可以根据不同的需求进行设置。
37.该产品生产工艺流程包含以下重点制程,1、a面线路使用直接网印、滚涂、干/湿膜曝光等线路生产方式,蚀刻后形成线路。2、b面使用直接网印、滚涂、干/湿膜曝光、模冲、模切等方式形成线路。3、以上a、b两面均经过100%aoi光学检测两层外边框自动打孔后裁切成单张。4、原则上使用a面(b面可以)用钻孔、激光打孔、模冲方式开出需要两层导通的孔。5、撕掉a面背后的离型膜,把b面线路层(设置有对位基准)对准a面背面的胶面,按照设计要求贴合,经冷/热压静置后撕掉b面线路后的承载膜。即完成线路转移制程。亦即本工艺特殊的制程。6、再对产品的a、b两层线路表面涂覆白油或贴覆盖膜等方式,即起到阻焊的作用。7、根据客户需求完成字符或表面处理等。8、可根据客户要求分切或整版交货。
38.同时本说明书中未作详细描述的内容均属于本领域技术人员公知的现有技术。
39.需要说明的是,在本文中,诸如第一和第二等之类的关系术语仅仅用来将一个实体或者操作与另一个实体或操作区分开来,而不一定要求或者暗示这些实体或操作之间存在任何这种实际的关系或者顺序。而且,术语“包括”、“包含”或者其任何其他变体意在涵盖非排他性的包含,从而使得包括一系列要素的过程、方法、物品或者设备不仅包括那些要素,而且还包括没有明确列出的其他要素,或者是还包括为这种过程、方法、物品或者设备所固有的要素。
40.尽管已经示出和描述了本发明的实施例,对于本领域的普通技术人员而言,可以理解在不脱离本发明的原理和精神的情况下可以对这些实施例进行多种变化、修改、替换和变型,本发明的范围由所附权利要求及其等同物限定。