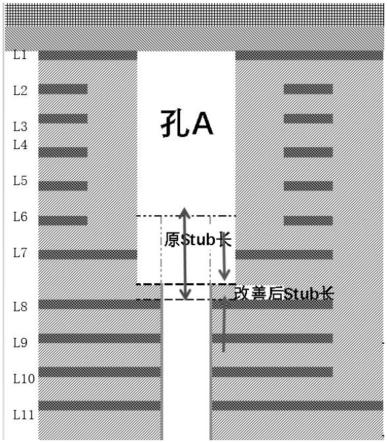
一种高精度pcb板加工方法
技术领域
1.本发明属于pcb加工技术领域,更具体的说涉及一种高精度pcb板加工方法。
背景技术:2.印制电路板(pcb)是电子设备中必不可少的关键元件,是高频高速信号传输的重要载体。随着电子技术的发展,信号传输速率及载波频率大幅增加,信号完整性受pcb电路结构影响越来越明显。理论分析,高频高速信号的损耗、串扰随传输距离增加而加剧,且也会大概率受其他噪声干扰,从而导致信号传输质量下降明显。在高频高速pcb制造过程中,为最大程度保证信号仅在预设的层与层之间进行导通,通常都会用到背钻孔技术。
3.背钻孔技术是通过机械控深钻孔的方法,使用直径比原来的孔粗0.15mm-0.2mm的钻针将电镀后的孔内不需导通且会对信号产生干扰的部分孔铜通过钻孔去除,保留需要导通的孔铜。
4.背钻孔深度控制原理是钻机通过电流感应控深,钻孔机装配有接触感应系统功能,一旦钻针接触导电物体,传感器装制会觉察到电流的改变,然后将信号传递给钻机,钻机立即以这个钻针接触的导电位置作为钻入深度的零点,然后钻机会钻入设定的深度。
5.由于多层板压合后板厚均匀性一般存在正负8%-10%的公差,且由于板内图形分布不均匀等原因板子会存在板弯翘现象,为保证背钻不至于超过目标层而导致目标层孔铜被钻掉后无法导通,因此实际背钻孔后往往存在较大的stub(该背钻掉的孔铜,还残留一截未完全钻掉),如附图1所示。以孔a为例,正常信号传输路径应为a
→b→c→
d,由于stub的存在实际信号输路径变为了a
→b→e→f→c→
d,导致信号出现振铃、上冲、下冲等异常,如附图2所示。
6.研究表明,stub会在高频高速pcb内形成寄生电容,且随stub长度的增加而变多,从而增加阻抗不连续异常。阻抗不连续会造成信号在传输过程中发生严重的回波损耗,stub还会对信号的插入损耗造成严重影响,stub越长高频时谐振越严重插损越大。
技术实现要素:7.针对现有技术的不足,本发明提供了一种可最大程度减少pcb背钻孔stub长度,从而降低stub对高频高速信号完整性的影响。
8.为实现上述目的,本发明提供了如下技术方案:一种高精度pcb板加工方法,包括如下步骤:
9.s1:设计,由背钻孔入钻方向看,在目标层上侧相邻层背钻钻针路径上设计导电铜图形,并将该层定义为参考层;
10.s2:计算,每个背钻孔进行两次计算背钻深度,第一次为初钻深度,第二次为精钻深度;
11.其中初钻深度=铝片理论厚度*88%+背钻起始层至参考层理论厚度*90%-钻机精度正公差;
12.其中精钻深度=参考层至目标层理论厚度*90%-钻机精度正公差;
13.s3:pcb板的钻前准备,将pcb板使用销钉固定在钻机的垫板上,pcb板上面放置铝片,使铝片与待钻pcb板对位重合,将铝片和pcb板固定;
14.s4:背钻孔加工,调取初钻的相关预设参数,启动初钻加工;初钻加工完成后,调取精钻的相关预设参数,启动精钻加工。
15.进一步的还包括步骤s5:检验,检查是否存在漏钻孔,出现漏钻孔的记录漏钻孔的位置,再次上钻机按照步骤s4进行补钻;使用孔位aoi检查背钻孔孔位精度,出现个别偏孔则报废处理,出现规律性偏孔异常时根据具体现象查找原因;使用定深规测量背钻孔深度,按每块pcb板上中下9点均分抽检,出现深度异常的情况立即停止批量生产,直到具体原因解决后再继续生产。
16.进一步的在步骤s3中,pcb板上面放置铝片后,再在铝片上面放置酚醛盖板,并将酚醛盖板、铝片和pcb板固定。
17.进一步的在步骤s3中,将酚醛盖板、铝片与pcb板对位重合,然后在四边使用美纹胶带封边粘合固定。
18.进一步的在步骤s4中,在初钻加工完成后,将pcb板上面的酚醛盖板与铝片移除,pcb板位置不动,然后在pcb板上叠放一层新的酚醛盖板,并通过美纹胶带将其与pcb板固定粘合,然后再进行精钻加工。
19.进一步的在步骤s5中,使用钻孔数孔机,检查是否存在漏钻孔。与现有技术相比,本发明的有益效果是:
20.1、本方案可最大程度减少pcb背钻孔stub长度,从而降低stub对高频高速信号完整性的影响,改善前后stub长度明显降低,且背钻孔深度越深则改善越明显;
21.2、采用本方案,可保证不同深度的背钻孔背钻后stub长度基本一致,从而有利于不同层间的信号设计及不同批次的pcb产品信号都能有接近一致的表现,有利于高频高速pcb产品的规模化及产业化。
附图说明
22.图1为采用现有技术方法进行背钻孔后pcb板的示意图;
23.图2为现有技术中的pcb板运行时理论信号与实际信号的示意图;
24.图3为采用本发明的方法进行背钻孔后pcb板的示意图;
25.图4为图3中孔a处的放大示意图。
具体实施方式
26.参照图4对本发明高精度pcb板加工方法的实施例做进一步说明。
27.在本发明的描述中,需要说明的是,对于方位词,如有术语“中心”,“横向(x)”、“纵向(y)”、“竖向(z)”、“长度”、“宽度”、“厚度”、“上”、“下”、“前”、“后”、“左”、“右”、“竖直”、“水平”、“顶”、“底”、“内”、“外”、“顺时针”、“逆时针”等指示方位和位置关系为基于附图所示的方位或位置关系,仅是为了便于叙述本发明和简化描述,而不是指示或暗示所指的装置或元件必须具有特定的方位、以特定方位构造和操作,不能理解为限制本发明的具体保护范围。
28.此外,如有术语“第一”、“第二”仅用于描述目的,而不能理解为指示或暗示相对重要性或隐含指明技术特征的数量。由此,限定有“第一”、“第二”特征可以明示或者隐含包括一个或者多个该特征,在本发明描述中,“数个”、“若干”的含义是两个或两个以上,除非另有明确具体的限定。
29.一种高精度pcb板加工方法,具体步骤如下,
30.s1、设计,由背钻孔入钻方向看,在目标层上侧相邻层背钻钻针路径上设计导电铜图形,并将该层定义为参考层;参考附图3中,孔a的l7层、孔b的l11层、孔c的l15层、孔d的l18层、孔e的l21层;
31.s2、计算,每个背钻孔进行两次计算背钻深度,第一次为初钻深度,第二次为精钻深度;
32.其中初钻深度=铝片理论厚度*88%+背钻起始层至参考层理论厚度*90%-钻机精度正公差;
33.其中精钻深度=参考层至目标层理论厚度*90%-钻机精度正公差;以附图3中孔a为例,初钻深度=(铝片理论厚度*88%+背钻起始层至参考层理论厚度*90%-钻机精度正公差)=(铝片理论厚度100um*88%+背钻起始层至参考层理论厚度l1层至l7层理论厚度860um*90%-钻机精度正公差50um)=(88um+774um-50um)=812um;
34.以附图3中孔a为例,精钻深度=(参考层至目标层理论厚度*90%-钻机精度正公差)=(参考层至目标层l7层至l8层理论厚度138um*90%-钻机精度正公差50um)=74.2um。
35.s3、pcb板的钻前准备,将pcb板使用销钉固定在钻机的酚醛垫板上,建议每块板子使用4颗直径3.2mm销钉,分别固定板子四角,以增加板子的固定牢固度;板子使用销钉固定后,板子上面依次放置铝片与酚醛盖板,铝片的作用是钻孔时将钻针高速旋转产生的高温及时散出,以避免高温对pcb板的碳化影响,同时可以提高钻针的使用寿命;酚醛盖板的作用是为了保证背钻孔的位置精度,由于背钻加工时钻针的旋转速度高达8万转每分钟,在钻针直接接触材质较硬的铝片或待钻板的瞬间会发生钻针偏移甚至断钻针的异常,为了减少这些异常的发生,建议在铝片上面加盖一层材质较软的酚醛盖板;酚醛盖板、铝片与待钻板对位重合后,在四边使用美纹胶带封边粘合固定,避免在背钻加工过程中出现铝片翘曲、移位等异常,影响背钻深度的精度;
36.s4、背钻孔加工,完成上述准备工作后,调取初钻的相关预设参数,启动初钻加工,具体参数可参考附表1;初钻加工完成后,将pcb板上面的酚醛盖板与铝片移除,pcb板位置不动仍然被销钉固定在钻机垫板上;然后在pcb板上叠放一层新的酚醛盖板,同样的新酚醛盖板四周再次与pcb板使用美纹胶带进行固定粘合;调取精钻的相关预设参数,启动精钻加工,具体参数可参考附表1;
37.s5、检验,使用钻孔数孔机,检查是否存在漏钻孔的异常,出现漏钻孔的记录漏钻孔的位置,再次上钻机按步骤s4进行补钻;使用孔位aoi检查背钻孔孔位精度,出现个别孔偏孔时直接报废处理,出现规律性偏孔异常时根据具体现象查找原因;使用定深规测量背钻孔深度,按每块pcb板上中下9点均分抽检,出现深度异常的情况立即停止批量生产,直到具体原因解决后再继续生产。
38.附表1:
39.40.41.42.[0043][0044]
以上所述仅是本发明的优选实施方式,本发明的保护范围并不仅局限于上述实施例,凡属于本发明思路下的技术方案均属于本发明的保护范围。应当指出,对于本技术领域的普通技术人员来说,在不脱离本发明原理前提下的若干改进和润饰,这些改进和润饰也应视为本发明的保护范围。